合成氨联醇工艺的甲醇合成工序的技术问
7万吨/年甲醇、3万吨/年合成氨新工艺技术探讨

1 中 20 . 6 0煤 气炉 固定 层 间歇 气化 、生 产 的低 氮煤 气
经集 中余 热 回收 ,集 中洗 涤降 温 除尘去 气 柜 。 2 出气柜 的低 氮煤气罗 茨鼓 风机加压 后经冷 却湿法 脱 . 硫 静 电除焦 一部 分 气体 进原 压缩 机一 段 、 段 加压 后 , 二 去 变 换将 多余 的 C O变 换 为氢 气 , 换率和 气 体组 成 由集散 变 控 制 , 果原 小氮 肥厂 产 品为碳 铵 经碳 化 系统脱 碳 并生产 如 碳 酸氢 铵 , 碳化 气仍 然进 原压 缩 系统 34 将 气体压 缩 至 .段
5 0 Pa 。 .M
4 由于生产 低氮煤体组成根 据醇氨 比进行调 节 , 煤气 炉
和煤 利用 率煤气炉 发气 量均要 比单醇高 , 前市 场 目 价格 较高 , ̄x 降低 甲醇 的成本有 较大 的优越性 。 - , t 5小 氮 肥厂 工艺 流程 不 变 ,原有设 备全 部 . 具有 投 资省 ,建 设周 期短 等 优点 。 6在 合成 高压 圈 内增 加 了等 高压 甲醇 甲烷 仳 . 醇化 既作 为净 化 装置 又生产 了部分 甲醇 , 甲烷 化1 洗 ,使 合 成 气净 化 度 大 大提 高 ,延 长 了合 成 触j 命 ,取 消铜洗 ,保 护 了环 境 。 7联 氨工艺与 单醇 比 由于气化系统煤 利用率 . 成圈循环 比小 , 成率要求 低 , 合 没有 放空气 , 投资
维普资讯
甲醇 的优越 性 , 免 了低 压 甲醇煤 气 化 隋性气 体 避 成 循环 量 较大 ,放 空气 量 大 ,能耗 较高 等缺 点 。 2 采用 固定层 气化 、 氮煤 气脱 硫等 组成 个 . 低 作 和生 产管 理 方便 ,气 体成 份容 易调 节 。 3 醇氨 比容 量调 节 , . 根据 市场 需 求 , 甲醇 生j
甲醇合成的工艺流程和设备

甲醇合成的工艺流程和设备甲醇合成是一种重要的工业化学反应,它是通过一系列的工艺流程和设备来完成的。
下面将详细介绍甲醇合成的工艺流程和设备。
第一步是气体净化。
原料气体主要是天然气或煤气,其中含有一些杂质,如硫化氢、二氧化碳、氨等。
这些杂质会对后续的合成反应产生不利影响,因此需要通过气体净化来去除。
气体净化主要包括硫化氢去除、二氧化碳去除和氨去除等步骤。
硫化氢可以通过催化氧化反应转化为硫,二氧化碳可以通过碱性溶液吸收,氨可以通过酸性溶液吸收。
第二步是合成气的制备。
合成气是甲醇合成的重要原料,它是一种混合气体,主要由一氧化碳和氢气组成。
合成气的制备一般采用催化剂转化法或气化法。
催化剂转化法是将天然气或煤气与蒸汽在催化剂的作用下反应生成合成气。
气化法是将煤、石油等碳质原料在高温、高压条件下气化生成合成气。
第三步是甲醇的合成。
合成气进入甲醇合成反应器后,经过一系列的反应生成甲醇。
甲醇合成一般采用低温高压条件下的催化反应。
常用的催化剂有铜-锌氧化物、铜-铝氧化物等。
甲醇合成反应的主要反应是一氧化碳和氢气生成甲醇。
反应温度一般在200-300摄氏度,压力一般在10-30兆帕。
甲醇的合成反应是一个平衡反应,需要通过适当的操作控制反应条件和催化剂的选择来提高甲醇的产率和选择性。
气体净化装置主要包括硫化氢去除器、二氧化碳去除器和氨去除器等。
硫化氢去除器通常采用催化氧化法,其中含有催化剂床层。
二氧化碳去除器采用碱性溶液吸收法,溶液中加入碱性物质,如钠碱。
氨去除器采用酸性溶液吸收法,溶液中加入酸性物质,如硫酸。
合成气制备装置主要包括催化转化装置和气化装置。
催化转化装置中含有催化剂床层,通过催化反应将天然气或煤气转化为合成气。
气化装置一般采用煤气化炉或石油气化炉,通过高温、高压条件下将煤或石油气化生成合成气。
甲醇合成反应器是甲醇合成的核心设备。
反应器一般采用垂直的压力容器,内部装有催化剂床层。
合成气经过加热后进入反应器,与催化剂发生反应生成甲醇。
合成氨联醇工艺的甲醇合成工序的技术问答[精编版]
![合成氨联醇工艺的甲醇合成工序的技术问答[精编版]](https://img.taocdn.com/s3/m/9f4e0454bed5b9f3f90f1cac.png)
合成氨联醇工艺的甲醇合成工序的技术问答[精编版]合成氨联醇工艺的甲醇合成工序的技术问答常熟开拓催化剂有限公司严廷良目录1、联醇的规模如何确定?2、联醇合成工艺流程应如何选择?3.在联醇的甲醇合成工序中决定最高甲醇产量的因素有那些方面?简单计算是怎样的?4.进合成塔的CO含量有那些因素来决定?进系统的CO含量是如何确定的?5.联醇中循环机大小是如何选择的?6.对带有螺旋板式换热器的合成内件,在生产中其主线为什么不允许关闭或通气过小?7.有热量回收的流程,往往出现甲醇低产时入塔CO降低到3%以下时,就很难达到自热平衡,必需开电炉才能维持应如何处理?8.高压外筒的接口偏小怎么办?9.联醇的工艺流程中,对进入系统的气体为什么要进行精制除去有害物质?10.联醇工艺流程中,在送出系统前为什么都用水洗回收残余的甲醇?11.合成氨上联醇工艺,为什么还必须上脱碳工艺?12.双系统时,采用什么形式操作较佳?13.联醇投产后对合成氨工艺有那些影响?14.联醇投产后增加了压缩机的该段间压差,有那些因素使联醇合成工序的阻力增加?15. 在开停车时,如何减少羰基金属化合物的生成量?16. 联醇生产中,循环机故障又无备机,如何避免催化剂不超温?17. 催化剂还原时为什么会在放出的水中有蓝色?18. 为什么有联醇的粗醇颜色变黑和黑色粉未沉淀物?19. 有那些因素会造成催化剂粉碎?20、在开工过程中对系统的置换用什么方法较妥?21、新的催化剂为什么要还原?升温还原时的出水量是多少?22、对铜基催化剂的还原,低氢还原和高氢还原有什么区别?23、高氢还原分成几个阶段?24.高氢还原的升温曲线是如何制定的,升温还原曲线图例是怎样的?25、铜基催化剂高氢还原时为什么有时还原的起始温度较低?26、铜基催化剂还原时,如何控制水汽浓度及出水量?27、高氢升温还原过程为什么系统压力取5MPa?28、为什么有些厂出现升温还原时,电炉还没有送,床层温度就已超温并大量出水?29、在还原过程中,会不断消耗H2,使系统压力下降,系统里氢含量下降,是否需要连续补H2、N2气及连续排放后提高氢含量?30.铜基催化剂还原终了如何判断?31.有后置锅炉的流程,在还原过程中,什时候该锅炉可投入运行?32.为什么在高氢还原时,不同批号的催化剂前期出水率及后期出水率会不相同?33.怎样选择甲醇合成催化剂?34.怎样减少和避免联醇生产中的结蜡问题?35.在催化剂升温还原过程中,为什么升到100℃左右时,测温显示会反常?36.在还原的盛期,遇到突然停电怎么处理?原开二台循环机进行还原时,突然有一台有故障必须停下来,怎么处理?37.为什么联醇生产后,有时会出现对氨合成催化剂的暂时中毒现象?38.入塔原料气中甲醇含量增加后,会对甲醇合成产生哪些影响?39.为什么催化剂升温还原时空速维持在3000~5000时-1而不能太高?40.停车时,为什么要尽量避免焖炉保压?41.为什么对铜基催化剂的还原应尽量避免使用含CO的气体作高氢还原的气源?42.正常生产中若突然出现催化剂层温度急速上升,只有降低原料气中CO含量才能使温度降下来为什么?43.采取那些措施,以延缓铜基催化剂的热老化及延长其使用寿命?44.为什么在内件安装好催化剂后,紧靠催化剂层上面是严禁动火的?45.在装好催化剂后当用H2、N2气作气源进行置换和试压试漏时,充压、卸压速度不能过低,为什么?46.为什么甲醇合成塔有时会出现径向平面温差大,甚至一侧轴向温度普遍偏低,而造成整塔催化剂的CO转化率下降?47、全厂长时间停车(如大修等),而联醇催化剂不更换时应如何保护?48、联醇工序临时停车,卸压后发现系统里有铜液或水进入系统为什么?49、在工厂的生产过程中发生内件损坏,但催化剂仍好用怎么办?50、使用怎样的内件,更适合于甲醇合成塔上的应用?回顾合成氨的联醇工艺,研究开发始于二十世纪六十年代并实现了工业化,这是化肥工业史上的一次创举,它使化肥企业的产品结构突破了单一的局面,节能降耗有了新发展,还增强了企业的市场应变能力,到二十世纪八、九十年代更是有了突飞猛进的飞跃,联醇在全国遍地开花。
甲醇合成原理方法与工艺
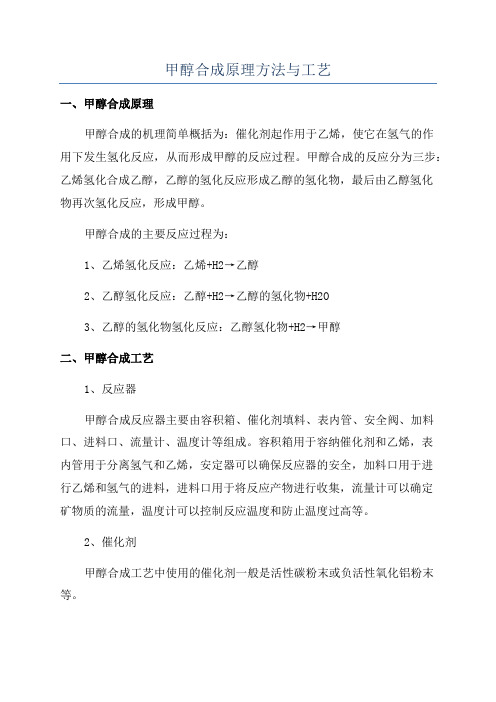
甲醇合成原理方法与工艺
一、甲醇合成原理
甲醇合成的机理简单概括为:催化剂起作用于乙烯,使它在氢气的作
用下发生氢化反应,从而形成甲醇的反应过程。
甲醇合成的反应分为三步:乙烯氢化合成乙醇,乙醇的氢化反应形成乙醇的氢化物,最后由乙醇氢化
物再次氢化反应,形成甲醇。
甲醇合成的主要反应过程为:
1、乙烯氢化反应:乙烯+H2→乙醇
2、乙醇氢化反应:乙醇+H2→乙醇的氢化物+H2O
3、乙醇的氢化物氢化反应:乙醇氢化物+H2→甲醇
二、甲醇合成工艺
1、反应器
甲醇合成反应器主要由容积箱、催化剂填料、表内管、安全阀、加料口、进料口、流量计、温度计等组成。
容积箱用于容纳催化剂和乙烯,表
内管用于分离氢气和乙烯,安定器可以确保反应器的安全,加料口用于进
行乙烯和氢气的进料,进料口用于将反应产物进行收集,流量计可以确定
矿物质的流量,温度计可以控制反应温度和防止温度过高等。
2、催化剂
甲醇合成工艺中使用的催化剂一般是活性碳粉末或负活性氧化铝粉末等。
合成氨联醇工艺的甲醇合成工序的技术问答

合成氨联醇工艺的甲醇合成工序的技术问答严廷良(常熟开拓催化剂有限公司 215500)回顾合成氨的联醇工艺,研究开发始于20世纪60年代并实现了工业化,这是化肥工业史上的一次创举,它使化肥企业的产品结构突破了单一的局面,节能降耗有了新发展,还增强了企业的市场应变能力,到20世纪80、90年代更是有了突飞猛进的飞跃,联醇在全国遍地开花。
我国是一个“多煤少油”的国家,甲醇开始向燃料市场倾斜,这已经是个无法阻挡的趋势,这就使合成氨工艺有了联醇后亦又有甲醇合成的联氨工艺的发展趋势。
而随着甲醇市场的红火,化肥行业不仅原有的联醇工艺不断完善,增加产量,仍有不少企业还在建设中。
在此新形势下,本人就接触到的联醇装置,设计、建设、施工投产、运行等一些问题做些剖析,汇集整理成问答形式成文如下。
1 联醇的规模如何确定?联醇规模的确定,也就是通常在行业里流行的醇氨比(实际上是醇与总氨的比例),最经济的联醇规模,在不增加脱碳能力或降低尿素产量,把变换剩余的CO使之合成甲醇,作为副产品,这时醇氨比在10%~20%,合成氨的经济效益最好,但这样的比例形不成生产规模,经不起市场变化,当甲醇旺火利润高,而化肥利润率低迷时,却无法提高甲醇产量,因此考虑联醇规模时,还应考虑甲醇的市场前景,可过高的醇氨比又使造气煤耗增加,增加脱碳的消耗和甲醇合成循环机的电耗等,而成本上升,影响合成氨的综合效益。
合成氨企业总体规模不大时,一般醇氨比在确定规模时考虑40%~50%,总体规模较大时醇氨比不超过40%。
对新建厂而言还考虑投资回报率,醇氨比过高,不如搞联氨工艺了,即单醇联产合成氨。
2 联醇合成工艺流程应如何选择?合成氨的联醇之甲醇合成工艺,老企业绝大部分是把甲醇合成设置在精炼铜洗前,即压缩机五段或六段出口处。
新建厂用双甲工艺的,也有把联醇放在与合成氨同一压力等级上,即所谓等高压联醇。
其甲醇合成工艺流程是随该工艺的不断完善而目前有下列三种。
普遍的是合成塔内自设换热器,无热量回收(见图1)。
甲醇合成工艺流程

甲醇合成工艺流程甲醇合成是一种重要的化学工艺,用于生产甲醇这种重要的有机化合物。
下面将介绍甲醇合成的工艺流程。
首先,甲醇合成的原料主要包括一氧化碳和氢气。
一氧化碳可以通过化石燃料的气化或者过程废气的处理得到。
而氢气可以通过天然气重整反应或者通过电解水得到。
在甲醇合成过程中,首先需要对原料进行净化和预热。
一氧化碳和氢气通过净化装置,去除其中的杂质和有毒物质。
然后,原料进入加热器,通过加热提高其温度,为后续的反应做准备。
接下来,原料进入甲醇合成反应器。
在反应器中,一氧化碳和氢气发生甲醇合成反应,生成甲醇和水。
这个反应是一个高压、高温的反应,需要使用催化剂来提高反应速率和选择性。
常用的催化剂包括铜、锌、铝和锆等金属催化剂。
反应器内部可以采用固定床、流化床或者微管等不同形式。
在反应过程中,甲醇和水汽经过冷却装置,进行冷却,使其冷凝成液体。
然后,通过分离装置,将液体甲醇和水汽进行分离。
水汽可以再循环利用,或者通过进一步处理后排放。
甲醇分离纯化是甲醇合成工艺中的重要环节。
甲醇需经过除杂工艺,去除其中的杂质,如碱金属、杂质醇、酮和酚等。
常用的方法有萃取、析出、蒸馏等。
经过精馏、提纯等处理,最终得到纯度高的甲醇产品。
在甲醇合成工艺中,还需要对废气进行处理。
废气中一般含有甲烷、氢气、一氧化碳等有价值的成分,可以通过分离和净化技术进行回收利用。
同时,废气中也含有一些有害物质,如二氧化碳、氮氧化物等,需要经过净化和处理后排放。
总结起来,甲醇合成的工艺流程主要包括原料净化预热、甲醇合成反应、冷却分离、甲醇纯化和废气处理等步骤。
这些步骤的操作和控制都需要高度的工艺和技术要求,以确保甲醇的合成和生产过程稳定、高效并符合环保要求。
联醇生产中的问题及处理

层温度。六段工艺气 中氨含 量高达 10 0 , 0 ×1 远远高于 甲醇工艺气小 于 2 ×1 的要求 ,从 5 0
而导致 甲醇的碱度超标 ,生成 的甲胺副产物与 甲 醇催化剂中的铜反应 降低 了甲醇催化剂的活性 。
第3 期
氨合成塔系统专用,l 、2 则既可用于甲醇生产 # #
又可用于合成 氨生产。由于进、出 口都 是单阀, 当阀门发生内漏时 ,必然会发生氨合成系统气体
串到甲醇系统。由于经验不足导致两次这样 的事 故发生,甲醇系统水冷器是列管式水冷器,管径
多 ,又没有将杂醇采出,最终导致石蜡堵塞 主、 预塔放空系统管道 ,特别是预塔放空气水冷器及 出 口管堵塞 ,造成预塔压力超标 ,安全 阀跳。因
此 , 甲醇生产中,杂醇应及时采 出;在 甲醇催 在 化剂使用后期 ,副产物石蜡生成太多时应考虑更 换甲醇合成催化剂。 我公司解决此问题的方法是在预塔水冷器后 放空管加入蒸汽 ,开车时微开低压蒸汽保证石蜡 不结晶堵塞管道。
小 ,当氨合成气 串入 甲醇系统后 ,氨即和 甲醇工
艺气中的 0 2 3 反应 ,在甲醇水冷器处生成碳铵结
4 高压阀门内漏导致 甲醇 系统堵塞超压
[ 收稿 日期]20—1 8 051- 0 [ 作者简介]丁应海 (92 , , 贵阳人 , 17 一)男 贵州 助理工程师 。
我公司共有 3台透平式循环机 ,3 透平机供 #
维普资讯
・
2 0・
中 氮 肥
晶形成堵塞 , 甲醇系统超压 ,幸亏及时将 甲醇 使 系统停车,用蒸汽溶解掉水冷器及循环机进出口 阀门处 的碳铵结 晶,才避免 了恶性事故 的发生。
联醇的甲醇合成工序几个技术问题的探讨

联醇的甲醇合成工序几个技术问题的探讨联醇甲醇合成工序是通过一系列的化学反应将碳氢化合物转化为甲醇的工艺过程。
该工艺被广泛应用于石化工业中,生产的甲醇被用于化学原料或燃料。
然而,在实践中,联醇甲醇合成过程存在一些技术问题,这些问题需要解决才能获得高质量的甲醇。
首先,醇分离是甲醇合成过程中的一个重要问题。
醇分离是指从反应物中分离出所需的甲醇并去除其他不需要的物质,例如水和未反应的醇。
目前,常用的醇分离方法主要包括蒸馏和萃取。
但这些方法存在一些问题,例如能耗高、操作难度大、设备复杂等。
因此,需要开发出更高效、更经济、更易操作的醇分离技术。
其次,甲醇质量也是甲醇合成过程中需要解决的一个问题。
甲醇的质量受到反应物的质量、反应温度、反应压力等因素的影响。
化学反应的平衡性以及反应物的纯度、质量等因素也会影响甲醇的质量。
因此,在甲醇合成过程中需要选择适当的反应条件、精细控制反应物的质量和纯度,以确保甲醇质量符合要求。
第三,催化剂也是影响甲醇合成过程的一个关键因素。
催化剂的选择和优化可以提高反应速度和产率。
目前,常用的催化剂包括氧化铜催化剂和锆硅酸盐催化剂等。
不同的催化剂有着不同的特点和适用范围,需要在实践中进行比较和选择。
最后,甲醇合成过程需要对反应条件进行精准控制。
反应温度、反应压力、醇与气体的比例等反应条件都需要进行精确控制,以确保反应过程的平稳进行。
反应过程的监测和控制需要先进的仪器设备和操作技能。
综上所述,联醇甲醇合成过程中存在一些技术问题,但这些问题可以通过不断的研发和改进而得以解决。
在今后的实践中,需要注意聚焦这些关键问题,并持续创新,以提高甲醇合成的效率和质量。
- 1、下载文档前请自行甄别文档内容的完整性,平台不提供额外的编辑、内容补充、找答案等附加服务。
- 2、"仅部分预览"的文档,不可在线预览部分如存在完整性等问题,可反馈申请退款(可完整预览的文档不适用该条件!)。
- 3、如文档侵犯您的权益,请联系客服反馈,我们会尽快为您处理(人工客服工作时间:9:00-18:30)。
合成氨联醇工艺的甲醇合成工序的技术问答常熟开拓催化剂有限公司严廷良目录1、联醇的规模如何确定?2、联醇合成工艺流程应如何选择?3.在联醇的甲醇合成工序中决定最高甲醇产量的因素有那些方面?简单计算是怎样的?4.进合成塔的CO含量有那些因素来决定?进系统的CO含量是如何确定的?5.联醇中循环机大小是如何选择的?6.对带有螺旋板式换热器的合成内件,在生产中其主线为什么不允许关闭或通气过小?7.有热量回收的流程,往往出现甲醇低产时入塔CO降低到3%以下时,就很难达到自热平衡,必需开电炉才能维持应如何处理?8.高压外筒的接口偏小怎么办?9.联醇的工艺流程中,对进入系统的气体为什么要进行精制除去有害物质?10.联醇工艺流程中,在送出系统前为什么都用水洗回收残余的甲醇?11.合成氨上联醇工艺,为什么还必须上脱碳工艺?12.双系统时,采用什么形式操作较佳?13.联醇投产后对合成氨工艺有那些影响?14.联醇投产后增加了压缩机的该段间压差,有那些因素使联醇合成工序的阻力增加?15. 在开停车时,如何减少羰基金属化合物的生成量?16. 联醇生产中,循环机故障又无备机,如何避免催化剂不超温?17. 催化剂还原时为什么会在放出的水中有蓝色?18. 为什么有联醇的粗醇颜色变黑和黑色粉未沉淀物?19. 有那些因素会造成催化剂粉碎?20、在开工过程中对系统的置换用什么方法较妥?21、新的催化剂为什么要还原?升温还原时的出水量是多少?22、对铜基催化剂的还原,低氢还原和高氢还原有什么区别?23、高氢还原分成几个阶段?24.高氢还原的升温曲线是如何制定的,升温还原曲线图例是怎样的?25、铜基催化剂高氢还原时为什么有时还原的起始温度较低?26、铜基催化剂还原时,如何控制水汽浓度及出水量?27、高氢升温还原过程为什么系统压力取5MPa?28、为什么有些厂出现升温还原时,电炉还没有送,床层温度就已超温并大量出水?29、在还原过程中,会不断消耗H2,使系统压力下降,系统里氢含量下降,是否需要连续补H2、N2气及连续排放后提高氢含量?30.铜基催化剂还原终了如何判断?31.有后置锅炉的流程,在还原过程中,什时候该锅炉可投入运行?32.为什么在高氢还原时,不同批号的催化剂前期出水率及后期出水率会不相同?33.怎样选择甲醇合成催化剂?34.怎样减少和避免联醇生产中的结蜡问题?35.在催化剂升温还原过程中,为什么升到100℃左右时,测温显示会反常?36.在还原的盛期,遇到突然停电怎么处理?原开二台循环机进行还原时,突然有一台有故障必须停下来,怎么处理?37.为什么联醇生产后,有时会出现对氨合成催化剂的暂时中毒现象?38.入塔原料气中甲醇含量增加后,会对甲醇合成产生哪些影响?39.为什么催化剂升温还原时空速维持在3000~5000时-1而不能太高?40.停车时,为什么要尽量避免焖炉保压?41.为什么对铜基催化剂的还原应尽量避免使用含CO的气体作高氢还原的气源?42.正常生产中若突然出现催化剂层温度急速上升,只有降低原料气中CO含量才能使温度降下来为什么?43.采取那些措施,以延缓铜基催化剂的热老化及延长其使用寿命?44.为什么在内件安装好催化剂后,紧靠催化剂层上面是严禁动火的?45.在装好催化剂后当用H2、N2气作气源进行置换和试压试漏时,充压、卸压速度不能过低,为什么?46.为什么甲醇合成塔有时会出现径向平面温差大,甚至一侧轴向温度普遍偏低,而造成整塔催化剂的CO转化率下降?47、全厂长时间停车(如大修等),而联醇催化剂不更换时应如何保护?48、联醇工序临时停车,卸压后发现系统里有铜液或水进入系统为什么?49、在工厂的生产过程中发生内件损坏,但催化剂仍好用怎么办?50、使用怎样的内件,更适合于甲醇合成塔上的应用?回顾合成氨的联醇工艺,研究开发始于二十世纪六十年代并实现了工业化,这是化肥工业史上的一次创举,它使化肥企业的产品结构突破了单一的局面,节能降耗有了新发展,还增强了企业的市场应变能力,到二十世纪八、九十年代更是有了突飞猛进的飞跃,联醇在全国遍地开花。
我国是一个“多煤少油”的国家,甲醇开始向燃料市场倾斜,这已经是个无法阻挡的趋势,这就使合成氨工艺有了联醇后亦又有甲醇合成的联氨工艺的发展趋势。
而随着甲醇市场的波动,化肥行业不仅原有的联醇工艺不断完善,且甲醇产量可随市场变化而调整,仍有不少企业还在建设中。
在此新形势下,本人就接触到的联醇装置,设计、建设、施工投产、运行、催化剂的使用等一些问题做些剖析,汇集整理成问答形式成文如下。
1、联醇的规模如何确定?联醇规模的确定,也就是通常在行业里流行的醇氨比(实际上是醇与总氨的比例),最经济的联醇规模,在不增加脱碳能力或降低尿素产量,把变换剩余的CO使之合成甲醇,作为副产品,这时醇氨比在10-20%,合成氨的经济效益最好,但这样的比例形不成生产规模,经不起市场变化,当甲醇旺火利润高,而化肥利润率低迷时,却无法提高甲醇产量,因此考虑联醇规模时,还应考虑甲醇的市场前景,可过高的醇氨比又使造气煤耗增加,增加脱碳的消耗和甲醇合成循环机的电耗等,而成本上升,影响合成氨的综合效益。
合成氨企业总体规模不大时,一般醇氨比在确定规模时考虑40-50%,总体规模较大时醇氨比不超过40%。
对新建厂而言还考虑投资回报率,醇氨比过高,不如搞联氨工艺了,即单醇联产合成氨。
2、联醇合成工艺流程应如何选择?合成氨的联醇之甲醇合成工艺,老企业绝大部分是把甲醇合成设置在精炼铜洗前,即压缩机五段或六段出口处。
新建厂用双甲工艺的,也有把联醇放在与合成氨同一压力等级上,即所谓等高压联醇.其甲醇合成工艺流程是随该工艺的不断完善而目前有下列三种。
普遍的是合成塔内自设换热器,无热量回收,如图一压缩来的气体与循环气混合进入油分,分二路,主线进合成塔筒体与内件夹套后入下部换热器,副线直接入塔底进入中心管与换热后的气体混合后入内件的触媒筐内。
而出塔的含有甲醇的气体直接进入水冷器,冷却后在醇分分离甲醇后一路去铜洗,另一路进循环机加压后再回到油分。
.醇分分离的粗醇再进一步经精馏后作产品销售。
从上面看出,合成塔内自设换热器占据了高压空间,使催化剂装填量减少,另外由于主副线气量调节有限而使该流程进塔CO的高限值受制约,而调节幅度降低,为此出现了第二种流程,设置塔外换热器。
如图二压缩来的气体与循环气混合进入油分,主线经换热器提温后进合成塔筒体与内件夹套,后进入内件中心管到触媒筐,副线可直接进内件中心管与主线气混合入触媒筐,出塔气进换热器后去水冷器、醇分。
此流程与前不同的是把内件里的换热器移到塔外,使合成塔高压空间充分利用,使调节幅度比以前更大了。
但该流程中要注意的是塔出口温度超过200℃以上,也就是合成塔出口到换热器进口及合成塔底部和换热器底部要接触超过200℃以上的气体,其材质必需是耐热合金钢。
为此该流程大部分都是在合成塔内保留部分换热器,使出塔温度不超过200℃而解决。
这样的流程与前流程无大的区别,热量均未利用,仅改变和扩大了调节手段,增加了甲醇产量。
现在为不少厂家所接受的流程是带有热量回收的流程。
如图三主线气进夹套后一出气到换热器,提温度后作为二进气入塔,进触媒筐,副线气可直接进塔或加到二进气上。
而合成出塔气进入废热锅炉(或水加热器),回收热量产生蒸汽(或加热全厂的锅炉用水)后进换热器、后到水冷器、醇分。
在这个流程中当需提高甲醇产量时其反应热可得到回收,还降低水冷器的负荷。
并能使调节更灵活,得到的甲醇产量也最高。
但必须考虑气体温度200℃以上设备、管道材质问题。
但其废热锅炉和换热器外筒都可充分利用合成氨淘汰下来的设备。
3.在联醇的甲醇合成工序中决定最高甲醇产量的因素有那些方面?简单计算是怎样的?在联醇中决定甲醇产量的是参加CO+H2—CH3OH 化学反应的CO量,从此反应式可看出,生产一吨甲醇需转化的CO量为:1000÷32×22.4=700Nm3/t也就是说合成塔确定后,其催化剂装填也是定值,那么单位时间通过单位体积催化剂上的气体量即空速是第一因素。
可联醇而言,此空速不能取得过高,一般在8000—10000时-1,例如一Ø800塔内装催化剂4m3。
则该塔最大通气量为4×10000=40000 Nm3/h。
由于各种调节手段决定了入塔的气体中CO最高含量和催化剂活性而决定了出塔气体中CO含量。
一般出塔CO在该空速下能达到0.5%以下,而入塔气体中的CO由内件结构及工艺流程所决定,如;以近几年的实践看,以均温型内件为例。
流程一当主副线全开时,其入塔CO可达4%,则此时该塔的最高产应为:设反应CO量为X Nm3/h40000×4%-(40000-3X)×0.5%=X解X:1421 Nm3/h。
折成CH3OH为:1421÷700=2.03t/h若流程二、三使催化剂容积到4.5 m3:其入塔气体中CO可达6%,则其产量可达:4.5×10000=45000 Nm3/h 45000×6%-(45000-3X)×0.5%=X解:X=2512.6 Nm3/h 折成CH3OH为:3.59t/h可以产量增高76.8%因此通气量一定后,决定甲醇产量的是进塔CO含量及CO转化率。
也就是要提高产量就要设法提高进塔CO含量,要提高催化剂活性,提高CO转化率即降低出塔CO含量。
4.进合成塔的CO含量有那些因素来决定?进系统的CO含量是如何确定的?从前述计算中可出,合成塔内CO转化率不变,则提高进塔CO含量就能增加产量。
以工艺流程和内件结构确定后,空速一定,在有限的调节手段内,进塔最高CO含量也就到一极限值。
在联醇中通过计算热量平衡得出,每转化1%的CO,使反应气体的绝热温升29-30℃。
若出塔温度控制在270℃,进入触媒筐的气体温度是30℃的话,则绝热温升可达:270-30=240℃,也就是此时反应的CO可达8%,这种状态实际是不可能的。
出塔温度达270℃,意味着在床层内的反应热点温度有可能超过300℃,这是催化剂操作温度不允许的,另外催化剂的活性温度的波幅较小(220—290℃),进口不预热直接进筐,使床层内能很快达到均温,这样的内件目前还没有一家能做到。
还以均温型内件为例,在流程一中,若以出床层温度240℃反应的CO百分比为3.5%其温升为: 3.5%×30=105℃则进入触媒筐的温度;240-105=135℃而流程二、三中反应CO的百分比为5.5%,温升为:5.5×30=165℃则进触媒筐温度要降到240-165=75℃这己经使内件设计制作上增加了难度,同时在操作中,可能使床层的温差增大。
在生产中进塔的CO含量高低由循环机打的循环量大小及进系统原料气中的CO含量高低来决定(也即由原料气中的CO含量决定)进系统的CO含量的计算如下:按第(3)题的计算,流程一的总入塔气量为40000 Nm3/h,现合成氨系统压缩机五或六段出气量为24000 Nm3/h ,即循环量为40000-24000=16000 Nm3/h设进系统气中CO含量为X% 则:(24000×X%+16000×0.5%)÷40000=4% 解X:X=6.3%而以流程二、三为例则:总气量45000 Nm3/h 循环量为:45000-24000=21000 Nm3/h 进系统的CO含量为X%(24000×X%+21000×0.5%)÷45000=6% 解X:X=10.8%5.联醇中循环机大小是如何选择的?工艺流程确定后应考虑选择循环机,要考虑在正常生产中达到最高甲醇产量时所需要的循环量,如第(4)题中的计算:流程一中循环量应为:16000Nm3/h,按压力13.0Mpa 应取:16000÷(130×60)=2.05 m3/min对循环机选用时不仅考虑正常生产时所需,还考虑备机,若在最大负荷时循环量是满负荷时该机故障,若无备机将来不及处理而使催化剂烧毁失活。