格特拉克公司离合器分泵零件设计资料表
离合器总泵及助力缸的结构说明及常
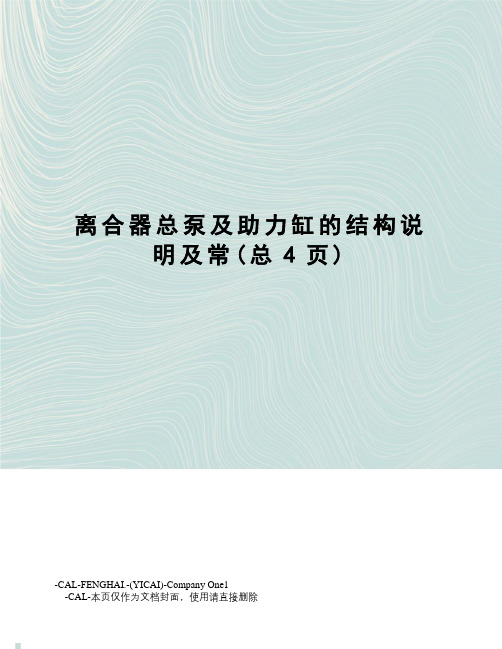
离合器总泵及助力缸的结构说明及常(总4页)-CAL-FENGHAI.-(YICAI)-Company One1-CAL-本页仅作为文档封面,使用请直接删除离合器总泵及助力缸的结构说明及常见故障判断离合器总泵及助力缸是一种比较容易出现故障的部件。
引起故障的原因有多种,有些是因为产品本身的问题,有些是由于使用维护不当。
为降低离合器总泵及助力缸的故障出现频率,提高车辆的运营效率,现将离合器总泵及助力缸的结构、工作原理说明一下,同时对一些常见的故障原因进行讨论分析。
一.产品结构示意图及工作原理结构示意图见下图1。
a. 活塞杆b.推杆c.控制阀杆d.大回位弹簧e.小回位弹簧f.气门g. 压缩空气通道 h. 排气通道 j. 制动液通道A:液压腔 B:气压腔 C.液压控制阀1#:进气口 4#:进液口 31#:排气口 32#:液压排气口(放气螺钉)1#为压缩空气输入口,4#为与离合器总泵连接的进液口,31#为排气口,32#为液压腔放气口。
离合器分离:踩下踏板,总泵制动液从4#口输入A腔,作用在活塞杆a 上,使推杆b产生向左的推力。
同时,制动液经j道进入C腔,推动控制阀杆c向左移动,打开气门f,压缩空气经g道流入B腔。
在气压力和液压力同时作用下,使推杆b继续向左移动,从而使离合器分离。
离合器接合:松开踏板,4#口液压降为零。
在离合器压盘的作用下,推杆b向右移动,同时控制阀杆c在回位弹簧e和气压的作用下向右移动,关闭气门f,空气经控制阀杆的通道h由31#口排向大气,推杆b回到起始位置。
二.安装方法1.助力器按前盖板上箭头指示方向,向上安装到车上,以利于液压腔内的空气顺利排出。
2.装上推杆,将推杆和分离机构连接。
3.按图示在1#口接上气接头,在4#口接上油管接头。
4.安装并调整限位螺栓长度,保证在分离轴承接触到离合器时,限位螺栓头部有8mm间隙。
三.对总泵、助力器注油、排气方法如下:参看图2。
A电动(手动)泵 B橡胶管 C开关 D放气螺钉 E踏板F油杯 G总泵出油接头 H总泵 J助力缸 K高压管方法1:踏板E处于自由状态。
汽车产品零部件性能描述书-离合总泵总成

文件更改状态记录前言本性能描述书是基于手动标杆车的性能要求而制定的,由于目前发动机未确定,故不能提供概念数模及相关数据;待发动机确定及手动标杆车离合总泵总成相关工作完成后方可进行下一步工作。
此版性能描述书主要用于主机厂招商工作,其中描述的各项性能指标,可能不完善,将在与供应商交流过程中更新完善,形成最终版,且各项性能要求将落实到二次开发件图纸中。
目录1.零部件简图及明细 (1)2.性能要求 (2)3.执行法规或标准 (2)4.试验方法 (2)5.检验规则 (3)6.提供资料平台 (3)6.1提供资料文件格式 (3)6.2设计公司提供资料内容 (3)6.3零部件供应商提供资料内容 (3)6.4确认程序 (3)7.成套性 (4)1.零部件简图及明细2.性能要求2.1离合总泵总成执行 Q/CC JT097-2008《汽车塑料件、橡胶件和热塑性弹性体件的材料标识和标记》标准;离合总泵总成符合Q/CC JT098-2008《汽车产品中有毒有害物质的限量要求》标准。
2.2离合总泵总成能在-45~120℃的工作环境下工作;2.3离合总泵总成在工作介质制动液DOT4内工作。
2.4运动阻力:活塞滑动时的运动阻力在25N以下;2.5离合总泵总成的工作液压为500 Pa ~10MPa;2.6离合总泵总成所有零件,包括橡胶件应对工作介质耐腐蚀;2.7密封性要求:a.气密性:压力0.2MPa±0.01 MPa;30S内压力降不大于100 Pa。
b.真空密封性:绝对压力250 Pa±50Pa;120S内压力升不大于200 Pa。
c.高压密封性:液压5MPa±0.1 MPa;120S内压力降不大于0.35M Pa。
2.8离合总泵缸径 mm,工作行程 mm;3.执行法规或标准Q/CC JT097-2008 汽车塑料件、橡胶件和热塑性弹性体件的材料标识和标记Q/CC JT098-2008 汽车产品中有毒有害物质的限量要求QC/T 17-92 汽车零部件耐候性试验一般规则4.试验方法4.1最小耐压试验(配套厂家提供标准,共同确认)4.2橡胶件的耐腐蚀试验(配套厂家提供标准,共同确认)4.3耐高低温试验(配套厂家提供标准,共同确认)4.4密封性试验:按2.74.5型式试验:按如下规定的要求进行,不允许出现功能故障或泄露;试验过程中工作介质损耗不大于5ml/100000次;试验结束后满足高压密封性要求。
离合器及操纵机构说明书
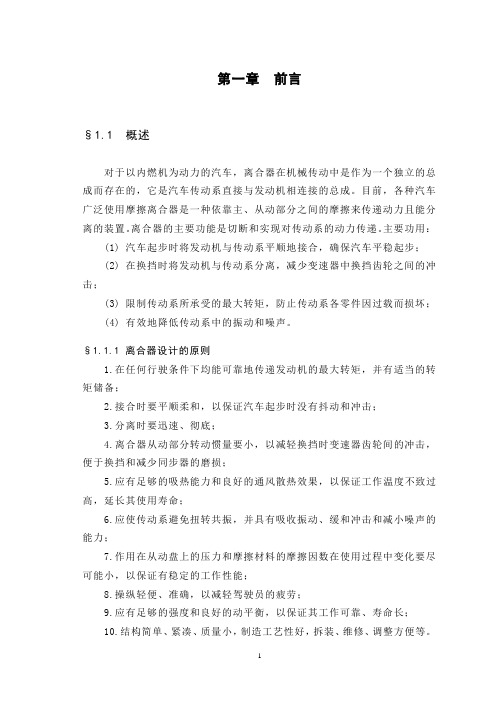
第一章前言§1.1 概述对于以内燃机为动力的汽车,离合器在机械传动中是作为一个独立的总成而存在的,它是汽车传动系直接与发动机相连接的总成。
目前,各种汽车广泛使用摩擦离合器是一种依靠主、从动部分之间的摩擦来传递动力且能分离的装置。
离合器的主要功能是切断和实现对传动系的动力传递。
主要功用:(1) 汽车起步时将发动机与传动系平顺地接合,确保汽车平稳起步;(2) 在换挡时将发动机与传动系分离,减少变速器中换挡齿轮之间的冲击;(3) 限制传动系所承受的最大转矩,防止传动系各零件因过载而损坏;(4) 有效地降低传动系中的振动和噪声。
§1.1.1 离合器设计的原则1.在任何行驶条件下均能可靠地传递发动机的最大转矩,并有适当的转矩储备;2.接合时要平顺柔和,以保证汽车起步时没有抖动和冲击;3.分离时要迅速、彻底;4.离合器从动部分转动惯量要小,以减轻换挡时变速器齿轮间的冲击,便于换挡和减少同步器的磨损;5.应有足够的吸热能力和良好的通风散热效果,以保证工作温度不致过高,延长其使用寿命;6.应使传动系避免扭转共振,并具有吸收振动、缓和冲击和减小噪声的能力;7.作用在从动盘上的压力和摩擦材料的摩擦因数在使用过程中变化要尽可能小,以保证有稳定的工作性能;8.操纵轻便、准确,以减轻驾驶员的疲劳;9.应有足够的强度和良好的动平衡,以保证其工作可靠、寿命长;10.结构简单、紧凑、质量小,制造工艺性好,拆装、维修、调整方便等。
§1.1.2 离合器的组成1. 主动部分主动部分包括飞轮、离合器盖、压盘等机件组成。
这部分与发动机曲轴连在一起。
离合器盖与飞轮靠螺栓连接,压盘与离合器盖之间是靠3-4个传动片传递转矩的2. 从动部分从动部分是由单片、双片或多片从动盘所组成,它将主动部分通过摩擦传来的动力传给变速器的输入轴。
从动盘由从动盘本体,摩擦片和从动盘毂三个基本部分组成。
为了避免转动方向的共振,缓和传动系受到的冲击载荷,大多数汽车都在离合器的从动盘上附装有扭转减震器。
(26)2.7离合器主要零部件结构设计

2.7离合器主要零部件结构设计[P2]l.从动盘总成从动盘总成主要由摩擦片、从动片、减振器和花键毂等组成。
从动盘对离合器工作性能影响很大,应满足如下设计要求:1)转动惯量应尽量小,以减小变速器换挡时轮齿间的冲击。
2)应具有轴向弹性,使离合器接合平顺,便于起步,而且使摩擦面压力均匀,减小磨损。
3)应装扭转减振器,以避免传动系共振,并缓和冲击。
[P3]为了使从动盘具有轴向弹性,常用的方法有:在从动盘上开"T"形槽,外缘形成许多扇形,并将扇形部分冲压成依次向不同方向弯曲的波浪形。
这种结构主要应用于货车。
将扇形波形片的左、右凸起段分别与左、右侧摩擦片聊接。
由于波形片比从动片薄,故这种结构轴向弹性较好,转动惯量较小,适宜于高速旋转,主要应用于乘用车和轻型商用车。
[P4]利用阶梯形例钉杆的细段将成对波形片的左片聊在左侧摩擦片上,并交替地把右片聊在右侧摩擦片上。
这种结构弹性行程大,弹性特性较理想,可使汽车起步极为平顺。
主要应用于中、高级乘用车。
[P5]将靠近飞轮的左侧摩擦片直接都合在从动片上,只在靠近压盘侧的从动片钟有波形片,右侧摩擦片用钾钉与波形片钾合。
这种结构转动惯量大,但强度高,传递转矩能力大,主要应用于商用车。
[P6]从动盘毂在离合器中承受载荷最大它一般采用齿侧对中的矩形花键安装在变速器的第一轴上,花键的尺寸可根据摩擦片的外径D与发动机的最大转矩选取。
离合器摩擦片在性能上应满足如下要求:1)摩擦因数较高且较稳定,工作温度、单位压力、滑磨速度的变化对其影响要小。
2)有足够的机械强度与耐磨性。
3)密度要小,以减小从动盘转动惯量。
[P7]4)热稳定性好,在高温下分离出的粘合剂少,无味,不易烧焦。
5)磨合性能好,不致刮伤飞轮和压盘表面。
6)接合时应平顺而不产生"咬合"或"抖动.现象。
7)长期停放后,摩擦面间不发生"粘着"现象。
[P8]离合器摩擦片所用的材料有石棉基摩擦材料、粉末冶金摩擦材料和金属陶瓷摩擦材料。
离合器设计说明书资料(00001).doc

第一章绪论现代汽车工业具有世界性,是开发型的综合工业,竞争也越来越激烈。我国自1953年创建第一汽车制造厂至今,已有130多家汽车制造厂,700多家汽车改装厂。随着我国国民经济的快速发展和人们生活水平的不断提高,对汽车的使用功能不断提出新的要求。目前大部分汽车采用离合器作为汽车的动力传递机构。离合器的发展概况在采用离合器的传动系统中,早期离合器的结果形式是锥形摩擦离合器。锥形摩擦离合器传递扭矩的能力,比相同直径的其他结构形式的摩擦离合器要大。但是,其最大的缺点是从动部分的转动惯量太大,引起变速器换挡困难。而且这种离合器在接合时也不够柔和,容易卡住。次后,在油中工作的所谓湿式的多片离合器逐渐取代了锥形摩擦离合器。但是多片湿式摩擦离合器的片与片之间容易被油粘住(尤其是在冷天油液变浓时更容易发生),导致分离不彻底,造成换挡困难。所以它又被干式所取代。多片干式摩擦离合器的主要优点是由于接触面数多,故接合平顺柔和,保证了汽车的平稳起步。但因片数较多,从动部分的转动惯量较大,还是感到换挡不够容易。另外,中间压盘的通风散热不良,易引起过热,加快了摩擦片的磨损甚至烧伤和破裂。如果调整不当还可能引起离合器分离不彻底。多年的实践经验使人们逐渐趋向于采用单片干式摩擦离合器。它具有从动部分转动惯量小,散热性好,结构简单,调整方便,尺寸紧凑,分离彻底等优点。而且只要在结构上采取一定措施,也能使其接合平顺。因此,它得到了极为广泛的应用。为了实现离合器的自动操纵,有自动离合器。采用自动离合器时可以省去离合器踏板,实现汽车的“双踏板”操纵。与其他自动传动系统(如液力传动)相比,它具有结构简单,成本低廉及传动效率高的优点。因此,在欧洲小排量汽车上曾得到广泛的应用。但是在现有自动离合器的各种结构中,离合器的摩擦力矩的力矩调节特性还不够理想,使用性能不尽完善。例如,汽车以高档低速上坡时,离合器往往容易打滑。因此必须提前换如低档以防止摩擦片的早期磨损以至烧坏。这些都需要进一步改善。随着汽车运输的发展,离合器还要在原有的基础上不断改进和提高,以适应新的使用条件。从国外的发展动向来看,近年来汽车的性能在向高速发展,发动机的功率和转速不断提高,载重汽车趋向大型化,国内也有类似的情况。此外,对离合器的使用要求也越来越高。所以,增加离合器的传扭能力,提高其使用寿命,简化操作,已经成为目前离合器的发展趋势。第二章方案论证第一节选定离合器的车型本次设计所选车型大众polo1.4mt该车主要参数如下表:表2-1大众polo1的主要性能参数第二节离合器设计基本要求为了保证离合器具有的工作性能,设计离合器应满足如下基本要求:(一)在任何行使条件下,既能可靠地传递发动机最大转矩,并有适当的转矩储备,又能防止传动系过载;(二)接合完全、平顺、柔和,使汽车起步时无抖动、无冲击,分离彻底、迅速;(三)工作性能(最大摩擦力矩或后备系数)稳定,即作用在摩擦片上的总压力不应因摩擦表面的磨损而有明显的变化,摩擦系数在离合器工作过程中应力求稳定;(四)从动部分的转动惯量要小,以减小挂档时的齿轮冲击,便于换档和减小同步器的磨损;(五)应能避免和衰减传动系的扭振,并具有吸收振动、缓和冲击和降低噪声的能力;(六)应有足够的吸热能力和良好的通风散热效果,以保证工作温度不致过高,延长其使用寿命通风;(七)操纵轻便、准确,以减轻驾驶员的疲劳;(八)具有足够的强度,工作可靠、使用寿命长;(九)力求结构简单、紧凑,质量小,制造工艺性好,拆装、维修、调整方便;(十)设计时要注意对旋转件的动平衡要求和离心力的影响。第三节确定离合器的结构型式一摩擦离合器机构型式的选择汽车离合器有摩擦式、电磁式和液力式三种类型。其中,摩擦式的应用最广泛。现代汽车摩擦离合器的典型结构型式是单片或双片干式,它由从动盘、压盘、压盘驱动装置、压紧弹簧(有沿圆周均布的圆柱螺旋弹簧、中央布置的锥形或圆柱螺旋弹簧和膜片弹簧等)、离合器盖、分离杠杆、分离轴承等构成。本次设计选定的机构型式为单片摩擦式。二从动盘数及干、湿式的选择(一) 单片干式摩擦离合器如图2-2,2-3,2-4所示,其结果简单,调整方便,轴向尺寸紧凑,分离彻底,从动件转动惯量小,散热性好,采用轴向有弹性的从动盘时也能接合柔顺。因此,广泛用于各级轿车及微、轻、中型客车与货车上,在发动机转矩不大于1000N·m的大型客车和重型货车上也有所推广。当转矩更大时可以采用双片离合器。(二) 双片干式摩擦离合器如图2-4所示。与单片离合器相比,由于摩擦面增多使传递转矩的能力增大,接合也更平顺、柔和;在传递相同转矩的情况下,其径向尺寸较小,踏板力较小。但轴向尺寸加大且结构复杂;中间压盘的通风散热性差易引起过热而加快摩擦片的磨损甚至烧伤碎裂;分离行程大,调整不当分离也不易彻底;从动件转动惯量大易使换档困难等。仅用于传递的转矩大且径向尺寸受到限制时。(三) 多片湿式离合器摩擦面更多,接合更加平顺柔和;摩擦片浸在油中工作,表面磨损小。但分离行程大、分离也不易彻底,特别是在冬季油液粘度增大时;轴向尺寸大;从动部分的转动惯量大,故过去未得到推广。近年来,由于多片湿式离合器在技术方面的不断完善,重型车上又有采用,并有不断增加的趋势。因为它采用油泵对摩擦表面强制冷却,使起步时即使长时间打滑也不会过热,起步性能好,据称其使用寿命可较干式高出5~6倍。通过各结构优缺点的比较及本次设计所针对的车型,故本次设计选用的是单片干式摩擦离合器。图2-1 双片离合器图2-2 拉式膜片弹簧离合器图2-3 膜片弹簧离合器图2-4 单片离合器第三章设计计算及参数的选择第一节离合器基本结构参数的选择一摩擦片设计离合器摩擦片在性能上应满足如下要求:1) 摩擦因数较高且稳定,工作温度、单位压力、滑磨速度的变化对其影响要小;2) 有足够的机械强度与耐磨性;3) 密度小,以减小从动盘的转动惯量;4) 热稳定性好,在高温下分离出的粘合剂少,无味,不易烧焦;5) 磨合性能好不致刮伤飞轮和压盘表面;6) 接合时应平顺,不产生“咬合”或“抖动”现象;7) 长期停放后,摩擦面不发生“粘着”现象。摩擦片的外径是离合器的重要参数。它对离合器的轮廓尺寸有决定性的影响,并根据离合,离合器器能全部传递发动机的最大转矩来选择。为了能可靠地传递发动机的最大的转矩Temax的静摩擦力矩Tc应大于发动机的最大转矩T,而离合器传递的最大静摩擦力矩Tc又取决于emax其摩擦面数Z、摩擦系数f、作用在摩擦面上的总压紧力P∑与摩擦片平均半径Rm,即Tc=βTemax=1.5.×126=189N.M式中β——离合器的后备系数。β(一) 后备系数[2]后备系数β是离合器设计时用到的一个重要参数,它反映了离合器传递发动机转矩的可靠程度。在选择β时应考虑以下几点:1)摩擦片在使用中磨损后,离合器还应能可靠地传递发动机的最大转矩。2) 要防止离合器滑磨过大 3) 要能防止传动系过载显然,为了可靠地传递发动机最大转矩和防止离合器滑磨过大,β不宜选取太小;为了使离合器尺寸不致过大,减少传动系过载,保证操纵轻便,β又不能选取太大;当发动机后备功率较大,使用条件较好时,β可选择小些;当使用条件恶劣,需要拖带挂车时,为提高起步能力,减少离合器磨损,β应选取大些;货车总质量越大,β也应选得越大;采用柴油机时,由于工作比较粗暴,转矩较不平稳,选取的β值应比汽油机大些;发动机缸数越多,转矩波动越小,β可选取小些;膜片弹簧离合器由于摩擦片磨损后压力保持较稳定,选取的β值可以比螺旋弹簧的小些;双片离合器的β值应大于单片离合器。各类汽车β值的选取范围通常为:轿车和微型车、轻型货车——β=1.20~1.75 中型和重型货车——β=1.50~2.25越野车、带拖挂的重型汽车和牵引汽车——β=1.80~4.00 根据上述原因及所选车型,选取β=1.50。 (二) 单位压力[2]0P单位压力0P 对离合器工作性能和使用寿命有很大的影响,选取时应考虑离合器的工作条件,包括发动机的后备功率大小,摩擦片尺寸、材料及其质量和后备系数等因素。离合器使用频繁,发动机后备系数较小时,0P 应取小些;当摩擦片外径缴大时,为了降低摩擦片外缘处的热负荷,0P 应取小些;后备系数较大时,可适当增大0P 。当摩擦片采用不同材料时,0P 按下列范围选取: 石棉基材料:0P =0.10~0.35MPa 粉末冶金材料:0P =0.35~0.60MPa ≥金属陶瓷材料:0P =0.70~1.5MPa根据所选车型及摩擦片所用材料,选取 0.10mp ≤0P ≤1.50mp 本次取0P =0.30MPa 。 (三) 摩擦片外径D 、内径d 和厚度h 的确定离合器应按转矩容量或热容量设计,摩擦片或从动片外径D 是基本尺寸。它关系到结构尺寸及质量的大小和使用寿命的长短设计是通常首先确定D 的值。由以下公式计算D 的值:(3-2)式中:max e T ——发动机的最大转矩 f ——摩擦系数 z ——摩擦面数 或由经验公式得:Te D maxDK =由选车型得K D =14.6max e T = 126N·m,D=163.88mm在同样外径时,选用较小的内径d 虽可增大摩擦面积,提高传递转矩的能力,但是会使摩擦面上的压力分布不均匀,使内外沿圆周的相对滑磨速度差别太大而造成摩擦面磨损不均匀,且不利于散热和扭转减振器的安装。摩擦片尺寸应符合尺寸系列标准GB5764—1998(《汽车用离合器面片》),所选的D 应使摩擦片最大圆周速度不超过65~70m/s,以免摩擦片发生飞离。所以由计算所得D 值及参照摩擦片尺寸系列标准GB5764—1998,最后选定摩擦片的尺寸为下表表3-1选定的摩擦片的尺寸(四) 摩擦片的校核:1、摩擦片外径D(mm)的选取应使最大圆周速度D V 不超过65~70m/s,即3[1]max 1065~70/60D e D m s v n π-=⨯≤ (3-3)式中,D V 为摩擦片的最大圆周速度(m/s);n max e 为发动机最高转速(r/min)。 将n max e =5000r/min,D=180mm,代入(3-3)式得: VD=47.1m/s<65~70m/s则摩擦片的最大圆周速度在安全范围内。2、为反映离合器传递的转矩并保护过载的能力,单位摩擦面积传递的应小于其许用值,即 [1]224[]()co co TcT T z D d π=≤- (3-4) 式中,co T 为单位摩擦面积传递的转矩(2/N m mm );[co T ]为其允许值(2/N m mm ),按表3-2选取。表3-2 单位摩擦面积传递的转矩 (2/N m mm )由D=180mm,选取co T =0.28×210-2/N m mm .则由(3-1)、(3-4)得:Tco=0.00712/N m mm >0.28×210-2/N m mm 不满足要求 故重新选取D=250mm d=155mm重新校核 :3[1]max 1065~70/60D e D m s v n π-=⨯≤VD=65.41<65~70m/[1]224[]()co co TcT T z D d π=≤- Tco=0.00312/N m mm 符合要求3摩擦片的内外径比c 应在0.53~0.70内 c=d/D=125÷180=0.694故符合要求4为了保证扭转减振器的安装,摩擦片内径d 必须大于减振器弹簧位置直径2Ro 约50mm,即d≥2Ro+50 。即:2Ro ≤75符合要求第二节 膜片弹簧设计(一) 膜片弹簧的结构特点膜片弹簧的结构形状如图3-1所示,它由弹簧钢板冲制而成。从图中可以看出,膜片弹簧在结构形状上分成两部分,在膜片弹簧大端处为一完整的截锥体,如图3-2的样子。它的形状像一个无底的碟子,与一般机械上用的碟形弹簧完全一样,故称作碟簧部分,膜片弹簧起弹性作用的正是此部分。碟形弹簧的弹性作用是这样的 沿其轴线方向加载,碟簧受压变平,卸载后又恢复原形(如图3-2所示)。可以说膜片弹簧是碟形弹簧的一种特殊结构形式,所不同是在膜片弹簧上还包含有径向开槽部分,此部分像一圈瓣片,其作用是:当分离离合器时作为分离杆,故此瓣片又称作分离指。分离指与碟簧部分交接处的径向槽呈长方圆形孔,这样做一方面可以减少分离指根部的应力集中(分离指根部过渡圆角半径应大于4.5mm),另一方面又可用来安置销钉固定膜片弹簧。图3-1 膜片弹簧 图3-2 碟形弹簧(二) 膜片弹簧的加载方式和变形情况离合器在接台与分离时,膜片弹簧的加载情况不一样,相应地存在着两种加载方式和变形形状。1、接合时 离合器接合时,膜片弹簧起压紧弹簧的作用。在压盘、离台器盖总成未与飞轮装台之前,膜片弹簧近似处于自由状态(如图3-3a所示),膜片弹簧对压盘无压紧作用。当压盘、离台器盖总成与飞轮装合时,离台器盖前端面与飞轮前端面靠拢,因此离台器盖通过支承环1对膜片弹簧施加载荷1P,膜片弹簧几乎被压平(如图3-3b所示),同时在压盘处也作用有载荷1P,1P即为压紧力。图3—3 膜片弹簧在不同工作状态时的变形 a)自由状态 b)压紧状态 c)分离状态2、分离时当分离轴承以2P力作用在膜片弹簧小端的分离爪上时,支承环1逐渐不起作用,而支承环2开始起作用,当力2P达到一定值耐,膜片弹簧被压翻,离合器分离(如图3-3c所示),2P称为分离力。(三)膜片弹簧的弹性变形特性如前所述,膜片弹簧起弹性作用的部分是其碟簧部分,碟簧部分的弹性变形特性和螺旋弹簧不一样,它是一种非线性弹簧,其特性与碟簧部分的内截锥高H及弹簧片原h之比值 H/h有关。不同的H/h值可以得到不同的弹性变形特性, 一般可分成下列四种情况:1 、H/h<2如图3-4所示,图中曲线A为 H/h=0.5时的无因次特性曲线,,从曲线形状可知:随着载荷P的增加,变形 也不断增加,这种膜片弹簧刚度很大,可以承受很大的载荷,适台于作为缓冲装置中的行程限制器。图3-4 不同H/h值的无因次特性曲线图3-5 膜片弹簧的弹性变形特性2、H/h2图3-4中曲线B为H/h=1.5时的无因次特性曲线,曲线中间有一段很平直、变形在增加.载荷P几乎保持不变,这种弹簧叫做零刚度弹簧。3、22图3-4中曲线C为H/h=2.75时的无因次特性曲线,图中可以看到膜片弹簧的特性曲线中有一段负刚度区域,即当变形增加时.载荷反而减小,具有这种特性的膜片弹簧很适用于作为离台器的压紧弹簧。因为可利用其负刚度区达到分离离台器时操纵省力之目的。当然.负刚度区域过大也不适宜,以免弹簧工作位置略微变动造成弹簧压紧力变化过大。4、2如图3-5所示,图中曲线为H/h=3时的无因次特性曲线,这种弹簧的特性曲线中具有更大的负刚度不稳定工况区,而且有载荷为负值的区域,这种弹簧适用于汽车液力传动中的锁止机构。(四) 膜片弹簧基本参数的选择1、比值H/h和h的选择如前所述,比值H/h对膜片的弹性特性影响极大,因此,要H/h 对弹簧特性的影响,正确地选择该比值,以得到理想的特性曲线及获得最佳的使用性能。为保证离合器压紧力变化不大和操纵轻便,汽车离合器用膜片弹簧的H/h一般为1.5~2.2,板厚为2~4mm。根据上述原因及所选车型,选取 h=3mm,则H=5.4mm。2、R/r比值及R、r的选择研究表明,R/r越大,弹簧材料利用率越低,弹簧越硬,弹性特性曲线受直径误差的影响越大,而且应力越高。碟形弹簧储蓄弹性能的能力,在R/r=1.8~2.0为最大,用于缓和冲击、吸收振动等需要储存大量弹性能的碟簧最佳。但对汽车离合器的膜片弹簧而言,并不要求储存大量的弹性能,而应根据结构布置和压紧力的要求,通常取R/r为1.2~1.35。为使摩擦片上压力分布较均匀,推式膜片弹簧的R值应取大于或等于摩擦片的平均半径R c,拉式膜片弹簧的r值宜取为大于或等于R c。根据上述原因及所选车型,选取,R=105mm,则r=80mm。3、α的选择 膜片弹簧自由状态下圆锥底角α与内截锥高度H 关系密切,α=arctanH/(R-r)≈H/(R-r),一般在9°~15°范围内。则代入H 、R 、r 值得:α=11°。4、压盘加载点半径1R 和支承环加载点半径1r 的确定 1R 和的取值将影响膜片弹簧的刚度。1r 应略大于r且尽量接近r,1R 应略小于R 且尽量接近R,因此,选取1R =124mm,1r =104mm 。5、分离指数目n 的选取 分类指数目n 常取为18,大尺寸膜片弹簧可取24,小尺寸可取12。考虑到所选车型,选取n=18。 图3—6 膜片弹簧的尺寸简图6、切槽宽度1δ、2δ及半径e r (图3-6)的确定 1δ=3.2~3.5mm,2δ=9~10mm,e r 的取值应满足r -e r ≥2δ的要求。因此选取1δ=3.4mm,2δ=9mm,e r =92mm 。7、膜片弹簧小端内半径0r (图3-6)及分离轴承作用半径f r 的确定 0r 由离合器的结构决定,其最小值应大于变速器第一轴花键的外径。因膜片弹簧的分离指起分离杠杆的作用,因此其杠杆比在一定范围内选取[1],即推式:2.3≤111fr r R r --≤4.5 拉式:3.5≤111fR r R r --≤9.0本设计为推式,折中选取杠杆比为3,而已知1R =124=mm 、 1r =104mm,则: 1113*()f r r R r =--=30mm而f r 与0r 的差值应在0≤f r -0r ≤4范围内[1],则选取0r =30mm 。第三节 扭转减振器的设计一、扭转减振器的功能扭转减振器主要由弹性元件(减振弹簧或橡胶)和阻尼元件(阻尼片)等组成。弹性元件的主要作用是降低传动系的首端扭转刚度,从而降低传动系扭转系统的某阶(通常为三阶)固有频率,改变系统的固有振型,使之尽可能避开由发动机转矩主谐量激励引起的共振;阻尼元件的主要作用是有效地耗散振动能量。所以,扭转减振器具有如下功能:1)降低发动机曲轴与传动系接合部分的扭转刚度,调谐传动系扭振固有频率。2)增加传动系扭振阻尼,抑制扭转共振响应振幅,并衰减因冲击而产生的瞬态扭振。3)控制动力传动系总成怠速时离合器与变速器轴系的扭振,消减变速器怠速噪声和主减速器与变速器的扭振与噪声。4)缓和非稳定工况下传动系的扭转冲击载荷和改善离合器的接合平顺性。扭转减振器具有线性和非线性特性两种。单级线性减振器的扭转特性如图3—9所示,其弹性元件一般采用圆柱螺旋弹簧,广泛应用于汽油机汽车中。当发动机为柴油机时,由于怠速时发动机旋转不均匀度较大,常引起变速器常啮合齿轮齿间的敲击,从而产生令人厌烦的变速器怠速噪声。在扭转减振器中另设置一组刚度较小的弹簧,使其在发动机怠速工况下起作用,以消除变速器怠速噪声,此时可得到两级非线性特性,第一级的刚度很小,称为怠速级,第二级的刚度较大。目前,在柴油机汽车中广泛采用具有怠速级的两级或三级非线性扭转减振器如图3—10所示。图3-9 单级线性减振器的扭转特性 图3-10 三级非线性减振器的扭转特性二、扭转减振器的主要参数选择 减振器的扭转刚度C α和阻尼摩擦元件间的摩擦转矩f T 是两个主要参数。其设计参数还包括极限转矩j T 和预紧转矩Ty 等。1. 极限转矩j T极限转矩为减振器在消除限位销与从动盘毂缺口之间的间隙△1(图2—15)时所能传递的最大转矩,即限位销起作用时的转矩。它与发动机最大转矩有关,一般可取[]2max max (1.2~1.4)j e j e T T T T =+∆= (3-19)取j T =2.0Temax,则由所选车型可得:j T =252N·m 。2、扭转刚度是Cα为了避免引起系统的共振,要合理选择减振器的扭转刚度,使共振现象不发生在发动机常用工作转速范围内。C α决定于减振弹簧的线刚度及其结构布置尺寸(图2—15)。C α=13j T =13×252=3276N·m /rad 。3、阻尼摩擦转矩f T由于减振器扭转刚度是,受结构及发动机最大转矩的限制,不可能很低,故为了在发动机工作转速范围内最有效地消振,必须合理选择减振器阻尼装置的阻尼摩擦转矩T μ。一般可按下式初选Tf=(0.06-0.17)Temax (3-23)则取f T =15.12 N·m 。4、预紧转矩Ty减振弹簧在安装时都有一定的预紧。研究表明,y T 增加,共振频率将向减小频率的方向移动,这是有利的。但是y T 不应大于f T ,否则在反向工作时,扭转减振器将提前停止工作,一般取Ty =(0.06-0.17)Temax,则Ty =12.6N·m 。三、 减振器的结构设计在初步选定减振器的主要参数后,即可根据布置上的可能来确定它的具体结构尺寸,并设计减振弹簧以满足其减振性能的要求。1、减振弹簧的位置半径RoRo 的尺寸应尽可能大些,如图3—11所示,一般取2)75.0~60.0(0d R = (3-24) 式中,d 为离合器摩擦片内径。则取Ro =0.6×155÷2=46.5mm 。2、减振弹簧个数nn 参照表3—3选取。表3—3 减振弹簧个数的选取3、减振弹簧总压力∑F当限位销与从动盘毂之间的间隙△1或△2被消除,减振弹簧传递转矩达到最大值时,减振弹簧受到的压力∑F 为0/R T F j =∑ =252÷0.0465=5419.35N (3-25)则F=5419.35 N。(一)从动盘总成从动盘总成主要由从动盘毂、摩擦片、从动片、扭转减振器等组成。从动盘对离合器工作性能影响很大,设计时应满足如下要求:(1)从动盘的转动惯量应尽可能小,以减小变速器换档时轮齿的冲击。(2)从动盘应具有轴向弹性,使离合器接合平顺,便于起步,而且使摩擦面压力均匀,以减小磨损。(3)应安装扭转减振器,以避免传动系共振,并缓和冲击。1.轴向弹性从动盘的结构形式为了使从动盘具有轴向弹性,常用的方法有:(1)在从动片外缘开6—12个“T”形槽,形成许多扇形,并将扇形部分冲压成依次不同方向弯的波浪形。两侧的摩擦片则分别铆在每隔一个的扇形上。“T”形槽还可以减小由于摩擦发热而引起的从动片翘曲变形。这种结构主要应用在商用车上。(2)将扇形波形片的左、右凸起段分别与左、右侧摩擦片铆接,由于波形片(1.0mm)比从动片(1.5mm)薄,这种结构的轴向弹性较好,转动惯量较小,适宜于高速旋转,主要应用于乘用车和最大总质量小于6t的商用车上。(3)利用阶梯形铆钉杆的细段将成对波形片的左片铆在左侧摩擦片上,并交替地把右片铆在右侧摩擦片上。这种结构的弹性行程较大,弹性特性较理想,可使汽车起步极为平顺。这种结构主要应用于发动机排量大于2.5L的乘用车上。(4)将靠近飞轮的左侧摩擦片直接铆合在从动片上,只在靠近压盘侧的从动片铆有波形片,右侧摩擦片用铆钉与波形铆合。这种结构的转动惯量大,但强度较高,传递转矩的能力大,主要应用于商用车上。2.从动盘毂从动盘毂是离合器中承受载荷最大的零件,它几乎承受发动机传来的全部转矩。它一般采用齿侧对的矩形花键安装在变速器的第一轴上,花键的尺寸可根据摩擦片的外径D与发动机的最大转矩Temax按国标GB1144-74选取(见表3—4)。从动盘的轴向长度不宜过小,以免在花键轴上滑动时产生偏斜而使分离不彻底,一般取1.0 1.4倍的花键轴直径。从动盘毂一般采用锻钢(如35、45、40Cr等),并经调质处理。为提高花键内孔表面硬度和耐磨性,可采用镀铬工艺:对减振弹簧窗口及从动片配合,应进行高频处理。花键选取后应进行挤压应力σj(MPa)及剪切应力τj(MPa)的强度校核:表3—3 离合器从动盘毂花键尺寸系列摩擦片外径发动机的最大转矩花键尺寸挤压应力σj/Mpa 齿数外径内径齿厚有效齿长。
430离合器零件图解目录(中文版)
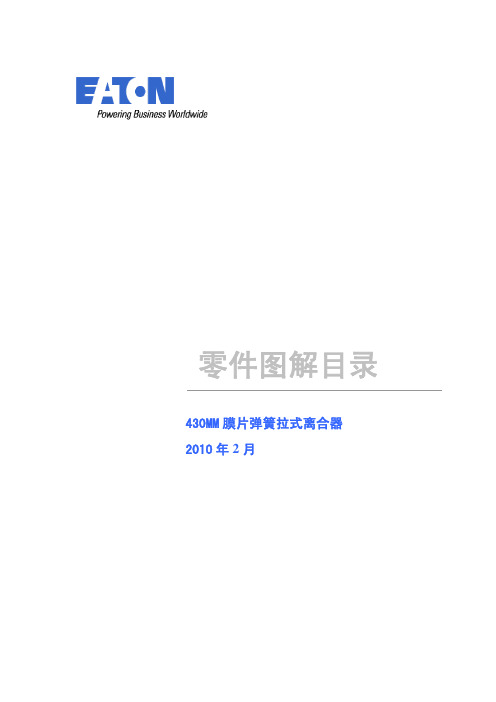
430mm 离合器总成
5
3 4
Байду номын сангаас
2
1
430mm 离合器总成
序号 1 2 3 4 5 零件号 125693 125479 16000-31 17000-31 128769 零件名称 分离轴承 快速卡环总成 离合器压盘 离合器盖总成 从动盘总成 数量 1 1 1 1 1 不单独提供 备注
伊顿公司版权所有。伊顿公司保留不需提前通知而进行更改的 权利。如需咨询或获取最新资料可致电伊顿客户支持热线: 800-820-1621 或 400-820-1621。 伊顿公司· 车辆集团· 上海市长宁区临虹路 280 弄 3 号·200335
零件图解目录430mm膜片弹簧拉式离合器2010年2月430mm离合器总成4成不单独提供15321430mm离合器总成序号零件号零件名称数量备注1125693分离轴承12125479快速卡环总13600031离合器压盘141700031离合器盖总成1512876
零件图解目录
430MM 膜片弹簧拉式离合器 2010 年 2 月
离合器从动盘设计说明书资料

一、 技术参数及论文要求 发动机型号:DA462Q发动机最大转矩[N ·m/(r/min )]:51.5/3750 主减速比:5.142 一档速比:3.482驱动轮类型与规格:4.5-12-8PR 汽车总质量(Kg ):1425Kg 使用工况:城市 离合器形式:单摩擦片二、 离合器摩擦片参数的确定2.1 摩擦片参数的选择摩擦片外径是离合器基本尺寸,它关系到离合器的结构重量和寿命,它和离合器所需传递转矩大小有一定关系。
按照发动机最大转矩初选D ,根据公式D=165mm == 式中,max e T 为发动机最大转矩,取max51.5TN m =⋅;k 为不同结构和使用条件对D 的影响系数,对于小轿车 取k=47。
一般情况下,小轿车β取值范围为1.2~1.3,宜取较小值,故初取β=1.2。
2.2 离合器基本参数的校核2.2.1 单位压力P为降低离合器滑磨时的热负荷,防止摩擦片损伤,对于小轿车,D 小于等于230mm 时,单位压力P 约为0.25Mpa ,用式(3-4)验算单位压力P 。
初选摩擦片的材料为石棉基摩擦材料因此摩擦系数M=0.25-0.4,推荐M=0.3;用公式(1) 取Re=2i203i30R 32R R R --时,Re=0.077 pA Z T μβRe emax =,Z=2 0.143MPA p =MPa(2)取Re=21(i R R +0)时,Re=0.07625 pA Z T μβRe emax =,Z=2 0.144p =MPa单位压力P 在容许范围内,即小于0.25mpa 认为所选离合器的尺寸,参数合适。
摩擦片的相关参数如表2表2摩擦片外径D 摩擦片内径d 后备系数β厚度b 单位压力Po 160mm110mm1.2 3.20.25MPa三、 扭转减振器的设计3.1 扭转减振器主要参数带扭转减振器的的从动盘结构简图如下图4.1所示弹簧摩擦式:图带扭转减振器的从动盘总成结构示意图1—从动盘;2—减振弹簧;3—碟形弹簧垫圈;4—紧固螺钉;5—从动盘毂;6—减振摩擦片7—减振盘;8—限位销由于现今离合器的扭转减振器的设计大多采用以往经验和实验方法通过不断筛选获得,且越来越趋向采用单级的减振器。
srga培训资料

GETRAG (Jiangxi) Transmission Co., Ltd.
2.详细说明--2.2过程描述
2.2.1生产工艺及场地变化(流程)
流程中涉及到的GJT部门可能会有所变化,在重新确 定各部门前,请供应商将SRGA发给采购部现场STA.
步骤1.1解释—怎样填写SRGA表格: 该表格分为两页,供应商必须完整填写第一页. 表格第一页分为两个部分,一部分为部件和供应商信息,另一部分为变更说明和实施计划. 供应商部件/产品信息. 变更类型包括影响格特拉克厂方、分供应商的变更说明. 当变更场地时,需要提供更多有关变更类型的信息。 .表格空白部分用来填写变更目的和说明。如果需要的话,用小图表标明变更内容并贴在上面或通过附件说明。 表格下半部分是变更实施计划的方位,开始必须由供应商填写并告知格特拉克工程部门。 当SRGA计划中的变更工作未全部完成时,必须先弄清楚下列内容: 变更什么? 变更对生产流程有什么影响? 该变更可能导致什么其他问题? 如果有的话,对部件/产品有什么影响? 采用何种检测方式对可能发生的故障进行检测? 为了解决这些问题,为了对变更的可行性进行全面评估,需要采用D-FMEA(失效模式和后果分析)以及有 效性测试计划。 .一份完整的变更和计划有利于格特拉克对SRGA进行快速评估。而一份说明不充分或不完整的计划可能导 致评估延迟。 实施的计划必须包含补救计划,以应客户要求检测、生产部件批准程序或功能试验不成功时之用。 第二页是同意方,即由格特拉克填写。 SRGA表格填写完成后,供应商必须将其提交给格特拉克采购部门的相关买方/技术部门。
GETRAG (Jiangxi) Transmission Co., Ltd.
2.详细说明--2.2过程描述
- 1、下载文档前请自行甄别文档内容的完整性,平台不提供额外的编辑、内容补充、找答案等附加服务。
- 2、"仅部分预览"的文档,不可在线预览部分如存在完整性等问题,可反馈申请退款(可完整预览的文档不适用该条件!)。
- 3、如文档侵犯您的权益,请联系客服反馈,我们会尽快为您处理(人工客服工作时间:9:00-18:30)。
放气螺钉罩
EPDM
编制:史蒙蒙
审核:陈章明
日期:2011-3-28
GB/T699
45#
GB/T699 GB699-88 GB5232 HG2865中的B类 HG/T2578中的II 类CA5464
表面氧化成绿色 表面发黑
适用F6N6等分泵
进油管接头 20#
适用GEA5等分泵
9 10 11
密封锥 皮圈 防尘罩
HPb59 EPDM EPDM
12 13
螺纹油孔塞
NBR
江西江铃集团深铃汽车零部件有限公司
离合器分泵零件设计资料表
序号 零件名称 实际使用 实际使用标准号 材料 表面处理及特殊要求
表面电泳漆处理(黑色),按标准 GB/T10125-1997达到中性盐水喷雾试验96 小时 表面处理:硬质阳极氧化,膜厚大于 0.01mm,表面硬度HV350~650;
备注
1
缸体
HT200
GB9439
2 3 4 5 6
活塞
铝6061
GB/T6892
密封垫片
纯铜T2
GB5231 GB342/ GB4357 GB/T699 GB/T699
表面发黑
弹簧 推杆 放气螺钉
70C 45# 45#
表面处理:D.Zn7.DC(镀彩锌);
表面处理:D.Zn7.DC(镀彩锌);
7
压紧螺钉
45#