无损检测综合知识介绍资料
《无损检测基础知识》课件
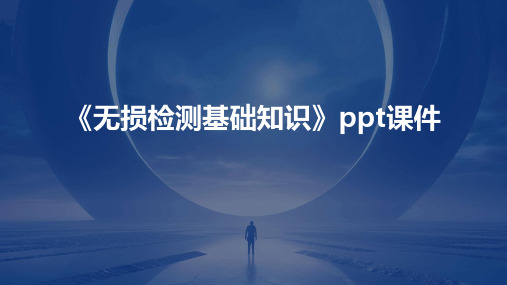
无损检测在轨道交通领域的应用实例
车辆关键部位检测
无损检测技术用于检测轨 道交通车辆的关键部位, 如车轮、转向架和车体的 疲劳裂纹和腐蚀。
轨道裂纹检测
通过无损检测技术,对轨 道的裂纹进行检测,确保 列车运行的安全性和稳定 性。
信号系统元件检测
无损检测用于评估信号系 统元件的完整性和可靠性 ,保障列车的正常运行。
无损检测还可以对产品进行可靠性评估和寿命预测,为产品的维护和更新提供科学 依据。
无损检测的应用领域
航空航天
无损检测在航空航天领域中广 泛应用于发动机、机身、机翼 等关键部件的检测,确保其质
量和安全性。
轨道交通
在轨道交通领域,无损检测用 于列车轮毂、车轴、转向架等 关键部件的检测,确保列车运 行安全。
报告编写
将整个检测过程和结果整理成 报告,并提交给相关部门或客 户。
无损检测的注意事项
01
02
03
04
安全性
确保检测过程中操作人员的安 全,采取必要的安全措施,如
佩戴防护眼镜、手套等。
准确性
确保检测结果的准确性,对设 备和器材进行定期校准和维护
。
可靠性
确保检测结果的可靠性,对检 测过程进行严格的质量控制。
无损检测技术涉及声学、光学、电学、磁学 、热学等多个学科领域,具有广泛的应用前
景。
无损检测的重要性
无损检测在工业生产中具有重要意义,能够提高产品质量、降低生产成本、避免因 破坏性检测而导致的损失。
通过无损检测,可以在生产过程中对原材料、零部件进行质量把关,及时发现缺陷 和问题,避免产品在使用过程中出现故障或事故。
《无损检测基础知识》ppt课件
contents
第4章无损检测基础知识

射线 铸件、焊件 表面及内部缺 陷 由照相底片或 荧光屏观察
超声 铸、锻、焊 件及板材 表面及内部 缺陷 根据回波信 号分析
磁粉
涡流
渗透 各种工件 表面缺陷 根据显示直 接观察
典型应用 探出缺陷 判伤方法
铸、锻、焊 棒、线、管 及冲压件等 材各种工件 表面及近表 表面及近表 面缺陷 面缺陷 根据磁痕直 仪表指标报 接观察 警
5)衰减特性:超声波在传播过程中,由于受到
介质及其中杂质的阻碍或吸收,其强度会产生衰 减,因此要对各种衰减进行抑制。
3. 超声波的基本参数 1)振幅:振动质点偏离平衡位置的最大距离。 2)频率(f):单位时间内质点完成全振动的次
数。其值与波动频率相等,所谓波动频率是指波 动过程中任一给定质点在单位时间内通过完整波 的个数。 3)周期(t):振动质点完成一次全振动所需要 的时间,单位为s。 4)波长(λ):单位为mm或m,波长越短分辨 力越高。 5)声速(c):单位为m/s或km/s。
质点振动方向与波的传播方向垂直 横波S(剪切波、切变波) ,只能在固体中传播。
机械波
表面波R(瑞利波)
质点的振动沿材料表面进行传播, 只能在固体中传播。 仅在频率、入射角及板厚为特定 值时才产生。按振动形态可分为 对称型和非对称型两种。只能在 厚度与波长相当的薄板中传播。
板波P(兰姆波)
纵波L
横波S
2.无损检测的作用 无损检查是提高产品质量,确保安全的重要手段 ,具有很大的经济效益和社会效益,其作用主要
有:
(1)无损探伤—对产品质量做出评价。通过对 构件等进行探测发现其表面或内部缺陷,并进行 定位定量分析。 (2)材料检查—用无损检测技术测定材料的物
理性能和组织结构,能判断材料的品种和热处理
NDT 无损检测知识大全

厚度和密度[物体材料的种类]、射线种类及其穿透距离。当物体中存在缺陷时,由于缺陷部 位的厚度和密度发生变化,穿过无缺陷完好部位和有缺陷部位的射线强度不同,因而使胶片 的感光程度不同,胶片处理后,就形成了黑白不同的影像。
射线照相法探伤是利用物质在密度不同、厚度不同时对射线的吸收程度不同(即使射 线的衰减程度不同),就会使零件下面的底片感光不同的原理,实现对材料或零件内部 质量的照相探伤。
一些其他信息,例如结构、性质、状态等,并试图通过测试掌握更多的信息。 无损评价(NDE):是将进入或目前正在进入的新阶段的名称,其内涵不仅仅是探测缺
陷、探测试件的结构、性质、状态,还要获取更全面、更深刻的、更准确的综合信息, 例如缺陷的形状、尺寸、位置、取向、缺陷部位的金相组织、残余应力等。
常用常规无损检测方法 1. 射线检测(Radiographic,简称RT) 2. 超声波检测(Ultrasonic Testing,简称UT) 3. 磁粉检测(Magnetic Testing,简称MT) 4. 渗透检测(Penetrant Testing,简称PT) 5. 涡流检测(Eddy Current,简称ET) 6. 声发射检测(Acoustic Emission,简称AE)
射线检测主要适用于体积型缺陷,如气孔等的检测;在特定的条件下,也可检测裂纹、 未焊透、未熔合等缺陷。
无损检测-全面

第5章无损检测5.1 无损检测简介在锅炉压力容器构件及焊缝的表面或内部,常常存在一些影响安全使用的缺陷,如裂纹、分层、夹渣、气孔、未熔合和未焊透等,这些缺陷的性质、尺寸和位置等是评价被检工件能否继续生产或正常使用的重要依据。
传统的破坏性检查即切割开后目视检查可检测上述缺陷,但因费用高、时间长、损伤大使各方面难以接受。
无损检测是在不损伤被检工件情况下,利用材料和材料中缺陷所具有的光学、声学、电磁学和流体力学等方面的特性检查材料中缺陷性质、尺寸和位置的方法。
因其具有费用低、时间短、无损伤等优点而得到广泛的应用。
本章扼要地介绍下列几种主要无损检测方法的原理、方式、操作程序等项内容。
5.2 焊缝射线透照检测RT5.2.1 射线的性质及其产生5.2.1.1 X射线、γ射线的性质X射线是一种类似于光、热和无线电波的电磁辐射波。
γ射线是某些放射性辐射元素在衰变过程中以电磁辐射形式所释放出来的一种能量。
射线的基本性质已为人们所掌握,概括起来有如下几点:⑴射线是不可见的。
⑵射线是直线传播的,传播速度与可见光一样(30万km/秒)。
⑶射线不受电场、磁场的作用。
⑷射线不能使用光学透镜、棱镜以及在电场、磁场中产生偏转的方法来改变其传播方向。
⑸射线到达物体后,其能量的传递以穿透为主,但仍有一小部分能量能产生反射、衍射、折射现象。
⑹射线能使空气电离。
⑺射线能杀伤生物细胞,对遗传因子也有影响。
因此,要特别注意免遭其害。
⑻某些物质吸收射线后,能发生莹光或激发光电子、反冲电子和二次电子使X射线胶片感光。
5.1.2.1X射线是在高速运动的电子和物体碰撞时产生的。
工业用X 射线一般是借助于X射线管而获得的(图5—1)。
X射线管内的真空度为10-6~10-7毫米水银柱高,管内的阴极是一个直径很小螺旋形钨丝,当有电流I通过时,就在其周围产生电子。
管内的阳极靶一般用耐高温的钨做成。
在阴极和阳极间施加高电压(工业通常采用150~420kv)使阳极带有正电荷,阴极产生的电子在高电压形成的静电场作用下以极高速度射向阳极靶,因受靶材料的原子阻挡,电子速度骤然下降,失去功能。
无损检测综合知识
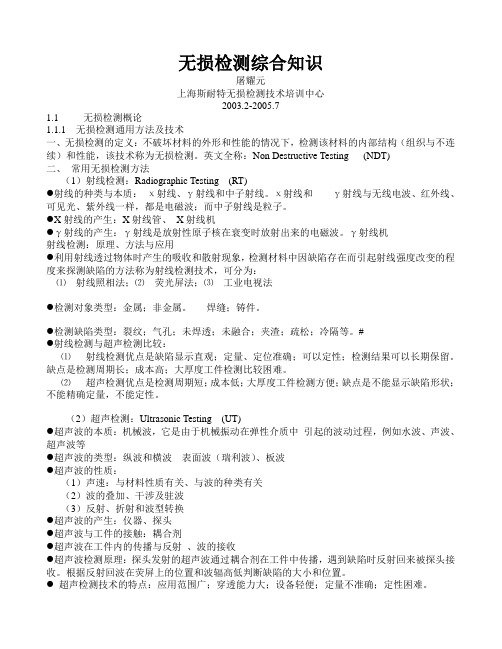
无损检测综合知识屠耀元上海斯耐特无损检测技术培训中心2003.2-2005.71.1 无损检测概论1.1.1 无损检测通用方法及技术一、无损检测的定义:不破坏材料的外形和性能的情况下,检测该材料的内部结构(组织与不连续)和性能,该技术称为无损检测。
英文全称:Non Destructive Testing (NDT)二、常用无损检测方法(1)射线检测:Radiographic Testing (RT)●射线的种类与本质:χ射线、γ射线和中子射线。
χ射线和γ射线与无线电波、红外线、可见光、紫外线一样,都是电磁波;而中子射线是粒子。
●X射线的产生:X射线管、X射线机●γ射线的产生:γ射线是放射性原子核在衰变时放射出来的电磁波。
γ射线机射线检测:原理、方法与应用●利用射线透过物体时产生的吸收和散射现象,检测材料中因缺陷存在而引起射线强度改变的程度来探测缺陷的方法称为射线检测技术,可分为:⑴射线照相法;⑵荧光屏法;⑶工业电视法●检测对象类型:金属;非金属。
焊缝;铸件。
●检测缺陷类型:裂纹;气孔;未焊透;未融合;夹渣;疏松;冷隔等。
#●射线检测与超声检测比较:⑴射线检测优点是缺陷显示直观;定量、定位准确;可以定性;检测结果可以长期保留。
缺点是检测周期长;成本高;大厚度工件检测比较困难。
⑵超声检测优点是检测周期短;成本低;大厚度工件检测方便;缺点是不能显示缺陷形状;不能精确定量,不能定性。
(2)超声检测:Ultrasonic Testing (UT)●超声波的本质:机械波,它是由于机械振动在弹性介质中引起的波动过程,例如水波、声波、超声波等●超声波的类型:纵波和横波表面波(瑞利波)、板波●超声波的性质:(1)声速:与材料性质有关、与波的种类有关(2)波的叠加、干涉及驻波(3)反射、折射和波型转换●超声波的产生:仪器、探头●超声波与工件的接触:耦合剂●超声波在工件内的传播与反射、波的接收●超声波检测原理:探头发射的超声波通过耦合剂在工件中传播,遇到缺陷时反射回来被探头接收。
无损检测基础知识-2012
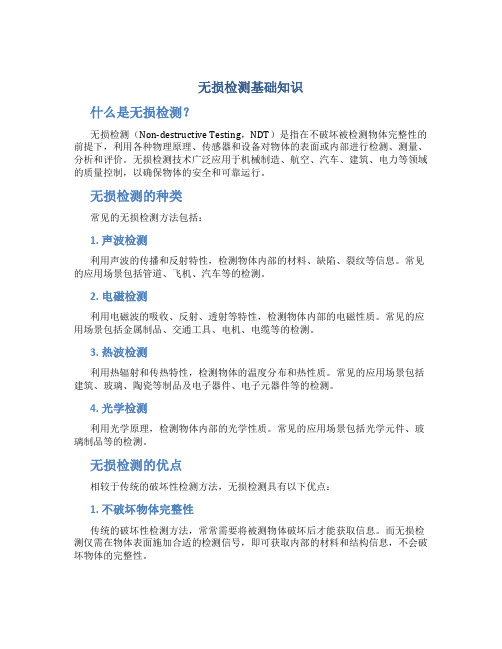
无损检测基础知识什么是无损检测?无损检测(Non-destructive Testing,NDT)是指在不破坏被检测物体完整性的前提下,利用各种物理原理、传感器和设备对物体的表面或内部进行检测、测量、分析和评价。
无损检测技术广泛应用于机械制造、航空、汽车、建筑、电力等领域的质量控制,以确保物体的安全和可靠运行。
无损检测的种类常见的无损检测方法包括:1. 声波检测利用声波的传播和反射特性,检测物体内部的材料、缺陷、裂纹等信息。
常见的应用场景包括管道、飞机、汽车等的检测。
2. 电磁检测利用电磁波的吸收、反射、透射等特性,检测物体内部的电磁性质。
常见的应用场景包括金属制品、交通工具、电机、电缆等的检测。
3. 热波检测利用热辐射和传热特性,检测物体的温度分布和热性质。
常见的应用场景包括建筑、玻璃、陶瓷等制品及电子器件、电子元器件等的检测。
4. 光学检测利用光学原理,检测物体内部的光学性质。
常见的应用场景包括光学元件、玻璃制品等的检测。
无损检测的优点相较于传统的破坏性检测方法,无损检测具有以下优点:1. 不破坏物体完整性传统的破坏性检测方法,常常需要将被测物体破坏后才能获取信息。
而无损检测仅需在物体表面施加合适的检测信号,即可获取内部的材料和结构信息,不会破坏物体的完整性。
2. 检测精度高无损检测能够准确地测量物体的内部材料、缺陷、裂纹等信息,相较于传统的视觉检测或测量方法,具有更高的检测精度和可靠性。
3. 检测速度快传统的破坏性检测方法常常需要进行破坏实验,且需要长时间的等待和处理。
而无损检测方法通常能够快速、准确地得出检测结果,提高检测效率和缩短检测时间。
无损检测技术是一项重要的质量控制和评价手段,广泛应用于各种制造、工程、科研领域。
本文介绍了无损检测的种类、优点和应用场景,希望能够对相关领域的工作者和学习者有所帮助。
无损检测介绍
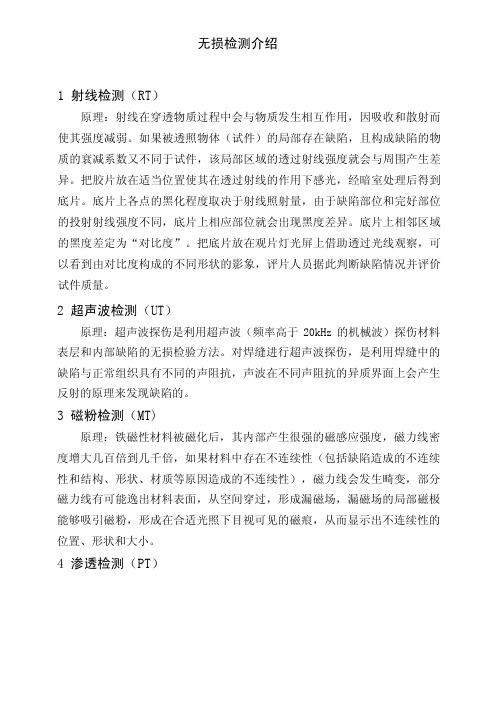
无损检测介绍1 射线检测(RT)原理:射线在穿透物质过程中会与物质发生相互作用,因吸收和散射而使其强度减弱。
如果被透照物体(试件)的局部存在缺陷,且构成缺陷的物质的衰减系数又不同于试件,该局部区域的透过射线强度就会与周围产生差异。
把胶片放在适当位置使其在透过射线的作用下感光,经暗室处理后得到底片。
底片上各点的黑化程度取决于射线照射量,由于缺陷部位和完好部位的投射射线强度不同,底片上相应部位就会出现黑度差异。
底片上相邻区域的黑度差定为“对比度”。
把底片放在观片灯光屏上借助透过光线观察,可以看到由对比度构成的不同形状的影象,评片人员据此判断缺陷情况并评价试件质量。
2 超声波检测(UT)原理:超声波探伤是利用超声波(频率高于20kHz的机械波)探伤材料表层和内部缺陷的无损检验方法。
对焊缝进行超声波探伤,是利用焊缝中的缺陷与正常组织具有不同的声阻抗,声波在不同声阻抗的异质界面上会产生反射的原理来发现缺陷的。
3 磁粉检测(MT)原理:铁磁性材料被磁化后,其内部产生很强的磁感应强度,磁力线密度增大几百倍到几千倍,如果材料中存在不连续性(包括缺陷造成的不连续性和结构、形状、材质等原因造成的不连续性),磁力线会发生畸变,部分磁力线有可能逸出材料表面,从空间穿过,形成漏磁场,漏磁场的局部磁极能够吸引磁粉,形成在合适光照下目视可见的磁痕,从而显示出不连续性的位置、形状和大小。
4 渗透检测(PT)原理:零件表面被试涂含有荧光染料或着色染料的渗透液后,在毛细管作用下,经过一定时间,渗透液可以渗进表面开口的缺陷中;经过除零件表面多余的渗透液后,再在零件表面施涂显象剂,同样,在毛细管作用下,显象剂将吸引缺陷中保留的渗透液,渗透液回渗到显象剂中;在一定的光源下(紫外线光或白光),缺陷处的渗透液痕迹被显示(黄绿色荧光或鲜艳红色),从而探测出缺陷的形貌及分布状态。
无损检测知识点总结

无损检测知识点总结导言无损检测是现代工程领域中一项非常重要的技术,它通过使用一系列的检测方法和设备,来对材料和构件进行检测,以发现其中可能存在的缺陷和问题。
无损检测方法可以帮助工程师和技术人员及时发现并解决问题,确保工程的安全性和可靠性。
本文将对无损检测的基本知识点进行总结,包括常用的无损检测方法、设备及应用实例等。
一、无损检测方法无损检测方法是指在不破坏被检测材料的前提下,利用物理、化学、超声波、磁力学、光学以及计算机技术等方法进行对被检测材料缺陷的检测。
目前常用的无损检测方法主要包括以下几种:1. 超声波检测(UT)超声波检测是利用超声波在被检材料中传播的变化规律,来检测材料中的缺陷。
通过测量超声波的传播速度和反射波的能量,可以获取材料内部的缺陷信息,如裂纹、气泡、夹杂物等。
超声波检测方法可以分为接触式超声波检测和非接触式超声波检测两种。
2. 射线检测(RT)射线检测是利用射线照射被检材料,通过测量射线的衰减和散射来检测材料中的缺陷。
射线检测方法可以分为X射线检测和γ射线检测两种,常用于金属材料中裂纹、气泡等缺陷的检测。
3. 磁粉检测(MT)磁粉检测是利用磁场对被检材料进行磁化,并在磁场下添加磁粉颗粒,通过观察磁粉颗粒在被检材料表面的分布情况,来检测材料中的缺陷。
磁粉检测方法可以快速、高效地检测材料表面和近表面的缺陷,如裂纹、疲劳等。
4. 涡流检测(ET)涡流检测是利用涡流流动的规律,对被检材料进行缺陷检测。
当电磁场作用于导电材料时,会在材料中产生涡流,通过测量涡流的衰减和变化,可以发现材料中的缺陷。
涡流检测方法通常用于金属材料中的裂纹、夹杂物等缺陷的检测。
5. 磁记号检测(MPI)磁记号检测是利用磁场对被检材料进行磁化,并在磁场中添加磁记号液体,通过观察磁记号液体在材料表面的分布情况,来检测材料中的缺陷。
磁记号检测方法通常用于金属材料中裂纹、焊缝、表面夹杂物等缺陷的检测。
6. 热红外检测(IRT)热红外检测是利用红外热像仪和红外热辐射技术,对被检材料进行缺陷检测。
- 1、下载文档前请自行甄别文档内容的完整性,平台不提供额外的编辑、内容补充、找答案等附加服务。
- 2、"仅部分预览"的文档,不可在线预览部分如存在完整性等问题,可反馈申请退款(可完整预览的文档不适用该条件!)。
- 3、如文档侵犯您的权益,请联系客服反馈,我们会尽快为您处理(人工客服工作时间:9:00-18:30)。
及玻璃制品。
液体渗透检测法的优点有: (1)不受被检试件几何形状、尺寸大小、化学成分和内部组织 结构的限制,也不受缺陷方位的限制,一次操作可同时检验开口于 表面的所有缺陷;
(2)检验的速度快,操作比较简便,大量的零件可以同时进行
批量检验; (3)缺陷显示直观,检测灵敏度高。
渗透检验的主要局限性有: (1)最主要的局限性是只能检出试件开口于表 面的缺陷,不能显示缺陷的深度及缺陷内部的形状 和大小; (2)无法或难于检查多孔的材料,表面粗糙时, 也会使试件表面的本底颜色或荧光底色增大,掩盖 了细小的、分散的缺陷; (3)检测结果受操作者的影响较大。
相法成为各种无损检测方法记录最真实、最直观、最全面、追踪性最好 的检测方法。
(2)可以获得缺陷的投影图像,缺陷定性定量准确
各种无损检测方法中,射线照相相对缺陷定性定量是最准的。在定
量方面,对体积型缺陷(气孔、夹渣类)的长度、宽尺寸的确定也很准,
其误差大致在零点几毫米。但对面积型缺陷(如裂纹、未熔合类),如 缺陷端部尺寸(高度和张口宽度)很小,则底片上影像尖端延伸可能辨
别不清,此时定量数据会偏小。
(3)体积型缺陷检出率很高,而面积型缺陷的检出率受到多
种因素影响 体积型缺陷一般情况下,直径在试件厚度的1%以上的体积型 缺陷可以检出。在薄试件中,可检出缺陷的最小尺寸受人眼分辨 率的限制,可达0.5mm或更小。面积型缺陷其检出率的影响因素 包括缺陷形态尺寸、透照厚度、透照角度、透照几何条件、源和 胶片种类、像质计灵敏度等。虽然如此,一般可以说厚试件中的
•图1 射线检测的基本原理
X
射
线
探
伤
机
2、射线检测技术应用及特点 射线检测技术在工业方面的主要应用可归纳为下 列三个方面: (1)制造工艺缺陷与服役缺陷检验; (2)密度、尺寸、厚度等的测量; (3)结构、装配质量检测。
特点:
(1)检测结果有直接记录——底片
由于底片上记录的信息十分丰富,且可以长期保存,从而使射线照
在评价某个无损检测结论的可靠性时,必须注意
无损检测技术的上述特点!即,对某些无损检测技术
必须考虑检验人员的技术资格。
二、 常用无损检测技术介绍
(一)射线检测技术
1、射线检测技术原理 当强度均匀的射线束透照物体时,如果物体的 局部区域存在缺陷或结构存在差异,它将改变物体 对射线的衰减,使得不同部位透射射线强度不同, 采用一定的检测器(例如胶片)检测透射射线强度, 就可以判断物体内部的缺陷和物质分布。
三、对送检零件的具体要求
(一)射线检测
1、送交射线检验的工件应经表面检验合格; 2、送检前,应清除妨碍检验和影响底片上缺陷影 像辨认的多余物; 3、对于铸件,应清除型砂、型芯、金属屑及油污, 切除后的浇、冒口残余量不得超过透照部位厚度的10%; 4、对于焊接件,应清除表面氧化皮、油污。
(二)超声检测
隔和疏松等缺陷;
(2)具有很高的检验灵敏度;
(3) 能直观地显示缺陷的位置、形状和尺寸,从显示
的磁粉痕迹能对缺陷性质作出判断 ; (4)检验几乎不受工件的大小和形状的限制。
磁粉检测的局限性是:
(1)只能适用于铁磁性材料,而且只能检查出工
件表面和近表面的缺陷,一般深度不超过1~2mm;
(2)如果工件表面有覆盖层、涂层、喷丸层等,
术,是焊接件、胶接质量、蜂窝夹层结构、大型铸件常用的检验技术。
超声检测的优点: (1)适用于金属、非金属、复合材料等多种材料制件的无损评价; (2)穿透力强,可对较大厚度范围的试件内部缺陷进行检测,可 以检测几米厚的钢锻件,适合于检测方向性强的缺陷;
(3)可较准确的测定缺陷的深度位置;
(4)对大多数超声技术的应用来说,仅需从一侧接近试件; (5)设备轻便,对人体无伤害。
无损检测基本知识介绍
航天三院159厂 张祥林
一、无损检测技术概述
(一)无损检测技术的内涵
无损检测是指以不损及其将来使用和使用可靠性
的方式,对材料或制件或此两者进行宏观缺陷检测,
几何特性测量,化学成分、组织结构和力学性能变化
的评价,并进而就材料或制件对特定应用的适用性进 行评价的一门学科。
具体地完成三方面的工作:
射线机透照厚度均小于100mm,对厚度大于100mm的工件照相
需使用加速器或Co60,因此是比较困难的。此外,板厚增大,射 线照相绝对灵敏度是下降的,也就是说对厚工件采用射线照相, 小尺寸缺陷以及一些面积型缺陷漏检的可能性增大。
(5)适宜检测对接焊缝,检测角焊缝效果较差,不适宜检测板材、 楱材、锻件
1、受检件表面不允许存在氧化皮、折叠、毛刺、 油污等; 2、受检件表面的粗糙度,对于AAA级检验, Ra应不大于1.6um;对于AA级或A级检验, Ra应 不大于3.2um;对于B级检验, Ra应不大于6.3um。
(三) 磁粉检测
(1)送检零件应清除油污、毛刺、砂粒、氧化皮、 金属屑等杂物; (2)凡能分解的组合件,应分解为单个零件进行送 检; (3) 对零件上有小开口和导向内腔的输油孔应加
(1)检验(检验,定位,测量,评定)材料或工件中的 缺陷; (2)评定材料或工件的完整性、性能和组成; (3)测定材料或工件的几何特性。
(二)无损检测技术体系
1 、无损检测技术的发展阶段
20世纪二十年代 进入工业领域
五十年代以前 常规无损检测技术 五十年代至七十年代 完善、改进、研究
九十年代以后 数字化技术时代
(三)磁粉检测技术
1、磁粉检测技术原理
磁粉检测的基础是缺陷处漏磁场和磁粉间的相互作用。 在铁磁性工件被磁化后,由于材料不连续性的存在,使工件 表面和近表面的磁力线在材料不连续性处发生局部畸变而产
生漏磁场,吸附施加在工件表面的磁粉,形成了在合适光照
下目视可见的磁痕,从而显示出材料不连续性的位置、形状 和大小,通过对这些磁痕的观察和分析,就能得出对影响制 品使用性能的缺陷的评价。
场条件有时会限制检测的进行。例如有内件的容器、有厚保温层的容 器、内部液态或液态介质未排空的容器等均无法检测。此外一些搭接 在厚度较大的端框上面的锁底电子束焊缝或者插接焊缝均无法检测。
(7)对缺陷在工作中厚度方向的位置、尺寸(高度)的确定 比较困难 除了一些根部缺陷可结合焊接知识和规律来确定其在工作中 厚度方向的位置,很多缺陷无法用底片提供的信息定位。缺陷高
检测角焊缝的布置比较困难,底片的黑度变化大,成像质量不够
好。不适宜检验板材、楱材、锻件的原因是板材、锻件中的大部分缺 陷与板平行,射线照相无法检出。此外楱材、锻件厚度较大,射线穿 透比较困难,效果也不好。 (6)有些试件结构和现场条件不适合射线照相
由于是穿透法检验,检测时需要接近工件的两面,因此结构和现
离防护和时间防护。
(二)超声检测技术
1、超声检测技术原理
超声检测的基本原理是基于超声波传播到声阻抗不
同的界面时,将按一定规律发生反射与折射。由于在声
阻抗不同的界面发生的反射与折射,将形成界面的反射
波,从而使透射的超声波强度发生衰减。
图2 超声检测原理
超声检测设备
2、超声检测技术应用与特点
超声检测技术是锻件、型材(板材、管材、棒材)的基本检验技
以堵塞;
(4)对于表面覆盖有涂覆层的零件,应尽量去掉覆
盖层后再进行检测。
(四)荧光检测
1、零件的待检表面应清洁、干燥; 2、零件表面的油污、油脂、涂层、腐蚀产物、 氧化皮、金属污物、焊剂、化学残留物等均应去除; 3、铝合金、镁合金、钛合金和镍合金等关键件, 机械加工后一般应先进行酸或碱浸蚀,然后才可送交 荧光渗透检验 ;
裂纹检出率较低,但对薄试件,除非裂纹或未熔合的高度和张口
宽度极小,否则只要照相角度适当,底片灵敏度符合要求,裂纹 检出率还是足够高的。
(4)适宜检验厚度较薄的工件而不适宜检验较厚工件
因为检验厚工件需要高能量的射线探伤设备。300kV便携式X
射线机透照厚度一般小于42mm,420kV移动式X射线机和Ir192 γ
4、不允许接触渗透剂的零件表面,应预先保护好。
谢谢大家!
2016-07-07
图3 磁粉检测原理
磁粉检测有三个必要步骤: (1)被检验的工件必须得到磁化; (2)必须在磁化的工件上施加合适的磁粉; (3)对任何磁粉的堆积必须加以观察和解释。
磁 粉 探 伤 机
2、磁粉检测技术特点
磁粉检测技术具有如下优点:
(1)是一种表面和近表面缺陷检验技术,主要是用于
检验表面和近表面区的裂纹、发纹、白点、折迭、夹杂、冷
回渗到零件表面上,形成放大了的缺陷显示,在黑光(荧光检验法)
或白光(着色检测法)观察,缺陷处可分别对应的发出黄绿色的荧光 或呈现红色显示。用目视检验,即可检测出缺陷的形貌和分布状态。
图4 渗透检测工艺过程
2、渗透检测技术应用与特点
液体渗透检测法可用于检验各种类型的裂纹、气孔、分层、缩孔、 疏松、冷隔、折叠及其他开口于表面的缺陷;广泛用于检验有色金属 和黑色金属的铸件、锻件、粉末冶金件、焊接件以及各种陶瓷、塑料
超声检测技术的主要局限性:
Байду номын сангаас
(1)由于纵波脉冲反射法存在盲区,和缺陷取向对检测灵
敏度的影响,对位于表面和非常接近表面的某些缺陷很难检测; (2)试件形状的复杂性对超声检测的可实施性有较大影响; (3)材料的某些内部结构,如晶粒度、相组成、非均匀性、 非致密性等,对超声检测的可实施性有较大影响; (4)很难对材料及制件中的缺陷作定性和定量表征; (5)为使超声波有效的进入试件,一般需要耦合剂。
说进行无损探伤,其实是不正确的!
3、无损检测技术的特点
(1)常规探伤技术中的射线照相检验技术、磁
粉探伤技术、渗透探伤技术、超声探伤技术,具有
的一个特殊性是,需要从检测结果对缺陷性质作出