培训教材_关于轮胎生产工艺
轮胎基本知识培训教材
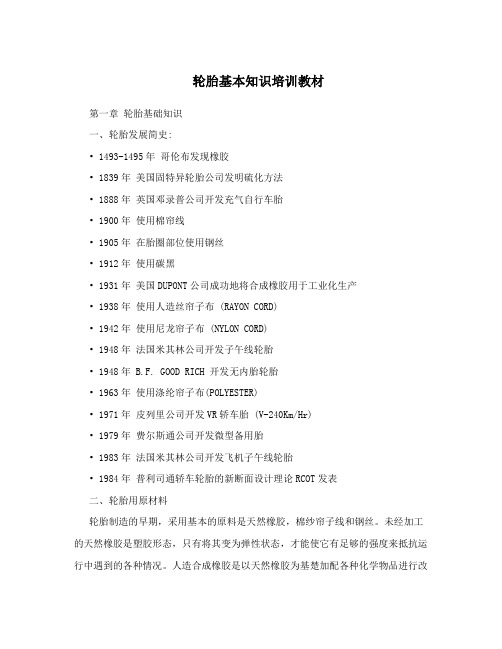
轮胎基本知识培训教材第一章轮胎基础知识一、轮胎发展简史:• 1493-1495年哥伦布发现橡胶• 1839年美国固特异轮胎公司发明硫化方法• 1888年英国邓录普公司开发充气自行车胎• 1900年使用棉帘线• 1905年在胎圈部位使用钢丝• 1912年使用碳黑• 1931年美国DUPONT公司成功地将合成橡胶用于工业化生产• 1938年使用人造丝帘子布 (RAYON CORD)• 1942年使用尼龙帘子布 (NYLON CORD)• 1948年法国米其林公司开发子午线轮胎• 1948年 B.F. GOOD RICH 开发无内胎轮胎• 1963年使用涤纶帘子布(POLYESTER)• 1971年皮列里公司开发VR轿车胎 (V-240Km/Hr)• 1979年费尔斯通公司开发微型备用胎• 1983年法国米其林公司开发飞机子午线轮胎• 1984年普利司通轿车轮胎的新断面设计理论RCOT发表二、轮胎用原材料轮胎制造的早期,采用基本的原料是天然橡胶,棉纱帘子线和钢丝。
未经加工的天然橡胶是塑胶形态,只有将其变为弹性状态,才能使它有足够的强度来抵抗运行中遇到的各种情况。
人造合成橡胶是以天然橡胶为基楚加配各种化学物品进行改良以达到硬度,耐磨,及抗热等特性。
在制造轮胎过程需要利用热和特定的化学品,作为引发变化的启动剂和加快变化的催化剂。
硫磺作为交叉连结的媒介(硫化)。
1( 橡胶:天然橡胶存在于橡树中的奶状树汁中。
割开橡胶树的树皮时,奶状树汁(胶乳)便会流出来。
这种橡树主要生长于东南亚、非洲和南美洲。
在胶乳加入醋酸和甲酸三至四小时后,一块白色的海棉状凝结块便形成了。
凝结物被传送到压片机组,在这里它同时被压平和清洗,再被切割成1/8英寸厚的长片段,放在架上烘干,然后在工厂里进行混合或加工。
橡胶需要加入化学品变成人工合成橡胶具备一些截然不同的特性,以适应各种产品所需要的特性。
轮胎对橡胶有很多样化的要求,其中有:抗热,抗磨,抗油,抓地力,防渗透,及有弹性(全橡胶)。
《轮胎制造工艺简介》课件
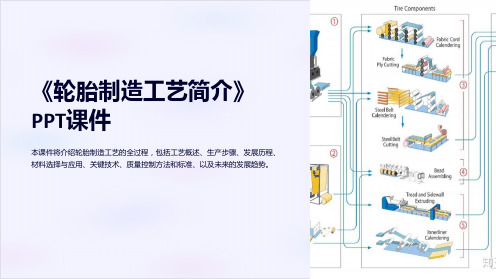
1
手工制作时期
轮胎是由手工制作而成,生产效率较低。
2
机械化时代
引入机械设备辅助生产,提高了生产效率和质量。
3
自动化生产线
采用自动化设备进行大规模生产,进一步提高了生产效率和一致性。
轮胎材料的选择与应用
轮胎制造中的材料选择至关重要,不同材料的应用能够影响轮胎的性能、耐久性和安全性。
橡胶
橡胶是轮胎的主要组成部分, 质量和种类的选择会直接影 响轮胎的性能。
耐久性测试
通过模拟实际使用条件对轮胎进行耐久性测 试,评估其寿命和性能。
符合标准
轮胎必须符合国家和行业的相关标准,确保 质量和安全。
持续改进
不断优化制造工艺和质量控制方法,提高轮 胎的质量和性能。
未来轮胎制造工艺的趋势
随着科技的不断进步,轮胎制造工艺也在不断演进,未来的趋势包括智能制造、可持续发展和个性 化定制等。
《轮胎制造工艺简介》 PPT课件
本课件将介绍轮胎制造工艺的全过程,包括工艺概述、生产步骤、发展历程、 材料选择与应用、关键技术、质量控制方法和标准、以及未来的发展趋势。
工艺概述
了解轮胎制造工艺的基本概念和原理,包括材料准备、成型、硫化和后续加工等关键环节。
1
材料准备
准备轮胎制造所需的原材料,包括橡胶、纤维材料和金属配件等。
成型
将原材料按照预定的轮胎模具进行成型。
硫化
将成型后的轮胎在高温和高压下进行硫化, 增强材料的耐用性。
质检
对硫化后的轮胎进行质量检测,确保符合各 项标准和要求。
包装
将质检合格的轮胎进行包装和标识,方便运 输和销售。
轮胎制造工艺的发展历程
轮胎制造工艺经历了多个阶段的发展,从最初的手工制作到现代的自动化生产线,不断提高生产效 率和质量。
铝合金轮毂生产工艺培训教材

前言为培养及提升公司员工素质与技能,使所有员工能了解和掌握在本职工作中所涉及的基本技术与知识以及在工作中所应遵循的准则,以提高公司生产及服务之品质,特编定《铝合金轮圈生产工艺培训教材》以供教育培训之用。
本教材在架构上分为七章,即「轮圈基本知识」、「铸造」、「热处理」、「机加工」、「涂装」、「铝料回收」、「品保基本知识」,对铝合金轮圈制造作一系统,循次渐进的介绍,使学员有更进一你好的了解与体会。
本教材仅涉及本厂铝合金轮圈制造的专业基础知识,并未涵盖所有的技术与知识,故讲师授课时应联系本厂实际生产状况加以具体阐释与讲解,学员应在实际工作中加以应用与消化,以期更合理发掌握和理解本教材。
第一章:轮圈基本知识1.1铝合金轮圈特性1.1.1安全性好:铝合金材质较软耐冲击且流行采用无内胎轮胎(真空胎)不易漏气,极少爆胎,从而保证了车辆的安全性。
1.1.2重量较轻:减少车辆重量,降低油耗以,提高国车速。
1.1.3散热性好:提高轮胎行驶性能,降低油耗,提高车速,并且延长轮胎使用寿命。
1.1.4精密性好:采用CNC(计算器数值控制)机床,装配尺寸及精度有保证,轮圈装车性能好,品质均一。
车辆行驶稳定性佳,操作性好。
1.1.5平衡性好:装车时一般不需加配重铅块,(即使另加配重块也在30克内)。
1.1.6美观工艺性好:客户可以根据自己的品位选择轮圈,以体现价值和个性。
1.1.7保养容易:永不生锈,平时只需清水清洗后用软布擦拭即可。
1.2铝合金轮圈制造流程1.2.1铝合金轮圈制造流程图1.2.2铝合金轮圈制造流程说明A.配料:将各种铝料按比例配好,保证铝水质量。
B.熔解:在熔角炉的熔角室里加热使铝料熔化成铝水。
C.处理:在保温炉内对铝水进行打渣、调质和除气处理;将铝水充分搅拌,以去除铝水中的铝渣及杂质;添加其它合金,保证铝水成份符合要求;用氩气或氮气除去铝水中含有的氢气等气体,保证铸件组织致密,减少针孔。
D.静置:处理完铝水要保持一段时间使之均匀后,方能浇注。
《汽车轮胎培训资料》PPT课件

×100
W(轮胎(lúntāi)的宽度 )
偏平比=
(Aspect Ratio)
H(轮胎的高度 )
W(轮胎的宽度 )
W(轮胎的宽度 )
(
H
轮 胎 的 高 度
)
※单位均mm
第二十一页,共67页。
轮胎(lúntāi)的通称(轿车)
①195:断面宽的通称 (mm)
② 60:偏平率的通称 (%)
195/60R14 86H
新材料(cáiliào)“合成橡胶Ⅱ”
化合剂
主要化合剂
.碳黑:橡胶的增强剂 .硫磺:使橡胶具有弹性和耐久性
.硫化促进剂:促进橡胶分子和硫 磺分子的结合
.老化防止剂:防止橡胶的老化
.龟裂防止剂:防止橡胶的龟裂
合成橡胶
纤维帘线
轮胎帘线
钢丝帘线
天然橡胶
橡胶
胎圈钢丝
化合剂
碳黑
一根也这么结实 呀!
胎圈钢丝
是根据轮胎的用途及尺寸
胎面 :
直接与路面接触的部分。保 护轮胎内侧帘布,延长轮胎 寿命的厚厚的橡胶层。表面
为提高排水性能,驱动(qū dònɡ)/制动性能刻有花纹。
胎肩:
轮胎的两肩部分。采用
成能够保护胎体和散
发内部热量的设计。
带束层:
是位于胎面和胎体之间的
补强层 。缓冲冲击,并可防止
(fángzhǐ)胎面产生的外
伤波及胎体,还可以防止
无内胎(nèitāi)轮胎
有内胎(nèitāi)轮胎
内衬
内胎
轮辋气门
气门
无内胎轮胎的优点 1.因为没有内胎,所以不会发生由内胎引起的故障。
2.即使被钉子等刺穿也不容易造成快速漏气,能够使走行 中的事故防患于未然。
轮胎基础知识及生产工艺
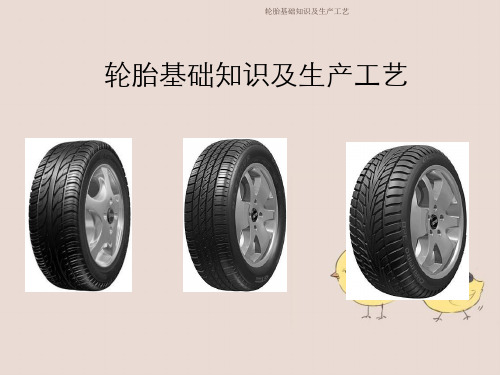
—— 轮胎组成各部件功能(续)
冠带层
其作用是束缚和保护带束层,提高高速性和抗刺穿。有端束带和 全束带两种形式。
轮胎基础知识及生产工艺
轮胎基础知识
—— 轮胎组成各部件功能(续)
带束层
是子午胎的特有结构。其作用是固定胎体及增高胎面的刚性,是 主要的受力部件
轮胎基础知识及生产工艺
轮胎基础知识
轮胎基础知识及生产工艺
轮胎基础知识
30×9.50R15 104 S LT
轻卡 速度级别 负荷指数 轮辋名义直径(英寸) 子午胎(Radial) 轮胎名义宽度(英寸) 轮胎名义外直径(英寸)
T 105/70 D 14 84 M
速度级别 负荷指数 轮辋名义直径(英寸) 斜交胎(Digonal) 名义扁平系数(%) 轮胎名义宽度(mm) 应急用(Temporary)
轮胎基础知识及生产工艺
轮胎基础知识及生产工艺
轮胎基础知识及生产工艺
轮胎基础知识
轮胎发展历程
1888年----第一条橡胶充气轮胎出现 1892年----出现了帘布,提高了轮胎的弹性 1895年----汽车的出现为轮胎发展注入活力 1942年---出现了尼龙轮胎,开创了轮胎生产的崭新时期 1946年---出现了钢丝子午线轮胎,是轮胎工业的一场革 命。
轮胎基础知识及生产工艺
轮胎基础知识
砌块花纹
如图所示,适合于在难通过的土路上和无路条件下使用,故也称为 越野花纹。它的特点是;花纹沟格深,凸出面积小,与路面附着力 大,所以适宜于在泥雪地、松软路面以及一般轮胎不易通行的坏道 路上行驶。它有良好的自行清除泥土的性能,在坏路面上行驶,不 容易附着泥土。因为这种轮胎的气压和普通轮胎相同,所以在较好 的路面上不宜使用这种轮胎,否则轮胎花纹会早期磨损,面且振动
优科豪马轮胎销知识培训 (1)
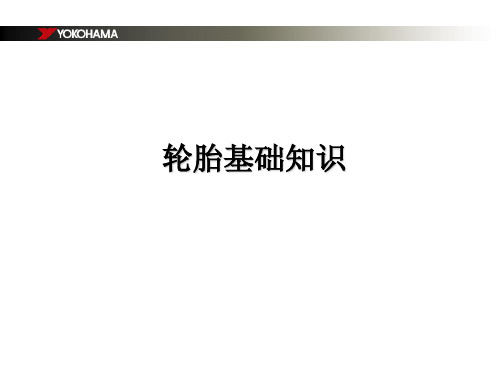
胎圈用橡胶
裹上橡胶后挤出
整理胎圈钢丝 胎面用橡胶
卷成钢丝圈
胎面挤出机
胎面挤出
冷却(冷却槽)
轮胎基础知识培训教材
加工好的胎体、带束层、胎面、 使生胎的橡胶在一定的热度和压 胎圈等各组件通过成型机组装 力下增强弹性。 成轮胎的形状。 制作轮胎表面的胎面花纹。 轮胎成型 检查工序(完成)
生胎完成
硫化工序
断面高 断面宽 X100
轮辋直径 断面宽 断面宽
断面高
轮胎的断面宽[mm]
轮胎基础知识培训教材
(以31*10.5R15 109S为例 ) 31×10.5 R 15 109 S
速度指数 载重指数 轮辋直径(英寸) 轮胎的断面宽(英寸)
轮 胎 外 径 断面宽
轮胎规格(2)
轮胎的外径(英寸)
轮辋直径
轮胎基础知识培训教材
轮胎基础知识
轮胎基础知识培训教材
轮胎的生产过程
原 材 料 物 理 混 合 天 然 橡 胶
轧 制 合 成 橡 胶
混合过程
主要材料
裁切
混合
轧制
各项材料 加工过程
硫黄
催化剂
氧化锌 碳黑
抗 氧 化 剂
轮胎基础知识培训教材
胎体部分(将帘线压延成带状) 胎体和带束层部分
压延机(将帘线的两面都挂上橡胶)
裁断
浸于药品中 压延机
路拱(程度不同影响不同)。
轮胎基础知识培训教材
不可避免的因素--工作和行程种类
长途行驶,胎温升高,减少轮胎正常里程数;
过高频率的停顿与启动加快胎面磨耗; 工作环境的路面情况恶劣、轮胎易意外破损,过早损坏。
轮胎基础知识培训教材
夏季的胎面磨耗程度一般会比冬季的快,
轮胎-胶料生产基础知识

胶料生产基础知识一、轮胎简介按结构分:斜交胎和子午线轮胎(分半钢和全钢)。
简介斜交胎与子午胎,全钢子午胎,一般由三层钢丝带束层、一层钢丝胎体及肩部各两层零度带束层组成。
二、轮胎制造工艺流程炼胶工序:生产混炼胶→压延压出工序:生产半成品部件→裁断成型工序:半成品加工与组装成胎胚→硫化工序:将胎胚硫化成成品胎→成品检验:外观和X光检验三、炼胶工序工艺流程1、母胶:原材料加工、称量(小药加工、称量;炭黑油料加工输送称量;生胶烘胶加工称量)→密炼机内混炼→双螺杆挤出压片→浸隔离剂→上冷却线挂片冷却→摆片2、终炼胶:母胶称量、小药称量→密炼机内混炼→开炼机补充混炼压片→浸隔离剂→上冷却线挂片冷却→摆片四、胶料生产工艺的几个基本概念1、塑炼①塑炼是指通过机械力、热、氧或化学塑解剂作用,使生胶的分子链断裂,使其由强韧的弹性状态转变为柔软的塑性状态的工艺过程。
②生胶塑炼的目的是为了获得工艺要求的可塑性,使混炼过程中橡胶与配合剂易于混合而且分散均匀,在压延时易于渗入纤维,在挤出和成型时容易操作,胶料溶解性和粘着性得以提高,并且获得适当的流动性,使模型制品有清晰的花纹轮廓。
子午胎胶料一般不单独进行塑炼。
2、混炼①混炼是指通过炼胶机将各种配合剂均匀加入具有一定塑性的生胶中的工艺过程。
②混炼的目的是在生胶中加入各种配合剂,以提高橡胶制品的使用性能,改善加工工艺性能,节约生胶及降低成本。
③混炼胶质量要求:一是能保证成品具有良好的物理机械性能,二是应具有良好的加工工艺性能。
④混炼,目前生产中一般分为母炼和终炼,相应的胶料称为母炼胶和终炼胶。
因为胶料配方体系有些配合剂对温度敏感,高温易起反应,一般要求在较低的混炼温度。
这些配合剂如硫化剂、促进剂、防焦剂及子午胎用的部分粘合剂等。
所以一般母炼胶是指在生胶中加入除硫化剂、促进剂、防焦剂及子午胎用的部分粘合剂等所有配合剂的胶料,母炼段一般是在高温快速下进行混炼的,现一般采用大型密炼机(如GK400N)进行生产。
轮胎成型岗位培训教材

轮胎成型岗位培训教材成型工艺参数控制1、成型平面宽度必须满足施工标准(公差±1mm)成型机平面宽:是指两个胎圈之间的距离.测量时根据机型不同分为内缘和外缘两种测量方式,卡客二车间LCZ-3机型使用外缘测量方式,其他成型机使用内缘的测量方式。
平面宽的大小直接影响轮胎的质量,不能随意调整和更改(平面宽过大时,易造成胎体变形,平面宽过小时,易造成胎里显线)测量平宽时,卷尺要顶在钢丝圈底部测量,对胎圈夹持器的各个爪位置进行测量,不能简单测量一个爪,保证各个钢爪在同一平面。
且保证从中心到两个胎圈的距离对称相等2、成型机头宽、定型及超定型宽度1)、成型机头宽要正确。
(不能过大或过小,否则胎圈就不能准确地落在锁块内,易造成脱圈、子口部位有深锁块痕、甚至出现子口显线等质量问题)2)、机头宽度的一般设定经验值如下:天津三鼓成型机:平宽+80/90mm左右天津两鼓成型机:平宽-70/80mm左右LCZ成型机、日本三鼓成型机:平宽-110mm左右四鼓成型机:平宽+90mm左右注意:机头宽度与成型鼓和生产的轮胎规格有关,不同成型鼓机头宽设定不完相同;在同一成型机生产不同轮胎,经验数值也不相同.最直接验证的方法是:根据经验值设定宽度后,然后将胎圈传送到锁块位置进行验证,保证胎圈恰好落在中间即可)3)、定型及超定型宽度决定胎胚形状(不易过大或过小,否则易出现胎胚形状异常)3、各部件定位准确性及位置定位角度1)胎侧子口与内衬层宽复合件定位要准确,不能随意内移或外移。
(否则,易出现子口显线、子口不饱满等质量缺陷)2)内衬层上料时,注意内衬层方向不要上反从胎里向胎体数依次为:WM/WA或GM层-GG或GB层(靠近胎体)。
3)胎圈包布(钢丝/尼龙加强层)按灯光内定位,加强层要求定位公差≤2mm。
当产品需要上钢丝(正八字型)和尼龙包布加强层(倒八字型)时,注意方向不能上反(定位不准确,易造成与胎体端点差级过大或过小,造成圈空圈裂等质量问题)4)胎体中心对准中心灯光,边部与边灯对齐,要求定位公差≤2mm。
- 1、下载文档前请自行甄别文档内容的完整性,平台不提供额外的编辑、内容补充、找答案等附加服务。
- 2、"仅部分预览"的文档,不可在线预览部分如存在完整性等问题,可反馈申请退款(可完整预览的文档不适用该条件!)。
- 3、如文档侵犯您的权益,请联系客服反馈,我们会尽快为您处理(人工客服工作时间:9:00-18:30)。
(5)倒炼: 混炼机排出的Q胶按照一定的厚度通过26”辊后利用输送带送到22”辊
(6)压片: 在26”辊上一次倒过的Q胶通过22”辊压成一定的厚度和宽度 (7)移送: 一定厚度和宽度打出的胶上钢印胶料编号, 区分1Batch 加压痕移送 (8)沉淀: 为了防止压成片状的混炼胶装载时相互粘连, 使胶通过装有隔离剂的Dip Tank,
(9)搬运及保管: 装载一定量的 Pallet上贴记录胶片编号、作业日、作业组、作业机台的标签,
搬运到指定的地点保管
** 用语解释: - A作业: 原材料橡胶加A药品后在密炼机里混合的作业 - A药品: 与原材料橡胶混合后加热也不会使橡胶硬化的药品类, 一般有补强剂、防老剂、 活性剂、软化剂、增粘剂等. - A胶 : 原材料橡胶和A药品混合完了的胶 (Compounds)
—-
179 —
8. 轮胎生产工艺
1. 炼胶工程
4. 炼胶工程对品质的影响
1)A作业对品质的影响 (1)在混炼胶中各种配合药品的作用
药品区分 碳黑(CARBON) 作 加强橡胶的强度 用 对品质的影响 如果没有定量投入, 压出工程Gauge不准确, 并且轮胎的磨耗 也受影响 操作油(Process Oil) 使橡胶加工(混炼/压出)圆滑的软化剂 定量以上投入时降低橡胶强度, 轮胎耐磨性、耐老化性下降, 引发脱层 氧化锌及硬脂酸 (Zno & Stearic Acid) 防止因臭氧而发生轮胎裂口及因轮胎 内部发热而发生脱层(SEPARATION) 定量以上投入时发生喷霜(Blooming)现象, 影响轮胎外观(特别是 A102); WAX又降低Topping Cord的粘度(Tack),引发U/F不良和 气泡类不良 增粘剂(TACKIFIER) CO-NAPH 提高半成品(压出及压延物)的粘度 维持钢丝(STEEL CORD)和橡胶的接合 定量以上投入时粘度过大(OVER TACK), 引发半成品的大量废弃 定量以上投入时急剧降低STEEL CORD和橡胶的接合力, 引发 BELT SEPARATION 及 SIDE SEPARATION 等品质问题
—182 —
8. 轮胎生产工艺
1. 炼胶工程
4. 炼胶工程对品质的影响
F. DIP POWDER要完全干燥: 炼胶室污染及因压出时混入水份而发生气泡(SPONGE现象) G. ROLLER DIE 操作者胶料编号MARKING 要彻底: 防止Q作业时误用胶料
2)Q作业对品质的影响
(1)混炼胶中各种配合药品的作用
Batch编号的标签后移到制定地点保管
(11)出库: 品质管理科Batch检查完了后只限合格的Pallet搬运到使用地点(压出/压延/钢丝) 使用 ** 用语解释: - Q作业: 把A胶和Q药品在密炼机里混合的作业 - Q药品: 与A胶混合后经过一定时间, 一定温度后使橡胶硬化的药品类, 一般有硫化剂、硫化 促进剂、硫化迟延剂等 - Q胶 : A胶和Q药品混合完了的胶 (Compounds)
药品区分 硫 磺 硫化剂 作 用 对品质的影响 定量以下投入时因橡胶强度下降(欠硫)而耐磨性降低, 定量以上 投入时发生半制品喷霜,成为粘度下降的原因 而且成品又发生因过硫引起的胎面裂口及品质低下 *为了防止硫磺喷霜, 使用不容性硫磺及高分子硫磺等, 是表面 OIL处理的硫磺. 密炼机放出温度105℃以上时不容性硫磺迅速 变成GROUND硫磺, 不容性硫磺的投入优点就会消失. 硫化促进剂 硫化迟延剂 降低硫化温度及促进硫化反应 加工中防止早期硫化(防止胶烧) 定量以下投入时发生欠硫, 过量投入时发生胶烧 定量以下投入时加工中引发早期硫化 (胶烧)
DIP TANK
Wig Wag
SPRAY
密 炼ห้องสมุดไป่ตู้机
卸 料 斗
挤 出 机
—-
174 —
8. 轮胎生产工艺
1. 炼胶工程
2. 炼胶工程流程图
2) Q作业工程流程图 Batch 抽样 流程图 A胶 计量 干 投 入 Q药品 计量 混 合 排 后 工 装 载 搬 运 保 管 出 库 程 移 送 检查
压
片 1次
压 片 2次
沉 淀
燥 ,
出
冷
却 Batch Off Machine
Roller Conveyor
Chain Conveyor
22” Sheet Mill
22” Sheet Mill
26” Dump Mill
Rheometer
使用设备
自动称(Q药品)
计量输送带
(橡胶)
投 入 输 送 带
SPRAY DIP TANK
(3)作业遵守事项及对品质的影响
A.MIXING CYCLE 及 OIL 投入时间
对碳黑分散度及橡胶粘度(MOONEY VISCOSITY)有很大影响 - 碳黑分散度下降时, 压出作业中边部容易被撕裂, 容易发生胶烧, 并且胎面磨损性差 - 橡胶粘度不仅影响压出物及Topping Gauge,如果粘度高时橡胶加工时发热大,容易胶烧 —181 —
—-
176 —
8. 轮胎生产工艺
1. 炼胶工程
3. 炼胶工程操作方法
1)A作业 (7)干燥冷却: 为了干燥通浸胶漕后粘在胶片表面的隔离剂, 冷却胶片, 把胶片挂在Bar Conveyor 的过程, Conveyor的一面是挂胶, 另一面抽出. (8)装载: 为了下一道工序, 把干燥并冷却的胶片装在 Pallet上, 一般装载5 Batch左右.
1)原料胶上均匀地添加配合剂
2)给后工程适当的加热性及作业性, 使加工容易 3)配合物(胶片)的物性充分发挥其目的
最佳混合是即满足上述3点质量要求, 又满足量(生产性)的要求的混合方法.
—-
172 —
8. 轮胎生产工艺
1. 炼胶工程概要
1. 炼胶工程
—-
173 —
8. 轮胎生产工艺
1. 炼胶工程
8. 轮胎生产工艺
—-
170 —
8. 轮胎生产工艺
1. 炼胶工程
1. 炼胶工程概要
2. 炼胶工程流程图
3. 炼胶工程操作方法
4. 炼胶工程对品质的影响
—-
171 —
8. 轮胎生产工艺
1. 炼胶工程
1. 炼胶工程概要
为了取得轮胎各部位用途别所需要的胶料特性, 在天然胶、合成胶上添加操作油、补强剂、 防老剂、活性剂、硫化剂及硫化促进剂等配合剂, 按照混合示方书均匀混合的工程 炼胶工程混炼的状态对所需要的橡胶制品的品质性能有重大影响, 对压出、压延、Bead、硫化 等后工程的作业性也给很大影响, 因此, 必须充分满足下列项目:
—-
177 —
8. 轮胎生产工艺
1. 炼胶工程
3. 炼胶工程操作方法
2)Q作业 (1)计量: 把混合的A胶和Q药品利用电子称和计量输送带按照混合示方书计量好一次作业的重量. (2)投入: 把计量好的A胶和Q药品投入到密炼机内的过程, 利用投入输送带投入 (3)混合: 计量投入的A胶和Q药品在密炼机内均匀混合的过程, 利用密封型混炼机混炼到混合 示方书规定的时间 (4)排出: 混炼一定时间后往外排出的过程
Wig Wag
密 炼 机
卸 料 斗
—-
175 —
8. 轮胎生产工艺
3. 炼胶工程操作方法
1)A作业
1. 炼胶工程
(1)计量: 把原材料橡胶和配合剂按照混合示方书称一次作业的重量, 有自动计量和手工计量. (2)投入: 把计量好的橡胶和配合剂投入到密炼机内的过程, 自动计量的是自动投入, 手工计量 的是在密炼机前面通过投入输送带投入
8. 轮胎生产工艺
1. 炼胶工程
4. 炼胶工程对品质的影响
B.药品用电子称及称量输送带精度维持: 技术标准上投入物的重量偏差是SPEC±1 以内 C.异物混入不良防止对策 - CARBON ROTARY SCREW FEEDER清扫: 禁止混入碳黑粒子 - 自动投入口的药品投入口清扫: 氧化锌和硬脂酸的定量投入 - ROLLER DIE CHAMBER 内部清扫: 禁止混入碳黑粒子 - ROLLER DIE EXTRUDER和CALENDER之间的清扫: 禁止杂胶的混合
- 天然胶切割机与合成胶切割机: 禁止混入钉子、木头、螺丝等异物
D.自动计量剂设定及手动药品称量作业时务必与混合示方书对照操作: 防止药品误使用及 定量投入 E.ROLLER DIE CALENDER上胶片的厚度要维持工程管理标准: 维持橡胶精度(MOONEY VISCOSITY),
TMIN不良防止, 胶烧防止
—-
183 —
8. 轮胎生产工艺
—-
180 —
8. 轮胎生产工艺
1. 炼胶工程
4. 炼胶工程对品质的影响
(2)各种POLYMER的特点 - 天然胶: 弹性优秀, 黏着里大, Green strength 高 - SBR - BR : 加工性优秀, 耐磨性与天然胶相同 : 耐磨性最优秀
- BUTYL RUBBER: 耐空气透气性优秀 - EPDM : 耐臭氧裂口性优秀
在胶料表面涂隔离剂的过程. 这时按照胶料的用途有时也分隔胶片(2,4,8分隔)
—178 —
8. 轮胎生产工艺
1. 炼胶工程
3. 炼胶工程操作方法
2)Q作业 (9)干燥冷却: 为了干燥通浸胶漕后粘在胶片表面的隔离剂, 冷却胶片, 把胶片挂在Bar Conveyor 的过程, Conveyor的一面是挂胶, 另一面抽出. (10)装载: 把干燥并冷却的胶片每一定量装在 Pallet上,贴记录胶料编号、作业日、作业组及
(3)混合: 计量投入的橡胶和配合剂在密炼机内均匀混合的过程, 密炼机有密封型和开放型,
我公司使用的是密封型 (4)排出: 在密炼机内达到一定时间, 一定电力或一定温度时往外排出的过程, 时间、电力或 温度在混合示方书上有规定 (5)Sheeting作业: 混炼机内排出的胶用SCREW推, 使其通过2个Roll Calender,被压成片状的 过程. (6)沉淀: 为了防止胶片装载时相互粘连, 使胶片通过装隔离剂的浸胶漕或SPRAY, 表面涂 隔离剂的过程