穿孔机试车工艺方案
穿孔机技术操作规程
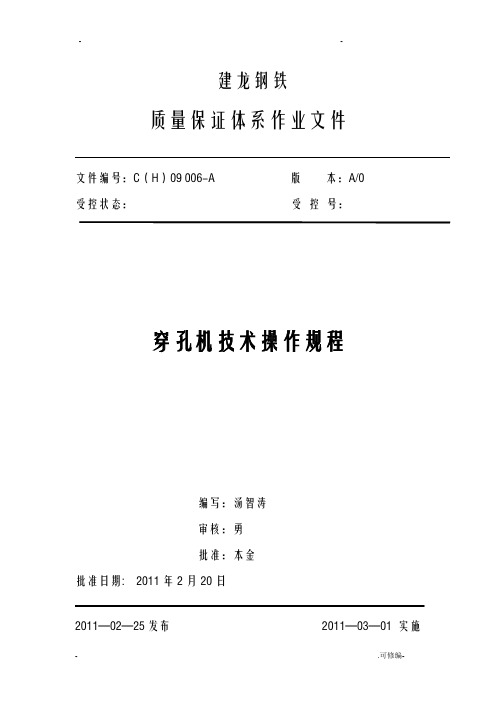
建龙钢铁质量保证体系作业文件文件编号:C(H)09 006-A 版本:A/0受控状态:受控号:穿孔机技术操作规程编写:汤智涛审核:勇批准:本金批准日期: 2011年2月20日2011—02—25发布2011—03—01 实施1 适用围:本规程适用于连轧厂穿孔机区操作工2 生产前设备检查2.1交接班时,检查主操作台上相关操作开关是否置于零位,区域生产方式是否置于手动。
2.2检查所有转动部件上有无杂物,若有须清理彻底。
2.3在相关区域进行工具检查和设备维护时,先检查该区域操作台各开关是否置于零位,动力电源是否已经切断,否则不能作业。
2.4在对转动杆件(如传动轴)进行点动操作前,先检查杆件上有无缠绕物,或有无人员在危险位置。
2.5完成设备或变形工具的检查维护工作后,将相关工具(如扳手、钳子等)带到指定的地方安全摆放,并将现场的油污和杂物按规定进行收集处理,不得将污染物随意排放到地沟。
2.6在控制电源合闸前,应确认无任何人员在危险区域。
2.7开机前,操作人员首先要进行视觉检查,确认设备及它的安全设施是否完好。
检查机器运转区域围(如:辊道上、横移链上以及其动作区域)有无人员停留,并启动开机警报装置。
2.8在“自动操作”或“手动操作”模式下。
操作人员要密切监控设备运转情况;若无操作人员监控,严禁设备运行。
2.9在自动操作模式过程中,任何人不允许在危险区域经过或逗留。
2.10设备的检修和维护以及排除故障时,必须在设备停机并停稳后进行;未经允许的人员不得参与机械的处理工作。
2.11更换辅助工具时控制电源必须关闭,长时间不生产时必须关闭传动系统。
3 安全确认3.1设备维护过程中安全确认(1)切断电源。
(2)主操作台和区域现场操作台旋转开关置于“0”位。
(3)确认已经停机,设备处于静止。
3.2设备启动前必须先确认(1)检修已彻底完成。
(2)设备允许安全运转。
(3)所有人员已离开设备危险区。
3.3穿孔机前区区域设备检查3.3.1穿孔机前区(1)检查环形炉出口斜台架上接料臂升降是否正常。
LXC50穿孔机技术方案

LXC50斜轧穿孔机组技术方案常熟市梅李机械制造有限公司2012-2-20目录一.穿孔机概述及各部件组成二.设备基本参数三.穿孔机组辅助设施要求及能源介质消耗四.穿孔机组供需双方公用设施界定五.交货工期、安装、试车与验收六.质量保证、设备售后服务七.图纸与文件交付八.工具、备件、易损件九.现场安全保障及其他十.设备供货范围一、穿孔机概述及各部件组成1. 概述:LXC系列穿孔机为二辊卧式斜轧穿孔机组,是热轧无缝钢管或热轧有色金属无缝管生产中最重要的变形工序,主要是将加热到予定温度的实心管坯穿制成相应规格的空心荒管。
其穿制工作是在两个相对于轧制线倾斜布置的主动轧辊、两个固定不动的导板和一个位于中间的随动顶头(轴向定位)构成的一个“环形封闭孔型”中进行。
2. 机器的构成2.1 本机组LXC50穿孔机组,见总图(LXC50-00),其主要组成部分有: (1).主电动机、主减速器、三联齿轮箱、万向传动轴、受料槽装配、穿孔机装配等组成的主传动系统。
(2).定心辊装置(五道)、升降辊装置(四道)、翻钢装置(一组)、顶杆装配等组成的荒管稳定及脱开系统。
(3).脱管及弹簧缓冲器、小车装配、锁车架装配、小车轨道装配、弹簧缓冲器、小车传动装置、冷却水装置等组成的后台阶系统。
(4).操作台、电控柜、电磁阀底架装配等组成的气电控制系统。
2.2 主要部件介绍(1).动力源为JR137-6A/N=320KW电机。
(2).主减速机ZL115(i=8)通过联轴器装配(二)及联轴器装配(三)将主电动机的输出扭矩传递给中心距A=400mm(i=1)、两输出轴上下布置且同方向旋转的三联齿轮箱将动力经两支SWC250A型万向传动轴分配到两个不同倾斜方向的轧辊轴上。
(3).穿孔机装配由上导辊调整装配、轴承座装配、机架装配、侧压减速机装配、下导卫装配、进口导管装配及冷却水管装配组成。
管坯在二个双锥形轧辊及上下导板与顶头组成的环形封密孔形中作螺旋运动。
穿孔机操作规程

3、穿孔机区技术操作规程3.1、穿孔机设备及工具概述3.1.1、锥形辊穿孔机性能机架结构机架上有2个上下布置的轧辊,两旁导板导向。
轧辊材质50 Mn60 Mn轧辊直径Φ1300~Φ1150 mm辊身长度 1000mm安装方式上下安装随轧辊装配及转鼓同时拆装喂入角8°~15°无级可调辗轧角15°固定额定辊速64 r/min轧辊转矩每个轧辊最大转矩为1100 kN.m 输出转速范围42~92 r/min输出速度范围600~1 150 mm/s生产率 max 1.5 pcs/min主传动主电机功率 1800KW ×2×2 DC转速 375/900 r/min过载系数 2主减速机速比 5.7893.1.2、工具概述3.1.2.1、穿孔机轧辊喉径处轧辊直径最大Ф1300 mm重车量 75mm轧辊辊身长度 1000mm入口锥角度 2.7°入口锥长度 425 mm出口锥角度 3.7°出口锥长度 575 mm轧辊材质50 Mn、60 Mn成分 C: 0.47~0.55Si: 0.15~0.40Mn: 0.60~0.90 P: Max 0.035S: Max 0.035硬度 220~250 HBW3.1.2.2、顶杆:规格:外径Φ121~Φ299 mm壁厚25~34 mm长度 17295mm(从法兰面至顶头鼻部)材质34CrMo4V、 35CrMnSiA或Cr5Mo冷却方式内水冷为主,外水冷为辅与接套、顶头的安装方式固定式,人工拆装3.1.2.3、顶头接套:规格外径Φ121~Φ299 mm;壁厚25~34 mm连接段长度 254~324mm材质34CrNi3Mo与顶杆、顶头的安装方式:固定式,人工拆装。
3.1.2.4、顶头:规格Ф200系列8种Ф250系列21种Ф300系列8种Ф330系列15种Ф350系列7种直径Φ116~Φ333mm长度370~650 mm材质成分C: 0.15~0.25Mn: 0.75~1.00Si: 0.50~0.60Ni: 2.5~3.2Cr: 1.00~1.60Mo: Max 0.50P: Max 0.035S: Max 0.035硬度 250~350 HBW冷却方式空心,内水冷为主,外水冷为辅与顶杆、接套的安装方式固定式,人工拆装3.1.2.5、导板:规格Ф200、Ф250、Ф300、Ф330、Ф350系列5种导板材质高碳高铬铸钢成分 C: 1.4~1.50Mn: 1.0~1.10Si: 0.50~0.70Ni: 8.00~10.00Cr: 25.00~27.00Mo: 0.50~0.70P: Max 0.04S: Max 0.04硬度 220~250 HBW3.1.2.6、入口导套规格Ф200、Ф250、Ф300、Ф350、Ф390系列5种导套材质203.1.2.7、脱管衬套规格1种Ф150(随机)导套材质45硬度 241~269 HBW表面淬火硬度HRC45~55深度 2 mm3.2、穿孔机正常工作的前提条件——轧辊形状、尺寸要符合要求,调整(辊距、导板距、咬入角等)要灵活,显示值与实际值要相符。
穿孔机组安全技术操作规程模版

穿孔机组安全技术操作规程模版章节一:安全管理制度1.1 目的为确保穿孔机组的安全运行,保障操作人员的人身安全和设备的正常运行,制定本安全技术操作规程。
1.2 适用范围本安全技术操作规程适用于公司穿孔机组的操作人员,并包括设备的正常维护和日常巡检。
1.3 责任1.3.1 公司负责制定和修订本安全技术操作规程,并提供相关培训。
1.3.2 穿孔机组操作人员有义务严格遵守本规程,并配合公司进行安全检查和培训。
章节二:设备安装与调试2.1 设备安装2.1.1 在安装穿孔机组前,必须进行现场勘察和设计,确保设备可以安全稳定地安装。
2.1.2 安装人员必须熟悉设备的安装和连接方法,严禁擅自改动设备连接线路和部件。
2.1.3 安装过程中必须保证设备的下部有足够的支撑力,防止设备倾翻和震动。
2.1.4 安装完成后,必须进行设备的基本性能测试和安全检查。
2.2 设备调试2.2.1 在设备调试前,必须确认电源和有关设备的电路连接正确,并设定合理的参数。
2.2.2 在调试过程中,必须保持机组运转平稳,确保工作环境安全,避免产生冲击、振动等潜在危险。
2.2.3 调试人员必须严格按照设备操作手册进行操作,并根据具体情况进行必要的调整。
2.2.4 调试过程中,必须注意观察设备的运行状态,及时排除可能存在的故障。
章节三:操作规范3.1 操作前准备3.1.1 操作人员必须穿戴符合安全要求的劳动防护用品,包括安全帽、防护眼镜、耳塞等。
3.1.2 检查设备的运行状态和相关参数,确保设备处于正常工作状态。
3.1.3 确认设备周围没有杂物和障碍物,保持工作环境清洁整洁。
3.2 操作过程3.2.1 操作人员必须按照操作手册进行设备操作,禁止擅自更改设备参数和程序。
3.2.2 在设备运行过程中,操作人员应时刻注意设备的运行状态,及时发现异常情况并采取相应措施。
3.2.3 操作人员在操作时不得随意触摸设备的旋转部分,避免发生伤害。
3.3 操作后整理3.3.1 在操作完成后,必须及时关闭设备的电源,并进行设备的清理和维护。
2021年穿孔机调整参数及常见缺陷

调整穿孔机遵循的原则欧阳光明(2021.03.07)调整正确的标志是?管坯咬入平稳,毛管抛出顺利,穿孔过程稳定,顶杆无明显跳动,毛管内外表面质量良好,毛管尺寸符合要求,主电机负荷正常为达到上述目的。
穿孔机调整应遵循的原则是?1.轧制线必须与穿孔中心线重合或者比穿孔中心线略底3~5毫米.2.两轧辊中心线的水平投影应同时平行于轧制线.3.两轧辊相对于穿孔中心线的倾角既前进角必须相等.4.确保顶杆在穿孔过程中有较高的钢性即顶杆不能有明显的跳动甩动.5.顶头所处的位置应适中以免造成前卡或者后卡事故.6.应实现无孔腔状态下的穿孔过程.7.穿孔工具如轧辊.顶头.导板都不应严重磨损.8.穿孔机调整工必须勤观察穿孔机运转的工作情况以及工具使用情况,必须勤检测毛管内外表面的质量以及尺寸,发现问题应及时处理.(如图)穿孔过程中主要的工艺参数1.穿孔过程中主要的工艺参数有变形参数、速度参数和温度参数、变形参数包括延伸系数、扩径率、扩展值、顶头前压下率、压缩带处管坯直径压下率、每半转压下率等。
2.速度参数包括轧辊转数、前进角轴向滑移系数(0.5~0.8),温度参数包括穿孔前管坯温度1230±20℃和穿孔后毛管温度1100℃.延伸系数怎样确定延伸系数是指毛管长度与管坯长度之比或者管坯断面积与毛管断面积之比.1.计算延伸系数的公式分别为烧损,一般取0.97~0.99斜底炉式可取大值,环形炉取小值。
2.毛管外径、壁厚和长度。
3.管坯直径、长度和断面积,延伸系数大则穿出的管子壁薄,但受到毛管内外表面质量咬入条件,轧卡等限制也不能太薄,一般小型穿孔机穿出毛管的壁厚为 4.5~5毫米.穿碳素钢管坯的延伸系数为3~4.5,穿合金钢管2.5~4延伸系数的下限受到顶杆强度和稳定性的限制,最小的延伸系数为1.2。
什么是扩展值?影响它的因素有那些?毛管内径与顶头直径之差叫做扩展值,由于在斜轧穿孔过程中管坯在变形区中呈椭圆形,因此毛管的内径始终会大于顶头直径。
穿孔机调整知识
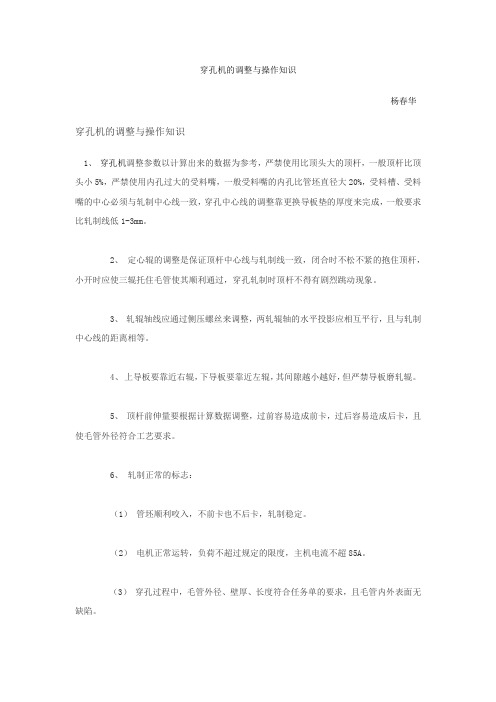
穿孔机的调整与操作知识杨春华穿孔机的调整与操作知识1、穿孔机调整参数以计算出来的数据为参考,严禁使用比顶头大的顶杆,一般顶杆比顶头小5%,严禁使用内孔过大的受料嘴,一般受料嘴的内孔比管坯直径大20%,受料槽、受料嘴的中心必须与轧制中心线一致,穿孔中心线的调整靠更换导板垫的厚度来完成,一般要求比轧制线低1-3mm。
2、定心辊的调整是保证顶杆中心线与轧制线一致,闭合时不松不紧的抱住顶杆,小开时应使三辊托住毛管使其顺利通过,穿孔轧制时顶杆不得有剧烈跳动现象。
3、轧辊轴线应通过侧压螺丝来调整,两轧辊轴的水平投影应相互平行,且与轧制中心线的距离相等。
4、上导板要靠近右辊,下导板要靠近左辊,其间隙越小越好,但严禁导板磨轧辊。
5、顶杆前伸量要根据计算数据调整,过前容易造成前卡,过后容易造成后卡,且使毛管外径符合工艺要求。
6、轧制正常的标志:(1)管坯顺利咬入,不前卡也不后卡,轧制稳定。
(2)电机正常运转,负荷不超过规定的限度,主机电流不超85A。
(3)穿孔过程中,毛管外径、壁厚、长度符合任务单的要求,且毛管内外表面无缺陷。
7、穿孔过程中常出现的问题及处理办法:(1)发生前卡时应做下列调整:1、管坯端部是否符合要求,头部是否有冷头。
2、导板位置是否合适,磨损是否严重,进口是否有障碍物。
3、顶头前伸量是否过大(顶头前压缩量过小)(2)发生中卡时应做下列调整:1、检查轧辊入口锥和导板是否磨损严重。
2、检查压缩量是否过大(轧距过小)3、管坯温度是否过低、过高,长度方向温度是否不均。
(3)发生后卡应做下列调整:1、顶头前伸量是否合适,顶头形状是否符合要求。
2、导板距和轧辊距的比值是否过大或过小(一般比值为1.1-1.6)3、顶头是否开裂和融化。
4、导板磨损是否严重。
5、管坯后端的温度是否过低或尺寸过细。
8、调整工调整定心辊或更换导板时必须给操作工以明确的信号,此时操作工应将操作手柄放到零位,且离开操纵把远一点,生产过程中严禁跨越顶杆、顶杆小车轨道和穿孔出口导道与第一组定心辊之间的通道,严禁在定心辊前逗留,以防鼓顶杆伤人。
穿孔机调整参数及常见缺陷

调整穿孔机遵循得原则调整正确得标志就是?管坯咬入平稳,毛管抛出顺利,穿孔过程稳定,顶杆无明显跳动,毛管内外表面质量良好,毛管尺寸符合要求,主电机负荷正常为达到上述目得、穿孔机调整应遵循得原则就是?1.轧制线必须与穿孔中心线重合或者比穿孔中心线略底3~5毫米。
2.两轧辊中心线得水平投影应同时平行于轧制线、3.两轧辊相对于穿孔中心线得倾角既前进角必须相等.4.确保顶杆在穿孔过程中有较高得钢性即顶杆不能有明显得跳动甩动。
5.顶头所处得位置应适中以免造成前卡或者后卡事故、6.应实现无孔腔状态下得穿孔过程、7.穿孔工具如轧辊、顶头。
导板都不应严重磨损.8.穿孔机调整工必须勤观察穿孔机运转得工作情况以及工具使用情况,必须勤检测毛管内外表面得质量以及尺寸,发现问题应及时处理.(如图).轧辊 2.钢管 3.顶杆 4.导板 5.顶头穿孔过程中主要得工艺参数1.穿孔过程中主要得工艺参数有变形参数、速度参数与温度参数、变形参数包括延伸系数、扩径率、扩展值、顶头前压下率、压缩带处管坯直径压下率、每半转压下率等。
2.速度参数包括轧辊转数、前进角轴向滑移系数(0。
5~0、8),温度参数包括穿孔前管坯温度1230±20℃与穿孔后毛管温度1100℃.延伸系数怎样确定延伸系数就是指毛管长度与管坯长度之比或者管坯断面积与毛管断面积之比.1.计算延伸系数得公式分别为烧损,一般取0.97~0。
99斜底炉式可取大值,环形炉取小值、2.毛管外径、壁厚与长度。
3.管坯直径、长度与断面积,延伸系数大则穿出得管子壁薄,但受到毛管内外表面质量咬入条件,轧卡等限制也不能太薄,一般小型穿孔机穿出毛管得壁厚为4。
5~5毫米、穿碳素钢管坯得延伸系数为3~4。
5,穿合金钢管2、5~4延伸系数得下限受到顶杆强度与稳定性得限制,最小得延伸系数为1、2。
什么就是扩展值?影响它得因素有那些?毛管内径与顶头直径之差叫做扩展值,由于在斜轧穿孔过程中管坯在变形区中呈椭圆形,因此毛管得内径始终会大于顶头直径。
穿孔机操作规程

3、穿孔机区技术操作规程3.1、穿孔机设备及工具概述3.1.1、锥形辊穿孔机性能机架结构机架上有2个上下布置的轧辊,两旁导板导向。
轧辊材质50 Mn60 Mn轧辊直径Φ1300~Φ1150 mm辊身长度 1000mm安装方式上下安装随轧辊装配及转鼓同时拆装喂入角8°~15°无级可调辗轧角15°固定额定辊速64 r/min轧辊转矩每个轧辊最大转矩为1100 kN.m 输出转速范围42~92 r/min输出速度范围600~1 150 mm/s生产率 max 1.5 pcs/min主传动主电机功率 1800KW ×2×2 DC转速 375/900 r/min过载系数 2主减速机速比 5.7893.1.2、工具概述3.1.2.1、穿孔机轧辊喉径处轧辊直径最大Ф1300 mm重车量 75mm轧辊辊身长度 1000mm入口锥角度 2.7°入口锥长度 425 mm出口锥角度 3.7°出口锥长度 575 mm轧辊材质50 Mn、60 Mn成分 C: 0.47~0.55Si: 0.15~0.40Mn: 0.60~0.90 P: Max 0.035S: Max 0.035硬度 220~250 HBW3.1.2.2、顶杆:规格:外径Φ121~Φ299 mm壁厚25~34 mm长度 17295mm(从法兰面至顶头鼻部)材质34CrMo4V、 35CrMnSiA或Cr5Mo冷却方式内水冷为主,外水冷为辅与接套、顶头的安装方式固定式,人工拆装3.1.2.3、顶头接套:规格外径Φ121~Φ299 mm;壁厚25~34 mm连接段长度 254~324mm材质34CrNi3Mo与顶杆、顶头的安装方式:固定式,人工拆装。
3.1.2.4、顶头:规格Ф200系列8种Ф250系列21种Ф300系列8种Ф330系列15种Ф350系列7种直径Φ116~Φ333mm长度370~650 mm材质成分C: 0.15~0.25Mn: 0.75~1.00Si: 0.50~0.60Ni: 2.5~3.2Cr: 1.00~1.60Mo: Max 0.50P: Max 0.035S: Max 0.035硬度 250~350 HBW冷却方式空心,内水冷为主,外水冷为辅与顶杆、接套的安装方式固定式,人工拆装3.1.2.5、导板:规格Ф200、Ф250、Ф300、Ф330、Ф350系列5种导板材质高碳高铬铸钢成分 C: 1.4~1.50Mn: 1.0~1.10Si: 0.50~0.70Ni: 8.00~10.00Cr: 25.00~27.00Mo: 0.50~0.70P: Max 0.04S: Max 0.04硬度 220~250 HBW3.1.2.6、入口导套规格Ф200、Ф250、Ф300、Ф350、Ф390系列5种导套材质203.1.2.7、脱管衬套规格1种Ф150(随机)导套材质45硬度 241~269 HBW表面淬火硬度HRC45~55深度 2 mm3.2、穿孔机正常工作的前提条件——轧辊形状、尺寸要符合要求,调整(辊距、导板距、咬入角等)要灵活,显示值与实际值要相符。
- 1、下载文档前请自行甄别文档内容的完整性,平台不提供额外的编辑、内容补充、找答案等附加服务。
- 2、"仅部分预览"的文档,不可在线预览部分如存在完整性等问题,可反馈申请退款(可完整预览的文档不适用该条件!)。
- 3、如文档侵犯您的权益,请联系客服反馈,我们会尽快为您处理(人工客服工作时间:9:00-18:30)。
负责人:
6事故状态:吊车不好使
处理办法:倒另外吊车
负责人:
7事故状态:自动吊具不好使
处理办法:倒备用吊具
负责人:
8事故状态:星型翻料勾不好使
处理办法:定心辊大打开,用吊车吊把拽翻料勾,把钢管翻到硼砂站上
②导板横向错位或磨损严重。当导板错位较大时,由于磨损不正常,使孔型形状改变,阻力增大,造成后卡;导板磨损严重时,椭圆度增大,若坯料末端进入变形区,动力不足以克服摩擦力产生后卡。
③小车烧。这时促使荒管前进和旋转的动力小于阻力,因而产生后卡,需要更换小车。
④轧辊倾角不一致。因角度不一致,轧制压缩带不在轧制中心线处相交,管坯在变形区反复弯曲变形,最后不能前进,造成后卡。
穿孔机试车工艺方案
1、工艺流程:
1.1穿孔机前区
1.1.1穿孔机前运输区
从环形炉出来的热管坯被抛到斜台架上。管坯从斜台架上滚到转向台架后热探检测到管坯,启动拨料装置将坯料送到横移链床上,横移链床以最快速度移动速度按0.8m/s将坯料送入穿孔机前辊道。穿孔机前输送辊道为斜置辊道,对坯料进行二次除鳞。热探检测到管坯,启动旋转的辊道(辊道倾角10°布置),辊道速度按0.5m/s。当管坯经过辊道末端的热探探测到管坯头端时,辊道停止,确保管坯头端在辊道末端的挡板前停下。
2、穿孔中心线在1月19日晚24点前调整完成,落实人:。
3、穿孔参数在1月20日下午4点调整完成,XXX提供实际调整参数。落实人:。
4、加热炉试车在1月23日晚24点前完成,达到装炉条件。XXX写出手动装料、出料操作步骤。落实人:。
5、穿孔机试车在1月22日晚24点前完成,达到生产轧钢条件,XXX写出手动轧钢操作步骤。落实人:。
2.5.2、中卡和尾卡
2.5.2.1中卡和尾卡的定义及产生原因:
⑴中卡:穿孔过程中顶头被卡在管坯的中部,此种情况出现较少,一般情况下,凡造成前卡的情况都可能造成中卡,其他几种情况如下:
①顶头破裂或熔化,轧厚壁管或轧制合金钢时,变形抗力大,顶头易劈裂或熔化,并与管坯粘接,造成旋转不前进。
②坯料夹渣管坯连续遭到破坏。
⑵坯料端部呈“炮弹头”形状。
主要原因:若轧制中心线与机架中心线偏离太大(如导板入口太高,两轧辊轴线与机架的距离不等,入口导孔不正等),这样坯料在变形区内走的是曲线,而不是直线,若送料过猛,就会出现常说的“炮弹头”的情况。
⑶坯料端部没有变形,只是断面中心被顶头鼻部压下一个凹坑。
①辊距太大。当辊距较轧制表要求的太大时,坯料被送入孔型后前进力克服不了顶头的阻力,使坯料只旋转不前进。
序号
名称
数量
备注
1
板子
2个
换顶杆用
2
撬棍
2个
别料
3
尖嘴钳子
2
换顶头用
4
钳子
2
换顶头用
5
手捶
2
换导板
6
大捶
1
换导板
以上工具放在穿孔机操作台。
负责人:
2.1.3其他准备工作
2.1.3.1氧气、乙炔各两瓶。
2.1.3.2割炬及风带一套。
2.1.3.35吨钢绳2副。
2.1.3.4自动吊具2个。
2.1.3.5∮89*2M钢管1支
⑤烧顶头。由于顶头冷却水不足,顶头质量差等引起顶头烧(部分熔化)使顶头和坯料粘在一起,发生包顶头现象,造成后卡。
⑥顶杆位置小。顶杆位置小,变形区后移,相对来说入口锥减小,出口锥增大,至管坯尾端进入变形区后,由于管坯与轧辊入口接触面积减小,摩擦力减小,造成只旋转不前进。
2)顶头露出以部分,管子后端壁很厚,呈“方头”状。
1.3.2穿孔机后运输区
毛管滚到接料钩上,接料钩下降到低位。此时当热探检测到毛管时启动翻料装置将其送到毛管内部清理站进行内部清理和除氧化皮。毛管内部清理站包括一组相同转速的转盘以保证毛管的旋转,并靠氮气和合适形状的喷嘴将抗氧化剂吹入毛管内部。毛管通过高架的输送小车运输到三辊限动芯棒连轧管机的入口,然后等待下次试穿。
1)管坯加热按照工艺要求。
2)按照工艺要求,进行调整顶伸量、辊距、导距。
3)穿孔机中心线要与轧制线重合。
4)按照工艺要求控制好穿孔机轧辊,顶头冷却水压力。
2.5.1.3处理方法:通知环形炉停止出料,穿孔机前区域选择开关打到手动位,停止主传动,操作前台推钢机到后退位置。三辊导向装置置于打开位,关闭机架冷却水和三辊导向装置的冷却水。①若管坯直接卡在孔型中,将穿孔机导板摆出,将辊距放开,之后用一根长约3米左右的推坯管从入口导套插入,顶到管坯上,之后点动操作止推小车向前,使顶头顶住推坯管将管坯顶出,当管坯全部脱离导筒后停止。②若管坯只旋转不咬入(不咬入分为一次不咬入和二次不咬入),可直接缩小些辊距。
主要原因如下:
①导板轴向错位,管坯在变形过程中不稳定轧制,前进阻力增大。
②椭圆度太大。出口太小,导板磨损严重,导板固定不牢或导板架跳动。当轧制快结束时,由于椭圆度太大,直径大的一边转到轧辊方向,受到突然来自径向的压力,来不及延伸和扩展,从而不能继续旋转,卡在轧辊中。
3)顶头完全露出,但带不出料。
产生原因如下:
XXX:负责穿后毛管吊运指挥工作。
XXX:负责生产现场安全、防火设施的准备及确认工作,现场秩序的维护工作。
2.2.2.3加热组职责分工
烧钢及装出料操作:
现场安全保障:
2.2.2.4穿孔组职责分工
操作:
调整:
工具准备:
穿后毛管吊运:
2.3生产准备要求
1、各种工具在1月20日中午12点之前备好,落实人:
1.1.2穿孔机入口区
当入口侧的热探检测到入口受料槽上无管坯且推钢机处于基位,挡料钩下降,管坯缓慢滚到入口受料槽上。
若穿孔机满足生产条件,推钢机将以0.5m/s速度前进,推动管坯向穿孔机前进。当坯料距离轧辊400mm时,推钢机推入速度降至0.3m/s。返回速度为0.7m/s。
在穿孔机前台设有废料收集台架,收集加热不合格或因临时故障剔出的坯料。
2、试车方案
2.1生产准备工作
2.1.1生产工具:
序号
名称
数量
备注
1
轧辊
1对
2
导板支持器
1对
3
导板
6块
2用4备
4
184顶头
3个
1用2备
5
178顶杆
2个
1用1备
6
推杆(1)
2个
1用1备
7
入口导筒
1个
8
顶杆连接销
8个
2用6备
9
模口
1个
以上工具中的备用工具放在穿孔机高位电机东侧平台上。
负责人:
2.1.2其他工具
拖出辊升起到毛管位托住毛管,同时所有三辊导向装置上辊全部打开。顶杆支撑装置上辊升起。止推小车夹紧装置打开,止推小车退回到基位。
夹送辊下降并与拖出辊一起启动,将毛管按0.5m/s速度移向脱管环。脱管环处热探探测到毛管头端接近脱管环时,辊道减速,避免毛管撞击脱管环,造成毛管头端变形。
一旦第2对热探探测到毛管的尾端,夹送辊升起。
②轧件温度过高,摩擦系数小,或轧件温度太低,阻力大,都会出现此种情况。
③顶头位置过前。使顶前压下量小,摩擦曳入力不足,且管坯中心疏松程度不够,咬入阻力增加,从而造成前卡。
④轧辊入口锥太大,使穿孔变形区段轧辊与坯料的接触面积小,引起摩擦力减小,使管坯前进的动力就下降了,而造成前卡。
2.5.1.2预防措施:
2事故状态:辊道不转
处理办法:用吊车及自动吊具把管坯吊到受料槽,然后剔料到废料台架。
负责人:
3事故状态:剔料拨叉不好使
处理办法:用吊车及自动吊具把管坯吊到
负责人:
4故状态:推料机不好使、受料槽内回炉料吊运
处理办法:先用受料槽液压缸把受料槽抬起,然后剔料到废料台架,之后用吊车挂自动吊具吊运。
负责人:
5事故状态:定心辊(包括机内定心辊)打不开
负责人:
9事故状态:负荷超载、主机掉电、钢管中卡
处理办法:主机降转速,停车,把轧辊放开,抽顶杆,把中卡料翻到硼砂站上,吊走。
负责人:
10事故状态:液压漏油
处理办法:操作台怕急停
负责人:
11ห้องสมุดไป่ตู้故状态:着火
处理办法:使用灭火器灭后
负责人:
12事故状态:前卡、不咬入
处理办法:用89钢管把管坯顶回受料槽,吊走。
以上工具放在操作台附近。
负责人:
2.2生产组织安排
2.2.1成立生产指挥组,组长:
副组长:
现场组:
加热组:
穿孔组:
2.2.2职责:
2.2.2.1XXX:负责∮177机组穿孔机热负荷试车生产条件的确认及生产组织工作。
2.2.2.2XXX:负责加热炉试车生产条件的确认及加热炉生产组织工作。
XXX:负责穿孔机试车生产条件的确认及生产工具准备、参数调整工作。
6、加热炉装炉在1月25日早8点前完成,落实人:。
7、管坯剔料放在剔料槽内,毛管放在连轧循环东侧,XXX写出毛管吊运步骤,落实人:。
8、轧出一支钢管后,立即停车,加热炉降温到800℃,把炉内剩下的料剔除到剔料筐。
2.4生产应急预案
1事故状态:出料小车停在炉内
处理办法:均热段降温;使用吊车往外拽
负责人:
1.2穿孔机区
穿孔过程中,管坯在轧辊、导板和顶头组成的孔型中变形,穿孔速度按0.5m/s设定,完成轧制后,主电机电流降低。轧制过程结束,工作辊再次空转,准备下一次轧制。
1.3穿孔机后区
1.3.1穿孔机出口区
穿孔机出口侧有7组三辊导向装置(其中有一组辊端伸入穿孔机本体机架牌坊内,称为机内定心,其它6组称为机外定心),每一组三辊导向装置前都设有1组(两个)热探。当毛管走出工作辊经过第一组三辊导向装置前的一组热探时,第1组三辊导向装置打开到毛管位。毛管通过第一个三辊导向装置,前端被下一对热探探测到时,第2个三辊导向装置打开到毛管位。以相同方式直到最后一个三辊导向装置打开到毛管位,直到轧制结束。当毛管距离抱辊约500mm时,每架抱紧辊打开速度应小于0.4m/s打开。