机械加工通用技术要求规范
机械加工、焊接、装配常用技术要求

1.去除飞边、毛刺,锐角倒钝; 2.尺寸未注公差参照GB/T 1804-2000 m等级; 3.形位未注公差参照GB/T 1184-1996 K等级。
1.进入装配的零件及部件(包括外购件、外协件),均必须具有检验部门的合格证方能进行装配; 2.零件在装配前必须清理和清洗干净,不得有毛刺、飞边、氧化皮、锈蚀、切屑、油污、着色剂和灰 尘等; 3.装配过程中零件不允许磕、碰、划伤和锈蚀; 4.部件要求运转顺畅无卡阻; 5.安装时严禁蛮力敲打等暴力操作方式。
(1) 尺寸公差精度等级按 B 级;
(2) 形位公差精度等级按 F 级;
(3) 焊逢质量评定等级按 BS, BK 级; 2.下料板材应光整,无毛刺.焊前材料进行预处理; 3.未注焊缝为连续角焊缝,焊角高8-10mm。
1.毛坯材料按照板材、棒材或锻件应符合如下对应要求: GB/T 2965-2007 钛及钛合金棒材; GB/T 3621-2007 钛及钛合金板材; GB/T 25137-2010 钛及钛合金锻件;
1.去除飞边、毛刺,锐角倒钝; 2.未注倒角C0.5; 3.尺寸未注公差参照GB/T 1804-2000 m等级; 4.形位未注公差参照GB/T 1184-1996 K等级; 5.热处理HRC48-52; 6.表面去除飞边、毛刺,锐角倒钝; 4.尺寸未注公差参照GB/T 1804-2000 m等级; 5.形位未注公差参照GB/T 1184-1996 K等级。
1.去除飞边、毛刺,锐角倒钝; 2.未注倒角C0.5; 3.尺寸未注公差参照GB/T 1804-2000 m等级; 4.形位未注公差参照GB/T 1184-1996 K等级; 5.表面镀锌。
1.去除飞边、毛刺,锐角倒钝; 2.尺寸未注公差参照GB/T 1804-2000 m等级; 3.形位未注公差参照GB/T 1184-1996 K等级; 4.表面硬质阳极氧化处理,氧化膜厚度40微米,颜色纯黑色,
外协机械加工通用技术要求

外协机械加工通用技术要求1、目的为了保证外协产品的加工质量,统一各加工协作单位的加工标准、要求,规范加工工艺,特制订本“外协机械加工通用技术要求”,以下简称为“要求”。
2、适用范围本“要求”适用于公司各外协单位的产品加工,并作为公司检验员的检验验收标准之一。
3、规范性引用文件下列文件对于本要求是必不可少的,凡是注日期的引用文件仅注日期的版本适用本要求。
凡是不注日期的引用文件其最新版本(包括所有修改单)适用于本文件。
GB/T3-1997普通螺纹收尾、肩距、退刀槽和倒角GB/T145-2001中心孔GB/T179-2003普通螺纹、公差GB/T1031-2009产品几何技术规范(GPS)表面结构轮廓法表面粗糙度参数及其数值。
GB/T1182-2008产品几何技术规范(GPS)几何公差形状方向位置和跳动公差标注GB/1184-1996开关和位置公差未注公差值ZD/XY-002不合格品控制程序4、术语和定义GB/1182-2008给出的术语和定义适用于本要求5、技术要求5.1加工原则5.1.1“基准先行”原则基准表面先加工,为后续工序作可靠的定位。
如轴类零件第一道工序一般为铣端面钻中心孔。
然后以中心孔定位加工其它表面。
5.1.2“先面后孔”原则当零件上有较大的平面可以用来作为定位基准时,总是先加工平面再以平面定位加工孔,保证孔和平面之间的位置精度,这样定位比较稳定,夹也方便,并可避免粗糙面钻孔引起的偏斜。
5.1.3“先主后次”原则先加工主要表面(位置精度要求较高的基准面和工作表面)后加工次要表面(如键槽、螺孔、坚固小孔等)次要表面一般在主要表面达到一定精度后最终精加工之前。
5.1.4“先粗后精”原则对于精度要求较高的零件,按由粗到精的顺序依次进行,逐步提高加工精度,这一点对于刚性较差的零件尤其不能忽视。
5.2一般要求5.2.1机械加工件的切削加工必须符合产品图样,工艺规程和本标准规定。
5.2.2机械加工件的已加工表面不得有锈蚀及影响性能寿命和外观的磕碰划伤等缺陷。
机械加工通用公差要求
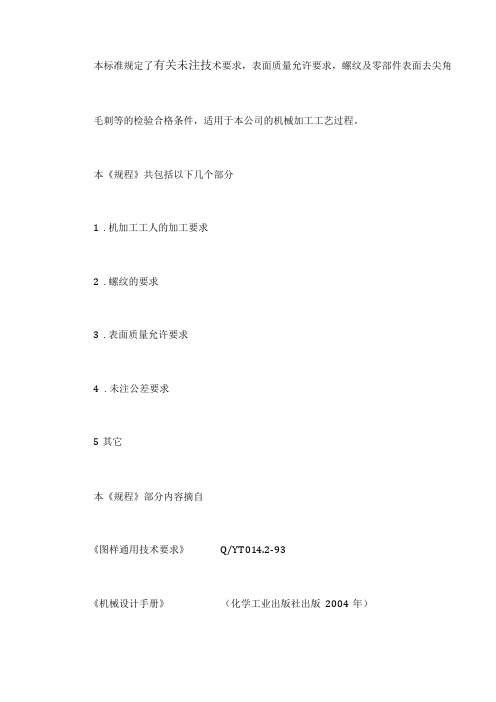
本标准规定了有关未注技术要求,表面质量允许要求,螺纹及零部件表面去尖角毛刺等的检验合格条件,适用于本公司的机械加工工艺过程。
本《规程》共包括以下几个部分1.机加工工人的加工要求2.螺纹的要求3.表面质量允许要求4.未注公差要求5其它本《规程》部分内容摘自《图样通用技术要求》Q/YT014.2-93《机械设计手册》(化学工业出版社出版2004年)《形状和位置公差未注公差值》GB/T1184-1996《国家标准普通螺纹》(中国标准出版社出版1986年)1.机械加工工人的加工要求1.1机加工人在加工前必须认真理解该零件的加工内容及有关技术要求,有疑问时必须向技术人员提出并解决后方可加工;1.2机加工人应对来料验收,确认合格后方可按图纸、工艺加工;1.3工艺文件要求使用工装时,必须按要求使用工装加工,必须明确工装的使用方法及注意事项;1.4开始工作前,须将所需的刀具、量具等必备工具准备好,并且要明确自己所需刀具、量具等工具的使用方法,以确保加工过程的顺利进行;1.5机加过程中的安全性应严格按《机械加工安全操作规程》执行;1.6零部件应按工序检查验收,即与前道工序检查合格后,方可转入下道工序加工;1.7凡采用工装与专用刀具加工零部件时,必须进行首件检查,合格后方可继续使用;1.8各种机床必须定时检查,定时润滑,确保机床正常运行。
1.9车间成品件与非成品件分开放置,做到分门别类,整齐、不混淆。
机床周围干净整齐,不乱摆放物品。
2.螺纹的要求2.1完整螺纹长度公差(极限)P:螺距(摘自Q/YT 022.1—1992)2.3攻螺纹前必须倒角,若无特别要求,倒角至螺纹大径;2.4螺纹侧面不得有妨碍螺纹综合量规自由旋入的碰伤,毛刺以及影响使用的凹痕,牙不完整等缺陷;3.表面质量允许要求3.1机械加工后的零部件,应符合产品图样,有关技术文件及本标准的规定;3.2零部件的已加工表面,不允许有磕、碰、伤及锈蚀现象;3.3除图样或技术要求外,加工的零部件必须去除毛刺、飞边,R不大于0.5 ;3.4钻孔后孔口必须去毛刺,倒角0.1〜0.3x45度;3.5精加工后的零件,不允许有因热处理后引起的退火、烧伤及裂纹等现象;3.6零部件精加工面,加工完成后应及时涂防锈油(脂),进行防锈处理,防止锈蚀;3.7零部件在工序转移与运输过程中,应备有工位器具,以防磕碰伤;3.10.1半精加工刀具切屑深度为0.5~2.5mm;3.10.2精加工刀具切屑深度为0.2~0.4mm;4.未注公差的要求为了便于查阅未注公差的公差要求,特将一些未注公差值列举如下:未注公差按照Q/YT 022.1—1992《机械加工零件未注公差尺寸的公差》执行,内容如下:注:若无特殊要求,优选K级注:若无特殊要求,优选K级注:若无特殊要求,优选K级4.7圆跳动未注公差值(摘自GB/T1184-1996)(mm)注:若无特殊要求,优选K级5.其他5.1本规程属于通用操作规程,如与工艺有异,按工艺执行。
机械加工通用技术要求规范
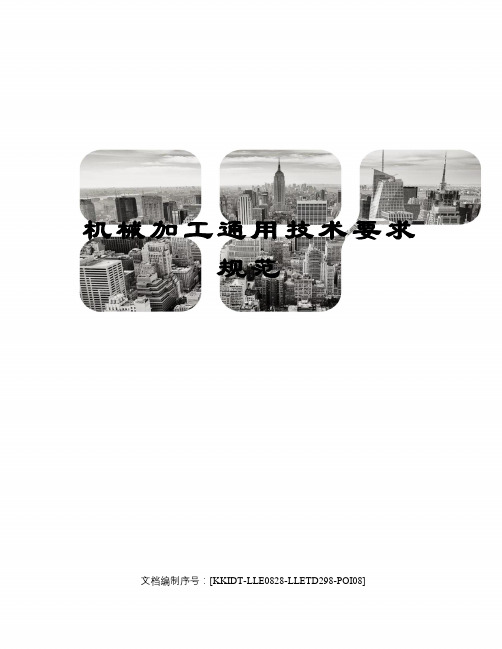
机械加工通用技术要求规范文档编制序号:[KKIDT-LLE0828-LLETD298-POI08]机械加工通用技术规范1.目的对机加工产品质量控制,以确保满足公司的标准和客户的要求。
本标准规定了各种机械加工应共同遵守的基本规则。
2.范围适用所有机加工产品,和对供应商机加工产品的要求及产品的检验。
3.定义A级表面:产品非常重要的装饰表面,即产品使用时始终可以看到的表面。
B级表面:产品的内表面或产品不翻动时客户偶尔能看到的表面。
C级表面:仅在产品翻动时才可见的表面,或产品的内部零件。
4.规范性引用文件下列文件对于本文件的应用是必不可少的。
凡是注日期的引用文件,仅注日期的版本适用于本文件。
凡是不注日期的引用文件,其最新版本(包括所有的修改单)适用于本文件。
GB/T 3-1997 普通螺纹收尾、肩距、退刀槽和倒角GB/T 145-2001 中心孔GB/T 197-2003 普通螺纹公差GB/T 1031-2009 产品几何技术规范(GPS) 表面结构轮廓法表面粗糙度参数及其数值GB/T 1182-2008 产品几何技术规范(GPS) 几何公差形状、方向、位置和跳动公差标注GB/T 1184-1996 形状和位置公差未注公差值GB/T 1568-2008 键技术条件GB/T 1804-2000 一般公差未注公差的线性和角度尺寸的公差GB/T 计数抽样检验程序第1部分:按接收质量限(AQL)检索的逐批检验抽样计划GB/T 4249-2009 产品几何技术规范(GPS) 公差原则GB/T 梯形螺纹第4部分:公差Q/JS 不合格品控制程序Q/JS 机柜半成品钣金件下料技术要求5.术语和定义GB/T 1182-2008给出的术语和定义及下列术语和定义适用于本文件。
切削加工用切削工具(包括刀具、磨具和磨料)把坯料或上多余的材料层切去成为切屑,使工件获得规定的几何形状、尺寸和表面质量的加工方法。
包括车削、铣削、刨削、磨削、拉削、钻孔、扩孔、铰孔、研磨、珩磨、抛光、超精加工及由它们组成的自动技术、数控技术、成组技术、组合机床、流水线、自动线。
机械加工通用技术规范

机械加工通用技术规范机械加工是指利用机床等设备对物体进行加工加工工艺,是工业生产中不可缺少的重要环节。
机械加工的质量和效率直接关系到产品的质量和生产效益,因此,机械加工通用技术规范的制定对提高产品加工精度和质量,提高生产效率具有极其重要的意义。
机械加工的通用技术规范1.机床的使用(1)机床必须符合国家标准,没有过期或者超期使用的机床不得用于生产。
(2)机床必须进行定期的维护与保养,并严格按照安全操作规程进行操作。
(3)机床的使用环境应保持整洁干燥,以保证机床的安全、稳定和精度,不得将机床放置在高温、高湿、有腐蚀性气体和震动的场所。
2.材料的选择(1)机械加工材料必须符合国家相关标准或行业标准,并有相应的证明文件。
(2)材料应查验尺寸精度、材料力学性能和化学成分等,以确保材料质量符合要求。
3.图纸和工艺文件(1)机械加工所需图纸必须符合国家标准或行业标准,并有相应的证明文件。
(2)工艺文件必须准确、清晰、明确,有必要的技术要求和规定。
(3)工艺文件中的加工工艺、尺寸、表面要求等项目必须符合图纸和设计要求,并做到与实际加工相一致。
4.加工精度的控制(1)在机械加工过程中,必须采取精度控制措施,控制误差范围在允许的范围内。
(2)在加工过程中,必须对机床进行定期检查与维修,保证机床的工作精度。
(3)在加工过程中,必须随时监测加工质量,及时检查和纠正加工过程中出现的问题。
5.安全生产措施(1)机械加工必须严格遵守安全操作规程,做好现场安全防范措施,控制生产事故。
(2)进行机械加工的人员必须经过相关机械加工培训和考核合格后才能上岗。
(3)进行机械加工时必须穿戴规范的劳动防护用品,如头盔、口罩、手套、护目镜等。
6.加工后的质量检测(1)在机械加工完成后,必须对加工零件进行严格的检验,以确保加工质量和精度符合图纸和技术要求。
(2)检测结果必须记录在相应的检测文件中。
通过以上机械加工通用技术规范,可以明确机械加工过程中的各项规范措施,有效保障产品加工质量和生产效率。
新版机械加工通用技术要求规范.pdf
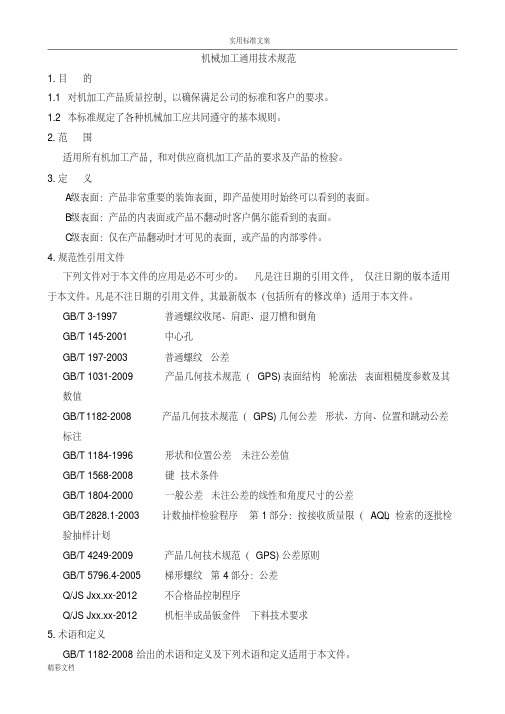
2)“先面后孔”原则 当零件上有较大的平面可以用来作为定位基准时,总是先加工平面,再以平面定位加 工孔,保证孔和平面之间的位置精度,这样定位比较稳定,装夹也方便,并可避免粗 糙面钻孔引起的偏斜。
2
>12~ >80~
80
140
>80~ >260~
260
630
4
8
>140~ 200
>200
>630~ >1000
1000
12
20
注 1: D 值用于盲孔和外端面倒圆。
注 2: 非圆柱面倒圆参照选用,其中 L 为与倒圆处有关的尺寸中最小的一个尺寸。
6.2.9 图样上未注明倒角,过度圆角的表面粗糙度,应以相连两表中 一面不进行加工时,则应取加工面的 Rd 值。
GB/T 1184-1996
形状和位置公差 未注公差值
GB/T 1568-2008
键 技术条件
GB/T 1804-2000
一般公差 未注公差的线性和角度尺寸的公差
GB/T 2828.1-2003 计数抽样检验程序 第 1 部分:按接收质量限( AQL)检49-2009
产品几何技术规范( GPS) 公差原则
GB/T 5796.4-2005 梯形螺纹 第 4 部分:公差
Q/JS Jxx.xx-2012
不合格品控制程序
Q/JS Jxx.xx-2012
机柜半成品钣金件 下料技术要求
5. 术语和定义
GB/T 1182-2008 给出的术语和定义及下列术语和定义适用于本文件。
机械加工通用技术规范
机械加工规范书1.目的1.1 对机加工产品质量控制,以确保满足公司的标准和客户的要求。
1.2 本标准规定了各种机械加工应共同遵守的基本规则。
2.范围适用所有机加工产品,和对供应商机加工产品的要求及产品的检验。
3.定义3.1 A级表面:产品非常重要的装饰表面,即产品使用时始终可以看到的表面。
3.2 B级表面:产品的内表面或产品不翻动时客户偶尔能看到的表面。
3.3 C级表面:仅在产品翻动时才可见的表面,或产品的内部零件。
4.机加工的要求4.1机加工件材料要符合图纸,选用的材料符合国家标准。
4.2机加工件图纸未注尺寸公差参考国家标准线性尺寸的未注公差GB/T1804-f要求进行检验。
4.3机加工件图纸未注角度公差参考国家标准角度的未注公差GB/T11335-m要求进行检。
4.4机加工件图纸未注形位公差参考国家标准形位的未注公差GB/T1184-H要求进行检验。
4.5图纸中尺寸标注为配合形式加工的,采用间隙配合,具体要求为:外配合为配合为配作对象最大尺寸+0.01~+0.10mm:内配合为配作对象最小尺寸-0.10~-0.01。
5.机加工质量的控制5.1 零件加工按照图纸加工,对图纸有标示不清、模糊、错误和对图纸产生疑问的与公司工艺人员联系。
5.2 零件加工按照工艺流程去做。
5.3零件加工过程中遇到加工错误或尺寸超出公差范围要与公司工艺人员联系,公司工艺人员将会确认零件可以采用或不可采用。
5.4 需要划线加工的零件,加工后不允许有划线的痕迹。
5.5 所有机加工的零件要去毛刺、钻孔后要倒角、棱角要倒钝(特殊要求除外)。
5.6两加工面间过度圆角或倒角的粗糙度,按其中较低的执行。
5.7两加工面间的根部,未要求清根的,其圆角半径均不大于0.5。
5.8零件的配合表面上,除图样及技术文件有规定外,不得刻打印记或作其它不易清除的标记。
5.9图样上未注明锪平深度的,其深度尺寸不作检查,以锪平为限。
5.10碰到零件加工错误不应该擅做主张对零件进行修改,应与公司工艺人员联系获得技术支持。
机械加工技术要求标准是什么?
机械加工技术要求标准是什么一般机械加工技术要求是按照图纸或者样品的要求,如果没有特殊说明的,通用机械加工技术要求是怎样的呢?一般机械加工技术要求1.零件去除氧化皮。
2.零件加工表面上,不应有划痕、擦伤等损伤零件表面的缺陷。
3.去除毛刺飞边。
机械加工热处理要求1.经调质处理,HRC50〜55。
2.零件进行高频淬火,350〜370℃回火,HRC40〜45。
3.渗碳深度0.3mm。
4. 进行高温时效处理。
机械加工公差要求1.未注形状公差应符合GB1184-80的要求。
2.未注长度尺寸允许偏差±0.5mm。
3. 铸件公差带对称于毛坯铸件基本尺寸配置。
机械加工零件棱角1.未注圆角半径R5。
2.未注倒角均为2X453. 锐角/尖角/锐边倒钝。
机械加工装配要求1.各密封件装配前必须浸透油。
2.装配滚动轴承允许采用机油加热进行热装,油的温度不得超过100℃。
3.齿轮装配后,齿面的接触斑点和侧隙应符合GB10095和GB11365的规定。
4.装配液压系统时允许使用密封填料或密封胶,但应防止进入系统中。
5.进入装配的零件及部件(包括外购件、外协件),均必须具有检验部门的合格证方能进行装配。
6.零件在装配前必须清理和清洗干净,不得有毛刺、飞边、氧化皮、锈蚀、切屑、油污、着色剂和灰尘等。
7.装配前应对零、部件的主要配合尺寸,特别是过盈配合尺寸及相关精度进行复查。
8.装配过程中零件不允许磕、碰、划伤和锈蚀。
9.螺钉、螺栓和螺母紧固时,严禁打击或使用不合适的旋具和扳手。
紧固后螺钉槽、螺母和螺钉、螺栓头部不得损坏。
10.规定拧紧力矩要求的紧固件,必须采用力矩扳手,并按规定的拧紧力矩紧固。
11.同一零件用多件螺钉(螺栓)紧固时,各螺钉(螺栓)需交叉、对称、逐步、均匀拧紧。
12.圆锥销装配时应与孔应进行涂色检查,其接触率不应小于配合长度的60%,并应均匀分布。
13.平键与轴上键槽两侧面应均匀接触,其配合面不得有间隙。
14.花键装配同时接触的齿面数不少于2/3,接触率在键齿的长度和高度方向不得低于50%。
机械加工标准
机加工通用技术要求1范围本标准规定了切削加工的术语和定义、技术要求、检验规则和搬运、贮存。
本标准适用于公司机加工车间的切削加工和特殊加工。
本标准不适用于钣金加工。
2规范性引用文件下列文件对于本文件的应用是必不可少的。
凡是注日期的引用文件,仅注日期的版本适用于本文件。
凡是不注日期的引用文件,其最新版本(包括所有的修改单)适用于本文件。
GB/T 3-1997 普通螺纹收尾、肩距、退刀槽和倒角GB/T 145-2001 中心孔GB/T 197-2003 普通螺纹公差GB/T 1031-2009 产品几何技术规范(GPS) 表面结构轮廓法表面粗糙度参数及其数值GB/T 1182-2008 产品几何技术规范(GPS) 几何公差形状、方向、位置和跳动公差标注GB/T 1184-1996 形状和位置公差未注公差值GB/T 1568-2008 键技术条件GB/T 1804-2000 一般公差未注公差的线性和角度尺寸的公差GB/T 2828.1-2003 计数抽样检验程序第1部分:按接收质量限(AQL)检索的逐批检验抽样计划GB/T 4249-2009 产品几何技术规范(GPS) 公差原则GB/T 5796.4-2005 梯形螺纹第4部分:公差Q/JS Jxx.xx-2012 不合格品控制程序Q/JS Jxx.xx-2012 机柜半成品钣金件下料技术要求3术语和定义GB/T 1182-2008给出的术语和定义及下列术语和定义适用于本文件。
3.1切削加工用切削工具(包括刀具、磨具和磨料)把坯料或工件上多余的材料层切去成为切屑,使工件获得规定的几何形状、尺寸和表面质量的加工方法。
包括车削、铣削、刨削、磨削、拉削、钻孔、扩孔、铰孔、研磨、珩磨、抛光、超精加工及由它们组成的自动技术、数控技术、成组技术、组合机床、流水线、自动线。
3.2特种加工特种加工亦称“非传统加工”或“现代加工方法”,泛指用电能、热能、光能、电化学能、化学能、声能及特殊机械能等能量达到去除或增加材料的加工方法,从而实现材料被去除、变形、改变性能或被镀覆等。
机械加工通用技术规范
机械加工规范书1.目的1.1 对机加工产品质量控制,以确保满足公司的标准和客户的要求。
1.2 本标准规定了各种机械加工应共同遵守的基本规则。
2.范围适用精工车间机加工产品,和对供应商机加工产品的要求及产品的检验。
3.定义3.1 A级表面:产品非常重要的装饰表面,即产品使用时始终可以看到的表面。
3.2 B级表面:产品的内表面或产品不翻动时客户偶尔能看到的表面。
3.3 C级表面:仅在产品翻动时才可见的表面,或产品的内部零件。
4.机加工的要求4.1机加工件材料要符合图纸,选用的材料符合国家标准。
4.2机加工件图纸未注尺寸公差参考国家标准线性尺寸的未注公差GB/T1804-f要求进行检验。
4.3机加工件图纸未注角度公差参考国家标准角度的未注公差GB/T11335-m要求进行检。
4.4机加工件图纸未注形位公差参考国家标准形位的未注公差GB/T1184-H要求进行检验。
4.5图纸中尺寸标注为配合形式加工的,采用间隙配合,具体要求为:外配合为配合为配作对象最大尺寸+0.01~+0.10mm:内配合为配作对象最小尺寸-0.10~-0.01。
5.机加工质量的控制5.1 零件加工按照图纸加工,对图纸有标示不清、模糊、错误和对图纸产生疑问的与公司工艺人员联系。
5.2 零件加工按照工艺流程去做。
5.3零件加工过程中遇到加工错误或尺寸超出公差范围要与公司工艺人员联系,公司工艺人员将会确认零件可以采用或不可采用。
5.4 需要划线加工的零件,加工后不允许有划线的痕迹。
5.5 所有机加工的零件要去毛刺、钻孔后要倒角、棱角要倒钝(特殊要求除外)。
5.6两加工面间过度圆角或倒角的粗糙度,按其中较低的执行。
5.7两加工面间的根部,未要求清根的,其圆角半径均不大于0.5。
5.8零件的配合表面上,除图样及技术文件有规定外,不得刻打印记或作其它不易清除的标记。
5.9图样上未注明锪平深度的,其深度尺寸不作检查,以锪平为限。
5.10碰到零件加工错误不应该擅做主张对零件进行修改,应与公司工艺人员联系获得技术支持。
- 1、下载文档前请自行甄别文档内容的完整性,平台不提供额外的编辑、内容补充、找答案等附加服务。
- 2、"仅部分预览"的文档,不可在线预览部分如存在完整性等问题,可反馈申请退款(可完整预览的文档不适用该条件!)。
- 3、如文档侵犯您的权益,请联系客服反馈,我们会尽快为您处理(人工客服工作时间:9:00-18:30)。
机械加工通用技术要求规范IMB standardization office【IMB 5AB- IMBK 08- IMB 2C】机械加工通用技术规范1.目的对机加工产品质量控制,以确保满足公司的标准和客户的要求。
本标准规定了各种机械加工应共同遵守的基本规则。
2.范围适用所有机加工产品,和对供应商机加工产品的要求及产品的检验。
3.定义A级表面:产品非常重要的装饰表面,即产品使用时始终可以看到的表面。
B级表面:产品的内表面或产品不翻动时客户偶尔能看到的表面。
C级表面:仅在产品翻动时才可见的表面,或产品的内部零件。
4.规范性引用文件下列文件对于本文件的应用是必不可少的。
凡是注日期的引用文件,仅注日期的版本适用于本文件。
凡是不注日期的引用文件,其最新版本(包括所有的修改单)适用于本文件。
GB/T3-1997普通螺纹收尾、肩距、退刀槽和倒角GB/T145-2001中心孔GB/T197-2003普通螺纹公差GB/T1031-2009产品几何技术规范(GPS)表面结构轮廓法表面粗糙度参数及其数值GB/T1182-2008产品几何技术规范(GPS)几何公差形状、方向、位置和跳动公差标注GB/T1184-1996形状和位置公差未注公差值GB/T1568-2008键技术条件GB/T1804-2000一般公差未注公差的线性和角度尺寸的公差GB/计数抽样检验程序第1部分:按接收质量限(AQL)检索的逐批检验抽样计划GB/T4249-2009产品几何技术规范(GPS)公差原则GB/梯形螺纹第4部分:公差Q/不合格品控制程序Q/机柜半成品钣金件下料技术要求5.术语和定义GB/T1182-2008给出的术语和定义及下列术语和定义适用于本文件。
切削加工用切削工具(包括刀具、磨具和磨料)把坯料或上多余的材料层切去成为切屑,使工件获得规定的几何形状、尺寸和表面质量的加工方法。
包括车削、铣削、刨削、磨削、拉削、钻孔、扩孔、铰孔、研磨、珩磨、抛光、超精加工及由它们组成的自动技术、数控技术、成组技术、组合机床、流水线、自动线。
特种加工特种加工亦称“非传统加工”或“现代加工方法”,泛指用电能、热能、光能、电化学能、化学能、声能及特殊机械能等能量达到去除或增加材料的加工方法,从而实现材料被去除、变形、改变性能或被镀覆等。
公司现有的特殊加工方法有线切割加工、激光加工、水切割加工。
公差带有一个或几个理想的几何线或面所限定的、由线性公差值表示其大小的区域。
6.技术要求加工原则1)“基准先行”原则基准表面先加工,为后续工序作可靠的定位。
如轴类零件第—道工序一般为铣端面钻中心孔,然后以中心孔定位加工其它表面。
2)“先面后孔”原则当零件上有较大的平面可以用来作为定位基准时,总是先加工平面,再以平面定位加工孔,保证孔和平面之间的位置精度,这样定位比较稳定,装夹也方便,并可避免粗糙面钻孔引起的偏斜。
3)“先主后次”原则先加工主要表面(位置精度要求较高的基准面和工作表面)后加工次要表面(如键槽、螺孔、紧固小孔等)。
次要表面一般在主要表面达到一定精度后,最终精加工之前。
4)“先粗后精”原则对于精度要求较高的零件,按由粗到精的顺序依次进行,逐步提高加工精度。
这一点对于刚性较差的零件,尤其不能忽视。
一般要求机械加工件的切削加工和必须符合产品图样,工艺规程和本标准规定。
机械加工件的已加工表面,不得有锈蚀及影响性能,寿命和外观的磕碰、划伤等缺陷。
除了特殊要求外,加工后的零部件不得有尖锐的棱角和毛刺。
精加工后的配合面,摩擦面和定位面等工作表面,不得打有损于表面质量的印记。
经热处理后的零件,精加工时不得产生退火、烧伤及裂纹等现象。
经加工后的零件在搬运、存放时,必须防止受到损伤、腐蚀及变形。
图样上未注明的倒角应符合表1的规定。
表1 mm注:非圆柱面倒角参照选用,其中l为与倒角处有关的尺寸中最小的一个尺寸。
图样上未注注明的倒圆尺寸,如无倾角要求时,应符合表2的规定。
表2 mm注1:D值用于盲孔和外端面倒圆。
注2:非圆柱面倒圆参照选用,其中L为与倒圆处有关的尺寸中最小的一个尺寸。
图样上未注明倒角,过度圆角的表面粗糙度,应以相连两表中Ra值较大的选取,如有一面不进行加工时,则应取加工面的Rd值。
在成对成组加工的零部件(如滑动轴承的上、下轴瓦,齿轮箱的上下盖等)上,应做出标记.未注尺寸公差未注公差尺寸(不包括倒角和倒圆半径)的极限偏差数值按GB/T1804-2000-m级取值。
数值见表3的规定。
表3未注公差尺寸的极限偏差数值mm倒角尺寸和倒圆半径的极限偏差数值按GB/T1804-2000-m级取值。
数值见表4的规定。
表4倒角尺寸和倒圆半径的极限偏差数值mm盲孔的钻孔深度,其允许偏差规定如下:1)孔深不大于50mm的为0~+3mm;2)孔深大于50mm的为0~+5mm。
凡锪平处以最低点测量,锪平深度的极限偏差为0~+5mm。
一面为加工面,一面为非加工面的未注尺寸公差的极限偏差应符合下列规定:1)铸件、锻件及焊接件按相应的非加工未注尺寸公差的极限偏差的70%取±值。
2)铸件、锻件的突缘或壁厚允许减薄,当壁厚≤10mm时,其减薄量不得大于壁厚的20%;当壁厚>10mm时,其减薄量不得大于壁厚的15%.未注形状公差直线度和平面度图样上未标注的直线度和平面度的公差值按GB/T1184-1996-H级取值,具体公差值见表5。
表5 mm圆度、圆柱度的未注公差值圆度、圆柱度的未注公差值要求见GB/T1184-1996中相关规定。
未注位置公差平行度平行度的未注公差值等于给出的尺寸公差值,或是直线度和平面度未注公差值中的相应公差值取较大者。
应取两要素中较长者作为基准,若两要素的长度相等则可选取一要素为基准。
垂直度取形成直角的两边中较长的一边作为基准,较短的一边作为被测要素,若两边的长度相等则可取其中任意一边作为基准,按GB/T1184-1996-H级取值,垂直度的未注公差值见表6.表6 mm对称度应取两要素中较长的一边作为基准,较短的一边作为被测要素,若两要素的长度相等则可取其中任意一要素作为基准,按GB/T1184-1996-H级取值,对称度的未注公差值见表7.注:对称度的未注公差值用于至少两个要素中的一个是中心平面,或两个要素的轴线相互垂直。
表7 mm同轴度同轴度的未注公差值未作规定。
在几极限情况下,同轴度的未注公差值可以和表8中规定的径向圆跳动的未注公差值相等,应取两要素中较长的一边作为基准,若两要素的长度相等则可取其中任意一要素作为基准。
圆跳动对于圆跳动的未注公差值,应以设计或工艺给出的支撑面作为基准,否则应取两要素中较长的一边作为基准,若两要素的长度相等则可取其中任意一要素作为基准。
按GB/T1184-1996-H级取值,圆跳动的未注公差值见表8.表8 mm垂直要素、倾斜要素由角度公差和直线度或平面度未注公差值分别控制。
圆跳动和全跳动的公差值不应大于该要素的形状和位置的未注公差的综合值。
任意两螺钉、螺栓孔中心距的极限偏差当图样上未注明时,按表9的规定。
表9 mm未注公差角度的极限偏差角度尺寸的极限偏差数值按角度短边长度确定,对圆锥角按圆锥素线长度确定。
角度尺寸的极限偏差数值按GB/T1804-2000-m级取值。
角度尺寸的极限偏差数值见表10.表10螺纹加工的螺纹表面不允许有黑皮、磕碰、乱扣和毛刺等缺陷。
螺纹的加工精度和表面粗糙度,当图样上未注明时应按下列规定:1)普通螺纹精度应按GB/T197-2003规定的6H、6g级。
内螺纹表面粗糙度值为μm;外螺纹表面粗糙度值为μm。
2)梯形螺纹精度应按GB/的规定。
内螺纹表面粗糙度值为μm;外螺纹表面粗糙度值为μm。
外螺纹轴线对杆部轴线及内螺纹轴线对孔部轴线的同轴度,分别不大于外螺纹大径及内螺纹大径的尺寸公差1/2.螺纹收尾、肩距、退刀槽和倒角应符合GB/T3-1997的规定。
攻制螺孔的轴线对端面的垂直度应按表11的规定。
表11 mm6.8螺纹、孔的检验:6.采用牙规、塞规检验或用螺钉检验,螺纹的底孔不大于标准底孔的。
6.图样上未注精度等级的普通螺均按GB197规定:内螺纹按7H;外螺纹7g加工和检验;未注明粗糙度的螺纹的粗糙度均为6.螺纹部分的长度公差按+倍螺距执行6.螺孔对端平面、螺栓外螺纹对支承平面垂直度匀差按100加工和检验6.内螺纹孔口按90°~120°倒角,倒角外圆应大于螺纹直径;外螺纹端部按45°倒角,倒角后小径应小于螺纹小径。
6.中心孔1.中心孔是否保留应在图样上注明,若未注明则认为有无均可,或按工艺规定。
2.中心孔的规格图样上如未注明时按A型(不带护锥)加工和检验。
尺寸见表七。
6.9零件的检验要全面到位防止不良的产品流入公司造成不必要的损失。
键和键槽键必须符合GB/T1568-2008的规定。
当键长与键宽之比≥8时,键工作面在长度方向的平面度应符合下列规定:1)当键宽≤6mm时,公差等级按7级;2)当键宽≥8~36mm时,公差等级按6级;3)当键宽≥40mm时,公差等级按5级;4)具体公差数值见表12。
表12 mm未注键槽两工作面平行度的公差应按表12中公差等级7级取值。
未注键槽的对称度按GB/T1184-1996附录B中表B4中9级取值。
中心孔图样中未注明、加工中又需要中心孔的零件,在不影响使用和外观的情况下,加工后中心孔可以保留。
中心孔应符合GB/T145-2001的规定。
表面粗糙度图样中未注明表面粗糙度应符合GB/T1031-2009的规定。
4.机加工的要求4.1机加工件材料要符合图纸,选用的材料符合国家标准。
4.2机加工件图纸未注尺寸公差参考国家标准线性尺寸的未注公差GB/T1804-f要求进行检验。
4.3机加工件图纸未注角度公差参考国家标准角度的未注公差GB/T11335-m要求进行检。
4.4机加工件图纸未注形位公差参考国家标准形位的未注公差GB/T1184-H要求进行检验。
图纸中尺寸标注为配合形式加工的,采用间隙配合,具体要求为:外配合为配合为配作对象最大尺寸+~+:内配合为配作对象最小尺寸~。
5.机加工质量的控制5.1零件加工按照图纸加工,对图纸有标示不清、模糊、错误和对图纸产生疑问的与公司工艺人员联系。
5.2零件加工按照工艺流程去做。
5.3零件加工过程中遇到加工错误或尺寸超出公差范围要与公司工艺人员联系,公司工艺人员将会确认零件可以采用或不可采用。
5.4需要划线加工的零件,加工后不允许有划线的痕迹。
5.5所有机加工的零件要去毛刺、钻孔后要倒角、棱角要倒钝(特殊要求除外)。
5.6两加工面间过度圆角或倒角的粗糙度,按其中较低的执行。
5.7两加工面间的根部,未要求清根的,其圆角半径均不大于。
5.8零件的配合表面上,除图样及技术文件有规定外,不得刻打印记或作其它不易清除的标记。