配料和混炼胶制造工艺
混炼胶生产工艺

混炼胶生产工艺混炼胶是将天然橡胶或合成橡胶与添加剂等原料混合,经过炼胶机的拉、剪、折等作用,使其成为固态胶料的工艺过程。
混炼胶主要分为两种类型:开炼和封闭式混炼。
开炼是将胶料与添加剂放入开炼机中,通过辊子的旋转和挤压,使胶料与添加剂彻底混合。
开炼机分为两辊机和三辊机,其中三辊机是最常用的。
开炼机中的三个辊子分别是主辊、副辊和辅助辊,通过调整辊子的转速和间距,可以控制胶料的温度、时间和剪切力。
开炼的优点是可以灵活调整添加剂的比例和炼胶温度,适用于生产各种不同性能的橡胶制品。
封闭式混炼是将胶料和添加剂放入封闭式混炼机中,通过高速旋转的螺杆将胶料和添加剂挤压、剪切和折叠,使其混合均匀。
封闭式混炼机具有密闭性好、能耗低、工艺简单等优点,适用于大批量生产相同性能的胶料。
混炼胶的生产工艺主要包括以下几个步骤:1. 胶料准备:将天然橡胶或合成橡胶切碎,并经过清洗、脱水等工艺处理,除去杂质和水分,使其达到生产要求。
2. 添加剂配方:根据橡胶制品的要求,制定合适的添加剂配方,包括硫化剂、活性剂、助剂等。
3. 混合:将胶料和添加剂按照一定比例放入混炼机中,通过机械作用,使其混合均匀。
4. 调温:根据橡胶和添加剂的特性,控制炼胶机的温度,使其达到最佳炼胶温度。
5. 炼胶:开炼或封闭式混炼机通过旋转、挤压、剪切等作用,将胶料和添加剂进行彻底混合,形成固态的胶料。
6. 切割和离心:经过炼胶机的处理,胶料被切割成块状,并通过离心机的旋转,将胶料中的水分去除。
7. 成型:将炼胶后的胶料放入成型机中,进行定型,形成成品。
混炼胶生产工艺的关键是控制炼胶机的温度、时间和剪切力。
温度过高或时间过长会导致胶料老化,性能下降;剪切力过大会使胶料的结构破坏,影响性能。
因此,在生产中需要严格控制这些参数,以获得符合要求的胶料。
混炼胶混炼工艺最终版本

DF混炼胶生产工艺发布日期:2012年3月12日实施日期:批准人:批准日期:实施日期:文件编号:发放编号:控制状态:持有人:大连巅峰集团2012年3月12日综述混炼胶概念及质量要求通过适当的加工将配合剂与生胶均匀的混合在一起制成质量均一的混合物,完成这一加工操作的工艺过程叫做混炼,混出的胶料叫混炼胶。
对混炼胶质量有两方面要求:一、是胶料应具有良好的物理机械性能。
二、是胶料本身具有良好的工艺加工性能。
为保证混炼胶质量、结合本公司的实际情况特此制订炼胶工艺规程。
炼胶工艺规程包括以下方面:①、生产工艺流程图②、原材料加工工艺③、配料工艺④、切胶工艺⑤、塑胶工艺⑥、混炼工艺⑦、一段,二段混炼胶在每一种胶料中应用⑧、返炼操作方法及要求⑨、不合格胶处理1、生产工艺流程图天然胶合成胶配合剂干燥扒皮加工切胶切胶塑炼检验(可塑度)配合制混炼胶取片检验制片沾浆冷却挂牌存放2、原材料加工工艺2.1 粉碎:固体的石蜡每块不大于50g.石油树脂、古马龙每块不大于50g, 松香每块不大于50g,所用设备为人工锤或万能粉碎机。
2.2筛选:硫磺供应厂家要用自制滚动筛选机筛选标准为100目全过。
2.3 加热过滤:机油加热120℃、时间24H,要求供应厂家要过滤120目×2。
2.4加热:松焦油10月1日到次年5月1次加热100℃以上,时间:24H 2.5干燥:烘干室温度: 50~~60℃。
烘干时间:24H~72H烘干范围: 天然胶 (5月1日-10月1日不烘胶).2.5.1技术要求:(1) 天然胶送加温室前必须将表面泥砂、木屑等杂质清理干净,发霉、发臭、腐烂变质的胶块不得送入车间。
(2) 被加温的生胶不得直接接触暖气片等加热热源,防止局部过热流淌。
(3) 生胶等级不得混杂,胶块不落地。
(4)加温后的生胶按先后顺序使用.2.5.2质量标准:(1) 烘完的生胶应保证内外温度均匀一致, 中心温度不低于25℃(2) 烘完的生胶表面无发霉变臭、无杂物和水迹。
橡胶的混炼及混炼工艺

橡胶的混炼及混炼工艺混炼就是将各种配合剂借助炼胶机机械力的作用均匀分散于橡胶中的工艺过程。
混炼过程就是将各种配合剂均匀地分散在橡胶中,以形成一个以橡胶为介质或者以橡胶与某些能和它相容的配合组分(配合剂、其它聚合物)的混合物为介质,以与橡胶不相容的配合剂(如粉体填料、氧化锌、颜料等)为分散相的多相胶体分散体系的过程。
对混炼工艺的具体技术要求是:配合剂分散均匀,使配合剂特别是炭黑等补强性配合剂达到最好的分散度,以保证胶料性能一致。
混炼后得到的胶料称为“混炼胶”,其质量对进一步加工和制品质量有重要影响。
混炼常用的设备是开炼机和密炼机。
①开炼机混炼开炼机混炼的必要条件是根据各种橡胶的粘弹性、松弛时间和转变温度等基本性质,选择合适的辊温(下表),使之处于包辊状态,以便进行混炼。
表1各种橡胶开炼机混炼的适用温度加料顺序是提高开炼机混炼质量的一个重要因素。
加料顺序不当会导致分散不均匀,脱辊、过炼,甚至发生早期硫化(焦烧)等质量问题。
原则上应根据配方中配合剂的特性和用量来决定加料顺序,宜先加量少、难分散者。
后加量大,易分散者;硫黄或者活性大、临界温度低的促进剂(如超速促进剂)则在最后加入,以防止出现早期硫化(焦烧)。
液体软化剂一般在补强填充剂等粉剂混完后再加入,以防止粉剂结团、胶料打滑、胶料变软致使剪切力小而不易分散。
橡胶包辊后,按下列一般的顺序加料:橡胶、再生胶、各种母炼胶→固体软化剂(如较难分散的松香、硬脂酸、固体古马隆树脂等)→小料(促进剂、活性剂、防老剂)→补强填充剂→液体软化剂→硫黄→超促进剂→薄通→倒胶下片。
对于某些特殊胶料(如硬质胶、海绵胶等),则需采取与上述一般加料顺序不同的混炼方法。
除了辊温和加料顺序影响开炼机混炼质量之外,在操作上尚需注意:填胶容量不宜过多,否则不易混炼均匀,一般合成胶容量应比天然橡胶小一些。
在保证混炼质量的前提下,混炼时间应尽量缩短,以防止胶料因过炼而导致物理机械性能下降和影响生产效率。
橡胶制品的基本生产工艺过程

橡胶制品的基本生产工艺过程橡胶制品的生产工艺是一个包含多个步骤的复杂过程。
以下是橡胶制品的基本生产工艺过程:1. 原材料准备:橡胶制品的主要原材料是天然橡胶和合成橡胶。
原材料需要进一步加工,以便在后续的工艺过程中使用。
这包括清洗、切割和破碎等步骤。
2. 配方调配:根据产品要求,制定合适的橡胶配方。
不同类型的橡胶制品需要不同的橡胶配方,以确保产品具有所需的物理性能和特性。
在配方中,可能需要添加硫化剂、防老化剂、增塑剂和填充剂等助剂。
3. 混炼:将橡胶原料和各种助剂混合在一起,形成混炼胶料。
这个过程可以使用混炼机完成,混炼机能够把原料均匀地混合在一起,并产生适当的热量以促进反应。
4. 成型:将混炼好的胶料放入模具中,并通过压力或挤压等方式进行成型。
成型过程根据产品的不同可以使用不同的技术,例如压延、注射、挤出和压痕等。
成型完成后,需要进行烘干或固化以确保产品的硬度和形状。
5. 处理和整理:对成型后的产品进行修整和整理,以确保产品的质量和外观。
这包括去除多余的边角料、刷洗和打磨等处理过程。
6. 检测和检验:对制造完成的橡胶制品进行检测和检验,以确保产品符合预定的标准和要求。
这可以包括物理性能、化学性质、外观和尺寸等方面的测试。
不合格的产品将进行返工或退货。
7. 包装和储存:将合格的产品进行包装,并标明产品的规格、批次和生产日期等信息。
然后将产品储存到仓库或发往销售渠道。
总的来说,橡胶制品的生产工艺包含了原料准备、配方调配、混炼、成型、处理和整理、检测和检验,以及最后的包装和储存。
其中每个步骤都需要精确的操作和控制,以确保最终产品的质量和效果。
橡胶制品的生产工艺是一个精细而复杂的过程,需要严格的控制和技术实力。
接下来将继续介绍橡胶制品的详细生产工艺过程以及一些常见的应用。
8. 二次加工:某些橡胶制品需要进行二次加工,以达到特定的要求和功能。
例如,橡胶密封件可能需要进行模切和槽口切割,橡胶管道可能需要进行穿刺和加强带的固定等。
炼胶工艺流程
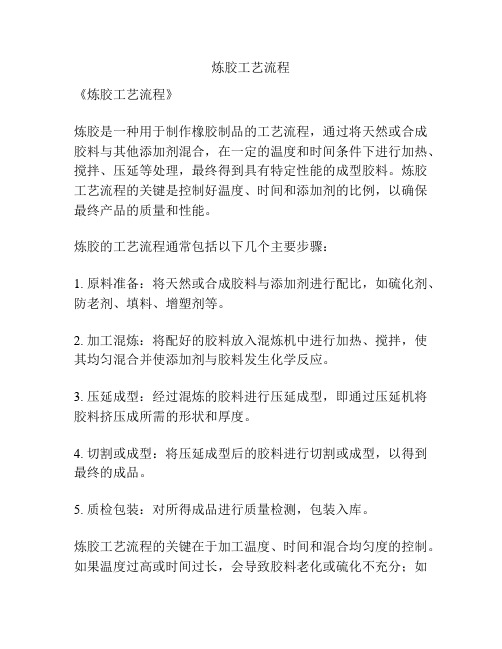
炼胶工艺流程
《炼胶工艺流程》
炼胶是一种用于制作橡胶制品的工艺流程,通过将天然或合成胶料与其他添加剂混合,在一定的温度和时间条件下进行加热、搅拌、压延等处理,最终得到具有特定性能的成型胶料。
炼胶工艺流程的关键是控制好温度、时间和添加剂的比例,以确保最终产品的质量和性能。
炼胶的工艺流程通常包括以下几个主要步骤:
1. 原料准备:将天然或合成胶料与添加剂进行配比,如硫化剂、防老剂、填料、增塑剂等。
2. 加工混炼:将配好的胶料放入混炼机中进行加热、搅拌,使其均匀混合并使添加剂与胶料发生化学反应。
3. 压延成型:经过混炼的胶料进行压延成型,即通过压延机将胶料挤压成所需的形状和厚度。
4. 切割或成型:将压延成型后的胶料进行切割或成型,以得到最终的成品。
5. 质检包装:对所得成品进行质量检测,包装入库。
炼胶工艺流程的关键在于加工温度、时间和混合均匀度的控制。
如果温度过高或时间过长,会导致胶料老化或硫化不充分;如
果混合均匀度不好,会影响到最终产品的性能。
炼胶工艺流程在橡胶制品生产中扮演着重要的角色,通过科学的工艺流程,可以得到质量稳定的橡胶制品。
同时,也需要不断进行工艺改进和技术创新,以适应不同类型和要求的橡胶制品生产。
橡胶试验胶料配料、混炼操作规程
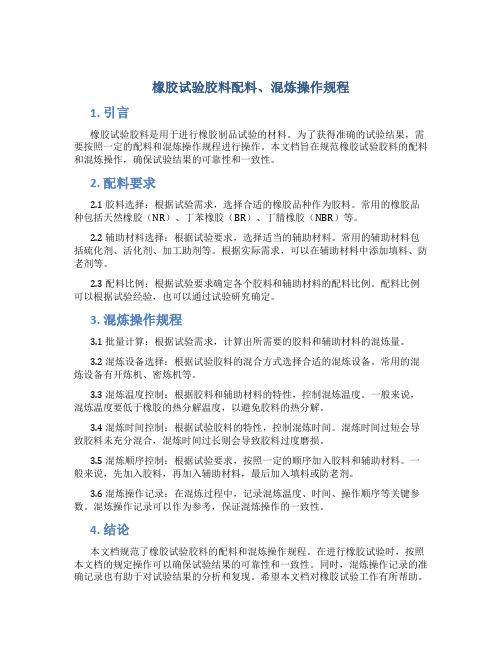
橡胶试验胶料配料、混炼操作规程1. 引言橡胶试验胶料是用于进行橡胶制品试验的材料。
为了获得准确的试验结果,需要按照一定的配料和混炼操作规程进行操作。
本文档旨在规范橡胶试验胶料的配料和混炼操作,确保试验结果的可靠性和一致性。
2. 配料要求2.1 胶料选择:根据试验需求,选择合适的橡胶品种作为胶料。
常用的橡胶品种包括天然橡胶(NR)、丁苯橡胶(BR)、丁腈橡胶(NBR)等。
2.2 辅助材料选择:根据试验要求,选择适当的辅助材料。
常用的辅助材料包括硫化剂、活化剂、加工助剂等。
根据实际需求,可以在辅助材料中添加填料、防老剂等。
2.3 配料比例:根据试验要求确定各个胶料和辅助材料的配料比例。
配料比例可以根据试验经验,也可以通过试验研究确定。
3. 混炼操作规程3.1 批量计算:根据试验需求,计算出所需要的胶料和辅助材料的混炼量。
3.2 混炼设备选择:根据试验胶料的混合方式选择合适的混炼设备。
常用的混炼设备有开炼机、密炼机等。
3.3 混炼温度控制:根据胶料和辅助材料的特性,控制混炼温度。
一般来说,混炼温度要低于橡胶的热分解温度,以避免胶料的热分解。
3.4 混炼时间控制:根据试验胶料的特性,控制混炼时间。
混炼时间过短会导致胶料未充分混合,混炼时间过长则会导致胶料过度磨损。
3.5 混炼顺序控制:根据试验要求,按照一定的顺序加入胶料和辅助材料。
一般来说,先加入胶料,再加入辅助材料,最后加入填料或防老剂。
3.6 混炼操作记录:在混炼过程中,记录混炼温度、时间、操作顺序等关键参数。
混炼操作记录可以作为参考,保证混炼操作的一致性。
4. 结论本文档规范了橡胶试验胶料的配料和混炼操作规程。
在进行橡胶试验时,按照本文档的规定操作可以确保试验结果的可靠性和一致性。
同时,混炼操作记录的准确记录也有助于对试验结果的分析和复现。
希望本文档对橡胶试验工作有所帮助。
Reference[1] 橡胶制品试验胶的混炼操作规程和配料规定,中国橡胶工业协会[2] 橡胶试验方法,中国标准出版社。
常见生胶与混炼胶的加工工艺
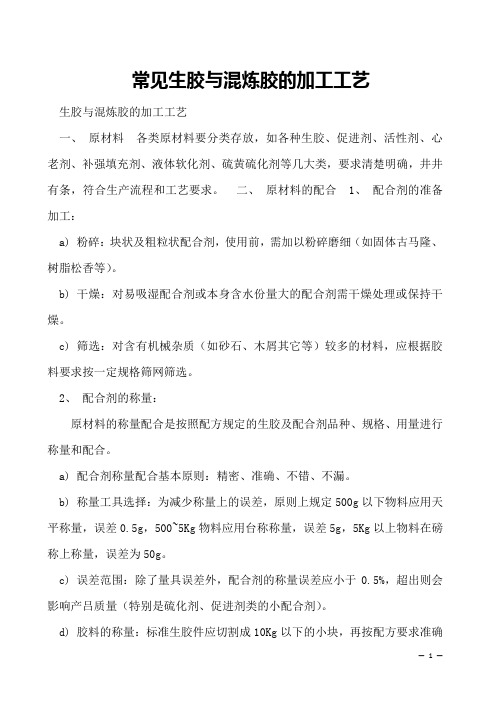
常见生胶与混炼胶的加工工艺生胶与混炼胶的加工工艺一、原材料各类原材料要分类存放,如各种生胶、促进剂、活性剂、心老剂、补强填充剂、液体软化剂、硫黄硫化剂等几大类,要求清楚明确,井井有条,符合生产流程和工艺要求。
二、原材料的配合 1、配合剂的准备加工:a) 粉碎:块状及粗粒状配合剂,使用前,需加以粉碎磨细(如固体古马隆、树脂松香等)。
b) 干燥:对易吸湿配合剂或本身含水份量大的配合剂需干燥处理或保持干燥。
c) 筛选:对含有机械杂质(如砂石、木屑其它等)较多的材料,应根据胶料要求按一定规格筛网筛选。
2、配合剂的称量:原材料的称量配合是按照配方规定的生胶及配合剂品种、规格、用量进行称量和配合。
a) 配合剂称量配合基本原则:精密、准确、不错、不漏。
b) 称量工具选择:为减少称量上的误差,原则上规定500g以下物料应用天平称量,误差0.5g,500~5Kg物料应用台称称量,误差5g,5Kg以上物料在磅称上称量,误差为50g。
c) 误差范围:除了量具误差外,配合剂的称量误差应小于0.5%,超出则会影响产吕质量(特别是硫化剂、促进剂类的小配合剂)。
d) 胶料的称量:标准生胶件应切割成10Kg以下的小块,再按配方要求准确称量后,备于投料使用,误凑巧不超过0.5%。
e) 操作:生胶配合剂的称量配合,应严格按照每日生产计划及配方要求进行,保正精度,避免药品的漏用和错用,称好的配合剂合理装载,做好标识,按一定的规则顺序放置备用,混炼时按一定的工艺要求顺序投料。
f) 质量控制:对具体胶料及所用的配合剂应有明确的文字标识,并设质量跟踪卡,以便质量检查及生产管理。
三、混炼工艺 1、生胶的塑炼:a) 投料:开炼机塑炼及混炼时,所有生胶、母胶、并用胶,须在靠炼胶机大齿轮一则加入。
b) 根据各种不同的生胶性能,应采用不同的塑炼方法,具体如下: 1) 天然胶:一段塑炼:以0.5~1mm辊距将生胶破开,薄通落盘,如此重复过机到规定时间或次数。
炼胶工艺流程
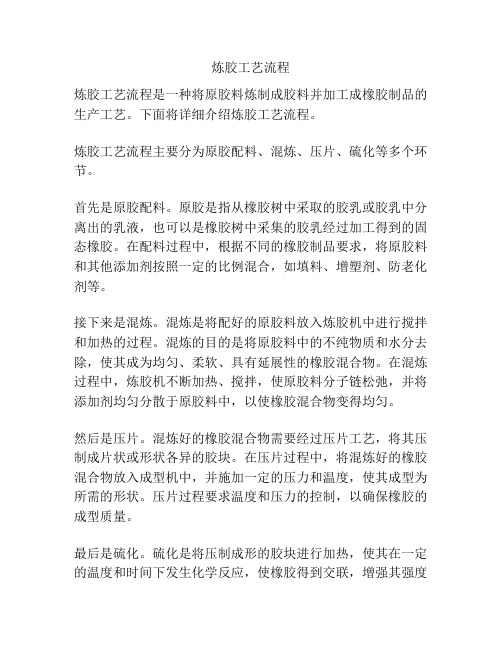
炼胶工艺流程炼胶工艺流程是一种将原胶料炼制成胶料并加工成橡胶制品的生产工艺。
下面将详细介绍炼胶工艺流程。
炼胶工艺流程主要分为原胶配料、混炼、压片、硫化等多个环节。
首先是原胶配料。
原胶是指从橡胶树中采取的胶乳或胶乳中分离出的乳液,也可以是橡胶树中采集的胶乳经过加工得到的固态橡胶。
在配料过程中,根据不同的橡胶制品要求,将原胶料和其他添加剂按照一定的比例混合,如填料、增塑剂、防老化剂等。
接下来是混炼。
混炼是将配好的原胶料放入炼胶机中进行搅拌和加热的过程。
混炼的目的是将原胶料中的不纯物质和水分去除,使其成为均匀、柔软、具有延展性的橡胶混合物。
在混炼过程中,炼胶机不断加热、搅拌,使原胶料分子链松弛,并将添加剂均匀分散于原胶料中,以使橡胶混合物变得均匀。
然后是压片。
混炼好的橡胶混合物需要经过压片工艺,将其压制成片状或形状各异的胶块。
在压片过程中,将混炼好的橡胶混合物放入成型机中,并施加一定的压力和温度,使其成型为所需的形状。
压片过程要求温度和压力的控制,以确保橡胶的成型质量。
最后是硫化。
硫化是将压制成形的胶块进行加热,使其在一定的温度和时间下发生化学反应,使橡胶得到交联,增强其强度和耐磨性。
硫化是一个重要的环节,通过硫化使橡胶制品具备了优良的性能,如耐候性、耐油性、耐磨性等。
以上就是炼胶工艺流程的主要环节。
通过原胶配料、混炼、压片和硫化等过程,将原始的橡胶材料加工成各种形态的橡胶制品。
炼胶工艺流程的每个环节都需要精确的控制温度、压力和时间等参数,以确保橡胶制品的质量和性能。
炼胶工艺的改进和创新对于提高橡胶制品的品质和降低生产成本具有重要意义。
- 1、下载文档前请自行甄别文档内容的完整性,平台不提供额外的编辑、内容补充、找答案等附加服务。
- 2、"仅部分预览"的文档,不可在线预览部分如存在完整性等问题,可反馈申请退款(可完整预览的文档不适用该条件!)。
- 3、如文档侵犯您的权益,请联系客服反馈,我们会尽快为您处理(人工客服工作时间:9:00-18:30)。
配料和混炼胶制造工艺混炼胶的主要工艺流程:配合剂的加工→橡胶和配合剂的称量→混炼→下片冷却存放→胶料快检。
一、配合剂的加工和称量:对橡胶制品所用的橡胶和配合剂进行准备加工,并按照技术配方规定称量配合的加工工艺过程,称为加工和配料工序。
1、原材料的加工:(1)天然胶要烘胶,配有烘胶房,大块切成小块。
(2)配合剂的加工和准备的目的:确保配合剂的质量,便于混炼的工艺操作,提高混炼分散效果,实现自动化条件,制造好的胶料。
(3)配合剂的加工方式:--粉碎:按一定的质量标准将大的颗粒粉碎或磨细。
目的:增加配合剂与生胶的接触面积,便于混炼均匀,便于配合剂的分散。
--干燥:将配合剂在专门设制的加温室或干燥器内进行加热干燥。
目的:除去和减少配合剂中水分及低挥发性杂质,保证配合剂质量。
因为水分过多易结团,则在混炼过程不利于分散,最后导致混炼不均。
--筛选:利用各种筛网设备对配合剂进行筛选。
目的:去掉颗粒大的杂物。
--熔化、过滤和蒸发脱水:对易熔化的固体和粘性液体进行加热熔化,通过筛网除去杂质,对于液体软化进行蒸发脱水。
目的:除去水分。
2、配合剂的称量和配合:(1)按照配方规定的配合剂的品种、规格、数量,按配方要求进行分别称量。
此工序对混炼胶的质量至关重要。
如漏配、错配,不符合称量公差。
多配、少配等。
(2)对称量和配合的操作要求。
a料种准确。
b称量准确。
c不漏配和错配。
d不多配和少配。
如:硫化剂和促进剂的称量天平的精度要求1-5g。
(3)配料工序要注意的方面:a要注意防潮,配合剂要存放在干燥的区域。
b有些配合剂如氧化镁(MgO)、氧化钙(CaO),遇到水后就会发生化学反应,就改变了配合剂本身的性能。
所以在配料和存放过程中必须注意防水,出现结团就不能使用。
c防火,如硫黄要特别注意,电气开关的下面不允许存放,生胶和CB也要注意防火。
特别注意电气焊。
d防混料,因为在配合室原材料很多,并且有些外观差不多,易出现混料,所以必须定置存放,有明显标志。
没有标志的药品,不能使用,必须经取样试验确定后才能使用。
二、混炼工序:1、将生胶与各种配合剂通过专用炼胶机均匀地混合成一体的加工工艺过程称为混炼工序。
经过混炼加工制成的胶料称为混炼胶。
混炼胶目的:(1)制备物理机械性能均匀一致,达到配方要求。
(2)改善胶料的加工工艺性能,满足后工序的加工要求。
(3)降低成本,满足产品质量要求。
(4)提高橡胶制品的使用性能。
2、混炼胶的质量要求:(1)保证胶料各项快检指标的合格。
(2)有良好的加工工艺性能。
(3)保证成品具有良好的物理机械性能。
3、生产合格混炼胶要满足:(1)配合剂分散均匀,避免出现结团现象。
(2)使胶料具有特定的粘度、焦烧值,保证各项工艺过程中的安全性和顺利进行。
(3)要使生胶与补强剂产生一定数量的结合橡胶,有良好的补强效果。
补强剂主要有CB、SiO2.nH2O(白炭黑)。
(4)在保证混炼胶质量的前提下,尽量缩短混炼时间,减少动力消耗,避免过炼。
4、胶料的混炼由密炼机、上辅机、下辅机组成的炼胶生产线。
(1)上辅机是将粉状、液体、颗粒状、块状等原材料经储备、称量、输送投入到密炼机的装置。
(2)下辅机是将密炼机混炼排出的胶料压片直到叠片切割等一系列的装置。
上辅机是为密炼机配套的,有炭黑、油类、粉药、生胶四类称量,输送装置,主要有a炭黑输送装置,即CB解包房,CB由风压打入储存罐内,按品种依次投入到悬挂的自动秤上,然后投入密炼机内。
b液体软化剂输送系统。
C小药称量系统,用低熔点的聚乙烯包装袋,包装,然后投入密炼机内。
下辅机有两种形式,A:开炼机;B:双螺杆挤出机,一般用于压母炼胶的胶片。
5、密炼机的工艺条件:(1)生胶和各种配合剂的重量和配料重量公差。
(2)装胶容量,即填充系数。
(3)密炼室的加料顺序。
大多数混炼分三段,分清每段所加的原材料。
(4)混炼时间。
(5)混炼排胶温度。
(6)上顶栓的压力。
(7)密炼机的转子转速。
(8)混炼胶的存放时间和存放温度,要求存放时间的目的是使各种配合剂充分分散。
(9)冷却水进水口的压力和温度及出水口温与进水口水温的温差,进水口温度为25±2℃,压力越大,流量越大。
如果进水温度过低,密炼室内易结水珠,配合剂易结团,温度过高,冷却效果不佳。
6、混炼周期的控制方法:时间、温度、能量消耗、功率积分等方法,一般控制方法以温度为主,辅助参考时间的方法,先进的方法是以能量为主,温度为辅。
7、各段胶要求要存放一段时间的目的有:(1)使胶料恢复疲劳、松驰,在密炼机中受到剪切力。
(2)减少胶料的收缩。
(3)使配合剂在胶料中继续扩散。
(4)使橡胶与炭黑进一步形成结合橡胶,提高补强效果。
三、胶料快检:混炼胶的质量好坏直接影响下工序的工艺性能和成品的最终质量,所以必须控制胶料的质量。
1、胶料快检:对密炼机混炼制成的终炼胶随即取胶料试片在很短的时间内用专门的快检仪器进行流变仪、门尼粘度、门尼焦烧、硬度、比重等多项指标的检验,以此判断终炼胶的合格。
2、快检检测设备和仪器:(1)平板硫化机,用于硫化胶料快检试片。
(2)6″炼胶机,用于炼压粘合胶料的试片。
(3)流变仪,用于胶料流变性能的检验,即硫化曲线。
(4)门尼焦烧仪器,用于胶料粘度值和焦烧时间的检验。
(5)硬度仪器,用于胶料的硬度的检验。
(6)比重,用于胶料的比重的检验。
(7)电力拉力机,用于粘合胶料的钢丝抽出力的检验。
(8)挺性检验仪器,用于胶料的挺性检验。
胶辊砻谷胶辊一、浅色砻谷胶辊配方1丁苯橡胶(1502) 100 氧化锌7硬脂酸1防老剂RD 0.5白炭黑80钛白粉5 环烷油4古马隆树脂4 二甘醇2促进剂CZ 1 硫黄5合计209.5硫化胶物性(150℃×60min)硬度(邵尔A型)84度;拉伸强度19.62MPa;扯断伸长率570%。
70℃×168h老化后性能变化:硬度+2度,拉伸强度-7.3%,扯断伸长率-28%。
阿克隆磨耗(5000次)1.815cm3;弹性42%。
配方2丁苯橡胶(1502) 100 氧化锌7硬脂酸1白炭黑(VN3) 65本质素处理的碳酸钙15 钛白粉5 环烷油5古马隆树脂5 二甘醇2促进剂CZ 1 胶体硫黄5 合计211硫化胶物性(160℃×30min)硬度(邵尔A型)89度;拉伸强度19.3MPa;300%定伸应力4.41MPa;扯断伸长率700%;撕裂强度33.3kN/m;80℃×2h 后硬度变化2度。
配方3丁苯橡胶(1500) 100 活性氧化锌2硬脂酸1防老剂RD 2白炭黑(VN3) 85古马隆树脂(70℃) 5 环烷抽5松香2 二甘醇3促进剂DM 1促进剂D 1促进剂H 2硫黄2.5苯甲酸1硅烷偶联剂Si-69 0或3 合计212.5或215.5硫化胶物性(150℃×60min;括号内、外相应为Si-69为3和0质量份的数据)硬度(邵尔A型)94度(94度);拉伸强度14.27MPa(19.8MPa);300%定伸应力5.69MPa(13.04MPa);扯断伸长率560%(435%);DIN磨耗166mm3(138mm3);定负荷伸长24%(16%)。
配方4(白色砻谷胶辊)溶聚丁苯橡胶(4003)①30溶聚丁苯橡胶(2000R)②40 顺丁橡③30氧化锌5硬脂酸2防老剂SP 1白炭黑(VN3) 60钛白粉5 二甘醇5环烷油5古马隆树脂8促进剂DM 1.5促进剂TMTM 0.3 硫黄5合计197.8①Tufprene 4003,日本旭化成公司生产。
②Tufprene 2000R,日本旭化成公司生产。
③Asadene NF 35R,日本旭化成公司生产。
硫化胶物性(160℃×10min)硬度(邵尔A型)91度;拉伸强度18.91MPa;扯断伸长率920%;撕裂强度49kN/m;阿克隆磨耗0.1cm3/1000转;德墨西亚屈挠龟裂4800次。
配方5丁苯橡胶(1502) 100 氧化锌7.5硬脂酸3防毫剂RD 1白炭黑75钛白粉11 二甘醇2环烷油2古马隆树脂3 促进剂CZ 1.2 硫黄4合计213.7配方6丁苯橡胶(1500) 83天然橡胶(SMR 5) 10 高苯乙烯树脂母胶①14 氧化锌5硬脂酸4防老剂264 1白炭黑(Hi-Sil 233) 80 聚乙二醇(4000) 3 古马隆树脂15促进剂H 1促进剂NOBS 2促进剂TMTM 0.7 不溶性硫黄10合计228.7①丁苯橡胶与高苯乙烯树脂的共混比例为50:50。
硫化胶物性(150℃×15min)硬度(邵尔A型)93度(20℃下测),85度(100℃下测);拉伸强度19.72MPa;100%定伸应力5.98MPa;扯断伸长率250%;皮克磨耗指数126。
弹性:29%(20℃下),52%(100℃下)。
古德里奇试验(50℃,17.5%,1MPa,20min):硬度(邵尔A型)92度,变形5.7%,生热27℃。
配方7丁苯橡胶(1500) 100 高密度聚乙烯20低密度聚乙烯10氧化锌5硬脂酸3防老剂D 1.5白炭黑70 古马隆树脂10硅烷偶联剂KH-580 1.5 促进剂D 0.5促进剂DM 1.5DCP 0.4硫黄9合计232.4硫化胶物性(151℃×35min)硬度(邵尔A型)92~95度;拉伸强度19.1MPa;扯断伸长率250%;阿克隆磨耗0.091cm3。
配方8丁苯橡胶50天然橡胶30寓苯乙烯树脂母胶①20 氧化锌5 机油1古马隆树脂6凡士林4促进剂M 1.5促进剂TMTD 0.2硬脂酸2防老剂SP 2 白炭黑80 硫黄6合计211.7①HS-860。
硫化胶物性硬度(邵尔A型)85度;拉伸强度17.8MPa;扯断伸长率316%;阿克隆磨耗0.106。
配方9丁苯橡胶40天然橡胶30丁腈橡胶(26) 30 氧化锌5硬脂酸2防老剂SP 2白炭黑80 机袖1古马隆树脂6凡士林4促进剂M 1.5促进剂TMTD 0.2 硫黄8合计213.7硫化胶物性硬度(邵尔A型)81度;拉伸强度16.4MPa;扯断伸长率306%;阿克隆磨耗0.098cm3。
配方10丁苯橡胶70 顺丁橡胶30 氧化锌10 硬脂酸2防老剂RD 1 白炭黑65 白艳华15钛白粉20三乙醇胺2环烷油5古马隆树脂3 促进剂CZ 1.2 硫黄4合计228.2配方11天然橡胶100 氧化锌5硬脂酸2防老剂SP 2 白炭黑85机油5 古马隆树脂6凡士林4促进剂M 1.5促进剂TMTD 0.2 硫黄10合计220.7硫化胶物性硬度(邵尔A型)83度;拉伸强度20.2MPa;扯断伸长率385%;阿克隆磨耗0.163cm3。
配方12天然橡胶(1号烟片) 100 活性氧化锌5硬脂酸3防老剂RD 2白炭黑(VN3) 80环烷油5松香2 二甘醇3促进剂D 1促进剂H 1促进剂CZ 1硫黄2.5苯甲酸1硅烷偶联剂Si-69 0或3 合计206.5或209.5硫化胶物性(10℃×30min;括号内、外相应为Si-69为9和。