2017《注塑缺陷的原因分析与解决对策》--邓益善
注塑缺陷原因分析与解决方案
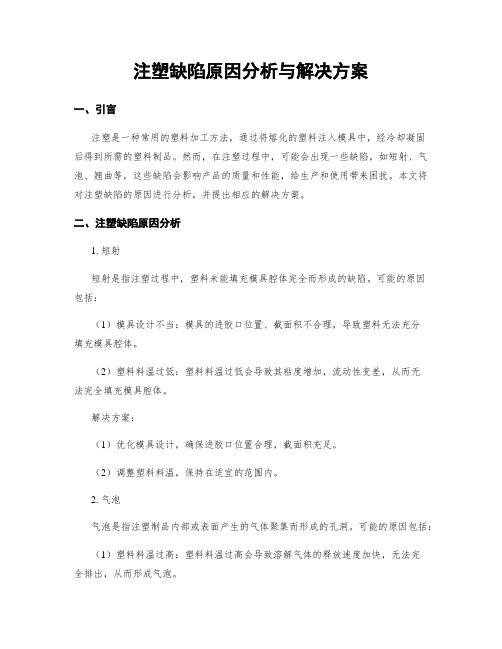
注塑缺陷原因分析与解决方案一、引言注塑是一种常用的塑料加工方法,通过将熔化的塑料注入模具中,经冷却凝固后得到所需的塑料制品。
然而,在注塑过程中,可能会出现一些缺陷,如短射、气泡、翘曲等,这些缺陷会影响产品的质量和性能,给生产和使用带来困扰。
本文将对注塑缺陷的原因进行分析,并提出相应的解决方案。
二、注塑缺陷原因分析1. 短射短射是指注塑过程中,塑料未能填充模具腔体完全而形成的缺陷。
可能的原因包括:(1)模具设计不当:模具的进胶口位置、截面积不合理,导致塑料无法充分填充模具腔体。
(2)塑料料温过低:塑料料温过低会导致其粘度增加,流动性变差,从而无法完全填充模具腔体。
解决方案:(1)优化模具设计,确保进胶口位置合理,截面积充足。
(2)调整塑料料温,保持在适宜的范围内。
2. 气泡气泡是指注塑制品内部或表面产生的气体聚集而形成的孔洞。
可能的原因包括:(1)塑料料温过高:塑料料温过高会导致溶解气体的释放速度加快,无法完全排出,从而形成气泡。
(2)模具排气不畅:模具腔体内的气体无法顺利排出,导致气泡的形成。
解决方案:(1)控制塑料料温,使其保持在适宜的范围内。
(2)优化模具结构,增加排气通道,确保气体能够顺利排出。
3. 翘曲翘曲是指注塑制品在冷却过程中,由于温度不均匀而导致的变形现象。
可能的原因包括:(1)模具温度不均匀:模具温度不均匀会导致注塑制品在冷却过程中收缩不均匀,从而产生翘曲。
(2)注塑压力不均匀:注塑过程中的压力分布不均匀,会导致塑料在模具中的填充不均匀,从而产生翘曲。
解决方案:(1)优化模具冷却系统,确保模具温度均匀。
(2)调整注塑过程中的压力分布,使之均匀。
三、结论注塑缺陷的原因多种多样,需要综合考虑多个因素。
在解决问题时,需要根据具体情况进行分析,并采取相应的解决方案。
通过优化模具设计、控制塑料料温、优化模具结构等手段,可以有效减少注塑缺陷的发生,提高产品质量和生产效率。
四、参考文献[1] 刘明, 张三. 注塑工艺缺陷原因分析及改进措施[J]. 塑料工业, 2018, 46(5): 12-15.[2] 王五, 李四. 注塑缺陷分析与解决方案研究[J]. 机械设计与制造, 2019, 37(2): 45-49.以上是对注塑缺陷原因分析与解决方案的详细描述,请参考。
注塑缺陷原因分析与解决方案
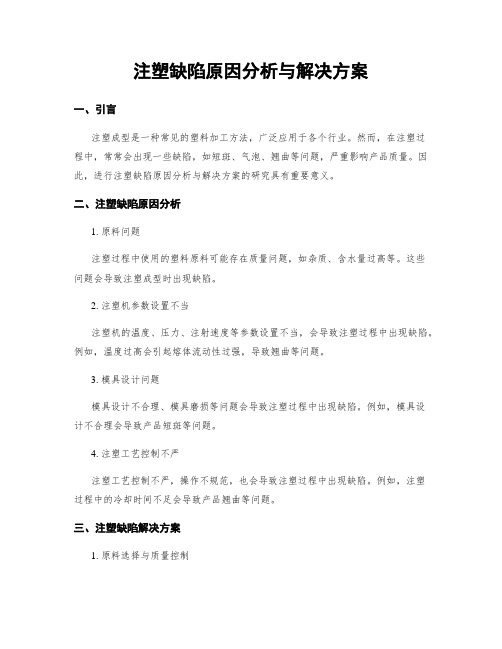
注塑缺陷原因分析与解决方案一、引言注塑成型是一种常见的塑料加工方法,广泛应用于各个行业。
然而,在注塑过程中,常常会出现一些缺陷,如短斑、气泡、翘曲等问题,严重影响产品质量。
因此,进行注塑缺陷原因分析与解决方案的研究具有重要意义。
二、注塑缺陷原因分析1. 原料问题注塑过程中使用的塑料原料可能存在质量问题,如杂质、含水量过高等。
这些问题会导致注塑成型时出现缺陷。
2. 注塑机参数设置不当注塑机的温度、压力、注射速度等参数设置不当,会导致注塑过程中出现缺陷。
例如,温度过高会引起熔体流动性过强,导致翘曲等问题。
3. 模具设计问题模具设计不合理、模具磨损等问题会导致注塑过程中出现缺陷。
例如,模具设计不合理会导致产品短斑等问题。
4. 注塑工艺控制不严注塑工艺控制不严,操作不规范,也会导致注塑过程中出现缺陷。
例如,注塑过程中的冷却时间不足会导致产品翘曲等问题。
三、注塑缺陷解决方案1. 原料选择与质量控制选择质量可靠的塑料原料供应商,并建立严格的原料质量控制流程。
对原料进行检测,确保无杂质、含水量符合要求。
2. 注塑机参数优化根据产品的特性和要求,合理设置注塑机的温度、压力、注射速度等参数。
通过试验和实践不断优化参数,提高注塑过程的稳定性和产品质量。
3. 模具设计与维护合理设计模具结构,避免出现短斑、翘曲等缺陷。
定期对模具进行维护和保养,及时更换磨损严重的部件,确保模具的稳定性和精度。
4. 注塑工艺控制与操作规范建立严格的注塑工艺控制流程,确保操作规范。
对注塑过程中的温度、压力、冷却时间等参数进行严格控制,避免出现缺陷。
5. 质量检测与反馈建立完善的质量检测体系,对注塑过程中的产品进行全面检测,及时发现和解决问题。
同时,建立反馈机制,将问题及时反馈给相关部门,进行改进和优化。
四、结论注塑缺陷是注塑成型过程中常见的问题,但通过对原因的分析和解决方案的实施,可以有效地提高产品质量,减少缺陷的发生。
因此,注塑缺陷原因分析与解决方案的研究具有重要的实际意义,并为注塑行业的发展提供了有益的参考。
注塑缺陷原因分析与解决方案
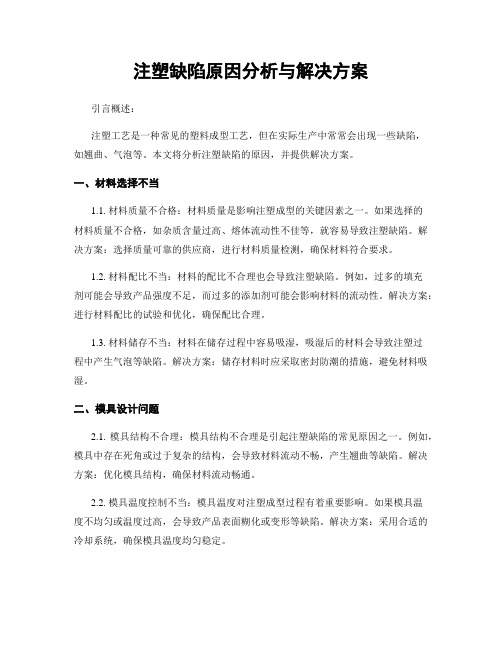
注塑缺陷原因分析与解决方案引言概述:注塑工艺是一种常见的塑料成型工艺,但在实际生产中常常会出现一些缺陷,如翘曲、气泡等。
本文将分析注塑缺陷的原因,并提供解决方案。
一、材料选择不当1.1. 材料质量不合格:材料质量是影响注塑成型的关键因素之一。
如果选择的材料质量不合格,如杂质含量过高、熔体流动性不佳等,就容易导致注塑缺陷。
解决方案:选择质量可靠的供应商,进行材料质量检测,确保材料符合要求。
1.2. 材料配比不当:材料的配比不合理也会导致注塑缺陷。
例如,过多的填充剂可能会导致产品强度不足,而过多的添加剂可能会影响材料的流动性。
解决方案:进行材料配比的试验和优化,确保配比合理。
1.3. 材料储存不当:材料在储存过程中容易吸湿,吸湿后的材料会导致注塑过程中产生气泡等缺陷。
解决方案:储存材料时应采取密封防潮的措施,避免材料吸湿。
二、模具设计问题2.1. 模具结构不合理:模具结构不合理是引起注塑缺陷的常见原因之一。
例如,模具中存在死角或过于复杂的结构,会导致材料流动不畅,产生翘曲等缺陷。
解决方案:优化模具结构,确保材料流动畅通。
2.2. 模具温度控制不当:模具温度对注塑成型过程有着重要影响。
如果模具温度不均匀或温度过高,会导致产品表面糊化或变形等缺陷。
解决方案:采用合适的冷却系统,确保模具温度均匀稳定。
2.3. 模具磨损严重:模具长时间使用后会出现磨损,磨损严重的模具会导致产品尺寸不准确或表面粗糙等缺陷。
解决方案:定期检查和维护模具,及时更换磨损严重的模具部件。
三、注塑工艺参数设置不当3.1. 注射压力过高或过低:注射压力是影响注塑成型的关键参数之一。
如果注射压力过高,会导致产品变形或开裂,而注射压力过低则会导致产品表面光洁度不高。
解决方案:根据产品要求和材料特性,合理设置注射压力。
3.2. 注射速度不合理:注射速度对产品的充填和冷却过程有着重要影响。
如果注射速度过快,会导致产品内部产生气泡或短射,而注射速度过慢则会导致产品表面瑕疵。
注塑制品缺陷的原因分析与解决措施

环境湿度变化大,影响塑料的稳定性和制品的外观。
空气污染
空气中存在灰尘、油雾等污染物,影响制品的外观和 质量。
03
注塑制品缺陷的解决措施
优化模具设计
模具设计合理化
确保模具设计符合产品要求,避免出现倒扣、 侧扣等设计不合理的地方。
避免模具损伤
提高模具的耐用性,避免使用过程中出现磨损 、断裂等问题。
优化浇口设计
合理设计浇口位置和大小,确保塑料能够均匀流入模具型腔。
把关原料质量
严格控制原料成分
确保原料中不含有杂质、异物等不良成分。
定期检测原料性能
对原料的性能进行定期检测,以确保其符合 生产要求。
加强原料存储管理
避免原料在存储过程中受潮、污染等问题。
调整工艺参数
合理调整注塑温度
根据塑料的性质和产品要求,合理调整注塑温度。
201 4
案例三:注塑制品出现银纹的原因及解决方法
原因分析
1. 塑料中含有水分或挥发性物质,导致银纹产 生。
2. 模具温度过低,导致塑料无法完全流动,出 现银纹。
案例三:注塑制品出现银纹的原因及解决方法
• 注射速度过快或压力过低,导致塑料在模具中流动不均匀,出现银纹。
案例三:注塑制品出现银纹的原因及解决方法
注塑制品缺陷的原因
分析与解决措施
汇报人:
日期:
• 注塑制品缺陷概述 • 注塑制品缺陷的原因分析 • 注塑制品缺陷的解决措施 • 注塑制品缺陷案例分析
目录
01
注塑制品缺陷概述
注塑制品常见缺陷
01 02 03 04
翘曲变形 缩痕 气泡 烧焦
注塑制品常见缺陷
01 02
溢边 裂纹
颜色差异
注塑缺陷原因分析与解决方案
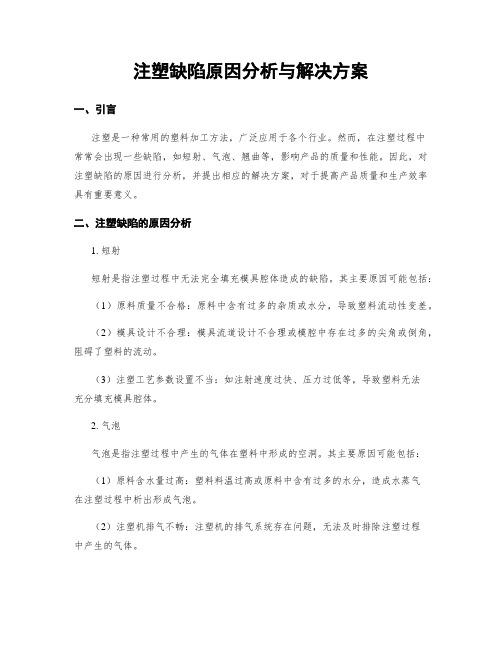
注塑缺陷原因分析与解决方案一、引言注塑是一种常用的塑料加工方法,广泛应用于各个行业。
然而,在注塑过程中常常会出现一些缺陷,如短射、气泡、翘曲等,影响产品的质量和性能。
因此,对注塑缺陷的原因进行分析,并提出相应的解决方案,对于提高产品质量和生产效率具有重要意义。
二、注塑缺陷的原因分析1. 短射短射是指注塑过程中无法完全填充模具腔体造成的缺陷。
其主要原因可能包括:(1)原料质量不合格:原料中含有过多的杂质或水分,导致塑料流动性变差。
(2)模具设计不合理:模具流道设计不合理或模腔中存在过多的尖角或倒角,阻碍了塑料的流动。
(3)注塑工艺参数设置不当:如注射速度过快、压力过低等,导致塑料无法充分填充模具腔体。
2. 气泡气泡是指注塑过程中产生的气体在塑料中形成的空洞。
其主要原因可能包括:(1)原料含水量过高:塑料料温过高或原料中含有过多的水分,造成水蒸气在注塑过程中析出形成气泡。
(2)注塑机排气不畅:注塑机的排气系统存在问题,无法及时排除注塑过程中产生的气体。
(3)注塑工艺参数设置不当:如注射速度过快、压力过高等,造成塑料内部气体无法顺利排出。
3. 翘曲翘曲是指注塑制品在冷却后出现变形的现象。
其主要原因可能包括:(1)模具温度不均匀:模具温度不均匀导致注塑制品冷却不均匀,从而引起翘曲。
(2)注塑过程中的应力积累:注塑过程中,塑料在注射后会受到冷却和收缩的影响,如果释放不及时,会导致应力积累引起翘曲。
(3)注塑工艺参数设置不当:如注射速度过快、冷却时间过短等,造成塑料冷却不充分,引起翘曲。
三、注塑缺陷的解决方案1. 短射的解决方案(1)优化原料质量:选择质量合格的原料,避免杂质和水分的存在。
(2)优化模具设计:合理设计模具流道,避免尖角和倒角的存在,保证塑料的顺畅流动。
(3)优化注塑工艺参数:合理设置注射速度和压力,确保塑料能够充分填充模具腔体。
2. 气泡的解决方案(1)控制原料含水量:确保塑料料温适宜,原料中的水分含量符合要求。
注塑缺陷的原因分析与解决对策

注塑缺陷的原因分析与解决对策主讲:邓益善(中国杰出注塑技术、模具设计优化技术培训实战专家,硕士)课程对象:注塑模具企业总经理、厂长、副总、部门经理、注塑工程师、注塑领班、调机技术员、模具结构设计工程师,产品设计开发工程师、跟模工程师、品管等等。
授课方式:讲师讲授 + 视频演绎 + 案例研讨 +角色扮演 + 讲师点评【课程背景】注塑成型不良品多、效率低,材料损耗多、成本居高不下、出现问题找不到原因?经常修模、频繁调机,注塑件批量退货、延误交期?长期以来,大多数相关工程师过分依赖自己片面的经验,对一些综合性的问题缺乏科学系统的分析能力,对已经出现的生产问题缺乏解决问题的措施。
邓益善老师基于扎实的生产实践与技术指导经历,将实实在在从根源上帮助解决这些问题和烦恼。
【课程价值】1.最佳注塑工艺参数设定方法,最佳模具设计方案;2.详细分析注塑缺陷的原因,提出大师级的注塑调机、模具设计、产品设计等解决方案;3.大量典型实例讲解、分析;4.学员自带不良品、现场解决问题、互动探讨;5.世界最先进的、全国独有的系统,全真展现注塑生产过程,动态显示生产现场看得见以及看不见的环节和变化,等于将注塑车间搬到培训大厅。
6.培养融汇注塑与模具技术的问题解决专家。
【培训内容】第一部分:塑料材料性能特点、使用注意事项第二部分:最佳注塑工艺设定方法1.时间、温度、压力、速度、位置等关键注塑工艺参数内在影响及设定要点;2.螺杆转速、背压、残料、松退等相关设定要点;3.多段充填的应用与设定;4.多段保压的应用与设定;5.速度/压力切换点的设定方法;6.塑料分子、玻璃纤维排向对质量的影响以及如何控制;7.内应力产生与注塑工艺条件之间的关系;8.内应力的检测方法、控制措施与改善技术;9.科学注塑技术:有效收集工艺信息与监测生产问题;第三部分:注塑现场问题分析与解决对策注塑问题描述、原因分析,如常见的缩孔、缩水、不饱模、毛边、熔接痕、银丝、喷痕、烧焦、翘曲变形、开裂/破裂、尺寸超差及其它等等,以及在产品结构设计、模具设计、成型工艺控制及塑料材料等方面之全面解决对策。
注塑缺陷原因分析与解决方案
注塑缺陷原因分析与解决方案一、引言注塑是一种常见的塑料加工方法,广泛应用于各个行业。
然而,在注塑过程中,可能会出现一些缺陷,影响产品的质量和性能。
本文将对注塑缺陷的原因进行分析,并提出相应的解决方案,以帮助企业改进注塑工艺,提高产品质量。
二、注塑缺陷原因分析1. 模具问题模具是注塑过程中的重要因素之一。
模具的设计和制造质量直接影响产品的成型质量。
常见的模具问题包括模具磨损、模具材料选择不当等。
这些问题可能导致产品表面粗糙、尺寸不准确等缺陷。
2. 塑料材料问题塑料材料的选择和质量也会对注塑产品的质量产生影响。
塑料材料的熔体流动性、热稳定性等性能与产品的成型质量密切相关。
如果选择的塑料材料不合适或质量不过关,可能会导致产品出现缺陷,如短斑、气泡等。
3. 注塑工艺参数问题注塑工艺参数的设置对产品的质量起着至关重要的作用。
常见的注塑工艺参数包括注射速度、保压时间、射胶压力等。
如果这些参数设置不当,可能会导致产品出现缺陷,如翘曲、收缩等。
4. 操作人员问题操作人员的技术水平和操作规范也会对注塑产品的质量产生重要影响。
如果操作人员操作不当,可能会导致产品出现缺陷,如烧焦、变形等。
三、注塑缺陷解决方案1. 模具问题解决方案针对模具问题,可以采取以下解决方案:- 定期检查和维护模具,及时修复磨损部位,确保模具的精度和质量。
- 选择合适的模具材料,确保模具的耐磨性和使用寿命。
2. 塑料材料问题解决方案针对塑料材料问题,可以采取以下解决方案:- 选择合适的塑料材料,根据产品的要求选择具有良好流动性和热稳定性的材料。
- 严格控制塑料材料的质量,确保供应商提供的材料符合产品的要求。
3. 注塑工艺参数问题解决方案针对注塑工艺参数问题,可以采取以下解决方案:- 根据产品的要求和塑料材料的性能,合理设置注塑工艺参数,确保产品的成型质量。
- 进行工艺参数的优化和调整,通过试模和实验,找到最佳的注塑工艺参数。
4. 操作人员问题解决方案针对操作人员问题,可以采取以下解决方案:- 加强操作人员的培训和技术水平提升,确保操作人员具备良好的注塑操作技能和操作规范。
注塑缺陷原因分析与解决方案
注塑缺陷原因分析与解决方案一、引言注塑成型是一种常用的塑料加工方法,广泛应用于各个行业。
然而,在注塑过程中,常常会出现一些缺陷,如短射、气泡、翘曲等问题,这些缺陷严重影响了产品的质量和性能。
因此,进行注塑缺陷原因分析并提出解决方案,对于提高产品质量和生产效率具有重要意义。
二、注塑缺陷原因分析1. 短射短射是指注塑件在充模过程中未能充满整个模腔,造成注塑件缺陷。
短射的原因可以有多种,如模具设计不合理、注射速度过快、注射压力不足等。
针对不同的原因,可以采取以下解决方案:- 检查模具设计,确保模腔设计合理,避免出现过于复杂或过于细长的结构;- 调整注射速度,避免过快的注射速度导致塑料无法充满整个模腔;- 调整注射压力,确保注塑件能够完全填充模腔。
2. 气泡气泡是注塑过程中常见的缺陷,会导致注塑件表面不光滑,影响外观质量。
气泡的形成原因主要有以下几点:塑料中含有挥发性成分、注射速度过快、模具排气不畅等。
为了解决气泡问题,可以采取以下措施:- 使用低挥发性塑料,减少塑料中的挥发性成分;- 调整注射速度,避免过快的注射速度导致气泡产生;- 检查模具排气系统,确保排气畅通。
3. 翘曲翘曲是指注塑件在冷却过程中由于内外表面温度差异引起的变形现象。
翘曲的原因主要有材料收缩率不一致、模具温度控制不当等。
为了解决翘曲问题,可以采取以下方法:- 选择具有一致收缩率的塑料材料,减少翘曲的可能性;- 控制模具温度,确保注塑件冷却均匀,避免温度差异导致翘曲。
三、解决方案的实施和效果评估在实施解决方案之前,需要进行充分的实验和测试,以验证方案的可行性和有效性。
在实施过程中,需要注意以下几点:1. 确保操作人员熟悉解决方案的具体步骤和操作要点;2. 根据实际情况,对解决方案进行适当的调整和优化;3. 对解决方案的实施效果进行评估,包括产品质量改善程度、生产效率提升等方面的指标。
通过实施解决方案,可以有效地解决注塑缺陷问题,提高产品质量和生产效率。
注塑成型缺陷的成因及解决方法
注塑成型缺陷的成因及解决方法注塑成型缺陷的成因及解决方法空隙往往发生在壁相对较厚的制品内并且是在最厚的地方。
一物理原因当制品内有泡产生时,经常认为是模具内的空气被流入模腔的熔料裹入。
另一个解释是料筒内的水气和气泡会想方设法进入到制品的内部。
所以说,这样的“泡”的产生有多方面的根源。
一开始,生产的制品会形成一层坚硬的外皮,并且视模具冷却的程度往里或快或慢的发展。
然而在厚壁区域里,中心部分仍继续保持较长时间的粘性。
外皮有足够强度抵抗任何应力收缩。
结果,里面的熔料被往外拉长,在制品内仍为塑性的中心部分形成空隙。
二与加工参数有关的原因与改良措施:1、保压太低提高保压压力2、保压时间太短提高保压时间3、模壁温度太低提高模壁温度4、熔料温度太高降低熔体温度三与设计有关的原因与改良措施:1、浇口横截面太小增加浇口横截面,缩短浇道2、喷嘴孔太小增大喷嘴孔3、浇口开在薄壁区浇口开在厚壁区注塑成型各种缺陷及解决方法2017-03-22 16:02 | #2楼一、龟裂龟裂是塑料制品较常见的一种缺陷,产生的主要原因是由于应力变形所致。
主要有残余应力、外部应力和外部环境所产生的应力变形。
(-)残余应力引起的龟裂残余应力主要由于以下三种情况,即充填过剩、脱模推出和金属镶嵌件造成的。
作为在充填过剩的情况下产生的龟裂,其解决方法主要可在以下几方面入手:(1)由于直浇口压力损失最小,所以,如果龟裂最主要产生在直浇口附近,则可考虑改用多点分布点浇口、侧浇口及柄形浇口方式。
(2)在保证树脂不分解、不劣化的前提下,适当提高树脂温度可以降低熔融粘度,提高流动性,同时也可以降低注射压力,以减小应力。
(3)一般情况下,模温较低时容易产生应力,应适当提高温度。
但当注射速度较高时,即使模温低一些,也可减低应力的产生。
(4)注射和保压时间过长也会产生应力,将其适当缩短或进行th 次保压切换效果较好。
(5)非结晶性树脂,如as树脂、abs树脂、pmma树脂等较结晶性树脂如聚乙烯、聚甲醛等容易产生残余应力,应予以注意。
注塑缺陷原因分析与解决方案
注塑缺陷原因分析与解决方案一、背景介绍注塑是一种常见的塑料加工工艺,广泛应用于各个行业。
然而,在注塑过程中,可能会出现一些缺陷,如短射、气泡、翘曲等问题,这些缺陷会直接影响产品的质量和性能。
因此,对注塑缺陷的原因进行分析,并提出相应的解决方案,对于提高产品质量和生产效率具有重要意义。
二、注塑缺陷的常见原因1. 原料质量问题:注塑过程中使用的塑料原料可能存在质量问题,如杂质、颗粒不均匀等,这些问题会导致注塑缺陷的产生。
2. 注塑机参数设置不当:注塑机的温度、压力、速度等参数的设置不当会导致注塑缺陷的产生。
例如,温度过高或过低都会对塑料的熔融和流动性产生影响。
3. 模具设计问题:模具的设计不合理,如出口处设计不良、冷却系统不完善等,会导致注塑缺陷的产生。
4. 注塑工艺操作问题:操作人员对注塑工艺的不熟悉或不规范操作,如注塑时间过长、注射速度过快等,都会引发注塑缺陷。
5. 环境因素:环境温度、湿度等因素也会对注塑缺陷产生影响,例如,湿度过高会导致塑料吸湿,从而产生气泡。
三、注塑缺陷的解决方案1. 优化原料选择:选择质量可靠的原料供应商,确保原料的纯度和均匀性。
进行原料检测,排除存在问题的原料。
2. 调整注塑机参数:根据不同的塑料材料和产品要求,合理设置注塑机的温度、压力、速度等参数,确保塑料材料的熔融和流动性。
3. 优化模具设计:对模具进行优化设计,确保出口处的设计合理,冷却系统完善,避免注塑缺陷的产生。
使用高质量的模具材料,提高模具的耐磨性和使用寿命。
4. 规范操作流程:对操作人员进行培训,提高其对注塑工艺的理解和操作技能。
建立规范的操作流程和记录,及时发现和解决问题。
5. 控制环境因素:保持注塑车间的适宜温湿度,避免环境因素对注塑缺陷的影响。
使用除湿设备,控制湿度在合理范围内。
四、注塑缺陷分析方法1. 观察法:通过对注塑产品外观的观察,发现缺陷的类型和位置,进而分析可能的原因。
2. 断面分析法:通过截取注塑产品的断面,观察其内部结构,分析缺陷产生的原因。
- 1、下载文档前请自行甄别文档内容的完整性,平台不提供额外的编辑、内容补充、找答案等附加服务。
- 2、"仅部分预览"的文档,不可在线预览部分如存在完整性等问题,可反馈申请退款(可完整预览的文档不适用该条件!)。
- 3、如文档侵犯您的权益,请联系客服反馈,我们会尽快为您处理(人工客服工作时间:9:00-18:30)。
注塑缺陷的原因分析与解决对策
【主办单位】一六八培训网
【时间地点】2017年04月15-16日上海 04月22-23日深圳
2017年08月19-20日上海 08月26-27日深圳
2017年12月16-17日深圳 12月23-24日上海
【收费标准】¥3200元/人(包括资料费、午餐及上下午茶点等)
3. 大量典型实例讲解、分析;
4. 学员自带不良品、现场解决问题、互动探讨;
5. 世界最先进的、全国独有的系统,全真展现注塑生产过程,动态显示生产现场看得见以及
看不见的环节和变化,等于将注塑车间搬到培训大厅。
片面的经验,对一些综合性的问题缺乏科学系统的分析能力,对已经出现的生产问题缺乏解决问题的措施。
邓益善老师基于扎实的生产实践与技术指导经历,将实实在在从根源上帮助解决这些问
第二部分:最佳注塑工艺设定方法
1. 如何设定各项关键注塑工艺参数;
2. 时间、温度、压力、速度、位置等参数设定要点;
3. 螺杆相关设定要点;
4. 多段充填的设定与实际使用;
5. 多段保压的设定与实际使用;
6. 速度/压力切换点的设定方法;
7. 多视窗注塑成型技术运用;
8. 塑料分子排向对质量的影响以及如何控制
9. 注塑残余内应力对质量的影响以及如何控制
第三部分:注塑现场问题分析与解决对策
注塑问题描述、原因分析,如常见的缩孔、缩水、不饱模、毛边、熔接痕、银丝、喷痕、烧焦、翘曲变形、开裂/破裂、尺寸超差及其它等等,以及在产品结构设计、模具设计、成型工艺控制及塑料材料等方面之全面解决对策。
1. 注塑件周边缺胶、不饱模的原因分析及解决对策;
2. 批锋(毛边)的原因分析及解决对策;
3. 注塑件表面缩水、缩孔(真空泡)的原因分析及解决对策;
4. 银纹(料花、水花)、烧焦、气纹的原因分析解决对策;
5. 注塑件表面水波纹、流纹(流痕)的原因分析及解决对策;
6. 注塑件表面夹水纹(熔接痕)、喷射纹(蛇纹)的原因分析及解决对策;
7. 注塑件表面裂纹(龟裂)的原因分析及解决对策;
8. 注塑件表面色差、光泽不良、混色、黑条、黑点的原因分析及解决对策;
9. 注塑件翘曲变形、内应力开裂的原因分析及解决对策;
10. 注塑件尺寸偏差的原因分析及解决对策;
11. 注塑件透明度不足、强度不足(脆断)的原因分析及解决对策;
12. 学员自带产品问题解答。
第四部分:模具设计优化
实际上目前有相当部分产品品质问题是由模具设计不合理导致的,只是很多模具设计相关人员将责任推给了注塑相关人员。
1. 如何设计注塑车间生产OK的模具;
2. 如何设计注塑车间稳定、高效生产的模具;
3. 如何设计上档次的模具;
4. 浇口合理设计;
5. 流道合理设计;
6. 冷却水路合理设计;
7. 产品缩水率的设定与调整;
第五部分:模流分析技术应用(融汇于第三、四部分)
如何利用目前世界最强大的Moldflow模流分析技术快速地有效地预测问题、优化注塑工艺
和模具设计,从根本上解决问题。
第六部分:现场案例分析与讨论
第七部分:模塑新工艺
1. 热流道技术应用及相关问题解决;
2. 双色成型技术应用及相关问题解决;
3. 粉末注射成型技术应用;
中国杰出注塑技术、模具设计优化技术培训实战专家,硕士,先后在美、德、
滚打,并在咨询顾问中积累了丰富的经验,尤其深谙注塑缺陷原因分析与解决方案、模具设计优化技术,对注塑机械、塑料材料具有相当的技术功底,形成了独具特色的实干型模具/注塑技术方法和体系。
邓老师实践经验丰富、讲授过程列举大量案例、特别强调实用性和可操作性,深受听课人员的好评和尊敬。
至今邓老师为满足企业的实际需要,先后举办了注塑技术、模具设计优化技术方面的内训、公开课程共计600多场,参训企业4000家左右,培养了一大批优秀的企业技术人才,目前主要分布在上海、深圳、广东、江浙地区大中型生产型企业。
为国内企业生产技术培训工作做出了突出贡献,实实在在为企业解决了设计与生产难题。