数控车床编程详解
数控车床编程实例详解(30个例子)(1)

半径编程车床编程实例一图3.1.1 半径编程%3110 (主程序程序名)N1 G92 X16 Z1 (设立坐标系,定义对刀点的位置)N2 G37 G00 Z0 M03 (移到子程序起点处、主轴正转)N3 M98 P0003 L6 (调用子程序,并循环6 次)N4 G00 X16 Z1 (返回对刀点)N5 G36 (取消半径编程)N6 M05 (主轴停)N7 M30 (主程序结束并复位)%0003 (子程序名)N1 G01 U-12 F100 (进刀到切削起点处,注意留下后面切削的余量)N2 G03 U7.385 W-4.923 R8(加工R8 园弧段)N3U3.215 W-39.877 R60 (加工R60 园弧段)N4 G02 U1.4 W-28.636 R40(加工切R40 园弧段)N5 G00 U4 (离开已加工表面)N6 W73.436 (回到循环起点Z 轴处)N7 G01 U-4.8 F100 (调整每次循环的切削量)N8 M99 (子程序结束,并回到主程序)1直线插补指令编程车床编程实例二%3305图3.3.5 G01 编程实例N1 G92 X100 Z10 (设立坐标系,定义对刀点的位置)N2 G00 X16 Z2 M03 (移到倒角延长线,Z 轴2mm 处)N3 G01 U10 W-5 F300 (倒3×45°角)N4 Z-48 (加工Φ26 外圆)N5 U34 W-10 (切第一段锥)N6 U20 Z-73 (切第二段锥)N7 X90 (退刀)N8 G00 X100 Z10 (回对刀点)N9 M05 (主轴停)N10 M30 (主程序结束并复位)圆弧插补指令编程车床编程实例三%3308N1 G92 X40 Z5 (设立坐标系,定义对刀点的位置)N2 M03 S400 (主轴以400r/min 旋转)N3 G00 X0 (到达工件中心)N4 G01 Z0 F60 (工进接触工件毛坯)N5 G03 U24 W-24 R15 (加工R15 圆弧段)N6 G02 X26 Z-31 R5 (加工R5 圆弧段)N7 G01 Z-40 (加工Φ26 外圆)N8 X40 Z5 (回对刀点)N9 M30 (主轴停、主程序结束并复位图3.3.8 G02/G03 编程实例2倒角指令编程车床编程实例四%3310图3.3.10.1 倒角编程实例N10 G92 X70 Z10 (设立坐标系,定义对刀点的位置)N20 G00 U-70 W-10 (从编程规划起点,移到工件前端面中心处)N30 G01 U26 C3 F100 (倒3×45°直角)N40 W-22 R3 (倒R3 圆角)N50 U39 W-14 C3 (倒边长为3 等腰直角)N60 W-34 (加工Φ65 外圆)N70 G00 U5 W80 (回到编程规划起点)N80 M30 (主轴停、主程序结束并复位)车床编程实例五倒角指令编程%3310N10 G92 X70 Z10 (设立坐标系,定义对刀点的位置)N20 G00 X0 Z4 (到工件中心)N30 G01 W-4 F100 (工进接触工件)N40 X26 C3 (倒3×45°的直角)N50 Z-21 (加工Φ26 外圆)N60 G02 U30 W-15 R15 RL=3(加工R15 圆弧,并倒边长为4 的直角)N70 G01 Z-70 (加工Φ56 外圆)N80 G00 U10 (退刀,离开工件)N90 X70 Z10 (返回程序起点位置)M30 (主轴停、主程序结束并复位)图3.3.10.2 倒角编程实例3车床编程实例六圆柱螺纹编程螺纹导程为1.5mm,δ=1.5mm,δ'=1mm ,每次吃刀量(直径值)分别为0.8mm、0.6 mm 、0.4mm、0.16mm图3.3.12 螺纹编程实例%3312N1 G92 X50 Z120 (设立坐标系,定义对刀点的位置)N2 M03 S300 (主轴以300r/min 旋转)N3 G00 X29.2 Z101.5 (到螺纹起点,升速段1.5mm,吃刀深0.8mm)N4 G32 Z19 F1.5 (切削螺纹到螺纹切削终点,降速段1mm)N5 G00 X40 (X 轴方向快退)N6 Z101.5 (Z 轴方向快退到螺纹起点处)N7 X28.6 (X 轴方向快进到螺纹起点处,吃刀深0.6mm)N8 G32 Z19 F1.5 (切削螺纹到螺纹切削终点)N9 G00 X40 (X 轴方向快退)N10 Z101.5 (Z 轴方向快退到螺纹起点处)N11 X28.2 (X 轴方向快进到螺纹起点处,吃刀深0.4mm)N12 G32 Z19 F1.5 (切削螺纹到螺纹切削终点)N13 G00 X40 (X 轴方向快退)N14 Z101.5 (Z 轴方向快退到螺纹起点处)N15 U-11.96 (X 轴方向快进到螺纹起点处,吃刀深0.16mm)N16 G32 W-82.5 F1.5 (切削螺纹到螺纹切削终点)N17 G00 X40 (X 轴方向快退)N18 X50 Z120 (回对刀点)N19 M05 (主轴停)N20 M30 (主程序结束并复位)4恒线速度功能编程车床编程实例七%3314图3.3.14 恒线速度编程实例N1 G92 X40 Z5 (设立坐标系,定义对刀点的位置)N2 M03 S400 (主轴以400r/min 旋转)N3 G96 S80 (恒线速度有效,线速度为80m/min)N4 G00 X0 (刀到中心,转速升高,直到主轴到最大限速)N5 G01 Z0 F60 (工进接触工件)N6 G03 U24 W-24 R15 (加工R15 圆弧段)N7 G02 X26 Z-31 R5 (加工R5 圆弧段)N8 G01 Z-40 (加工Φ26 外圆)N9 X40 Z5 (回对刀点)N10 G97 S300 (取消恒线速度功能,设定主轴按300r/min 旋转)N11 M30 (主轴停、主程序结束并复位)车床编程实例八%3317图3.3.17 G80 切削循环编程实例M03 S400 (主轴以400r/min 旋转)G91 G80 X-10 Z-33 I-5.5 F100(加工第一次循环,吃刀深3mm)X-13 Z-33 I-5.5(加工第二次循环,吃刀深3mm)X-16 Z-33 I-5.5(加工第三次循环,吃刀深3mm)M30 (主轴停、主程序结束并复位)5车床编程实例九G81 指令编程(点画线代表毛坯)图3.3.20 G81 切削循环编程实例%3320N1 G54 G90 G00 X60 Z45 M03 (选定坐标系,主轴正转,到循环起点)N2 G81 X25 Z31.5 K-3.5 F100 (加工第一次循环,吃刀深2mm)N3 X25 Z29.5 K-3.5 (每次吃刀均为2mm,)N4 X25 Z27.5 K-3.5 (每次切削起点位,距工件外圆面5mm,故K 值为-3.5)N5 X25 Z25.5 K-3.5 (加工第四次循环,吃刀深2mm)N6 M05 (主轴停)N7 M30 (主程序结束并复位车床编程实例十G82 指令编程(毛坯外形已加工完成)%3323N1 G55 G00 X35 Z104(选定坐标系G55,到循环起点)N2 M03 S300 (主轴以300r/min 正转)N3 G82 X29.2 Z18.5 C2 P180 F3(第一次循环切螺纹,切深0.8mm)N4 X28.6 Z18.5 C2 P180 F3(第二次循环切螺纹,切深0.4mm)N5 X28.2 Z18.5 C2 P180 F3(第三次循环切螺纹,切深0.4mm)N6 X28.04 Z18.5 C2 P180 F3(第四次循环切螺纹,切深0.16mm)N7 M30 (主轴停、主程序结束并复位)图3.3.23 G82 切削循环编程实例6车床编程实例十一外径粗加工复合循环编制图3.3.27 所示零件的加工程序:要求循环起始点在A(46,3),切削深度为1.5mm(半径量)。
数控车床编程实例详解(30个例子)(1)

车床编程实例一半径编程图3.1.1 半径编程%3110 (主程序程序名)N1 G92 X16 Z1 (设立坐标系,定义对刀点的位置)N2 G37 G00 Z0 M03 (移到子程序起点处、主轴正转)N3 M98 P0003 L6 (调用子程序,并循环6 次)N4 G00 X16 Z1 (返回对刀点)N5 G36 (取消半径编程)N6 M05 (主轴停)N7 M30 (主程序结束并复位)%0003 (子程序名)N1 G01 U-12 F100 (进刀到切削起点处,注意留下后面切削的余量)N2 G03 U7.385 W-4.923 R8(加工R8 园弧段)N3U3.215 W-39.877 R60 (加工R60 园弧段)N4 G02 U1.4 W-28.636 R40(加工切R40 园弧段)N5 G00 U4 (离开已加工表面)N6 W73.436 (回到循环起点Z 轴处)N7 G01 U-4.8 F100 (调整每次循环的切削量)N8 M99 (子程序结束,并回到主程序)直线插补指令编程图3.3.5 G01 编程实例%3305N1 G92 X100 Z10 (设立坐标系,定义对刀点的位置)N2 G00 X16 Z2 M03 (移到倒角延长线,Z 轴2mm 处)N3 G01 U10 W-5 F300 (倒3×45°角)N4 Z-48 (加工Φ26 外圆)N5 U34 W-10 (切第一段锥)N6 U20 Z-73 (切第二段锥)N7 X90 (退刀)N8 G00 X100 Z10 (回对刀点)N9 M05 (主轴停)N10 M30 (主程序结束并复位)车床编程实例三圆弧插补指令编程%3308N1 G92 X40 Z5 (设立坐标系,定义对刀点的位置)N2 M03 S400 (主轴以400r/min 旋转)N3 G00 X0 (到达工件中心)N4 G01 Z0 F60 (工进接触工件毛坯)N5 G03 U24 W-24 R15 (加工R15 圆弧段)N6 G02 X26 Z-31 R5 (加工R5 圆弧段)N7 G01 Z-40 (加工Φ26 外圆)N8 X40 Z5 (回对刀点)N9 M30 (主轴停、主程序结束并复位图3.3.8 G02/G03 编程实例倒角指令编程图3.3.10.1 倒角编程实例%3310N10 G92 X70 Z10 (设立坐标系,定义对刀点的位置)N20 G00 U-70 W-10 (从编程规划起点,移到工件前端面中心处)N30 G01 U26 C3 F100 (倒3×45°直角)N40 W-22 R3 (倒R3 圆角)N50 U39 W-14 C3 (倒边长为3 等腰直角)N60 W-34 (加工Φ65 外圆)N70 G00 U5 W80 (回到编程规划起点)N80 M30 (主轴停、主程序结束并复位)车床编程实例五倒角指令编程%3310N10 G92 X70 Z10 (设立坐标系,定义对刀点的位置)N20 G00 X0 Z4 (到工件中心)N30 G01 W-4 F100 (工进接触工件)N40 X26 C3 (倒3×45°的直角)N50 Z-21 (加工Φ26 外圆)N60 G02 U30 W-15 R15 RL=3(加工R15 圆弧,并倒边长为4 的直角)N70 G01 Z-70 (加工Φ56 外圆)N80 G00 U10 (退刀,离开工件)N90 X70 Z10 (返回程序起点位置)M30 (主轴停、主程序结束并复位)图3.3.10.2 倒角编程实例车床编程实例六圆柱螺纹编程螺纹导程为1.5mm,δ=1.5mm,δ'=1mm ,每次吃刀量(直径值)分别为0.8mm、0.6 mm 、0.4mm、0.16mm图3.3.12 螺纹编程实例%3312N1 G92 X50 Z120 (设立坐标系,定义对刀点的位置)N2 M03 S300 (主轴以300r/min 旋转)N3 G00 X29.2 Z101.5 (到螺纹起点,升速段1.5mm,吃刀深0.8mm)N4 G32 Z19 F1.5 (切削螺纹到螺纹切削终点,降速段1mm)N5 G00 X40 (X 轴方向快退)N6 Z101.5 (Z 轴方向快退到螺纹起点处)N7 X28.6 (X 轴方向快进到螺纹起点处,吃刀深0.6mm)N8 G32 Z19 F1.5 (切削螺纹到螺纹切削终点)N9 G00 X40 (X 轴方向快退)N10 Z101.5 (Z 轴方向快退到螺纹起点处)N11 X28.2 (X 轴方向快进到螺纹起点处,吃刀深0.4mm)N12 G32 Z19 F1.5 (切削螺纹到螺纹切削终点)N13 G00 X40 (X 轴方向快退)N14 Z101.5 (Z 轴方向快退到螺纹起点处)N15 U-11.96 (X 轴方向快进到螺纹起点处,吃刀深0.16mm)N16 G32 W-82.5 F1.5 (切削螺纹到螺纹切削终点)N17 G00 X40 (X 轴方向快退)N18 X50 Z120 (回对刀点)N19 M05 (主轴停)N20 M30 (主程序结束并复位)恒线速度功能编程%3314车床编程实例七图3.3.14 恒线速度编程实例N1 G92 X40 Z5 (设立坐标系,定义对刀点的位置)N2 M03 S400 (主轴以400r/min 旋转)N3 G96 S80 (恒线速度有效,线速度为80m/min)N4 G00 X0 (刀到中心,转速升高,直到主轴到最大限速)N5 G01 Z0 F60 (工进接触工件)N6 G03 U24 W-24 R15 (加工R15 圆弧段)N7 G02 X26 Z-31 R5 (加工R5 圆弧段)N8 G01 Z-40 (加工Φ26 外圆)N9 X40 Z5 (回对刀点)N10 G97 S300 (取消恒线速度功能,设定主轴按300r/min 旋转)N11 M30 (主轴停、主程序结束并复位)车床编程实例八%3317M03 S400 (主轴以400r/min 旋转)G91 G80 X-10 Z-33 I-5.5 F100(加工第一次循环,吃刀深3mm)X-13 Z-33 I-5.5(加工第二次循环,吃刀深3mm)X-16 Z-33 I-5.5(加工第三次循环,吃刀深3mm)M30 (主轴停、主程序结束并复位)图3.3.17 G80 切削循环编程实例车床编程实例九G81 指令编程(点画线代表毛坯)图3.3.20 G81 切削循环编程实例%3320N1 G54 G90 G00 X60 Z45 M03 (选定坐标系,主轴正转,到循环起点)N2 G81 X25 Z31.5 K-3.5 F100 (加工第一次循环,吃刀深2mm)N3 X25 Z29.5 K-3.5 (每次吃刀均为2mm,)N4 X25 Z27.5 K-3.5 (每次切削起点位,距工件外圆面5mm,故K 值为-3.5)N5 X25 Z25.5 K-3.5 (加工第四次循环,吃刀深2mm)N6 M05 (主轴停)N7 M30 (主程序结束并复位车床编程实例十G82 指令编程(毛坯外形已加工完成)%3323N1 G55 G00 X35 Z104(选定坐标系G55,到循环起点)N2 M03 S300 (主轴以300r/min 正转)N3 G82 X29.2 Z18.5 C2 P180 F3(第一次循环切螺纹,切深0.8mm)N4 X28.6 Z18.5 C2 P180 F3(第二次循环切螺纹,切深0.4mm)N5 X28.2 Z18.5 C2 P180 F3(第三次循环切螺纹,切深0.4mm)N6 X28.04 Z18.5 C2 P180 F3(第四次循环切螺纹,切深0.16mm)N7 M30 (主轴停、主程序结束并复位)图3.3.23 G82 切削循环编程实例车床编程实例十一外径粗加工复合循环编制图3.3.27 所示零件的加工程序:要求循环起始点在A(46,3),切削深度为1.5mm(半径量)。
数控车床编程实例详解(30个例子)

车床编程实例一半径编程图3.1.1 半径编程%3110 (主程序程序名)N1 G92 X16 Z1 (设立坐标系,定义对刀点的位置)N2 G37 G00 Z0 M03 (移到子程序起点处、主轴正转)N3 M98 P0003 L6 (调用子程序,并循环6 次)N4 G00 X16 Z1 (返回对刀点)N5 G36 (取消半径编程)N6 M05 (主轴停)N7 M30 (主程序结束并复位)%0003 (子程序名)N1 G01 U-12 F100 (进刀到切削起点处,注意留下后面切削的余量)N2 G03 U7.385 W-4.923 R8(加工R8 园弧段)N3U3.215 W-39.877 R60 (加工R60 园弧段)N4 G02 U1.4 W-28.636 R40(加工切R40 园弧段)N5 G00 U4 (离开已加工表面)N6 W73.436 (回到循环起点Z 轴处)N7 G01 U-4.8 F100 (调整每次循环的切削量)N8 M99 (子程序结束,并回到主程序)1直线插补指令编程%3305车床编程实例二图3.3.5 G01 编程实例N1 G92 X100 Z10 (设立坐标系,定义对刀点的位置)N2 G00 X16 Z2 M03 (移到倒角延长线,Z 轴2mm 处)N3 G01 U10 W-5 F300 (倒3×45°角)N4 Z-48 (加工Φ26 外圆)N5 U34 W-10 (切第一段锥)N6 U20 Z-73 (切第二段锥)N7 X90 (退刀)N8 G00 X100 Z10 (回对刀点)N9 M05 (主轴停)N10 M30 (主程序结束并复位)圆弧插补指令编程车床编程实例三%3308N1 G92 X40 Z5 (设立坐标系,定义对刀点的位置)N2 M03 S400 (主轴以400r/min 旋转)N3 G00 X0 (到达工件中心)N4 G01 Z0 F60 (工进接触工件毛坯)N5 G03 U24 W-24 R15 (加工R15 圆弧段)N6 G02 X26 Z-31 R5 (加工R5 圆弧段)N7 G01 Z-40 (加工Φ26 外圆)N8 X40 Z5 (回对刀点)N9 M30 (主轴停、主程序结束并复位图3.3.8 G02/G03 编程实例2倒角指令编程%3310车床编程实例四图3.3.10.1 倒角编程实例N10 G92 X70 Z10 (设立坐标系,定义对刀点的位置)N20 G00 U-70 W-10 (从编程规划起点,移到工件前端面中心处)N30 G01 U26 C3 F100 (倒3×45°直角)N40 W-22 R3 (倒R3 圆角)N50 U39 W-14 C3 (倒边长为3 等腰直角)N60 W-34 (加工Φ65 外圆)N70 G00 U5 W80 (回到编程规划起点)N80 M30 (主轴停、主程序结束并复位)倒角指令编程%3310车床编程实例五N10 G92 X70 Z10 (设立坐标系,定义对刀点的位置)N20 G00 X0 Z4 (到工件中心)N30 G01 W-4 F100 (工进接触工件)N40 X26 C3 (倒3×45°的直角)N50 Z-21 (加工Φ26 外圆)N60 G02 U30 W-15 R15 RL=3(加工R15 圆弧,并倒边长为4 的直角)N70 G01 Z-70 (加工Φ56 外圆)N80 G00 U10 (退刀,离开工件)N90 X70 Z10 (返回程序起点位置)M30 (主轴停、主程序结束并复位)图3.3.10.2 倒角编程实例3车床编程实例六圆柱螺纹编程螺纹导程为1.5mm,δ=1.5mm,δ'=1mm ,每次吃刀量(直径值)分别为0.8mm、0.6 mm 、0.4mm、0.16mm图3.3.12 螺纹编程实例%3312N1 G92 X50 Z120 (设立坐标系,定义对刀点的位置)N2 M03 S300 (主轴以300r/min 旋转)N3 G00 X29.2 Z101.5 (到螺纹起点,升速段1.5mm,吃刀深0.8mm)N4 G32 Z19 F1.5 (切削螺纹到螺纹切削终点,降速段1mm)N5 G00 X40 (X 轴方向快退)N6 Z101.5 (Z 轴方向快退到螺纹起点处)N7 X28.6 (X 轴方向快进到螺纹起点处,吃刀深0.6mm)N8 G32 Z19 F1.5 (切削螺纹到螺纹切削终点)N9 G00 X40 (X 轴方向快退)N10 Z101.5 (Z 轴方向快退到螺纹起点处)N11 X28.2 (X 轴方向快进到螺纹起点处,吃刀深0.4mm)N12 G32 Z19 F1.5 (切削螺纹到螺纹切削终点)N13 G00 X40 (X 轴方向快退)N14 Z101.5 (Z 轴方向快退到螺纹起点处)N15 U-11.96 (X 轴方向快进到螺纹起点处,吃刀深0.16mm)N16 G32 W-82.5 F1.5 (切削螺纹到螺纹切削终点)N17 G00 X40 (X 轴方向快退)N18 X50 Z120 (回对刀点)N19 M05 (主轴停)N20 M30 (主程序结束并复位)4恒线速度功能编程%3314车床编程实例七图3.3.14 恒线速度编程实例N1 G92 X40 Z5 (设立坐标系,定义对刀点的位置)N2 M03 S400 (主轴以400r/min 旋转)N3 G96 S80 (恒线速度有效,线速度为80m/min)N4 G00 X0 (刀到中心,转速升高,直到主轴到最大限速)N5 G01 Z0 F60 (工进接触工件)N6 G03 U24 W-24 R15 (加工R15 圆弧段)N7 G02 X26 Z-31 R5 (加工R5 圆弧段)N8 G01 Z-40 (加工Φ26 外圆)N9 X40 Z5 (回对刀点)N10 G97 S300 (取消恒线速度功能,设定主轴按300r/min 旋转)N11 M30 (主轴停、主程序结束并复位)车床编程实例八%3317M03 S400 (主轴以400r/min 旋转)G91 G80 X-10 Z-33 I-5.5 F100(加工第一次循环,吃刀深3mm)X-13 Z-33 I-5.5(加工第二次循环,吃刀深3mm)X-16 Z-33 I-5.5(加工第三次循环,吃刀深3mm)M30 (主轴停、主程序结束并复位)图3.3.17 G80 切削循环编程实例5车床编程实例九G81 指令编程(点画线代表毛坯)图3.3.20 G81 切削循环编程实例%3320N1 G54 G90 G00 X60 Z45 M03 (选定坐标系,主轴正转,到循环起点)N2 G81 X25 Z31.5 K-3.5 F100 (加工第一次循环,吃刀深2mm)N3 X25 Z29.5 K-3.5 (每次吃刀均为2mm,)N4 X25 Z27.5 K-3.5 (每次切削起点位,距工件外圆面5mm,故K 值为-3.5)N5 X25 Z25.5 K-3.5 (加工第四次循环,吃刀深2mm)N6 M05 (主轴停)N7 M30 (主程序结束并复位车床编程实例十G82 指令编程(毛坯外形已加工完成)%3323N1 G55 G00 X35 Z104(选定坐标系G55,到循环起点)N2 M03 S300 (主轴以300r/min 正转)N3 G82 X29.2 Z18.5 C2 P180 F3(第一次循环切螺纹,切深0.8mm)N4 X28.6 Z18.5 C2 P180 F3(第二次循环切螺纹,切深0.4mm)N5 X28.2 Z18.5 C2 P180 F3(第三次循环切螺纹,切深0.4mm)N6 X28.04 Z18.5 C2 P180 F3(第四次循环切螺纹,切深0.16mm)N7 M30 (主轴停、主程序结束并复位)图3.3.23 G82 切削循环编程实例6车床编程实例十一外径粗加工复合循环编制图3.3.27 所示零件的加工程序:要求循环起始点在A(46,3),切削深度为1.5mm(半径量)。
数控车床编程基本学习-PPT
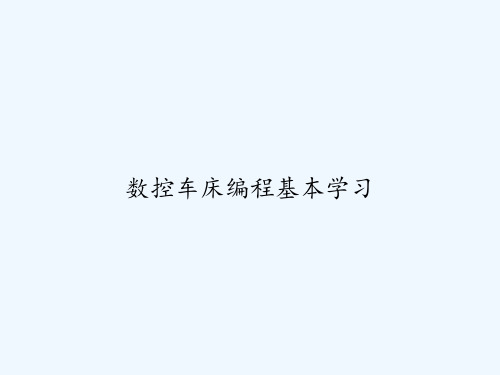
X 中间点
O
参考点R
刀尖当前位置 Z
图3-5 自动返回参考点
6、螺纹切削指令(G32)
指令格式 G32 X(U)_ Z(W)_ F(E)_ 指令功能 切削加工圆柱螺纹、圆锥螺纹和平面螺纹(涡形螺纹) 。
指令说明 1)F—公制螺纹的导程
E—英制螺纹的导程
2)F表示长轴方向的导程 如果X轴方向为长轴,F为半径值。 对于圆锥螺纹,其斜角α在450以下时,Z轴方向为长轴;
2
U
2
X
O
Z
图3-12 G94车削端面固定循环
G94指令车削圆锥面时的程序段格式如下:
G94 X(U)_Z(W)_R_F_;
其中,R为端面斜度线在Z轴的投影距离。若顺序动作2的 进给方向在Z轴的投影方向和Z轴方向一致,则R取负值;若顺 序动作2的进给方向在Z轴的投影方向和Z轴方向相反,则R取正 值。在图3-13中,因为顺序动作2的进给方向在Z轴的投影方向 和Z轴方向一致,所以R取负值。
必须注意的是,执行G27指令的前提是机床在通电后刀具 返回过一次参考点(手动返回或者用G28指令返回)。此外,使 用该指令时,必须预先取消刀具补偿的量。
执行G27指令之后,如欲使机床停止,须加入一辅助功能 指令M00,否则,机床将继续执行下一个程序段。
2) 自动返回参考点指令G28 G28指令可以使刀具从任何位置以快速点定位方式经过中间 点返回参考点。 格式:G28 X _Z _; 其中,X、Z是中间点的坐标值。 执行该指令时,刀具先快速移动到指令值所指定的中间点, 然后自动返回参考点,相应坐标轴指示灯亮。 和G27指令相同,执行G28指令前,应取消刀具补偿功能。 G28指令的执行过程如图3-5所示。
(3)参数的输入 假想刀尖的位置如下图3-10:
数控车床编程实例详解

车床编程实例一半径编程半径编程(主程序程序名)(设立坐标系,定义对刀G37 GOO Z0 M03 (移至UN3 M98 P0003(调用子程序,并循环6(返回对刀点)(取消半径编程)(主轴停)(主程序结束并复位)(子程序名)(进刀到切削起点处,注意留下后面切削的N2 G03 U7.385 4.923 R8 (加工R8园弧段)N3 U3.215 39.877 R60(加工R60园弧段)N4 G02 U1.4 28.636 R40(加工切R40园弧段)N5 GOO U4(离开已加工%3110N1 G92 X16 Z1点的位置)N2子程序起点处、主轴正转)L6次)N4 GOO X16 Z1N5 G36N6 MO5N7 M3O%OOO3N1 GO1 12 F1OO余量)(移到表面)N6 W73.436N7 G01 4.8 F100N8 M99(调整每环起点2(子程序结束,并回到主程序)图 3.3.5 G01 编程实例%3305N1 G92 X100 Z10(设立坐标系,定义对刀点的位置)N2 G00 X16 Z2 M03 (移到倒角延长 线,Z 轴2处)N3 G01 U10 5 F300 (倒 3X 45° 角) N4 48 (加工①26外圆)N5 U34 10 (切第一段 锥)N6 U20 73 (切 第二段锥)N7 X90 (退刀)N8 G00 X100 Z10(回对刀占)N9 M05(主轴停)N10 M30(主程序结束并复位)车床编程实例三圆弧插补指 令编程(设立坐标系,定义对刀点的位置) (主轴以400旋转)(到达工件中心) 直线插补指 令编程 车床编程实例二■&q li%3308N1 G92 X40 Z5 N2 M03 S400 N3 G00 X0 N4 G01 Z0 F60工进接触工件毛坯)(加工R15圆弧段)(加工R5圆弧段)N5 G03 U24 24 R15N6 G02 X26 31 R52图3.3.8 G0203 编程实 例N7 G01 40 N8 X40 Z5 N9 M30 (加工①26外圆)(主轴停回对刀点序结束并复位3%3310N10 G92 X70 Z10 (设立坐标系,定义对刀点的位置) N20 G00 70 10 (从编程规划起点,移到工件前端面中心处) N30 G01 U26 C3 F100 (倒 3X 45° 直角) N40 22 R3 (倒 R3 圆角)N50 U39 14 C3 (倒边长为3等腰直角) N60 34 (加工①65外圆) N70 G00 U5 W80 (回到编程规划起点) N80 M30 (主轴停、主程序结束并复位)车床编程实例五倒角指令 编程%3310N10 G92 X70 Z10 (设立坐标系,定义对刀点的位置) N20 G00 X0 Z4 (至U 工件中 心)N30 G01 4 F100(工进接触工件)N40 X26 C3 (倒 3 X 45° 的 直角)N50 21 (加工①26外 圆)N60 G02 U30 15 R15 3(加工R15圆弧,并倒边长为4的直角) N70 G01 70 (加工① 56 外圆)N80 G00 U10倒角指令 编程车床编程实例四角编程实例(退刀,离开工件)N90 X70 Z10 (返回程序起点位置)M30 (主轴停、主程序结束并复位)图3.3.10.2 倒角编程实例3车床编程实例六圆柱螺纹编程螺纹导程为 1.5 , 5 =1.5 , 5 '=1 ,每次吃刀量(直径值)分别为0.8、0.6 、0.4、0.16100图3.3.12 螺纹编程实例3%3312N1 G92 X50 Z120 (设立坐标系,定义对刀点的位置) N2 M03 S300 (主轴以300旋转) N3 G00 X29.2 Z101.5 (到螺纹起点,升速段 1.5,吃刀深 0.8)N4 G32 Z19 F1.5 (切削螺纹到螺纹切削终点,降速段N5 G00 X40 (X 轴方向快退) N6 Z101.5 (Z 轴方向快退到螺纹起点处) N7 X28.6 (X 轴方向快进到螺纹起点处,吃刀深 N8 G32 Z19 F1.5 (切削螺纹到螺纹切削终点 N9 G00 X40 (X 轴方向快退) N10 Z101.5 (Z 轴方向快退到螺纹起点处) N11 X28.2 (X 轴方向快进到螺纹起点处,吃刀深 N12 G32 Z19 F1.5 (切削螺纹到螺纹切削终点 N13 G00 X40 (X 轴方向快退) N14 Z101.5 (Z 轴方向快退到螺纹起点处)N15 11.96 (X 轴方向快进到螺纹起点处,吃刀深N16 G32 82.5 F1.5 (切削螺纹到螺纹切削终点)N17 G00 X40N18 X50 Z120 N19 M05 N20 M300.6) 0.4) 0.16) (X 轴方向快退) (回对刀点) (主轴停) 主程序结束并复位)恒线速度功 能编程车床编程实例七图3.3.14 恒线速 度编程实例%3314N1 G92 X40 Z5 N2 M03 S400 N3 G96 S80 N4 G00 X0 速) N5 G01 Z0 F60 —件)N6 G03 U24 24 R15 (加工 N7 G02 X26 31 加工R5圆 (加 N9 X40 Z5(设立坐标系,定义对刀点的位置) 主轴以400旋转)(恒线速度有效,线速度为 80)刀到中心,转速升高,直到主轴到最大限(工进接触工 R15圆弧段) R5 弧段)N8 G01 40 工①26外圆) N10 G97 S300 转) N11 M30 c 取消刀线速度功能,设定主轴按~~30O 「(主轴停、主程 车床编程实例八%3317 M03 S400(主轴以400旋转)G91 G80 10 33 5.5 F100(加工第一次循环,吃 刀深3)序结Se—g陛33 ——一」养加窮二次循环,吃16 33 5.5(加工第三次循环,吃 刀深3)M30 (主轴停、主程序结束并复位)图3.3.17 G80 切削循环编程实例5车床编程实例九G81指令编程(点画线代表毛坯)图 3.3.20%3320N1G54 G90 GOO X60 Z45 M03 (选定坐标系,主轴正转,到循加工第一次循环,吃刀深 (每次吃刀均为2,) (每次切削起点位,距工件外圆面 (加工第四次循环,吃刀深 2) (主轴停) (主程序结束并复位 车床编程实例十G82指令编程(毛坯外形已加工完成) %3323 N1 G55 GOO X35 Z104(选定坐标系G55,到 循环起点)N2 M03 S300 (主轴以300正转)N3 G82 X29.2 Z18.5 C2 P180(第一次循环切螺纹,切深 0.8)N4 X28.6 Z18.5 C2 P180 F3(第二次循环切螺纹,切深 0.4)N5 X28.2 Z18.5 C2 P180 F3(第三次循环切螺纹,切深 0.4)N6 X28.04 Z18.5 C2 P180 F3(第四次循环切螺纹,切 深0.16 )G81切削循环编程实例环起点)N2 G81 X25 Z31.5 3.5 F100 N3 X25 Z29.5 3.5N4 X25 Z27.5 3.5K 值为-3.5)N5 X25 Z25.5 3.5N6 M05N7 M305,故 __ 4》 __________soN7 M30 (主轴停、主程序结束并复位)图3.3.23 程G82 切削循环编实例6车床编程实例十一外径粗加工复合循环编制图 3.3.27 所示零件的加工程序:要求循环起始点在A (46,3几切削深度为1.5 (半径量)。
数控车床编程
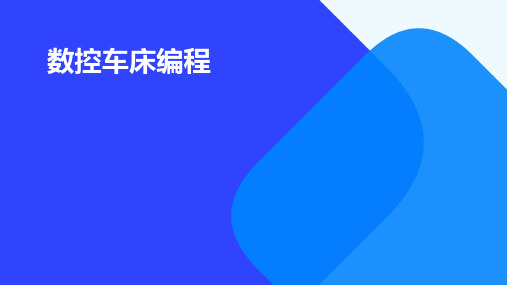
T代码编程语言
T代码编程语言主要用于刀具参数的设置和管理,如刀具号、刀具补偿值 等。
T代码编程语言可以提高加工精度和加工效率,通过合理设置刀具参数, 可以减少换刀次数和加工误差。
T代码编程语言需要在G代码编程语言的基础上使用,以实现完整的加工过 程控制。
03
数控车床编程实例
简单零件的数控车床编程
04
数控车床编程技巧
优化加工路径
减少空行程
在编程时,应尽量减少刀具在空行程中的移动距离,以提高加工效 率。
合理选择切削参数
根据工件材料、刀具类型和加工要求,合理选择切削速度、进给速 度和切削深度等参数,以优化加工效率和加工质量。
考虑刀具补偿
在编程时,应考虑刀具的长度、直径和刀尖半径等参数,进行适当 的补偿,以减小加工误差。
ABCD
第二步是确定加工方案, 包括选择合适的刀具、切 削参数、加工路径等。
第四步是程序调试和优化, 通过实际加工测试和调整, 确保程序能够满足加工要 求。
数控车床编程的注意事项
注意事项一
确保刀具路径的安全性,避免 刀具与工件发生碰撞。
注意事项二
合理选择切削参数,以减小刀 具磨损和保证加工质量。
注意事项三
据,优化生产计划和调度。
跨平台协作
在工业4.0中,数控车床编程将实现与其他制造系统的跨平台 协作,实现数据共享和流程整合,提高生产效率和灵活性。
数控车床编程的未来发展方向
人工智能与机器学习技术的应用
01
未来数控车床编程将更加注重人工智能和机器程。
个性化定制的需求满足
02
随着个性化需求的增加,数控车床编程将更加注重个性化定制,
满足不同加工需求和工艺要求。
数控车床编程教学
数控车床编程教学
一、引言
数控车床是一种自动化机床,其编程是数控车床操作的核心。
掌握数控车床编程可提高生产效率、加工精度,本文将系统介绍数控车床编程教学内容。
二、基础知识
1. 数控车床概述
数控车床是一种通过预先输入数控程序指令,控制车床自动进行加工的机床。
2. 基本编程原理
数控车床编程原理是根据加工要求编写G代码,通过解析G代码来控制车床实现自动加工。
三、编程环境搭建
1. 需要工具
•数控车床
•编程软件
2. 编程流程
1.制定加工方案
2.编写G代码
3.上传程序到数控车床
4.执行加工
四、常用G代码指令
1. G00:快速移动
•示例:G00 X100 Y50 Z30
2. G01:直线插补
•示例:G01 X50 Y40 Z20 F100
3. G02/G03:圆弧插补
•示例:G02 X50 Y40 Z20 I10 J5 F100
五、实例分析
通过一个实际加工案例,演示数控车床编程的具体步骤与应用。
六、常见错误与调试
介绍常见的数控车床编程错误及调试方法,帮助读者更好地应对实际操作中的问题。
结语
数控车床编程是一项重要的技能,在现代制造业中发挥着重要作用。
通过本文的学习,读者可以掌握数控车床编程的基本原理与实践技巧,提高生产效率与加工质量。
希望读者可以在实践中不断提升,更好地应用于实际生产中。
数控车床编程实例详解(30个例子)
数控车床编程实例详解(30个例子)1. 基础G00轨迹移动G00指令可以用于快速移动机床上的工具,不做切削。
例如,要将铣刀从(0,0,0)点移动到(100,100,0)可以使用下面的编程:G00 X100 Y100 Z02. 简单的G01直线插补3. 向X正方向设定工件原点在某些情况下,需要在工件上设计的特定原点作为整个程序的起点。
在下面的例子中,我们将工件原点移到X轴上的10毫米位置:G92 X104. G02 G03 模拟圆弧G02和G03指令可以用于沿着一条圆弧轨迹移动工具。
例如,以下代码将插入一个逆时针圆弧:G03 X50 Y50 I25 J05. 床上对刀长度测量刀具长度对刀是数控车床操作的重要步骤。
在这个例子中,我们使用手动设定对刀。
首先,我们将铣刀移动到Z轴处的一个位置,然后将刀具轻轻放置在工件上以测量其长度。
最后,我们将刀具测量值输入机床,以便于适当地调整刀具长度。
6. 坐标旋转在某些情况下,需要在XY平面上绕特定角度旋转工件,以便于确保最佳切削角度。
在这个例子中,我们将工件绕着Z轴旋转45度:G68 X0 Y0 R457. 使用M code 启动或停止旋转工件M03用于启动旋转工作台的主轴,M05用于关闭它。
例如,以下代码段启动了工作台的主轴,并等待它旋转到合适速度,以便于切削。
8. 镜像轨迹在制造工具或零件时,可能需要将一个轮廓沿着特定轴镜像。
例如,以下代码镜像X 轴上的轮廓:G01 X50 Y0G01 X0 Y50G01 X-50 Y0G01 X0 Y-50MHE29. 使用G04指令延迟程序G04指令用于程序内部的延迟。
例如,以下代码让机床停顿1秒钟:G04 P100010. 利用G10指令改变工作坐标系G10指令可以用于更改工作坐标系。
例如,下面的代码段将当前坐标系设定为{X50 Y50 Z0}:11. 使用G17, G18和G19指令绘制园形、X-Y平面和Z-X平面G17G02 X50 Y50 I25 J0G02 X0 Y0 I-25 J0G02 X-50 Y50 I0 J25G02 X0 Y100 I25 J0G02 X50 Y50 I0 J-25G02 X0 Y0 I-25 J0MHE2M30指令可以用于彻底结束程序。
数控车床基本指令编程
3.G00指令应用举例 G00指令应用举例
绝对值编程:G00 X120.0 Z100.0; 增量值编程:GOO U80.0 W80.0;
三、直线插补指令编程(G01) 直线插补指令编程( )
1.指令格式
X( G01 X(U) Z( W) F ; ●G01指令是模态代码 G01指令是模态代码 G01指令是模态代码,它是直线运动的命令, 规定刀具在两坐标或三坐标间以插补联动方式 按F指定的进给速度作任意斜率的直线运动。 ●绝对值编程时 绝对值编程时,刀具以F指令的进给速度进 绝对值编程时 行直线插补,运动到工件坐标系X、Z点; ●增量值编程时 增量值编程时,刀具以F进给速度运动到距 增量值编程时 离现有位置为U、W的点。 ●F进给速度在没有新的F指令以前一直有效 F进给速度在没有新的F指令以前一直有效, 不必在每个程序段中都写入F指令。
(3)尺寸字 尺寸字用于确定机床上刀具运动终点的坐标位置。 其中,第一组 X,Y,Z,U,V,W,P,Q,R 用于确定终 点的直线坐标尺寸;第二组 A,B,C,D,E 用于确定终点的角 度坐标尺寸;第三组 I,J,K 用于确定圆弧轮廓的圆心坐标尺 寸。在一些数控系统中,还可以用P指令暂停时间、用R指令圆 弧的半径等。 (4)进给功能字F 进给功能字F 进给功能字的地址符是F,又称为F功能或F指令,用于指定 切削的进给速度。对于车床,F可分为每分钟进给和主轴每转进 给两种,对于其它数控机床,一般只用每分钟进给。F指令在螺 纹切削程序段中常用来指令螺纹的导程。
3.G01指令应用举例 (2) G01指令应用举例
O2002(已调试) T0101; M03 S400; G00 X31.0 Z3.0; G01 Z-50.0 F80.0; X36.0; Z3.0; X30.0; Z-50.0; X36.0; G00 X100.0 Z50.0; M05; M30;
数控车床的编程与操作讲义
数控车床的编程与操作讲义数控车床的编程与操作数控车床是⼀种⾼精度、⾼效率的⾃动化机床,也是使⽤数量最多的数控机床,⼤约占数控机床总数的25%。
本讲义以FANUC0TD系统为例介绍数控车床的编程与操作。
1.数控车床加⼯的基本知识1.1 数控车床的分类1.1.1 按主轴的布置形式分类:(1)卧式数控车床:机床主轴轴线处于⽔平位置数控车床。
(2)⽴式数控车床:机床主轴轴线处于垂直位置数控车床。
1.1.2 按数控系统控制的轴数分类:(1)两轴控制的数控车床:机床上只有⼀个回转⼑架,可实现X、Z两坐标轴联动控制。
(2)四轴控制数控车床:机床上只有两个回转⼑架,可实现X、Z和U、W四坐标轴联动控制。
(3)多轴控制数控车床:机床除了控制X、Z两坐标轴外,还可以控制其他坐标轴,实现多轴控制,如具有C轴控制功能。
对于车削加⼯中⼼或柔性制造单元,都具有多轴控制功能。
1.2 数控车床的加⼯特点1、适应性强,⽤于单件、⼩批⽣产的零件的加⼯在普通车床上加⼯不同的零件,⼀般需要调整车床和附件,以使车床适应加⼯零件的要求。
⽽数控车床加⼯不同形状的零件时只要重新编制或修改加⼯程序就可以迅速达到加⼯要求,⼤⼤缩短了⽣产准备时间。
2、加⼯精度⾼,加⼯出的零件互换性好数控加⼯的尺⼨精度通常在0.005~0.1mm之间,不受零件复杂程度的影响。
加⼯中消除了操作者的⼈为误差,提⾼了同批零件尺⼨的⼀致性,使产品质量保持稳定,降低了废品率。
3、具有较⾼的⽣产率和较低的加⼯成本机床的⽣产率主要是指加⼯⼀个零件所需要的时间。
其中包括机动时间和辅助时间。
数控车床的主轴转速和进给速度变化范围⼤,并可⽆级调速,加⼯时可选⽤最佳切削速度和进给速度,可实现恒转速(G97)和恒线速(G96),以使切削参数最优,这就⼤⼤的提⾼⽣产率,降低了加⼯成本。
1.3 数控车床的主要⽤途数控车床主要⽤于加⼯精度要求⾼、表⾯粗糙度值要求⼩,零件形状复杂,单件、⼩批⽣产的轴套类、盘类等回转表⾯的加⼯;还可以钻孔、扩孔、镗孔以及切槽加⼯;还可以在内、外圆柱⾯上,内、外圆锥⾯上加⼯各种螺距的螺纹。
- 1、下载文档前请自行甄别文档内容的完整性,平台不提供额外的编辑、内容补充、找答案等附加服务。
- 2、"仅部分预览"的文档,不可在线预览部分如存在完整性等问题,可反馈申请退款(可完整预览的文档不适用该条件!)。
- 3、如文档侵犯您的权益,请联系客服反馈,我们会尽快为您处理(人工客服工作时间:9:00-18:30)。
• M03,M04和M05为一组指令,在执行时 一直有效,直到被同组的指令取代,如指 令M03被M04(或M05)取代。 • 编程举例: 设置刀具进给速度为 400mm/min,主轴转速为300r/min,主 轴正转,刀具沿直线插补,主轴反转,刀 具继续沿直线插补,编程如下:
• N30 G01 X20. Z60. F400 S300 M03; 主轴正转直线插补 • N40 M05; 主轴停转 • N50 G01 X70. Z50. M04;主轴反转, 继续直线插补 • 提示:在指令M03和M04之间转换时(主轴 正反转切换时)一般要求使用指令M05(主 轴停)来进行过渡。
•1 主轴功能S___ 1) 主轴功能S控制主轴转速,其后的数 值表示主轴速度,单位由G96、G97决 定; 2) G96 S___表示主轴恒线速度旋转, S指定切削线速度,其后的数值单位为: 米/每分钟(m/min)。常与G50 S___连 用,以限制主轴的最高转速。(G96恒 线速度有效,G97取消恒线速度)模态 指令 。
(回对刀点)
(主轴停止)
(程序结束并复位)
6、G02顺圆插补、G03逆圆插补 格式:G02/G03 X__Z__I__K__(R__)F__ 说明: 1) G02为顺圆插补;G03为逆圆插补,用 以在指定平面内按设定的进给速度沿圆弧 轨迹切削; 2) 圆弧顺时针(或逆时针)旋转的判别方 式为:利用右手定则为工作坐标系加上Y 轴,沿Y轴正向往负向看去,顺时针方向 用G02,反之用G03,如下图:
• 3) G99 F__进给速度单位是每转进给量 (mm/r),范围0.0001~500.0000(mm/r), 系统默认; • 4) G32/G76/G92 F__ 指定螺纹的螺距, 范围0.0001~500.0000(mm/r)。
• 5) 借助于机床控制面板上的倍率按键, F可在一定范围内进行修调,当执行螺纹 切削循环G76、G92及螺纹切削G32 时,倍率开关失效,进给倍率固定在 100%。 • 6) F为续效指令,直到被新的 F值所取 代,而工作在 G00方式下,快速定位的 速度是各轴的最高速度,与所编 F无关。
3 刀具功能――T 说明: 1)T代码用于选刀,其后的 4 位数字分别 表示选择的刀具号和刀具补偿号; 2)执行 T 指令,转动转塔刀架,选用指定 的刀具; 3)当一个程序段同时包含 T 代码与刀具移 动指令时,先执行 T 代码指令,而后执行 刀具移动指令;
• 4)刀具的补偿包括刀具偏置补偿、刀 具磨损补偿及刀尖圆弧半径补偿,刀 尖位置; • 5)T指令同时调入刀补寄存器中的补 偿值。刀尖圆弧补偿号与刀具偏置补 偿号对应; • 6)取消刀补 T__00。
倒直角 绝对坐标指令: N0001 N0005 N0010 G01 Z-20. C4 F0.4; X50. C2; Z-40.
倒圆角
相对坐标指令:
N0001 N0005 N0010 G01 W-22. R4.; U30. R2.; W-20.
如图2 所示,用直线插补指令编程。
%3306
N10 G00 X0 Z0 M03;(移到倒角延 长线)
图 3 G02/G03 参数说明
例1: 如图所示,加工圆弧AB、BC,加工路线为C→B→A, 采用圆心和终点(I、K)的方式编程。
1)绝对编程
N20 N30
G03 X120. Z70. I0 K-40.;加工BC G02 X88. Z38. I0 K-20.;加工AB
G00 X40. Z110.; G03 U80. W-40. I0 K-40. F200;(R40) G02 U-32. W-32. I0 K-20.;(R20)
但为了提高刀具的使用寿命和降低加工工件的表面粗 糙度,通常将刀尖磨成半径不大的圆弧(一般圆弧半径R是 0.2—1.6之间,球头车刀可达4mm),如图1b所示X向和Z 向的交点P称为假想刀尖,该点是编程时确定加工轨迹的点, 数控系统控制该点的运动轨迹。然而实际切削时起作用的 切削刃是圆弧的切点A、B,它们是实际切削加工时形成工 件表面的点。很显然假想刀尖点P或圆心与实际切削点A、B 是不同的点,所以如果在数控加工或数控编程时不对刀尖 圆角半径进行补偿,仅按照工件轮廓进行编制的程序来加 工,势必会产生加工误差,如图3所示。
2) 相对编程
N10 N20 N30
7、G40、G41、G42 刀尖半径补偿取消,左偏刀尖半 径补偿,右偏刀尖半径补偿
刀尖圆弧补偿的引出:
• 编制数控车床加工程序时,理论上是将车刀刀尖看成一个点, 按这个刀尖点或圆心来编程,如图1a所示的P点就是理论刀尖, 图2为刀尖放大图。
(a )
(b)
图1 圆头刀假想刀尖 图2 刀尖圆弧放大图
指令列表 • 1、主轴功能S • 2、进给功能F • 3、刀具功能T
• 4、辅助功能M
• 5、快速定位G00 • 6、直线插补G01
• 7、顺圆插补G02、逆圆插补G03 • 8、刀尖半径补偿取消G40 、左偏刀尖半径 补偿G41 ,右偏刀尖半径补偿G42
• 9、自动回参考点 G28 • 10、暂停指令 G04 • 11、单一固定循环指令G90、G92、G94 • 12、复合固定循环指令G70、G71、G72
N20 G01 X26. C3.;(倒3×45°角)
N30 Z-48.;
图2 G01编程实例
(加工Φ 26 外圆) (切第一段锥) (切第二段锥) (退刀)
N40 U34. W-10.; N50 U20. Z-73.; N60 X90.;
N70 G00 X100. Z10.;
N: • N5G98F10;(车削进给速度为10mm/min)
图1 每转进给量 图2 每分钟转进给量 图3 螺纹切削
例 4: ( 车削进给速度 0.2mm/r) • N5G99F0.2; 例 5: • N5G32F5; (螺纹螺距为5mm)
M 代码及功能表
代码 模 态 功 能 说 明 代码 M00 M02 非模 态 非模 态 非模 态 程序暂停 程序结束 M03 M04 模态 功 能 说 明 模态 模态 主轴正转 主轴反转
例:命令刀具从点A快速移动到点B,编程如下:
N20 G90 G00 X60.Z25.;或 N20 G00 U40.W15.;或 N20 G00 X60.W15.;或 N20 G00 U40.Z25.;
G00移动方式 图
• 刀具的移动方式有三种: 1) 各轴以其最快的速度同时移动,通常 情况下因速度和移动距离的不同先后到达 目标点,刀具移动路线为任意的。 • 2) 各轴按设定的速度以联动的方式移动 到位,刀具移动路线为一条直线。 3) 各轴按输入的坐标字顺序分别快速移 动到位,刀具的移动路线为阶梯形。
图2 G02/G03插补方向
3)I、K分别为平行于X、Z的轴,用来表示 圆心的坐标,因为I,K后面数值为圆弧 起点到圆心矢量的分量(圆心坐标-起 点坐标),故始终为增量值, I始终为 半径增量值 。 4) 当已知圆弧终点坐标和半径,可以选取 半径编程的方式插补圆弧,R为圆弧半 径,当圆心角小于180度时R为正;大于 180度时R为负。
4、快速定位指令 G00 格式:G00 X(U)___ Z(W)___ 说明: 1)X、Z:为绝对编程时,快速定位终 点在工件坐标系中的坐标。X向为直径编 程。因为测量和图纸上的零件尺寸均以直 径值表示,所以用直径值编程。为提高工 件的径向尺寸精度,X向的脉冲当量可取 Z向的一半。
• 2)U、W:为增量编程时,快速定位 终点相对于起点的位移量。U向为直径 编程。 • 3)G00 指令刀具相对于工件以各轴 预先设定的速度,从当前位置快速移 动到程序段指令的定位目标点,不能 用 F-规定。快移速度可由面板上 的 “快速修调”修正。 • 4)同一程序行中X、U、 Z、W可以 混合编程。
图4 刀具补偿画面
格式:G40/G41/G42 (G00/G01)X__ Z__
说明:
1) 补偿方向的判断:逆着Y轴看,沿着刀具
前进的方向看,刀具在工件左侧为左刀补 G41,在右侧为右刀补G42; 2) 在车床刀具补偿设定的画面中,包括刀具 位臵补偿、刀尖半径补偿、假想刀尖位臵 序号。即除了输入刀具位臵,刀头圆角半 径外,还应输入假想刀尖相对于圆头刀中 心的位臵,这是因为内、外圆车刀或左、 右偏刀的刀尖位臵不同,假想刀尖位臵序 号共有10个(1~8,0,9),如图5所示, 均看成后臵刀架。
例 1: (主轴以600m/min的恒 • N5G96S600; 线速度旋转) • N10G50S1200; (主轴的最高转速为 1200r/min ) 例 2: • N5G97S600; (主轴以600r/min的转速旋转)
2 进给功能 F
• 1) F指令表示工件被加工时刀具相对于工 件的合成进给速度,其后的数值表示刀具 进给速度,单位由G99、G98及G32、G76、 G92决定。 • 2) G98 F__进给速度单位是每分钟进给量 (mm/min),范围1~15000(mm/min);
加工图1所示工件的锥面部分。
一、直径编程 O3351 N1 G00 X20. W-44.; N5 G01U30. Z50.F0.5; N10 G00 X180. Z254.; N15 M30;
图1 锥面加工
倒角、倒圆角
• • • • •
格式:G01 X_(Z_)C_ F_;(倒直角) G01 X_(Z_)R_ F_;(倒圆角) 说明: 1)目前倒角已不分正负符号,如C2与C-2等效。 2)在一行程序中只能出现X或Z坐标值。
• 准备功能G代码 • 准备功能 G指令由 G后一或二位数值组成, 它用来规定刀具和工件的相对运动轨迹、 机床坐标系、坐标平面、刀具补偿、坐标 偏置等多种加工操作。 • G 功能根据功能的不同分成若干组,其中 00组的G 功能(G04、G28、G70-G76) 称非模态 G 功能,其余组的称模态G功能。