机电一体化课程设计报告
机电一体化课程设计报告

机电一体化系统设计基础课程设计报告专业:机械电子工程班级:机电0811学号: 2008716022姓名:陈智建指导教师:刘云、柯江岩2012 年 1 月 13 日目录第一节绪论 (3)1.1课程设计目的意义 (3)1.2课程设计任务描述 (3)1.3数控铣床的性能指标设计要求 (3)第二节总体方案设计 (4)2.1主轴驱动系统设计方案 (4)2.2 X/Y/Z轴控制系统方案设计 (4)2.3电气系统设计方案 (4)第三节传动系统设计 (5)3.1主轴传动系统的设计 (5)3.1.1主轴电机选择 (5)3.1.2变频器的选择 (5)3.1.3主轴传动系统设计 (5)3.2伺服驱动系统设计 (6)3.2.1伺服传动机构设计 (6)3.2.2伺服电机选择 (6)3.2.3 滚珠丝杠的选择 (6)3.2.4滚珠丝杠支承的选择 (7)3.3设计验算校核 (8)3.3.1惯量匹配验算 (8)3.3.2伺服电机负载能力校验 (8)3.3.3系统的刚度计算 (9)3.3.4固有频率计算 (10)3.3.5死区误差计算 (10)3.3.6系统刚度变化引起的定位误差计算 (11)第四节电气系统设计 (11)后附6张系统框图和元器件图。
(14)第五节心得体会 (15)参考文献 (16)第一节绪论1.1课程设计目的意义机电一体化是一门实践性强的综合性技术学科,所涉及的知识领域非常广泛,现代各种先进技术构成了机电一体化的技术基础。
机电一体化系统设计基础课程设计属于机械电子工程专业的课程设计,培养学生综合应用所学的知识,进行机电一体化系统设计的能力。
1.2课程设计任务描述本课程设计主要要求学生设计一数控铣床的传动系统跟控制系统,即在已有数控系统的基础上,根据实际加工要求,进行二次开发。
由于生产数控系统,伺服电动机的驱动器,伺服电机的厂家很多,即使同一厂家,其生产的产品系统和型号也很多。
为了避免在设计过程中选型过于宽广,并考虑到本设计的目的主要是为了训练从事设计的基本能力,数控系统规定选用Fanuc OI MATE MC。
机电一体化系统设计报告

机电一体化系统设计报告一、引言二、设计目标本设计的目标是开发一种智能家居系统,实现家庭电器和设备的远程自动化控制。
该系统能够根据用户需求进行智能调整,提高家庭的舒适度和能源利用效率。
三、系统组成1.硬件部分硬件部分主要包括各种传感器、执行器、控制器和通信模块等。
传感器用于感知环境的温度、湿度、光照等参数,执行器用于控制家电设备的开关、调节等动作,控制器用于数据处理和决策,通信模块用于与用户远程交互和传输数据。
2.软件部分软件部分包括嵌入式系统的开发和云端平台的搭建。
嵌入式系统负责实时数据采集、处理和控制执行器,云端平台负责用户界面的设计、数据分析和远程控制指令的传输。
四、系统功能1.环境感知与自动调节系统通过传感器感知室内的温度、湿度和光照等参数,根据预设的调节策略自动调节空调、加湿器、照明等设备,提供舒适的生活环境。
2.节能和安全控制系统根据室内外环境的变化调节电器设备的运行状态,达到节能的目的。
同时,系统还能够通过云端平台进行远程监控和控制,保障家庭安全。
3.远程操控用户可以通过手机等移动终端实时监控家庭环境和设备状态,并远程操控家电设备。
用户可以随时随地调整温度、湿度、照明等参数,提高生活便利性。
五、系统优势本设计的机电一体化系统具有以下优势:1.高效智能:系统能够根据用户需求智能调节设备,提高能源利用效率和居住舒适度。
2.远程操控:用户可以通过移动终端实时监控和操控家电设备,提高生活便利性。
3.节能环保:系统通过预设策略和远程监控实现节能控制,减少能源浪费和环境污染。
六、系统应用本系统可广泛应用于家庭、办公室、酒店等场所,满足人们对生活环境的需求,提高生活品质和工作效率。
七、结论通过机电一体化系统的设计和开发,可以实现家庭电器和设备的智能控制,提高能源利用效率和生活舒适度。
该系统具有远程操控、节能环保等优势,可应用于家庭、办公室等场所。
在未来的发展中,还可进一步完善系统功能,提升系统的性能和可靠性。
机电一体化专业课程设计报告
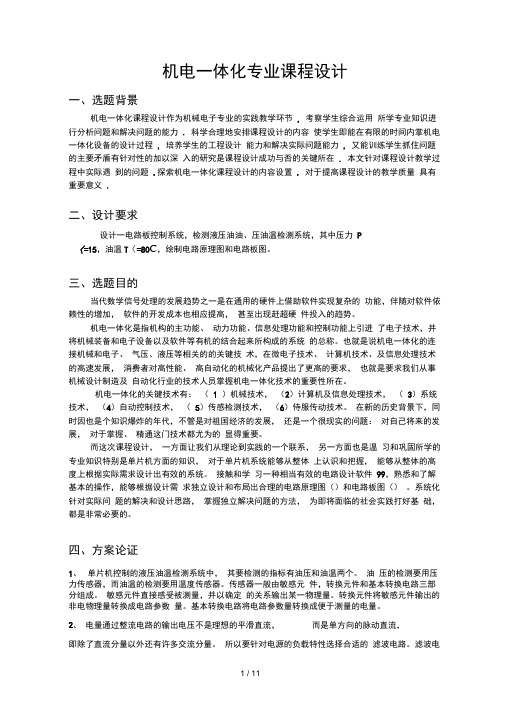
机电一体化专业课程设计一、选题背景机电一体化课程设计作为机械电子专业的实践教学环节, 考察学生综合运用所学专业知识进行分析问题和解决问题的能力. 科学合理地安排课程设计的内容使学生即能在有限的时间内掌机电一体化设备的设计过程, 培养学生的工程设计能力和解决实际问题能力, 又能训练学生抓住问题的主要矛盾有针对性的加以深入的研究是课程设计成功与否的关键所在. 本文针对课程设计教学过程中实际遇到的问题,探索机电一体化课程设计的内容设置, 对于提高课程设计的教学质量具有重要意义.二、设计要求设计一电路板控制系统,检测液压油油、压油温检测系统,其中压力P〈=15,油温T〈=80C,绘制电路原理图和电路板图。
三、选题目的当代数学信号处理的发展趋势之一是在通用的硬件上借助软件实现复杂的功能,伴随对软件依赖性的增加,软件的开发成本也相应提高,甚至出现赶超硬件投入的趋势。
机电一体化是指机构的主功能、动力功能、信息处理功能和控制功能上引进了电子技术,并将机械装备和电子设备以及软件等有机的结合起来所构成的系统的总称。
也就是说机电一体化的连接机械和电子、气压、液压等相关的的关键技术,在微电子技术、计算机技术、及信息处理技术的高速发展,消费者对高性能、高自动化的机械化产品提出了更高的要求,也就是要求我们从事机械设计制造及自动化行业的技术人员掌握机电一体化技术的重要性所在。
机电一体化的关键技术有:( 1 )机械技术,(2)计算机及信息处理技术,(3)系统技术,(4)自动控制技术,(5)传感检测技术,(6)侍服传动技术。
在新的历史背景下,同时因也是个知识爆炸的年代,不管是对祖国经济的发展,还是一个很现实的问题:对自己将来的发展,对于掌握、精通这门技术都尤为的显得重要。
而这次课程设计,一方面让我们从理论到实践的一个联系,另一方面也是温习和巩固所学的专业知识特别是单片机方面的知识,对于单片机系统能够从整体上认识和把握,能够从整体的高度上根据实际需求设计出有效的系统。
机电一体化课程设计报告书

机电一体化系统课程设计题目自动分拣工件机械手的设计班级机械1211学生蒋金成学号 1220116105同组凌一锐上文龙薛俊起迄日期2015年12月25日~ 2016年1月5日指导教师汪帮富讲师机械工程学院目录1. 自动分拣工件机械手设计的要求、目的及意义 (1)1.1要求 (3)1.2目的及意义 (3)2. 总体方案设计与论证 (4)2.1总体方案设计 (4)2.1.1主体功能 (4)2.1.2执行机构 (5)2.1.3驱动机构 (6)2.1.4控制机构 (6)2.2总体方案论证 (4)2.2.1调试过程 (6)2.2.2调试中出现的问题及解决方法 (7)2.2.3 结果分析 (8)3. 机构分析与计算 (3)3.1机械手总体设计 (8)3.2机身的总体设计 (9)4. 关键部件设计与校核 (4)4.1机械手手抓的设计计算 (9)4.1.1选择手抓的类型及夹紧装置 (10)4.1.2 手抓的力学分析 (11)4.1.3机械手手抓夹持精度的分析计算 (11)5. 结论 (12)6.收获、体会 (12)7.参考文献 (13)1、自动分拣工件机械手设计的要求、目的及意义1.1要求1、机械手将传送带A上的大号物品传送到传送带B上,其他小号的物品让其流走。
机械手所有的动作均由液压驱动,上升,下降,左移,右移均由(双线圈)三位四通电磁阀控制,夹紧,放松用一个(单线圈)二位四通电磁阀控制,通电夹紧,断电放松。
所有电磁线圈驱动电源:直流,电压24V,电流1A,位置检测用:行程开关,光电开关,压力继电器。
2、系统操作可实现单循环,自动循环功能。
3、设计控制系统和输入/输出信号调理电路及功率驱动电路原理图。
4、设计控制系统程序流程图并用汇编语言编写其中的某一段程序。
5、设计操作台面板布置示意图。
6、编写设计说明书和使用说明书。
7、在满足控制要求的前提下,力求控制系统简单,经济。
1.2目的及意义现代计算机技术的产业革命,将世界经济从资本经济带入到知识经济时代。
机电一体化课程设计报告
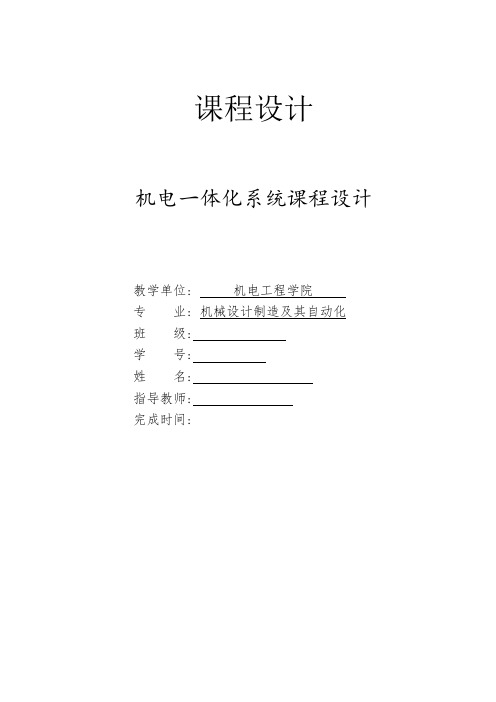
课程设计机电一体化系统课程设计教学单位: 机电工程学院专业: 机械设计制造及其自动化班级:学号:姓名:指导教师:完成时间:课程(产品)设计任务书目录1. 总体方案设计 (1)1.1. 设计目的 (1)1.2. 设计任务 (1)1.3. 总体方案的确定 (2)2. 机械传动部件的计算与选型 (4)2.1. 导轨上移动部件的重量估算 (4)2.2. 铣削力的计算 (4)2.3. 直线滚动导轨副的计算与选型 (5)2.4. 滚珠丝杠螺母副的计算与选型 (6)2.5. 步进电动机减速箱的选用 (9)2.6. 步进电动机的计算与选型 (9)2.7. 增量式旋转编码器的选用 (12)3. 控制系统和人机接口设计 (12)I/O口地址分配表 (13)4. 总结 (14)5. 附录 (15)5.1. 机械装配图 (15)5.2. 电气连线图 (15)5.3. PLC控制程序 (16)参考文献 (17)1.总体方案设计1.1. 设计目的设计的目的和意义。
课程设计是一个重要的时间性教学环节,要求学生综合的运用所学的理论知识,独立进行的设计训练,主要目的:1)通过设计,使学生全面地、系统地了解和掌握数控机床的基本组成及其想怪知识,学习总体的方案拟定、分析与比较的方法。
2)通过对机械系统的设计,掌握几种典型传动元件与导向元件的工作原理、设计计算及选用的方式3)培养学生独立分析问题和解决问题的能力,学习并树立“系统设计”的思想4)锻炼提高学生应用手册和标准、查阅文献资料及撰写科技论文的能力1.2. 设计任务题目:X—Y数控工作台机电系统设计任务:设计一种供立式数控铣床使用的X-Y数控工作台,主要参数如下:1)立铣刀最大直径d=15mm;2)立铣刀齿数Z=3;3)最大铣削宽度mmae15=;4)最大背吃刀量mmap8=;5)加工材料为碳素钢;6)X 、Y 方向的脉冲当量mmy x 005.0==δδ/脉冲;7)X 、Y 方向的定位精度均为mm 01.0±;8)工作台尺寸210mm ×250mm,加工范围为230mm ×270mm ; 9)工作台空载最快移动速度min/3000mm v v y x ==;10)工作台进给最快移动速度min/400max max mm v v f y f x ==;11)移动部件总重量为661.5N ; 12)每齿进给量mm f z 1.0= 13)铣刀转速n=300r/min1.3. 总体方案的确定1.机械传动部件的选择(1)导轨副的选用 要设计的X-Y 工作台是用来配套轻型的立式数控铣床的,需要承受的载荷不大,但脉冲当量小、定位精度高,因此,决定选用直线滚动导轨副,它具有摩擦系数小、不易爬行、传动效率高、结构紧凑、安装预紧方便等优点。
机电一体化系统设计报告

机电一体化系统设计报告
摘要:本报告旨在介绍机电一体化系统的设计内容,包括系统需求分析、系统设计原理、硬件选型、软件开发以及系统测试与验证。
通过详细
的阐述和分析,展现了我们团队在机电一体化技术领域的研究和实践成果。
1.引言
1.1背景介绍
1.2研究目的
2.系统需求分析
2.1功能需求
2.2性能需求
2.3可靠性需求
2.4安全性需求
3.系统设计原理
3.1机电一体化系统原理
3.2动力学分析
3.3控制策略选择
4.硬件选型
4.1电机选型
4.2驱动器选型
4.3传感器选型
4.4控制器选型
5.软件开发
5.1系统架构设计
5.2控制算法设计与实现
5.3数据处理与通信模块设计
5.4用户界面设计
6.系统测试与验证
6.1功能测试
6.2性能测试
6.3可靠性测试
6.4安全性测试
7.结果与讨论
7.1实验数据分析
7.2系统优化与改进
8.结论
附录:系统设计图纸、电气原理图、控制流程图等技术资料
总之,本报告涵盖了机电一体化系统设计的相关内容,从系统需求分析到系统设计原理、硬件选型、软件开发以及测试验证等方面,对系统设
计的全过程进行了详细的阐述和分析。
希望这份报告能为机电一体化技术的应用和研究提供一定的参考价值。
机电一体化(波轮式全自动洗衣机)课程设计
目录前言........................................... 错误!未定义书签。
洗衣机说明书1. 课程设计的任务.............................. 错误!未定义书签。
2. 洗衣机简介 (2)2.1全自动洗衣机特点 (3)2.2洗衣机工作原理概述 (4)3. 传动方案讨论 (4)4.传动系统的设计计算 (6)4.1减速离合器的结构和工作原理简介 (6)4.2减速离合器零部件的计算与选择 (13)4.3减速离合器零件装配图 (16)5.进/排水系统结构原理简介 (16)5.1进水电磁阀的结构与工作原理 (17)5.2排水电磁阀的结构与工作原理 (18)5.3水位开关控制原理 (20)6.控制系统的设计 (22)6.1控制芯片的选择 (22)6.2程序框图 (22)6.3控制程序设计 (24)6.4电气控制图 (39)心得体会 (40)参考文献 (41)附录 (41)前言本次机电一体化课程设计的重点在于硬件部分的减速离合器设计。
经过小组提出方案对比与讨论,最终决定使用单向轴承式减速离合器,具体讨论过程将在后面的说明书中详细介绍。
减速离合器的各部件的选择、设计是洗衣机硬件部分的设计重点,其具有体积小,功能多,零部件构成复杂等特点。
主要构成部分有离合装置,制动装置以与行星轮系二级减速装置,这些装置的设计尺寸选择,功能原理将在后面的洗衣机说明书中详细介绍。
考虑到设计的是家用洗衣机,并根据对洗衣机体积,功能的要求确定洗衣机采用以单片机为核心的通用自动控制装置,它具有功能强、可靠性强、编程简单、使用方便、体积小等特点。
该控制系统可实现用编写的程序进行逻辑控制、定时、记数和算术运算等,并通过数字量和模拟量的输入/输出来控制机械设备或生产过程。
该设计为单片机控制的全自动家用洗衣机,主要介绍了全自动洗衣机的工作原理(主要是重点设计部件减速离合器),控制系统的单片机的选型和资源的配置,控制系统程序设计与调试,控制系统单片机程序。
机电一体化系统课程设计报告
机电一体化系统课程设计设计说明书设计题目:X-Y数控工作台机电系统设计院校:班级:姓名:学号:2011年12 月24 日目录机电一体化系统设计课程设计任务书1.总体方案1.1导轨副的选用1.2 丝杆螺母副的选用1.3 减速装置的选用1.4 伺服电动机的选用1.5 检测装置的选用2.控制系统的设计3.机械传动部件的计算与选型3.1导轨上移动部件的重量估算3.2铣削力的计算3.3直线滚动导轨副的计算与选型3.4滚珠丝杠螺母副的计算与选型3.5步进电动机减速箱的选用3.6步进电动机的计算与选型3.7增量式旋转编码器的选用4.工作台机械装配图的绘制5.工作台控制系统的设计6.步进电动机驱动电源的选用7.设计总结参考文献[1]张建民.《机电一体化系统设计》第三版.高等教育出版社[2]尹志强.《系统设计课程设计指导书》.机械工业出版社五、工作台控制系统的设计X-Y数控工作台的控制系统设计,可以参考本章第一节的车床数控系统,但在硬件电路上需要考虑步进电动机(编码器)反馈信号的处理,在软件上要实现半闭环的控制算法。
六、步进电动机驱动电源的选用本例中X、Y向步进电动机均为90BYG2602型,生产厂家为常州宝马集团与公司。
查表4-14选择与之配套的驱动电源为BD28Nb型,输入电压100VAC,相电流4A,分配方式为二相八拍。
该驱动电源与控制器的接线方式如图6-25所示。
七、增量式旋转编码器的选用本设计所选步进电动机采用半闭环控制,可在电动机的尾部转轴上安装增量式旋转编码器,用以检验电动机的转角与转速。
增量式旋转编码器的分辨力应与步进电动机的步距角相匹配。
由步进电动机的步距角α=0.75°,可知电动机转动一转时,需要控制系统发出360/α=480个步进脉冲。
考虑到增量式旋转编码器输出的A、B相信号,可以送到四倍频电路进行电子四细分(见第四章第五节相关内容),因此,编码器的分辨力可选120线。
这样控制系统每发一个步进脉冲,电动机转过一个步距角,编码器对应输出一个脉冲信号。
机电一体化技术课程设计
机电一体化技术课程设计一、教学目标本课程旨在让学生了解和掌握机电一体化技术的基本概念、原理和应用,培养学生对机电一体化技术的兴趣和热情,提高学生的实际操作能力和创新能力。
知识目标:使学生了解机电一体化技术的基本概念、组成部分及其相互关系;掌握机电一体化技术的基本原理和关键技术;了解机电一体化技术的应用领域和发展趋势。
技能目标:使学生能够运用所学知识分析、解决机电一体化技术领域的问题;具备一定的实际操作能力,能够进行简单的机电一体化系统设计、调试和维护。
情感态度价值观目标:培养学生对机电一体化技术的兴趣和热情,增强学生对科技创新的敏感度;培养学生团队协作、积极探究的学习态度,提高学生的问题解决能力。
二、教学内容本课程的教学内容主要包括机电一体化技术的基本概念、原理和应用。
具体安排如下:第1-2课时:机电一体化技术的基本概念,包括定义、组成部分及其相互关系。
第3-4课时:机电一体化技术的基本原理,包括传感器技术、执行器技术、控制技术等。
第5-6课时:机电一体化技术的应用领域,包括工业自动化、机器人、汽车电子等。
第7-8课时:机电一体化技术的发展趋势,包括智能化、网络化、绿色化等。
第9-10课时:机电一体化技术的实际操作,包括简单机电一体化系统的设计、调试和维护。
三、教学方法为了提高教学效果,本课程将采用多种教学方法,包括讲授法、讨论法、案例分析法、实验法等。
讲授法:通过教师的讲解,使学生掌握机电一体化技术的基本概念、原理和应用。
讨论法:引导学生针对机电一体化技术的相关问题进行思考和讨论,提高学生的创新能力和问题解决能力。
案例分析法:通过分析具体的机电一体化技术应用案例,使学生更好地理解和掌握相关知识。
实验法:让学生亲自动手进行实验,培养学生的实际操作能力和实践能力。
四、教学资源为了支持本课程的教学,我们将选择和准备以下教学资源:教材:《机电一体化技术》教材,用于引导学生系统地学习机电一体化技术的基本知识。
机电一体化专业课程设计报告
机电一体化专业课程设计一、选题背景机电一体化课程设计作为机械电子专业的实践教学环节, 考察学生综合运用所学专业知识进行分析问题和解决问题的能力. 科学合理地安排课程设计的内容使学生即能在有限的时间内掌机电一体化设备的设计过程, 培养学生的工程设计能力和解决实际问题能力, 又能训练学生抓住问题的主要矛盾有针对性的加以深入的研究是课程设计成功与否的关键所在. 本文针对课程设计教学过程中实际遇到的问题,探索机电一体化课程设计的内容设置, 对于提高课程设计的教学质量具有重要意义.二、设计要求设计一电路板控制系统,检测液压油油、压油温检测系统,其中压力P〈=15,油温T〈=80C,绘制电路原理图和电路板图。
三、选题目的当代数学信号处理的发展趋势之一是在通用的硬件上借助软件实现复杂的功能,伴随对软件依赖性的增加,软件的开发成本也相应提高,甚至出现赶超硬件投入的趋势。
机电一体化是指机构的主功能、动力功能、信息处理功能和控制功能上引进了电子技术,并将机械装备和电子设备以及软件等有机的结合起来所构成的系统的总称。
也就是说机电一体化的连接机械和电子、气压、液压等相关的的关键技术,在微电子技术、计算机技术、及信息处理技术的高速发展,消费者对高性能、高自动化的机械化产品提出了更高的要求,也就是要求我们从事机械设计制造及自动化行业的技术人员掌握机电一体化技术的重要性所在。
机电一体化的关键技术有:( 1 )机械技术,(2)计算机及信息处理技术,(3)系统技术,(4)自动控制技术,(5)传感检测技术,(6)侍服传动技术。
在新的历史背景下,同时因也是个知识爆炸的年代,不管是对祖国经济的发展,还是一个很现实的问题:对自己将来的发展,对于掌握、精通这门技术都尤为的显得重要。
而这次课程设计,一方面让我们从理论到实践的一个联系,另一方面也是温习和巩固所学的专业知识特别是单片机方面的知识,对于单片机系统能够从整体上认识和把握,能够从整体的高度上根据实际需求设计出有效的系统。
- 1、下载文档前请自行甄别文档内容的完整性,平台不提供额外的编辑、内容补充、找答案等附加服务。
- 2、"仅部分预览"的文档,不可在线预览部分如存在完整性等问题,可反馈申请退款(可完整预览的文档不适用该条件!)。
- 3、如文档侵犯您的权益,请联系客服反馈,我们会尽快为您处理(人工客服工作时间:9:00-18:30)。
机电一体化系统设计基础课程设计报告专业:机械电子工程班级:机电0811学号: 2008716022姓名:陈智建指导教师:刘云、柯江岩2012 年 1 月 13 日目录第一节绪论 (3)1.1课程设计目的意义 (3)1.2课程设计任务描述 (3)1.3数控铣床的性能指标设计要求 (3)第二节总体方案设计 (4)2.1主轴驱动系统设计方案 (4)2.2 X/Y/Z轴控制系统方案设计 (4)2.3电气系统设计方案 (4)第三节传动系统设计 (5)3.1主轴传动系统的设计 (5)3.1.1主轴电机选择 (5)3.1.2变频器的选择 (5)3.1.3主轴传动系统设计 (5)3.2伺服驱动系统设计 (6)3.2.1伺服传动机构设计 (6)3.2.2伺服电机选择 (6)3.2.3 滚珠丝杠的选择 (6)3.2.4滚珠丝杠支承的选择 (8)3.3设计验算校核 (8)3.3.1惯量匹配验算 (8)3.3.2伺服电机负载能力校验 (9)3.3.3系统的刚度计算 (9)3.3.4固有频率计算 (10)3.3.5死区误差计算 (11)3.3.6系统刚度变化引起的定位误差计算 (11)第四节电气系统设计 (12)第五节总结 (15)参考文献 (15)附:6张系统框图和元器件图第一节绪论1.1课程设计目的意义机电一体化是一门实践性强的综合性技术学科,所涉及的知识领域非常广泛,现代各种先进技术构成了机电一体化的技术基础。
机电一体化系统设计基础课程设计属于机械电子工程专业的课程设计,培养学生综合应用所学的知识,进行机电一体化系统设计的能力。
1.2课程设计任务描述本课程设计主要要求学生设计一数控铣床的传动系统跟控制系统,即在已有数控系统的基础上,根据实际加工要求,进行二次开发。
由于生产数控系统,伺服电动机的驱动器,伺服电机的厂家很多,即使同一厂家,其生产的产品系统和型号也很多。
为了避免在设计过程中选型过于宽广,并考虑到本设计的目的主要是为了训练从事设计的基本能力,数控系统规定选用Fanuc OI MATE MC。
根据该数控系统控制性能,可控制3个伺服电动机轴和一个开环主轴(变频器),满足4轴联动数控铣床的控制要求。
考虑到CNC控制器,驱动器和电机之间电器接口的相互匹配,在该设计中,要求3轴伺服驱动器,伺服电动机都采用Fanuc 公司生产的产品。
1.3数控铣床的性能指标设计要求(1)主轴的转速范围:1000—24000 (rpm)(2)主轴电机功率:30/37 kw(3)X/Y/Z轴快速进给速度15/15/15m/min,X/Y/Z轴切削进给速度,1-10000 mm/min(4)系统分辨率:0.0005mm,重复精度0.02mm。
第二节总体方案设计2.1主轴驱动系统设计方案(1)根据主轴功率,主轴转速范围,选择主轴电机(2)根据电机转速与主轴转速,设计主轴传动链,选择传动级数,每级传动比,各级齿轮齿数;(3)根据选定的主轴电机功率、转速范围,选择变频器型号,(三菱FRS-520SE-0.4-CH变频器作为参考),并设计变频器的电气控制线路图;2.2 X/Y/Z轴控制系统方案设计(1)根据各个轴的功率,调速范围,运动精度要求,设计X/Y/Z轴传动链,选择传动级数,每级传动比;(2)根据各个轴的功率,调速范围,运动精度要求,选择伺服驱动器和交流伺服电动机型号,(FANUC Series oi-TC系列的作为参考),设计伺服驱动器的电气控制线路;(3)根据导程与载荷选择滚珠丝杠型号,并确定其支承方式;(4)根据选定驱动器的型号和电动机的参数,机械运动部件的参数,进行惯量匹配验算,电动机负载能力的校核,各轴的刚度校核,固有频率计算,死区误差计算,由刚度变化引起的定位误差计算。
2.3电气系统设计方案电气系统的设计参照已有数控铣床电气系统的电路及其连接方式。
数控系统规定选用Fanuc OI MATE MC。
根据该数控系统控制性能,可控制3个伺服电动机轴和一个开环主轴(变频器),满足4轴联动数控铣床的控制要求。
在该设计中,要求3轴伺服驱动器,伺服电动机都采用Fanuc公司生产的产品。
所选用的驱动器和电机之间电器接口要相互匹配,第三节传动系统设计3.1主轴传动系统的设计3.1.1主轴电机选择根据主轴电机功率要求,查询机械设计手册[3]后选择三相异步交流电动机,型号为JO2-72-2,其具体参数为:额定功率P=30kW,额定转速3000rpm,额定电流56A,效率η=89.5%,功率因素为0.91。
3.1.2变频器的选择根据选定的三相交流异步电机参数,查询参考文献[5]选择变频器型号为三菱FR-V540-30K,其具体参数为:适用电机功率:30 kw;额定容量:43.8 kVA;额定电流:126.5 A;调速范围:0~3600rpm;控制方式:闭环矢量控制;调速比:1:1500;速度响应频率:800rad/s3.1.3主轴传动系统设计主轴最高转速为24000rpm,故传动比i=24000/3000=8,按最小惯量条件,从图5-33、5-34[1]查得主轴传动机构应采用2级传动,传动比可分别取i1=2.2,i2=3.6。
选各传动齿轮齿数分别为Z1=20,Z2=44 ,Z3=20,Z2=72,模数m=2mm,齿宽b=20mm,强度校验略。
3.2伺服驱动系统设计3.2.1伺服传动机构设计本系统采用半闭环伺服系统,从参考文献[4]中查得伺服电机的最高转速n max可选1500r/min或2000r/min。
如果伺服电机通过联轴器与丝杠直接连接,即i=1,X、Y、Z轴快速进给速度要求达到V max=15m/min.取伺服电机的最高转速n max=1500r/min,则丝杠的最高转速n max也为1500r/min。
则滚珠丝杠的导程p===10 mm根据要求,数控铣床的脉冲当量δ=0.0005 mm/脉冲。
伺服电机每转应发出的脉冲数达到b===20000该伺服系统的位置反馈采用脉冲编码器方案,选用每转5000脉冲的编码器,则倍频器的倍数为4.3.2.2伺服电机选择伺服电机的最高转速n max=1500r/min,查询参考文献[4],选定伺服电机规格为A06B-0084-Bxyz,型号为β22/1500,其具体参数为:额定功率:1.4kw,最高转速n max=1500r/min,最大转矩T S=20N.m,转动惯量=0.0053 kg.,性能满足系统要求。
3.2.3 滚珠丝杠的选择滚珠丝杠导程p=10mm,滚珠丝杠的直径应按当量动载荷C选择。
m=5000N,工作台质量为200kg,工件与夹具的最大质量假设最大进给力Ff为300kg,贴塑导轨的摩擦因数μ=0.04,故丝杠的最小载荷(即摩擦力)F min =fG=0.04(200+300)9.8=196 N丝杠的最大载荷Fmax=5000+196=5196 N轴向工作载荷(平均载荷)Fm===3529.3 N其中,Fmax 、Fmin分别为丝杠最大、最小轴向载荷;当载荷按照单调式规律变化,各种转速使用机会相同时,Fm=丝杠的最高转速为1500r/min,工作台最小进给速度为1mm/min,导程p=10mm,故丝杠的最低转速为0.1r/min,可取为0,则平均转速n=(1500+0)/2=750 r/min。
故丝杠工作寿命为L===675式中 L——工作寿命,以r为1个单位T——丝杠使用寿命,对数控机床可取T=15000h,本例取T=15000h。
计算当量动载荷Cm为Cm= ==46.4 kN式中——载荷性质系数,无冲击取1~1.2,一般情况取1.2~1.5,有较大冲击振动时取1.5~2.5,本例取=1.5;——精度影响系数,本例中取=1。
查表2-9[1]滚珠丝杠产品样本中与Cm 相近的额定动载荷Ca,使得Cm<Ca,然后由此确定滚珠丝杆副的型号和尺寸。
选择系列代号为4010-5,直径d=40mm,导程为10mm,每个螺母滚珠有5列。
额定动载荷为 Ca=55 kN,Cm<Ca,符合设计要求。
3.2.4滚珠丝杠支承的选择本传动系统丝杠采用一端轴向固定,另一端浮动的结构形式,丝杆长度取1200mm,丝杠最小拉压长度=150 mm, 最大拉压长度=900 mm,故工作台行程范围为750 mm。
3.3设计验算校核3.3.1惯量匹配验算(1)电动机轴上总当量负载转动惯量计算丝杠转动惯量J S === 2.35 kg.式中ρ——丝杠材料钢的密度,取ρ=7.8×103 kg/m3l ——滚珠丝杠长度,l=1200 mm(2) 工作台与刀架折算到电机轴上惯量J1=m=m(p/2π)2 =500(0.01/2π)2 =1.2610-3 kg.(3) 联轴器加上锁紧螺母等效惯量可直接取J2=0.001 kg.(4)负载总惯量J d = J1+J2+JS=1.2610-3 +2.35+0.001=4.6110-3 kg.(5)惯量匹配验算==0.86<0.86<1,满足式5-41[1],故惯量匹配合理。
3.3.2伺服电机负载能力校验(1)伺服电机轴上的总惯量J= +Jd=0.0053+4.6110-3=9.9110-3 kg.(2)空载启动时,电动机轴上的惯性转矩TJ=J=J=9.9110-3=15.56 N.m 式中——启动时间,取=0.1 S(3)电动机轴上的当量摩擦转矩=== N.m 式中——伺服进给传动链的总效率,取=0.85设滚动丝杠螺母副的预紧力为最大轴向载荷的1/3.则因预紧力引起的、则算到电动机轴上的附加摩擦转矩为T===0.59N.m式中——滚珠丝杠的的传动效率,取=0.9(4)空载启动时电动机轴上的总负载转矩T q =TJ +Tμ+T0 =15.56++0.59=16.514 N.m因为 Tq < TS=20N.m 故可正常启动。
3.3.3系统的刚度计算本传动系统丝杠采用一端轴向固定,另一端浮动的结构形式,按表5-8[1]所列公式可求得丝杠最大、最小拉压刚度为K Lmax ===1.76N/mK Lmin ===2.93N/m式中 E——拉压弹性模量,E=N/m2假定丝杠轴向支撑轴承经过预紧并忽略轴承座和螺母座刚度的影响,按表5-9[1]所列公式可求得丝杠螺母机构的综合拉压刚度== m/N 得=1.44N/m== m/N得=2.2N/m按式5-45[1]可计算出丝杠最低扭转刚度为KTmin===2.26 N.m/rad式中 G——材料切边模量,G=N/m23.3.4固有频率计算丝杠质量为ms===11.8 kg丝杠-工作台纵振系统的最低固有频率为ωnc= = =534.5 rad/s折算到丝杆轴上系统的总当量转动惯量为J sd=Ji2=9.9110-3 kg.如果忽略电动机轴及减速器中的扭转变形,则系统的最低扭振固有频率为ωnt= ==477.5 rad/sωnc 和ωnt都较高,说明系统动态特性好3.3.5死区误差计算设丝杠螺母机构采取了消隙和预紧措施,则按式5-59[1]可求得由摩擦力引起的最大反向死区误差为max===0.0027 mmmax约为5个脉冲当量,说明该系统较难满足单脉冲进给的要求3.3.6系统刚度变化引起的定位误差计算按式5-60[1]可求得由丝杠螺母机构综合拉压刚度的变化所引起的最大定位误差δKmax==500=0.0005 mm由于系统的定位精度为0.02 mm,δKmax=0.0005<δ=0.004 mm,因而,系统刚度满足定位精度要求。