轮胎结构设计所用计算方法研判.pdf222222
轮胎结构及设计(02)
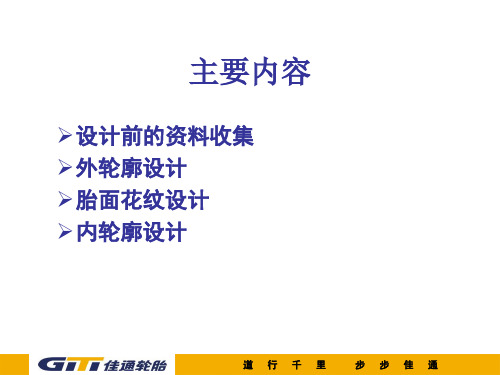
佳
通
模型尺寸的确定
2.5 胎肩轮廓R0、R1 • 圆胎肩 由R0、R1两段圆弧组成,R0=(10—30) mm,R1过P1、P2点。 • 平胎肩 由一段圆弧R1组成,R1过P1、P2点。
道
行
千
里
步
步
佳
通
模型尺寸的确定
2.6 上胎侧轮廓R3 • 一段圆弧R3。 • 两段圆弧R2、R3。 • 一段从P2点开始的切线加圆弧R3组成。 ( R3的圆心在断面水平轴上)
设计参数(层级、气压、负荷及 花纹形式等) 充气前后及使用过程中外缘尺寸 的变化情况 室内试验数据 实际使用中的性能及主要优缺点 使用部门的建议和要求
道 行 千 里 步 步 佳 通
外轮廓设计
轮胎充气后外缘尺寸(D’、B’、C’)的确定 模型尺寸的确定 胎面花纹设计
道
道 行 千 里 步 步 佳 通
花纹沟深度的确定
• • 根据轮胎规格、花纹类型、胎体强度、车辆行 驶速度以及要求达到的行时里程综合考虑选值 要考虑与其它花纹设计参数的比例关系(如花 纹沟的宽度,花纹块面积,花纹节距数等的关 系)
道
行
千
里
步
步
佳
通
花纹沟断面形状的确定
4.1 花纹沟宽度 • 花纹沟宽度是花纹设计的基本参数,由胎面的耐 磨性和抓着力两个因素决定 • 花纹沟的分布要均匀,不能使花纹块大小差异过 大(应控制在20~50%以内),同时花纹块的 宽度不得小于花纹深度的2倍
步
步
佳
通
安全倍数计算
4.3 钢圈安全倍数(钢圈安全倍数:①有内胎: 必须大于5;②无内胎:外直径小于1000mm 的必须大于5,外直径大于1000mm的必须大 于10 ) Sc=2×T×m/(P×sinβ×(Rm2-Rc2)) 其中:T: 钢丝破断力,kg m: 钢丝根数 P: 充气压力,kg/cm2 Rm:断面水平轴半径,mm Rc:轮辋点半径,mm
汽车轮胎的有限元阐述

汽车轮胎的有限元阐述有限元分析法在对汽车轮胎力学结构进行分析之时,使研究工作达到了巅峰的阶段,这一分析方法在应用之时把汽车轮胎看作各向异性连接体,轮胎的构造与材质得到了简易的分析,同时能够将与轮胎相关的信息整体地呈现出来,进而完成对起初轮胎性能推测的目标。
目前有限元分析法在轮胎的充气形状和应力、载荷—位移曲线、接地面积和形状、轮胎的滚动阻力以及侧偏特性等方面都得到了广泛的应用,且取得了良好的应用效果。
1 汽车轮胎结构力学非线性有限元分析1.1 建设有限元汽车轮胎模型众所周知,汽车轮胎在地面运行的状态为滚动,在计算量上应用初始构形会产生很多弊端。
而有限元分析法的使用对轮胎模型进行建设之时有效地应用轮胎滚动构性这一参考构形,此时三维实体单元模拟的组成元素为以下种类:轮胎、轮惘及刚性路面;汽车有限元模型的建立健全,把轮胎运动的形式细化为刚体滚动和纯变形两类;而接触单元模拟成为表示轮胎与地面之间的相互作用的效果;胎面花纹沟被省略的同时细化网络将汽车轮胎接触区域周边的面貌呈现出来;三维超弹性模拟应用在轮胎胎面橡胶上;使用三维复合材料单元模拟的对象主要是胎体帘布层、带束层和冠带层;六面体八节点等参元模拟用于建设汽车轮胎结构;对于以上一切的单元,其均具有变形能力强、高硬度的特征。
1.2 对汽车轮胎承载部件受力情况的分析应用有限元分析法对195/651R489H型号的高速轿车子午线轮胎垂直加载这一工作状况下的结构进行分析。
因为汽车轮胎在垂直载荷的作用下,此时轮胎自体与地表接触时不是轴对称这是必然的结果,那么此时与轮胎相接触的地面区域势必会产生复杂多变的应力,且发生无规则的形变。
有限分析法在应用之时发现在接触底的中心轮胎胎体帘布层无应力产生,而当汽车轮胎与接地中心背离之时胎体帘布层受到了拉应力的作用,并且在接触区域的始末端拉应力的数值是最大的;有限元分析法在对汽车轮胎的带束层进行分析之时,发现其并不是在轮胎接地内、外区域均受到拉应力的作用,在接地区域内部其只受压应力,而产生压应力最大的位置依然是汽车轮胎接地区域的中心,并且轮胎第一带束层接地中心的压应力远远小于第二带束层,在接地区域的其他范围内第一、二带束层所受的压应力值基本一致。
午线轮胎结构设计方法
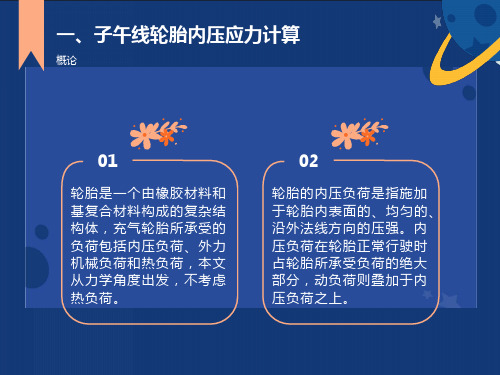
第二节. K值计算的困难与实测之局限
从箍紧系数K的定义式(1)可知,欲求K值,关键在于求得H值。因此,首先应求解无带束子午胎的充气断面形状。以薄膜理论为基础结合余弦法则和网格分析所得到的斜交胎充气平衡轮廓的数学解析式已为人们所熟知: 其中αk为帘线与周向所构成的冠角,当上式外推至αk=90°时有:
1
综上所述,箍紧系数的理论计算困难重重,实际测定又并非良法,不得不另辟蹊径。
2
第三节.无带束子午胎平衡轮廓的一个几何特征
其中:N——胎体帘线总根数;Tc——单根胎体帘线张力;rm——水平轴半径 ;rk——平衡内轮廓胎冠处半径;P——充气内压
02
在分析子午胎的内压应力时,曾依据带束层的实际内压分担率g(s)的分布, 胎体对带束层的支撑宽度bD边缘点D的径向坐标RD建立起轴向力平衡条件:
01
假设3. 充气断面内轮廓曲线形状在变形前后均可用椭圆弧进行描述。
03
假设2:充气断面内轮廓周长在轮胎变形过程中保持不变。
02
第二节 物理分析
先将本文中涉及的一些数值和符号加以说明,见图1。
其中: rk:胎里半径 rc:轮辋点半径 椭圆内轮廓曲线径向半径 椭圆内轮廓曲线横向半径 轮辋半宽 rm:零点半径 R:轮辋点以上椭圆弓形面积形心点半径 RD:支撑带束层的胎体宽度边缘点半径
01
H0:无带束时充气子午线轮胎的断面高度; H´:有带束时充气子午线轮胎的断面高度。
02
箍紧系数是轮胎力学分析中一个比较重要的参数, 从力学角度而言,使用箍紧系数作为函数变量推导出带束内压应力的泛函解析式是相当困难的。
01
针对上述情况,我们作出以下假设:
02
假设1:轮辋点以上的子午线轮胎充气断面内轮廓曲线是一段椭圆弧。
轮胎CAD设计方法

轮胎CAD设计方法学习目的与要求通过学习了解橡胶CAD技术和RCAD轮胎结构设计系统的组成;掌握轮胎RCAD设计方法、设计内容和设计流程;且会运用“轮胎结构设计系统”绘制轮胎外胎花纹总图和材料分布图。
第一节 CAD轮胎结构设计概述一、橡胶CAD技术简介计算机辅助设计(CAD)是指利用计算机来辅助设计人员进行产品和工程的设计,是传统技术与计算机技术的结合。
设计人员通过人机交互操作方式进行产品设计构思和论证,进行产品总体设计、技术设计、相关信息的输出,以及技术文档和有关技术报告的编制。
计算机辅助设计已在很多领域得到广泛应用,如橡胶工业中制品的配方设计、结构设计、模具设计等。
橡胶CAD技术是CAD技术的一个应用领域,特指运用计算机辅助橡胶相关设计人员进行产品和工程设计的技术。
随着计算机性能的迅速提高,计算机在橡胶行业中的应用日益广泛深入。
计算机辅助设计(CAD)是计算机应用的重要领域。
国内已有部分大型橡胶企业建立起较完整的CAD系统,设计开发新产品,提高市场竞争能力。
另外,少数大型企业采用CAD技术后产生的明显的经济效益,对中小企业的影响十分巨大。
它们首先应用计算机和相应的CAD软件组成CAD系统,进行产品的配方设计和工程图纸的绘制,与传统设计方法相比提高了效率。
同时,应用范围也不断扩大,而且逐步深化。
从80年代起,国内一些高等院校和科研机构在橡胶CAD技术领域内进行了大量的研究工作,自行开发了一些实用的CAD软件。
如青岛科技大学开发的“橡胶配方优化设计系统”、“轮胎结构设计系统”等。
目前徐州工业职业技术学院正在应用青岛科技大学开发的“轮胎结构设计系统”。
在实践教学和企业培训上效果显著。
由于计算机技术的引进,大大地促进了设计能力的提高,这种能力的提高,不但体现在工作效率和工作质量方面,更体现在先进的计算机技术对传统的工作方式的促进和变革方面。
但要指出,CAD技术不能代替人们的设计行为,而只是实现这些行为的先进手段和工具,而人们的设计行为,则由专业技术人员的创造能力和工作经验,以及现代设计方法等提供的科学思维方法和实施办法来确定。
第三章 轮胎结构设计(2精品PPT课件

t —胎圈底部倾斜角,度;
r —轮辋底部倾斜角,度。
D.计算实例
以9.00-20轮胎为例,计算钢丝圈所受应力和钢丝 的根数。
• 已知条件:P=657kPa, k Rk=47.9cm,R0=37.25cm, =50.92°
rn=26.67cm,S1=1372kN/根,K=5~7倍
钢圈结构示意图
(a)6层轮胎4-2结构; (b)8层轮胎3-3-2结构 (c)10层轮胎4-4-2结构;(d)12层轮胎4-4-4结构
一般6层以下的轮胎用单钢丝圈,包围方法有2-2结 构和4-2结构;6层以上轮胎用双钢丝圈,包圈方法有33-2,4-4-2,4-4-4,4-4-6,5-5-4,6-6-4等结构;三个钢 丝圈的包圈方法有6-4-4-4结构。
n T K S1
式中 :n—钢丝根数;
S 1—钢丝强度,用于斜底轮辋,或同时可用平底轮辋 和斜底轮辋
计算胎圈所受应力时,应考虑加上胎圈与轮辋过盈配合时因 过盈力而造成的附加应力,以便增加胎圈的钢丝根数,确保胎 圈必要的强度。
计算钢丝圈所受的总应力应等于钢丝圈在内压作用下所受应 力T与轮胎对轮辋过盈力(箍紧力)Tt之和。
可用加大三角胶条,提高帘布反包高度和 增加胎圈宽度等方法,增大下胎侧补强区域, 提高下胎侧的刚性,防止子口折断。补强区 域是以胎圈底部为起点,约在(0.4~ 0.46)H1的范围内,见图2-19所示。
④内轮廓各部位弧度半径
应参照外轮廓相对应部位的弧度半 径;内轮廓冠部和胎侧部弧度半径的圆 心位置与外轮廓对应弧度半径的圆心位 置一致,均设在中心线和水平轴上。胎 肩部内轮廓弧度半径圆心点可自由确定, 但必须与冠、侧部内轮廓弧度均匀相切, 其半径约为40~8Omm,应视轮胎规格 而定。
轮胎结构设计

B 耐磨性较好 周向排列的带束层,加固了胎冠,使轮胎周向不能伸张, 极大的减少了轮胎滚动过程中胎面沿路面的滑移摩擦,显著提 高了胎面的耐磨性和抗机械损伤性能。和普通轮胎比耐磨提高 了30~ 30~70%。 70%。
高分子科学与工程学院
13
§1-2
轮胎的组成及分类
C 抓着性较好 子午线轮胎胎体柔软,下沉量大,胎面与路面接触面积大,接触 压力分布均匀。同时,胎冠刚性大,胎面周向滑移小。所以胎面与路 面抓着性好,比普通胎提高10 ~50%,同时牵引性能和越野性能好,行 面抓着性好,比普通胎提高10~ 50%,同时牵引性能和越野性能好,行 驶安全,通过向好,爬坡性能好。 D 行驶温度低 胎体帘线子午排列,消除了普通结构轮胎交叉排列层间剪切移动。 因此,消耗能量少,生热低。另外,由于胎体帘布层数少,胎测较 薄,也便于散热。所以行驶温度比普通轮胎低30 ~70%。 薄,也便于散热。所以行驶温度比普通轮胎低30~ 70%。 E 使用寿命长 综合寿命比普通轮胎提高50 ~100%,一般路面 10万公里,好路面 万公里,好路面 综合寿命比普通轮胎提高50~ 100%,一般路面10 14万公里,坏路面 7万公里左右。 14万公里,坏路面7 不足:侧向稳定性较差,胎侧易裂口,工艺复杂,造价较高,投资大。 不足:侧向稳定性较差,胎侧易裂口,工艺复杂,造价较高,投资大。
承受车 辆负荷
轮胎的功能及使用性能
功能二.牵引/制动功能:
向路面传递驱动、 制动力
功能三.机动稳定性:
改变 和保 持车 辆行 驶方 向
功能四.行驶舒适性:
吸收来自地 面的震动
高分子科学与工程学院
§1-1
轮胎的功能及使用性能
(1)承受汽车负荷。 (2)和汽车悬架共同缓冲来自路面的冲击,保证汽车有良好 的行使平顺性、舒适性。 (3)为传动驱动力和制动力,提供足够的附着力。 (4)为改变或保持行使方向提供足够的操纵与方向的稳定性。 二、轮胎的使用性能
轮胎的有限元分析

目录摘要IIIAbstract IV1 绪论 11.1 选题的目的和意义 11.2本课题国内外的研究现状 11.3本课题研究内容 12子午线轮胎特点 22.1 子午线轮胎的结构特点 22.2子午线轮胎的结构分析 23子午线轮胎三维整体有限元模型建立 43.1通用软件简介 43.2单元的选取 53.3 轮胎模型的简化 83.3.1模型建立的要求 83.3.2轮胎模型的简化 93.3.3几何建模 94子午线轮胎静态接触的有限元分析 114.1 有限元分析流程 114.2静态接触的载荷和边界条件的处理 124.2.1轮胎有限元模型的三维非线性 124.2.2轮胎单元材料参数的数值 124.2.3轮胎有限元分析的参数化及模型的自动生成 144.2.4 静态接触的载荷和边界条件的处理 184.3轮胎有限元结果分析 194.3.1静态接触载荷工况 194.3.2轮胎在静态接地状况下的有限元结果分析 205 总结与展望 245.1 总结 245.2 不足与展望 245.3 有限元技术在轮胎和车辆工程中应用展望 24参考文献 25基于ANSYS的汽车轮胎有限元分析研究摘要本文主要基于ANSYS软件非线性分析技术,采用三维体单元和接触单元,建立了子午线轮胎的静态接触状态下的有限元模型并对其进行分析研究。
利用CATIA对子午线轮胎进行几何建模,运用ANSYS软件对其进行有限元分析,定义材料属性和单元属性,考虑接触问题,得到适合研究轮胎特性的有限元模型。
根据轮胎结构特征及单元的特征,利用ANSYS的参数设计语言APDL对分析问题进行参数化,提高效率,便于对同类问题的分析研究。
关键词:ANSYS;子午线轮胎;接触变形; CATIA ; APDLANSYS AND RESEARCH OF MOTOR TYRE BASED ON ANSYSAbstractThis paper mainly performs the analysis and research on the radial tyre based on the non-linear analysis of ANSYS and applied software of ANSYS,using three-demension solid element and contacting element , three-dimension finite element contact model of static radial tyre is built.The geometry model of tire is got in CATIA.A finite element model of radial tire is created in ANSYS.Define material characteristics and element types. The contact problem is considered.We got a proper finite element model for studying tire’s characteristic.According to the tyre structural and element charateristic,APDL is applied for research of the analytic problem so as to increase efficiency,so the resembling analysis will be simplified and done easily.Key words: ANSYS ;radial-tyre ;contact- deformation ;CATIA ;APDL1 绪论1.1 选题的目的和意义轮胎作为联结汽车车身与道路的部件,是影响行驶车辆的操纵稳定性、安全性和平顺性的一个关键因素。
第四章 子午线轮胎结构设计(2)22

高速轿车子午胎除钢丝帘线之外;还采用1~2 层尼龙帘线,以增加带束与胎面胶的附着力和箍 紧力。
轿车胎常用的钢丝帘线规格有: 1×4×0.23 1×5×0.23 2+7×0.20+1×0.15 1×4×0.25 1×5×0.25 2+7×0.23+1×0.1 1×4×0.28 2+2×0.28 2+2×0.25
(2)轿车子午线轮胎带束层设计
①带束层材料
作为轿车子午线轮胎带束层材料是比较多的, 有人造丝、玻璃纤维、芳纶(B纤维)、钢丝等,其 中以用钢丝居多,芳纶则很有发展前途,因轻量 化对轮胎是一项很重要的指标。现推广使用的钢 丝帘线结构有:
4×0.25,5×0.25,2+7×0.22+0.15,2+2×0.25/0.28等;发 展的结构有2+2×0.25/0.28,2×0.30HE, 3×0.30HE,2+7×0.22等。
②带束层的层数、角度、密度
纤维带束层:一般为4~6层,角度为13~18°。层间交叉 排列;
钢丝带束层:一般为2层,角度为15~22°。 帘线角度还与轮胎速度级别有关:S级轮胎为24°,H级为
22°,V级为20°。 纤维带束层密度一般为8~14根/cm(据帘线的强度与直径
而定),钢丝带束层密度一般为5~8根/cm(亦据帘线的 强度与直径而定)。帘线密度的选取应考虑其与胶料的粘 合性能。
带束层帘线角度的取值,既要考虑到带束 层对胎体的箍紧系数,又要照顾到便于加工。据 报道带束层角度大于20°,就不能使胎体获得必要 的箍紧效果。但角度太小,不仅使带束层的裁断 和接头等工艺操作复杂化,而且对轮胎的使用性 能不利,容易产生带束层脱层的危险。对子午线 轮胎耐磨性来说,带束层帘线的最宜角度为15~ 20°。但在很大程度上取决于帘线的模量和胶料的 粘附强度,且与轮胎规格有关。
- 1、下载文档前请自行甄别文档内容的完整性,平台不提供额外的编辑、内容补充、找答案等附加服务。
- 2、"仅部分预览"的文档,不可在线预览部分如存在完整性等问题,可反馈申请退款(可完整预览的文档不适用该条件!)。
- 3、如文档侵犯您的权益,请联系客服反馈,我们会尽快为您处理(人工客服工作时间:9:00-18:30)。
作者简介:胡立平(1960—),男,黑龙江林口县人,哈尔滨工业大学(威海)汽车工程学院轮胎研究所顾问,高级工程师,主要从事轮胎结构设计理论研究和CAD软件开发工作。
轮胎结构设计所用计算方法研判胡立平(黑龙江省牡丹江市太平路西菜园街牡丹江书画院综合楼 157000) 摘要:简要论述了对轮胎结构设计中所用计算方法的正确性进行研判的基本方法,指出实验验证和逻辑证明是两种有效的基本手段;强调了实验验证方法对优化试验设计方法的倚重,即对逻辑分析的依赖性;阐明了逻辑证明方法的重要性、实用性和经济高效性;重点推介了几种常用的逻辑检验方法,并针对性地给出了具体应用实例剖析。
关键词:轮胎;结构设计;计算方法;实验证明;逻辑证明 中图分类号:TQ336.1+1 文献标志码:B 文章编号:1006-8171(2013)06-0334-04 不适宜的计算方法是产品设计过程中必须防范的,本文讨论对计算方法正确与否的常规鉴别手段。
1 实验验证实验验证是最基本的,也是最传统的方法。
原则上,在轮胎结构设计中采用的所有计算方法的正确性都必须能够经受严格的试验证明。
1.1 常用的实验方法众所周知,实验科学是现代科学发展最快的领域之一,而通过实验来验证轮胎结构设计中所用计算方法的准确性,最常用的采集数据方法仍然是直接测量法,但包括无损内部测量等间接测量法的发展更快,应用也越来越多。
传统的测量手段因简单有效仍被大量使用,而光学方法,埋入式应力、应变、温度传感器以及超声波、X光、核磁共振等方法的应用则为更全面地测量轮胎的受力、变形或位移以及振动、发声、生热等创造了可能性和更多的选择途径。
1.2 优化试验设计方法验证试验必须科学、严谨、可靠,因此原则上需要进行一系列的实验来检验计算方法在各种可能条件下的计算结果的准确性,才能获得正确的研判结论。
而对所有可能条件下的计算结果都进行实验验证往往相当困难甚至是不可能完成的,因此掌握一定的优化试验设计方法是十分必要的,例如正交试验法、优选法、均匀性试验法等,科学地安排验证试验的内容和数量,才能以最少的人力和物力消耗在最短的时间内获得充分必要的试验数据,为研判结论提供可靠的支持。
显而易见,试验方案的优劣不只取决于方案中试验的数量,还取决于其相互逻辑关系。
2 逻辑证明逻辑推理是人类探索未知世界的利器,也是检验真理的常用手段。
逻辑证明甚至还能用于一些实验验证无法检验的对象,而用于计算方法或计算公式的研判有时也更具优势,可节省大量人力、物力和时间等,因而更经济高效。
下面讨论几种最常用的逻辑检验方法。
2.1 公理推断法公理推断法是最直接的逻辑证明方法,直接用定理及其推论进行推导证明。
这种方法特别适用于数理模型及其导出的计算公式的证明,例如拉普拉斯方程、薄膜网络理论及其导出的平衡轮廓公式以及胎体帘线和钢丝圈的应力计算公式、有限元算法模型等。
2.2 演算推导法从已知的论点或公式出发,通过计算推导过程得出研判结论,广义上也属于公理推断法。
相对于较为抽象的证明过程,其简洁清晰的演算步骤更容易被理解接受,因此在工程技术中的应用更为广泛。
例如对轮胎胎圈的过盈箍紧张力的计433轮 胎 工 业 2013年第33卷第6期算,国内绝大部分轮胎企业的设计人员都是采用《橡胶工业手册》修订版轮胎分册所推荐的计算公式[1]:Tt=Ebrδr/(2t)(1)式中,Tt为胎圈的过盈箍紧张力;E为胎圈底部材料平均弹性模量,一般为30~50MPa;b为胎圈宽度;r为胎圈平均半径;t为胎圈底部材料厚度;δr为胎圈对轮辋的过盈箍紧量。
δr按下式计算:δr=dr-dt+2a(tanαt-tanαr)(2)式中,dr为轮辋标定直径,dt为胎圈着合直径,a为轮辋边缘到胎圈中心的距离,αt为胎圈底部倾斜角度,αr为轮辋底部倾斜角度。
但式(1)的计算结果往往大大低于实际值。
实际上我国轮胎企业低估胎圈张力的情况较普遍,导致水压爆破试验的结果经常达不到胎圈安全倍数的设计值。
当然导致胎圈张力理论值被低估的因素很多,过盈箍紧张力被低估只是其中的原因之一[2]。
下面采用演算推导法找出其算法的问题所在。
式(1)源于环绕材料的张力等于圆环半径与径向支撑强力的乘积,对于胎圈:Tt=rF(3)式中,F为径向支撑强力,根据式(1)则有F=Ebδr/(2t)(4) 式(3)中只有两项参数,r的物理意义明确,因此Tt与F正相关。
考察F的计算,式(4)可以写成虎克定律的形式:F=E′ε(5)式中,E′为胎圈底部材料根据受力全宽度计算的表观弹性模量,ε为胎圈底部材料的径向压缩应变。
E′=Eb(6)ε=δr/(2t)(7) 检查式(1)~(7)及相关的计算过程,可以发现b,r,δr,t,dr,dt,a,αt,αr和ε等各参数的设定和计算都无懈可击,仅剩E′和E存疑;而E′与E在此例中的关系也经得起推敲,于是最后仅剩的疑点就落在了E上。
常规条件下的E被用到不适当的场合而导致出现问题。
下面对此予以剖析。
橡胶-帘线复合材料常规条件下受到一维压缩时会在另外两个维度有所伸张,式(1)中采用的E所表征的就是此种情况下的材料属性。
但在胎圈与轮辋配合体系中,胎圈底部材料在轮辋着合处的受力变形则截然不同:其受力状态显然不属于简单的一维压缩,因其在另外两个维度的伸张受到限制,其中周向完全受限成为封闭空间不可伸张,而横向因胎圈与轮缘接触一侧受到内压作用而使伸张部分受限。
因此其实际压缩模量不仅不可能等于相应的平面层合材料自由压缩模量的理论值或测试值,而且要大得多,可以达到数量级的差别。
显然如果要通过试验测试得到可用于式(1)的E,则测试条件必须符合胎圈与轮辋的实际配合情况。
如果忽略边际效应,通过理论计算可得胎圈底部材料的压缩弹性模量基本相当于其横向(即经向,帘线纵向方向)的伸张模量,显然与式(1)推荐的E可以有好几个数量级的差别。
但由于胎圈底部材料宽度很小,边际效应对表观压缩模量影响巨大,且胎圈越窄,边际效应影响越大,实际计算中必须予以考虑。
2.3 因子分析法因子分析法为逐一分析公式中的各个变量与目标函数的逻辑关系以研判其合理性的方法。
对于经验公式以及未知其属性来源的计算公式,虽然不能直接推导证明,但仍可以秉承逻辑推导的理念检验其内部的逻辑关系,这便是因子分析方法的实质,与公理推断法的精髓相通。
如果发现存在逻辑上的矛盾,则可判定该公式存在错误,反之如果相关因子都能够自洽,则可初步确认该公式在逻辑上的正确性,但其准确性还需通过辅助试验进一步确认,此时辅助试验一般用来检验公式中相关常数的可靠性。
下面用一个简单的实例剖析进一步说明。
一些专业文献曾推荐一个计算轮胎钢丝圈的内压张力(T)的经验公式:T=Psinα(R2m-R2d)/2(8)式中,P为轮胎充气压力,α为胎体张力作用于钢丝圈的方向与水平方向的夹角,Rm为水平轴半径,Rd为钢丝圈半径。
533胡立平.轮胎结构设计所用计算方法研判式(8)被一些国际大型轮胎企业列入设计规范作为可以选用的计算公式,是值得商榷的。
从式(8)可以看出,其结构与广泛应用的由充气平衡轮廓导出的计算钢丝圈内压张力的公式很相似:T=P(R2k-R2m)/2(9)式中,Rk为胎体帘布胎冠顶点半径。
但式(8)中没有对钢丝圈张力影响巨大的参数Rk,而括弧项也由式(9)中的胎体帘布顶点半径与水平轴半径的平方差换成了水平轴半径与钢丝圈半径的平方差,此外还比公式(9)增加了一项校正因子sinα。
对式(8)进行因子分析可以发现,R2m与T呈正相关,即在其他条件不变的情况下,水平轴越高,钢丝圈张力越大,显然与力学分析的结论相悖,产生逻辑矛盾,可以判断式(8)是不恰当的。
其实式(8)中由于缺少了Rk的效应,已经暴露了其缺陷,而且其中sinα项的实际作用也是有问题的,当然其正确与否都已不影响判定结论。
还有与此例极为类似的计算钢丝圈张力的经验公式,只是将式(8)中的Rd换成了轮辋点半径(Rc),当然同样也是不恰当的计算公式。
虽然用因子分析法证明式(8)的不恰当相当简单,但剖析其在实际应用中的迷惑性却别具意义。
因为首先式(8)和(9)的计算结果处于同一数量级,相差不是特别大,因此相对容易被工程技术人员接受;其次是我国轮胎行业内仍然比较流行用轮胎的设计结构参数代替充气平衡状态的结构参数来计算各种应力,从而使按照式(9)计算的钢丝圈张力也会产生误差;而且尤其需要强调的是,当采用设计结构参数代替充气平衡状态的结构参数来计算钢丝圈张力时,不仅使计算精度下降而且极易产生受设计者主观意向影响的有倾向性的计算误差,例如常见一些产品设计说明书中有“为了降低子午线轮胎胎圈部位所受应力,Rm取值大一些”等诸如此类的说明,从而使按照式(9)计算钢丝圈张力的结果变小,人为地导致计算结果偏低,而此时按照式(8)计算的相应结果则会随Rm值的提高而变大,导致偶尔也会在一定程度上缩小计算误差;这大概也是不恰当的式(8)也会被认可的原因之一。
2.4 交互认证法交互认证法是对同一命题采用不同的算法求解,对算法进行交互认证的方法。
例如对所质疑的计算公式,如果还有其他适用于同一领域的经验公式等,则可用它们对同一命题进行计算,通过结果分析实现交互认证。
例如采用不同的单元结构和网格划分形式进行有限元计算,以验证其解的收敛性和稳定性。
2.5 用解析解验证近似计算结果的方法虽然在实际工作中原则上凡是能够求得解析解的地方就不需要也不应该采用近似计算方法计算,但在研究工作中则不失为一种有效的鉴定近似计算方法可靠性的手段。
例如,轮胎充气平衡轮廓的解析解以及垂直静负荷下的解析解都可以用来验证有限元方法计算的静态分析结果的可靠性。
当然对于更复杂的情况,例如轮胎的非对称受力变形以及动态的应力应变场和温度场的分析等,由于难以求得解析解而只能采用有限元方法进行近似模拟分析,因此也就谈不上用解析解验证,此时可采用第2.4节所述方法验证其解的收敛性和稳定性,再辅之以实验验证方法确定其算法的可靠性。
3 结语实验验证和逻辑证明是研判计算方法正确与否的两种基本手段,二者各自独立又相互关联。
实验验证历来是研判计算方法正确性的重要方法,未来也仍然具有不可替代的重要性。
而要提高其研判效果和效率,则必须注重对试验内容、方法和过程的逻辑分析,即掌握优化试验方法的运用。
逻辑证明也是研判计算方法正确与否的重要方法之一,因为逻辑推理也是检验真理的有效手段,而且往往更经济、高效。
逻辑证明所用的定理和定律大多来源于以往大量实践经验的提炼,因此两种研判方法存在天然的相互联系。
根据具体情况,既可以采用一种方法进行研判,也可以两种方法联合使用。
取舍的依据为保证研判获得正确结论并使研判过程的成本最低。
参考文献:[1]梁守智,钟延壎,张丹秋,等.橡胶工业手册第四分册轮胎633轮 胎 工 业 2013年第33卷第6期[M].修订版.北京:化学工业出版社,1989:403.[2]胡立平,张薇.轮胎结构设计中常见的计算结果与实测值偏差较大现象的原因分析[J].轮胎工业,2013,33(1):54-60.第17届中国轮胎技术研讨会论文Assessment of Calculation Method Used in Tire Structure DesignHU Li-ping(Mudanjiang Shuhuayuan Building,Taiping Road,Caiyuan Street,Mudanjiang 157000,China)Abstract:The basic method to estimate the correctness of the calculation method used in tirestructure design was discussed,which pointed out the experimental verification and logic proof weretwo effective basic approaches.It was emphasized that the experimental verification method was basedon the optimal design of test method,namely depending on the logic analysis.The importance,practica-bility and economic efficiency of the logical proof method were demonstrated.Several commonly usedlogic test methods were then recommended with specific examples.Key words:tire;structure design;calculation method;experimental verification;logical proof普利司通“推进”费尔斯通载重轮胎中图分类号:TQ336.1 文献标志码:D美国《现代轮胎经销商》(www.moderntire-dealer.com)2013年3月21日报道:2013年3月21—23日在美国中部肯塔基州的路易斯维尔展览中心举办的载重汽车展(简称MATS)上,普利司通商业解决方案公司推出“Those With Drive,Drive a Firestone”活动。