首件签样流程图
首件确认流程
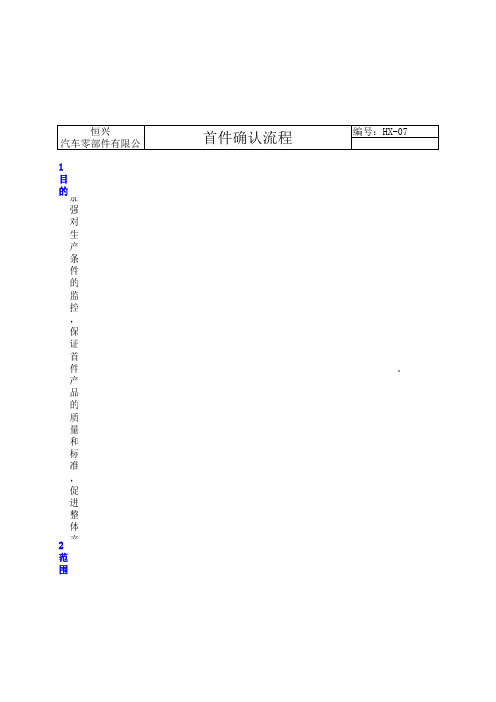
首件确认流程
编号:HX-07
目的 加强对生产条件的监控,保证首件产品的质量和标准,促进整体产品质量的控制 。 2 范围 。 适用于每班开班时,对于首件生产前准备工作,及首件确认标准和状态的指导 3 术语
无
4
控制流程 担 当 流 程 和 标 准 备 注
操作者
作业点检
首开机点检设备、模 具、材料状态
异常 问题 处理
结束
5 6
相关文件
无
使用表单
《生产起始点检表》 《自检记录》 作者
生产出首件 工艺问题
调整工 班长
工艺复核
调整工、班长进行 工艺确认 检验依据限度样件 检验异常重新调试
质检员
N
首件检验
N
质检员
操作者
模具 设备 原材 料问
首件封存 人、机、料、 法、环等因素 变化
质检员首件粘贴标识
正常生产
当人、机、料、法、 环等因素变化时需 重新封存首件
首件、初件、初面生产确认流程

调试≤5大块
生产
生产1大块, 若存 在异常, 可生产 第2次, 直至OK。
生产3大块, 工程\生产\依 次确认后, 质量确认出异常, 开稽核单。(确认要有记录)
生产1大块, 若存 在异常, 可生产 第2次, 直至OK。
生产3大块, 工程\生产\依 次确认后, 质量确认出异常, 开稽核单。(确认要有记录)
版本:V1.0 拟制:
审核:
生产:
质量:
批准:
生效日期:
备注: 1.工具:Grommet棒
首件/初件/初面生产确认流程 aabb:::
操
GF
ab
目的:完善和明确首件、初件、初面的生产及确认规则.
首 件 流 程
同型号滚单可不生产胶板
程序和物料OK
生产T面胶板
生产T面首件
备注: 1.工具:Grommet棒
同型号滚单可不生产胶板
生产B面胶板
生产B面首件
测试首件 测试PASS 正常Biblioteka 初 件 流 程开班生产
初件印刷检查
初件贴片检查
初件炉后检查 三个检查环节均通过 正常生产
1.印刷员必须100%检查 开班的前两大块。
2.工程九点前检查一次.
工程\生产\质量三方 检查初件贴片状态。 (检查同样要有记录).
工程\生产\质量三方 检查初件焊接状态。 (检查同样要有记录).
注意:以上三个检查环节任意一个出问题时都必 须即时改善,并重新跟踪整个流程。若已发生批 量不良,则由质量部制定维修方案进行返工。
初 面 流 程
换面生产
初面印刷检查
初面贴片检查
初面炉后检查 三个检查环节均通过 正常生产
1.印刷员必须100%检查 开班的前两大块。
首件确认流程

首件确认后,把附样的信息写到首件上面去,由质检员把附样及时归还给计划员;
质检员
计划员
计划员收到附样后,及时归还给业务跟单员,计划员要做好交接记录;
计划员
跟单员
新产品打样
质检员依据产品的外观检查合格后交由品质经理与工程部共同确认完整样品。
质检员
品质经理
总经办抽查作业流程ຫໍສະໝຸດ 标准责任人检查
责任
业务附样
业务附样应该提供给计划员完整客户信息(颜色、钩型、材质、尺寸、型号等要求),附样上要写清楚订单号码和产品信息;
跟单员
计划员
总经办抽查
1、检查人员每次检查不合格,需要开部门联系单,直接按照每次5元标准进行对责任人进行处罚,屡犯屡罚;
2、下流程没有检查上流程,或没有检查到上流程存在的问题的,责任由下流程承担,如果下流程能够提供已经对上流程处罚的部门联系单证明(需有责任人签字),则责任转移到上流程;
总经办抽查
安装印刷车间首检由部门主管交给质检员,由质检员10分钟回复结果;
质检员
部门主管
品管确认
质检员收到首检应在10分钟内确认,并填写(首检确认\检验记录表)。要求如实填写:产品重量、尺寸
规格及相关测试等。交由当班班长签名并大货生产;
质检员
品质经理
总经办抽查
质检员发现任何与计划分单或者附样不符的首检样品时,当班班长应在10分钟之内进行现场解决;
3、如果下流程对上流程责任人进行处罚时,责任人拒绝签字确认的,由下流程提报上流程上一级主管签字确认,责任按照“每往上一级,处罚增加一倍”的原则进行;
PMC
计划员在接收到订单时,必须有附样,并且把形状样或颜色样需要写清楚,否则,计划员不可以接收订单;
首件制作与确认流程

1.品质组长对首件与《首件确认单》上核对内 容,进行核对,并在《首件确认单》做好对 应记录 2.将首件装入PE袋中,并在上面做好对应的签 名与标示。 3.对于新产品、新订单、及特殊、订制订单的 首件,由IPQC交给业务业核对。必须经过该 订单的业务员进行核对,并签名确认。
1.核对确认好的首交还生产拉长 2.按生产计划将一个首件放置产线拉头看板指 定位置,另一个从拉头流下,每个工位的作业 人员拿起来查看与现有物料核对,无误后流入 终检位的指定位置 与拉长面对面当面交接,并在《派料 单》上备注签名确认好
1.IPQC拿对应《BOM》核对物料 2.严格按照《作业指导书》和工艺文 件进行制作 3.首件制作的数量是2个
《BOM》 《作业指导书》
拉长完成首件制作后,填写好《首件确认单》
与首件一同交IPQC核对
《首件确认单》
品质部
IPQC进行首件图档确 认
IPQC进行首件让所有的物料进行图档确认, 并在《首件确认单》做好对应记录
品质部
IPQC进行首件与MPC 样品的核对
IPQC进行首件与MPC样品的核对,确认好 作业工艺,实物对照,并在《首件确认单》 做好对应记录
品质部 业务部
生产部
IPQC将核对好的首件交品 质组长及业务员审核
3.工单完成后,首件方可投入产线包装
NO 变更日期
变更履历记录栏 变更内容
担当
承认
深圳市脉威时代科技有限公司
流程名称 序 发行部门
號 責任單位
生产部
生产部
流程图
首件制作与确认流程
发行日期
流程
物料员领完物料
SOP编号
承认
确认
确认
产品首件鉴定和检验程序(含表格)
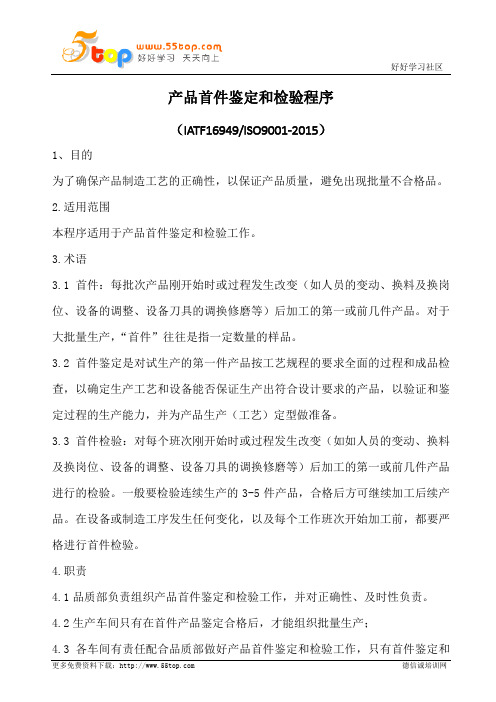
产品首件鉴定和检验程序(IATF16949/ISO9001-2015)1、目的为了确保产品制造工艺的正确性,以保证产品质量,避免出现批量不合格品。
2.适用范围本程序适用于产品首件鉴定和检验工作。
3.术语3.1首件:每批次产品刚开始时或过程发生改变(如人员的变动、换料及换岗位、设备的调整、设备刀具的调换修磨等)后加工的第一或前几件产品。
对于大批量生产,“首件”往往是指一定数量的样品。
3.2首件鉴定是对试生产的第一件产品按工艺规程的要求全面的过程和成品检查,以确定生产工艺和设备能否保证生产出符合设计要求的产品,以验证和鉴定过程的生产能力,并为产品生产(工艺)定型做准备。
3.3首件检验:对每个班次刚开始时或过程发生改变(如如人员的变动、换料及换岗位、设备的调整、设备刀具的调换修磨等)后加工的第一或前几件产品进行的检验。
一般要检验连续生产的3-5件产品,合格后方可继续加工后续产品。
在设备或制造工序发生任何变化,以及每个工作班次开始加工前,都要严格进行首件检验。
4.职责4.1品质部负责组织产品首件鉴定和检验工作,并对正确性、及时性负责。
4.2生产车间只有在首件产品鉴定合格后,才能组织批量生产;4.3各车间有责任配合品质部做好产品首件鉴定和检验工作,只有首件鉴定和检验合格才能批量生产。
4.4品质部应做好产品首件鉴定和检验工作,并对其结果进行确认;5.首件产品鉴定工作程序5.1首件鉴定范围a)新产品(加工工序多或复杂)在工艺定型前的首件;b)不连续的批生产,间隔一年后又恢复生产的首件;c)设计图纸发生重大更改后生产的首件;d)工艺规程发生重大更改后生产的首件;e)合同要求指定的首件。
5.2首件鉴定的内容a)首件生产所依据的技术、工艺文件是否正确、完整、协调、有效,并能指导生产;b)产品加工的工艺安排是否合理可行,适合批量生产;c)所用采购产品是否符合规定要求;d)选用的所有设备能否满足生产要求,生产环境是否满足生产要求;e)生产操作人员是否具备相应的能力;f)首件质量与其质量记录是否相符,质量问题是否按规定得到处理;g)有顾客要求的工序是否经顾客签署认可。
供应商首样检验流程

版本. 修订记录修订人发行日期A/0部门 Dept. 评审 Reviewed 部门 Dept. 评审 Reviewed 部门 Dept. 评审 Reviewed□行政人事部□生产部□财务部□事业部□采购部□焊接培训中心□质量部□设备部□工程部□物料部Approved By: Prepared By:Reviewed By:目录1.0Purpose目的 (2)2.0 Scope范围 (2)3.0 Responsibility职责 (2)3.1 进料检验员 (2)3.2 项目工程师 (2)3.3 CQE工程师 (3)3.4 SQE工程师 (3)3.5 生产工段长 (3)3.6开发工程师 (3)3.7 文控 (3)3.8 质量经理,项目经理 (3)4.0 Defination定义 (3)5.0 Procedure程序 (3)5.1首件检查的准备 (3)5.2 FAI 流程 (3)6.0 Flow chart流程 (4)7.0 Reference 相关文件 (4)8.0 Record记录 (4)1.0Purpose目的为产品的供应资格的认定过程提供指导, 进行供方质量保证能力、符合性、适用性的验证,以保证批量采购件的质量满足规定的要求。
2.0 Scope范围本程序适用于新产品开发、工艺更改等由伟泰的供应商提供的产品(板材、包材除外)。
3.0 Responsibility职责3.1 进料检验员3.1.1 依FAI相关技术要求,提供符合性的检测数据,并作出样品符合性结论。
3.1.2 检测结论知会开发工程师和供应商质量工程师。
3.1.3及时更新“FA报告概要”,记录送检次数和结果。
3.1.4负责“样品区域”管理,建立样品台帐并及时更新。
3.2 项目工程师3.2.1 提供正确、有效、完整的技术文件(图纸上注明“临时”字样)。
协助开发工程师及时与供方解决在制造过程中出现的技术问题。
3.2.2主导并确定样品承认时应进行的适用性、可靠性验证项目及验证方法,得出验证结论,并在相关《供应商送样批准表》上签字。
首件确认流程
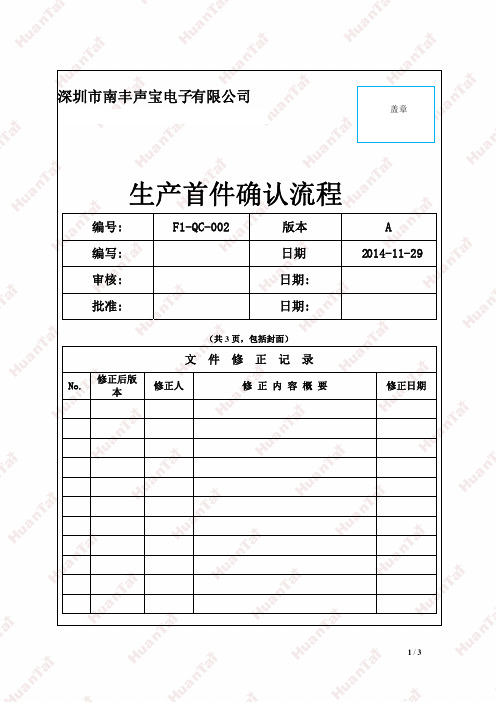
善,如有必要可知会生产、品质主管要按标准要求来作业。
4.4 生产收到品质部首件确认完毕通知,对通过的型号开始安排量产,对不合格型号按改
善意见重新制作合格样或返修合格再次送检确认。
4.5 生产必须等首件确认合格后方能进行批量生产,以免造成不必要返工浪费。
4.6 首件确认后,IPQC 第一时间到各工位确认生产产品质量与标准要求是否一致、是否按
3.1 生产部负责首件制作及送检,品质IPQC参与制作
3.2 品质部负责组织首件确认、生产时质量标准落实监督,确认包括原材料、尺寸、工艺
制作方法、上下道工序组装适配。
3.3 工程部负责新产品及配合旧产品异常时首件确认
3.4 首件确认不合格或首件未经确认擅自生产,出现质量异常直接由生产责任者负责
3.5 首件确认失误或首件未确认完便出具质量凭证,造成质量异常由相关确认者负责
A 3
附(流程图):
责任部门 生产部
首件确认流程图 过程/活动
首样制作
产生记录
相关文件
品质部
首样检验
品质部
NG
判定
OK
《首样确认单》
《成品检验 标准》
工程部
工程判定
《首样确认单》
工程部
解决方案
《产品解决方案》
生产部
批量生产
3/3
首样样板生产。
4.7 确认合格首件需先放在首件放置处,直到批生产完毕后才流入下工序或包装
5.相关支持文件
5.1《成品检验标准》
6.相关记录
2/3
盖章
6.1《首件
生产首件确认流程
文件编号: 制订 : 制订日期: 版本 : 页数 :
F1-QC-002 品质部 2014-11-29
首件确认流程

4.2.3 工单变换时; 4.2.4 换版或换材料开始时; 4.2.5 机器故障后再开始生产时;
4.2.6 异常调校时确认。
编
审
核
核准日
制:
批:
准:
期:
深圳市格利特印刷有限公司
文件编 号
版本
A/0
制行日
文件名称
首件确认流程
期
页码 第 2 页共 3 页 4.3 首件检验步骤:
4.3.1 印刷检验重点:将待检验彩纸平放在检验台上,首先对纸张材质、
时,应第一时间停止生产,找其部门组长/主管或 PQC 人员(由工 程或市场人员裁定)进行重新确认和作最后处理决定。 视为无效。如有模糊不清或有疑点,经过确认后方可作业。 4.1.9 各部门整理工艺变更资料,清楚传递变更信息,以利首件确认的核对。 4.2 首件确认的时机 4.2.1 正常工单开始生产时第一张合格品; 4.2.2 人员变换时;
尺寸、规格、纸张纸纹方
向进行核对底色、彩纸啤位尺寸 OK 后,然后按主 体文字图案从左向右逐个区域检查确认,将有异常 处用笔圈起,并知会当班机长改善。对于多模产品 应将其分开逐个核对看颜色是否与样稿一致。 4.3.2 啤机检验重点:①尺寸②对色位③埋口对位是否困难④成型是否 OK ⑤要求刀利、线直、孔圆⑥是否走位、啤错方向或 啤错面底⑦啤机抽取时是否拖花⑧钢板刀痕是否 压花彩盒⑨是否有压痕、爆色、爆线。
生产主管确认
生产主管确认 品质确认
生产大货
生产大货
编制:
品质确认 生产大货
审 批:
生产大货
核准:
品质异常工 单
生产主管确认 机组长确认
工程主管确认
品质主管确认
生产大货
核准日 期: