Master CAM X 第3章 二维铣削加工
MasterCAM练习题14:二维铣削加工
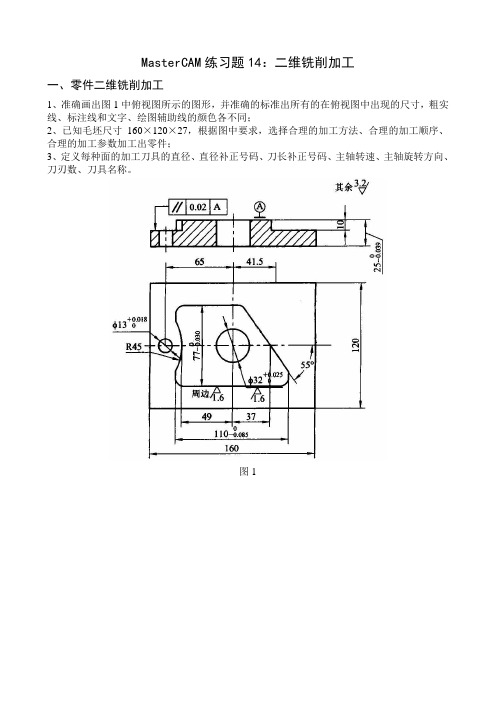
MasterCAM练习题14:二维铣削加工
一、零件二维铣削加工
1、准确画出图1中俯视图所示的图形,并准确的标准出所有的在俯视图中出现的尺寸,粗实线、标注线和文字、绘图辅助线的颜色各不同;
2、已知毛坯尺寸160×120×27,根据图中要求,选择合理的加工方法、合理的加工顺序、合理的加工参数加工出零件;
3、定义每种面的加工刀具的直径、直径补正号码、刀长补正号码、主轴转速、主轴旋转方向、刀刃数、刀具名称。
图1
二、曲面铣削加工
1、绘制如图2所示的零件图形,并对其进行曲面加工。
准确标注在图2中出现的尺寸,标注线和文字、粗实线的颜色各不同;
2、根据图中要求,选择合理的加工方法、合理的加工顺序、合理的加工参数加工出零件。
图2。
Mastercam二维铣削加工
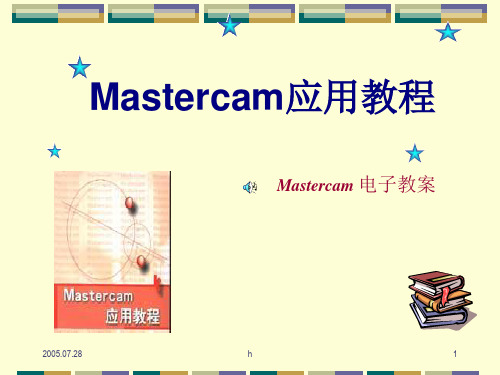
Mastercam 电子教案
2005.07.28
h
1
第8章 二维铣削加工
Mstercam二维刀具路径模组用来生成二 维刀具加工路径,包括外形铣削、挖槽、 钻孔、面铣削、全圆铣削等加工路径。 各种加工模组生成的刀具路径一般由加 工刀具、加工零件的几何模型以及各模 组的特有参数来定义。不同模组可进行 加工的几何模型和参数各不相同。本章 将分别介绍各模组的功能及使用方法。
2005.07.28
h
3
2005.07.28
“Contour”对话框
h
4
“Tools parameters”对话框中的有关刀具参数输入框 的含义与刀具设置中的相同,下面对本选项卡中的有 关按钮进行介绍。
1. Home position按钮
选中“Home position”按钮前的复选框,单击 “Home position”按钮,即可打开“Home position” 对话框。该对话框用来设置工件坐标系(G54)的原 点位置,其值为工件坐标系原点在机械坐标系中的坐 标值,可以直接在输入框中输入或单击“Select”按 钮在绘图区选取一点。
h
11
3. Ramp(螺旋式外形加工)
只有二维曲线串连时有螺旋式加工,一般是
用来加工铣削深度较大的外形。在进行螺旋式
外形加工时,可以选择不同的走刀方式。单击 “Ramp”按钮,打开 “Ramp contour”对 话框。系统共提供了3种走刀方式,当选中 Angle或Depth单选钮时,都为斜线走刀方式; 而选中Plunge单选钮时,刀具先进到设置的铣 削层的深度,再在XY平面移动。对于Angle和 Depth选项,定义刀具路径与XY平面的夹角方 式各不相同,Angle选项直接采用设置的角度, 而Depth选项是设置每一层铣削的Ramp depth (总进刀深度)。
mastercam实例教程二维加工
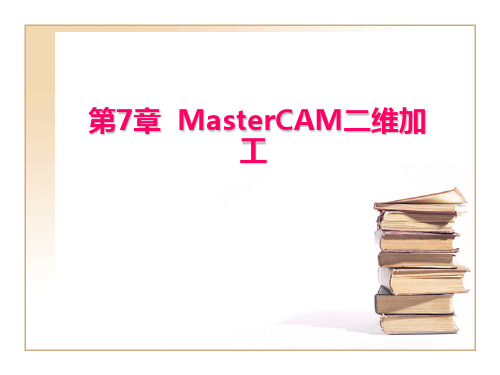
• (5)使用路径模拟和实体切削模 拟功能,对生成的刀具路径进行验 证检查。
• (6)执行刀具路径的后置处理, 生成数控加工NC程序。
• 5.1.2
刀具管理
• 1.刀具管理器 • • / / / 命令,显示Tools Manager(刀具管理器)对话框。 选择
图5.2
刀具管理器对话框
• 2.定义刀具类型 • 选择主菜单 / / / 命令,系统进入 Tools Manager(刀具管理器) 对话框。
• 4.进/退刀向量(Lead in /out) • 为了使刀具平稳地进入和退出工件, 一般要求在所有的2D和3D外形铣削路径 的起点或终点位置。
•
产生一段与工件加工外形相接的进 刀路径或退刀路径,从而防止过切或产 生毛边。
图5.29
进/退刀向量对话框
• (1)直线进/退刀(Line) • 系统提供了两种进/退刀引线方向。
•
而实际粗切量往往要小于最大粗切 量的设定值,系统会按以下方法重新调 整粗切量。
• ①按公式:(总切削量–精修量×次 数–Z向预留量)/ 最大粗切量求值并 取整,即为实际粗切次数。
• ②实际粗切量=(总切削量–精修量× 次数–Z向预留量)/ 实际粗切次数。
• (2)分层铣深次序(Depth cut order) • 按外形(By contour),表示分层铣 深时。先沿一个外形边界铣削至设定的深 度,之后进行下一个外形边界的 铣削。
•
在列表框中单击鼠标右键弹出快 捷菜单。
图5.3
右键菜单
图5.4
定义刀具对话框
• 2.定义刀具的尺寸参数
图5.5
Tool选项卡的参数设置
• 3.定义刀具的切削参数
图5.6
基于Master CAM的二维零件数控加工

基于Master CAM的二维零件数控加工
高占华;曹巨江;张利平;闫茹
【期刊名称】《模具技术》
【年(卷),期】2007(000)003
【摘要】通过一个典型零件分析了Master CAM的零件造型、设计方法和编辑技巧,讨论了二维轮廓刀具路径的生成方法,得出了Master CAM作为一款高端CAD/CAM软件,在实际加工中有着广泛的应用.
【总页数】4页(P49-51,58)
【作者】高占华;曹巨江;张利平;闫茹
【作者单位】陕西科技大学,机电工程学院,陕西,西安,710021;陕西科技大学,机电工程学院,陕西,西安,710021;陕西科技大学,机电工程学院,陕西,西安,710021;陕西科技大学,机电工程学院,陕西,西安,710021
【正文语种】中文
【中图分类】TP391.73
【相关文献】
1.基于MasterCAM的双面加工零件的数控加工技巧 [J], 周栋华
2.基于Mastercam十字架凸模零件数控加工 [J], 谢远辉;肖敏;钟睿
3.一种基于MasterCAM X5和数控加工中心的零件表面雕刻技术 [J], 徐文俊;郑丽文;申文权;林钰珍;巫少龙
4.基于MasterCAM的纺织机械模具型腔零件的数控加工 [J], 钟明灯;许艳华
5.基于MasterCAM的金属零件的数控加工 [J], 崔立辉
因版权原因,仅展示原文概要,查看原文内容请购买。
二维加工

Mastercam X3实训课件
两段路径一起观察
只观察一段路径
Mastercam X3实训课件
4 钻孔加工
4.1 孔的基本加工方法 Mastercam提供了丰富的钻孔方式,而 且可以自动输出对应的钻孔固定循环加指令, 如钻孔、铰孔、镗孔和攻丝等加工方式。 Mastercam提供了七种孔加工的各种标准固 定循环方式,而且允许用户自定义符合自身 要求的循环方式。
Mastercam X3实训课件
在挖槽加工参数中还有一个粗/精铣选项卡
粗切 走刀方式 刀间距百分比 (对刀具直径) 刀间距长度 粗切角度 精切 精铣次数/量/精修次数 精铣外边界 从粗铣结束位置开 始精铣 刀具路径最佳 化 由内而外环切
螺旋式下刀 高速加工
补偿方式 精铣进给率 精铣主轴转数 进退刀量 薄壁精铣
Mastercam X3实训课件
1.2 外形铣削实例 1. 创建基本图形
以原点为矩形中心
Mastercam X3实训课件
2. 选择机床 首先需要挑选一台实现加工的机床,直接 选择 Machine Type |Mill |Default即可,即 选择系统默认的铣床来进行加工。 本例图素最大尺寸为 100×80 的一个矩形, 因此考虑将采用 104×84 的矩形毛坯,每边 留出 2mm余量,并且设计毛坯厚度为 20mm, 材料选择为铝材。
3. 选择刀具和设置加工参数 制定一把直径为3的钻头作为本次加工 的刀具
选择的刀具
Mastercam X2 基础教程
三段路径一起仿真
独立路径仿真
2 挖槽加工
2.1 槽的基本加工方法 零件上的槽和岛屿,都是通过将工件上制定区域内的材 料挖去而成。一般使用端铣刀(EndMill)进行加工。 挖槽刀具路径生成的一本步骤和外形铣削基本相同,主 要参数有刀具参数、挖槽加工参数和粗精铣参数。 在铣槽时可按刀具的进给方向,分为顺铣和逆铣两种方 式。顺铣有利于获得较好的加工性能和表面加工质量。 有时在槽内往往还包含一个称之为“岛屿”区域,可以 在分层铣削加工过程中,特别补充一段路径加工岛屿顶面。 在挖槽加工时,可以附加一个精加工操作,可以一次 完成两个刀具路径规划。
项目三 MasterCAM软件的二维加工的刀路定义及自动编程

点选“操作管理”菜单,在操作管理器对话框中选择所定义的外形铣削刀路,再点“实体验证”即可进行实体播放模式的模拟加工。点播放控制条的第三个按钮“ ? ”即可开始刀路模拟。
3)后处理
根据上述轮廓铣削的刀路,按照FANUC-0i系统的后处理文件MPFAN.PST中的设置,产生程序。在操作管理器中点“后处理”,弹出对话框后确认后处理文件后,点选“储存NC档”、“编辑”选项为有效,确定后即可生成并显示出NC程序。检查程序指令是否是按进行刀路定义时所设定的NC参数生成的,如有异常返回到操作管理器进行编辑。
1)定义刀具路径
点选“工作设定”以进行毛坯、工件原点定义,设置毛坯X=100,Y=100,Z=40;选择工件原点X=0,Y=0,Z=0,确定即可。
点选“刀具路径”→ “外形铣削”菜单,从底边中部开始逆时针串连,点“执行”后,在弹出对话框的空白区点鼠标右键,选择Ø12的平底立铣刀具,默认刀具及刀补号,设定进给率200,Z向进给率90,提刀速率400;程序号1234,主轴转速1200,冷却液为喷油,其余默认。
刀补位置:有刀尖和刀具中心两种选择。主要用于刀具长度Z方向的补偿设定,它仅影响球刀和牛鼻刀等成型刀的编程。
刀具转角设定:指在轮廓类铣削加工程序生成时,是否需要在图形尖角处自动加上一段过渡圆弧。对于刀补功能不完善的数控系统,当图形尖角较小时,其刀补结果可能会导致补偿轨迹超程,此时可以借助此刀具转角设定功能,设定为小于135°或所有尖角自动添加圆角,便可避免加工时出错的可能。本项设定的效果如图3所示。
(5)程序名称:即主程序番号。在NC程序中产生O xxxx的指令。若在某些方式的加工参数设定项中设定了使用子程序(副程式)的功能,则子程序番号将由系统自动产生。
(6)起始程序行号和行号增量:指生成NC程序中行首的N代码的起始号和行号增量。
第3章 二维铣削加工
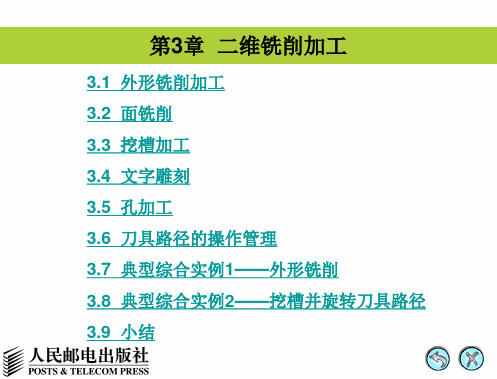
3.3 挖槽加工
• 在挖槽模组参数设置中,加工通用参数与外形加 工设置方法相同,其特有的【2D挖槽参数】和 【粗切/精修的参数】的设置如下:
• 一、挖槽类型 系统提供如下5种方式:标准挖槽、面加工、使用岛 屿深度、残料加工、开放。 • 二、加工方向 系统提供了顺铣、逆铣2种加工方向。 • 三、深度分层 • 四、粗加工参数 主要有:(1)走刀方式;(2)粗加工参数; (3)下刀方式。
第3章 二维铣削加工
3.1 外形铣削加工
3.2 面铣削
3.3 挖槽加工 3.4 文字雕刻 3.5 孔加工 3.6 刀具路径的操作管理 3.7 典型综合实例1——外形铣削 3.8 典型综合实例2——挖槽并旋转刀具路径 3.9 小结
引言
• 与其他软件相比,Mastercam X最具特色的 就是它的二维铣削加工。 • Mastercam系统的加工(CAM)部分主要由 铣削、车削和雕刻(激光线切割)等3大模块组成。 其中铣削模块是Mastercam X的主要功能,可以 进行外形铣削、型腔加工、钻孔加工、平面加工、 曲面加工以及多轴加工等的模拟及代码生成。 • Mastercam X提供了多种铣床类型,一般情 况下使用默认的铣床类型。
图3-25 加工模拟结果
• 本实例的操作步骤如下:
• 1.创建几何模型,进入加工环境。 • 2.设置工件毛坯。 • 3.设定刀具。 • 4.设置外形铣削参数。 • 5.生成刀具路径,模拟加工。 • 6.保存文件。
3.2 面铣削
• 在设置面铣削参数时,除了要设置一组刀具、材 料等共同参数外,还要设置一组其特有的加工参 数。 这些参数主要有如下2种:
3.1.2 加工起点及方向的设置
• 在对外形进行串联选择时,需要注意以下几点。
9___MasterCAM_X5_二维加工与线架加工
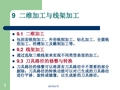
2.外形加工参数 设置 (1)外形铣削类 型 (2)补正型式 (3)补正方向 (4)最佳化 (5)寻找相交性
2016/9/15
(6)曲线打断成线段的 误差值 (7)3D曲线的最大深 度变化量 (8)XY方向预留量 (9)Z方向预留量
14
9.1.2 外形铣削加工
(1)外形铣削类型 当选择二维曲线串连时,可以选 择的类型有“2D”、“2D倒角”、“斜插下刀”和 “残料加工”4种类型;当选择三维曲线串连时,可 以选择的类型有“2D”、“3D”和“3D倒角”3种类 型。
2016/9/15
27
9.1.3 钻孔加工
2.点的选择(续)
(8)点的排序选项 单击“排序”按钮,设置点的排列方式。
28
2016/9/15
9.1.3 钻孔加工
“Drill/Cou nterbore” 对话框
29
2016/9/15
9.1.3 钻孔加工
3.钻孔参数设置
(1)选择钻孔循环方式 系统提供了8种预定义钻孔 循环方式。 1)选择“Drill/Counterbore”用于钻孔深度小于钻 头直径3倍的一般钻孔或点窝加工。 2)选择“深孔啄钻-完整回缩”用于钻孔深度大于钻 头直径3倍且不易排屑的深孔加工。 3)选择“深孔啄钻-增量回缩”用于韧性材料的断屑 式钻孔 。 4)选择“攻牙”用于攻左旋螺纹或右旋螺纹。
(2)补正型式 有“电脑”补正,“控制器”补正、 “两者”、“两者反向”和“关”5个选项。
(3)补正方向 可以设置为左刀补,也可设置为右刀 补,与切削方式的选择相关 。
2016/9/15
15
9.1.2 外形铣削加工
- 1、下载文档前请自行甄别文档内容的完整性,平台不提供额外的编辑、内容补充、找答案等附加服务。
- 2、"仅部分预览"的文档,不可在线预览部分如存在完整性等问题,可反馈申请退款(可完整预览的文档不适用该条件!)。
- 3、如文档侵犯您的权益,请联系客服反馈,我们会尽快为您处理(人工客服工作时间:9:00-18:30)。
3.3 挖槽加工
• 在挖槽模组参数设置中,加工通用参数与外形加 工设置方法相同,其特有的【2D挖槽参数】和 【粗切/精修的参数】的设置如下:
• 一、挖槽类型 系统提供如下5种方式:标准挖槽、面加工、使用岛 屿深度、残料加工、开放。 • 二、加工方向 系统提供了顺铣、逆铣2种加工方向。 • 三、深度分层 • 四、粗加工参数 主要有:(1)走刀方式;(2)粗加工参数; (3)下刀方式。
有如下2个参数的设置:贯穿深度距离和刀尖角度。
• 二、循环方式
常用的8种标准钻孔循环方式如下: Dril/Counterbore(钻孔或镗盲孔)、深孔啄钻、断屑 式、攻牙、Bore #1(镗孔#1)、Bore #2(镗孔#2)、 Fine bore(精镗)。
• 三、其他参数
有以下特殊参数:首次啄钻、副次啄钻、安全余隙、 回缩量、停留时间、提刀偏移量。
3.1.6
后置处理
• 后处理就是将NCI刀具路径文件翻译成数控NC程 序(即加工程序)。在【后处理程式】对话框中 设置后处理过程的相关参数,有如下分组:
• 一、选择后处理器 • 二、【NC文件】分组框 • 三、【NCI文件】分组框
3.1.7
工程实例——外形铣削
• 本实例主要介绍外形铣削加工的一般过程,完成 后的效果如图3-25所示。
3.1.3
刀具参数设置
• 在【定义刀具】对话框中对刀具的如下参数进 行选择或设置。
• 一、刀具类型
系统提供丰富的刀具类型,直接单击需要的刀具 图标,就可以进行刀具尺寸参数的编辑。
• 二、编辑刀具
在实际加工中,需要根据不同的情况,对刀具外 形尺寸进行不同的设置。
• 三、切削参数
用户还可以对刀具的切削参数进行设置。
3.1 外形铣削加工
• 外形铣削加工可分为以下2种加工类型:
• 二维轮廓加工 • 三维轮廓加工
• 二维外形铣削加工的原理图如图3-2所示。
图3-2 外形铣削原理图
3.1.1 工件设置
• Mastercam X中的工件设置主要有以下内容:
• 一、工件类型选择 • 二、工件尺寸设置 • 三、工件原点设置 • 四、工件材料设置
图3-25 加工模拟结果
• 本实例的操作步骤如下:
• 1.创建几何模型,进入加工环境。 • 2.设置工件毛坯。 • 3.设定刀具。 • 4.设置外形铣削参数。 • 5.生成刀具路径,模拟加工。 • 6.保存文件。
3.2 面铣削
• 在设置面铣削参数时,除了要设置一组刀具、材 料等共同参数外,还要设置一组其特有的加工参 数。 这些参数主要有如下2种:
• 一、铣削方式 软件中的铣削方式主要有:双向、单向-顺铣、 单向-逆铣、一刀式。 • 二、刀具移动方式 软件中提供了如下3种刀具移动方式:高速回圈、 线性、快速进给。
加工实例 • 在3.1.7节加工实例的基础上,对工件上表面进行 面铣削加工,操作步骤如下:
• 1.打开3.1.7节保存的文件。 • 2 .选取面铣削加工的边界。 • 3 .选取轮廓后进行确认。 • 4 .选取铣削刀具,设置加工参数。 • 5 .完成参数设置。 • 6 .所有参数设置完后,系统计算出刀具路径。 • 7 .进行加工模拟。 • 8 .保存文件。
• 1.打开3.3节保存的文件。 • 2 .选取槽的边界。 • 3 .确认后系统打开【雕刻】对话框进行加工参数 设置。 • 4 .设置雕刻深度。 • 5 .生成刀具路径,模拟加工。 • 6 .保存文件。
3.5 孔加工
• 孔加工模组除了具有基本的高度参数设置外,还 有以下几组其特有的参数设置:
• 一、钻尖补偿
第3章 二维铣削加工
3.1 外形铣削加工
3.2 面铣削
3.3 挖槽加工 3.4 文字雕刻 3.5 孔加工 3.6 刀具路径的操作管理 3.7 典型综合实例1——外形铣削 3.8 典型综合实例2——挖槽并旋转刀具路径 3.9 小结
引言
• 与其他软件相比,Mastercam X最具特色的 就是它的二维铣削加工。 • Mastercam系统的加工(CAM)部分主要由 铣削、车削和雕刻(激光线切割)等3大模块组成。 其中铣削模块是Mastercam X的主要功能,可以 进行外形铣削、型腔加工、钻孔加工、平面加工、 曲面加工以及多轴加工等的模拟及代码生成。 • Mastercam X提供了多种铣床类型,一般情 况下使用默认的铣床类型。
3.1.2 加工起点及方向的设置
• 在对外形进行串联选择时,需要注意以下几点。
• 被串联的图形原则上都需要封闭。 • 串联起始点(绿色箭头)尽量在外轮廓交点处。 • 注意分歧点提示。 • 对于存在重复图素的图形进行串联时,可能会导致 系统无法识别封闭的图形。
• 另外,在对几何模型进行串联操作时候,必须注 意串联的起点和方向。
3.8 典型综合实例2——挖槽并旋转刀具路径
• 挖槽并利用旋转刀具路径功能加工如图3-83所示 的零件。
图3-83 最终加工结果
• 加工的操作步骤如下:
• 1.打开附盘文件“mcx\第3章\圆盘.mcx”。 • 2 .机床类型设置。 • 3.毛坯设置。 • 4.挖槽加工。 • 5.新建直径为5mm的平底刀并设置刀具参数。 • 6.新建直径为10mm的平底刀,选中直径为5mm的平 底刀并进行2D挖槽参数和粗切/精修的参数的设置。 • 7.确认后,系统自动生成挖槽刀路。 • 8 .设置旋转刀具路径参数。 • 9 .确认后,生成旋转刀具路径刀路。 • 10 .用挖槽方法加工中间圆。 • 11 .模拟加工过程,保存图形。
3.1.4
铣削参数设置
• 在【外形铣削参数】选项卡内对外形铣削的如下 参数进行设置:
• 一、外形铣削类型 • 二、高度设置 • 三、刀具补偿 • 四、余量设置
3.1.5
加工模拟
• 【实体切削验证】对话框中的控制选项以及按钮 比较多,主要可以分为以下几类:
• 一、模拟控制及刀具显示控制 • 二、显示控制 • 三、停止选项 • 四、其他功能 • 五、信息显示
3.9 小结
• 常用的二维铣削方法包括外形铣削、面铣削、 挖槽加工、钻孔加工以及雕刻加工等,请注意其 功能、参数设置和具体的操作过程。 • CAM技术注重实践,在学习过程中,一定要 将理论知识与生产环境(材料、设备以及生产条 件)结合起来,不要盲目照抄书本。特别是工艺 参数的选择,一定要在具体的生产环境下进行, 否则会理论脱离实际,请务必强化实践环节。
加工实例 • 在前面加工实例的基础上继续进行孔加工:
• 1.打开3.4节保存的文件。 • 2 .选取孔加工的位置。 • 3 .确认选取。 • 4 .进行参数设置。 • 5 .生成刀具路径,模拟加工。 • 6 .保存文件。
3.6 刀具路径的操作管理
• 可以在【操作管理器】对话框中移动某个操 作的位置来改变加工次序,也可以通过改变刀具 路径参数、刀具及与刀具路径关联的几何模型等 来改变刀具路径。 • 其中的操作按钮区域,如图3-66所示。
图3-66 操作按钮区
3.7 典型综合实例1——外形铣削
• 设计外形铣削高弯头,仿真结果如图3-67所示。
图3-67 最终加工结果
• 一、设计思路
• 毛坯设置。 • 选择加工方法并设置刀具。 • 模拟加工过程。
• 二、操作过程
• 1.打开附盘文件“\mcx\第3章\弯头.mcx”。 • 2 .机床类型设置。 • 3.毛坯设置。 • 4.外形铣削刀具路径。 • 5.用同样的方法铣削第二个线环。 • 6.设置刀具参数,按图3-79所示设置参数。 • 7.模拟加工过程,保存图形。
加工实例 • 在前面加工实例的基础上继续进行挖槽加工:
• 1.打开3.2节保存的文件。 • 2 .选择槽的边界。 • 3 .确认后系统打开【挖槽(标准挖槽)】对话框。 • 4 .设置挖槽加工参数。 • 5 .生成刀具路径,模拟加工。 • 6 .保存文件。
3.4 文字雕刻• 雕刻的数设置方法与挖槽相似。 • 在前面加工实例的基础上继续进行雕刻加工: