蜗杆传动基本几何尺寸计算
蜗轮蜗杆计算公式(简洁版)

0
20 1.2004E-08 1.2E-08
中心距a(d1+d2+2*X2*m)/2 蜗杆分度圆导程角(γ)=atan(Z1/q) =atan(m*Z1/d1) 蜗杆齿顶高ha1(ha*=1)=m*ha*=(da1d1) 蜗轮齿顶高ha2=(ha*+X2)*m=(da2d2) 蜗杆齿根高hf1=(ha*+c*)m=(d1df1)/2 蜗轮齿根高hf2=(d2-df2)/2=m*(ha*X2+C*) 蜗杆分度圆直径d1=q*m 蜗轮分度圆直径d2=m*Z2=2a-d1-2*X2*m 蜗杆齿顶圆直径da1=(q+2) *m=d1+2*ha1=d1+2*m*h* 蜗轮喉圆直径da2= (Z2+2+2*X2)*m=d2+2*ha2 蜗杆齿根圆直径df1=d1-2*hf1
Z1大、 29.48
Z1小
Z1大、
33 29.48
普通圆柱螺杆L≥ X -1 -0.5 0 0.5 1
Z1=1~2 46
39.44 51.44 56.4 60.4
蜗杆螺纹部分长度L
圆弧圆柱蜗杆
Z1=3~4
X2
Z1
46
<1
1~2
49.16
1~1.5
1~2
61.16
<1
3~4
62.4
1~1.5
3~4
64.4
80
0
80
80
6.3434076 6.3434076 #DIV/0! 6.3434076
4
22
4
66
4
4.8
0
0
4.8
4.8
36 35.9999999
普通圆柱蜗杆传动的基本参数及几何尺寸计算
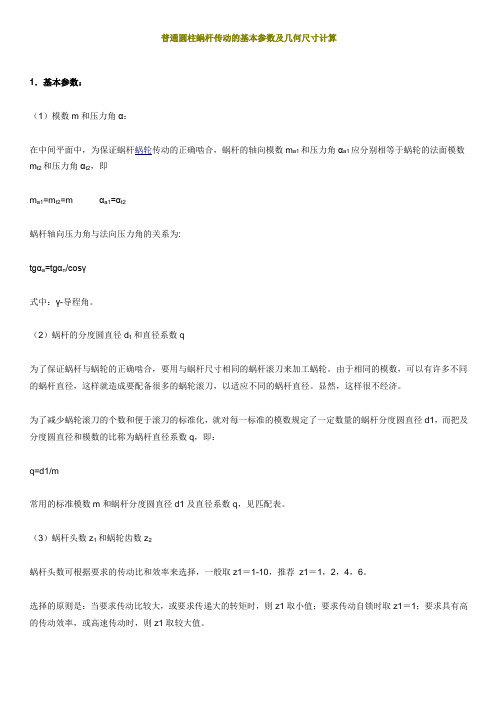
普通圆柱蜗杆传动的基本参数及几何尺寸计算1.基本参数:(1)模数m和压力角α:在中间平面中,为保证蜗杆蜗轮传动的正确啮合,蜗杆的轴向模数m a1和压力角αa1应分别相等于蜗轮的法面模数m t2和压力角αt2,即m a1=m t2=mαa1=αt2蜗杆轴向压力角与法向压力角的关系为:tgαa=tgαn/cosγ式中:γ-导程角。
(2)蜗杆的分度圆直径d1和直径系数q为了保证蜗杆与蜗轮的正确啮合,要用与蜗杆尺寸相同的蜗杆滚刀来加工蜗轮。
由于相同的模数,可以有许多不同的蜗杆直径,这样就造成要配备很多的蜗轮滚刀,以适应不同的蜗杆直径。
显然,这样很不经济。
为了减少蜗轮滚刀的个数和便于滚刀的标准化,就对每一标准的模数规定了一定数量的蜗杆分度圆直径d1,而把及分度圆直径和模数的比称为蜗杆直径系数q,即:q=d1/m常用的标准模数m和蜗杆分度圆直径d1及直径系数q,见匹配表。
(3)蜗杆头数z1和蜗轮齿数z2蜗杆头数可根据要求的传动比和效率来选择,一般取z1=1-10,推荐z1=1,2,4,6。
选择的原则是:当要求传动比较大,或要求传递大的转矩时,则z1取小值;要求传动自锁时取z1=1;要求具有高的传动效率,或高速传动时,则z1取较大值。
蜗轮齿数的多少,影响运转的平稳性,并受到两个限制:最少齿数应避免发生根切与干涉,理论上应使z2min≥17,但z2<26时,啮合区显著减小,影响平稳性,而在z2≥30时,则可始终保持有两对齿以上啮合,因之通常规定z2>28。
另一方面z2也不能过多,当z2>80时(对于动力传动),蜗轮直径将增大过多,在结构上相应就须增大蜗杆两支承点间的跨距,影响蜗杆轴的刚度和啮合精度;对一定直径的蜗轮,如z2取得过多,模数m就减小甚多,将影响轮齿的弯曲强度;故对于动力传动,常用的范围为z2≈28-70。
对于传递运动的传动,z2可达200、300,甚至可到1000。
z1和z2的推荐值见下表(4)导程角γ蜗杆的形成原理与螺旋相同,所以蜗杆轴向齿距p a与蜗杆导程p z的关系为p z=z1p a,由下图可知:tanγ=p z/πd1=z1p a/πd1=z1m/d1=z1/q导程角γ的范围为3.5°一33°。
机械设计(7.2.1)--圆柱蜗杆传动主要参数和几何尺寸计算
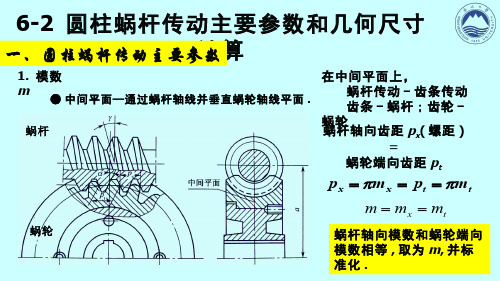
变 圆分离 ;
位 : 蜗杆分度线与蜗轮分度
中心距较标准值改 变;
位 , 减小 .
正变位 , 增大 ; 负变
(4) 变位后 , 蜗轮分度圆仍然与其节圆重 合,
但轮尺尺寸有变化 .
负变位 x2<0
标准 x2=0
正变位 x2>0 变位系数 , 过小 ,
( 变位后的 ) 实际中心距
a
a
a
1 2
(d1
● 蜗杆径向尺寸: d1= 按标准或自定 齿全高 , 齿顶高 , 齿根高及顶圆、
根圆同标准齿轮 , 无关变位 .
da1 d1 2ha1;ha1 ha*m d f 1 d1 2hf 1;hf 1 (ha* c* )m
ha* 1.0,0.8(短);c* 0.2,0.15,0.25
与链传动不同
7. 蜗轮齿数 表z26-3 给出了 z2 荐用值 ( 结合传动比和 蜗杆头数, z1=1,2,4,6) 。
为避免根切:
z1=1 , z2>17~18
z1=2 , z2>27
动力传动时,
z2<80, 根强度
避免尺寸过大 , 削弱齿
6-2 圆柱蜗杆传动主要参数和几何尺寸计算 一、圆柱蜗杆传动主要参 数
6-2 圆柱蜗杆传动主要参数和几何尺寸计算 一、圆柱蜗杆传动主要参 数
一、圆柱蜗杆传动主要参数
4. 蜗杆分度圆直径 d1(1) 为保证正确啮合,用蜗杆尺寸基
本相同的滚刀来加工蜗轮 .
(2) 为减少滚刀的数量和使之标准化 ,每个标准模数的规定了一定数量 的滚刀直径 ( 即蜗杆直径 ).
(3) 表 6-2 列出了 m 和 d1 常用标准 值.
普通圆柱蜗杆传动基本几何尺寸计算关系式
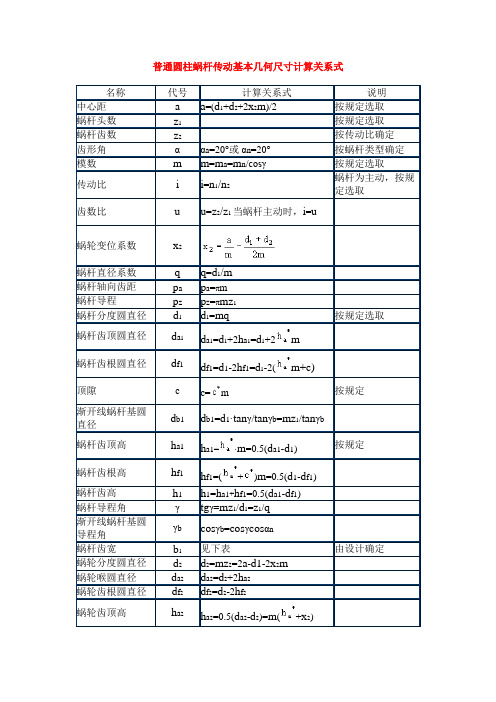
名称
代号
计算关系式
说明
中心距
a
a=(d1+d2+2x2m)/2
按规定选取
蜗杆头数
z1
按规定选取
蜗杆齿数
z2
按传动比确定
齿形角
α
αa=20°或αn=20°
按蜗杆类型确定
模数
m
m=ma=mn/cosγ
按规定选取
传动比
i
i=n1/n2
蜗杆为主动,按规定选取
齿数比
u
u=z2/z1当蜗杆主动时,i=u
经磨削的蜗杆,按左式所求的长度应再增加下列值:
当m<10mm时,增加25mm;
当m=10~16mm时,增加35~40mm;
当m>16mm时,增加50mm;
2
≤da2+1.5m
4
≤0.67da1
≤da2+m
0
-0.5
-1.0
0.5
1.0
≥(12.5+0.09z2)m
≥(9.5+0.09z2)m
≥(10.5+z1)m
蜗轮咽喉母圆半径
rg2
rg2=a-0.5da2
蜗轮齿宽
b2
由设计确定
蜗轮齿宽角
θ
θ=2arcsin(b2/d1)
蜗杆轴向齿厚
sa
sa=0.5πm
蜗杆法向齿厚
sn
sn=sa·cosγ
蜗轮齿厚
st
按蜗杆节圆处轴向齿槽宽ea'确定
蜗杆节圆直径
d1'
d1'=d1+2x2m=m(q+2x2)
蜗轮蜗杆的计算

蜗轮蜗杆的计算公司标准化编码 [QQX96QT-XQQB89Q8-NQQJ6Q8-MQM9N]蜗轮、蜗杆的计算公式:1,传动比=蜗轮齿数÷蜗杆头数2,中心距=(蜗轮节径+蜗杆节径)÷2 3,蜗轮吼径=(齿数+2)×模数 4,蜗轮节径=模数×齿数5,蜗杆节径=蜗杆外径-2×模数 6,蜗杆导程=π×模数×头数7,螺旋角(导程角)tg β=(模数×头数)÷蜗杆节径 一.基本参数:(1)模数m 和压力角α:在中间平面中,为保证蜗杆蜗轮传动的正确啮合,蜗杆的轴向模数m a1和压力角αa1应分别相等于蜗轮的法面模数m t2和压力角αt2,即 m a1=m t2=m αa1=αt2蜗杆轴向压力角与法向压力角的关系为: tgαa =tgαn /cosγ 式中:γ-导程角。
(2)蜗杆的分度圆直径d 1和直径系数q为了保证蜗杆与蜗轮的正确啮合,要用与蜗杆尺寸相同的蜗杆滚刀来加工蜗轮。
由于相同的模数,可以有许多不同的蜗杆直径,这样就造成要配备很多的蜗轮滚刀,以适应不同的蜗杆直径。
显然,这样很不经济。
为了减少蜗轮滚刀的个数和便于滚刀的标准化,就对每一标准的模数规定了一定数量的蜗杆分度圆直径d1,而把及分度圆直径和模数的比称为蜗杆直径系数q ,即: q=d1/m常用的标准模数m 和蜗杆分度圆直径d1及直径系数q ,见匹配表。
(3)蜗杆头数z 1和蜗轮齿数z 2蜗杆头数可根据要求的传动比和效率来选择,一般取z1=1-10,推荐 z1=1,2,4,6。
选择的原则是:当要求传动比较大,或要求传递大的转矩时,则z1取小值;要求传动自锁时取z1=1;要求具有高的传动效率,或高速传动时,则z1取较大值。
蜗轮齿数的多少,影响运转的平稳性,并受到两个限制:最少齿数应避免发生根切与干涉,理论上应使z2min≥17,但z2<26时,啮合区显着减小,影响平稳性,而在z2≥30时,则可始终保持有两对齿以上啮合,因之通常规定z2>28。
蜗杆传动基本尺寸计算公式
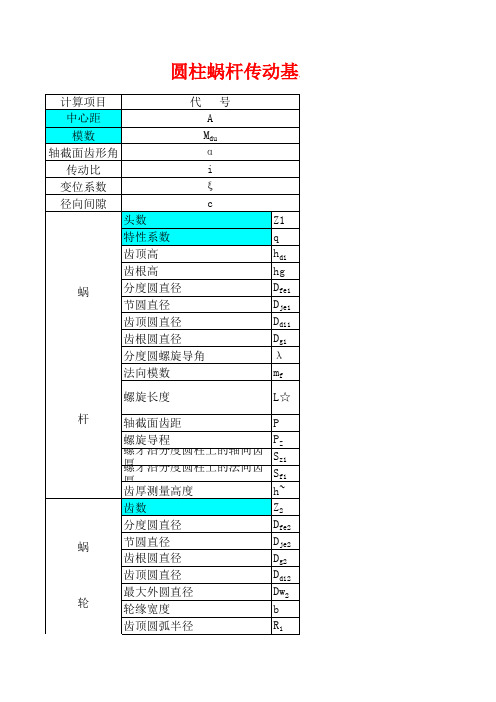
计算项目中心距模数轴截面齿形角传动比变位系数径向间隙头数Z1特性系数q 齿顶高h di 齿根高hg 分度圆直径D fe1节圆直径D je1齿顶圆直径D di1齿根圆直径D g1分度圆螺旋导角λ法向模数m f 轴截面齿距P螺旋导程P Z 螺牙沿分度圆柱上的轴向齿厚S z1螺牙沿分度圆柱上的法向齿厚S f1齿厚测量高度h~齿数Z 2分度圆直径D fe2节圆直径D je2齿根圆直径D g2齿顶圆直径D di2最大外圆直径Dw 2轮缘宽度b 齿顶圆弧半径R 1代 号A M du α螺旋长度L☆蜗 轮圆柱蜗杆传动基本几i ξc蜗杆齿根圆弧半径R 2轮基本几何尺寸计算公式公 式计算结果备注A=0.5M du(Z2+q+2ξ)175.00Mdu=2A/(Z2+q+2ξ) 3.15α=20°20.00i=Z2/Z1=n1/n297.00ξ=(A/Mdu)-0.5(q+z2) 2.06C=0.25Mdu0.79Z1=1,2,4 1.00q=Dfe1/Mdu10.00hdi=Mdu 3.15hg=1.25Mdu 3.94Dfe1=qMdu31.50Dje1=Dfe1+2Mduξ=Mdu(q+2ξ)44.45Ddi1=Mdu(q+2)37.80Dg1=Mdu(q-2.5)23.63λ=arctgZ1/q0.10mf=Mducosλ 3.13L=(12+0.1z2)Mdu68.36Z1=1,2 L=(13+0.1z2)Mdu71.51Z1=4 P=πMdu9.90PZ=πMduZ19.90Sz1=0.45πMdu97.00Sf1=Sz1cosλ96.52h~=Mdu 3.15Z2=iZ197.00Dfe2=MduZ2305.55Dje2=Dfe2=MduZ2305.55Dg2=2(A-0.5Ddi1-0.25Mdu)310.63Ddi2=2(A-0.5Dfe1+Mdu)324.80Dw2=Ddi2+Mdu327.95b=0.65Ddi124.57R1=0.5Dfe1-Mdu12.60R1=0.5Ddi1+0.25Mdu19.69。
蜗轮蜗杆的计算
蜗轮、蜗杆的计算公式: 1,传动比=蜗轮齿数÷蜗杆头数 2,中心距=(蜗轮节径+蜗杆节径)÷2 3,蜗轮吼径=(齿数+2)×模数 4,蜗轮节径=模数×齿数 5,蜗杆节径=蜗杆外径-2×模数 6,蜗杆导程=π×模数×头数7,螺旋角(导程角)tg β=(模数×头数)÷蜗杆节径 一.基本参数:(1)模数m 和压力角α:在中间平面中,为保证蜗杆蜗轮传动的正确啮合,蜗杆的轴向模数m a1和压力角αa1应分别相等于蜗轮的法面模数m t2和压力角αt2,即 m a1=m t2=m αa1=αt2蜗杆轴向压力角与法向压力角的关系为: tgαa =tgαn /cosγ 式中:γ-导程角。
(2)蜗杆的分度圆直径d 1和直径系数q为了保证蜗杆与蜗轮的正确啮合,要用与蜗杆尺寸相同的蜗杆滚刀来加工蜗轮。
由于相同的模数,可以有许多不同的蜗杆直径,这样就造成要配备很多的蜗轮滚刀,以适应不同的蜗杆直径。
显然,这样很不经济。
为了减少蜗轮滚刀的个数和便于滚刀的标准化,就对每一标准的模数规定了一定数量的蜗杆分度圆直径d1,而把及分度圆直径和模数的比称为蜗杆直径系数q,即:q=d1/m常用的标准模数m和蜗杆分度圆直径d1及直径系数q,见匹配表。
(3)蜗杆头数z1和蜗轮齿数z2蜗杆头数可根据要求的传动比和效率来选择,一般取z1=1-10,推荐 z1=1,2,4,6。
选择的原则是:当要求传动比较大,或要求传递大的转矩时,则z1取小值;要求传动自锁时取z1=1;要求具有高的传动效率,或高速传动时,则z1取较大值。
蜗轮齿数的多少,影响运转的平稳性,并受到两个限制:最少齿数应避免发生根切与干涉,理论上应使z2min≥17,但z2<26时,啮合区显着减小,影响平稳性,而在z2≥30时,则可始终保持有两对齿以上啮合,因之通常规定z2>28。
另一方面z2也不能过多,当z2>80时(对于动力传动),蜗轮直径将增大过多,在结构上相应就须增大蜗杆两支承点间的跨距,影响蜗杆轴的刚度和啮合精度;对一定直径的蜗轮,如z2取得过多,模数m 就减小甚多,将影响轮齿的弯曲强度;故对于动力传动,常用的范围为z2≈28-70。
涡轮蜗杆基本知识
普通圆柱蜗杆传动的基本参数及几何尺寸计算1.基本参数:(1)模数m和压力角α:m a1=m t2=mαa1=αt2蜗杆轴向压力角与法向压力角的关系为:tgαa=tgαn/cosγ式中:γ-导程角。
(2)蜗杆的分度圆直径d1和直径系数q为了保证蜗杆与蜗轮的正确啮合,要用与蜗杆尺寸相同的蜗杆滚刀来加工蜗轮。
由于相同的模数,可以有许多不同的蜗杆直径,这样就造成要配备很多的蜗轮滚刀,以适应不同的蜗杆直径。
显然,这样很不经济。
为了减少蜗轮滚刀的个数和便于滚刀的标准化,就对每一标准的模数规定了一定数量的蜗杆分度圆直径d1,而把及分度圆直径和模数的比称为蜗杆直径系数q,即:q=d1/m常用的标准模数m和蜗杆分度圆直径d1及直径系数q,见匹配表。
(3)蜗杆头数z1和蜗轮齿数z2蜗杆头数可根据要求的传动比和效率来选择,一般取z1=1-10,推荐z1=1,2,4,6。
选择的原则是:当要求传动比较大,或要求传递大的转矩时,则z1取小值;要求传动自锁时取z1=1;要求具有高的传动效率,或高速传动时,则z1取较大值。
蜗轮齿数的多少,影响运转的平稳性,并受到两个限制:最少齿数应避免发生根切与干涉,理论上应使z2min≥17,但z2<26时,啮合区显著减小,影响平稳性,而在z2≥30时,则可始终保持有两对齿以上啮合,因之通常规定z2>28。
另一方面z2也不能过多,当z2>80时(对于动力传动),蜗轮直径将增大过多,在结构上相应就须增大蜗杆两支承点间的跨距,影响蜗杆轴的刚度和啮合精度;对一定直径的蜗轮,如z2取得过多,模数m就减小甚多,将影响轮齿的弯曲强度;故对于动力传动,常用的范围为z2≈28-70。
对于传递运动的传动,z2可达200、300,甚至可到1000。
z1和z2的推荐值见下表。
4)导程角γ蜗杆的形成原理与螺旋相同,所以蜗杆轴向齿距p a与蜗杆导程p z的关系为p z=z1p a,由下图可知:tanγ=p z/πd1=z1p a/πd1=z1m/d1=z1/q导程角γ的范围为3.5°一33°。
蜗杆与斜齿轮传动几何尺寸计算公式
mn
Z β α ha* c* d ha hf h da df a a' x
mn Z1 d1
α=20° ha*=1 c*=0.25 蜗杆 d1 取标准值,斜齿轮 d 2 =
mn Z 2 cosβ
ha1 = ha*mn
ha 2 = (ha* + x2 )mn h f 2 = (ha* + c* x2 )mn
蜗杆斜齿轮的传动几何尺寸计算
序号 1 2 3 4 5 6 7 8 9 10 11 12 13 14 15 名称 模数 齿数 导程角或螺旋角 分度圆压力角 齿顶高系数 径向间隙系数 分度圆直径 齿顶高 齿根高 齿全高 齿顶圆直径 齿根圆直径 标准中心距 计算中心距 变位系数 代号 公式 取标准值 蜗杆头数 Z1,斜齿轮齿数 Z2 sin β =
h=ha+hf da=d+2ha df=d-2hf
h f 1 = (ha* + c* )mn
a=
d1 + d 2 2
按实际值取值 x1=0
x2 =
a' a mn pa = π mn cos β
16 17 18
蜗杆轴向齿距 蜗杆法向齿距 蜗杆导程 蜗杆分度圆柱轴向 齿厚
pa pn pz
pn = π Байду номын сангаасn
22 公法线长度 wk
其中
wk * = cos an [π (k 0.5) + Z 'invan ] Z' = invat Z2 invan
备注:1.上述公式来源于齿轮论坛的部分齿轮 EXCEL 计算 软件,参考了圆柱蜗杆传动的几何尺寸计算( 《齿轮机构设 计与应用》 ) 2.上述的公式有遗漏的,也有部分不是很正确的,希望大家 予以指正!
蜗轮蜗杆的计算
蜗轮、蜗杆的计算公式:1,传动比=蜗轮齿数÷蜗杆头数2,中心距=(蜗轮节径+蜗杆节径)÷23,蜗轮吼径=(齿数+2)×模数4,蜗轮节径=模数×齿数5,蜗杆节径=蜗杆外径-2×模数6,蜗杆导程=π×模数×头数7,螺旋角(导程角)tgβ=(模数×头数)÷蜗杆节径一.基本参数:(1)模数m和压力角α:在中间平面中,为保证蜗杆蜗轮传动的正确啮合,蜗杆的轴向模数m a1和压力角αa1应分别相等于蜗轮的法面模数m t2和压力角αt2,即m a1=m t2=mαa1=αt2蜗杆轴向压力角与法向压力角的关系为:tgαa=tgαn/cosγ式中:γ-导程角。
(2)蜗杆的分度圆直径d1和直径系数q为了保证蜗杆与蜗轮的正确啮合,要用与蜗杆尺寸相同的蜗杆滚刀来加工蜗轮。
由于相同的模数,可以有许多不同的蜗杆直径,这样就造成要配备很多的蜗轮滚刀,以适应不同的蜗杆直径。
显然,这样很不经济。
为了减少蜗轮滚刀的个数和便于滚刀的标准化,就对每一标准的模数规定了一定数量的蜗杆分度圆直径d1,而把及分度圆直径和模数的比称为蜗杆直径系数q,即:q=d1/m常用的标准模数m和蜗杆分度圆直径d1及直径系数q,见匹配表。
(3)蜗杆头数z1和蜗轮齿数z2蜗杆头数可根据要求的传动比和效率来选择,一般取z1=1-10,推荐z1=1,2,4,6。
选择的原则是:当要求传动比较大,或要求传递大的转矩时,则z1取小值;要求传动自锁时取z1=1;要求具有高的传动效率,或高速传动时,则z1取较大值。
蜗轮齿数的多少,影响运转的平稳性,并受到两个限制:最少齿数应避免发生根切与干涉,理论上应使z2min≥17,但z2<26时,啮合区显著减小,影响平稳性,而在z2≥30时,则可始终保持有两对齿以上啮合,因之通常规定z2>28。
另一方面z2也不能过多,当z2>80时(对于动力传动),蜗轮直径将增大过多,在结构上相应就须增大蜗杆两支承点间的跨距,影响蜗杆轴的刚度和啮合精度;对一定直径的蜗轮,如z2取得过多,模数m就减小甚多,将影响轮齿的弯曲强度;故对于动力传动,常用的范围为z2≈28-70。
- 1、下载文档前请自行甄别文档内容的完整性,平台不提供额外的编辑、内容补充、找答案等附加服务。
- 2、"仅部分预览"的文档,不可在线预览部分如存在完整性等问题,可反馈申请退款(可完整预览的文档不适用该条件!)。
- 3、如文档侵犯您的权益,请联系客服反馈,我们会尽快为您处理(人工客服工作时间:9:00-18:30)。
备注
Z1=1,2 Z1=4
R1=0.5Ddi1+0.25Mdu
19.69
圆柱蜗杆传动基本几何尺寸计算公式
计算项目
代号
中心距
A
模数
Mdu
轴截面齿形角
α
传动比
i
变位系数
ξ
径向间隙
c
头数
Z1
特性系数
q
齿顶高
hdi
齿根高
hg
蜗
分度圆直径
Dfe1
节圆直径
Dje1
齿顶圆直径
Ddi1
齿根圆直径
Dg1
分度圆螺旋导角
λ
法向模数
mf
螺旋长度
L☆
杆
轴截面齿距
P
螺旋导程 螺牙沿分度圆柱上的轴向齿 厚螺牙沿分度圆柱上的法向齿 厚
传动基本几何尺寸计算公式
公式
A=0.5Mdu(Z2+q+2ξ) Mdu=2A/(Z2+q+2ξ) α=20° i=Z2/Z1=n1/n2 ξ=(A/Mdu)-0.5(q+z2) C=0.25Mdu Z1=1,2,4 q=Dfe1/Mdu hdi=Mdu hg=1.25Mdu Dfe1=qMdu Dje1=Dfe1+2Mduξ=Mdu(q+2ξ) Ddi1=Mdu(q+2) Dg1=Mdu(q-2.5) λ=arctgZ1/q mf=Mducosλ L=(12+0.1z2)Mdu L=(13+0.1z2)Mdu P=πMdu PZ=πMduZ1 Sz1=0.45πMdu Sf1=Sz1cosλ h~=Mdu Z2=iZ1 Dfe2=MduZ2 Dje2=Dfe2=MduZ2 Dg2=2(A-0.5Ddi1-0.25Mdu) Ddi2=2(A-0.5Dfe1+Mdu) Dw2=Ddi2+Mdu b=0.65Ddi1 R1=0.5Dfe1-Mdu
计算结果 175.00
3.15 20.00 97.00 2.06 0.79 1.00 10.00 3.15 3.94 31.50 44.45 37.80 23.63 0.10 3.13 68.36 71.51 9.90 9.90 97.00 96.52 3.15 97.00 305.55 305.55 310.63 324.80 327.95 24.57 12.60
PZ Sz1 Sf1
齿厚测பைடு நூலகம்高度
h~
齿数
Z2
分度圆直径
Dfe2
蜗
节圆直径
Dje2
齿根圆直径
Dg2
齿顶圆直径
Ddi2
最大外圆直径
Dw2
轮
轮缘宽度
b
齿顶圆弧半径
R1
轮
齿根圆弧半径
R2
注:☆磨削蜗
杆需加长:Mdu
≤10时,加长
25MM;10≤Mdu
≤16时,加长
35MM;Mdu>16
时,加长40-
50MM