QHDL 617-2011机加工通用技术标准
机械设计制造常用技术要求汇总
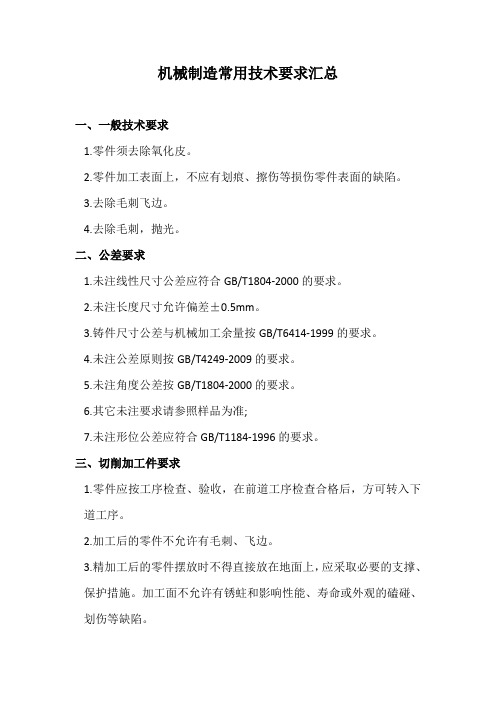
机械制造常用技术要求汇总一、一般技术要求1.零件须去除氧化皮。
2.零件加工表面上,不应有划痕、擦伤等损伤零件表面的缺陷。
3.去除毛刺飞边。
4.去除毛刺,抛光。
二、公差要求1.未注线性尺寸公差应符合GB/T1804-2000的要求。
2.未注长度尺寸允许偏差±0.5mm。
3.铸件尺寸公差与机械加工余量按GB/T6414-1999的要求。
4.未注公差原则按GB/T4249-2009的要求。
5.未注角度公差按GB/T1804-2000的要求。
6.其它未注要求请参照样品为准;7.未注形位公差应符合GB/T1184-1996的要求。
三、切削加工件要求1.零件应按工序检查、验收,在前道工序检查合格后,方可转入下道工序。
2.加工后的零件不允许有毛刺、飞边。
3.精加工后的零件摆放时不得直接放在地面上,应采取必要的支撑、保护措施。
加工面不允许有锈蛀和影响性能、寿命或外观的磕碰、划伤等缺陷。
4.滚压精加工的表面,滚压后不得有脱皮现象。
5.最终工序热处理后的零件,表面不应有氧化皮。
经过精加工的配合面、齿面不应有退火、发蓝、变色的现象。
6.加工的螺纹表面不允许有黑皮、磕碰、乱扣和毛刺等缺陷。
7.零件去除氧化皮。
8.零件加工表面上,不应有划痕、擦伤等损伤零件表面的缺陷。
四、材料要求1.材料:Q235-A,除有特殊说明。
五、模具要求1.未注拔模斜度2°-3°;六、涂装要求1.所有需要进行涂装的钢铁制件表面在涂漆前,必须将铁锈、氧化皮、油脂、灰尘、泥土、盐和污物等除去。
2.除锈前,先用有机溶剂、碱液、乳化剂、蒸汽等除去钢铁制件表面的油脂、污垢。
3.经喷丸或手工除锈的待涂表面与涂底漆的时间间隔不得多于6h。
4.铆接件相互接触的表面,在连接前必须涂厚度为30~40μm防锈漆。
搭接边缘应用油漆、腻子或粘接剂封闭。
由于加工或焊接损坏的底漆,要重新涂装。
5.表面涂装按照相应的标准要求。
七、热处理要求1.零件经淬火处理后,硬度应达到50~55HRC。
机械设计行业中常用标准
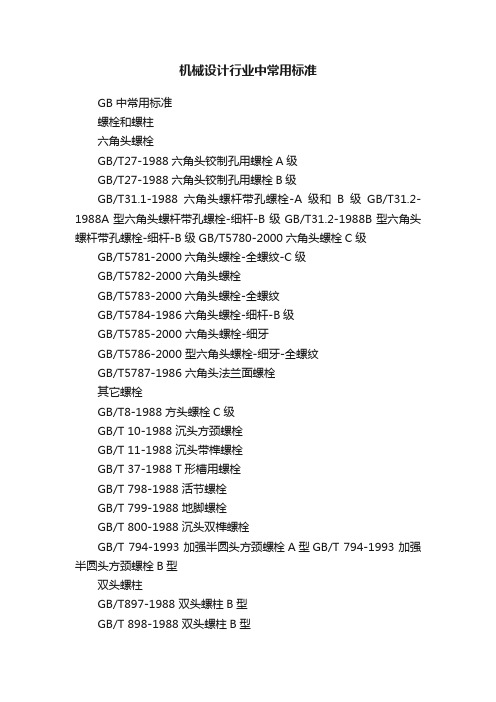
机械设计行业中常用标准GB中常用标准螺栓和螺柱六角头螺栓GB/T27-1988六角头铰制孔用螺栓A级GB/T27-1988六角头铰制孔用螺栓B级GB/T31.1-1988六角头螺杆带孔螺栓-A级和B级GB/T31.2-1988A型六角头螺杆带孔螺栓-细杆-B级GB/T31.2-1988B型六角头螺杆带孔螺栓-细杆-B级GB/T5780-2000六角头螺栓C级GB/T5781-2000六角头螺栓-全螺纹-C级GB/T5782-2000六角头螺栓GB/T5783-2000六角头螺栓-全螺纹GB/T5784-1986六角头螺栓-细杆-B级GB/T5785-2000 六角头螺栓-细牙GB/T5786-2000 型六角头螺栓-细牙-全螺纹GB/T5787-1986 六角头法兰面螺栓其它螺栓GB/T8-1988 方头螺栓C级GB/T 10-1988 沉头方颈螺栓GB/T 11-1988 沉头带榫螺栓GB/T 37-1988 T形槽用螺栓GB/T 798-1988 活节螺栓GB/T 799-1988 地脚螺栓GB/T 800-1988 沉头双榫螺栓GB/T 794-1993 加强半圆头方颈螺栓A型GB/T 794-1993 加强半圆头方颈螺栓B型双头螺柱GB/T897-1988 双头螺柱B型GB/T 898-1988 双头螺柱B型GB/T 899-1988 双头螺柱B型GB/T 900-1988 双头螺柱B型GB/T 901-1988 等长双头螺柱-B级GB/T 953-1988 等长双头螺柱-C级螺母六角螺母1型六角螺母C级(GB41-86)GB56-1988六角厚螺母GB808-1988小六角特扁细牙螺母GB/T6170-2000(1型六角螺母)GB/T6171-2000(1型六角螺母-细牙)GB/T6172.1-2000六角薄螺母GB/T6173-2000六角薄螺母-细牙GB/T6174-2000六角薄螺母-无倒角GB/T6175-2000(2型六角螺母)GB/T6176-2000(2型六角螺母-细牙) GB/T6177.1-2000六角法兰面螺母GB/T6177.2-2000六角法兰面螺母细牙六角锁紧螺母GB/T6184-2000(1型全金属六角锁紧螺母)GB/T6185.1-2000(2型全金属六角锁紧螺母)GB/T6185.2-2000(2型全金属六角锁紧螺母-细牙) GB/T6186-2000(2型全金属六角锁紧螺母-9级)六角开槽螺母GB6179-1986(1型六角开槽螺母-C级)GB6180-1986(2型六角开槽螺母-A级和B级)GB6181-1986六角开槽薄螺母-A和B级GB9457-1988(1型六角开槽螺母)GB9458-1988(2型六角开槽螺母-细牙-A级和B级) GB9459-1988六角开槽薄螺母GB6178-1986(1型六角开槽螺母-A和B级)圆螺母GB810-1988小圆螺母GB817-1988带槽圆螺母GB812-1988圆螺母滚花高螺母GB806-1988滚花高螺母GB807-1988滚花薄螺母其它螺母GB923-1988盖形螺母GB39-1988方螺母-C级螺钉十字槽螺钉GB/T818-2000十字槽盘头螺钉H型GB/T818-2000十字槽盘头螺钉Z型GB/T818-76 十字槽半圆头螺钉GB/T819.1-2000十字槽沉头螺钉第一部分H型GB/T819.1-2000十字槽沉头螺钉第一部分Z型GB/T820-2000十字槽半沉头螺钉H型GB/T820-2000十字槽半沉头螺钉Z型GB/T822-2000十字槽圆柱头螺钉H型GB/T823-1988十字槽小盘头螺钉GB9074.13十字槽外六角平垫弹垫组合螺钉(十字槽凹穴六角头螺栓)GB/T 29.2-88? 十字槽凹穴六角头螺栓GB9074.17不带十字的外六角组合螺栓GB/T9074.8 十字槽小盘头平垫、弹垫三组合螺钉GB9074.4 十字槽圆头平垫、弹垫三组合螺钉GB9074.1-88 十字槽盘头螺钉和平垫圈组合件GB/T 9074.15-1988六角头螺栓和弹簧垫圈组合件GB / T 97-2002; A级; 销轴用; 用于螺钉和垫圈组合件; 用于自攻螺钉和垫圈组合件平垫圈GB90744-88十字槽盘头螺钉、平垫圈和弹簧垫圈组合件国内标准共享版块紧定螺钉GB71-1985开槽锥端紧定螺钉GB/T73-1985开槽平端紧定螺钉GB/T74-1985开槽凹端紧定螺钉GB/T75-1985开槽长圆柱端紧定螺钉GB/T77-2000内六角平端紧定螺钉GB/T78-2000内六角锥端紧定螺钉GB/T79-2000内六角圆柱端紧定螺钉GB/T80-2000内六角凹端紧定螺钉GB83-1988方头长圆柱球面端紧定螺钉GB84-1988方头凹端紧定螺钉GB85-1988方头长圆柱端紧定螺钉GB86-1988方头短圆柱锥端紧定螺钉GB821-1988方头平端紧定螺钉紧定螺钉GB71-1985开槽锥端紧定螺钉GB/T73-1985开槽平端紧定螺钉GB/T74-1985开槽凹端紧定螺钉GB/T75-1985开槽长圆柱端紧定螺钉GB/T77-2000内六角平端紧定螺钉GB/T78-2000内六角锥端紧定螺钉GB/T79-2000内六角圆柱端紧定螺钉GB/T80-2000内六角凹端紧定螺钉GB83-1988方头长圆柱球面端紧定螺钉GB84-1988方头凹端紧定螺钉GB85-1988方头长圆柱端紧定螺钉GB86-1988方头短圆柱锥端紧定螺钉GB821-1988方头平端紧定螺钉圆柱头螺钉GB833-1988开槽大圆柱头螺钉GB/T70.1-2000内六角圆柱头螺钉GB/T65-2000开槽圆柱头螺钉GB/2673-2004 梅花槽沉头螺钉GB/2672-2004 梅花槽圆柱头螺栓JB/T6686-1993 梅花头法兰螺栓德标德标美标?GB/T9074.4/GB9074.8盘头组合螺钉GB/T9074.13十字外六角组合螺钉GB/T9074.17外六角三合螺钉铆钉系列:半空心铆钉、实心铆钉、铜铆钉、铝铆钉、铁铆钉规格从1.0-6.0 2.机螺丝系列:GB818、GB819、GB65、GB67、GB68、GB820、GB77等。
机械设计常用技术要求汇总
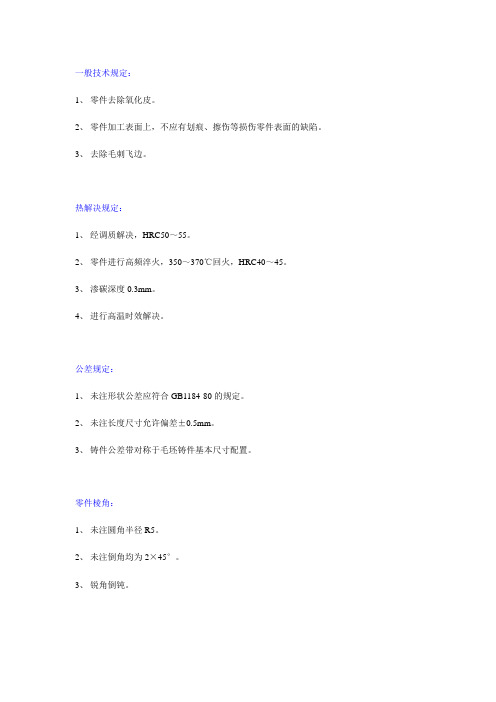
一般技术规定:1、零件去除氧化皮。
2、零件加工表面上,不应有划痕、擦伤等损伤零件表面的缺陷。
3、去除毛刺飞边。
热解决规定:1、经调质解决,HRC50~55。
2、零件进行高频淬火,350~370℃回火,HRC40~45。
3、渗碳深度0.3mm。
4、进行高温时效解决。
公差规定:1、未注形状公差应符合GB1184-80的规定。
2、未注长度尺寸允许偏差±0.5mm。
3、铸件公差带对称于毛坯铸件基本尺寸配置。
零件棱角:1、未注圆角半径R5。
2、未注倒角均为2×45°。
3、锐角倒钝。
装配规定:1、各密封件装配前必须浸透油。
2、装配滚动轴承允许采用机油加热进行热装,油的温度不得超过100℃。
3、齿轮箱装配后应设计和工艺规定进行空载实验。
实验时不应有冲击、噪声,温升和渗漏不得超过有关标准规定。
4、齿轮装配后,齿面的接触斑点和侧隙应符合GB10095和GB11365的规定。
5、装配液压系统时允许使用密封填料或密封胶,但应防止进入系统中。
6、进入装配的零件及部件(涉及外购件、外协件),均必须具有检查部门的合格证方能进行装配。
7、零件在装配前必须清理和清洗干净,不得有毛刺、飞边、氧化皮、锈蚀、切屑、油污、着色剂和灰尘等。
8、装配前应对零、部件的重要配合尺寸,特别是过盈配合尺寸及相关精度进行复查。
9、装配过程中零件不允许磕、碰、划伤和锈蚀。
10、螺钉、螺栓和螺母紧固时,严禁打击或使用不合适的旋具和扳手。
紧固后螺钉槽、螺母和螺钉、螺栓头部不得损坏。
11、规定拧紧力矩规定的紧固件,必须采用力矩扳手,并按规定的拧紧力矩紧固。
12、同一零件用多件螺钉(螺栓)紧固时,各螺钉(螺栓)需交叉、对称、逐步、均匀拧紧。
13、圆锥销装配时应与孔应进行涂色检查,其接触率不应小于配合长度的60%,并应均匀分布。
14、平键与轴上键槽两侧面应均匀接触,其配合面不得有间隙。
15、花键装配同时接触的齿面数不少于2/3,接触率在键齿的长度和高度方向不得低于50%。
机械加工检验标准及方法
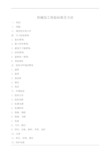
机械加工检验标准及方法一. 目的:二. 范围:三. 规范性引用文件四. 尺寸检验原则1.基本原则:2.最小变形原则:3.最短尺寸链原则:4.封闭原则:5.基准统一原则:6.其他规定五. 检验对环境的要求1.温度2.湿度3.清洁度4.振动5.电压六. 外观检验1.检验方法2.检验目距3.检测光源4.检测时间5.倒角、倒圆6.批锋、毛刺7.伤痕8.刀纹、振纹9.凹坑、凸起、缺料、多料、台阶10.污渍11.砂孔、杂物、裂纹12.防护包装七. 表面粗糙度的检验1.基本要求2.检验方法:3.测量方向4.测量部位5.取样长度八. 线性尺寸和角度尺寸公差要求1.基本要求2 线性尺寸未注公差九.形状和位置公差的检验1.基本要求3.检测方法十.螺纹的检验1.使用螺纹量规检验螺纹制件2.单项检验十一.外协加工件的检验规定1.来料检验2. 成品检验计划十二.判定规则附注:1.泰勒原则一. 目的:为了明确公司金属切削加工检验标准,使检验作业有所遵循,特制定本标准。
二. 范围:本标准适用于切削加工(包括外协、制程、出货过程)各检验特性的检验。
在本标准中,切削加工指的是:车削加工、铣削加工、磨削加工、镗削加工、刨削加工、孔加工、拉削加工和钳工作业等。
本标准规定了尺寸检验的基本原则、对环境的要求、外观检验标准、线性尺寸公差要求、形位公差要求、表面粗糙度的检验、螺纹的检验和判定准则。
注:本标准不适用于铸造、锻造、钣金、冲压、焊接加工后的检验,其检验标准另行制定。
本标准不拟对长度、角度、锥度的测量方法进行描述,可参看相关技术手册;形位公差的测量可参看GB/T1958-1980;齿轮、蜗杆的检验可参看相关技术手册。
三. 规范性引用文件下列文件中的条款通过本标准的引用而成为本标准的条款。
凡是注日期的引用文件,其随后所有的修改单(不包括勘误的内容)或修订版均不适用于本标准,然而,鼓励根据本标准达成协议的各方研究是否可使用这些文件的最新版本。
机械加工产品质量检验标准(液压支架、采煤机电控箱)
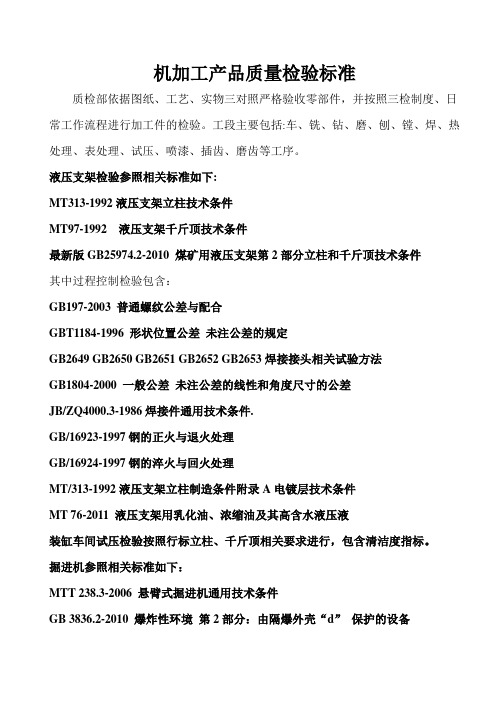
机加工产品质量检验标准质检部依据图纸、工艺、实物三对照严格验收零部件,并按照三检制度、日常工作流程进行加工件的检验。
工段主要包括:车、铣、钻、磨、刨、镗、焊、热处理、表处理、试压、喷漆、插齿、磨齿等工序。
液压支架检验参照相关标准如下:MT313-1992液压支架立柱技术条件MT97-1992 液压支架千斤顶技术条件最新版GB25974.2-2010 煤矿用液压支架第2部分立柱和千斤顶技术条件其中过程控制检验包含:GB197-2003 普通螺纹公差与配合GBT1184-1996 形状位置公差未注公差的规定GB2649 GB2650 GB2651 GB2652 GB2653焊接接头相关试验方法GB1804-2000 一般公差未注公差的线性和角度尺寸的公差JB/ZQ4000.3-1986焊接件通用技术条件.GB/16923-1997钢的正火与退火处理GB/16924-1997钢的淬火与回火处理MT/313-1992液压支架立柱制造条件附录A电镀层技术条件MT 76-2011 液压支架用乳化油、浓缩油及其高含水液压液装缸车间试压检验按照行标立柱、千斤顶相关要求进行,包含清洁度指标。
掘进机参照相关标准如下:MTT 238.3-2006 悬臂式掘进机通用技术条件GB 3836.2-2010 爆炸性环境第2部分:由隔爆外壳“d”保护的设备GB 3836.4-2010 爆炸性环境第4部分:由本质安全型“i”保护的设备加工件的形位公差未注公差按GBT1184-1996 GB1804-2000执行。
采煤机参照相关标准如下:MTT 84-1997 滚筒采煤机型式和基本参数.加工件的形位公差未注公差按GBT1184-1996 GB1804-2000执行。
液压支架加工件检验标准要点:一、直属件1、销轴内容包括:尺寸、外观、粗糙度、未注公差、主零主项用游标卡尺、外径千分尺、深度尺等检查各尺寸,外圆加工应在公差范围,放量不允许超出极限偏差的1/3,用粗糙度对比样块结合手感检查车序粗糙度,不符合图纸则判定不合格。
机械加工件检验标准
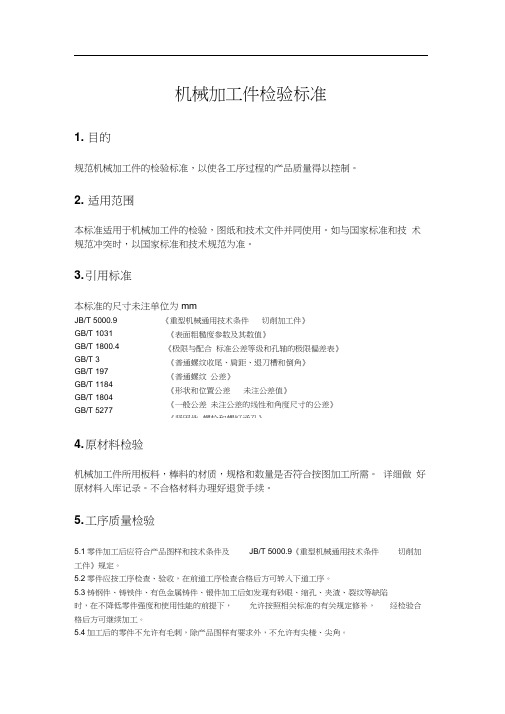
机械加工件检验标准1. 目的规范机械加工件的检验标准,以使各工序过程的产品质量得以控制。
2. 适用范围本标准适用于机械加工件的检验,图纸和技术文件并同使用。
如与国家标准和技术规范冲突时,以国家标准和技术规范为准。
3. 引用标准本标准的尺寸未注单位为mmJB/T 5000.9 GB/T 1031 GB/T 1800.4 GB/T 3GB/T 197 GB/T 1184 GB/T 1804 GB/T 5277《重型机械通用技术条件切削加工件》《表面粗糙度参数及其数值》《极限与配合标准公差等级和孔轴的极限偏差表》《普通螺纹收尾、肩距、退刀槽和倒角》《普通螺纹公差》《形状和位置公差未注公差值》《一般公差未注公差的线性和角度尺寸的公差》《紧固件螺栓和螺钉通孔》4. 原材料检验机械加工件所用板料,棒料的材质,规格和数量是否符合按图加工所需。
详细做好原材料入库记录。
不合格材料办理好退货手续。
5. 工序质量检验5.1零件加工后应符合产品图样和技术条件及JB/T 5000.9《重型机械通用技术条件切削加工件》规定。
5.2零件应按工序检查、验收,在前道工序检查合格后方可转入下道工序。
5.3铸钢件、铸铁件、有色金属铸件、锻件加工后如发现有砂眼、缩孔、夹渣、裂纹等缺陷时,在不降低零件强度和使用性能的前提下,允许按照相关标准的有关规定修补,经检验合格后方可继续加工。
5.4加工后的零件不允许有毛刺,除产品图样有要求外,不允许有尖棱、尖角。
5.5精加工后的零件不允许直接摆放在地面上,应采取必要的支撑、保护措施。
加工面不允许有锈蚀和影响性能、寿命或外观的磕碰、划伤等缺陷。
5.6精加工后的配合面、摩擦面和定位面等工作表面不允许打印标记。
5.7最终工序为热处理的零件,热处理后表面不应有氧化皮。
精加工后的配合面、齿面不应有退火、发蓝、变色的现象。
5.8对于生产图样中要求电镀锌或热镀锌的零件,图中要求的配合面尺寸为含镀层后的尺寸。
5.9表面电镀锌涂层的质量要求:1)镀层外观光滑细致、无起泡、起层、剥落、烧焦及海绵状沉淀;2)经铬酸钝化后,应具有绿黄略带有红色的彩虹色;3)镀层表面允许有不严重的流痕及轻微的刮痕印,允许工件边缘色彩稍淡;4)钝化膜有一定的光泽,不到呈暗褐无光的泥巴色;5)钝化膜应牢固,用布揩擦不掉;在50C〜60C的热水中煮1小时,颜色无显著减退。
机械加工通用技术规范(DOC)
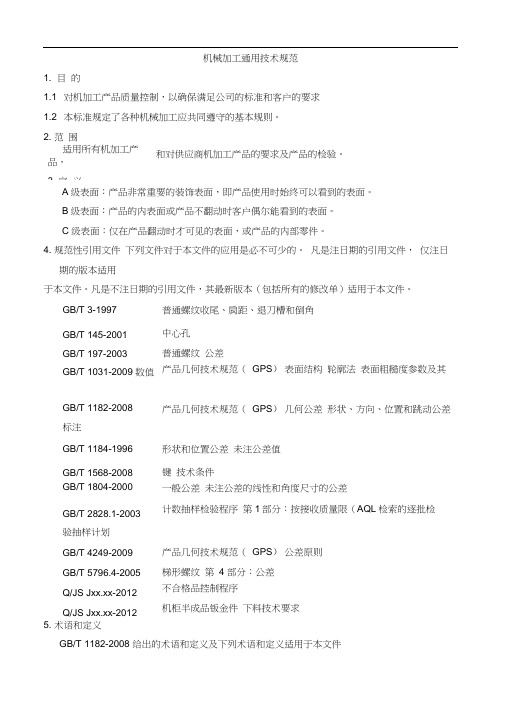
机械加工通用技术规范1. 目的1.1 对机加工产品质量控制,以确保满足公司的标准和客户的要求1.2 本标准规定了各种机械加工应共同遵守的基本规则。
2. 范围适用所有机加工产和对供应商机加工产品的要求及产品的检验。
品,3. 定义A级表面:产品非常重要的装饰表面,即产品使用时始终可以看到的表面。
B级表面:产品的内表面或产品不翻动时客户偶尔能看到的表面。
C级表面:仅在产品翻动时才可见的表面,或产品的内部零件。
4. 规范性引用文件下列文件对于本文件的应用是必不可少的。
凡是注日期的引用文件,仅注日期的版本适用于本文件。
凡是不注日期的引用文件,其最新版本(包括所有的修改单)适用于本文件。
GB/T 3-1997普通螺纹收尾、肩距、退刀槽和倒角GB/T 145-2001中心孔GB/T 197-2003普通螺纹公差GB/T 1031-2009 数值产品几何技术规范(GPS)表面结构轮廓法表面粗糙度参数及其GB/T 1182-2008产品几何技术规范(GPS)几何公差形状、方向、位置和跳动公差标注GB/T 1184-1996形状和位置公差未注公差值GB/T 1568-2008键技术条件GB/T 1804-2000一般公差未注公差的线性和角度尺寸的公差计数抽样检验程序第1部分:按接收质量限(AQL检索的逐批检GB/T 2828.1-2003验抽样计划GB/T 4249-2009产品几何技术规范(GPS)公差原则GB/T 5796.4-2005梯形螺纹第 4 部分:公差Q/JS Jxx.xx-2012不合格品控制程序Q/JS Jxx.xx-2012机柜半成品钣金件下料技术要求5. 术语和定义GB/T 1182-2008 给出的术语和定义及下列术语和定义适用于本文件5.1 切削加工用切削工具(包括刀具、磨具和磨料)把坯料或上多余的材料层切去成为切屑,使工件获得规定的几何形状、尺寸和表面质量的加工方法。
包括车削、铣削、刨削、磨削、拉削、钻孔、扩孔、铰孔、研磨、珩磨、抛光、超精加工及由它们组成的自动技术、数控技术、成组技术、组合机床、流水线、自动线。
机械设计行业GB中常用标准

机械设计行业GB中常用标准GB中常用标准螺栓和螺柱六角头螺栓GB/T27-1988六角头铰制孔用螺栓A级GB/T27-1988六角头铰制孔用螺栓B级GB/T31.1-1988六角头螺杆带孔螺栓-A级和B级GB/T31.2-1988A型六角头螺杆带孔螺栓-细杆-B级GB/T31.2-1988B型六角头螺杆带孔螺栓-细杆-B级GB/T5780-2000六角头螺栓C级GB/T5781-2000六角头螺栓-全螺纹-C级GB/T5782-2000六角头螺栓GB/T5783-2000六角头螺栓-全螺纹GB/T5784-1986六角头螺栓-细杆-B级GB/T5785-2000 六角头螺栓-细牙GB/T5786-2000 型六角头螺栓-细牙-全螺纹GB/T5787-1986 六角头法兰面螺栓其它螺栓GB/T8-1988 方头螺栓C级GB/T 10-1988 沉头方颈螺栓GB/T 11-1988 沉头带榫螺栓GB/T 37-1988 T形槽用螺栓GB/T 798-1988 活节螺栓GB/T 799-1988 地脚螺栓GB/T 800-1988 沉头双榫螺栓GB/T 794-1993 加强半圆头方颈螺栓A型GB/T 794-1993 加强半圆头方颈螺栓B型双头螺柱GB/T897-1988 双头螺柱B型GB/T 898-1988 双头螺柱B型GB/T 899-1988 双头螺柱B型GB/T 900-1988 双头螺柱B型GB/T 901-1988 等长双头螺柱-B级GB/T 953-1988 等长双头螺柱-C级螺母六角螺母1型六角螺母C级(GB41-86)GB56-1988六角厚螺母GB808-1988小六角特扁细牙螺母GB/T6170-2000(1型六角螺母)GB/T6171-2000(1型六角螺母-细牙)GB/T6172.1-2000六角薄螺母GB/T6173-2000六角薄螺母-细牙GB/T6174-2000六角薄螺母-无倒角GB/T6175-2000(2型六角螺母)GB/T6176-2000(2型六角螺母-细牙)GB/T6177.1-2000六角法兰面螺母GB/T6177.2-2000六角法兰面螺母细牙六角锁紧螺母GB/T6184-2000(1型全金属六角锁紧螺母)GB/T6185.1-2000(2型全金属六角锁紧螺母)GB/T6185.2-2000(2型全金属六角锁紧螺母-细牙) GB/T6186-2000(2型全金属六角锁紧螺母-9级)六角开槽螺母GB6179-1986(1型六角开槽螺母-C级)GB6180-1986(2型六角开槽螺母-A级和B级)GB6181-1986六角开槽薄螺母-A和B级GB9457-1988(1型六角开槽螺母)GB9458-1988(2型六角开槽螺母-细牙-A级和B级) GB9459-1988六角开槽薄螺母GB6178-1986(1型六角开槽螺母-A和B级)圆螺母GB810-1988小圆螺母GB817-1988带槽圆螺母GB812-1988圆螺母滚花高螺母GB806-1988滚花高螺母GB807-1988滚花薄螺母其它螺母GB923-1988盖形螺母GB39-1988方螺母-C级螺钉十字槽螺钉GB/T818-2000十字槽盘头螺钉H型GB/T818-2000十字槽盘头螺钉Z型GB/T818-76 十字槽半圆头螺钉GB/T819.1-2000十字槽沉头螺钉第一部分H型GB/T819.1-2000十字槽沉头螺钉第一部分Z型GB/T820-2000十字槽半沉头螺钉H型GB/T820-2000十字槽半沉头螺钉Z型GB/T822-2000十字槽圆柱头螺钉H型GB/T823-1988十字槽小盘头螺钉GB9074.13十字槽外六角平垫弹垫组合螺钉(十字槽凹穴六角头螺栓)GB/T 29.2-88 十字槽凹穴六角头螺栓GB9074.17不带十字的外六角组合螺栓GB/T9074.8 十字槽小盘头平垫、弹垫三组合螺钉GB9074.4 十字槽圆头平垫、弹垫三组合螺钉GB9074.1-88 十字槽盘头螺钉和平垫圈组合件GB/T 9074.15-1988六角头螺栓和弹簧垫圈组合件GB / T 97-2002; A级; 销轴用; 用于螺钉和垫圈组合件; 用于自攻螺钉和垫圈组合件平垫圈GB90744-88十字槽盘头螺钉、平垫圈和弹簧垫圈组合件国标准共享版块紧定螺钉GB71-1985开槽锥端紧定螺钉GB/T73-1985开槽平端紧定螺钉GB/T74-1985开槽凹端紧定螺钉GB/T75-1985开槽长圆柱端紧定螺钉GB/T77-2000六角平端紧定螺钉GB/T78-2000六角锥端紧定螺钉GB/T79-2000六角圆柱端紧定螺钉GB/T80-2000六角凹端紧定螺钉GB83-1988方头长圆柱球面端紧定螺钉GB84-1988方头凹端紧定螺钉GB85-1988方头长圆柱端紧定螺钉GB86-1988方头短圆柱锥端紧定螺钉GB821-1988方头平端紧定螺钉紧定螺钉GB71-1985开槽锥端紧定螺钉GB/T73-1985开槽平端紧定螺钉GB/T74-1985开槽凹端紧定螺钉GB/T75-1985开槽长圆柱端紧定螺钉GB/T77-2000六角平端紧定螺钉GB/T78-2000六角锥端紧定螺钉GB/T79-2000六角圆柱端紧定螺钉GB/T80-2000六角凹端紧定螺钉GB83-1988方头长圆柱球面端紧定螺钉GB84-1988方头凹端紧定螺钉GB85-1988方头长圆柱端紧定螺钉GB86-1988方头短圆柱锥端紧定螺钉GB821-1988方头平端紧定螺钉圆柱头螺钉GB833-1988开槽大圆柱头螺钉GB/T70.1-2000六角圆柱头螺钉GB/T65-2000开槽圆柱头螺钉GB/2673-2004 梅花槽沉头螺钉GB/2672-2004 梅花槽圆柱头螺栓JB/T6686-1993 梅花头法兰螺栓德标德标美标ASME/ANSI B 18.2.1-2010。
- 1、下载文档前请自行甄别文档内容的完整性,平台不提供额外的编辑、内容补充、找答案等附加服务。
- 2、"仅部分预览"的文档,不可在线预览部分如存在完整性等问题,可反馈申请退款(可完整预览的文档不适用该条件!)。
- 3、如文档侵犯您的权益,请联系客服反馈,我们会尽快为您处理(人工客服工作时间:9:00-18:30)。
Q/HDL 上海鸿得利重工股份有限公司企业标准机加工通用技术标准2011—12—25 发布2012—01—01实施上海鸿得利重工股份有限公司发布前言本标准针对工程机械的机械加工件通用技术要求,包括切削加工件的一般公差,角度尺寸的一般公差,形状和位置公差的一般公差等内容而制定。
本标准由上海鸿得利重工股份有限公司研发中心工艺研究所提出并起草。
本标准由上海鸿得利重工股份有限公司研发中心技术管理部标准化组归口。
本标准主要起草人:刘志坚、陈娜。
本标准为第1次制定。
21范围本标准规定了工程机械的机械加工件通用技术要求,包括切削加工件的一般公差,角度尺寸的一般公差,形状和位置公差的一般公差等内容。
本标准适用于公司各类机械加工件。
2引用标准下列标准包含的条文,通过在本标准中引用而构成为本标准的条文。
在标准出版时,所有版本均为有效。
所有标准.会被修订,使用本标准的各方应探讨使用下列标准最新版本的可能性。
GB/T3 普通螺纹收尾、肩距、退刀槽和倒角。
GB/T145 中心孔GB/T197 普通螺纹公差与配合(直径1~355mm)GB/T1184 形状和位置公差未注公差值GB/T1568 键技术条件GB/T1804 一般公差,未注公差的线性和角度尺寸的公差GB/T 2828.1计数抽样检验程序第1部分: 按接收质量限(AQL)检索的逐批检验抽样计划GB/T5796.4 梯形螺纹第4部分:公差GB/T5277 紧固件螺栓和螺钉通孔GB/T6403.4 零件倒圆与倒角JB/T5940 工程机械高锰钢铸件通用技术条件JB/T5941 工程机械有色合金铸件通用技术条件3一般要求3.1机械加工件必须符合产品图样、工艺规程和本标准的要求。
3.2机械加工件加工表面须保证其使用性能和外观质量,不允许有锈蚀、磕碰、划伤、裂纹、剥离及脱皮等缺陷。
3.3除有特殊要求外,加工后的零件不允许留有尖棱、尖角和毛刺。
3.4经加工后的零件在搬运、存放时,必须防止受到损伤、腐蚀及变形。
3.5精加工后的表面,摩擦面和定位面等工作表面不允许在其上打印标记。
3.6倒角图样中未注明的倒角表面粗糙度Ra值取12.5um,符合图1和表1的规定。
34图1表1 倒角高度 mm3.7 倒圆图样中未注明倒圆尺寸,又无清根要求时,应符合图2和表2的规定。
图2表2 倒角半径 mm注: D 1)值用于盲孔倒圆。
非圆柱面的倒圆可参照此表。
3.8 成组配对加工的零件,如滑动轴承上下轴瓦、齿轮箱上下盖及配对使用的螺旋锥齿轮等应有标记。
4未注尺寸公差4.1未注线性尺寸公差(不包括倒圆半径及倒角)的极限偏差按GB/T 1804表1中m 级选取,其值见表3。
表3 mm54.2倒角高度和倒圆半径按GB/T6403.4的规定选取。
其尺寸的极限偏差数值按GB/T 1804表2中mC 级选取,见图3和表4。
图3表4 倒圆半径与倒角高度尺寸的极限偏差数值 mm 4.3 齿轮、蜗轮、链轮的齿形倒角应符合表5的规定 ,倒角尺寸的极限偏差应符合4.2条款表5 mm4.4 盲孔钻孔深度的极限 偏差不得超过下列规定:a )孔深小于或等到于50mm 时,极限偏差为0.30+ mm 。
b) 孔深大于50mm 时,极限偏差为0.50+ mm 。
4.5 凡锪平处以最低点测量,锪平深度的极限偏差为0.50+ mm 。
4.6 一面为加工面,一面为非加工面的未注尺寸偏差应符合下列规定。
a) 铸件、锻件及焊接件按相应的工程机械通用技术条件中规定的非加工未注尺寸公差的极限偏差的70%对称分布。
b) 铸、锻件的凸缘或壁厚允许减薄,当壁厚小于或等于10mm 时,其减薄量不得大于壁厚的20%;当壁厚大于10 mm 时,其减薄量不得大于壁6厚的15%。
5未注形状和位置公差5.1 未注形状公差5.1.1 图样上未标注的直线度和平面度的公差值按GB/T1184表1中H 级取值,具体公差值见表6。
表6 mm注:表中被测要表尺寸L ,对直线公差值系指被测要素的长度尺寸,对平面度公差值系指被测表面轮廓的较大尺寸。
5.1.2圆度图样上圆度的未注公差值等于直径公差值,但不应大于GB/T1184表4中的径向圆跳动值,其值见表7。
表7 圆度的未注公差值 mm5.2未注位置公差5.2.1 图样上未注的对称度的公差值按GB/T1184表3中K 级取值,具体数值见表8,对称度应取两要素中较大者作为基准,较短者作为被测要素;若两要素长度相等则可任选一要素作为基准.表8 对称度的未注公差值 mm5.2.2平行度平行度的未注公差值等于给出的尺寸公差值,或是直线度和平行度未注公差中的相应公差值取较大者。
应取两要素中的较大长者作为基准,若两要素的长度相等则可选任一要素为基准。
5.2.3垂直度图样上垂直度的未注公差值按GB/T 1184表2规定中H 级选取.其数值见表9。
取形成直角的两边中较长的一边作为基准,较短的一边作为被测要素;若两边的长度相等则可取其中的任意一边作为基准。
7表9 垂直度的未注公差值 mm5.2.4同轴度在极限状况下,同轴度的未注公差值可以与表7中规定的径向圆跳动的未注公差相等,应选两要素中的较长者为基准,若两要素长度相等则可任选一要素为基准。
5.2.5圆跳动圆跳动的(径向、端面和斜向)的未注公差值见表7。
对于圆跳动的未注公差值,应以设计或工艺给出的支承面作为基准,否则应取两要素中较长的一个作为基准;若两要素长度相等则可任选一要素为基准。
5.2.6任意两螺钉、螺栓孔中心距的极限偏差当图样上未注明时,按表10的规定。
螺钉和螺钉通孔尺寸按GB/T 5277选取。
表10 mm6 未注公差角度的极限偏差角度尺寸的极限偏差按GB/T 1804的表3选取,其数值见表11,表中长度值按短边长度确定;若为圆锥角,当锥度为1:3~1:500的圆锥,按圆锥长度确定;当锥度大于1:3的圆锥,按其素线长度确定。
表11 角度尺寸的极限偏差数值 mm7 圆柱体结合面的表面粗糙度选择按表12 选取表128螺纹8.1 加工的螺纹表面不允许有黑皮,磕碰,乱扣和毛刺等缺陷。
8.2 螺纹的加工精度和表面粗糙度,当图样上未注明时,应按下列规定:a)普通螺纹精度应按GB/T 197规定的6H、6g级,内螺纹表面粗糙度Ra值为12.5um,外螺纹表面粗糙度Ra为6.3um。
b)梯形螺纹精度应按GB/T 5796.4的规定,内螺纹表面粗糙度Ra值为6.3um,外螺纹表面粗糙度Ra值为3.2um。
898.3 外螺纹轴线对杆部轴线的同轴度及内螺纹轴线对孔部轴线的同轴度,分别不大于外螺纹大径及内螺纹大径的尺寸公差之半(图4)。
图48.4 螺纹收尾,肩距,退刀槽,倒角应符合 GB/T 3的规定。
8.5 攻制螺孔的轴线对端面的垂直度应按表13的规定。
表13 mm8.6 丝杆、蜗杆等端面的第一圈螺纹,螺牙应修整,其端部牙形厚度应大于1mm 。
9键和键槽9.1 键符合GB/T 1568的规定。
9.2 当键长L 与键宽b 之比大于或等于8时,键工作面长度方向的平行度应符合下列规定,其数值见表14。
表14 mm注:1)当键宽小于或等于6 mm 时,公差等级按7级。
2)当键宽大于或等于8~36 mm 时,公差等级按6级。
3)当键宽大于或等于40 mm 时,公差等级按5级。
9.3 未注键槽两工作面平行度的公差应按表13中等级7级选取。
9.4 未注键槽的对称度按GB/T 1184附表4中9级取值,其数值见表15。
表 15 mm10中心孔10.1图样中未注明,加工中又需要中心孔的零件,在不影响使用和外观的情况下,加工后的中心孔可以保留。
10.2 除有特殊要求,中心孔应符合GB/T 145的规定。
11检验规则11.1凡经机械加工件,由制造厂质量检验部门按图样、有关技术文件和本标准进行检查和验收11.2 机械加工件的外观按3.2~3.5条要求进行检查。
11.3 机械加工件的未注尺寸、公差和角度公差分别按第4条和第6条要求进行检查。
11.4 机械加工件的未注形状和位置公差按第5条要求进行检查。
11.5 机械加工螺纹的外观、尺寸精度、形位公差、表面粗糙度按第8条要求进行检查。
11.6 键和键槽的尺寸精度、形位公差按第9条要求进行检查。
11.7 主要机械加工件应逐件检查几何形状与尺寸;一般机械加工件应抽检几何形状与尺寸,抽检方法由制造厂根据产品批量大小和质量水平按GB/T2828.1在产品技术标准或订货技术要求中做具体规定。
12标志、包装、运输、贮存12.1 出厂的机械加工件应有制造厂的标志。
12.1.2 标志的位置应不使机械化加工件的质量受到损伤。
12.1.3 机械加工件出厂应附有合格证或质量证明书,其中应注明:a) 制造厂名称;b) 零件名称,图号;c) 材质;d) 制造日期。
12.2 包装、运输和贮存机械加工件的包装、运输和贮存应符合有关标准或订货协议的规定。
10。