企业风险评价一览表
企业风险评价(LEC法)一览表.doc

危险源辨识、风险评价(LEC 法)一览表作业条件危险性评价(LEC)作业判别序号危险源(危害因素)可能的事故、后果风险控制措施活动依据L E C D级别培训不到位人员伤害 D 3 2 15 90 3电线破损老化触电 D 1 2 15 30 2无漏电保护器 D 3 2 15 90 3外壳带电 D 1 2 15 30 2未穿戴防护服 D 3 2 15 90 3 执行培训管理程序、安全技术操作规1 电焊作业焊钳绝缘不好 D 1 2 15 30 2 程、电焊气焊作业指导书,加强监督操作场所附近有易燃物火灾 D 3 1 15 45 2 管理焊接时无防火措施 D 3 1 15 45 2焊接时产生弧光眼睛伤害 D 3 2 3 18 1焊接时产生有毒气体中毒 D 1 2 3 6 1电焊火花烫伤 D 6 2 3 36 2 不可容许风险111培训不到位 D 3 2 15 90 3 执行安全技术操作规程、培训管理程 1 手工气焊2 人员伤害序、电焊气焊作业指导书,加强监督(割)作业直接在水泥地面上切割 D 3 2 3 18 1 0管理焊(割)炬操作时回火 D 3 6 3 54 2 0停止作业后焊(割)炬未关严 D 3 3 7 63 2 0执行安全技术操作规程、培训管理程手工气焊氧气、乙炔皮管老化 D 3 6 7 126 3 1 2 火灾序、电焊气焊作业指导书,加强监督(割)作业焊(割)炬各阀门密封不严 D 3 6 3 54 2 0管理操作场所附近有易燃物 D 3 1 15 45 2 0焊接时无防火措施 D 3 1 15 45 2 0人员伤亡 D 3 2 15 90 3 执行培训管理程序、起重搬运安全作 1 培训不到位设备损坏 D 3 1 15 45 2 业指导书,并加强监督管理0物体砸人 D 10 1 1 10 1 严禁超高作业、佩戴安全防护用品,0 超高作业3 叉车作业物体损坏 D 10 1 1 10 1 设专人指挥0超负荷作业叉车及物体损坏 D 10 1 1 10 1 严禁超负荷工作、禁止叉车带人、佩0叉车带人人员伤害 D 3 2 7 42 2 戴安全防护用品、设专人指挥,加强0作业时前叉附近有人人员伤害 D 3 2 7 42 2 监督管理04行车作业5高空作业6剪板机操作人员伤亡 D 3 2 15 90 3 1 培训不到位特制并实施特种设备管理办法、执行设备损坏 D 3 115 45 2 0未及时联系检验 D 1 615 90 3培训管理程序、起重搬运安全作业指1 限位开关失灵 D 1 6 15 90 3导书,并加强监督管理1 歪拉斜吊 D 1 615 90 3 1 起吊重物的绳索不符合安全要求 D 1 6 15 90 3制定并实施特种设备管理办法、执行1起重伤害培训管理程序、起重搬运安全作业指起吊作业完成后吊钩未升至安全高度 D 3 3 3 27 2导书,并加强监督管理0 行车零件坠落 D 1 6 15 90 3 1 升降机构打滑 D 1 6 15 90 3 1坠物伤人 D 3 3 3 27 2 提高警惕、集中工作注意力0 物体坠落损坏设备 D 3 1 7 21 2 使用登高工具0 未使用登高工具人员摔伤 D 3 3 7 63 2 使用登高工具0 剪、压脚踏开关无护罩 D 3 6 3 54 2 0剪板机剪压区无防护栏、网 D 3 6 3 54 2 执行设备安全技术操作规程,并加强0机械伤害剪、压机床离合器缺陷 D 3 6 3 54 2 监督管理,加强安全意识培训0 剪、压机床制动器与离合器协调失误 D 3 6 7 126 3 1未正确使用辅助工具 D 3 6 7 126 3闭式压力机登高维修保养,安全防护栏高处坠落 D 3 2 15 90 3 等装置不符要求剪、压机械 PE 连接缺损触电危险 D 6 15 90 3剪压上料、落料噪声职业危害 D 6 6 3 108 3剪压机作业未使用按钮站 D 1 6 15 90 3机械伤害刀板松动 D 1 6 15 90 3未定期更换机油 D 3 1 1 3 1培训不到位 D 3 1 3 9 1 7 折弯机操作机械伤害发生异常未立即停机检查处理 D 3 2 15 90 3机床后部站人 D 1 2 15 30 2板料折弯时未压牢固 D 6 2 15 180 47 折弯机操作未停车校正工件和模具机械伤害 D 6 1 15 105 3未佩戴安全防护用品 D 1 2 3 6 1站在砂轮机的正前方操作 D 3 6 3 54 2 8 砂轮机操作机械伤害未定期更换砂轮片 D 3 6 7 126 21111110 执行安全技术操作规程,并加强监督0 管理 11 执行安全技术操作规程,并加强监督1 管理0 执行安全技术操作规程,并加强监督0 管理0未戴防护眼镜 D 6 6 3 108 3打磨细小的、大的和不好拿的工件 D 3 6 7 126 2砂轮受潮、沾水后继续使用 D 3 6 3 54 2砂轮磨损严重或径向跳动过大、震动大D 1 6 3 18 1时继续使用高速切削时未装防护挡板 D 6 6 3 108 3操作者未戴防护眼镜 D 6 6 3 108 3戴手套操作 C9 铣床操作拆装立铣刀时,用手托刀盘机械伤害 D 3 6 3 54 2拆掉限位块加工超长、超宽零件 D 3 3 3 27 2快速进刀时,左手远离手柄 D 1 6 2 12 1未停车测量、取卸工件 D 3 3 7 63 2高速切削时未戴防护眼镜 D 6 6 3 108 3工件未夹紧 D 1 6 7 42 210 车床操作用砂布光内孔时,将手指或手臂伸进工机械伤害D 1 6 7 42 2件打磨切断小料时用手接 D 3 6 3 54 21111 执行安全技术操作规程,并加强监督0 管理10 执行安全技术操作规程,并加强监督管理0戴手套操作 C 1执行安全技术操作规程,并加强监督10 车床操作切大料时直接切断机械伤害 D 1 6 3 18 1 0管理一手扶攻丝架(后扳牙架)一手开车 D 3 6 3 54 2 0用手扶工件 D 3 3 7 63 2 0用手清除铁屑 D 6 3 1 18 1执行安全技术操作规程、机械加工安11 钻床操作戴手套操作机械伤害C 1全作业指导书,加强监督管理在旋转的刀具下,翻转、卡压或测量工D 3 3 7 63 2 0件安装刀具时紧固螺钉和销子凸出镗杆损坏工件 D 1 1 7 7 1 0 回转半径戴手套操作 C 1机床开动时,量尺寸、对样板 D 3 3 7 63 2 执行安全技术操作规程,并加强监督0 12 镗床操作镗孔、扩孔时将头贴近加工孔观察吃刀机械伤害管理D 3 3 7 63 2 0情况使用平旋刀盘式自制刀盘进行切削时,D 3 3 7 63 2 0站在对面或伸头察看干磨或修砂轮时,未戴防护眼镜 D 6 6 3 108 3 执行安全技术操作规程,并加强监督 1 13 磨床操作机械伤害操作者站在砂轮的正面 D 3 3 3 27 2 管理0吃刀量过大,砂轮破裂飞出 D 3 3 3 27 2 0使用有缺陷的砂轮 D 3 6 7 126 3 1砂轮未退到安全位置时,测量、装卸工D 3 3 7 63 2 0件14 刨床操作工件装夹不牢固机械伤害 D 3 3 7 63 2 执行安全技术操作规程,并加强监督0未停车调整行车挡铁 D 3 3 7 63 2 0 14 刨床操作未停车测量工件、清扫铁削机械伤害 D 6 3 7 126 3 管理 1工作台行程范围内有人员活动 D 3 3 7 63 2 0离合器不完好连车或滑车造成挤压伤 D 6 3 7 126 3 1操作面板指示信号错误导致设备事故机械伤害 D 1 7 1 0 或人员伤害急停装置失灵造成压伤 D 3 1 7 21 2 定期检查,遵守操作规程等各项规定,015 冲压操作设备电线裸露导致设备故障或人员伤培训后上岗,佩带好防护用品,杜绝D 1 1 15 15 1 0害触电违章作业。
危险源识别与风险评价结果一览表33
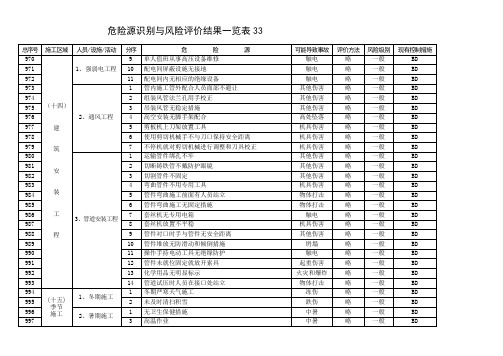
1
管内施工管外配合人员面部不避让
其他伤害
略
一般
BD
974
2
组装风管法兰孔用手校正
其他伤害
略
一般
BD
975
3
吊装风管无稳定措施
其他伤害
略
一般
BD
976
4
高空安装无脚手架配合
高处坠落
略
一般
BD
977
5
剪板机上刀架放置工具
机具伤害
略
一般
BD
978
6
使用剪切机械手不与刀口保持安全距离
机具伤害
略
一般
BD
979
985
6
管件弯曲施工无固定措施
物体打击
略
一般
BD
986
7
套丝机无专用电箱
触电
略
一般
BD
987
8
套丝机放置不平稳
机具伤害
略
一般
BD
988
9
管件对口时手与管件无安全距离
其他伤害
略
一般
BD
989
10
管件堆放无防滑动和倾倒措施
坍塌
略
一般
BD
990
11
操作手持电动工具无绝缘防护
触电
略
一般
BD
991
12
管件未就位固定就放开索具
起重伤害
略
一般
BD
992
13
化学用品无明显标示
火灾和爆炸
略
一般
BD
企业风险评价

第八条
符合
重大危险源安全评估与安全验收评价一起进行,以安全验收评价报告代替安全评估报告,确认重大危险源等级为三级。
3
危险化学品单位是本单位重大危险源安全管理的责任主体,其主要负责人对本单位的重大危险源安全管理工ห้องสมุดไป่ตู้负责,并保证重大危险源安全生产所必需的安全投入。
不涉及
不属于新开发工艺
11
国内首次使用的化工工艺,必须经过省级人民政府有关部门组织的安全可靠性论证;
不涉及
不属于首次使用工艺
12
涉及危险化工工艺、重点监管危险化学品的装置装设自动化控制系统;
《危险化学品生产企业安全许可证实施办法》
第9.3条
符合
13
涉及危险化工工艺的大型化工装置装设紧急停车系统;
不涉及
符合
应急预案中已明确
35
生产、储存和使用氯气、氨气、光气、硫化氢等吸入性有毒有害气体的企业,除符合本条第一款的规定外,还应当配备至少两套以上全封闭防化服;构成重大危险源的,还应当设立气体防护站(组)。
《危险化学品生产企业安全许可证实施办法》
第21.2条
不涉及
不生产、储存和使用氯气、光气、硫化氢
表2 重大危险源安全管理及安全生产条件
《危险化学品重大危险源监督管理暂行规定》(国家安全生产监督管理总局第40号令)
第四条
符合
主要负责人对本单位的重大危险源安全管理工作负责,并保证重大危险源安全生产所必需的安全投入
4
重大危险源有下列情形之一的,应当委托具有相应资质的安全评价机构,按照有关标准的规定采用定量风险评价方法进行安全评估,确定个人和社会风险值:
企业危险源辨识和风险评价表(新)

企业危险源辨识和风险评价表(新) 企业安全危险源辨识和风险评价表单位:序号岗位或工序危险源伤害后果风险级别控制措施1 办公设备不按规定插插座触电 4 按操作规程进行规范2 办公设备电源线老化、破损漏电电人、火灾3 管理制度/应急预案3 上下班路上行车交通事故人员伤害、人员摔伤4 遵守交通守则,注意自身保护。
4 拖地地面湿滑人员摔伤5 设置临时警示5 吃饭食物不干净、腐蚀变质食物中毒 5 加强自我防范6 办公场所财产被盗财产损失 4 上下班注意锁门。
7 吸烟烟头乱丢火灾 3 管理制度/应急预案8 使用空调电线短路火灾 4 使用前检查9 使用空调空调氟立昂泄露致病 5 使用前检查10 复印、打印作业环境不良,废气的排放职业病 5 保持室内通风11 使用电脑电脑辐射职业病 4 增强防护意识,合理安排使用时间。
12 因公外出工作交通事故隐患、突发事件 4 提高安全防护意识。
13 外来人员管理不严 4 按规定现场检查把关15 锅炉违章作业 3 按规定现场检查把关16 下料过程违章作业、设备失灵 3 管理制度/应急预案18 倒坡口过程违章作业、设备失灵 3 管理制度/应急预案19 卷园、折弯过程违章作业、设备失灵 3 管理制度/应急预案20 起重设备违反操作规程。
起重伤害机械伤害 3 按规定佩戴防护用品21 机加工违章作业机械伤害 4 按规定进行检查把关22 防护不当机械伤害 3 管理制度/应急预案23 砂轮使用机械伤害 4 按规定进行检查把关24 起重伤害物体打击 4 管理制度/应急预案25 物体打击物体打击 3 管理制度/应急预案26 切割过程起重设备违反操作规程。
起重伤害 4 管理制度/应急预案27 违章作业、设备失灵机械伤害 3 管理制度/应急预案28 起重设备违反操作规程。
起重伤害物体打击 4 按规定佩戴防护用品29 材料搬运物体打击 4 按规定佩戴防护用品30 物理灼伤物理灼伤 3 管理制度/应急预案31 物理灼伤物理灼伤 3 管理制度/应急预案32 起重设备违反操作规程。
服装企业危险源辨识与风险评价信息一览表

3、每月对设备进行保养、
4、每周对设备完好情况进行检查;
5、配发高温防护手套;
位员工人走机关;
4、每月定期利用班前会进行安全教育培训;
7、每天打扫机台卫生;
8、定期检查空压气管;
9、定期清理电控箱;
3、加强机台用电管理,做到每位员工人走机关;
4、每月定期利用班前会进行安
2、增设高温提示标识;
3、定期组织设备检查;
8、定期检查空压气管;9、增设警示标语;
10、高处作业设置安全防护设
2、定期组织相关培训,提高操作技能;
3、定期组织操作工安全培训,提高安全意识和技能;
2、使用机器时首先检查设备的
完好性;
4、空压机定期保养维护;
5、空压机周围保持通道通畅
4、定期组织配电室线路检查;
5、增设防鼠板;
6、定期组织安全培训,提高操作人员的安全技能。
危险源识别与风险评价结果一览表4

略
一般
BD
93
5
易燃易爆仓库无良好的通风条件,且仓库照明等电气设备不符合防火规定
火灾/爆炸
略
一般
BD
94
6
氧气瓶、乙炔瓶平放卧倒
火灾/爆炸
略
一般
BD
95
7
氧气瓶、乙炔瓶暴晒
火灾/爆炸
略
一般
BD
96
8
各种气瓶无标准色标
爆炸
略
一般
BD
97
9
气瓶无防振圈和防护帽
爆炸
略
一般
BD
98
10
氧气、乙炔气管混用
爆炸
略
一般
BD
99
7、材料堆码放
1
建筑材料码放不整、超高
坍塌
略
一般
BD
100
2
楼层物料不按规定堆放
物体打击
略
一般
BD
101
3
存放物料未按规定靠墙码放或堆放
倒塌/物体打击
略
一般
BD
102
(四)
高处作业
1、三宝四口及临边防护
1
安全帽、网、带未进行定期检查
高处坠落
略
一般
BD
103
2
安全网规格材质不合要求
高处坠落
危险源识别与风险评价结果一览表4
总序号
施工区域
人员/设施/活动
分序
危 险 源
可能导致事故
评价方法
风险级别
现有控制措施
79
(三)
施
工
全
过
程
4、电焊气焊
割施工
企业风险评价(LEC法)一览表
作业序号活动1 电焊作业危(wei)险源(危害因素)培训不到位电线破损老化无漏电保护器外壳带电未穿戴防护服焊钳绝缘不好操作场所附近有易燃物焊接时无防火措施焊接时产生弧光焊接时产生有毒气体电焊火花可能的事故、后果人员伤害触电火灾眼睛伤害中毒烫伤判别依据DDDDDDDDDDD作业条件危(wei)险性评价(LEC)不可容风险控制措施L E C D 许风险级别3 2 15 90 3 11 2 15 30 2 03 2 15 90 3 11 2 15 30 2 03 2 15 90 3 执行培训管理程序、安全技术操作规11 2 15 30 2 程、电焊气焊作业指导书,加强监督 03 1 15 45 2 管理03 1 15 45 2 03 2 3 18 1 01 2 3 6 1 06 2 3 36 2 0培训不到位手工气焊2(割)作业直接在水泥地面上切割焊(割)炬操作时回火住手作业后焊(割)炬未关严手工气焊氧气、乙炔皮管老化2(割)作业焊(割)炬各阀门密封不严操作场所附近有易燃物焊接时无防火措施培训不到位超高作业3 叉车作业超负荷作业叉车带人作业时前叉附近有人人员伤害火灾人员伤亡设备损坏物体砸人物体损坏叉车及物体损坏人员伤害人员伤害DDDDDDDDDDDDDDD333333333310101033226366112111122153377315151515111779018546312654454590451010104242312232223211122执行安全技术操作规程、培训管理程序、电焊气焊作业指导书,加强监督管理执行安全技术操作规程、培训管理程序、电焊气焊作业指导书,加强监督管理执行培训管理程序、起重搬运安全作业指导书,并加强监督管理严禁超高作业、佩戴安全防护用品,设专人指挥严禁超负荷工作、禁止叉车带人、佩戴安全防护用品、设专人指挥,加强监督管理1114 5 6 行车作业高空作业剪板机操作培训不到位未及时联系检验限位开关失灵歪拉斜吊起吊重物的绳索不符合安全要求起吊作业完成后吊钩未升至安全高度行车零件坠落升降机构打滑物体坠落未使用登高工具剪、压脚踏开关无护罩剪板机剪压区无防护栏、网剪、压机床离合器缺陷剪、压机床制动器与离合器协调失误人员伤亡设备损坏起重伤害坠物伤人损坏设备人员摔伤机械伤害DDDDDDDDDDDDDDDD331111311333333321666636631366661515151515153151537733379045909090902790902721635454541263233332332222223特制并实施特种设备管理办法、执行培训管理程序、起重搬运安全作业指导书,并加强监督管理制定并实施特种设备管理办法、执行培训管理程序、起重搬运安全作业指导书,并加强监督管理提高警惕、集中工作注意力使用登高工具使用登高工具执行设备安全技术操作规程,并加强监督管理,加强安全意识培训111111117 7 8 折弯机操作折弯机操作砂轮机操作未正确使用辅助工具闭式压力机登高维修保养,安全防护栏等装置不符要求剪、压机械 PE 连接缺损剪压上料、落料噪声剪压机作业未使用按钮站刀板松动未定期更换机油培训不到位发生异常未即将停机检查处理机床后部站人板料折弯时未压坚固未停车校正工件和模具未佩戴安全防护用品站在砂轮机的正前方操作未定期更换砂轮片高处坠落触电危(wei)险职业危害机械伤害机械伤害机械伤害机械伤害DDDDDDDDDDDDDDD336113331661336266661122212667151531515131515151533712690901089090399030180105654126333333113243122执行安全技术操作规程,并加强监督管理执行安全技术操作规程,并加强监督管理执行安全技术操作规程,并加强监督管理1111111119 10 铣床操作车床操作未戴防护眼镜打磨细小的、大的和不好拿的工件砂轮受潮、沾水后继续使用砂轮磨损严重或者径向跳动过大、震动大时继续使用高速切削时未装防护挡板操作者未戴防护眼镜戴手套操作拆装立铣刀时,用手托刀盘拆掉限位块加工超长、超宽零件快速进刀时,左手远离手柄未停车测量、取卸工件高速切削时未戴防护眼镜工件未夹紧用砂布光内孔时,将手指或者手臂伸进工件打磨切断小料时用手接机械伤害机械伤害DDDDDDCDDDDDDDD63316633136113666666636366663733333327377310812654181081085427126310842425432213322123222执行安全技术操作规程,并加强监督管理执行安全技术操作规程,并加强监督管理1111110 车床操作11 钻床操作12 镗床操作13 磨床操作戴手套操作切大料时直接切断一手扶攻丝架(后扳牙架)一手开车用手扶工件用手清除铁屑戴手套操作在旋转的刀具下,翻转、卡压或者测量工件安装刀具时紧固螺钉和销子凸出镗杆回转半径戴手套操作机床开动时,量尺寸、对样板镗孔、扩孔时将头贴近加工孔观察吃刀情况使用平旋刀盘式自制刀盘进行切削时,站在对面或者伸头察看干磨或者修砂轮时,未戴防护眼镜操作者站在砂轮的正面机械伤害机械伤害损坏工件机械伤害机械伤害CDDDDCDDCDDDDD133631333636633313336333717777733185463186376363631082712212122232执行安全技术操作规程,并加强监督管理执行安全技术操作规程、机械加工安全作业指导书,加强监督管理执行安全技术操作规程,并加强监督管理执行安全技术操作规程,并加强监督管理1111吃刀量过大,砂轮破裂飞出 D 3 3 3 27 2 0使用有缺陷的砂轮 D 3 6 7 126 3 1砂轮未退到安全位置时,测量、装卸工D 3 3 7 63 2 0件14 刨床操作工件装夹不坚固机械伤害 D 3 3 7 63 2 执行安全技术操作规程,并加强监督0未停车调整行车挡铁 D 3 3 7 63 2 014 刨床操作未停车测量工件、清扫铁削机械伤害 D 6 3 7 126 3 管理1工作台行程范围内有人员活动 D 3 3 7 63 2 0离合器不完好连车或者滑车造成挤压伤D 6 3 7 126 3 1操作面板指示信号错误导致设备事故机械伤害 D 1 7 1 0 或者人员伤害急停装置失灵造成压伤 D 3 1 7 21 2 定期检查,遵守操作规程等各项规定,015 冲压操作设备电线裸露导致设备故障或者人员伤培训后上岗,佩带好防护用品,杜绝D 1 1 15 15 1 0害触电违章作业。
危险源识别与风险评价结果一览表22
总序号
施工区域
人员/设施/活动
分序
危 险 源
可能导致事故
评价方法
风险级别
现有控制措施
532
(七)
施
工
机
械
32、施工升降机
19
安装后未按照规定要求做坠落实验
机具伤害
略
一般
BD
533
20
电梯内载重严重偏心
机具伤害
略
一般
BD
534
21
操作人员未切断总电源离开岗位
机具伤害
略
机具伤害
略
一般
BD
553
40
设备未接地或接地不符合要求
触电
略
一般
BDLeabharlann 55433、塔式起重机1
无力矩限制器或失效
机具伤害
略
一般
BD
555
2
无超高变幅行走限位或失效
机具伤害
略
一般
BD
556
3
吊钩无保险或吊钩磨损超标
机具伤害
略
一般
BD
557
4
塔吊卷扬机滚筒无保险装置
机具伤害
略
一般
BD
A、制定目标、指标和管理方案;B、执行运行控制程序;C、教育与培训;D、监督检查E、制定应急预案
一般
BD
535
22
电梯在恶劣天气使用
机具伤害
略
一般
BD
536
23
用行程开关做停止的控制开关
机具伤害
略
一般
BC
537
24
在电梯内向楼层内抛掷物件
(一)毛纺企业危险源辨识与风险评价信息一览表2016.12.9
(一)毛纺企业危险源辨识与风险评价信息一览表
2、按安全操作规程,配备相应的劳动防
护用品;
维修牌;
4、对生产设备要定期进行维护保养,避免因长期失修造成安全隐患;Array规操作;
2、及时巡检,杜绝不安全因素;
5、定期做好设备清洁工作;
6、按照规定佩戴劳动防护用品;
4、定期对生产设备进行维护保养,消除
安全隐患;
训,提高员工的操作水平及安全意识;2、加强巡检,及时修理或整改设备等存在的安全隐患;
操作规程进行培训;
2、加强巡检,及时修理或整改设备等存在的安全隐患;
10、执行电气检维修制度操作规程,配备劳动防护用品;
患的部件,避免不必要的损害;
7、设置安全防护设施、佩戴劳动防护用
止违章违规操作;
4、按要求设置静电消除器;
2、加强安全管理控制措施,严禁违章操作;
用设备,禁止违章操作;
置防护用品和消防设施,设置警示标志、定期检查、定期进行安全及操作培训。
7、正确使用生产用具,及时更换已损坏
2、加强巡检,定期做好设备的维护保养工作;
3、在特殊部位张贴按安全警示标识;Array
劳动防护用品;
2、加强安全操作培训,必须持证上岗;
用电部位;
防腐、防鼠措施;
4、加强安全用电防护措施培训,提高人员的安全防护意识;
培训,加强员工的安全意识;
9、合理摆放消防器材,布局合理,以达到应急救援的目的;。
(二)服装企业危险源辨识与风险评价信息一览表2016.12.9
高安全操作技能;
2、制定相应的安全操作规程;
4、每周对设备完好情况进行检查;
5、配发高温防护手套;
6、蒸汽管道安全附件定期检验
训;
2、制定机台安全操作规程;
扣眼机6、制定设备保养清单,每月对
相应机台进行保养;
7、每天打扫机台卫生;
8、操作人员必须佩戴防护眼镜
训;
2、制定机台安全操作规程;
3、加强机台用电管理,做到每位员工人走机关;
位员工人走机关;
4、每月定期利用班前会进行安全教育培训;6、制定设备保养清单,每月对相应机台进行保养;7、每天打扫机台卫生;
9、规范管线布置,电气线路与其他管线之间按照规范要求设
操作规程作业;
2、增加仓库照明电器数量;
3、定期发放手套等劳保用品;
4、制定设备保养计划实施;
5、配备高温防护劳保用品;
6、加强对蒸汽管道。
阀门的检
3、电工作业人员必须持证上岗;
4、维修过程中必须防止维修操。
2、加强专业技能培训,提升专业技能;
3、电焊工作业人员必须持证上岗;
2、使用机器时首先检查设备的完好性;
场3、定期组织员工进行安全培训;
4、每年组织两次安全逃生演2、每年组织空压机操作培训,
2、配电室门口配有高压危险标识;。
- 1、下载文档前请自行甄别文档内容的完整性,平台不提供额外的编辑、内容补充、找答案等附加服务。
- 2、"仅部分预览"的文档,不可在线预览部分如存在完整性等问题,可反馈申请退款(可完整预览的文档不适用该条件!)。
- 3、如文档侵犯您的权益,请联系客服反馈,我们会尽快为您处理(人工客服工作时间:9:00-18:30)。
存在焊接气割作业
人员伤害
D
1
6
7
42
2
刷漆操作在指定场所
0
工作场地狭小,安全距离内有电焊、切割等明火作业
D
6
3
7
126
3
1
工作环境通风条件差
中毒
D
6
6
3
108
3
1
未正确穿戴劳保用品
D
3
6
3
54
2
执行安全技术操作规程,并加强监督管理
0
19
热处理过程
设备漏电
触电
D
1
1
15
15
1
定期检查,遵守操作规程等各项规定,
7
63
2
使用登高工具
0
6
剪板机操作
剪、压脚踏开关无护罩
机械伤害
D
3
6
3
54
2
执行设备安全技术操作规程,并加强
监督管理,加强安全意识培训
0
剪板机剪压区无防护栏、网
D
3
6
3
54
2
0
剪、压机床离合器缺陷
D
3
6
3
54
2
0
剪、压机床制动器与离合器协调失误
D
3
6
7
126
3
1
未正确使用辅助工具
D
3
6
7
126
3
1
闭式压力机登高维修保养,安全防护栏等装置不符要求
0
未定期更换砂轮片
D
3
6
7
126
2
0
未戴防护眼镜
D
6
6
3
108
3
1
打磨细小的、大的和不好拿的工件
D
3
6
7
126
2
0
砂轮受潮、沾水后继续使用
D
3
6
3
54
2
0
砂轮磨损严重或径向跳动过大、震动大时继续使用
D
1
6
3
18
1
0
9
铣床操作
高速切削时未装防护挡板
机械伤害
D
6
6
3
108
3
执行安全技术操作规程,并加强监督管理
D
1
6
40
240
3
1
化学危险品库通风条件不良
中毒和窒息
D
6
15
45
2
0
化学品堆放超高、失稳导致化学品泄漏
物体打击
D
1
6
40
240
3
0
21
丙烷站
丙烷仓库库通风条件不良,易燃气体积聚
火灾、爆炸
D
1
6
15
90
3
执行丙烷站安全管理制度、加强安全意识培训、检查丙烷站日常检查,应急预案
1
丙烷库房消防器材失效未及时更换
作业时抛丸机泄漏铁砂在螺旋输送电机上造成的短路
电器火灾
D
3
2
15
90
3
1
作业时零件架比较多人容易绊倒、撞到
人身伤害
D
3
2
7
42
2
0
产生过程中产生的废气和烟雾对人和环境的污染
D
3
2
15
90
3
1
18
刷漆操作
油漆、稀释剂等化学配料和汽油易燃物品,全部集中存放在简易库房内
火灾
C
设置油漆专用库,易燃易爆物品分类隔离存放,严禁烟火
1
0
电气控制柜不完好造成电气事故
D
1
1
15
15
1
0
登高检修直梯无自锁造成人员伤害
机械伤害
D
1
7
1
0
零件锋利边沿或毛刺割伤
D
3
2
15
90
3
1
设备漏油造成火灾或摔伤
人员伤害
D
3
2
7
42
2
0
冲压噪音超标造成职业伤害
职业伤害
D
3
2
15
90
3
1
安全知识缺乏操作失误
机械伤害
D
3
2
7
42
2
0
无任何防范措施进入模区
1
工件未夹紧
D
1
6
7
42
2
0
用砂布光内孔时,将手指或手臂伸进工件打磨
D
1
6
7
42
2
0
切断小料时用手接
D
3
6
3
54
2
0
10
车床操作
戴手套操作
机械伤害
C
执行安全技术操作规程,并加强监督管理
1
切大料时直接切断
D
1
6
3
18
1
0
一手扶攻丝架(后扳牙架)一手开车
D
3
6
3
54
2
0
11
钻床操作
用手扶工件
机械伤害
D
3
D
3
3
7
63
2
0
15
冲压操作
离合器不完好连车或滑车造成挤压伤
机械伤害
D
6
3
7
126
3
定期检查,遵守操作规程等各项规定,培训后上岗,佩带好防护用品,杜绝违章作业。
1
操作面板指示信号错误导致设备事故或人员伤害
D
1
7
1
0
急停装置失灵造成压伤
D
3
1
7
21
2
0
设备电线裸露导致设备故障或人员伤害
触电
D
1
1
15
15
D
3
6
5
90
3
1
金切机床PE连接不可靠、电源线老化破损
触电
D
6
15
45
2
0
机床电器箱柜线路不符合要求
D
3
6
3
54
2
0
违章作业、未正确穿戴劳动防护用品和正确使用工具
机械伤害
D
3
6
5
90
3
1
设备维修未切断电源或未采取有效防护措施
触电
D
3
6
3
54
2
0
17
抛丸操作
操作过程中手缩回太慢,手可能会夹在零件与机床间
D
3
2
15
90
3
1
机床后部站人
D
1
2
15
30
2
0
7
折弯机操作
板料折弯时未压牢固
机械伤害
D
6
2
15
180
4
执行安全技术操作规程,并加强监督管理
1
未停车校正工件和模具
D
6
1
15
105
3
1
未佩戴安全防护用品
D
1
2
3
6
1
0
8
砂轮机操作
站在砂轮机的正前方操作
机械伤害
D
3
6
3
54
2
执行安全技术操作规程,并加强监督管理
1
储罐超过检验有效期
爆炸
D
1
6
15
90
3
1
压力表超过检验有效期
D
1
6
15
90
3
1
安全阀超过检验有效期
D
1
6
15
90
3
1
23
压力容器
空压机机身、曲轴箱等主要受力部件强度和刚度缺陷,
机械伤害
D
1
6
5
30
2
执行设备安全操作规程、定期安检、加强日常监督管理
0
储气罐未在检验期内使用
容器爆炸
D
1
6
15
90
3
1
储气罐安全附件缺损或未定期校验
0
16
金属切割操作
金切机床操作手柄、开关失灵
机械伤害
D
3
6
5
90
3
定期检查,遵守操作规程等各项规定,培训后上岗,佩带好防护用品,杜绝违章作业。
1
金切机床安全防护罩盖栏等装置缺损
D
3
6
5
90
3
1
金切机床加工长料没有采用防弯装置或没有设置防护栏
D
3
6
5
90
3
1
金切机床旋转部位的楔、销、键突出部位大于3毫米
1
操作者未戴防护眼镜
D
6
6
3
108
3
1
戴手套操作
C
1
拆装立铣刀时,用手托刀盘
D
3
6
3
54
2
0
拆掉限位块加工超长、超宽零件
D
3
3
3
27
2
0
快速进刀时,左手远离手柄
D
1
6
2
12
1
0
未停车测量、取卸工件
D
3
3
7
63
2
0
10
车床操作
高速切削时未戴防护眼镜
机械伤害
D
6
6
3