合成气制备甲醇原理与工艺
甲醇生产原理

甲醇生产原理
甲醇是一种常见的有机化合物,其化学式为CH3OH。
甲醇的生产原理主要基于合成气的反应,合成气是一种由一氧化碳和氢气组成的气体混合物。
以下是甲醇的生产原理:
1. 合成气制备:首先,通过煤炭、天然气等碳源进行气化或重整反应,产生含有一氧化碳和氢气的合成气。
合成气可根据不同的反应条件和催化剂组合进行生产。
2. 反应器选择:将合成气送入甲醇合成反应器中。
常用的反应器有低温反应器和高温反应器。
低温反应器可通过合成气的洗涤和压缩降低温度,利于甲醇的选择性生成。
高温反应器则有利于反应速率的提高。
3. 反应催化:甲醇合成反应通常在催化剂的存在下进行。
常用的催化剂有金属氧化物,如铜-锌-铝催化剂。
催化剂可以提高甲醇生成的速率和选择性。
4. 反应条件:甲醇的合成受到反应温度、压力和催化剂活性等条件的影响。
通常在中等压力(10-100大气压)和适当的温度(200-300摄氏度)下进行反应。
5. 分离提纯:在反应后,甲醇与未反应的气体、杂质物质等要进行分离和提纯。
常用的方法包括蒸汽混合、蒸馏、吸附等工艺。
通过上述原理,合成气中的一氧化碳和氢气可实现有效转化为
甲醇。
甲醇是一种重要的工业原料,在化工、能源、医药和农业等领域有着广泛的应用。
甲醇生产原理的研究和改进,有助于提高甲醇的生产效率和质量。
甲醇合成的工艺方法介绍
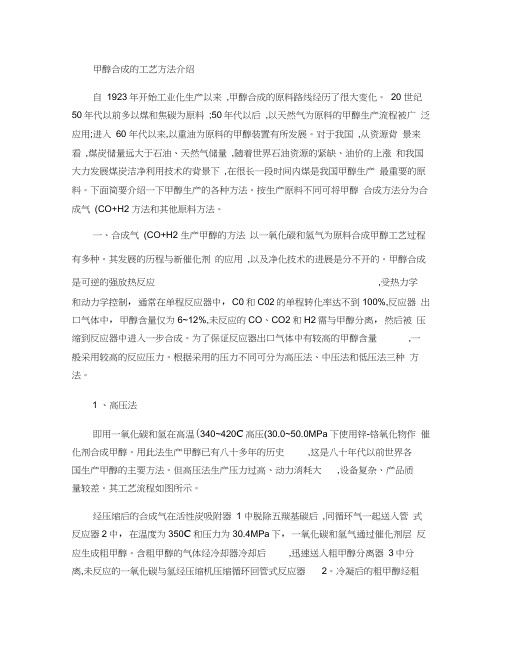
甲醇合成的工艺方法介绍自1923年开始工业化生产以来,甲醇合成的原料路线经历了很大变化。
20 世纪50年代以前多以煤和焦碳为原料;50年代以后,以天然气为原料的甲醇生产流程被广泛应用;进入60 年代以来,以重油为原料的甲醇装置有所发展。
对于我国,从资源背景来看,煤炭储量远大于石油、天然气储量,随着世界石油资源的紧缺、油价的上涨和我国大力发展煤炭洁净利用技术的背景下,在很长一段时间内煤是我国甲醇生产最重要的原料。
下面简要介绍一下甲醇生产的各种方法。
按生产原料不同可将甲醇合成方法分为合成气(CO+H2 方法和其他原料方法。
一、合成气(CO+H2 生产甲醇的方法以一氧化碳和氢气为原料合成甲醇工艺过程有多种。
其发展的历程与新催化剂的应用,以及净化技术的进展是分不开的。
甲醇合成是可逆的强放热反应,受热力学和动力学控制,通常在单程反应器中,C0和C02的单程转化率达不到100%,反应器出口气体中,甲醇含量仅为6~12%,未反应的CO、CO2和H2需与甲醇分离,然后被压缩到反应器中进入一步合成。
为了保证反应器出口气体中有较高的甲醇含量,一般采用较高的反应压力。
根据采用的压力不同可分为高压法、中压法和低压法三种方法。
1 、高压法即用一氧化碳和氢在高温(340~420C高压(30.0~50.0MPa下使用锌-铬氧化物作催化剂合成甲醇。
用此法生产甲醇已有八十多年的历史,这是八十年代以前世界各国生产甲醇的主要方法。
但高压法生产压力过高、动力消耗大,设备复杂、产品质量较差。
其工艺流程如图所示。
经压缩后的合成气在活性炭吸附器 1 中脱除五羰基碳后,同循环气一起送入管式反应器2中,在温度为350C和压力为30.4MPa下,一氧化碳和氢气通过催化剂层反应生成粗甲醇。
含粗甲醇的气体经冷却器冷却后,迅速送入粗甲醇分离器3中分离,未反应的一氧化碳与氢经压缩机压缩循环回管式反应器2。
冷凝后的粗甲醇经粗甲醇储槽 4 进入精馏工序,在粗分离塔5顶部分离出二甲醚和甲酸甲酯及其他低沸点不凝物,重组分则在精分离塔 6 中除去水和杂醇,得到精制的甲醇。
甲醇燃料原理

甲醇燃料原理引言:甲醇是一种常见的有机化合物,其化学式为CH3OH。
甲醇燃料是一种可再生能源,具有低碳排放、高能量密度和易于储存等优点,因此在能源领域备受关注。
本文将介绍甲醇燃料的原理,包括甲醇的制备、燃烧过程及其在发动机中的应用。
一、甲醇的制备:甲醇的制备主要有两种方法,一种是通过合成气反应制备,另一种是通过生物质转化制备。
1. 通过合成气反应制备甲醇:合成气是一种由一氧化碳和氢气组成的混合气体,可以通过多种方法制备,如煤气化、天然气重整和生物质气化等。
合成气反应是指将合成气在催化剂的作用下转化为甲醇的过程。
常用的催化剂有氧化锌、氧化铬和铜锌等。
合成气反应的主要反应方程式为:CO + 2H2 → CH3OH2. 通过生物质转化制备甲醇:生物质转化是指利用生物质原料,如木材、秸秆和废弃农作物等,通过生物化学或热化学方法将其转化为甲醇的过程。
生物质转化可以通过生物发酵、热解和气化等方式进行。
其中,生物发酵是将生物质经过微生物的作用产生醇类化合物,再通过蒸馏和纯化得到甲醇。
二、甲醇的燃烧过程:甲醇的燃烧是指甲醇与氧气在适当的条件下发生氧化反应的过程。
甲醇燃烧是一个复杂的过程,主要包括点火、氧化和传质等步骤。
1. 点火:点火是指在适当的温度和压力下,通过外界能量输入引发甲醇和氧气的反应。
点火温度是指甲醇与氧气发生自燃反应所需的最低温度,一般为400-500摄氏度。
点火温度取决于甲醇的浓度、压力和混合气体的初始温度等因素。
2. 氧化:氧化是指甲醇与氧气发生化学反应产生二氧化碳、水和能量的过程。
甲醇的氧化反应方程式为:2CH3OH + 3O2 → 2CO2 + 4H2O3. 传质:传质是指燃烧过程中产生的热量和产物通过传导、对流和辐射等方式传输到周围环境的过程。
三、甲醇燃料在发动机中的应用:甲醇燃料在内燃机中的应用可以分为两种方式:直接燃烧和间接燃烧。
1. 直接燃烧:直接燃烧是指将甲醇燃料直接喷射到发动机燃烧室中与空气混合燃烧的过程。
甲醇的制备方法与工艺

甲醇的制备方法与工艺嘿,你知道甲醇吗?这可是个相当有趣的东西呢!今天我就来给你讲讲甲醇的制备方法与工艺。
先来说说从合成气制备甲醇的方法吧。
合成气是什么呢?简单来说,就是一氧化碳和氢气的混合气体,这就像是两个小伙伴组合在一起,准备开启一场奇妙的化学之旅。
在这个过程中,有一个很重要的反应,一氧化碳和氢气在一定的条件下会发生反应生成甲醇。
这就好比是两个性格不同的朋友,在特定的环境里相互作用,最后变成了一个全新的角色——甲醇。
要让这个反应顺利进行,那可得讲究不少条件呢。
压力就是一个关键因素。
一般来说,需要比较高的压力,就像是给一氧化碳和氢气这两个小伙伴施加一点压力,让它们更好地融合在一起。
这时候你可能会问,多高的压力才算合适呢?通常是在5 - 10MPa左右。
当然啦,这可不是随随便便定的数值,那可是经过无数次的实验和摸索才得出来的。
温度也很重要啊。
这个反应的温度大概在200 - 300°C之间。
想象一下,这就像是给一氧化碳和氢气在一个温度适宜的“小房间”里,让它们愉快地反应。
如果温度太高或者太低,就像这个“小房间”太热或者太冷,那它们的反应就会受到影响,要么反应不完全,要么就会产生一些其他不想要的东西,这可就糟糕啦!而且呀,还需要有合适的催化剂。
催化剂就像是一个神奇的小助手,能让反应更快更高效地进行。
常见的催化剂有铜基催化剂。
这铜基催化剂就像一个超级有经验的老师傅,引导着一氧化碳和氢气按照正确的方式组合成甲醇。
要是没有这个催化剂,那反应就会慢吞吞的,就像没有老师傅指挥,大家都乱了套一样。
我有个朋友叫小李,他就在一家化工企业里参与甲醇的生产。
有一次,他就跟我讲他们厂里在调整合成气制备甲醇的工艺参数时发生的趣事。
他说,刚开始他们没有掌握好压力,结果生产出来的甲醇产量很低,质量也不怎么样。
他当时可着急了,就像热锅上的蚂蚁一样。
后来经过不断地研究和调整,终于找到了合适的压力范围,产量一下子就上去了,他高兴得像个孩子似的。
甲醇合成原理方法与工艺
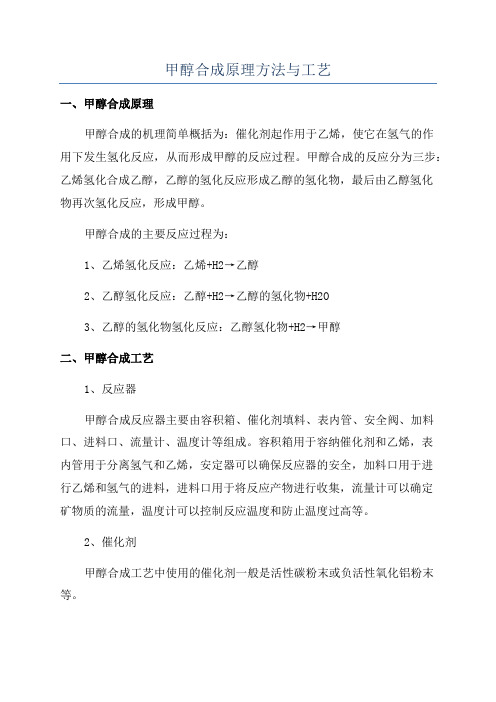
甲醇合成原理方法与工艺
一、甲醇合成原理
甲醇合成的机理简单概括为:催化剂起作用于乙烯,使它在氢气的作
用下发生氢化反应,从而形成甲醇的反应过程。
甲醇合成的反应分为三步:乙烯氢化合成乙醇,乙醇的氢化反应形成乙醇的氢化物,最后由乙醇氢化
物再次氢化反应,形成甲醇。
甲醇合成的主要反应过程为:
1、乙烯氢化反应:乙烯+H2→乙醇
2、乙醇氢化反应:乙醇+H2→乙醇的氢化物+H2O
3、乙醇的氢化物氢化反应:乙醇氢化物+H2→甲醇
二、甲醇合成工艺
1、反应器
甲醇合成反应器主要由容积箱、催化剂填料、表内管、安全阀、加料口、进料口、流量计、温度计等组成。
容积箱用于容纳催化剂和乙烯,表
内管用于分离氢气和乙烯,安定器可以确保反应器的安全,加料口用于进
行乙烯和氢气的进料,进料口用于将反应产物进行收集,流量计可以确定
矿物质的流量,温度计可以控制反应温度和防止温度过高等。
2、催化剂
甲醇合成工艺中使用的催化剂一般是活性碳粉末或负活性氧化铝粉末等。
甲醇制备工艺毕业论文

甲醇制备工艺毕业论文甲醇是一种重要的基础化工原料,广泛用于合成甲醛、甲酸、丙二醇等有机化工产品。
目前,甲醇的生产工艺以合成气法为主,本文将重点介绍该工艺,并探讨其优化方向。
一、合成气法制备甲醇工艺合成气法是目前工业生产中最主要的制备甲醇工艺,其过程如下:1. 原料准备合成气法制备甲醇的主要原料是天然气、煤气或石油气等,首先需要经过预处理除除硫、除水、除二氧化碳等杂质。
2. 合成气制备将准备好的原料气体进入氧化反应器,在催化剂的作用下进行氧化转化,生成合成气。
氧化反应器中通常采用多层床式反应器,催化剂采用金属氧化物催化剂,如CUO-ZnO-Al2O3、Cr2O3等。
3. 气体净化合成气中含有甲烷、氮气、二氧化碳、一氧化碳、氢等杂质,需要进行净化和升压,使气体达到进入甲醇反应器的质量和压力标准。
4. 合成甲醇将净化后的合成气进入甲醇反应器,通过催化剂的作用,进行甲烷和一氧化碳的加氢制甲醇反应。
甲醇反应器主要采用三相流床式反应器,催化剂常用CuO-ZnO-Al2O3。
5. 甲醇提纯将合成甲醇经过蒸馏或萃取等方法进行分离和富集,最终得到高纯度的甲醇产品。
二、甲醇工艺优化在甲醇合成过程中,主要存在以下几个技术难点:1. 甲醇选择性甲醇的生成不是唯一的产物,同时还会有副产物二甲醚和甲醛等生成。
提高甲醇选择性,降低副产物产量,是优化工艺的一个重要目标。
2. 反应热平衡甲醇反应放热严重,容易引起反应器温度升高,进而影响反应速率和产物选择性。
如何控制反应热平衡,防止反应温度过高,是优化工艺的另一个重要问题。
3. 催化剂失活甲醇合成过程中,催化剂可能因积碳、硫化等原因失活,导致产物选择性下降,产量减小。
如何延长催化剂的寿命,是优化工艺的另一个考虑因素。
综合以上问题,优化甲醇制备工艺的关键是提高甲醇选择性、控制反应热平衡和延长催化剂寿命。
可采取以下措施进行优化:1. 优化催化剂的结构、组分和活性,提高甲醇催化活性和选择性。
甲醇合成原理方法与工艺

甲醇合成原理方法与工艺图1煤制甲醇流程示意图煤气经过脱硫、变换,酸性气体脱除等工序后,原料气中的硫化物含量小于0.1mg/m3。
进入合成气压缩机,经压缩后的工艺气体进入合成塔,在催化剂作用下合成粗甲醇,并利用其反应热副产3.9MPa中压蒸汽,降温减压后饱和蒸汽送入低压蒸汽管网,同时将粗甲醇送至精馏系统。
一、甲醇合成反应机理自CO加氢合成甲醇工业化以来,有关合成反应机理一直在不断探索和研究之中。
早期认为合成甲醇是通过CO在催化剂表面吸附生成中间产物而合成的,即CO是合成甲醇的原料。
但20世纪70年代以后,通过同位素示踪研究,证实合成甲醇中的原子来源于CO2,所以认为CO2是合成甲醇的起始原料。
为此,分别提出了CO和CO2合成甲醇的机理反应。
但时至今日,有关合成机理尚无定论,有待进一步研究。
为了阐明甲醇合成反应的模式,1987年朱炳辰等对我国C301型铜基催化剂,分别对仅含有CO或CO2或同时含有CO和CO2三种原料气进行了甲醇合成动力学实验测定,三种情况下均可生成甲醇,试验说明:在一定条件下,CO和CO2均可在铜基催化剂表面加氢生成甲醇。
因此基于化学吸附的CO连续加氢而生成甲醇的反应机理被人们普遍接受。
对甲醇合成而言,无论是锌铬催化剂还是铜基催化剂,其多相(非匀相)催化过程均按下列过程进行:①扩散——气体自气相扩散到气体一催化剂界面;②吸附——各种气体组分在催化剂活性表面上进行化学吸附;③表面吸附——化学吸附的气体,按照不同的动力学假说进行反应形成产物;④解析——反应产物的脱附;⑤扩散——反应产物自气体一催化剂界面扩散到气相中去。
甲醇合成反应的速率,是上述五个过程中的每一个过程进行速率的总和,但全过程的速率取决于最慢步骤的完成速率。
研究证实,过程①与⑤进行得非常迅速,过程②与④的进行速率较快,而过程③分子在催化剂活性界面的反应速率最慢,因此,整个反应过程的速率取决于表面反应的进行速率。
提高压力、升高温度均可使甲醇合成反应速率加快,但从热力学角度分析,由于CO、C02和H2合成甲醇的反应是强放热的体积缩小反应,提高压力、降低温度有利于化学平衡向生成甲醇的方向移动,同时也有利于抑制副反应的进行。
合成气生产甲醇工艺流程
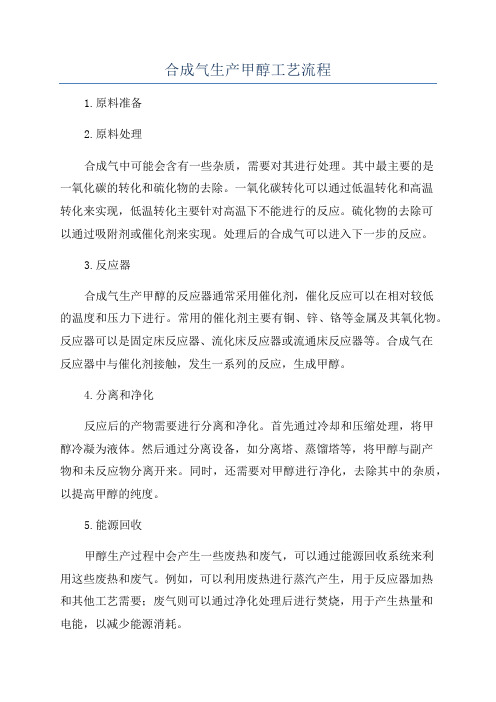
合成气生产甲醇工艺流程1.原料准备2.原料处理合成气中可能会含有一些杂质,需要对其进行处理。
其中最主要的是一氧化碳的转化和硫化物的去除。
一氧化碳转化可以通过低温转化和高温转化来实现,低温转化主要针对高温下不能进行的反应。
硫化物的去除可以通过吸附剂或催化剂来实现。
处理后的合成气可以进入下一步的反应。
3.反应器合成气生产甲醇的反应器通常采用催化剂,催化反应可以在相对较低的温度和压力下进行。
常用的催化剂主要有铜、锌、铬等金属及其氧化物。
反应器可以是固定床反应器、流化床反应器或流通床反应器等。
合成气在反应器中与催化剂接触,发生一系列的反应,生成甲醇。
4.分离和净化反应后的产物需要进行分离和净化。
首先通过冷却和压缩处理,将甲醇冷凝为液体。
然后通过分离设备,如分离塔、蒸馏塔等,将甲醇与副产物和未反应物分离开来。
同时,还需要对甲醇进行净化,去除其中的杂质,以提高甲醇的纯度。
5.能源回收甲醇生产过程中会产生一些废热和废气,可以通过能源回收系统来利用这些废热和废气。
例如,可以利用废热进行蒸汽产生,用于反应器加热和其他工艺需要;废气则可以通过净化处理后进行焚烧,用于产生热量和电能,以减少能源消耗。
6.产品储存和包装最后,甲醇可以通过储罐进行储存,并进行相应的包装和运输,以供应市场需求。
合成气生产甲醇的工艺流程基本上包括了原料准备、原料处理、反应器、分离和净化、能源回收以及产品储存和包装等步骤。
整个工艺需要进行精细的控制和操作,以确保产品的质量和工艺的稳定性。
同时,还应注意环境保护措施,减少对环境的影响。
- 1、下载文档前请自行甄别文档内容的完整性,平台不提供额外的编辑、内容补充、找答案等附加服务。
- 2、"仅部分预览"的文档,不可在线预览部分如存在完整性等问题,可反馈申请退款(可完整预览的文档不适用该条件!)。
- 3、如文档侵犯您的权益,请联系客服反馈,我们会尽快为您处理(人工客服工作时间:9:00-18:30)。
合成气制备甲醇原理与工艺简要概述班级:xxxxxxxxxxxxxxxxxxxxx专业:化学工程与工艺姓名:xxxxx学号:************指导教师:xxxxx一、甲醇的认识1.物理性质无色透明液体,易挥发,略带醇香气味;易吸收水分、CO2和H2S,与水无限互溶;溶解性能优于乙醇;不能与脂肪烃互溶,能溶解多种无机盐磺化钠、氯化钙、最简单的饱和脂肪醇。
2.化学性质3.甲醇的用途(1)有机化工原料甲醇是仅次于三烯和三苯的重要基础有机化工原料(2)有机燃料(1)、甲醇汽油混合燃料;(2)、合成醇燃料;(3)、与异丁烯合成甲基叔丁基醚(MTBE)、高辛烷值无铅汽油添加剂;(4)、与甲基叔戊基醚(TAME)合成汽油含氧添加剂4.甲醇的生产原料甲醇合成的原料气成分主要是CO 、 CO2、 H2 及少量的N2 和CH4。
主要有煤炭、焦炭、天然气、重油、石脑油、焦炉煤气、乙炔尾气等。
天然气是生产甲醇、合成氨的清洁原料,具有投资少、能耗低、污染小等优势,世界甲醇生产有90%以上是以天然气为原料,煤仅占 2%。
二、合成气制甲醇的原理1.合成气的制备a.煤与空气中的氧气在煤气化炉内制得高 CO 含量的粗煤气;b.经高温变换将 CO 变换为 H2 来实现甲醇合成时所需的氢碳比;c.经净化工序将多余的 CO2 和硫化物脱除后即是甲醇合成气。
说明:由于煤制甲醇碳多氢少,必需从合成池的放气中回收氢来降低煤耗和能耗,回收的氢气与净化后的合成气配得生产甲醇所需的合成气, 即( H2-CO2) /( CO+CO2)=2.00~2.05。
2.反应机理主反应OH CH H CO 322→+ △H 298=-90.8kJ/molCO 2 存在时 O H OH CH H CO 23222+→+ △H 298=-49.5kJ/mol副反应O H OCH CH H CO 233242+→+O H CH H CO 2423+→+O H OH H C H CO 2942384+→+O H CO H CO 222+→+增大压力、低温有利于反应进行,但同时也有利于副反应进行,故通过加入催化剂,提高反应的选择性,抑制副反应的发生。
3. 影响合成气制甲醇的主要因素(1)合成甲醇的工业催化剂1)分类a.锌铬催化剂:1966年以前几乎所有厂家都使用该催化剂,目前逐渐被淘汰;b.铜基催化剂:铜铬铝系和铜锌铬系得到广泛应用;c.钯系催化剂:未工业化;d.低温液相催化剂:未工业化。
2)特点3)注意①为延长催化剂寿命,开始应用较低温度,过一定时间再升至适宜温度,其后随着催化剂老化程度升高,反应程度也相应的变高;②因反应放热,反应热应及时移出,否则副反应增加,催化剂易烧结,活性降低。
故严格控制温度,及时有效地移走反应热是合成塔设计、操作的关键。
(2)空速空速:影响选择性和转化率,直接关系到催化剂的生产能力和单位时间的放热量。
适宜的空速与催化剂的活性、反应温度及进塔气体的组成有关ZnO-Cr2O3: 20000-40000h-1CuO-ZnO-Al2O3: 10000h-1注意:a.增加空速在一定程度上能够增加甲醇产量;b.增加空速有利于反应热的移出,防止催化剂过热;c.空速太高:转化率降低,循环气量增加,从而增加能量消耗;增加分离设备和换热负荷,引起甲醇分离效果降低;带出热量太多,造成合成塔内的催化剂温度难以控制。
(3)原料气组成甲醇合成原料气化学计量比约为 H2︰CO=2︰1CO含量:不利温度控制;引起羰基铁在催化剂上的积聚,使催化剂失活,一般采用氢过量。
H2过量: 抑制高级醇、高级烃和还原性物质的生成,提高甲醇的浓度和纯度; 氢导热性好,利于防止局部过热和催化剂床层温度控制。
Zn-Cr2O3: H2与CO比约为4.5;铜基催化剂: H2与CO比为2.2- 3.0四、生产甲醇的工艺流程(一)生产工序甲醇生产流程图1.原料气的制备合成甲醇,首先是制备原料氢和碳的氧化物。
(已述)2.净化净化有两个方面:一是脱除对甲醇合成催化剂有毒害作用的杂质,如含硫的化合物。
原料气中硫的含量即使降至1ppm,对铜系催化剂也有明显的毒害作用,因而缩短其使用寿命,对锌系催化剂也有一定的毒害。
经过脱硫,要求进入合成塔气体中的硫含量降至小于0.2ppm。
脱硫的方法一般有湿法和干法两种。
二是调节原料气的组成,使氢碳比例达到前述甲醇合成的比例要求,其方法有两种。
(1)变换。
如果原料气中一氧化碳含量过高(如水煤气、重质油部分氧化气),则采取蒸汽部分转换的方法,使其形成如下变化反应:CO+H2O H2 + CO2。
增加有效组分氢气,从而提高了系统中能的利用效率。
(2)脱碳。
如果原料气中二氧化碳含量过多,使氢碳比例过小,可以采用脱碳方法除去部分二氧化碳。
脱碳方法一般采用溶液吸收,有物理吸收和化学吸收两种方法。
3.压缩通过往复式或透平式压缩机,将净化后的气体压缩至合成甲醇所需要的压力,压力的高低主要视催化剂的性能而定。
4.合成根据不同的催化剂,在不同的压力下,温度为240~270℃或360~400℃,通过催化剂进行合成反应,生成甲醇。
由于受催化剂选择性的限制,生成甲醇的同时,还有许多副反应伴随发生,所以得到的产品是以甲醇为主和水以及多种有机杂质混合的溶液,即粗甲醇。
5.蒸馏粗甲醇通过蒸馏方法清除其中有机杂质和水,而制得符合一定质量标准的较纯的甲醇,称精甲醇。
同时,可能获得少量副产物。
(二)、常用的反应器:1.气固催化反应器气固催化反应器甲醇合成装置国内外 30 万 t 以上装置使用的甲醇合成塔,虽然塔型较多, 归纳起来主要有以下五类:①冷管式合成塔这种合成塔源于氨合成塔, 在催化剂内设置足够换热面积的冷气管, 用进塔冷管来移走反应热。
这种塔型碳转化率较高但仅能在出塔气中副产 0.4MPa 的低压蒸汽。
目前大型装置中很少采用。
②激式合成塔这是最早的低压甲醇合成塔, 是用进塔冷气冷激来带走反应热。
该塔结构简单, 也适于大型化。
但碳的转化率低, 出塔的甲醇浓度低, 循环量大, 能耗高, 又不能副产蒸汽。
现基本已淘汰。
③多床内换热式合成塔这种合成塔由大型氨合成塔发展而来。
目前氨合成塔均采用三床 ( 四床) 内换热式合成塔。
针对甲醇合成的特点采用四床(或五床)内换热式合成塔.各床层是绝热反应, 在各床出口将热量移走。
这种塔型结构简单, 造价低, 不需特种合金钢, 转化率高, 适合于大型或超大型装置, 但反应热不能全部直接副产中压蒸汽。
④固定管板列管合成塔这种合成塔就是一台列管换热器, 催化剂在管内, 管间(壳程)是沸腾水, 将反应热用于副产 3.0MPa~4.0MPa 的中压蒸汽。
固定管板列管合成塔虽然可用于大型化, 但受管长、设备直径、管板制造所限。
在日产超过 2 000t时, 往往需要并联两个。
这种合成塔由于列管需用特种不锈钢, 因而是造价最高的一种。
⑤水管式合成塔将床层内的传热管由管内走冷气改为走沸腾水。
这样可较大地提高传热系数, 更好地移走反应热, 缩小传热面积, 多装催化剂, 同时可副产 2.5MPa ~4.0MPa 的中压蒸汽, 是大型化较理想的塔型。
最近在国外 60 万 t 以上大型装置大为推广。
综上所述:大型合成塔的选用原则是,大型装置不宜选用激冷式和冷管式塔; 列管式合成塔虽目前国内用得最多, 但价格昂贵; 大型厂宜用水管式合成塔、多床内换热式合成塔和固定管板的列管式合成塔; 在串塔流程或双级流程中也可采用两种塔型组合。
2.气液固三相反应器(1)三相床反应过程的主要特点①床层的等温性导热系数大、热容大的惰性液相热载体,高度湍动的气-液-固三相导致反应热迅速分散和传向冷却介质,使得床层接近等温。
因而,优于气-固催化法:不会出现床层温度不合理分布;不会出现局部过热;不会对催化剂和设备造成危害。
②反应的高效性细颗粒催化剂的采用;高浓度反应组分(CO、H2)采用的可能性;较佳温度的维持催化剂内表面利用率极高;高浓度反应组分有利于正反应速率;较佳的温度兼顾了平衡推动力,因此,可获得较大的原料气转化率和主产物选择性。
③操作的可塑性优良的传热性能与合理的产气配置极低的床层压降, 操作气速(或质量空速)可在较大范围内变化而反应器内仍能正常稳定操作。
这是气-固相催化法不可能的;主要取决于起始流化速度与床层节涌速度;与分布器的类型、设计参数和反应器的结构设计有关。
(2)主要反应器由于气-液-固三相物料在过程中的流动状态不同, 三相反应器主要有:滴流床、浆态床、搅拌釜、流化床、携带床1)滴流床反应器在甲醇合成中应用操作过程:滴流床反应器与传统的固定床反应器的结构类似, 由颗粒较大的催化剂组成固定层, 液体以液滴方式自上而下流动, 气体一般也是自上而下流动,气体和液体在催化剂颗粒间分布。
滴流床兼有浆态床和固定床的优点, 与固定床相类似。
它的催化剂装填量大且无磨蚀, 床层中的物料流动接近于活塞流且无返混现象存在, 同时它又具备浆态床高转化率等温反应的优点, 适合于低氢碳比的合成气。
2)浆态床工艺操作过程:催化剂呈极细的粉末分布在溶中,进行甲CO和H2合成原料气经压缩,从反应器以鼓泡方式进入催化剂浆态床中,气体在搅拌桨或是气流的搅动作用下形成分散的细小气泡在反应器内运动。
醇的合成反应,反应热被液态烃所吸收,反应后的气体和液态烃从塔顶排出,进入初级气液分离器,分离出的液体烃经换热返回反应器。
气体与原料气进行换热交换,并在次级气液分离器进一步分离,甲醇产品经冷却,分离和脱气后送甲醇储罐,未经转化的气体少部分放空,大部分循环使用。
注意:浆态床反应器中催化剂悬浮量过大时, 会出现催化剂沉降和团聚现象。
要避免这些现象的发生, 就得加大搅拌器功率, 但这同时使得搅拌桨和催化剂的磨蚀加大, 反应中的返混程度增加。
这种料浆反应器催化剂的装填量有一定的限度, 所以操作中空速不能太大(三)工艺流程工业上合成甲醇工艺流程主要有高压法和中、低压法。
1.高压法合成甲醇的工艺流程高压法工艺流程一般指的是使用锌铬催化剂,在高温高压下合成甲醇的流程,如图所示。
由压缩工段送来的新鲜原料气,先进入铁油分离器(5),在此与循环压缩机(4)送来的循环气汇合。
这两种气体中的油污、水雾及羰基化合物等杂质同时在铁油分离器中除去,然后进入甲醇合成塔(1)。
CO与H2在塔内于30MPa左右压力和360~420℃温度下,在锌铬催化剂上反应生成甲醇。
转化后的气体经塔内热交换预热刚进入塔内的原料气,温度降至160℃以下,甲醇含量约为3%。
经塔内热交换后的转化气体混合物出塔,进入喷淋式冷凝器(2),出冷凝器后混合物气体温度降至30~35℃,再进入高压甲醇高压法合成甲醇工艺流程图1-合成塔;2-水冷凝器;3-甲醇分离器;4-循环压缩机;5-铁油分离器;6-粗甲醇中间槽分离器(3)。