硅橡胶混炼胶
硅橡胶的成分
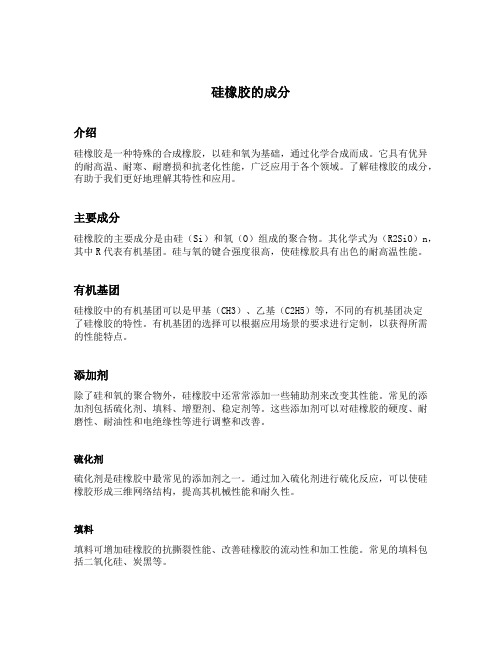
硅橡胶的成分介绍硅橡胶是一种特殊的合成橡胶,以硅和氧为基础,通过化学合成而成。
它具有优异的耐高温、耐寒、耐磨损和抗老化性能,广泛应用于各个领域。
了解硅橡胶的成分,有助于我们更好地理解其特性和应用。
主要成分硅橡胶的主要成分是由硅(Si)和氧(O)组成的聚合物。
其化学式为(R2SiO)n,其中R代表有机基团。
硅与氧的键合强度很高,使硅橡胶具有出色的耐高温性能。
有机基团硅橡胶中的有机基团可以是甲基(CH3)、乙基(C2H5)等,不同的有机基团决定了硅橡胶的特性。
有机基团的选择可以根据应用场景的要求进行定制,以获得所需的性能特点。
添加剂除了硅和氧的聚合物外,硅橡胶中还常常添加一些辅助剂来改变其性能。
常见的添加剂包括硫化剂、填料、增塑剂、稳定剂等。
这些添加剂可以对硅橡胶的硬度、耐磨性、耐油性和电绝缘性等进行调整和改善。
硫化剂硫化剂是硅橡胶中最常见的添加剂之一。
通过加入硫化剂进行硫化反应,可以使硅橡胶形成三维网络结构,提高其机械性能和耐久性。
填料填料可增加硅橡胶的抗撕裂性能、改善硅橡胶的流动性和加工性能。
常见的填料包括二氧化硅、炭黑等。
增塑剂可以使硅橡胶变得更加柔软和可塑,提高其可加工性。
稳定剂稳定剂可以抑制硅橡胶在加工和使用过程中的老化和劣化,延长硅橡胶的寿命。
加工方法硅橡胶的成分确定后,需要进行相应的加工方法以获得所需的形状和性能。
1.混炼:将硅橡胶和各种添加剂进行混合,通常使用开炼机进行混炼,以确保添加剂均匀分散。
2.成型:混炼后的硅橡胶将被送入成型机中,通过挤出、压延、注塑等方式,制成所需形状的硅橡胶制品。
3.硫化:成型后的硅橡胶制品需经过硫化反应,通常在高温下进行,以形成硬硫化层,提高其耐热性和耐寒性。
应用领域硅橡胶由于其独特的性能,被广泛应用于各个领域。
汽车行业硅橡胶在汽车行业中被用于制造密封件、隔音件、悬挂部件等。
其耐高温和耐磨性能使得硅橡胶可以在各种恶劣的工作环境中长期稳定运行。
医疗器械硅橡胶是许多医疗器械的关键组成部分,如医用导管、人工心脏瓣膜等。
硅橡胶的性能及制备工艺

优异的生理特性:无毒无味、生物相容性好、 耐生物老化、较好的抗凝血性、长期植入体内 物理性能下降甚微、耐高温严寒( -90°- 250°)良好的电绝缘性、耐氧老化性、耐光老 化性以及防霉性、化学稳定性等。
经混炼、挤出,热空气硫化成型, 制得符合医用要求 的加成型硅橡胶胶管。
基本原理: 加成型硅橡胶使用铂络合物作催化剂, 含氢硅油作交联剂, 聚 硅氧烷末端及中间的乙烯基与交联剂发生加成反应, 其交联 机理如下:
从反应机理看, 加成型硅橡胶的制品无低分子物生成, 产 品硫化均匀, 具有优良的耐硫化返原性。
2、工艺流程
以2 , 4 - 二氯过氧化苯甲酰为硫化剂、110 - 2 甲基乙烯基硅 橡胶(平均摩尔质量5.5 ×105 g/ mol , 乙烯基摩尔分数 0.17 % )为原料, 制备出外观无瑕疵,邵尔A 硬度55~70 度, 最小扯断力90~180 N 的硅橡胶胶管。
硅氮烷在加 工过程中要 求进行热处 理并有氨气 放出,大批 量生产对环 境有污染。
硅橡胶依其烃基种类的不同, 可以分为二甲基硅橡胶、 甲基乙烯基硅橡胶、甲基苯基硅橡胶、氟硅橡胶。在实 际生产中应用较多的是甲基乙烯基硅橡胶,
一般用高纯度的(CH3)2SiCl2 (99.98%)水解,所 得的硅二醇随即发生分子间脱水经缩聚后就可以生成 高分子的线型多缩硅醇。聚合度在2000以上,相对 分子质量在40-50万之间的高聚物是无色透明软糖状 的弹性物质,称为硅橡胶。
硅橡胶
➢概述 ➢医用级材料的制备机理 ➢医用硅橡胶的性能要求 ➢硅橡胶的制备工艺
✓普通橡胶 ✓硅橡胶胶管
——过氧化物型硅橡胶胶管 ——加成型硅橡胶 ✓医用硅橡胶GY - 131 的合成
211189470_硅橡胶的结晶行为及动力学研究
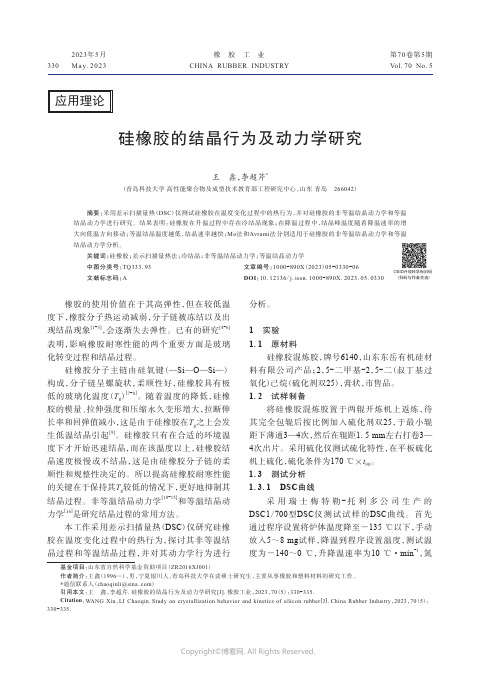
橡 胶 工 业CHINA RUBBER INDUSTRY330第70卷第5期Vol.70 No.52023年5月May.2023硅橡胶的结晶行为及动力学研究王 鑫,李超芹*(青岛科技大学 高性能聚合物及成型技术教育部工程研究中心,山东 青岛 266042)摘要:采用差示扫描量热(DSC )仪测试硅橡胶在温度变化过程中的热行为,并对硅橡胶的非等温结晶动力学和等温结晶动力学进行研究。
结果表明:硅橡胶在升温过程中存在冷结晶现象;在降温过程中,结晶峰温度随着降温速率的增大向低温方向移动;等温结晶温度越低,结晶速率越快;Mo 法和Avrami 法分别适用于硅橡胶的非等温结晶动力学和等温结晶动力学分析。
关键词:硅橡胶;差示扫描量热法;冷结晶;非等温结晶动力学;等温结晶动力学中图分类号:TQ333.93 文章编号:1000-890X (2023)05-0330-06文献标志码:A DOI :10.12136/j.issn.1000-890X.2023.05.0330橡胶的使用价值在于其高弹性,但在较低温度下,橡胶分子热运动减弱,分子链被冻结以及出现结晶现象[1-3],会逐渐失去弹性。
已有的研究[4-6]表明,影响橡胶耐寒性能的两个重要方面是玻璃化转变过程和结晶过程。
硅橡胶分子主链由硅氧键(—Si —O —Si —)构成,分子链呈螺旋状,柔顺性好,硅橡胶具有极低的玻璃化温度(T g )[7-8]。
随着温度的降低,硅橡胶的模量、拉伸强度和压缩永久变形增大,拉断伸长率和回弹值减小,这是由于硅橡胶在T g 之上会发生低温结晶引起[9]。
硅橡胶只有在合适的环境温度下才开始迅速结晶,而在该温度以上,硅橡胶结晶速度极慢或不结晶,这是由硅橡胶分子链的柔顺性和规整性决定的。
所以提高硅橡胶耐寒性能的关键在于保持其T g 较低的情况下,更好地抑制其结晶过程。
非等温结晶动力学[10-15]和等温结晶动力学[16]是研究结晶过程的常用方法。
硅橡胶

硅橡胶 - 特点硅橡胶分热硫化型(高温硫化硅胶HTV)和室温硫化型(RTV),其中室温硫化型又分缩聚反应型和加成反应型。
高温硅橡胶主要用于制造各种硅橡胶制品,而室温硅橡胶则主要是作为粘接剂、灌封材料或模具使用。
热硫化型用量最大,热硫化型又分甲基硅橡胶(MQ)、甲基乙烯基硅橡胶(VMQ,用量及产品牌号最多)、甲基乙烯基苯基硅橡胶PVMQ(耐低温、耐辐射),其他还有睛硅橡胶、氟硅橡胶等。
?高温硫化甲基硅橡胶于1944年由美国通用电气公司研制成功。
1952年,美国陶-康宁公司L.斯特布莱唐和K.波尔曼蒂尔研制出双组分室温硫化硅橡胶;1953~1955年制成甲基乙烯基硅橡胶;1956~1957年出现硅氟橡胶;1958~1959年开发成功单组分室温硫化硅橡胶;之后出现加成型硅橡胶系列产品。
世界上有十多个国家生产硅橡胶。
80年代以来,每年以15%左右的速度增长。
中国从60年代初期开始相继研制成功各类硅橡胶,现均有批量生产。
硅橡胶主要有下列品种:高温硫化硅橡胶? 生胶无色透明,有塑性,分子量35万~70万,能溶于苯等溶剂中,制品耐氧化,抗臭氧,高频下电气绝缘性优良,耐电弧、耐电晕,并有透气和对人体生理惰性等特点。
大量用作苛刻条件下的电线、电缆绝缘层,密封件,导管,登月鞋等。
因其无致癌性,有较好的抗凝血性和生物相容性,已大量用于制作人体内外用的导管、插管、人工关节等。
高温硫化硅橡胶通常以高纯度八甲基环四硅氧烷和带有-C6H5、-CH=CH2、-CH2CH2-CF3等基团的环四硅氧烷为原料,用酸碱催化剂开环共聚,经脱除催化剂和低挥发分即得硅生胶。
橡胶加工时,先加入结构控制剂(二苯基甲硅二醇)和补强填料(气相法二氧化硅)、抗氧剂(三氧化二铁)等,再在炼胶机上混炼,经高温(约200℃)处理后加有机过氧化物(2,5-二甲基-2,5-二叔丁基过氧化己烷)作硫化剂。
混炼胶入模后要加温、加压。
制品出模后有的还要后硫化。
混炼胶可挤成管、条、包覆电线电缆。
硅橡胶与氟橡胶共混胶的介电性能研究

温度 时 , 小 。硅 橡 胶 和 氟 橡 胶 的共 混 胶 会 8减 出现 两种 弹性 体相 的介 电松 弛特征 。纯氟橡 胶
具 有最 高 的 C“一 偶 极 密 度 , 显 示 出 最 大 F 并 的介 电松弛 强度 ( g 低温 非 松 驰介 电常数 与 T 时 松 驰介 电常数之 差 ) 。随 着 氟 橡胶 在 共 混 胶 中
生。
关 键 词 : 硅 橡胶 与 氟橡 胶 共 混 胶 ; 电性 能 ;共 混 介
中 图分 类 号 : Q 3 3 9 T 3 .3 文 献 标 识 码 : B 文章 编 号 :6 1 2 2 2 1 ) 30 1 -5 1 7 — 3 ( 0 0 0 - 40 8 0
值得 一 提 的是 , 里 的硅橡 胶 和 氟橡 胶都 是 用 这
0 前 言
以四氟 乙烯/ 丙烯/ , 1 1二 氟 乙烯三 元共 聚
过氧化物 进行 硫化 的 。
在 电气设 备 中用 作绝 缘材料 的聚 合物和 聚 合 物混炼 胶 , 直被认 为具 有较大 的应用 前景 , 一
物 为基料 的氟橡 胶可作 为一种 特种 聚合物 用于 各种 场 合 , 密封 圈 、 如 O形 圈 、 管 、 管 和 电 胶 软 缆 。但 这种 材料有 一大缺 点 , 即耐 低温性 较差 。 将氟橡 胶 与 硅橡 胶 进行 共混 , 可提 高其 耐 低温 性 能 。硅 橡胶本 身作 为介 电材料 可用于 高温 电 缆 。之前 的资料 显 示 … , 橡胶 和 氟橡 胶 的共 硅
起 的韧 性 产生 之 缘 故 ; 且 在 一2 C ~0℃ 范 并 5o 围 内发生 了尖 窄 的 O转 变 , 归 因 于 其相 对 刚 L 这 性 以及 含 1 1 氟 乙烯链 段 的极性 氟化 物发 生 ,二
硅橡胶及硫化剂知识
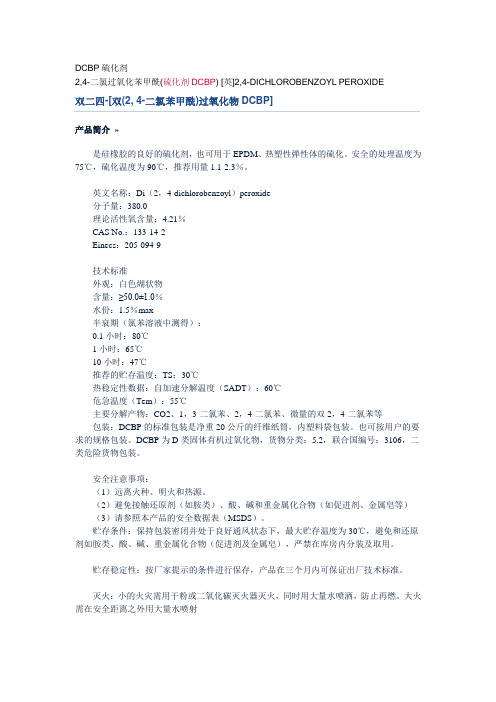
DCBP硫化剂2,4-二氯过氧化苯甲酰(硫化剂DCBP) [英]2,4-DICHLOROBENZOYL PEROXIDE双二四-[双(2, 4-二氯苯甲酰)过氧化物DCBP]产品简介»是硅橡胶的良好的硫化剂,也可用于EPDM、热塑性弹性体的硫化。
安全的处理温度为75℃,硫化温度为90℃,推荐用量1.1-2.3%。
英文名称:Di(2,4-dichlorobenzoyl)peroxide分子量:380.0理论活性氧含量:4.21%CAS No.:133-14-2Einecs:205-094-9技术标准外观:白色煳状物含量:≥50.0±1.0%水份:1.5%max半衰期(氯苯溶液中测得):0.1小时:80℃1小时:65℃10小时:47℃推荐的贮存温度:TS:30℃热稳定性数据:自加速分解温度(SADT):60℃危急温度(Tem):55℃主要分解产物:CO2、1,3-二氯苯、2,4-二氯苯、微量的双2,4-二氯苯等包装:DCBP的标准包装是净重20公斤的纤维纸筒,内塑料袋包装。
也可按用户的要求的规格包装。
DCBP为D类固体有机过氧化物,货物分类:5.2,联合国编号:3106,二类危险货物包装。
安全注意事项:(1)远离火种、明火和热源。
(2)避免接触还原剂(如胺类)、酸、碱和重金属化合物(如促进剂、金属皂等)(3)请参照本产品的安全数据表(MSDS)。
贮存条件:保持包装密闭并处于良好通风状态下,最大贮存温度为30℃,避免和还原剂如胺类、酸、碱、重金属化合物(促进剂及金属皂),严禁在库房内分装及取用。
贮存稳定性:按厂家提示的条件进行保存,产品在三个月内可保证出厂技术标准。
灭火:小的火灾需用干粉或二氧化碳灭火器灭火,同时用大量水喷洒,防止再燃。
大火需在安全距离之外用大量水喷射DTBP(引发剂A)(TPA )化学名过氧化二叔丁基 CAS-No 110-05-4C 8H 18O 2=146.22• 安全数据闪点..................开口18℃、闭口12℃ 自加速分解温度(SADT) ..................80℃ 报警温度(Tem) ..............................75℃ 联合国编号(UN-No ) .....................3107 中国危险化学品编号(CN-No ) (52026)• 理化特性状态………………………………………液态 比重()………………………………~0.8折光指数()…………………………~1.39熔点………………………………………-40℃ 沸点………………………………………111℃ 理论活性氧含量…………………………10.94%• 主要质量指标外观…………………………浅黄色透明液体 含量…………………………Min.98.5% 色度…………………………Max.60黑曾 Fe…………………………Max.0.0003%二叔丁基过氧化物(DTBP)98%MIN化学名:过氧化二叔丁基Cas NO. 110-05-4结构式:用途:DTBP为挥发性、微黄色透明液体,是一种二烷基有机过氧化物。
液体硅橡胶热炼工序稀释原理

液体硅橡胶热炼工序稀释原理
液体硅橡胶热炼工序中的稀释是指通过加入一定比例的溶剂或稀释剂,将硅橡胶的粘稠度降低,使其更容易操作和加工。
具体的稀释原理如下:
1. 溶剂选择:选择适合的溶剂或稀释剂是关键。
一般选用有机溶剂,如烷烃类、芳香烃类或醚类溶剂。
溶剂的选择要考虑与硅橡胶相溶性好、挥发性适中、对硅橡胶性能影响较小等特性。
2. 溶剂加入:将选用的溶剂或稀释剂逐渐加入硅橡胶中,同时进行机械搅拌或搅拌加热,并保持一定的时间,使溶剂与硅橡胶充分混合。
3. 扩散和溶胀作用:加入溶剂后,溶剂会扩散到硅橡胶分子链中,发生相互作用。
一方面,溶剂可以在硅橡胶中进行溶胀,使硅橡胶分子间的距离增加,从而降低了粘度;另一方面,溶剂也可以在硅橡胶分子链上发生物理或化学吸附,改变硅橡胶的相互作用力,降低其粘稠度。
4. 溶剂挥发:在热炼过程中,溶剂会随着高温下的蒸发挥发。
通过适当的炼胶温度和时间控制,使溶剂充分挥发,留下经稀释后的硅橡胶。
通过稀释作用,液体硅橡胶在热炼工序中的粘稠度得到降低,从而更容易操作和加工。
稀释后的硅橡胶可以有效地改善其流动性、降低黏度,便于在后续的成型、注射或涂覆等工艺中使用。
硅橡胶存在问题及发展建议

硅橡胶存在问题及发展建议
1)热硫化硅橡胶
世界上发达国家的硅橡胶的产量及消费量都已达到了很高的水平,而且发展十分迅速。
虽然我国近几年来在HTV的生产技术和生产能力方面有了很大的提高,并且已有一些硅橡胶的生产技术和产品进入了国际市场。
但全面地讲,我国的硅橡胶工业与国际先进水平相比,仍有不小的差距。
因此,开发和建立较大的具有经济规模的热硫化硅橡胶生胶及混炼胶装置,开发混炼胶系列品种特别是高品质品种,对于改变我国混炼胶在产量和品种上都要依赖国外的现状,促进我国有机硅及其相关行业技术进步有着十分重要的意义。
2)室温硫化硅橡胶
以单组份密封胶为例,由于无序的市场竞争,大多数生产厂家为了降低成本,采用价格较低的回收料作为主要原料,所采用的交联剂也大多为一些小厂的产品,质量不稳定,从而造成最终产品的整体质量下降,性能受到影响。
高性能的密封胶主要还是使用的进口和进口分装产品,如幕墙用的结构胶以及耐候胶等。
这些都是今后应该注意解决的问题。
高性能建筑密封胶和加成型硅橡胶是研发热点。
建筑密封胶着重是提高表干时间和硫化时间,及与基材的粘接性,尤其是与浇筑混凝土的粘接性。
同时应实现连续化生产,克服间歇式配胶工艺存在的生产稳定性较差,损耗较大,功效不高等缺点。
加成型硅橡胶主要是提高其柔软性和透明度,还有就是开发单组分加成型硅橡胶。
用于其他特种用途的硅橡胶,如阻燃硅橡胶灌封料、高阻尼硅橡胶、高耐蚀高抗撕硅橡胶、抗电磁干扰硅橡胶、耐高温(350℃以上)硅橡胶等,虽然总的需求量不是很大,但对我国的国防建设和尖端科技以及国民经济的发展都有着不可替代的作用,这些也需要我们下大力气去开发研究。
- 1、下载文档前请自行甄别文档内容的完整性,平台不提供额外的编辑、内容补充、找答案等附加服务。
- 2、"仅部分预览"的文档,不可在线预览部分如存在完整性等问题,可反馈申请退款(可完整预览的文档不适用该条件!)。
- 3、如文档侵犯您的权益,请联系客服反馈,我们会尽快为您处理(人工客服工作时间:9:00-18:30)。
硅橡胶混炼胶的加工工艺——linjing2011/3/16 热硫化硅橡胶是有机硅产品中产量大,应用十分广泛的一类产品。
硅橡胶具有优良的耐高低温性能,可在-60~250℃范围内长期使用,并且还有优良的电气绝缘性能,能耐臭氧、耐气候老化,憎水、防潮,并有良好的生理惰性。
在热硫化硅橡胶生胶中加入补强填料、硫化剂(或先不加)及其它助剂,经混炼即成混炼胶,可用模压、挤出等一般橡胶加工方法加工成各种硅橡胶制品。
混炼硅橡胶一般可在通用型橡胶开炼机上配制,大规模生产则在捏合机或密闭式混炼设备中进行。
以下是基本配合工艺:硅橡胶生胶:聚合度5000~10000 乙烯基0.03%~0.15%;填料:气相法白炭黑、沉淀法白炭黑、硅藻土、石英粉等;浸润剂(结构化控制剂):末端反应性基团的(聚)硅氧烷;混炼设备:密闭混炼机、双辊机、捏合机等;热处理工艺:150~180℃下1~2h;过滤网:100~250 目不锈钢网。
【生胶制备混炼胶】硅橡胶生胶→白炭黑+结构控制剂+加工助剂→倒胶、混炼(开炼机则薄通至混匀)→热处理→过滤出胶【硅橡胶成型】混炼胶返炼+交联剂等→薄通(8~10次)→挤出或压片、硫化成型→二次硫化→成品各工艺详细说明:1、混炼:当采用开炼机混炼时,最好在开炼机辊筒上方装备防尘或抽风装置,以减少白炭黑的飞扬。
在混炼过程中不得有其他杂质或胶粒混入,温度应控制在40℃以下,开足冷却水。
开炼机混炼吃粉较慢,每批胶料的混炼时间约在20~40min之间。
采用密炼机混炼,不但可以提高生产效率、降低劳动强度,而且还能够减少白炭黑的飞扬和改善操作环境。
密炼机混炼的操作顺序基本与开炼机相似,但对间隔时间的要求并不严格。
每批胶料的混炼时间约为8~18min,密炼机的填充系数应控制在0.7~0.75的范围较为适宜。
排胶温度与填料种类有关,通常应控制在50℃~70℃的范围。
2、热处理:当采用未经表面改性的气相法白炭黑作为补强剂时,胶料中必须加入结构控制剂。
因此,胶料的热处理也就成为一道必需的工序。
热处理的目的主要在于:使结构控制剂与白炭黑表面(Si-OH)进一步结合,并消除胶中低分子挥发物。
一般的热处理的条件为:在氮气保护下或减压的捏合机中160℃~200℃处理1~1.5h。
3、过滤:对挤出制品、压延制品、涂胶制品、膜片制品来讲,机械杂质和未分散的配合剂粒子是导致产品出现质量问题的主要因素之一。
因此,对上述制品所用的胶料必须进行过滤。
过滤时可采用滤胶机,也可用普通挤出机替代。
机筒、螺杆的温度应控制到最低,滤网规格以120~200目为宜。
4、返炼:胶料经停放后,因凝胶含量增加、可塑性降低,所以使用时必须进行返炼。
胶料返炼应适可而止,返炼不足,胶料柔软性差,表面不平整;而返炼过度,则胶料表面会发粘,不利于操作。
混炼胶的组成与硫化硅橡胶的特性——linjing2011/3/161、生胶:硅橡胶生胶种类有:二甲基硅橡胶(简称甲基硅橡胶)、甲基乙烯基硅橡胶(简称乙烯基硅橡胶)、甲基苯基乙烯基硅橡胶(简称苯基硅橡胶)以及氟硅、腈硅橡胶等。
热硫化硅橡胶绝大部分使用的是甲基乙烯基硅橡胶,特别是生胶分子链末端用乙烯基二甲基硅氧烷(乙烯基双封头)链节封端的类型为市场主要产品类型。
表:生胶中乙烯基含量与所适应的胶料品种表:乙烯基硅橡胶的可使用温度与时间(连续不间断)表:(端)二乙烯基聚二甲基硅氧烷摩尔质量与粘度的关系经验数据乙烯基的质量分数与摩尔质量的关系可用下列式换算:摩尔质量=54×100÷乙烯基质量分数市售的乙烯基生胶一般为110甲基乙烯基硅橡胶,按其乙烯基含量不同分为110-1,110-2和110-3三种型号。
每种型号按分子量大小又分为A和B两种牌号。
表:110甲基乙烯基硅橡胶的理化性能备注:好的生胶分子量分布在±10万以内,且催化剂残留低。
相关的项目指标可以根据Q/SC 30-1998《110甲基乙烯基硅橡胶》、行标HG/T 3312-2000《110甲基乙烯基硅橡胶》进行检测。
生胶的粘度对于硫化硅橡胶的性能有一定的影响,生胶的粘度越小,分子量越小,(端)乙烯基含量越高。
低粘度的乙烯基硅油其乙烯基含量较高,交联点增加,使得交联的密度大,从而可以使硅橡胶的硬度得到提高;而随着生胶粘度的增加,乙烯基含量减少,交联点密度降低,硫化之后的橡胶硬度减小,但趋势渐减慢。
刚开始随着生胶粘度的增加,硅橡胶分子量增大,其分子链增长,分子链缠绕程度增强,硫化后的硅橡胶的撕裂强度、伸长率增加而到峰值;同时分子链缠结程度提高使其相互滑动的可能性减小,硫化后的硅橡胶的撕裂强度、永久变形小幅上升后减小。
但当生胶粘度继续增加时,乙烯基含量减少,交联点减少,使得交联的密度降低,从而导致硫化硅橡胶的撕裂强度、伸长率和拉伸强度都下降,最终趋于稳定值。
邵氏硬度动力粘度动力粘度拉伸强度撕裂强度伸长率伸 长 率 拉伸强度 撕裂强度2、填料:添加填料可以提高硅橡胶的机械性能,填料用量对硅橡胶的电学性能及机械性能的影响比较大。
填料一般为无机物质,主要有白炭黑、二氧化钛、石英粉、高岭土、微粉化的滑石以及沉淀碳酸钙等等。
硅橡胶中使用的增强填料主要是白炭黑,包括气相法和沉淀法白炭黑。
硅橡胶生胶由于分子间内聚能密度低,硫化胶的拉伸强度只有0.35MPa左右,几乎无使用价值,需要用气相法或沉淀法白炭黑进行补强来提高硫化硅橡胶机械性能。
随着白炭黑用量的增加,硫化后的硅橡胶的撕裂和拉伸强度都增加,硬度逐渐增加而后减小,而体积电阻率逐渐减小。
由于有机硅化合物本身具有良好的绝缘性,填料的加入会对分子链造成影响,使得硫化后的硅橡胶电阻率下降。
但是由于填料有补强效果,从而可以提高硅橡胶的机械性能,使得硅橡胶的硬度提高,不过若填料加入过多,会影响到聚合物分子链间的交联,使得硅橡胶的硬度反而降低。
刚开始随着填料用量的增加,硫化胶的伸长率有较大提高,同时撕裂强度和拉伸强度也缓慢增加;而当填料用量过多时,使生胶分子间“隔离”较远,从而影响到聚合物分子链间的交联,机械性能反而下降。
研究表明填料用量高于26份后,拉伸强度出现下降的趋势。
兼顾硫化后硅橡胶的各项性能以及成本等因素,一般白炭黑的用量以30份左右(百分比%)为宜。
3、结构控制剂采用气相白发黑补强的硅橡胶胶料贮放过程中会变硬,降低可塑性,从而逐渐失去加工工艺性能,这种现象称作“结构化”效应。
实验表明,胶料的硬化程度与白炭黑的比表面积及白炭黑表面的隔离羟基有关。
究其原因:由于白炭黑粒子的比表面积大且表面含大量Si-OH基(粒子间的凝聚力相当强,容易团聚而使其在硅橡胶生胶中分散困难,不利于补强),活性Si-OH基及其吸附水在常温下与生胶分子末端的硅羟基及残留烷氧基发生缩合反应,某些活性羟基还能与硅橡胶分子链形成氢键型的化学吸附,而形成立体网络结构。
为防止和减弱这种“结构化”倾向而加入的配合剂,称为“结构控制剂”。
结构控制剂能防止或延缓结构化作用,是由于这些物质的活性基团与白炭黑表面的活性羟基发生缩合反应,从而防止了白炭黑和生胶之间的作用。
通常可采取处理补强填料白炭黑和混炼时添加结构化控制剂两种方法。
但处理白炭黑的成本太高,现在大多采用混炼时添加结构化控制剂就地处理白炭黑的办法。
加入适宜的结构化控制剂不仅解决了硅橡胶混炼胶的加工性和贮存稳定性,也可明显改善混炼胶的抗撕、伸长率、流变性等综合性能,而且可以在保证硫化胶的性能的情况下增加填料的用量从而降低成本。
结构控制剂通常为含Si-OH、Si-NH-Si或含硼原子的低分子有机硅化合物。
可归纳为以下四类::(1) 含羟基硅烷类凡羟基含量越高,则活性越大,抗结构化效果必然越好;(2) 烷氧基硅烷类包括各种烷氧基硅烷和低分子聚硅氧烷;(3) 硅氨(氮)烷类此类结构控制剂比较高效,价格较高,有气味,需要热处理除去;(4) 含硼硅氧烷类由硼酸和各类氯硅烷缩合而成,其特点是有效期可长达6个月以上。
目前使用最普遍的抗结构剂为(端)二羟基低聚二甲基硅氧烷,即低分子羟基硅油。
羟基含量是其主要性能指标,羟基含量越高,抗结构性越好,用量越少。
使用羟基硅油作结构化控制剂具有抗结构性好,使用方便,所得的混炼胶透明等优点,但是存在着功能单一,稳定性差(常伴随脱水缩台反应),用量较大,易使胶料发粘,加热或硫化成型时有臭味,用量稍多就会降低扯断强度、加大扯断永久变形和回弹性等问题。
除羟基硅油外,二苯基硅二醇、甲基苯基二乙氧基硅烷、四甲基乙撑二氧二甲基硅烷及硅氮烷(六甲基二硅氮烷和六甲基环三硅氮烷与八甲基环四硅氮烷的混合物)等也可以用作抗结构剂,其中二苯基二羟基硅烷还能提高混炼胶的物理机械性能和耐热老化性能,特别是高温下的永久变形较小。
其余结构控制剂的功能都较单一。
但二苯基硅二醇为固体结晶状物质,其用量一般为气相白炭黑用量的5~10%。
采用二苯基硅二醇的胶料在混炼后(加入硫化剂之前),必须进行热处理(160~200℃×0.5~1h)才能迅速和充分地发挥其结构控制作用,使用起来不方便。
而且其制品透明度方面不及羟基硅油。
其他的结构控制剂均为液体,使用时胶料可不需进行热处理(除硅氮烷,采用硅氮烷的胶料也应进行热处理,以增强它的结构控制作用,使胶料中的氨气能挥发完全。
热处理条件一般为180~200℃×lh),混炼停放2~3天后,胶料可塑性即明显增加。
有些结构控制剂有延迟硫化作用,使用时应适当增加硫化剂的用量。
结构控制剂的用量与其本身的活性以及白炭黑的类型、胶料所需的性能有关,当胶料中采用比表面积较大的气相白炭黑时,结构控制剂的用量应适当的增加,或最好采用活性较高的结构控制剂,如硅氮烷。
采用两种结构控制剂复配的方法较采用某一种结构控制剂的效果更好。
如:羟基硅油+硅氮烷,二苯基硅二醇+硅氮烷等等。
另外特殊的:氟硅橡胶所使用的结构控制剂应均为含氟的低分子有机硅化合物,如羟基氟硅油和含氟硅氮烷等,这样才不致于使硫化胶的耐溶剂性和耐油性能下降。
4、脱模剂分内、外脱模剂。
大部分内脱模剂会降低混炼胶的透明度,可在返炼薄通时加入。
——linjing2011/3/17。