四氯化钛精制车间设计
四氯化钛生产车间工艺

储矿备料1、基本原理外购的石油焦和氯化钠含有的水分会造成对产品的影响,根据原料的水分要求对石油焦和氯化钠进行微波干燥,通过烘烤物料,蒸发水分,使石油焦和氯化钠含水≤0.5%。
2、工艺流程氯化工艺1、基本原理熔盐氯化是固体含钛物料与气体氯气在介质熔盐里温度为720-800оC的反应。
氯化反应目的是使TiO2最大程度氯化,TiO2的氯化速率取决于多种因素,例如温度,氧化物的活性,还原剂及氯化剂的类型,熔盐的物理特性和成分(表面X力、黏度、润湿性)。
参与氯化反应组分的催化性能。
熔盐氯化主要反应方程式如下:TiO2+C+2Cl2====TiCl4+CO2铁,铝,锰,铬的氧化物在和氯气反应后生成的氯化物极易溶解在熔盐中,作为氯化反应的催化剂。
在氯化熔盐中,这些氯化物适宜的浓度能增加熔盐的活性,能提高高钛渣的氯化速率。
氯气浓度对氯化反应有很大影响,入炉氯气浓度一般在80%到90%(vol.),其余为空气。
氯化反应的温度通过从淋洗循环槽返回的泥浆量调整氯化炉温度。
放热反应产生的多余热量蒸发了返炉泥浆中的四氯化钛,然后四氯化钛就和混合炉气一起进入冷凝系统。
生产粗四氯化钛是升华和冷凝的过程。
冷凝是改变物质的物理状态,从气相变为液相,而升华是没有经过中间的液相,直接从固相转变为气相,这些过程均伴随着热损失。
混合炉气从气相转变为液相或固相的温度取决于混合炉气中各种物质的蒸汽分压。
氯化工序的产品是粗四氯化钛,首先冷凝高沸点氯化物,然后冷凝四氯化钛及低沸点氯化物。
2、工艺流程粗四氯化钛工艺流程图粗四氯化钛3、主要生产过程及技术参数外购的NaCl和石油焦(含水量都为1%),人工开袋后送入各自料仓,经微波干燥后(含水量都变为0.5%)皮带输送到斗式提升机,再由斗式提升机送到各自干燥后料仓,然后由埋刮板输送机送到氯化工段的氯化钠仓和煅后焦仓;外购和自产的高钛渣,人工开袋后送入高钛渣料仓,经埋刮板输送机送到斗式提升机,再由斗式提升机送到高钛渣干燥后料仓,然后由埋刮板输送机送到氯化工段的高钛渣仓。
沸腾氯化生产四氯化钛工艺技术

沸腾氯化生产四氯化钛工艺技术沸腾氯化生产四氯化钛工艺技术沸腾氯化生产四氯化钛是一种常用的工业化学反应,被广泛应用于冶金、化工、材料等领域。
该工艺技术以钛精矿为原料,经过氯化、还原、蒸馏等多道工序,最终制得四氯化钛,其技术难度较高,需要严格的工艺控制,下面将从原料、反应原理、工艺流程、工艺控制和优化等方面介绍沸腾氯化制备四氯化钛的工艺技术。
一、原料沸腾氯化制备四氯化钛的原料是钛精矿。
钛矿是指含有三氧化二钛(TiO2)的天然矿物,常见的矿物有金红石、铁钛矿、钛铁矿等,其中以钛铁矿是一种重要的原料。
钛精矿中含有杂质,主要有铁、钒、锰、铜、铅、锡、锑、硅、钾等,这些杂质会影响到生产的品质和成本。
二、反应原理反应原理如下所示:TiO2+2Cl2+C=TiCl4+CO2三、工艺流程沸腾氯化生产四氯化钛的工艺流程如下:将钛精矿加入氯化锂和碳之中,经过加热反应产生TiCl4和CO2,然后再将产生的气体放入到反应釜中,采用沸腾氯化的方法进行反应,生成纯度高的四氯化钛。
在加热反应时,需要控制温度和加热速率,以免铁、钒等杂质造成污染。
在沸腾氯化反应时,需要控制反应速率和温度,以免产生杂质和产物的挥发损失。
四、工艺控制和优化沸腾氯化制备四氯化钛的过程涉及到多道反应和多步操作,因此要严格控制每一步操作的温度、压力和物料加料方法。
此外,对于工艺中产生的副产品和废气需要进行处理和回收利用,以提高资源利用率。
为了提高反应速率和增加四氯化钛产量,可以采用催化剂辅助反应。
此外,还可以采用流化床反应器等新型反应器,以提高反应效率和控制反应体系。
总之,沸腾氯化生产四氯化钛的工艺技术具有较高的难度,需要在嚴格控制反應過程的溫度、氣壓、加料方法等方面下,采用催化剂辅助反应、废气和副产品回收利用、采用新型反应器等措施进行工艺优化,才能保证产物的高纯度和高质量,提高生产效率和降低成本。
为了更好地了解沸腾氯化生产四氯化钛的工艺技术,需要对相关的数据进行分析。
四氯化钛毕业设计

摘要:四氯化钛的生产过程主要是由配料、氯化和精制三部分组成,氯化工艺主要有沸腾氯化、熔盐氯化和竖炉氯化三种方法。
沸腾氯化是现行生产四氯化钛的主要方法(中国、日本、美国采用),其次是熔盐氯化(独联体国家采用),而竖炉氯化已被淘汰。
沸腾氯化一般是以钙镁含量低的高品位富钛料为原料,沸腾氯化就是是高太渣和石油焦按3:1的比例混合与氯气处于流态化得状态下进行氯化。
关键词:沸腾氯化精制检验Abstract:The production process is mainly composed of ingredients, chlorinated and refined three parts, chlorination process, main boiling salt chlorinated and chlorinated shaft furnace chlorinated three methods. The production is boiling chlorinated four methods of titanium chloride (China, Japan, the United States), followed by melting chloride (salt), and the commonwealth countries adopt shaft furnace has been eliminated. Chloride, Boiling chlorinated generally low levels of calcium and magnesium in high-grade raw materials for the rich titanium, boiling chlorinated is too high and the proportion of petroleum coke mixed with 3 according to the chlorine in fluidized state under chloride.Keywords: Boiling chloride refine inspection目录第一章:总论1.1 设计任务和内容```````````````````````````````````(3) 1.2 生产方法及反应原理```````````````````````````````(3) 1.3 三废治理和环境保护```````````````````````````````(5) 1.4 设计依据和指导思想```````````````````````````````(7) 第二章:工艺设计2.1 概述工艺流程````````````````````````````````````(7) 2.2 设计生产能力产品方案及质量指标``````````````````(8) 2.3 原材料消耗及规格````````````````````````````````(12) 2.4 主要工艺参数````````````````````````````````````(13) 2.5 物料衡算````````````````````````````````````````(13) 2.6 工艺设备及设备一览表````````````````````````````(15) 2.7 工艺流程说明````````````````````````````````````(16) 2.8 原料、半成品、成品的化验````````````````````````(17) 第三章:四氯化钛生产工艺的新技术动态和发展趋势3.1 中国四氯化2.1```````````````````````````````````(21) 3.2 四氯化钛行业市场`````````````````````````````````(23) 3.3 对中国钛行业建议`````````````````````````````````(24) 3.4 环境和安全```````````````````````````````````````(25) 3.5 高品位富钛料的制造技术```````````````````````````(26) 3.6 四氯化钛除钒新工艺```````````````````````````````(26)3.7 生产过程的自动控制和管理`````````````````````````(27) 3.8 工艺流程图及主要设备图```````````````````````````(27) 3.9 参考文献`````````````````````````````````````````(27)第一章:总论世界钛主要生产国按产能从大到小排列依次为:美国、独联体、日本和中国,欧洲只有少量生产。
四氯化钛生产流程及注意事项

四氯化钛生产流程及注意事项5.1 一般规定5.1.1 氯化工序和精制工序宜设置于同一建筑物内。
5.1.2 生产与卫生排气应分开设置废气处理系统。
氯化和精制可共用废气处理系统。
5.1.3 四氯化钛生产系统内设备、构筑物、地面和地沟表面应进行防腐处理。
5.1.4 四氯化钛生产系统内应根据设备的维修情况设置起吊装置。
维修点附近宜设置集气装置。
5.1.5 四氯化钛生产系统宜设置设备清洗室和干燥室。
5.1.6 四氯化钛生产系统内的储存和管道应设排净阀口。
管道坡度应大于等于1%。
5.1.7 四氯化钛系统应设置事故倒运储槽,容量应满足系统内最大容器的容量,并应设置于系统内的最低位置。
5.1.8 四氯化钛生产系统建筑物宜采用敞开式厂房。
5.1.9 四氯化钛生产作业区域内必须设置冲洗装置、洗眼器和Cl2、HCl、CO浓度检测报警装置。
5.1.10 四氯化钛储罐区应设置围堰。
5.1.11 四氯化钛生产现场应设置存放应急用石灰的区域。
5.1.12 四氯化钛生产区域每层楼宜配置一台移动式轴流风机。
5.1.13生产和贮存四氯化钛的设备必须设置压力平衡系统,排放的废气应接入废气处理系统。
5.1.14 粗四氯化钛生产与精四氯化钛的压力平衡系统应分开设置。
5.1.15 钛冶炼厂氯化工序应备用一台氯化炉或一套氯化系统。
5.1.16 四氯化钛生产采用的还原剂和富钛料含水量高于0.5%时应设干燥设施。
5.1.17 还原剂宜直接外购合格粒度的产品。
5.1.18 粗四氯化钛的贮存、输送、管路材质可选择碳钢,精四氯化钛贮存、输送、管路材质宜采用不锈钢。
5.1.19 粗四氯化钛储存隔离气体宜采用氮气,精四氯化钛储存隔离气体应采用氩气。
5.2氯化5.2.1 氯化工艺有熔盐氯化和沸腾氯化两种,氯化工艺应按下列条件确定:1.富钛料的成分和杂质含量。
富钛料TiO2含量大于86%,钙、镁氧化物总量低于2%,宜采用沸腾氯化工艺;钙、镁氧化物总量大于2%,宜采用熔盐氯化工艺;采用熔盐氯化工艺,TiO2含量宜大于74%。
粗四氯化钛的精制

ⅲ)失效铜丝的再生洗涤的操作麻烦,劳动强度 大,劳动条件差,并产生含铜废水污染,也不便 于从中回收钒,除钒成本高。
所以,铜丝除钒法仅适合于处理含钒量低的原 料和小规模生产海绵钛厂使用。
(2)冷冻结晶法除钒
TiCl4-VOCl3 系 两 组 分 凝 固 点 差 异 较 大 , 约 相 差 54℃,因此也可采用冷冻结晶法除VOCl3,但冷冻消耗 的能量很大,故也未获得工业应用。
14
2.化学法除钒
化学除钒的实质: (ⅰ)选择性还原或选择性沉淀
在粗TiCl4中加入一 种化学试剂,使VOCl3(或VCl4)杂 质生成难溶的钒化合物和TiCl4相互分离。
16
③除铝的方法
一般是将用水增湿的食盐或活性炭加入TiCl4中进行处理, AlCl3与水反应生成AlOCl沉淀:
AlCl3+H2O=AlOCl +2HCl
加入的水也可以使TiCl4发生部分水解生成TiOCl2:
TiCl4+H2O=TiOCl2+2HCl
有 AlCl3存在时,可将TiOCl2重新转化为TiCl4:
(ⅱ)选择性吸附
选择吸附剂,选择性吸附VOCl3(或VCl4),使钒杂质和 TiCl4相互分离。
15
(1) 铜除钒法 ① 原理 以铜作还原剂,将VOCl3选择性还原为VOCl2, 生成的VOCl2是沸点较高又不溶于TiCl4的固体物质, 它粘附在金属铜上,从而与TiCl4分离。
VOCl3 + Cu → VOCl2↓ + 1/2Cu2Cl2 ② AlCl3对除钒效果影响 当 AlCl3在TiCl4中的浓度大于0.01%时,则会 使铜表面钝化,阻碍除钒反应的进行。所以,当粗 TiCl4中的AlCl3浓度较高时,一般要在除钒之前进 行除铝。
四氯化钛精制车间设计
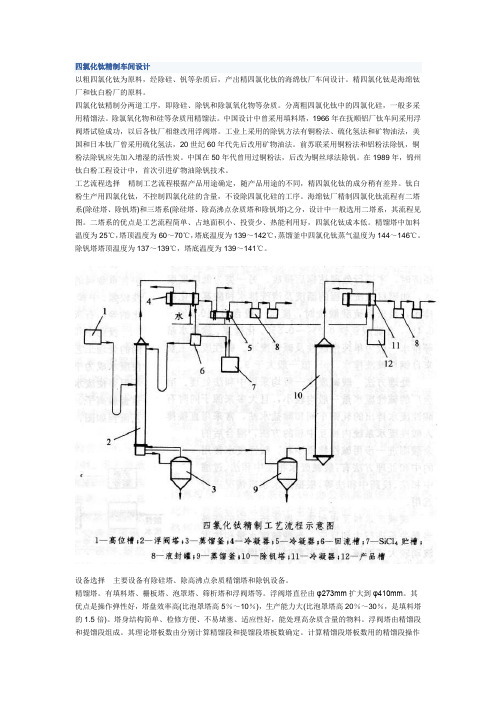
四氯化钛精制车间设计以粗四氯化钛为原料,经除硅、钒等杂质后,产出精四氯化钛的海绵钛厂车间设计。
精四氯化钛是海绵钛厂和钛白粉厂的原料。
四氯化钛精制分两道工序,即除硅、除钒和除氯氧化物等杂质。
分离粗四氯化钛中的四氯化硅,一般多采用精馏法。
除氯氧化物和硅等杂质用精馏法。
中国设计中曾采用填料塔,1966年在抚顺铝厂钛车间采用浮阀塔试验成功,以后各钛厂相继改用浮阀塔。
工业上采用的除钒方法有铜粉法、硫化氢法和矿物油法,美国和日本钛厂曾采用硫化氢法,20世纪60年代先后改用矿物油法。
前苏联采用铜粉法和铝粉法除钒,铜粉法除钒应先加入增湿的活性炭。
中国在50年代曾用过铜粉法,后改为铜丝球法除钒。
在1989年,锦州钛白粉工程设计中,首次引进矿物油除钒技术。
工艺流程选择精制工艺流程根据产品用途确定,随产品用途的不同,精四氯化钛的成分稍有差异。
钛白粉生产用四氯化钛,不控制四氯化硅的含量,不设除四氯化硅的工序。
海绵钛厂精制四氯化钛流程有二塔系(除硅塔、除钒塔)和三塔系(除硅塔、除高沸点杂质塔和除钒塔)之分,设计中一般选用二塔系,其流程见图。
二塔系的优点是工艺流程简单、占地面积小、投资少、热能利用好,四氯化钛成本低。
精馏塔中加料温度为25℃,塔顶温度为60~70℃,塔底温度为139~142℃,蒸馏釜中四氯化钛蒸气温度为144~146℃。
除钒塔塔顶温度为137~139℃,塔底温度为139~141℃。
设备选择主要设备有除硅塔、除高沸点杂质精馏塔和除钒设备。
精馏塔。
有填料塔、栅板塔、泡罩塔、筛析塔和浮阀塔等。
浮阀塔直径由φ273mm扩大到φ410mm。
其优点是操作弹性好,塔盘效率高(比泡罩塔高5%~10%),生产能力大(比泡罩塔高20%~30%,是填料塔的1.5倍)。
塔身结构简单、检修方便、不易堵塞、适应性好,能处理高杂质含量的物料。
浮阀塔由精馏段和提馏段组成。
其理论塔板数由分别计算精馏段和提馏段塔板数确定。
计算精馏段塔板数用的精馏段操作方程式为:式中n为塔板数;Yn+1,为n+1层塔板上汽相中SiCl4分子浓度百分数;Xn为塔内n层塔板液相中SiCl4的分子浓度百分数;R为回流比;Xp为塔顶馏出物中SiCl4的分子浓度百分数。
粗四氯化钛制备流程

第二章粗四氯化钛的生产1. 功能氯化车间是进行粗四氯化钛的生产。
粗四氯化钛的生产是15000吨/年海绵钛生产线的一个组成部分。
采用带组合式冷凝系统的熔盐氯化炉来生产粗四氯化钛(CТТ)。
粗四氯化钛的生产能力将不低于68500吨/年。
氯化车间厂房是一座多用途的建筑物,除用作四氯化钛生产外,还用于四氯化钛的精制、粗四氯化钛和精四氯化钛的储存。
2.氯化车间物料平衡3、生产工艺3.1主要设备:粗四氯化钛(CТТ)生产所需的生产线和运输设备包括:炉前料仓;混合炉料配料设备和将炉料输送到氯化炉的加料仓的管式输送机;熔盐氯化炉,粗四氯化钛生产能力:80-100吨/天两个可互换的收尘室;两个喷淋洗涤器,与一个循环矿浆罐和一个冷却器相互连接;两个喷淋冷凝器,与一个喷淋罐、一个冷却器和一个捕集器相互连接;两个尾气风机沉降槽,储罐。
3.2粗四氯化钛生产工艺包括如下几个阶段:∙所需原料的接收和氯化炉料的准备;∙氯化∙从气体混合物中收尘以去除氯化升华物∙气体混合物(VGM)的冷凝∙粗四氯化钛冷凝物的沉降∙对从气体混合物中分离的氯化升华物的清洗氯化车间有三条CTT生产线(两用一备,当某条运行生产线由于大修而停车时,备用生产线投入使用)。
3.2.1氯化将粉碎的钛渣、石油焦和NaCl按照一定的比例配制成混合炉料,炉料从配料料仓通过给料螺旋以适当的速度加入到氯化炉中。
混合炉料在700-800︒С温度下和氯化物的熔化环境中,与氯气相互作用形成钛、铁、铝等的氯化物。
反应体系的温度通过反应释放出的热量和四氯化钛循环矿浆蒸发吸热来保持。
反应的主要产物以蒸汽-气体形态从氯化炉输送往收尘和冷凝设备系统。
当氯气通入氯化炉熔盐层时会强烈搅动熔盐,同时入炉氯气被加热并分散在熔盐介质中,并使从熔盐界面上部加入到炉内的高钛渣和石油焦固体混合料充分地分散在熔盐中,氯化炉内主要反应为:TiO2+C+2Cl2 700-800℃TiCl4+CO2TiO2+2C+2Cl2 700-800℃ TiCl4+2COTiO2+2CO+Cl2 700-800℃ TiCl4+2CO2根据氯气的流速来调节氯化炉进料速度,矿浆返回氯化炉的速度根据熔体温度进行调节,氯气的进气压力控制在0.1-0.15Mpa。
- 1、下载文档前请自行甄别文档内容的完整性,平台不提供额外的编辑、内容补充、找答案等附加服务。
- 2、"仅部分预览"的文档,不可在线预览部分如存在完整性等问题,可反馈申请退款(可完整预览的文档不适用该条件!)。
- 3、如文档侵犯您的权益,请联系客服反馈,我们会尽快为您处理(人工客服工作时间:9:00-18:30)。
四氯化钛精制车间设计以粗四氯化钛为原料,经除硅、钒等杂质后,产出精四氯化钛的海绵钛厂车间设计。
精四氯化钛是海绵钛厂和钛白粉厂的原料。
四氯化钛精制分两道工序,即除硅、除钒和除氯氧化物等杂质。
分离粗四氯化钛中的四氯化硅,一般多采用精馏法。
除氯氧化物和硅等杂质用精馏法。
中国设计中曾采用填料塔,1966年在抚顺铝厂钛车间采用浮阀塔试验成功,以后各钛厂相继改用浮阀塔。
工业上采用的除钒方法有铜粉法、硫化氢法和矿物油法,美国和日本钛厂曾采用硫化氢法,20世纪60年代先后改用矿物油法。
前苏联采用铜粉法和铝粉法除钒,铜粉法除钒应先加入增湿的活性炭。
中国在50年代曾用过铜粉法,后改为铜丝球法除钒。
在1989年,锦州钛白粉工程设计中,首次引进矿物油除钒技术。
工艺流程选择精制工艺流程根据产品用途确定,随产品用途的不同,精四氯化钛的成分稍有差异。
钛白粉生产用四氯化钛,不控制四氯化硅的含量,不设除四氯化硅的工序。
海绵钛厂精制四氯化钛流程有二塔系(除硅塔、除钒塔)和三塔系(除硅塔、除高沸点杂质塔和除钒塔)之分,设计中一般选用二塔系,其流程见图。
二塔系的优点是工艺流程简单、占地面积小、投资少、热能利用好,四氯化钛成本低。
精馏塔中加料温度为25℃,塔顶温度为60~70℃,塔底温度为139~142℃,蒸馏釜中四氯化钛蒸气温度为144~146℃。
除钒塔塔顶温度为137~139℃,塔底温度为139~141℃。
设备选择主要设备有除硅塔、除高沸点杂质精馏塔和除钒设备。
精馏塔。
有填料塔、栅板塔、泡罩塔、筛析塔和浮阀塔等。
浮阀塔直径由φ273mm扩大到φ410mm。
其优点是操作弹性好,塔盘效率高(比泡罩塔高5%~10%),生产能力大(比泡罩塔高20%~30%,是填料塔的1.5倍)。
塔身结构简单、检修方便、不易堵塞、适应性好,能处理高杂质含量的物料。
浮阀塔由精馏段和提馏段组成。
其理论塔板数由分别计算精馏段和提馏段塔板数确定。
计算精馏段塔板数用的精馏段操作方程式为:式中n为塔板数;Yn+1,为n+1层塔板上汽相中SiCl4分子浓度百分数;Xn为塔内n层塔板液相中SiCl4的分子浓度百分数;R为回流比;Xp为塔顶馏出物中SiCl4的分子浓度百分数。
Y与X的平衡方程式为:式中α为平均相对挥发度。
以上二式联立,可求得Xn、Yn之值,当Xn<Xf时,第n块理论塔板为加料板。
Xf为原料液相粗TiCl4中低沸点物的含量,分子浓度百分数。
提馏段塔板数:提馏段方程Yn=ƒ(Xn)与平衡方程(2)联立可得Xn,当Xn<Xw时即可满足要求;Xw为塔底流出物中低沸点物的克分子浓度百分数。
实际塔板数按下式确定:精馏段实际塔板数:提馏段实际塔板数:式中n为提馏段的塔板数:0.4为精馏段塔板效率;0.3为提馏段塔板效率。
除钒设备有矿物油除钒系统和铜丝球塔等。
铜丝球塔优点是设备结构简单(内装φ2mm紫铜丝绕成的φ100~150mm的铜丝球),操作方便。
但铜的价格高、供应困难、生产操作不能连续化。
车间配置与技术要求仪表控制室配置在生产操作较集中处,各生产设备按工艺流程方向配置;塔顶冷凝系统设备可考虑露天配置。
生产系统的设施要求严格密闭,设备及管道检修完毕,必须干燥后方可组装。
车间内应设有设备干燥室。
为保证产品质量,浮阀塔系统后面的设备及管道采用不锈钢制作。
主要技术指标粗四氯化钛的质量要求见富钛料氯化车间设计,精四氯化钛的质量要求见表。
生产每吨精TiCl4的消耗指标为粗TiCl4 1.05~1.073t;电124~174kW•h;精TiCl4的实收率为95%左右。
富钛料氯化车间设计以富钛料车间生产的钛渣或金红石(天然或人造)为原料,经氯化和收尘冷凝系统,生产粗四氯化钛的海绵钛厂车间设计。
氯化有固定层氯化、熔融盐氯化和流态化氯化(沸腾氯化)。
20世纪60年代以前,设计都选用固定层氯化系统。
60年代中期,美国钛金属公司(TIMET)在扩建中采用流态化氯化金红石技术,其后,国外各钛厂相继淘汰了固定层氯化工艺,改用流态化氯化炉。
唯有苏联用熔融盐氯化取代固定层氯化。
在中国,1968年,天津化工厂钛车间采用流态化炉氯化钛渣的新工艺,此后中国各钛厂均改用流态化氯化炉,其规格为φ600~φ1000mm。
只有锦州铁合金厂采用熔融盐氯化炉。
1990。
年遵义钛厂试验成功用φ1200mm无筛板流态化氯化炉氯化高钛渣。
车间设计内容主要包括:工艺流程选择、设备选择、车间配置与技术要求、主要技术经济指标。
工艺流程选择流态化氯化及熔融盐氯化工艺的选择,决定于原料品位与成分。
富钛料中TiO2含量在90%以上,钙和镁含量低于2%时可选用前者;TiO2含量低于80%,钙和镁含量高于2%选用后者。
流态化氯化工艺流程见图。
熔融盐氯化工艺,除炉型与之截然不同外,其收尘冷凝系统与之相同。
在海绵钛工程设计中,当粗四氯化钛产量大于4000t/a时,要设计两套以上氯化系统,其中一套备用。
氯化的收尘冷凝系统要与氯化炉的最大产量相适应。
流态化氯化除对原料的品位及CaO+MgO含量有要求外,还要求粒度为80~120目的高于80%;煅烧后石油焦的固定碳高于90%,粒度为20~80目的高于80%;混合氯气浓度(体积浓度)高于80%。
氯化炉反应带温度为800~1000℃,炉子出口温度为500~700℃。
收尘冷凝器最后的出口温度为120~150℃;淋洗塔最后的出口温度不高于5℃;冷冻盐水温度为-10~-15℃。
沸腾压差为588~980Pa;炉子出口压力为98~392Pa;折流板槽出口压力为98Pa。
氯气压力为0.2~0.3MPa。
熔融盐氯化与流态化氯化技术条件大体相同。
氯化系统中四氯化钛的淋洗,第一套管冷凝器的冷却介质为水;第二套管冷凝器的冷却介质采用冷冻液。
设备选择主要设备有氯化炉、收尘冷凝器、淋洗塔和沉降槽等。
流态化氯化炉多为圆柱型流态化床,结构简单、制造方便,炉料不需制团和团块焦化工序,炉单位面积产量高、为自热反应,但物料粒度的要求比较严格。
流态化炉炉底面积按下式计算:F底=V/W式中V为单位时间流态化床层的气流量,m3/s,其与单位时间炉产四氯化钛量,单位四氯化钛耗氯气量及氯气浓度有关;W为正常流态化时气流计算速度,m/s;F底为炉底面积,m2。
熔融盐氯化炉的生产能力比固定层氯化炉高4~6倍,定期排出废盐。
氯化炉的生产周期比固定层氯化炉长2~3倍,适用于低品位及含CaO+MgO高的原料。
熔融盐氯化炉直径按下式计算:式中Q为氯化炉日产四氯化钛量,t/d;q为氯化炉单位面积日产四氯化钛量,t/(m2•d);D为氯化炉直径,m。
收尘设备有旋风收尘器、电收尘器、布袋收尘器和隔板除尘器等。
隔板除尘器虽然效率低,但结构简单,防腐蚀性能好、耐高温,仍为设计选用。
车间配置与技术要求仪表室配置在生产操作较集中的楼层,靠近氯化炉的端头,在仪表室内能观察到氯化炉的操作。
在厂房内氯化炉按单台炉配置,其它各设备根据工艺流程方向配置。
设备间尽量缩短连接管路,保持气密性,防止管道堵塞和污染扩散。
设置设备清洗设施和设备干燥室。
设备清洗和冲渣房要有排风系统。
生产尾气排风机用钛制风机,卫生排风机采用玻璃钢制风机,尾气塔及管道用非金属耐酸腐蚀材料制造。
厂房、楼板、柱、梁及其它构件采用钢筋}昆凝土结构。
墙、柱及其它构件要作防腐处理,设备及管道涂防腐漆。
地面要求耐酸腐蚀。
厂房内、外设酸性污水沟,污水汇集污水站,统一处理。
主要技术经济指标钛渣和金红石的质量要求见富钛料车间设计,粗四氯化钛质量要求和氯化车间单耗分别见表1和表2。
表1粗四氯化钛的质量要求表2车间技经指标(以每吨粗TiCl4计)海绵钛厂还原蒸馏车间设计以精四氯化钛为原料,用精镁还原,经真空蒸馏和破碎,制成商品海绵钛的海绵钛厂车间设计。
工艺流程选择还原蒸馏工艺有非联合法和联合法。
前者工序繁杂,劳动生产率低,污染环境,单位产品的物耗、能耗、成本及基建投资高。
后者生产工艺流程简单,生产率高,劳动条件和产品质量好,单位产品的物耗、能耗、成本和基建投资低。
此外。
还有半联合法,其优缺点介于以上二者之间。
还原蒸馏联合法的工艺流程见图。
在还原蒸馏联合法流程作业中,首先将还原蒸馏器清洗、干燥,放入还原蒸馏联合炉内加热后,加入液态镁和精四氯化钛,在氩气保护下进行还原反应。
反应过程中,排出反应副产物—氯化镁,送镁电解车间回收镁和氯气。
还原结束后,在热态下直接转入真空蒸馏。
蒸馏冷凝物—镁和氯化镁在封闭状态下,直接返回还原过程。
蒸馏结束冷却到室温后,从还原蒸馏器中取出海绵钛,经破碎、包装,制得符合标准的成品海绵钛。
设计采用的主要工艺参数是:还原反应温度为800~920℃;还原反应压力控制在23000~2600Pa;还原剂一镁的过量系数控制在45%~50%;氯化镁排出率为93%~96%;单位面积精四氯化钛加入速度为90~160kg/(h•m2)。
真空蒸馏的最高温度与设备材质有关。
选用锅炉钢板时,最高温度控制在980℃以下;采用耐热合金钢板时,最高温度为1000~1100℃。
蒸馏真空度为5.3~0.06Pa。
在还原蒸馏器出炉冷却过程中,采用氩气保护,压力控制在6600~26000Pa。
海绵钛成品粒度为0.8~12.7mm。
还原蒸馏车间生产工艺流程示意图1-还原蒸馏器;2-喷枪;3-起重机;4-机械真空泵;5-镁抬包;6-四氯化钛高位槽;7-氯化镁抬包;8-还原蒸馏炉;9-风机;10-过滤嚣;11-真空阀;12-油压剪切机;13-起重机;14-机械真空泵;15-油扩散泵;16-颚式破碎机;17-起重机;18-油碎机;19-筛分机;20-成品桶;2l-包装机设备选择主要设备有还原蒸馏设备,精四氯化钛及液态镁加料设备,破碎、包装设备和起重运输设备。
还原蒸馏设备,按结构型式,有非联合式、半联合式和联合式。
非联合式还原设备又分为上排氯化镁和下排氯化镁两种。
蒸馏设备分为上冷式和下冷式。
联合式分为I形和倒U形。
还原蒸馏联合设备技术经济指标先进。
设备规格和数量按工厂生产规模并通过物料平衡和热平衡计算确定。
还原蒸馏联合炉台数计算公式如下:n1=Q(t1+t2)/8760Q1ε1ε2还原蒸馏器台数计算公式如下:n2=Q(t1+t2+t3+t4+t5+t6)/8760Q1ε1ε2式中n1为还原蒸馏炉台数,台;n2为还原蒸馏器台数,台;t1为还原蒸馏占炉时间,h;t2为辅助工作占炉时间,h;Q为年产量,t/a;Q1为炉产量,t/炉;ε1为产品合格率,%;ε2为设备利用率,%;t3为准备时间,h;t4为炉外冷却时间,h;t5为拆卸、取出时间,h;t6为安装、预抽真空检漏时间,h。
联合炉既可在还原期正压下工作,能够排出还原反应余热,又能在蒸馏期负压下工作。
还原蒸馏器既可在还原期高温、正压下工作,又可在蒸馏期高温、负压下工作,满足还原与蒸馏期的完全互换,合理的气流导向,便于判断和处理事故。