压缩试验
材料压缩试验(抗压强度检测)

材料压缩试验压缩试验是测定材料在轴向静压力作用下的力学性能的试验,是材料机械性能试验的基本方法之一。
试样破坏时的最大压缩载荷除以试样的横截面积,称为压缩强度极限或抗压强度。
压缩试验主要适用于脆性材料,如铸铁、轴承合金和建筑材料等。
对于塑性材料,无法测出压缩强度极限,但可以测量出弹性模量、比例极限和屈服强度等。
与拉伸试验相似,通过压缩试验可以作出压缩曲线。
图中为灰铸铁和退火钢的压缩曲线。
曲线中纵坐标P为压缩载荷,横坐标Δh为试样承受载荷时的压缩量。
如将两坐标值分别除以试样的原截面积和原高度,即可转换成压缩时的应力-应变曲线。
图中Pp为比例极限载荷,P0.2为条件屈服极限载荷,P b为破坏载荷。
在压缩试验中,试样端面存在较大的摩擦力,影响试验结果。
试样越短影响越大,为减少摩擦力的影响,一般规定试样的长度与直径的比为1~3,同时降低试样的表面粗糙度,涂以润滑油脂或垫上一层薄的聚四氟乙烯等材料。
国家标准:压缩试验:GB/T7314-2005《金属材料室温压缩试验方法》抗压强度:CECS278-2010剪压法检测混凝土抗压强度技术规程CJ/T445-2014给水用抗冲抗压双轴取向聚氯乙烯(PVC-0)管材及连接件DG/TJ08-2020-2007结构混凝土抗压强度检测技术规程-回弹法、超声回弹综合法、钻芯法(附条文说明)DG/TJ08-507-2003高强混凝土抗压强度非破损检测技术规程(附条文说明)GB/T10424-2002烧结金属摩擦材料抗压强度的测定GB/T10516-2012硝酸磷肥颗粒平均抗压碎力的测定GB/T11106-1989金属粉末用圆柱形压坯的压缩测定压坯强度的方法GB/T11837-2009混凝土管用混凝土抗压强度试验方法GB/T12587-2003橡胶或塑料涂覆织物抗压裂性的测定GB/T13465.3-2002不透性石墨材料抗压强度试验方法GB/T14041.3-2010液压滤芯第3部分:抗压溃(破裂)特性检验方法GB/T14201-1993铁矿球团抗压强度测定方法GB/T14208.3-2009纺织玻璃纤维增强塑料无捻粗纱增强树脂棒机械性能的测定第3部分:压缩强度的测定GB/T1454-2005夹层结构侧压性能试验方法GB/T15560-1995流体输送用塑料管材液压瞬时爆破和耐压试验方法GB/T15777-1995木材顺纹抗压弹性模量测定方法GB/T1935-2009木材顺纹抗压强度试验方法GB/T1936.1-2009木材抗弯强度试验方法GB/T1938-2009木材顺纹抗拉强度试验方法GB/T1939-2009木材横纹抗压试验方法GB/T1942-2009木材抗劈力试验方法GB/T1943-2009木材横纹抗压弹性模量测定方法GB/T19496-2004钻芯检测离心高强混凝土抗压强度试验方法GB/T1964-1996多孔陶瓷压缩强度试验方法GB/T22307-2008密封垫片高温抗压强度试验方法抗弯:GB/T13465.2-2002不透性石墨材料抗弯强度试验方法GB/T14235.2-1993熔模铸造模料抗弯强度测定方法GB/T1936.1-2009木材抗弯强度试验方法GB/T1936.2-2009木材抗弯弹性模量测定方法GB/T3002-2004耐火材料高温抗折强度试验方法GB/T4741-1999陶瓷材料抗弯强度试验方法JB/T2980.2-1999熔模铸造型壳高温抗弯强度试验方法JB/T6247-1992型壳高温抗弯强度试验仪以上有青岛东标检测提供。
压缩、弯曲及剪切试验
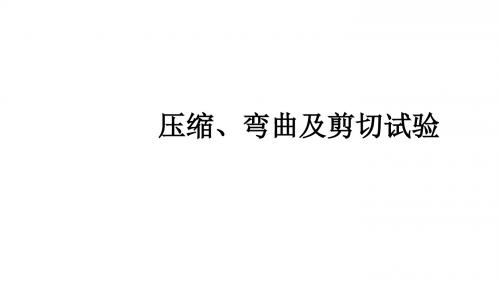
2. 试样 • 压缩试验用试样有圆柱体、正方形柱体、矩 形板和带凸耳状试样四种形式,其中圆柱体试 样、正方形柱体试样是两种常用的侧向无约束 试样,其尺寸见图1。
• 试样长度由试验目的确定: • L=(2.5~3.5)d0的试样适用于测定规定非比 例压缩应力σ pc、规定总压缩应力σ tc、压缩屈 服点σ sc及抗压强度σ bc;L=(5~8)d0的试样适 用于测定规定非比例压缩应力σ pc0.01、压缩弹 性模量Ec;L=(1~2)d0的试样形作图法测定,力轴按上节规定, 变形放大倍数应根据屈服阶段的变形量来确定。 在力—变形曲线图上,见图 5。 判读屈服平台的恒定力或屈服阶段的最小力, 或不计初始瞬时效应的最小力Fsc,按下式计算:
(4)抗压强度的测定
• 试样压至破坏,从力—变形曲线上确定最大 压缩力或从测力度盘上读取最大力 Fbc,按下式 计算:
三点弯曲试验:
四点弯曲试验:
当采用分级施加弯曲力时,按上述方法施加预弯曲力F0, 从F0至相应于σ pb0.01(或σ rb0.01)的50%的弯曲力范围 内测定m(m≥5)对力和挠度的数据,且数据点应尽量 均匀分布。用最小二乘法将弯曲力和相应的挠度数据拟 合直线。按公式(26)计算该直线的斜率Δ F/Δ f,然 后将此斜率代入公式(24)或(25)计算弯曲弹性模量。
pc
Fpc S0
• 2)逐次逼近法: • 如果力—变形曲线无明显弹性直线段,采用逐 次逼近法测规定非比例压缩应力。首先在曲线 上直观估计一点A0(见图3),约为规定非比例 压缩应变0.2%的力FA0,而后在微弯曲线上取G0、 Q0两点,其分别对应的力0.1 FA0、0.5FA0,作直 线G0Q0,按上述方法过C点作平行于G0Q0的直线 CA1交曲线于A1点,如A1与A0重合,则FA0即为 Fpc0.2;如A1未与A0重合,则需采取与上述相同 步骤进行第二次逼近,此时取A1对应的FA1来分 别确定0.1FA1、0.5FA1对应的点G1、Q1,然后如 前述过C作平行线来确定交点A2。重复相同步骤 直至最后一次得到的交点与前一次的重合。
压缩试验原理

压缩试验原理
压缩试验是一种常用的材料力学试验方法,用于确定材料在受力下的压缩性能。
其原理基于以下几个方面:
1. 试验样品制备:从所需要测试的材料中制备出符合规格要求的试样。
试样的尺寸和形状应该符合相关的标准或要求,以确保试验结果的有效性和可比性。
2. 试验设备:将试样放置于试验设备中,这通常是一台压力机。
压力机由压力加载装置和测量装置组成。
3. 载荷加载:将试样放置在压力机的上下平面之间,并应用一个已知的恒定负荷。
该负荷可以通过压力机上的控制面板调节和监测。
加载的速率和持续时间可以根据需要进行调整。
4. 载荷传递:受加载作用,试样开始发生塑性变形,并将载荷传递到试样内部的各个部分。
载荷作用下,材料内部的原子或分子结构会发生移动,试样会发生相应的体积压缩。
5. 测量变形:通过连接到试样的挠度计或应变计来测量试样的变形。
这些测量设备可以精确地测量试样的位移或应变,从而获得试样在加载过程中的变形情况。
6. 载荷-变形曲线:根据测量到的载荷和试样的变形数据绘制
载荷-变形曲线。
该曲线可以提供有关材料的力学性能,如压
缩强度、屈服点、变形硬化等信息。
7. 结果分析:通过对载荷-变形曲线的分析,可以评估材料的
力学性能和应对外力的能力。
这些结果可以用于材料设计、工程分析和质量控制等领域。
总的来说,压缩试验原理是通过加载已知的恒定负荷到试样上,并测量试样的变形来确定材料的压缩性能。
这种试验方法广泛应用于各个领域,如建筑、汽车、航空航天等行业。
压缩测试的国际标准
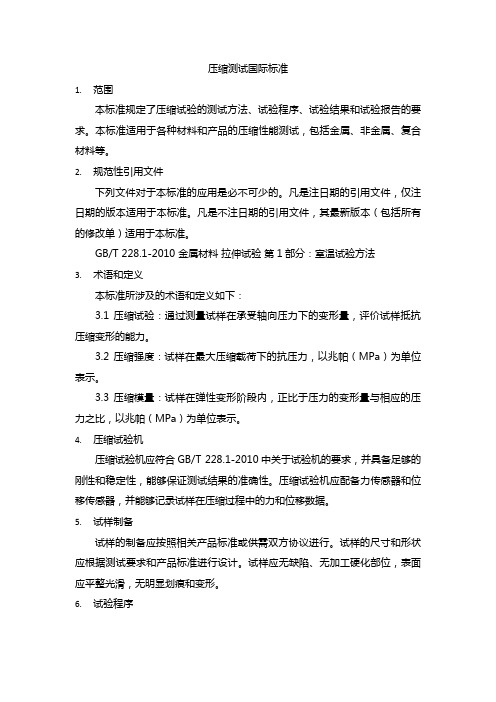
压缩测试国际标准1.范围本标准规定了压缩试验的测试方法、试验程序、试验结果和试验报告的要求。
本标准适用于各种材料和产品的压缩性能测试,包括金属、非金属、复合材料等。
2.规范性引用文件下列文件对于本标准的应用是必不可少的。
凡是注日期的引用文件,仅注日期的版本适用于本标准。
凡是不注日期的引用文件,其最新版本(包括所有的修改单)适用于本标准。
GB/T 228.1-2010 金属材料拉伸试验第1部分:室温试验方法3.术语和定义本标准所涉及的术语和定义如下:3.1 压缩试验:通过测量试样在承受轴向压力下的变形量,评价试样抵抗压缩变形的能力。
3.2 压缩强度:试样在最大压缩载荷下的抗压力,以兆帕(MPa)为单位表示。
3.3 压缩模量:试样在弹性变形阶段内,正比于压力的变形量与相应的压力之比,以兆帕(MPa)为单位表示。
4.压缩试验机压缩试验机应符合GB/T 228.1-2010中关于试验机的要求,并具备足够的刚性和稳定性,能够保证测试结果的准确性。
压缩试验机应配备力传感器和位移传感器,并能够记录试样在压缩过程中的力和位移数据。
5.试样制备试样的制备应按照相关产品标准或供需双方协议进行。
试样的尺寸和形状应根据测试要求和产品标准进行设计。
试样应无缺陷、无加工硬化部位,表面应平整光滑,无明显划痕和变形。
6.试验程序6.1 将试样放置在压缩试验机的上下压板之间,调整试样的位置,使上下压板与试样接触良好,避免试样在测试过程中滑动或倾斜。
6.2 设定压缩试验机的测试参数,包括力传感器和位移传感器的灵敏度、最大载荷、压缩速度等。
根据测试要求和产品标准,选择合适的测试参数。
6.3 开始压缩测试,记录试样在压缩过程中的力和位移数据。
在测试过程中,应保持试样不受外界干扰,避免试样发生变形或损坏。
6.4 测试结束后,将试样取出,观察试样的变形情况,记录试样的压缩强度和压缩模量。
压缩试验

压缩试验目的: 1.测定实验中低碳钢压缩时的屈服极限;2、测定实验中铸铁的抗压强度;3、观察并比较低碳钢(塑性材料的代表)和铸铁(脆性材料的代表)在压缩时的变形和破坏现象。
实验设备:YDD-1型多功能材料力学试验机(图2.6)、150mm游标卡尺、【试件】标准低碳钢、铸铁压缩试件(图2.1)。
数据分析(1)验证数据设置双窗口显示数据,左窗口实时曲线、右窗口显示力- 位移X-Y曲线。
单击左窗口,横向压缩数据,显示全数据;单击右窗口,X-Y增加数据,显示力-位移X-Y曲线。
从低碳钢压缩实验曲线中清晰地看到低碳钢压缩时的屈服阶段,铸铁则无屈服阶段。
(2)读取数据①荷载数据的读取选择单光标,选择左右图光标同步,放大左图屈服阶段,读取屈服荷载。
当然也可以象拉伸试验一样采取双光标读出屈服荷载。
将得到的数据,填入到相应表格。
这样就得到了屈服极限σ s 。
铸铁无屈服荷载,极限荷载的读取同低碳钢。
②试件变形指标的读取用游标卡尺测量压缩后试件的最大直径及高度,填入到相应表格,以得到压缩实验过程中的最大应力。
这样就完成了数据读取的过程。
(3)分析数据通过实验前的测量及实验后的数据读取就得到了我们所需要的数据,代入相应的公式或计算表格即可得到拉伸的各项力学指标。
低碳钢屈服强度铸铁的强度极限对于铸铁试件而言,由于其无屈服现象故其不存在流动极限。
对于低碳钢时间而言,由于在压缩过程中试件的面积不断增大,承受的荷载持续增加,习惯上认为低碳钢试件无极限承载力,但假如计算时考虑试件面积的变化,会发现达到一定荷载后,压缩过程的应力应变曲线趋于平缓。
在实际实验时,可以通过利用在压缩过程中测得的试件高度的变化来求得试件的对应面积,这样就可以得到压缩过程的曲线,实际分析时往往将数据转化为Matlab格式后进行分析处理,另外,在荷载较大时需考虑机架变形引起的测试误差,可通过在不加试件压缩的情况下测得机架变形与荷载的对应关系,在实际分析数据时去掉此系统误差,这样就可以较准确地得到低碳钢压缩时的曲线。
实验3土的压缩试验

(1)固体颗粒的压缩; (2)孔隙水和孔隙气体的压缩,孔隙气体 的溶解; (3)孔隙水和孔隙气体的排出;
纯水、固体颗粒的压缩量常可略不计; 土体压缩主要来自孔隙水和气的排出。
• 土体受力后引起的变形: • 体积变形 剪切变形
•
• 体积变形:主要由正应力引起,它只会使土 体压密、体积缩小,但不会导致土体破坏。
再压缩试验时土体体积变化特征:
(1) 土体的变形是由可恢复的弹 性变形和不可恢复的塑性变形 两部份组成
(2) 回 弹 曲 线 和 再 压 线 曲 线 构 成 一迴滞环,土体不是完全弹性 体的又一表征;
(3) 回 弹 和 再 压 缩 曲 线 比 压 缩 曲 线平缓得多。
(4)当再加荷时的压力超过b点, 再压缩曲线就趋于初始压缩曲 线的延长线。
一、侧限(单向)压缩试验:
单向固结仪:
应力状态: 1´= Z 2´=K0 Z 3´=K0 Z
应变特性: Z x=0 y=0
测定: 轴向应力 轴向变形
透水孔
• 杠杆式压缩仪: • 400~600kpa • 高压固结仪:
• 1600~5000kpa
百分表
透水石
传压板 水槽 环刀 内环
试样
•施加荷载,静置至变形稳定 •逐级加大荷载
(2)、e ~ lgP 曲线
对直线段:
e
1
0.9
Cc
e Cc (lg ')
0.8
0.7
压缩指数
0.6
压缩指数的单位问题
100
1000 lgP
压缩系数与压缩指数
Cc 是无量纲系数,同压缩系数a 一样,压缩 指数Cc值越大,土的压缩性越高。 虽然压缩系数a 和压缩指数Cc 都是反映土的压 缩性的指标,但是两者有所不同。前者随所取 的初始压力及压力增量的大小而异,而后者在 较高的压力范围内却是常量,不随压力而变。
压缩实验
实验三 压缩实验一、实验目的1.测定压缩时低碳钢的屈服极限s σ和铸铁的强度极限b σ。
2.观察低碳钢和铸铁压缩时的变形和破坏现象,并进行比较和分析原因。
二、设备和量具1.万能材料试验机。
2.游标卡尺。
三、实验原理及步骤低碳钢和铸铁等金属材料的压缩试样一般制成圆柱形,高h o 与直径d o 之比在1~3 的范围内。
目前常用的压缩试验方法是两端平压法。
这种压缩试验方法,试样的上下两端与试验机承垫之间会产生很大的摩擦力,它们阻碍着试样上部及下部的横向变形,导致测得的抗压强度较实际偏高。
当试样的高度相对增加时,摩擦力对试样中部的影响就变得小了,因此抗压强度与比值h o /d o 有关。
由此可见,压缩试验是与试验条件有关的。
为了在相同的试验条件下,对不同材料的抗压性能进行比较,应对h o /d o 的值作出规定。
实践表明,此值取在1~3的范围内为宜。
若小于l ,则摩擦力的影响太大;若大于3,虽然摩擦力的影响减小,但稳定性的影响却突出起来。
低碳钢试样压缩时同样存在弹性极限、比例极限、屈服极限而且数值和拉伸所得的相应数值差不多,但是在屈服时却不象拉伸那样明显。
从进入屈服开始,试样塑性变形就有较大的增长,试样截面面积随之增大。
由于截面面积的增大,要维持屈服时的应力,载荷也就要相应增大。
因此,在整个屈服阶段,载荷也是上升的,在测力盘上看不到指针倒退现象,这样,判定压缩时的P S 要特别小心地注意观察。
在缓慢均匀加载下,测力指针是等速转动的,当材料发生屈服时,测力指针的转动将出现减慢,这时所对应的载荷即为屈服载荷P S。
由于指针转动速度的减慢不十分明显,故还要结合自动绘图装置上绘出的压缩曲线中的的拐点来判断和确定P S。
低碳钢的压缩图(即P一△1曲线)如图3—1所示,超过屈服之后,低碳钢试样由原来的圆柱形逐渐被压成鼓形,即如图3—3。
继续不断加压,试样将愈压愈扁,但总不破坏。
所以,低碳钢不具有抗压强度极限(也可将它的抗压强度极限理解为无限大),低碳钢的压缩曲线也可证实这一点。
压缩试验的原理
压缩试验的基本原理1. 介绍压缩试验是一种常用的实验方法,用于评估材料的力学性能和变形行为。
通过施加压力来压缩材料,并测量相应的应力和应变,从而得到材料的力学参数。
本文将详细介绍压缩试验的基本原理和相关概念。
2. 压缩试验装置压缩试验通常使用万能材料试验机进行,该机器由主要部件组成:上夹具、下夹具和加载系统。
上夹具和下夹具用于固定样品,加载系统用于施加压力。
3. 原理在进行压缩试验时,样品受到垂直方向上的力,即压力。
这个力导致样品发生变形,即压缩。
根据胡克定律(Hooke’s Law),应力(Stress)与应变(Strain)之间存在线性关系。
3.1 应力(Stress)应力是指单位面积上受到的力,即单位面积上的压力。
在压缩试验中,应力可以通过以下公式计算:σ=F A其中,F是施加到样品上的力,A是样品的初始横截面积。
3.2 应变(Strain)应变是指材料受力后发生的变形程度。
在压缩试验中,应变可以通过以下公式计算:ε=ΔL L0其中,ΔL是样品在受力后的长度变化,L0是初始长度。
3.3 应力-应变曲线通过测量不同应力和应变下的数据,可以得到应力-应变曲线。
该曲线描述了材料在受力过程中的力学行为。
根据实验结果绘制的曲线可以分为几个阶段。
3.3.1 弹性阶段在开始施加压力时,材料会发生弹性变形,在去除压力后能够完全恢复到原来的形状。
此时,应力与应变之间存在线性关系,并且满足胡克定律。
3.3.2 屈服点当施加的压力达到一定程度时,材料会发生塑性变形,即无法完全恢复到原来的形状。
这个点被称为屈服点。
在屈服点之后,材料会继续发生塑性变形,但应力-应变曲线的斜率开始减小。
3.3.3 局部最大点在继续施加压力的过程中,应力-应变曲线会出现一个局部最大点。
这个点表示材料达到了最大的应力值。
在该点之后,材料开始发生断裂。
3.3.4 断裂点当施加的压力继续增加时,材料会发生断裂,即完全失去结构和功能。
此时,应力会迅速下降到零。
压缩试验分析
压缩试验分析1. 概述压缩试验是测定材料在轴向静压力作用下的力学性能的试验,是材料机械性能试验的基本方法之一。
主要用于测定金属材料在室温下单向压缩的屈服点和脆性材料的抗压强度。
压缩性能是指材料在压应力作用下抗变形和抗破坏的能力。
工程实际中有很多承受压缩载荷的构件,如大型厂房的立柱、起重机的支架、轧钢机的压紧螺栓等。
这就需要对其原材料进行压缩试验评定。
1.2 概念压缩屈服强度:当金属材料呈现屈服现象时,试样在试验过程中达到力不在增加而继续变形时所对应的压缩应力。
上压缩屈服强度:试样发生屈服而力首次下降前的最高压缩应力。
下压缩屈服强度:屈服期间不计瞬时效应时的最低压缩应力。
抗拉强度:对于脆性材料,试样压至破坏过程中的最大压缩应力。
压缩弹性模量:试验过程中,轴向压应力与轴向应变呈线性比例关系范围内的轴向压应力与轴向应变的比值。
1.3 试验设备仪器及试样设备仪器:(1)材料万能试验机;(2)游标卡尺。
压缩试样通常为柱状,横截面有圆形和方形两种。
试样受压时,两端面与试验机压头间的摩擦力会约束试样的横向变形,且试样越短,影响越大;但试样太长容易产生纵向弯曲而失稳。
1.4 压缩试验的力学分析低碳钢低碳钢试样装在试验机上,受到轴向压力F作用,试样产生变形量△l 两者之间的关系如图。
低碳钢压缩时也有弹性阶段、屈服阶段和强化阶段。
低碳钢压缩变形,不会断裂,由于受到上下两端摩擦力影响,形成“鼓形”。
试样直径相同时,低碳钢压缩曲线和拉伸曲线的弹性阶段几乎重合,屈服点也基本一致。
低碳钢是塑性材料,试样屈服后,塑性变形迅速增长,其横截面积也随之增大,增加的面积又能承受更大的载荷,所以只能测得屈服极限,无法测得强度极限。
铸铁铸铁试样装在试验机上,受到轴向压力F作用,试样产生变形量△l两者之间的关系如图。
灰铸铁的抗压强度是其抗拉强度的3-4倍。
铸铁在较小变形下出现断裂,略成“鼓形”,断面的法线与轴线成45—55度;试样直径相同时,铸铁压缩曲线和拉伸曲线差异较大,其抗压强度远大于抗拉强度。
简述压缩试验使用仪器
简述压缩试验使用仪器
压缩试验是一种材料力学性质测试方法,可以用于评估材料的强度、硬度、韧性等力学性能。
在压缩试验中,通常使用以下仪器:
1. 压缩试验机:用于施加压缩载荷,并测量材料在压缩载荷下的变形和应力应变关系。
压缩试验机通常由主机、控制系统、载荷传感器、位移传感器、夹具等组成。
2. 压缩试样:用于进行压缩试验的样品,通常是制备成一定尺寸和形状的试样,如圆柱形、平板形等。
3. 夹具:用于固定试样,使其在压缩试验中保持稳定的位置和形状。
夹具的种类和形状根据试样的形状和尺寸而定。
4. 载荷传感器和位移传感器:用于测量压缩载荷和试样的变形量,并将数据传输到计算机或数据采集器中进行处理和分析。
5. 数据采集器或计算机软件:用于接收和处理传感器测量的数据,生成压缩试验的结果和图表,并进行数据存储和管理。
压缩试验可以用于测试各种材料的力学性能,如金属材料、塑料、橡胶、复合材料等。
在工业生产和科学研究中,压缩试验是一种常用的材料力学性能测试方法。
- 1、下载文档前请自行甄别文档内容的完整性,平台不提供额外的编辑、内容补充、找答案等附加服务。
- 2、"仅部分预览"的文档,不可在线预览部分如存在完整性等问题,可反馈申请退款(可完整预览的文档不适用该条件!)。
- 3、如文档侵犯您的权益,请联系客服反馈,我们会尽快为您处理(人工客服工作时间:9:00-18:30)。
紧贴在刚性芯模上的短圆筒加压。
Er
ph
R
1
zr
rz
管状试样试验
:在圆筒外表面测
得的圆周应变
-用于评定具有各种纤维叠层形式的丝束缠绕材料的力学性能。
加载方式有内压和外压两种。 可进行的试验有:轴向拉伸、轴向压缩和剪切等。 所加载荷:可单一种或耦合方式。如:轴向拉伸和压缩加扭转;
管状试件轴向压缩试验的特点:
-因变形集中在端部表面附近,出现总体失稳或局部失稳, 端面开裂和挤压。因而,必须增加试样的相对厚度,但同 时确为保证应力状态均匀性增加了困难。
内压和外压加载试验
-管子的内压和外压加
载试验,用于长丝缠绕
制件的质量控制和材料
的力学性能研究(主要
是周向弹性模量 E 和
轴向强度
[ 25/ 90]层板压缩破坏表面呈现层裂 [ 45/ 0 / 45/ 90 ]T300增强复合材料端口形貌
[ 30]/29层0 板压缩破坏表面纤维断裂
侧向形貌,900层横向裂缝,层间组阻挡裂纹扩 展
[ 25]/层90板受压分层纤维断裂及其留在
基体中的烙印
[ 30 /]9T层0 板破坏表面
若 a13 a,23 在整个横截面上不均匀地分布着应力 x 以及在
纵截面上相应有应力 r
和
;当测定强度
i(e z
)u时,必须
考虑 x 和 是稳定的。
-各向 异性管受拉-压时,只有管状试件横截面同材料的 横向异性平面重合(如单向复合材料管状试件,其纤维方 向和管子轴线严格同向时)没有径向应力和周向应力。
ASTM推荐的标准(mm)
硼纤维复合材料
l
b
139.7 6.35
碳纤维复合材料
139.7 6.35
玻璃纤维复合材料 139.7 6.35
试样的标距长度:25.4
h
1.5 : 2.0 1.5 : 3.0 3.2 : 4.0
变截面试样
-变截面试样的 形状和尺寸取决 于试验的目的。
•消除应力集中
-如高模量纤维 聚合物复合材料, 通常采用标距段 很明显的试样, 以保证试样的破 坏发生在标距段。
-测定强度时,应选择板状或变截面试样;
-测定模量时,应选择圆截面或夹层梁试样;
杆和板状试样的制备 与尺寸
•在弹性对称主轴方向 上切取;
•宽度和厚度上对称于 试样纵轴;
•保证破坏发生在标距 段;
•夹头的选择要谨慎;
在选择试样尺寸时,要考虑正应力 中,标距长度要不失稳。
y
和剪切应力
xy 的应力集
可测得的常数:
iu x
;
eu x
E
i x
;
E
eu x
z
-管状试验主要用来评价各种增强纤维叠层形式的复合材料的 力学性能,为了方便,常将管状式样看成没有边界效应的无限 宽的平板试样。
•该种等效办法只能有条件使用。
原因:
①因为二者的制造方法不同;
②管状件制造时,很难保证纤维含量和铺层角度恒定;
•对棱柱试件纵向加载时发现, 支撑面的纵向和横向应变大 大的超过了试件标距段的应 变。这样其相应的应力可能 超过了试件本身的横向强度 而导致提早破坏。
-由于强度的各向异性的敏感性,高强度的单性复合材料 对应力集中特别敏感。如:对短试件而言,应变场不均匀, 可造成拉伸、压缩弹性模量差别明显,这不是试件本身的 原因,而是加工误差和尺寸选择不正确所致。
1/ 1 0.4k2 k-试样几何形状和各向异性的参数
第二个区域中,环发生压缩破坏。 第三个区域(厚壁环)中,要考虑边界条件,不仅要考虑 也要考虑 r 三个区域的边界取决于材料的各项异性。
当外力加载时,由于内层的剥离,要正确计算压缩强度通常 非常困难。
-当内层片保持为环状时的能量与同一层片剥离和失稳后的 能量之差,高于内层片的结合能量时,内层片发生剥离并随 后失稳。当层片厚度为 h0 时,临界应力等于:
-对开盘式加载试验主要用于定性评价 不同材料的弹性和强度性能。
P
R
h
P
测定性能: E ,
测量数据: P, i ,ij
几何尺寸: R / h,b, h
可测定 曲线的 线性段
除对开盘式加载方式外,还有柔性圆环和液压式加载方式。 加载的方法同拉伸时相同。
P
P
P
R
R
P
P
柔性圆环式加载
pD 2h
E
pD
2h
-承受内压的厚壁管的周向应力和径向应力可由(La-me) 公式确定:
pR2 R02 Ri2
1
R02 r2
r
pRi2 R02 Ri2
1
R02 r2
式中 Ri , R0, r 试样的内径、外径和先用半径
当 r Ri 周向应力和径向应力最大
纤维初始波纹度;分布不均等。
2)中模量( Em=200 : 700MPa)
横向破裂-材料组分泊松比的差别; 试样全场范围内不均匀;也有可能是 局部破坏造成。此时的临界载荷要以 发生局部破坏的材料的性能来确定。
3)高模量(Em 2000MPa)
压缩破坏(纤维受450角剪切)-而增 强纤维无任何局部屈曲。
1
r
0.916E
h Ri
2
k
h0 Ri
1
2
式 k 4.77 /(E Ri )
中 -格里菲斯提出的比破坏能
Ri 环的那半径
环状试样内表面分层
由剥离造成的分层可分为两种:①对于螺旋缠绕的试样,可 能会使缠绕开始松散;②对于圆周叠层的试样,可能会出现 逐层剥离现象。
③在各向异性体中,应力张量和应变张量的轴只是在个别情况 下吻合,而受单向拉伸和压缩时,管状试件上的应力状态不能 简单的等同于板状试件。
下列表中的差别,不仅是由于试件的制造方法不同,而且也 是由于厚度不同以及7层和13层碳纤维复合材料的叠层顺序 不同所致。
材料和加载方式
7层碳纤维复合材料 拉伸 压缩 13层碳纤维复合材料 拉伸 压缩
复合材料的压缩试验
板样试件的压缩
-沿着纤维增强方向的压缩试验是普遍采取
的试验方式,其重要性等同于拉伸试验。
P
与板样试件拉伸的关系
一般情况下,等同于纤维聚合物复合材料在 弹性对称主轴方向进行拉伸试验的所有基本 关系,但要考虑变形方向。
纤维聚合物复合材料的拉伸与压缩试验性
质的差别比各向同性材料大。
P
压缩试验的特性-注意点
h
h 液压式加载
对于环状试样在外压下进行压缩试验时,如何正确选择 h / R 是主要问题。在实际压缩试验时,应考虑破坏压力和相对厚度 间的关系有三个定义明显的区域。 第一个区域(薄壁环)中,由于失稳而丧失承载能力。此时, 失稳的临界压力可由下式计算:
p r p*r
式中:p*r 3E I / R3--环轴线的单位长度上的临界压力
Celanese
夹具
具对 加试 工件 精厚 度度 要有 求限 高制
及 夹
联合加载
防止屈曲和失稳的方法
环状试样的压缩
-对于弹性模量 E 的测定与环状试件
拉伸相同。环的截面内除有压缩应力外, 还有弯曲应力。
弯曲应力大小取决于:
①材料的力学性能;②试样相对尺寸; ③夹具结构
•如用对开盘作环状试件拉伸相同,在距 间隙处环的应力最大。主要原因是施加 压缩载荷时,有偏心效应存在。
应变速率的影响
静强度受应变速率的影响较大;而压 缩弹性模量和断裂伸长对应变速率不 敏感;
试样的形状和尺寸
-与拉伸试验相比,更依赖于 试件的形状和尺寸。 •在实际试验中,应避免使用 尺寸过小的试件。 原因: ①变形难以测准; ②标距段小,应变均匀度不够; ③支撑面的挤压和变形约束效 应难以消除 ④加工困难并导致尺寸效应
1、与材料弹性对称主轴成不同角度的各向异性性能、层间应力 和受压时结构对称效应。
2、加载方式和材料结构所决定的特性。
变形特点
一般情况下, 曲线是非线性
的. 然而,如玻璃、硼、碳纤维等刚 性纤维增强的复合材料,沿纤维方 向加载时,应力-应变图从加载开 始到破坏前实际上都是线性的。有 时,也能观察到同拉伸试验相同的 断裂特性。
-在实际试验过程中,至少有一个支撑面相对与试验纵轴 保持静止,因此,具有非对称性增强纤维叠层的试件不易 进行压缩试验。
破坏模式-取决于材料:
①增强纤维方式;
②材料组分的力学性能
③试验的相对尺寸
视基体的模量不同主要破坏模式有3
1)低模量( Em 15 : 25MPa)
局部屈曲-制作中的变化因素。如:
[ 45/ 0]/碳布45压缩破坏断口
•载荷垂直于增强纤维方向,复合材料常由于在同基体 剪切强度相当的应力下失稳而破坏,此时试样破碎成 棱柱块。
-实际试验过程中,可能是以上多 种破坏模式的耦合,常是线性与非 线性行为,层间应力、表面层开裂、 总体失稳、端面破坏或垂直层片开 裂等,因此必须仔细观察-分析- 记录试件的破坏模式,未指明破坏 模式的复合材料试验结果无可比性。
解释:
1)若破坏前出现断裂,则是由于 部分增强纤维的失稳。
2)若在较小载荷下,从 曲
线上出现断裂,则可能是试件本身 及安装不正确或变形受到了约束。
•当垂直于纤维铺层方向加 载时,呈现出非线性,其 程度取决于聚合物基体的 性能。
•纤维与基体粘接不牢时, 这时材料远没达到最大载 荷,随着粘接界面的破坏 而开始破坏。