苯、甲苯、二甲苯混合物中甲苯的回收装置设计
化工原理苯和甲苯的分离项目设计方案

化工原理苯和甲苯的分离项目设计方案第1章绪论精馏塔是进行精馏的一种塔式汽液接触装置,又称为蒸馏塔。
有板式塔与填料塔两种主要类型。
根据操作方式又可分为连续精馏塔与间歇精馏塔。
蒸气由塔底进入,与下降液进行逆流接触,两相接触中,下降液中的易挥发(低沸点)组分不断地向蒸气中转移,蒸气中的难挥发(高沸点)组分不断地向下降液中转移,蒸气愈接近塔顶,其易挥发组分浓度愈高,而下降液愈接近塔底,其难挥发组分则愈富集,达到组分分离的目的。
由塔顶上升的蒸气进入冷凝器,冷凝的液体的一部分作为回流液返回塔顶进入精馏塔中,其余的部分则作为馏出液取出。
塔底流出的液体,其中的一部分送入再沸器,热蒸发后,蒸气返回塔中,另一部分液体作为釜残液取出。
1.1概述高径比很大的设备称为塔器。
塔设备是炼油、化工、石油化工等生产中广泛应用的气液传质设备,更是成为化工、炼油生产中最重要的设备之一。
常见的可在塔设备中完成的单元操作有:精馏、吸收、解吸和萃取等。
此外,工业气体的冷却与回收,气体的湿法净制和干燥,以及兼有气液两相传质和传热的增湿、减湿等。
而工业上对塔设备的主要要:(1)生产能力大;(2)传热、传质效率高;(3)气流的摩擦阻力小;(4)操作稳定,适应性强,操作弹性大;(5)结构简单,材料耗用量少;(6)制造安装容易,操作维修方便。
此外,还要求不易堵塞、耐腐蚀等。
根据塔气液接触部件的结构型式,可分为板式塔和填料塔。
板式塔设置一定数目的塔板,气体以鼓泡或喷射形式穿过板上液层进行质热传递,气液相组成呈阶梯变化,属逐级接触逆流操作过程。
填料塔装有一定高度的填料层,液体自塔顶沿填料表面下流,气体逆流向上(也有并流向下者)与液相接触进行质热传递,气液相组成沿塔高连续变化,属微分接触操作过程。
它们都可使气(或汽)液或液液两相之间进行紧密接触,达到相际传质及传热的目的。
而板式塔又大致可分为两类:(1)有降液管的塔板,如泡罩、浮阀、筛板、导向筛板、新型垂直筛板、蛇形、S型、多降液管塔板;(2)无降液管的塔板,如穿流式筛板(栅板)、穿流式波纹板等。
苯甲苯精馏塔设计
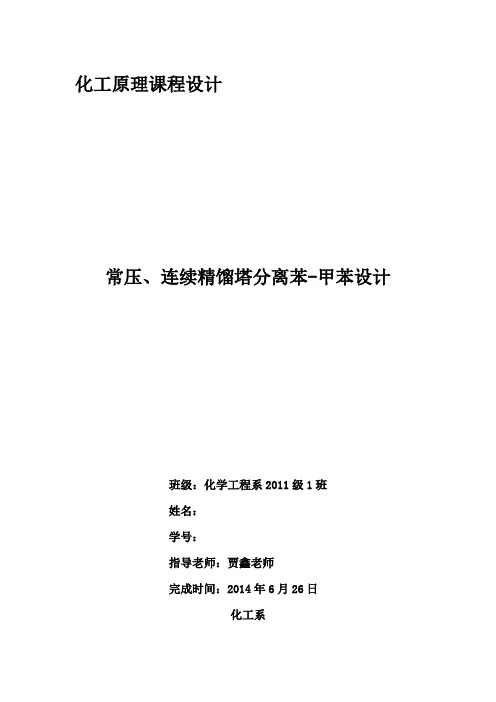
化工原理课程设计常压、连续精馏塔分离苯-甲苯设计班级:化学工程系2011级1班姓名:学号:指导老师:贾鑫老师完成时间:2014年6月26日化工系常压、连续精馏塔分离苯-甲苯设计一、前言1.1设计任务及条件:泡点进料(q=1),塔顶进入全凝器,塔釜间接蒸汽加热,塔板压降:(0.5-0.7)KPa1.2物系用途及性质(1)苯的性质:摩尔质量78.11g/mol,密度0.8786 g/mL,相对蒸气密度(空气=1):2.77,蒸汽压(26.1℃):13.33kPa,临界压力:4.92MPa,熔点278.65 K (5.51 ℃),沸点353.25 K (80.1 ℃),在水中的溶解度 0.18 g/ 100 ml 水,标准摩尔熵So(298.15K):173.26 J/mol·K,标准摩尔热容 Cpo:135.69 J/mol·K (298.15 K),闪点 -10.11℃(闭杯),自燃温度 562.22℃,结构:平面六边形,最小点火能:0.20mJ,爆炸上限(体积分数):8%,爆炸下限(体积分数):1.2%,燃烧热:3264.4kJ/mol,溶解性:微溶于水,可与乙醇、乙醚、乙酸、汽油、丙酮、四氯化碳和二硫化碳等有机溶剂互溶。
它有机化合物,是组成结构最简单的芳香烃,在常温下为一种无色、有甜味的透明液体,并具有强烈的芳香气味。
苯可燃,有毒。
苯难溶于水,易溶于有机溶剂,本身也可作为有机溶剂。
苯是一种石油化工基本原料。
苯的产量和生产的技术水平是一个国家石油化工发展水平的标志之一。
苯具有的环系叫苯环,是最简单的芳环。
(2)苯在工业上的用途:苯是工业上一种常用溶剂,主要用于金属脱脂。
苯有减轻爆震的作用而能作为汽油添加剂。
苯在工业上最重要的用途是做化工原料。
苯可以合成一系列苯的衍生物:苯与乙烯生成乙苯,后者可以用来生产制塑料的苯乙烯与丙烯生成乙丙烯,后者可以经乙丙苯法莱生产丙酮与制树脂和粘合剂的苯酚,制尼龙的环己烷,合成顺丁烯二酸酐,用于制作苯胺的硝基苯,用于农药的各种氯苯,合成用于生产洗涤剂和添加剂的各种烷基苯,合成氢醌、蒽醌等化工产品。
化工原理设计-苯-甲苯二元混合液连续精馏装置的设计 精品

化工原理课程设计任务书一、设计课题:苯-甲苯二元混合液连续精馏装置的设计 二、设计条件与工艺要求 1、生产能力(以进料量计): 74000 吨/年2、原料液组成:x AF = 0.44 (注:浓度均指易挥发组分的摩尔分率)3、产品要求:=AD x 0.98 , =AW x 0.024、工艺条件(1)操作压力:塔顶压力(表压)约4kPa 。
(2)原料温度:原料液温度20℃,经过与塔釜液体产品间接换热或者进一步预热,温度提升至入塔时所指定的温度65℃。
(3)进料方式:在最适宜的进料板上连续进料。
(4)回流热状态:泡点回流。
(5)塔板压降:≤0.7kPa 。
(6)塔釜间接蒸汽加热,所用的加热蒸汽压力为200kP a (绝对压)。
仅利用其冷凝热。
(7)塔顶设全凝器,利用冷却水间接换热,冷却水的进、出口温度分别规定为t in =25℃,t out =43℃ 。
(8)年工作日:300天。
三、设计内容1、苯-甲苯二元混合液连续精馏工艺流程的设计绘制出所设计的连续精馏工艺流程图,同时对生产过程原理进行文字叙述。
2、筛板精馏塔的设计计算内容 (1)全塔物料衡算,计算产品D 、W 的量。
(2)确定R min 和R 。
(3)图解法确定理论塔板数N T 及最适宜的进料位置,确定精馏段的理论塔板数N T,1 。
(4)合理确定筛板塔板的总效率E 0 ,确定实际塔板数和实际进料位置。
(5)分别确定精馏段的汽相体积流量、汽体流速和塔径,提馏段的汽相体积流量、汽体流速和塔径。
(6)进行精馏段的塔板结构设计、提馏段的塔板结构设计:包括选择溢流形式(多选单溢流)、设计堰长、降液区面积,确定开孔区面积,设计堰高,设计降液管底隙高度,确定筛孔孔径,选择筛孔布置方式并计算具体布置尺寸。
(7)分别进行精馏段塔板的流体力学验算、提馏段塔板的流体力学验算。
(8)绘出精馏段塔板的负荷性能图,计算操作弹性,绘出提馏段塔板的负荷性能图,计算操作弹性。
超强粗苯回收工艺设计

设计说明本设计涵盖了焦炉煤气中吸收苯族烃,并采用富油脱苯。
苯族烃的吸收过程为典型的多组分吸收,为了叙述与设计计算方便,可近似看作单组分吸收,同时洗油吸收煤气中的苯族烃又是物理吸收过程,服从拉乌尔定律和道尔顿定律。
包括物料衡算,热量衡算,填料塔尺寸的计算、填料的选取及辅助设备的计算和选取。
其中,塔高为34米,塔径为4.8米,填料层高度为26米。
对洗苯塔进行了工艺计算,而对苯族烃的吸收因素以及洗油的选取与质量要求,作了简单阐述。
对脱苯工段设计为生产一种苯的工艺流程,即得到粗苯产品。
在循环利用方面,设置有富油再生装置。
并介绍了采用管式炉加热富油脱苯的工艺方法,对管式炉加热过程进行了物料及热量衡算,并简单求取其加热面积,从而确定的管式炉的型号。
最后,根据工艺参数、计算的主设备及辅助设备的参数,绘制了焦炉煤气洗苯塔的物料流程图、带控制点的物料流程图和主设备图。
关键词:管式炉;富油脱苯;洗苯塔Design specificationThis designing introduces a tubular heating furnace oil-rich off the process of benzene method, the tube furnace heating process the material and heat balance, and simple to obtain the heating area to determine the tube furnace model., including material calculation ,heat calculation ,packed tower calculation ,packing size of auxiliary equipment selection and calculation .Among them ,the tower is 34 high meters,4.8 diameter meters .The design covers the family of benzene absorption in coke oven gas hydrocarbons, using benzene-rich oil off. Finally hydorcaription benzene absorption typical multi-component absorption, in order to facilitate the description and design calculations, can be approximated as single component absorption, and wash oil absorption of hydrocarbon gas in the benzene family is the physical absorption process, subject to Raoul Law and Dalton’s law. Carried out researches on the washing process calculation benzene tower, the absorption of hydrocarbons benzene family factors,the selection and quantity of wash oil requirements. Workshop Section on benzene removal is designed process of produce; the products are benzene in recycling, and the settings of rich oil regeneration device. Finally, according to the process parameters, calculate the main equipment and auxiliary equipment parameters, equipment chart including Wash benzene tower coke oven gas flow chart, and the material with the material control flow chart and main device figure.Keywords: tube type stove; the rich oil takes off benzene; ash benzene tower.目录设计说明 (I)主要符号说明 (III)1 总论 (1)1.1引言 (1)1.2文献综述 (2)1.2.1粗苯的物理性质 (2)1.2.2洗油吸收苯族烃的基本原理 (2)1.2.3富油脱苯原理 (2)1.3设计任务的依据 (3)2 生产方案说明 (5)2.1用洗油吸收煤气中的苯族烃 (5)2.2富油脱苯 (5)2.3设备的选型 (5)2.3处理能力 (6)3 生产流程说明 (7)3.1总流程概述 (7)3.2吸收苯族烃工艺流程 (7)3.3、富油脱苯工艺流程 (7)4 洗油吸收粗苯填料塔设计 (9)4.1任务及操作条件 (9)4.2、吸收工艺流程的确定 (9)4.3物料计算 (9)4.3.1 进塔混合气中各组分的量 (9)4.3.2 混合气进出塔的体积组成 (10)4.3.3 混合气进出塔比摩尔组成 (10)4.3.4 出塔混合气量 (10)4.4汽液平衡曲线 (11)4.4.1 吸收剂(洗油)的用量 (12)4.4.2 操作线方程 (12)4.5塔径计算 (13)4.6填料层高度计算 (15)4.7填料层压降计算 (19)4.8填料吸收塔的附属设备 (19)4.8.1液体分布器 (19)4.8.2 液体再分布器 (20)4.8.3 填料支撑板 (20)4.8.4 填料压板及床层限制板 (21)4.8.5 气体入塔分布和排液装置 (21)4.8.6 人孔的设计: (21)4.8.7 气体接管尺寸计算 (22)4.8.8 液体接管尺寸计算 (22)4.9设备强度校核计算 (23)4.9.1 壁厚设计及校核 (23)4.9.2 封头设计 (24)4.9.3 圆筒的应力 (25)4.9.4 塔高的计算: (25)5 管式炉加热富油脱苯工段 (27)5.1生产流程选择 (27)5.2脱苯工段的设备计算 (27)5.3管式炉 (28)5.3.1 管式炉物料衡算 (28)5.3.2 加热面积的确定 (33)5.4洗油再生器 (35)设计结果 (38)参考文献 (40)附录 (41)附图1:粗苯回收填料塔设备图 (41)附图2:粗苯回收物料流程图 (41)附录3:带控制点的粗苯回收工艺流程图 (41)致谢 (42)主要符号说明英文字母:名称单位a t填料层有效传质比表面积m2/m3a w填料层的润湿比表面积m2/m³c 粗苯(蒸汽)比热容J/(g·K)C 厚度附加量mmC L洗油平均比热容kJ/kmol·℃C1负偏差mmC2腐蚀裕量mmd 鲍尔环外径mmd0盘上开孔孔径mmD 塔径mD G、D L溶质在液相和气相中的扩散系数m2∕sD i筒体内径mmE 亨利常数atmF 加热面积m2F1辐射段炉管加热面积m2F2、F3对流段蒸汽、富油部分加热面积m2g 重力加速度m/s2G 蒸馏用直接蒸汽消耗量kg/hG CB粗苯产量kg/hG F富油量kg/hG Fi富油中各组分量kg/hG m洗油量kg/hG N富油中奈含量kg/hG P贫油量kg/hG S进入再生器内水蒸气量kg/hH 塔高mH d粗苯微分溶解热kJ/kmolH OG传质单元高度mN OG传质单元数L 吸收剂用量kmol/hL' 吸收液质量流速kg/(m2·h)L喷液体喷淋密度M i各物质相对分子质量kg/kmolP i0 各组分饱和蒸汽压kPaq1、q2、q3洗油、粗苯、水带入或带出热量kJ/hQ 单位时间内炉管吸收热量kJ/hQ m管式炉供给富油热量kJ/hQ v管式炉供给蒸气的热量kJ/hQ i各分段带入带出热量kJ/hu 空塔气速m/su F液泛速度m/sV g煤气耗量m3/hV 混合气流量kmol/sx 溶质组分在液相中的摩尔分率X 气相摩尔比S脱吸因数Z′ 填料层高度m希腊字母:μ液相粘度Pa·mLΦ填料因子ψ形状系数ϕi各组分留在液相中的分率或质量含量1 总论1.1 引言粗苯和煤焦油是炼焦化学产品回收中最重要的两类产品。
苯、甲苯、二甲苯分离过程工艺设计说明书
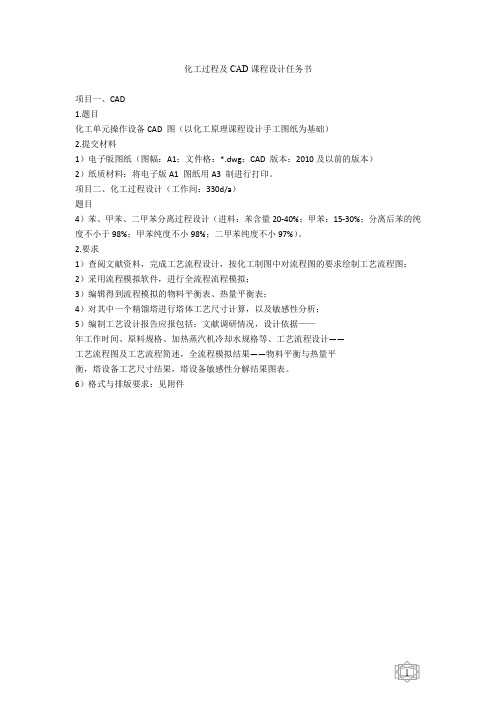
化工过程及CAD课程设计任务书项目一、CAD1.题目化工单元操作设备CAD 图(以化工原理课程设计手工图纸为基础)2.提交材料1)电子版图纸(图幅:A1;文件格:*.dwg;CAD 版本:2010及以前的版本)2)纸质材料:将电子版A1 图纸用A3 制进行打印。
项目二、化工过程设计(工作间:330d/a)题目4)苯、甲苯、二甲苯分离过程设计(进料:苯含量20‐40%;甲苯:15‐30%;分离后苯的纯度不小于98%;甲苯纯度不小98%;二甲苯纯度不小97%)。
2.要求1)查阅文献资料,完成工艺流程设计,按化工制图中对流程图的要求绘制工艺流程图;2)采用流程模拟软件,进行全流程流程模拟;3)编辑得到流程模拟的物料平衡表、热量平衡表;4)对其中一个精馏塔进行塔体工艺尺寸计算,以及敏感性分析;5)编制工艺设计报告应报包括:文献调研情况,设计依据——年工作时间、原料规格、加热蒸汽机冷却水规格等、工艺流程设计——工艺流程图及工艺流程简述,全流程模拟结果——物料平衡与热量平衡,塔设备工艺尺寸结果,塔设备敏感性分解结果图表。
6)格式与排版要求:见附件年处理量18.86万吨三苯分离项目工艺设计说明书第一章总论1.1 项目概况本项目为在任务书的要求下设计一个简单的三苯分离工艺。
由于苯、甲苯、二甲苯之间沸点温差相差明显,存在较大温差,故可用传统精馏操作即可分离,无需太过复杂的工艺要求。
对于三元混合物的分离,应采用连续精馏流程。
连续精馏具有生产能力大,产品质量稳定等优点。
采用全凝器为主,以使于准确的控制回流比。
利用液体混合物中各组分挥发度的不同并借助于多次部分汽化和部分冷凝达到轻重组分的分离。
1.2 设计依据化工过程及CAD课程设计任务书;1.3 生产工艺及全厂总流程1.3.1 生产工艺蒸馏是利用液体混合物中各组分挥发的不同并借助于多次不分汽化和部分冷凝达到轻,重组分分流的方法。
蒸馏操作在化工,石油化工,轻工等工业生产中占有重要的地位。
37800ta苯—甲苯精馏装置设计

37800t/a苯—甲苯精馏装置设计一、前言1.1设计内容本设计的题目是苯-甲苯连续精馏的设计,即需设计一个精馏塔用来分离苯和甲苯,采用连续操作方式,设计一筛板塔,具体工艺参数如下:料液处理量: 37800t/a原料液组成: 0.6(质量分率)塔顶馏出液组成: 0.98(质量分率)塔底馏出液组成: 0.02(质量分率)操作压力:塔顶压强为4kPa(表压)进料状况:泡点回流比: R=1.8Rmin生产时间:每年330天,每天24小时连续工作单板压降:kpa7.01.2课程设计的工艺流程:苯和甲苯的原料混合物经卧式列管式预热器至泡点后送入筛板塔中。
气相混合物在精馏塔中上升,而液相混合物在精馏塔中下降。
气相混合物上升到塔顶上方的冷凝器中,这些气相混合物被降温到泡点,气态部分重新回到精馏塔中,这个过程就叫做回流。
液相混合物就从塔底一部分进入到塔底产品冷却器中,一部分进入再沸器,在再沸器中被加热到泡点温度重新回到精馏塔。
最终,完成苯与甲苯的分离。
精馏设备所用的设备及其相互联系,总称为精馏装置,其核心为精馏塔。
常用的精馏塔有板式塔和填料塔两类,通称塔设备,和其他传质过程一样,精馏塔对塔设备的要求大致如下:①产能力大:即单位塔截面大的气液相流率,不会产生液泛等不正常流动。
②效率高:气液两相在塔内保持充分的密切接触,具有较高的塔板效率或传质效率。
③流体阻力小:流体通过塔设备时阻力降小,可以节省动力费用,在减压操作是时,易于达到所要求的真空度。
④有一定的操作弹性:当气液相流率有一定波动时,两相均能维持正常的流动,而且不会使效率发生较大的变化。
⑤结构简单,造价低,安装检修方便。
⑥能满足某些工艺的特性:腐蚀性,热敏性,起泡性等。
二、设计方案的确定本设计任务为分离苯—甲苯混合物。
对于二元混合物的分离,应采用连续精馏流程。
设计中采用泡点进料,将原料液通过预热器加热至泡点后送入精馏塔内。
塔顶上升蒸汽采用全凝器冷凝,冷凝液在泡点下一部分回流至塔内,其余部分经冷却器冷却后送至储罐。
- 1、下载文档前请自行甄别文档内容的完整性,平台不提供额外的编辑、内容补充、找答案等附加服务。
- 2、"仅部分预览"的文档,不可在线预览部分如存在完整性等问题,可反馈申请退款(可完整预览的文档不适用该条件!)。
- 3、如文档侵犯您的权益,请联系客服反馈,我们会尽快为您处理(人工客服工作时间:9:00-18:30)。
苯、甲苯、二甲苯混合物中甲苯的回收装置设计 摘要:目前国内采用传统颗粒活性炭装置,吸附能力低,资源浪费严重,本文采用了性能优越的吸附材料和先进的工艺设计,使甲苯的回收率达到95%以上,而且甲苯的品质好,可以直接作为原料使用,实现了清洁生产和废弃资源化,收到了很好的环境效益和经济效益。为此本文设计了一个吸附柱,柱高为4.5m,底面直径为0.6m,选用活性炭作为吸附剂。该吸附柱可用于甲苯的回收,处理能力为10000cm3/h。 关键词:吸附柱; 活性炭 ;甲苯回收;废物资源化
Benzene, toluene, xylene, toluene mixture design recovery
Yang Wei Wei (Mechanical and Electrical Engineering machine from 10-3 classes 0310967) Abstract: At present, the traditional granular activated carbon unit, the adsorption capacity is low, serious waste of resources, this article uses the superior performance of adsorption materials and advanced process design, toluene recovery rate of 95%, and toluene of good quality, can be directly as a raw material used to achieve cleaner production and waste recycling, received a very good environmental and economic benefits. This paper designs an adsorption column, column height of 4.5m, bottom diameter of 0.6m, use activated carbon as adsorbent. The toluene adsorption column can be used for the recovery, processing capacity of 10000cm3 / h. Keywords: adsorption column; activated carbon; toluene recovery; waste recycling
0. 前言 芳烃是石油化工工业的重要基础原料,在总数约为800万种的已知有机化合物中,芳烃化合物占了约30%,其中BTX芳烃(苯、甲苯、二甲苯)被称为一级基本有机原料。BTX芳烃主要来自石油馏分催化重整生成油和裂解汽油,少部分来自煤焦油。近年来通过轻质烃类芳构化及重芳烃轻质化来生产BTX芳烃的技术得到了较快的发展。由于科学技术的飞速进步以及人们对生活和文化的需求日益提高,促进了以芳烃为基础原料的化学纤维、塑料、橡胶等合成材料以及品种繁多的有机溶剂、农药、医药、染料、香料、涂料、化妆品、添加剂、有机合成中间体等生产的迅猛发展。苯最大的用途是生产苯乙烯、环己烷和苯酚。其次是硝基苯、顺酐、氯苯、直链烷基苯等;甲苯大部分用作汽油组分,它的化工利用主要是生产硝基甲苯(TNT)、苯甲酸、异氰酸酯等;二甲苯中用量最大的是对二甲苯,是生产聚酯纤维和薄膜的主要原料,邻二甲苯是制造增塑剂、醇酸树脂、不饱和聚酯树脂的原料。 二战期间甲苯被大量用于制作TNT,作为炸药原料;战后甲苯用于制作TNT的比例减小,而大部分用作汽油的掺和组分和溶剂,用作化工原料的比例较小,C9芳烃则大都用作汽油的掺和组分,作为燃料烧掉了。为了充分利用甲苯和C9芳烃资源,解决苯和二甲苯的需求,人们将直接用途较少相对过剩的甲苯和C9芳烃通过甲苯歧化或甲苯与C9芳烃烷基转移反应生成用途广泛、供不应求的苯和二甲苯,满足市场需求。 传统的甲苯回收装置存在很多缺点和回收装置设计上的问题,使得甲苯的回收成本较高,回收率较低,品质差,大都不能直接作为配胶原料继续使用。在甲苯歧化与烷基转移反应生产苯和二甲苯的过程中,未转化的甲苯需要从产品中回收后,从新作为原料循环使用,以提高甲苯的最终转化率。本文设计了一固定床吸附住可用于上述过程中,甲苯的回收和再利用。
1. 吸附剂的选择 由于活性碳是比较非极性的物质,对有机质具有很强的亲和性;即使在有水分的存在,吸附性能下降的也不大;而且比较廉价等原因,它在有机溶剂类的吸附中用的很多。特别是回收溶剂中常用的成型颗粒活性炭,它是以煤、石油、木材、椰子壳等为原料,经过炭化、粉碎、成型、烧成(炭化)及水蒸气活化,制成的粒度为2-5mm的产物。此外,也使用将原料炭化、破碎、筛分以后,用水蒸汽活化过的、粒度为1mm以下的破碎状活性炭。纤维状活性炭是将再生纤维素、聚丙烯酯、酚醛树脂及沥青系纤维等,经过炭化、活化处理制成的。 活性炭的吸附性能由孔隙大小与比表面积决定。可以认为,孔隙的大小决定对吸附质的选择性,而比表面积的大小决定吸附容量。活性炭的特点是比表面积及比孔容积大,单位重量的吸附量也大。 根据活性炭吸附剂的上述特点及本设计中拟采用固定床吸附柱,因此本设计中,拟采用以石油沥青为原料,制造的耐磨性能好的直径0.5-1mm的球形活性炭作为吸附剂。使用这种活性炭,回收装置的吸附、脱附操作能够连续进行。
2. 吸附时间的确定 在间歇操作装置,吸附器吸附床层和再生设备需要配套使用,整套装置一般需要有两个吸附柱,一个在使用,一个再生,外加一个加热器和冷却器,冷凝器等附属设备。这套设备要能经济地连续操作使用,必须使 吸附操作时间≥加热时间+冷却时间 吸附时间τs:
wBwsMCuAVG00
式中Vw-吸附器的工作容器 G0-不计吸附质的吸附剂用量 加热时间τh
''0hpfMhpfMwhpshtCthCGMtGC
式中 G-吸附剂重量加吸附相当量和贮器当量之和; Cpc-吸附剂的比热; Cps-吸附相的比热; Cpw-贮器的比热; Δt-再生时,床层温度升高的差值; Gc-贮器的重量; τh-加热时间 Δth’-加热时,再生气入口和出口之间的平均温度差。 冷却时间τc
0'0pccwscMpfcw
GCtCMGCtV Δtc-冷却后,床层的温度降; Δth‘-冷却时,再生气体进口和出口的平均温度差。 虽然可以通过必要的理论计算获得吸附时间、加热时间、冷却时间以确定为满足连续操作所需的条件,但工作量较大,在本设计中实际意义并不大。根据经验,一般吸附剂的活化过程(包括加热脱附、冷却)的时间一般不会超过12小时,以及工厂中实际安排工作的需要,本设计中假定单个吸附柱的吸附操作时间为12小时,即每12小时切换一次为一周期。
3.饱和吸附床层高度的计算 3.1有效吸附容量 根据文献(1)中的数据可知,活性炭的物性参数如下,其吸附容量为0.153Kg甲苯/Kg活性炭,同时假定循环使用中吸附剂不发生劣化,残余量为0。
表1活性炭物性参数 规格 比表面积 a1/m2/g 孔隙率 ξ 空隙率 Є 几何因子 m 大孔率 βa 堆积密度 ρb
φ2.39 979 0.41 0.33 2.03 0.5 640
3.2甲苯总量W1
1100.867120.9WKg=93.6 3.3饱和吸附床层高度L0 吸附剂用量
93.6611.80.153WGq甲苯
床层容积 2611.80.96640bGVm
如空塔线速为0.1cm/s,吸附塔的截面积 21
100000.280.103600VAmu
塔的直径 40.60tADm
饱和吸附床层高度
00.963.430.28VLmA
4.吸附传质区的长度和吸附柱高度的确定 从吸附等温线计算吸附传质区的长度[2] 0.9*0.111.17aF
udCLmKaCC
吸附柱高度 01.173.434.0222aLLLm
安全计取4.5m。 4.结论与新装置的高性能分析 理论计算表明,欲回收处理量为10000cm3/h的甲苯,吸收塔的高度约为4.50m,塔的底面直径为0.6m。 吸附材料的优劣,直接关系到回收率的高低,回收品质和运行成本。工业上对吸附材料的要求是,必须有大的比表面积,高的空隙率,均匀的孔径,而且要求脱附后污染物的残留量尽可能的少。 颗粒活性炭比表面积一般为700-1000 m2/g,其直径多为几毫米甚至十几毫米,微孔孔道长,而且孔径大小不一,除小孔外,还有0.01-0.1um的中孔和0.5-5um的大孔。 活性炭纤维比表面积达1000-2500 m2/g.由于其中微孔都开在纤维细丝的表面,因孔道极端,与颗粒活性炭都相差2个数量级。同时,孔径均一,绝大多数为特别适合气体吸附的小孔,因而具有更大的有效比表面积。由于活性炭纤维孔道极短,使得活性炭纤维吸附容量大,吸附和脱附速度高,它的吸附容量是普通活性炭的1-40倍,吸附速率是颗粒活性炭的10-100倍。许多工程实践也都证明,活性炭纤维的吸附率可达92%-98%,而且使用寿命长大大延长了吸附剂的更换周期,从而使设备的年均投资也大为降低。 参考文献 1胡怀修等.五氟脲嘧啶生产过程中甲醇、甲苯的回收研究.环境科学与技术1995/02 .
2 《化学工程手册》编辑委员会.化学工程手册第17卷,化学工业出版社,1985. 3李国文,刘强,樊青娟等.活性炭吸附甲苯动力学研究.化学工程,2000,28(1):25-28. 4. 李守信等.回收涂布生产废气中甲苯的新型装置.中国环保产业.2006/07.
5李法耿等.氯化苄合成副产酸中甲苯的回收.氯碱工业.2008/03. 6王俐等.苯酐生产技术进展.【期刊】精细石油化工进展.中国石化集团北京化工研究院 北京.2002-02-15.
7 C·P·阿莱斯; M·博伦斯; E·梵登海德. 制备烷二醇及碳酸二烷基酯的方法. 国际壳牌研究有限公司. 2011-04-13. 8 D·L·拉里格; R·D·怀特利; M·J·拉巴达; J·M·奥基亚利尼; K·A·利弗; M·S·延科沃伊. 集装箱化的气体分离系统 气体产品与化学公司. 2008-11-19. 9 杰弗里·T·米勒; 陈波; 克雷格·W·柯林; 乔治·A·小胡夫; 马文·L·卡德维尔. 使用选择性渗透分离的对二甲
苯方法. BP北美公司. 2006-12-27. 10【科技成果】西安交通大学. 废旧塑料混合物的回收再利用技术. 11 李成; 李俊明; 刘喜龙等. 一种易挥发烃类油气混合物回收方法探讨 热能动力工程与热科学国家重点实验室清华大学热能工程系; 中国石油辽阳石化公司. 2010-09-12. 12 徐效梅等. 油气混合物回收方法及装置. 上海神明控制工程有限公司. 2011-05-18.