液压缸主要尺寸的确定 (2)
液压缸的设计计算
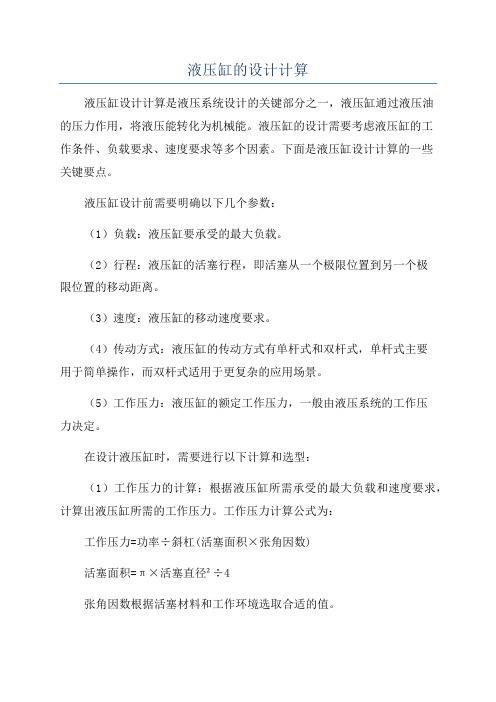
液压缸的设计计算液压缸设计计算是液压系统设计的关键部分之一,液压缸通过液压油的压力作用,将液压能转化为机械能。
液压缸的设计需要考虑液压缸的工作条件、负载要求、速度要求等多个因素。
下面是液压缸设计计算的一些关键要点。
液压缸设计前需要明确以下几个参数:(1)负载:液压缸要承受的最大负载。
(2)行程:液压缸的活塞行程,即活塞从一个极限位置到另一个极限位置的移动距离。
(3)速度:液压缸的移动速度要求。
(4)传动方式:液压缸的传动方式有单杆式和双杆式,单杆式主要用于简单操作,而双杆式适用于更复杂的应用场景。
(5)工作压力:液压缸的额定工作压力,一般由液压系统的工作压力决定。
在设计液压缸时,需要进行以下计算和选型:(1)工作压力的计算:根据液压缸所需承受的最大负载和速度要求,计算出液压缸所需的工作压力。
工作压力计算公式为:工作压力=功率÷斜杠(活塞面积×张角因数)活塞面积=π×活塞直径²÷4张角因数根据活塞材料和工作环境选取合适的值。
(2)液压缸尺寸的计算:根据所需承受的最大负载和工作压力,计算出液压缸的尺寸。
液压缸尺寸计算公式为:活塞面积=承受的负载÷工作压力活塞直径=(4×活塞面积÷π)^0.5根据液压缸的类型和具体要求,还需要进行一些其他计算,如活塞杆直径、带式液压缸的带宽和带材厚度的计算等。
(3)液压缸速度的计算:根据液压缸的移动速度要求,结合液压缸的流量特性和阀门的流量系数等参数,计算出所需的液压缸速度。
液压缸速度计算公式为:流量=活塞面积×速度速度=流量÷活塞面积其中,流量需要根据阀门流量系数、压差等因素计算得出。
为了确保液压缸的工作效果和可靠性,设计时还需要考虑液压缸的密封性、液压阀的选型、活塞材料的选择和润滑等方面的计算和选型。
总结起来,液压缸的设计计算包括工作压力的计算、液压缸尺寸的计算以及液压缸速度的计算等。
液压油缸标准尺寸表
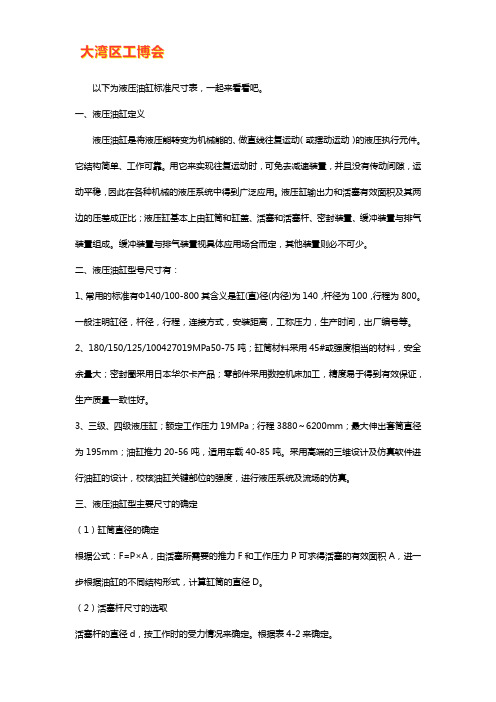
1、常用的标准有Φ140/100-800其含义是缸(直)径(内径)为140,杆径为100,行程为800。一般注明缸径,杆径,行程,连接方式,安装距离,工称压力,生产时间,出厂编号等。
2、180/150/125/100427019MPa50-75吨;缸筒材料采用45#或强度相当的材料,安全余量大;密封圈采用日本华尔卡产品;零部件采用数控机床加工,精度易于得到有效保证,生产质量一致性好。
以下为液压油缸标准尺寸表,一起来看看吧。
一、液压油缸定义
液压油缸是将液压能转变为机械能的、做直线往复运动(或摆动运动)的液压执行元件。它结构简单、工作可靠。用它来实现往复运动时,可免去减速装置,并且没有传动间隙,运动平稳,因此在各种机械的液压系统中得到广泛应用。液压缸输出力和活塞有效面积及其两边的压差成正比;液压缸基本上由缸筒和缸盖、活塞和活塞杆、密封装置、缓冲装置与排气装置组成。缓冲装置与排气装置视具体应用场合而定,其他装置则必不可少。
(2)活塞杆尺寸的选取
活塞杆的直径d,按工作时的受力情况来确定。根据表4-2来确定。
(3)油缸长度的确定
油缸筒长度=活塞行程+活塞长度+活塞导向长度+活塞杆密封及导向
长度+其它长ห้องสมุดไป่ตู้。活塞长度=(0.6—1)D;活塞杆导向长度=(0.6—1.5)d。其它长度指一些特殊的需要长度,如:两端的缓冲装置长度等。某些单活塞杆油缸油时提出最小导向程度的要求,如:H≥L/20+D/2。
3、三级、四级液压缸;额定工作压力19MPa;行程3880~6200mm;最大伸出套筒直径为195mm;油缸推力20-56吨,适用车载40-85吨。采用高端的三维设计及仿真软件进行油缸的设计,校核油缸关键部位的强度,进行液压系统及流场的仿真。
如何确定液压油缸规格型号(液压油缸选型参考)解读
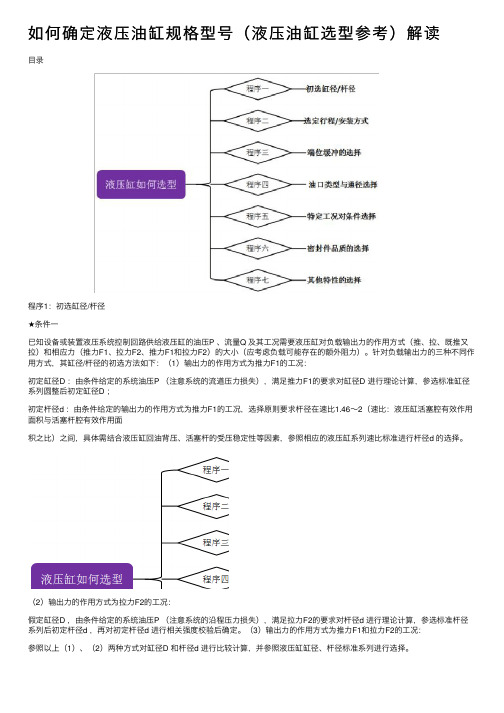
如何确定液压油缸规格型号(液压油缸选型参考)解读⽬录程序1:初选缸径/杆径★条件⼀已知设备或装置液压系统控制回路供给液压缸的油压P 、流量Q 及其⼯况需要液压缸对负载输出⼒的作⽤⽅式(推、拉、既推⼜拉)和相应⼒(推⼒F1、拉⼒F2、推⼒F1和拉⼒F2)的⼤⼩(应考虑负载可能存在的额外阻⼒)。
针对负载输出⼒的三种不同作⽤⽅式,其缸径/杆径的初选⽅法如下:(1)输出⼒的作⽤⽅式为推⼒F1的⼯况:初定缸径D :由条件给定的系统油压P (注意系统的流道压⼒损失),满⾜推⼒F1的要求对缸径D 进⾏理论计算,参选标准缸径系列圆整后初定缸径D ;初定杆径d :由条件给定的输出⼒的作⽤⽅式为推⼒F1的⼯况,选择原则要求杆径在速⽐1.46~2(速⽐:液压缸活塞腔有效作⽤⾯积与活塞杆腔有效作⽤⾯积之⽐)之间,具体需结合液压缸回油背压、活塞杆的受压稳定性等因素,参照相应的液压缸系列速⽐标准进⾏杆径d 的选择。
(2)输出⼒的作⽤⽅式为拉⼒F2的⼯况:假定缸径D ,由条件给定的系统油压P (注意系统的沿程压⼒损失),满⾜拉⼒F2的要求对杆径d 进⾏理论计算,参选标准杆径系列后初定杆径d ,再对初定杆径d 进⾏相关强度校验后确定。
(3)输出⼒的作⽤⽅式为推⼒F1和拉⼒F2的⼯况:参照以上(1)、(2)两种⽅式对缸径D 和杆径d 进⾏⽐较计算,并参照液压缸缸径、杆径标准系列进⾏选择。
★条件⼆已知设备或装置需要液压缸对负载输出⼒的作⽤⽅式(推、拉、既推⼜拉)和相应⼒(推⼒F1、拉⼒F2、推⼒F1和拉⼒F2)⼤⼩(应考虑负载可能存在的额外阻⼒)。
但其设备或装置液压系统控制回路供给液压缸的油压P 、流量Q 等参数未知,针对负载输出⼒的三种不同作⽤⽅式,其缸径/杆径的初选⽅法如下:(1)根据本设备或装置的⾏业规范或特点,确定液压系统的额定压⼒P ;专⽤设备或装置液压系统的额定压⼒由具体⼯况定,⼀般建议在中低压或中⾼压中进⾏选择。
(2)根据本设备或装置的作业特点,明确液压缸的⼯作速度要求。
液压缸设计计算实例
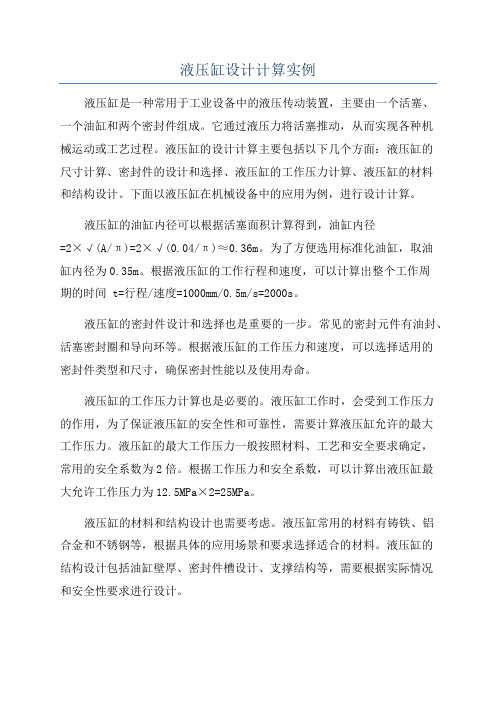
液压缸设计计算实例液压缸是一种常用于工业设备中的液压传动装置,主要由一个活塞、一个油缸和两个密封件组成。
它通过液压力将活塞推动,从而实现各种机械运动或工艺过程。
液压缸的设计计算主要包括以下几个方面:液压缸的尺寸计算、密封件的设计和选择、液压缸的工作压力计算、液压缸的材料和结构设计。
下面以液压缸在机械设备中的应用为例,进行设计计算。
液压缸的油缸内径可以根据活塞面积计算得到,油缸内径=2×√(A/π)=2×√(0.04/π)≈0.36m。
为了方便选用标准化油缸,取油缸内径为0.35m。
根据液压缸的工作行程和速度,可以计算出整个工作周期的时间 t=行程/速度=1000mm/0.5m/s=2000s。
液压缸的密封件设计和选择也是重要的一步。
常见的密封元件有油封、活塞密封圈和导向环等。
根据液压缸的工作压力和速度,可以选择适用的密封件类型和尺寸,确保密封性能以及使用寿命。
液压缸的工作压力计算也是必要的。
液压缸工作时,会受到工作压力的作用,为了保证液压缸的安全性和可靠性,需要计算液压缸允许的最大工作压力。
液压缸的最大工作压力一般按照材料、工艺和安全要求确定,常用的安全系数为2倍。
根据工作压力和安全系数,可以计算出液压缸最大允许工作压力为12.5MPa×2=25MPa。
液压缸的材料和结构设计也需要考虑。
液压缸常用的材料有铸铁、铝合金和不锈钢等,根据具体的应用场景和要求选择适合的材料。
液压缸的结构设计包括油缸壁厚、密封件槽设计、支撑结构等,需要根据实际情况和安全性要求进行设计。
综上所述,液压缸设计计算涉及液压缸的尺寸计算、密封件的设计和选择、液压缸的工作压力计算、液压缸的材料和结构设计等方面。
通过合理计算和选取,可以设计出安全可靠的液压缸,满足机械设备的工作需求。
液压缸结构设计
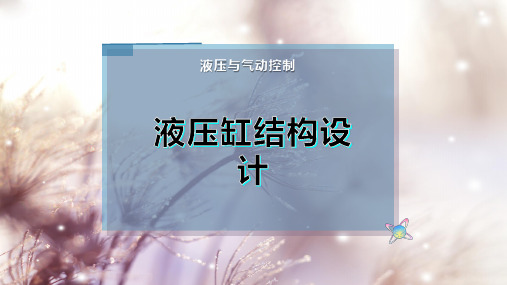
1.3 强度校核
1. 缸筒壁厚校核 在中、低压液压系统中,液压缸的缸筒壁厚常由结构工艺
上的要求决定,强度问题是次要的,一般不须验算。在高压系 统中,即
1.3 强度校核 2. 活塞杆直径校核 (1)强度计算。活塞杆强度按下式校核
(2)稳定性计算。活塞杆所能承受的负载F,应小于使它保持 工作稳定的临界负载Fk。
3.螺栓强度校核
1.3 强度校核
3.螺栓强度校核 液压缸盖固定螺栓在工作过程中同时承受拉应力和扭应力,
其螺栓直径ds可按下式校核
液压与气动控制
d值也可由D和λv来决定。按国家标准进行圆整。行业标准规定 了单杆活塞液压缸两腔面积比的标准系列 。
3)缸筒长度L 液压缸的缸筒长度L由最大工作行程决定, 通常缸筒的长度=活塞最大行程+活塞长度+活塞杆导向长度+ 活塞杆密封长度+其他长度,其中活塞长度=(0.6~1)D,活塞 杆导向长度= (0.6~1.5)d。其他长度是指一些特殊装置所需 长度,如液压缸两端缓冲装置所需的长度等。缸筒的长度一般 不超过其内径的20倍。
4)最小导向长度H 对于一般的液压缸,当液压缸的最大行 程为L,缸筒直径为D时,最小导向长度H为:
活塞的宽度B一般取B=(0.6~1)D。导向套滑动面长度A,在 D<80mm时,取A=(0.6~1)D,在D>80mm时,取A=(0.6~ 1)d。为保证最小导向长度,过分增大A和B都是不合适的,必要时 可在导向套和活塞之间装一隔套(图中零件K),隔套的长度C由 需要的最小导向长度H决定,即
1.2 液压缸主要尺寸计算
1)缸筒内径D 根据负载大小和选定的工作压力,或运动速 度和输入流量,按本章有关算式确定后,再从国家标准中选取 相近尺寸加以圆整。
液压缸标准缸径尺寸

液压缸标准缸径尺寸液压缸是一种常用的执行元件,广泛应用于工业生产中的各个领域。
在液压系统中,液压缸的尺寸大小直接影响着其工作性能和使用效果。
因此,选择合适的液压缸标准缸径尺寸对于液压系统的设计和使用至关重要。
首先,我们需要了解液压缸的标准缸径尺寸是如何确定的。
液压缸的标准缸径尺寸通常由液压缸的工作压力、工作速度、工作行程以及所需的输出力来决定。
在确定液压缸的标准缸径尺寸时,需要考虑到液压缸在工作过程中所承受的压力和力的大小,以及所需的工作速度和行程,从而确定合适的缸径尺寸。
其次,不同类型的液压缸在选择标准缸径尺寸时会有所不同。
例如,单作用液压缸和双作用液压缸在确定标准缸径尺寸时需要考虑的因素也会有所差异。
另外,液压缸的结构形式和工作原理也会对标准缸径尺寸的选择产生影响。
因此,在选择液压缸标准缸径尺寸时,需要根据具体的工作条件和要求来进行综合考虑和分析。
此外,液压缸的标准缸径尺寸还需要考虑到液压系统的整体设计和配套。
在液压系统中,液压缸的标准缸径尺寸需要与液压泵、阀门、管路等其他元件相匹配,以确保整个液压系统的正常运行和协调工作。
因此,在选择液压缸标准缸径尺寸时,需要充分考虑液压系统的整体设计和配套情况,以实现最佳的工作效果和性能。
最后,正确选择液压缸的标准缸径尺寸对于提高液压系统的工作效率和稳定性具有重要意义。
合适的液压缸标准缸径尺寸可以有效地提高液压系统的工作效率,降低能源消耗,延长液压元件的使用寿命,提高系统的可靠性和稳定性,从而为工业生产提供更加可靠和高效的动力支持。
综上所述,液压缸标准缸径尺寸的选择是液压系统设计和使用过程中的关键环节。
正确选择合适的液压缸标准缸径尺寸可以有效地提高液压系统的工作效率和稳定性,为工业生产提供可靠的动力支持。
因此,在液压系统设计和使用过程中,需要充分考虑液压缸的标准缸径尺寸选择,以实现最佳的工作效果和性能。
液压缸选型参考

【液压缸选定程序】程序1:初选缸径/杆径(以单活塞杆双作用液压缸为例)※ 条件一已知设备或装置液压系统控制回路供给液压缸的油压P、流量Q及其工况需要液压缸对负载输出力的作用方式(推、拉、既推又拉)和相应力(推力F1、拉力F2、推力F1和拉力F2)的大小(应考虑负载可能存在的额外阻力)。
针对负载输出力的三种不同作用方式,其缸径/杆径的初选方法如下:(1)输出力的作用方式为推力F1的工况:初定缸径D:由条件给定的系统油压P(注意系统的流道压力损失),满足推力F1的要求对缸径D进行理论计算,参选标准缸径系列圆整后初定缸径D;初定杆径d:由条件给定的输出力的作用方式为推力F1的工况,选择原则要求杆径在速比1.46~2(速比:液压缸活塞腔有效作用面积与活塞杆腔有效作用面积之比)之间,具体需结合液压缸回油背压、活塞杆的受压稳定性等因素,参照相应的液压缸系列速比标准进行杆径d的选择。
(2)输出力的作用方式为拉力F2的工况:假定缸径D,由条件给定的系统油压P(注意系统的沿程压力损失),满足拉力F2的要求对杆径d进行理论计算,参选标准杆径系列后初定杆径d,再对初定杆径d进行相关强度校验后确定。
(3)输出力的作用方式为推力F1和拉力F2的工况:参照以上(1)、(2)两种方式对缸径D和杆径d进行比较计算,并参照液压缸缸径、杆径标准系列进行选择。
※ 条件二已知设备或装置需要液压缸对负载输出力的作用方式(推、拉、既推又拉)和相应力(推力F1、拉力F2、推力F1和拉力F2)大小(应考虑负载可能存在的额外阻力)。
但其设备或装置液压系统控制回路供给液压缸的油压P、流量Q等参数未知,针对负载输出力的三种不同作用方式,其缸径/杆径的初选方法如下:(1)根据本设备或装置的行业规范或特点,确定液压系统的额定压力P;专用设备或装置液压系统的额定压力由具体工况定,一般建议在中低压或中高压中进行选择。
(2)根据本设备或装置的作业特点,明确液压缸的工作速度要求。
液压缸计算公式(液压缸内径和活塞杆直径的确定等)
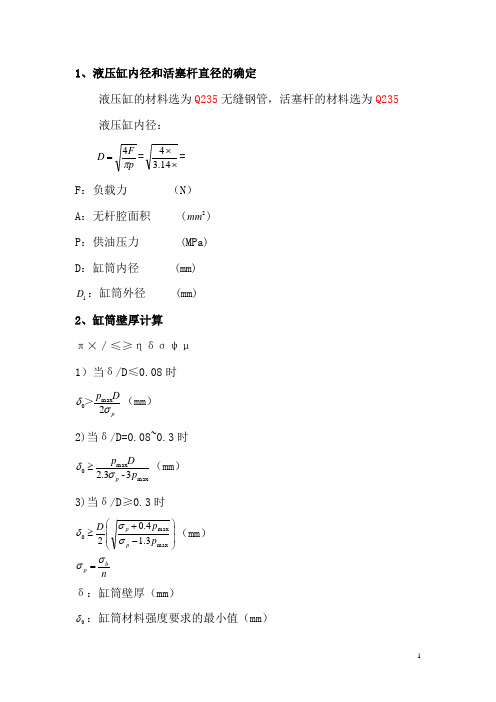
1、液压缸内径和活塞杆直径的确定液压缸的材料选为Q235无缝钢管,活塞杆的材料选为Q235 液压缸内径:p FD π4==⨯⨯14.34=F :负载力 (N )A :无杆腔面积 (2mm )P :供油压力 (MPa)D :缸筒内径 (mm)1D :缸筒外径 (mm)2、缸筒壁厚计算π×/≤≥ηδσψμ1)当δ/D ≤0.08时pDp σδ2max 0>(mm )2)当δ/D=0.08~0.3时maxmax 03-3.2p Dp p σδ≥(mm )3)当δ/D ≥0.3时⎪⎪⎭⎫⎝⎛-+≥max max 03.14.02p p D p p σσδ(mm ) n bp σσ=δ:缸筒壁厚(mm )0δ:缸筒材料强度要求的最小值(mm )m ax p :缸筒内最高工作压力(MPa )p σ:缸筒材料的许用应力(MPa )b σ:缸筒材料的抗拉强度(MPa )s σ:缸筒材料屈服点(MPa )n :安全系数3 缸筒壁厚验算21221s )(35.0D D D PN -≤σ(MPa) D D P s rL 1lg3.2σ≤ PN :额定压力rL P :缸筒发生完全塑性变形的压力(MPa)r P :缸筒耐压试验压力(MPa)E :缸筒材料弹性模量(MPa)ν:缸筒材料泊松比 =0.3同时额定压力也应该与完全塑性变形压力有一定的比例范围,以避免塑性变形的发生,即:()rL P PN 42.0~35.0≤(MPa)4 缸筒径向变形量⎪⎪⎭⎫ ⎝⎛+-+=∆ν221221D D D D E DP D r (mm )变形量△D 不应超过密封圈允许范围5 缸筒爆破压力DD PE b 1lg 3.2σ=(MPa)6 缸筒底部厚度PP D σδmax21433.0≥(mm )2D :计算厚度处直径(mm )7 缸筒头部法兰厚度PL a d r Fbh σπ)(4-=(mm )F :法兰在缸筒最大内压下所承受轴向力(N )b :连接螺钉孔的中心到法兰内圆的距离(mm )a r :法兰外圆的半径(mm )L d :螺钉孔直径如不考虑螺钉孔,则:Pa r Fbh σπ4=(mm )8 螺纹强度计算螺纹处拉应力()2214D d KF-=πσ (MPa)螺纹处切应力)(2.033101D d KFd K -=τ (MPa)合成应力P n στσσ≤+=223 许用应力0sn P σσ=F :螺纹处承受的最大拉力0d :螺纹外径 (mm )1d :螺纹底径 (mm )K :拧紧螺纹系数,不变载荷取K=1.25~1.5,变载荷取K=2.5~4 1K :螺纹连接的摩擦因数,1K =0.07~0.2,平均取1K =0.12s σ:螺纹材料屈服点(MPa )0n :安全系数,取0n =1.2~2.59 缸筒法兰连接螺栓强度计算螺栓螺纹处拉应力zd KF214πσ= (MPa )螺纹处切应力zd KFd K 31012.0=τ (MPa)合成应力P n σστσσ≤≈+=3.1322z :螺栓数量10、缸筒卡键连接卡键的切应力(A 处)lD P l D D P 441max 121max ==ππτ (MPa)卡键侧面的挤压应力 )2(h 4)2(44121max 2212121max h D D P h D D D P c -=--=πππσ卡键尺寸一般取h=δ,l=h,2hh h 21==验算缸筒在A 断面上的拉应力[]22121max 22121max)(4-)(4D h D D P D h D D P --=-=ππσ (MPa)11、缸筒与端部焊接焊缝应力计算()n d D F b σηπσ≤-=21214 (MPa)1D :缸筒外径 (mm )1d :焊缝底径 (mm )η:焊接效率,取η=0.7b σ:焊条抗拉强度 (MPa)n :安全系数,参照缸筒壁的安全系数选取如用角焊ησh D F 12= h —焊角宽度 (mm )12、活塞杆强度计算1)活塞杆在稳定工况下,如果只承受轴向推力或拉力,可以近似的用直杆承受拉压载荷的简单强度计算公式进行计算:P d Fσπσ≤=24 (MPa)2)如果活塞杆所承受的弯曲力矩(如偏心载荷等),则计算式: P d W M A F σσ≤⎪⎪⎭⎫⎝⎛+= (MPa) 3)活塞杆上螺纹、退刀槽等部位是活塞杆的危险截面,危险截面的合成应力应该满足:P n F σσ≤≈222d 8.1 (MPa) 对于活塞杆上有卡键槽的断面,除计算拉应力外,还要计算校核卡键对槽壁的挤压应力:()[]pp c d d F σπσ≤+-=243212 F :活塞杆的作用力(N )d :活塞杆直径 (mm )P σ:材料许用应力,无缝钢管P σ=100~110MPa ,中碳钢(调质)P σ=400MPad A :活塞杆断面积 (2mm )W :活塞杆断面模数 (3mm )M :活塞杆所承受弯曲力矩(N.m )2F :活塞杆的拉力 (N )2d :危险截面的直径 (mm )1d :卡键槽处外圆直径 (mm )3d :卡键槽处内圆直径 (mm )c :卡键挤压面倒角 (mm )pp σ:材料的许用挤压应力(MPa )13、活塞杆弯曲稳定行计算活塞杆细长比计算 dL B 4=λ B L :支铰中心到耳环中心距离(油缸活塞杆完全伸出时的安装距);1)若活塞杆所受的载荷力1F 完全在活塞杆的轴线上,则按下式验算:kK n F F ≤1 2261210B K L K I E F ⨯=π (N )()()51108.111⨯=++=b a E E (MPa ) 圆截面:44049.064d d I ==π(4m )K F :活塞杆弯曲失稳临界压缩力 (N )K n :安全系数,通常取K n =3.5~6K :液压缸安装及导向系数(见机械设计手册5卷21-292) 1E :实际弹性模量(MPa )a :材料组织缺陷系数,钢材一般取a ≈1/12b :活塞杆截面不均匀系数,一般取b ≈1/13E :材料弹性模量,钢材 5101.2⨯=E (MPa )I :活塞杆横截面惯性矩(4m )d A :活塞杆截面面积 (2m )e :受力偏心量 (m )s σ:活塞杆材料屈服点(MPa )S :行程 (m )2)若活塞杆所受的载荷力1F 偏心时,推力与支承的反作用力不完全处在中线上,则按下式验算:βσsec 81106e d A F d S K +⨯= (N )其中:62010⨯=EI L F a B K β 一端固定,另一端自由0a =1,两端球铰0a =0.5,两端固定0a =0.25, 一端固定,另一端球铰0a =0.3514、 缸的最小导向长度220DS H +≥(mm )导向套滑动面的长度1)在缸径≤80mm 时A=(0.6~1)D2)在缸径>80mm 时A=(0.6~1)d活塞宽度取B=(0.6~1)D15、圆柱螺旋压缩弹簧计算材料直径:PKCP d τn 6.1≥CC C K 615.04414+--= 或按照机械设计手册选取(5卷11-28) d DC = 一般初假定C-5~8有效圈数:'8'd3n n 4P P D P F Gd n ==弹簧刚度n C GDn D G P 43488d '==总圈数x n +=1nx :1/2 (见机械设计手册第5卷 11-18) 节距:n dH t )2~1(0-=间距:d t -=δ自由高度:d n H )(10+=最小工作载荷时高度:101-F H H =GD C P Gd D P F 414311n 8n 8==或者'11P PF =最大工作载荷时的高度n n F H H -0=GD C P Gd D P F n n 443n n 8n 8==或者'n1P P F = 工作极限载荷下的高度j j F H H -0=GDC P GdD P F j j 443j n 8n 8==或者'j 1P P F =弹簧稳定性验算 高径比:DH b 0=应满足下列要求两端固定 b ≤5.3 一端固定,另一端回转 b ≤3.7 两端回转 b ≤2.6 当高径比大于上述数值时,按照下式计算:n B C P H P C P >0'=C P :弹簧的临界载荷 (N )B C :不稳定系数 (见机械设计手册第5卷 11-19) n P :最大工作载荷 (N )强度验算: 安全系数 P S S ≥+=maxmin075.0τττ0τ: 弹簧在脉动循环载荷下的剪切疲劳强度,(见机械设计手册第5卷 11-19)m ax τ: 最大载荷产生的最大切应力 n 3max 8P d KDπτ=, m in τ: 最小载荷产生的最小切应力 13in8P dKD m πτ=, P S :许用安全系数 当弹簧的设计计算和材料实验精度高时,取P S =1.3~1.7 , 当精确度低时,取 P S =1.8~2.2静强度: 安全系数P SS S ≥=maxττ S τ:弹簧材料的屈服极限15 系统温升的验算在整个工作循环中,工进阶段所占的时间最长,为了简化计算,主要考虑工进时的发热量。
- 1、下载文档前请自行甄别文档内容的完整性,平台不提供额外的编辑、内容补充、找答案等附加服务。
- 2、"仅部分预览"的文档,不可在线预览部分如存在完整性等问题,可反馈申请退款(可完整预览的文档不适用该条件!)。
- 3、如文档侵犯您的权益,请联系客服反馈,我们会尽快为您处理(人工客服工作时间:9:00-18:30)。
液压缸主要尺寸的确定ﻫﻫ
液压缸是液压传动的执行元件,它和主机工作机构有直接的联系,对于不同的机种和机构,液压缸具有不同的用途和工作要求。
因此,在设计液压缸之前,必须对整个液压系统进行工况分析,编制负载图,选定系统的工作压力(详见第九章),然后根据使用要求选择结构类型,按负载情况、运动要求、最大行程等确定其主要工作尺寸,进行强度、稳定性和缓冲验算,最后再进行结构设计。
ﻫ1.液压缸的设计内容和步骤
ﻫ(1)选择液压缸的类型和各部分结构形式.ﻫ
(2)确定液压缸的工作参数和结构尺寸。
ﻫ(3)结构强度、刚度的计算和校核。
(4)导向、密封、防尘、排气和缓冲等装置的设计。
ﻫﻫ(5)绘制装配图、零件图、编写设计说明书。
ﻫ
2。
计算液压缸的结构尺寸液压缸的结构尺寸主下面只着重介绍几项设计工作。
ﻫﻫ
要有三个:缸筒内径D、活塞杆外径d和缸筒长度L。
ﻫ(1)缸筒内径D。
液压缸的缸筒内径D是根据负载的大小来选定工作压力或往返运动速度比,求得液压缸的有效工作面积,从而得到缸筒内径D,再从GB2348-80标准中选取最近的标准值作为所设计的缸筒内径。
ﻫ根据负载和工作压力的大小确定D:
①以无杆腔作工作腔时?ﻫﻫ(4—32)
②以有杆腔作工作腔时?ﻫ
(4—33)ﻫ
式中:pI为缸工作腔的工作压力,可根据机床类型或负载的大小来确定;Fmax为最大作用负载。
ﻫﻫ(2)活塞杆外径d。
活塞杆外径d通常先从满足速度或速度比的要求来选择,然后再校核其结构强度和稳定性。
若速度比为λv,则该处应有一个带根号的式子:ﻫﻫ(4-34)ﻫﻫ也可根据活塞杆受力状况来确定,一般为受拉力作用时,d=0.3~0。
5D。
ﻫﻫ受压力作用时:ﻫﻫpI<5 MPa时,d=0.5~0.55Dﻫﻫ
5MPa<pI<7MPa时,d=0。
6~0。
7DﻫﻫpI>7MPa时,d=0.7D
ﻫ(3)缸筒长度L。
缸筒长度L由最大工作行程长度加上各种结构需要来确定,即: L=l+B+A+M+C
式中:l为活塞的最大工作行程;B为活塞宽度,一般为(0.6-1)D;A为活塞杆导向长度,取(0。
6-1.5)D;M为活塞杆密封长度,由密封方式定;C为其他长度。
ﻫ一般缸筒的长度最好不超过内径的20倍。
ﻫﻫ另外,液压缸的结构尺寸还有最小导向长度H。
(4)最小导向长度的确定。
ﻫ当活塞杆全部外伸时,从活塞支承面中点到导向套滑动面中点的距离称为最小导向长度H(如图4—19所示)。
如果导向长度过小,将使液压缸的初始挠度(间隙引起的挠度)增大,影响液压缸的稳定性,因此设计时必须保证有一最小导向长度.
ﻫ
图4-19油缸的导向长度ﻫ
K—隔套ﻫ
对于一般的液压缸,其最小导向长度应满足下式:ﻫ
H≥L/20+D/2(4-35)ﻫﻫ式中:L为液压缸最大工作行程(m);D为缸筒内径(m).
ﻫ一般导向套滑动面的长度A,在D<80mm时取A=(0。
6-1.0)D,在D>80m m时取A=(0。
6-1。
0)d;活塞的宽度B则取B=(0.6—1。
0)D.为保证最小导向长度,过分增大A和B都是不适宜的,最好在导向套与活塞之间装一隔套K,隔套宽度C由所需的最小导向长度决定,即:ﻫﻫC=H
—(4—36)
ﻫ采用隔套不仅能保证最小导向长度,还可以改善导向套及活塞的通用性.
ﻫ3.强度校核对液压缸的缸筒壁厚δ、活塞杆直径d和缸盖固定螺栓的直径,在高压系统中必须进行强度校核。
ﻫ(1)缸筒壁厚校核。
缸筒壁厚校核时分薄壁和厚壁两种情况,当D/δ≥10时为薄壁,壁厚按下式进行校核:ﻫﻫδ>=ptD/2[σ](4-37)
ﻫ式中:D为缸筒内径;pt为缸筒试验压力,当缸的额定压力pn≤16MPa时,取pt=1.5pn,pn为缸生产时的试验压力;当pn>16MPa时,取
pv=1。
25pn;[σ]为缸筒材料的许用应力,[σ]=σb/n,σb为材料的抗拉强度,n为安全系数,一般取n=5。
ﻫﻫ当D/σ<10时为厚壁,壁厚按下式进行校核:ﻫﻫδ≥(4-38)ﻫ
在使用式(4-37)、式(4-38)进行校核时,若液压缸缸筒与缸盖采用半环连接,δ应取缸筒壁厚最小处的值。
?ﻫﻫ(2)活塞杆直径校核。
活塞杆的直径d按下式进行校核:ﻫ
d≥(4—39)ﻫﻫ式中:F为活塞杆上的作用力;[σ]为活塞杆材料的许用应力,[σ]=σb/1.4。
ﻫ(3)液压缸盖固定螺栓直径校核。
液压缸盖固定螺栓直径按下式计算:ﻫﻫd ≥(4—40)
式中:F为液压缸负载;Z为固定螺栓个数;k为螺纹拧紧系数,k=1.12~1.5,[σ]=
σs/(1。
2-2。
5),σs为材料的屈服极限.ﻫﻫ4。
液压缸稳定性校核活塞杆受轴向
压缩负载时,其直径d一般不小于长度L的1/15。
当L/d≥15时,须进行稳定性校核,应使活塞杆承受的力F不能超过使它保持稳定工作所允许的临界负载Fk,以免发生纵向弯曲,破坏液压缸的正常工作。
Fk的值与活塞杆材料性质、截面形状、直径和长度以及缸的安装方式等因素有关,验算可按材料力学有关公式进行.
ﻫ5。
缓冲计算液压缸的缓冲计算主要是估计缓冲时缸中出现的最大冲击压力,以便用来校核缸筒强度、制动距离是否符合要求。
缓冲计算中如发现工作腔中的液压能和工作部件的动能不能全部被缓冲腔所吸收时,制动中就可能产生活塞和
缸盖相碰现象。
ﻫ小编推荐水泵控制柜、自动供水设备、无负压给水设备、无负压供水设备、变频恒压供水设备、水泵变频控制柜、水泵变频控制箱、变频水泵控制箱首选上海市三星水泵厂上海意海耐腐蚀泵制造有限公司上海市新三星给排水设备有限公
司转自:国际泵阀贸易网ﻫ
ﻫ液压缸在缓冲时,缓冲腔内产生的液压能E1和工作部件产生的机械能E2分别为:
ﻫE1=pcAclc (4—41)ﻫ
E2=ppAplc+mV2—Fflc (4-42)
式中:pc为缓冲腔中的平均缓冲压力;pp为高压腔中的油液压力;Ac、Ap 为缓冲腔、高压腔的有效工作面积;Lc为缓冲行程长度;m为工作部件质量;v0为工作部件运动速度;Ff为摩擦力。
ﻫ式(4-42)中等号右边第一项为高压腔中的液压能,第二项为工作部件的动能,第三项为摩擦能.当E1=E2时,工作部件的机械能全部被缓冲腔液体所吸收,由上两式得:ﻫ
Pc=E2/Aclc (4—43)
如缓冲装置为节流口可调式缓冲装置,在缓冲过程中的缓冲压力逐渐降低,假定缓冲压力线性地降低,则最大缓冲压力即冲击压力为:ﻫﻫPcmax=Pc+mυ02/2Acl c (4—44)
ﻫ如缓冲装置为节流口变化式缓冲装置,则由于缓冲压力Pc始终不变,最大缓冲压力的值如式(4-43)所示.ﻫﻫ
6.液压缸设计中应注意的问题液压缸的设计和使用正确与否,直接影响到它的性能和易否发生故障。
在这方面,经常碰到的是液压缸安装不当、活塞杆承受偏载、液压缸或活塞下垂以及活塞杆的压杆失稳等问题。
所以,在设计液压缸时,必须注意以下几点:ﻫ
(1)尽量使液压缸的活塞杆在受拉状态下承受最大负载,或在受压状态下具有良
好的稳定性
(2)考虑液压缸行程终了处的制动问题和液压缸的排气问题.缸内如无缓冲装置
和排气装置,系统中需有相应的措施,但是并非所有的液压缸都要考虑这些问题。
(3)正确确定液压缸的安装、固定方式。
如承受弯曲的活塞杆不能用螺纹连接,要用止口连接。
液压缸不能在两端用键或销定位。
只能在一端定位,为的是不致阻碍它在受热时的膨胀.如冲击载荷使活塞杆压缩。
定位件须设置在活塞杆端,如为拉伸则设置在缸盖端。
ﻫ(4)液压缸各部分的结构需根据推荐的结构形式和设计标准进行设计,尽可能做到结构简单、紧凑、加工、装配和维修方便。
ﻫﻫ(5)在保证能满足运动行程和负载力的条件下,应尽可能地缩小液压缸的轮廓尺寸。
ﻫ(6)要保证密封可靠,防尘良好.液压缸可靠的密封是其正常工作的重要因素。
如泄漏严重,不仅降低液压缸的工作效率,甚至会使其不能正常工作(如满足不了负载力和运动速度要求等)。
良好的防尘措施,有助于提高液压缸的工作寿命. ﻫ总之,液压缸的设计内容不是一成不变的,根据具体的情况有些设计内容可不做或少做,也可增大一些新的内容。
设计步骤可能要经过多次反复修改,才能得到正确、合理的设计结果。
在设计液压缸时,正确选择液压缸的类型是所有设计计算的前提。
在选择液压缸的类型时,要从机器设备的动作特点、行程长短、运动性能等要求出发,同时还要考虑到主机的结构特征给液压缸提供的安装空间和具体位置.ﻫ
如:机器的往复直线运动直接采用液压缸来实现是最简单又方便的。
对于要求往返运动速度一致的场合,可采用双活塞杆式液压缸;若有快速返回的要求,则宜用单活塞杆式液压缸,并可考虑用差动连接.行程较长时,可采用柱塞缸,以减少加工的困难;行程较长但负载不大时,也可考虑采用一些传动装置来扩大行程。
往复摆动运动既可用摆动式液压缸,也可用直线式液压缸加连杆机构或齿轮-—齿条机构来实现。