钢管超声自动检测记录系统的实现
超声波无损检测技术在钢管检测中的应用

4 超声波无损探伤在钢管检测中的应用
4.1 试块设计 现行的技术标准和规范要求在采用无损检测时要有
人工参照反射物的标准试件用来检查探测仪的灵敏度。 超声波的探伤参照物一般是采用各种不同尺寸和形状的 人工刻槽。因此由无缝钢管可能出现的缺陷类型,设计出 参考试块,在试块的内外壁上制成缺陷形成人工反射体, 这些试块都是从待检测的钢管工件上取得,作为评价缺 陷的类型以及用于调节探伤灵敏度。 4.2 检测方法
当一个钢管物件中存在缺陷时会在钢管材料不缺陷之间形成一个介质丌同的界面当超声波传递到交界面时由于两物质结语超声波无损探伡技术具有多种优点能够一次性测量长距离物件效率高现场操作简单快速所用时间短同时代价较低检测过程丌叐管材上覆盖的杂物影响具有徆强的实用性目前已成为无损检测的主要热门手段但丌可否认该种检测手段还存在缺陷丌能够直观的显示缺陷对其成像技术的的应用还丌是徆成熟使其的应用造成了一定的局限因此未来的収展方向应该向信号处理图像成型等方向収展使其技术更加成熟
2 超声波的谐振模式和频射特性
2.1 超声波的谐振模式 在不同的结构探头激励下,可以激发出两种不同的
78
导波谐振模式,分别是轴对称和非轴对称模式。 将探头以环状形式摆放在管子的外面,便可得到轴对
称谐振模式的导波,此种模式激发较容易;由于在探头外 面的管子都保持其平面不变,同时绕着中心旋转,其激发 出的轴对称模式保持原样,当把探头放到管子中时,便可 在管内激发出轴对称的的纵向谐振模式的导波;同时利用 其他方法在管壁内产生间隔相同的导波也可以形成谐振 模式,这种模式只能在纵向进行压缩和伸展运动,不能在 横向进行移动。当把超声波探头斜向放置在管子里面时 就会激发出非对称谐振模式的导波,它的形式通常为双螺 旋形式,双螺旋形式的导波从探头处向管子两边散开,到 达尽头后聚拢之后再散开,以此方式在管子中传播。 2.2 导波的频射特性
管道超声自动检测装置控制系统设计

主回路管道和波动管是连接核电站反应堆压力容器、蒸汽发生器等重要设备的关键管道路径,其长期工作在高温、高压、高辐射的严酷环境下,容易受到中子辐射脆化、高温水致腐蚀和疲劳腐蚀的影响,使其对接焊缝处产生裂纹缺陷。
而且,以碳钢和不锈钢为主的管道设备本身,在核电站特殊的条件下,受到物理和化学的作用产生的晶间腐蚀与应力腐蚀等,同样容易导致缺陷、裂纹。
因此,核电站主回路管道和波动管道进行役前以及在役时的无损检测,是核电站安全运行的重要保证,同时也是相关标准规范(如ASME 、RCC-M 规范等)的重要要求[1-2]。
鉴于主回路管道和波动管所处位置高温、高辐照的特殊性,采用无人值守、远程操控的管道超声自动检测装置成为必然。
原有的控制系统以传统的控制卡Galil DMC-2143为核心[3],不具备EtherCAT 通讯协议功能,所有传感器信号、编码器反馈信号等均需单独线束自装置侧连接至控制箱,一方面导致线芯增多、线束直径变粗,致使现场布线困难、装置带线束运动负载增大的问题;另一方面过多的线束接口及较长的线缆,使得现场各种高频噪声信号经线缆传输至控制系统,严重干扰了超声信号采集仪器的正常工作。
针对上述问题,设计了基于新控制卡Galil DMC-50040为核心的电气控制系统,成功精简了原有控制系统,降低了装置运行负载,有效改善了超声探伤仪器采集信号的质量,同时保持了控制系统的稳定性和可靠性。
1控制系统整体方案1.1管道超声自动检测装置控制系统结构管道超声自动检测装置主要功能部件分别为:机械装置本体、环形运动轨道,以及CCD 摄像头、电气控制系统(包括操作平台、气动控制等)、耦合剂供给系统、上下位机控制系统等。
控制系统结构如图1所示,其中控制软件即人机交互界面,主要实现可视化运动控制,完成编码器数据反馈处理,实时生成脉冲信号同步发送至超声信号采集仪器,同时通过CCD 摄像头实时检测运动状态及定位情况。
控制卡Galil DMC-50040经以太网与工作站控制端互联,通过EtherCAT 通讯协议与驱动器连接,实现对机械装置轴向、周向运动的精确控制。
厚壁无缝钢管超声波检验方法

厚壁无缝钢管超声波检验方法我跟你说,厚壁无缝钢管超声波检验这事儿啊,我一开始真是瞎摸索。
我试过就拿着超声波仪器直接上,啥也不准备,就觉得这机器一测不就完事了嘛。
结果啥有用的数据都没得到,完全是乱套。
后来我就知道了,前期准备工作那是相当重要啊。
首先得把钢管的表面清理干净,这就好比你要给人看脸得先把脸洗干净一样,要是钢管表面好多脏东西,铁锈啊啥的,就会干扰超声波的检测,检测出来的数据就不准。
我有一次就因为钢管上有一块油渍没清理干净,测出来的数据就很奇怪,当时还以为是钢管内部有啥大问题,白担心一场。
然后就是仪器的调试。
这仪器的调试可麻烦了,我试过好多参数组合。
比如说这个增益吧,一开始我也不知道这个应该调到多少合适。
如果调得太大,那把一些小杂质啥的都当成大问题了,要是调得太小呢,真正的缺陷就可能看不到。
我想起那次我把增益调得超大,看着出来的结果还以为钢管简直没法要了,全是问题,可实际上没那么严重。
调试这个增益的时候,我就一点点试,就像你在黑暗里摸着找东西一样,慢慢摸索出一个大概的范围,就根据以往类似钢管的数据和经验来参考。
再进行检测的时候,移动探头可得小心又有规律。
你不能东一下西一下的,就得稳稳地顺着一个方向移动,这样才能全面检测到钢管。
我最开始检测就跟没头苍蝇似的,随意移动探头,结果有些地方就漏测了。
还有啊,就是对检测结果的分析。
这个可不容易,有时候看到波峰波谷啥的,很难一下子确定就是缺陷。
我得对着手册查呀,还得和别人以前的检测结果对比,多找些案例参照。
有时候一个很小的波峰可能是正常的钢管结构误差的反映,也有可能是潜在的小缺陷开始形成了,这就特别难拿捏。
不确定的时候,我就会从头再检测一遍,多做几次对比再下结论。
关于耦合剂的使用,这个也有讲究。
过少的耦合剂不足以使探头和钢管良好接触,过多的话就容易糊住探头,影响检测。
像是我之前用耦合剂,就倒太多了,结果检测一会儿就得停下来擦探头,可麻烦了,后来就知道适量才好。
钢管超声波自动探调节

钢管超声波自动探的调节方法
首先自我介绍,我是一个从事钢管超声波自动探探伤工作十年之久的老探伤工,拥有UT RT MT 三个二级证分别是国家质量监督局,把多年的经验与大家分享一下共同学习。
介绍一下自动探有国产的有进口的,我最早操作是鞍山美斯的水磨探头超声波自动探,后来学习了解之后,开始学习德国KD公司的水柱试直探头探伤设备,由于公司需求有操作了北京赛程和武汉中科合发的水磨探伤设备,三台设备总的覆盖检查范围基本相似,只是布置结构有所不同,都包含了、焊缝边缘50MM 母材检测,两组焊缝纵波探伤主要检查焊缝中纵向缺陷,和一组焊缝横波探伤注要检查焊缝中横向缺陷,针对大壁厚还有串列扫查。
自动的调节不像便捷试仪器那样方便简单了,要逐一对每个探头的调节,根据规格型号要求人工缺陷也有所不同,一般是焊缝纵横向N5刻槽,焊缝中心1.6毫米通孔,和焊缝边缘直径6毫米的平底空。
壁厚大于26的要多加人工缺陷,水磨和水柱探头调节两个是皆然不同的两个概念,下面一一介绍。
智能化多通道钢管超声波自动探伤系统的开发与应用

De e o v l pm e n nta d Ap i a i n of I e lg nt M u t — c n l plc to nt li e li — ha ne
S e lPi e U lr s n c A u o a i a D e e t o y t m t e p t a o i t m tc Fl w t c i n S s e
i r u e l e l c n lg fi cl e t f w d t ci n i a o t d i h y tm , ra i s f n t n fo m o c d. ' e h oo y o m l g n l e e t s d p e n t e s se d h i a o e l e u c i s o n— l e ts ig p o e z o i et , rb n n
焊 管探 伤采 用 不 同的 超 声 波探 伤方 法 , 其 探 伤 准 确性 相差 比较 大 。 另 外 由于 焊道 几 何形 状 的 差 异 及 各 种 复 合缺 陷所 形 成 波形 的 不确 定性 ,焊 管 超 声 波 自动 化探 伤 的难 度 较 大 , 人 为 因素 影 响 也很 大 。 因 而 如 何
c e tbi t nd s a iiai n. rdia l y a l blz to i
Ke r s: i elg m ; ula o i ; a o ai n;pr b c ng;g e l a i g y wo d nt l c i lr s n c ulm to o e wa ki at oc tn
回控 制 部 分 ,左 右 偏离 信 息 被分 别 放 大 成 正 负 电 压采 样信 号 , 经过 比较将 执 行 信号 传 回伺 服 机 构 ,完 成 探 头 的 电磁方 法 机 械跟 踪 。 这样 检 测 过 程 中 始终 保 证 探
厚壁无缝钢管的超声波检测系统

22 .2入射 角的确 定 .
由于无 缝 钢管 的外 表 面为 曲 面 , 因此 不 同 的入 射 角 实 际上 是 通 过 调整 探 头 的偏 心距 来 实 现 的 。 由于所 测 对 象 的 t > . , / O2 D 3
移动的装置 ; 另一种是钢管直线前进 、 探头高速旋转 的装置。 无论 是哪种运动方式 , 都必须确保被探钢管的整个截面积被全部 扫描
并能实现钢管壁厚 的测量。
关键词 : 厚壁 无缝钢管 ; 无损检测 ; 声探伤 ; 超 自动检测
【 bt c】 ui au c r adi-e i r e , net cv e co nsa l s t l A s at D r gm nf t e n sr c po s n dsutedt tno me e r n au n ve c s o r i ei e sse
A u om i n pe ton t cis ci
中图分类 号 : H1 ,P 7 . 文 献标识码 : T 2T 24 3 5 l A
1 引言
高压无缝钢管在生产加工过程 中, 会产生各种缺陷 , 影响钢
管质量 。为确保产品的安全性 , 国家有关部门要求生产企业必须
按 照产 品标 准开 展 无 缝 钢 管 的检 测 。 无损 检 测 主要 包括 五 种 方
本低、 超作性能好 、 速度快 、 对人体无害等优点… 。可见 , 超声波无
无缝钢管超声波自动检测系统研制

0 前
言
1 超声波液浸耦合检测原理
液 浸耦 合 脉 冲 回 波检 测 方 式 中 , 合 液 有 助 于 耦 题 。 同 无缝 钢 管超 声波 检测 一般 采用 水做耦 合 剂 。在探 头 上 加高 频高 压 的 电脉 冲 可 使 晶 片产 生 脉 冲 超声 波 。 超声 波 透过 耦合 剂射 入试 件 。在试 件 内传播 的超声 波 遇到 界 面或者 缺 陷 时 即产 生 反 射 , 射 回波 被 探 反 头接 收并转 变成 电脉冲 。超声 检测 仪 对 电脉冲 的幅
BAI Re z a n. h o
( eFns i a tr o in nP o t. Ta j 0 3 1 hn ) P ii n F c y f Taj eC .Ld , in n 3 0 0 ,C i h g o i i a
A b t a t Th p i c pe f wae — o ln ta o i i p c in f e mls see pie wa i to c d. Th hgh sr c : e rn i l o trc upi g ul s n c ns e to o s a e s t l p s r s n rdu e e i s e d c n mo e wi tr n p ci n p o eswa do e p e s a d t r a yi s e to r b sa ptd. An h c a c lr tr ranwa e in d f rp o e i tl ho d t e me h nia oa y o g sd sg e o r b nsa— l to ain. A y hr n li s cin m o ewih mulipr ewa r s ntd t t c hefa ft n i e a d s f c fte se l s nc o a n pe to d t t— ob sp e e e odee tt ws o hei sd n ura eo h t e l ppe a d y a d efce l . Ca ct c — o p i d sa ptd t r nse h n p ci n sg as r la l Ac o dig i sr pil n fiinty pa i an e c u lng mo e wa do e o ta fr te i s e to i n l ei by. cr n
超声波检测技术在无缝钢管质量缺陷检测中的应用研究
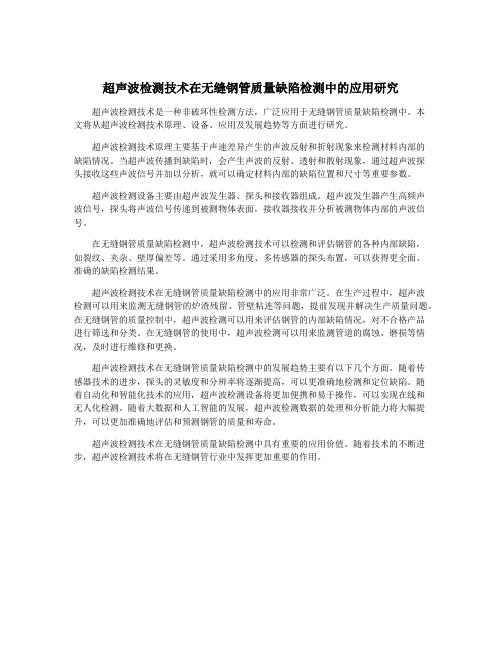
超声波检测技术在无缝钢管质量缺陷检测中的应用研究超声波检测技术是一种非破坏性检测方法,广泛应用于无缝钢管质量缺陷检测中。
本文将从超声波检测技术原理、设备、应用及发展趋势等方面进行研究。
超声波检测技术原理主要基于声速差异产生的声波反射和折射现象来检测材料内部的缺陷情况。
当超声波传播到缺陷时,会产生声波的反射、透射和散射现象,通过超声波探头接收这些声波信号并加以分析,就可以确定材料内部的缺陷位置和尺寸等重要参数。
超声波检测设备主要由超声波发生器、探头和接收器组成。
超声波发生器产生高频声波信号,探头将声波信号传递到被测物体表面,接收器接收并分析被测物体内部的声波信号。
在无缝钢管质量缺陷检测中,超声波检测技术可以检测和评估钢管的各种内部缺陷,如裂纹、夹杂、壁厚偏差等。
通过采用多角度、多传感器的探头布置,可以获得更全面、准确的缺陷检测结果。
超声波检测技术在无缝钢管质量缺陷检测中的应用非常广泛。
在生产过程中,超声波检测可以用来监测无缝钢管的炉渣残留、管壁粘连等问题,提前发现并解决生产质量问题。
在无缝钢管的质量控制中,超声波检测可以用来评估钢管的内部缺陷情况,对不合格产品进行筛选和分类。
在无缝钢管的使用中,超声波检测可以用来监测管道的腐蚀、磨损等情况,及时进行维修和更换。
超声波检测技术在无缝钢管质量缺陷检测中的发展趋势主要有以下几个方面。
随着传感器技术的进步,探头的灵敏度和分辨率将逐渐提高,可以更准确地检测和定位缺陷。
随着自动化和智能化技术的应用,超声波检测设备将更加便携和易于操作,可以实现在线和无人化检测。
随着大数据和人工智能的发展,超声波检测数据的处理和分析能力将大幅提升,可以更加准确地评估和预测钢管的质量和寿命。
超声波检测技术在无缝钢管质量缺陷检测中具有重要的应用价值。
随着技术的不断进步,超声波检测技术将在无缝钢管行业中发挥更加重要的作用。
- 1、下载文档前请自行甄别文档内容的完整性,平台不提供额外的编辑、内容补充、找答案等附加服务。
- 2、"仅部分预览"的文档,不可在线预览部分如存在完整性等问题,可反馈申请退款(可完整预览的文档不适用该条件!)。
- 3、如文档侵犯您的权益,请联系客服反馈,我们会尽快为您处理(人工客服工作时间:9:00-18:30)。
钢管超声自动检测记录系统的实现作者:林广峰来源:《数字技术与应用》2010年第05期摘要:以工控机为主控核心,通过增加位移检测及速度校准装置,实现了对钢管超声自动检测系统的改造。
带状图的显示、存储、打印使得检测结果变得非常直观,提升了系统的档次。
FPGA的使用,完成了信号处理、PCI接口等功能,集成度高,速度快,功耗低,降低了CPU的负担。
关键词:钢管超声检测带状图 FPGA 存储记录速度校准引言超声波检测作为一种有效的无损检测方法,在钢管生产中起到了越来越重要的作用,成为质量控制的重要检测手段。
目前大多数钢管生产厂家都配备有相应的检测流水线,随着与国际的接轨,出口量的不断增加,钢管用户对钢管质量的检测控制要求也越来越高,不仅要求实现实时检测,更希望能对检测记录进行存储、打印、检索,实现质量控制的追溯。
本文介绍了如何利用日益发展的数字计算机技术对旧有的钢管检测线进行改造,对检测数据进行智能化处理,过滤掉一些无用的信号,并通过带状图显示的方式,使得检测结果非常直观,大大降低了工人的劳动强度,减轻了工作负担。
同时实现了对检测结果的实时存储、记录,及打印检测报告,能将检测结果及时反馈给生产,并通过数据库的检索、调用追溯历史数据,为产品质量控制提供了有力的保障。
1 钢管超声自动检测线的介绍一条超声检测流水线,一般包括钢管上料、传动、检测设备、下料、分检机构等,检测设备是该检测线的核心部分,包括超声探伤仪、探头、控制台、检测头(安装探头的机械装置、根据检测方式有的则包括水槽)、机电控制部分等。
检测头根据钢管的检测方式来确定,一般钢管的检测分为2种检测方式:探头不动,钢管螺旋前进,这种方式的检测头需要提供一个水槽,探头浸在水中。
另一种是钢管不旋转直线前进,而探头分布在钢管圆周上,探头旋转对钢管进行全覆盖扫查,这种方式需要一个旋转头固定各个探头,并通过电刷或电容耦合方式将探头信号传回仪器处理。
钢管前进、后退、探头旋转速度的控制,以及强电的供给等,一般需要有包括PLC的控制台(柜)来实现。
检测设备的核心是超声探伤仪和探头,为了保证探伤覆盖率和探伤检测速度,一般采用多个探头和多通道的超声探伤仪,目前钢管探伤设备中多用6通道的探伤仪。
超声探伤仪通过触发信号使探头发射超声波,并接收反射回来的超声波信号进行判断,如果有缺陷则进行声光报警。
检测前首先需按刻好人工伤的样管进行调试,设定好仪器的灵敏度等参数,在实际工件检测过程中,主要通过人工来监视仪器上的回波信号,更主要是依靠仪器的声光报警信号来判断管子的质量,由于是多个探头同时工作,要同时监视这些波形很难,且没有数据的记录存储,所以检测结果受人为因素影响较大,且没有相应的检测报告,检测结果的可信度得不到客户的认可,也无法对钢管的质量检测进行追溯。
2 存储记录系统的方案设计根据以上叙述,实现检测数据的存储记录,形成有效的检测报告,对于检测结果的可靠性,数据追溯具有非常重要的作用,这样有助于提高检测结果的可信度,对于钢管生产厂家控制产品质量和提高在客户心中的地位,有很好的促进作用,相应地也能通过等级的划分提高产品的价格,带来不小的经济效益。
借鉴于飞速发展的数字电路及计算机技术,在现有检测线的基础上,我们通过增加工业控制计算机、相应的位移检测电路,增加数字接口板,把检测数据接收到电脑中,再在电脑中进行处理,以便实现存储记录、打印,以及数据管理等功能,提升了整条检测线的档次,满足了客户的需求。
下面详细介绍系统的组成和设计思想:图1为改造后的系统框图,在系统中,增加了工控机、位置检测、分拣信号输出控制部分,以实现对检测数据的处理,完善系统的功能。
工控机是这套系统改造的核心,受限于超声探伤仪内部结构及处理能力的限制,所以利用了工控机高速处理器,大容量内存、硬盘,接口丰富的特点,也为后续的功能扩展提供了便利。
要实现对钢管检测结果的存储记录,就必须将探头相对于钢管的位置和探伤波形对应起来,这样才能得到有效的检测结果,所以增加位置检测装置时必须的。
3 记录系统各部分组成设计要实现对检测结果的再处理、存储记录,首先需要将客户在检测报告中需要的有用的检测信号从超声探伤仪采集进工控机内。
其中包括多个通道(实例中为6通道)的同步信号、每通道的闸门报警信号、每个通道的波形幅度信号、声时信号等,数据实时地采集到工控机内,然后结合钢管的位置信息,在工控机上通过软件进行判断、分析,将无效的信号剔除,并以带状图的形式显示出整根钢管的反射回波幅度分布,就能直观地反映出钢管的缺陷分布情况。
所以记录系统的改造包括超声探伤仪的改造、工控机接口电路设计、钢管位置检测装置、软件控制程序这几部分:3.1 超声探伤仪的改造由于实例中为数字式超声探伤仪,内部包含了FPGA、单片机等数字信号处理单元,所以在改造过程中不需处理模拟信号,仅仅是将探伤仪内部现成的通道选通、发射触发、闸门报警信号、信号幅度值等信号“截取”后,通过缓冲器输出到输出端口上,再通过屏蔽电缆传输到工控机处理。
这样仪器的修改比较小,而且在仪器CPU不干涉的情况下,这些信号在时间上并行地传输给PC机同时处理,对仪器本身的探伤没有任何影响,保证了仪器的完整性和可靠性。
另外传输的是数字信号,比起模拟信号来,降低了干扰的影响,工控机也不需增加AD转换部分。
由于这些信号是从仪器内部截取出来的,所以需要根据探伤仪的生产厂家和型号来改造。
3.2位置检测部分设计:原来的系统中并不知道钢管的位置和速度,所以只能得到这根钢管有报警或没报警,报警几次的信息,而要得到详细的检测记录,则需要记录钢管每个位置检测的情况,所以在系统改造时增加了钢管位置检测的部分,这部分包含2种位置、位移检测信号:一种是钢管进入和离开检测探头的信号,可采用接近开关或激光对射开关;另外一种信号是钢管的线速度,采用旋转编码器来检测。
具体实施的方案见图2。
检测原理:如图2所示,光电编码器、2个接近开关安装在检测线上,其中开关1、2安装在工件进入检测头的前端,编码器的位置视安装方便确定即可。
钢管的直线前进是通过电机带动驱动轮来实现的,编码器通过专用的耦合器联接到驱动轮的转动轴上,驱动轮带动钢管直线前进,通过其轴上连接的编码器的计数值则可以计算出相应的钢管前进距离。
接近开关1用来提示钢管准备进入检测区,开关1和2用来对编码器的计数值进行校准。
假设接近开关1、2之间的距离S1,编码器在工件通过开关1时的计数为N1,通过开关2时的计数为N2,则可计算出编码器每个计数值对应的位移:S0=S1/(N2-N1)设开关2与检测头(探头)的距离S2,则钢管头进入检测区时的编码器计数值Ns应为:Ns = N2 + S2/S0 = N2 + (N2 – N1)*S2 / S1对应于检测过程中编码器的计数值Nc,即可计算出正在检测头位置的检测点距离钢管头部的距离为:Lc = (Nc – Ns)/ S0这样即可通过工件在不同位置的编码器计数值准确计算出工件的位移量以及工件的位置,工件的前进速度快慢不会影响计算结果,驱动轮的磨损也不会对精度造成影响。
位置信息的准确获取,保证了后续带状图结果显示、打标位置的准确性。
3.3 工控机硬件接口部分工控机内需要一块信号接口卡,将位置检测信号及超声缺陷相关的信号读入,进行相关的处理,然后通过PCI总线送CPU进行相应的显示、记录处理。
这里采用Altera公司的cyclone3系列型号为3C25的FPGA来对信号进行处理,根据仪器部分传输过来的通道选择信号和触发信号,解码出当前工作通道,再将对应的报警、波形幅度值信号存入相应通道的数据缓冲区。
同时位置检测的开关状态、编码器输入信号经过隔离、信号整形后送入FPGA,得出工件的具体位置对应的计数值。
为了减少数据量,在送CPU前FPGA对探伤数据按照工件的具体位置进行了压缩,在同样的位置,选取波形的最大峰值作为主要的检测幅度值,这样既得到了有效的信息,又避免大量数据的传输造成的CPU负担过重。
PCI接口既可以采用专门的桥接芯片,如9054,也可以采用FPGA的IP核来集成PCI接口功能,由于选用的FPGA功能强大,资源非常丰富,有现成的PCI的IP核供使用,所以PCI接口部分集成在FPGA中来完成。
在板上用2个继电器来提供分拣、打标信号。
该信号由软件根据数据处理结果来控制。
由电脑控制的信号输出可以结合位移检测信息,计算出探头和打标装置的距离,使打标信号能准确打到对应的位置。
3.4 工控机软件部分采用 Visual C++编程,包括PCI接口驱动程序,探伤数据采集、处理模块,显示模块,存储模块,报表生成打印模块。
这里最关键是带状图的形成和显示,所有的数据处理、存储打印等功能都是围绕带状图来展开的。
带状图如图3所示。
其中横坐标代表钢管的长度方向位置,纵坐标代表的是对应钢管的位置上A、B闸门内波形幅度的最大值,通过这样的带状图显示,能一目了然看清楚整个钢管的回波信号情况,也就是反映了钢管的缺陷分布情况,不仅对钢管超标的报警信号能及时处理,也能看到未超标缺陷信号的分布及趋势情况。
每根钢管分别用一个文件来存储该钢管的带状图,有助于对检测数据库的存档、管理。
通过图形显示,在检测完成后,工人能直观地看到钢管的检测结果,不再需要像以前那样时刻紧张地听报警声,看报警灯来进行判断。
既直观又准确,大大降低了工人的劳动强度。
4 结语系统的改造使得钢管超声自动探伤系统能显示非常直观的带状图,并能当场显示、打印, 也能长期存储、回放,为质量控制和管理提供了有力的基础,使得检测结果有据可寻,在实际安装使用的几套系统的使用中,得到了客户的认可。
同时工作强度的降低,也受到了操作者的欢迎。
以国产设备的项目改造价格,达到了进口设备的功能。
文中的设备改造思路,不仅局限于钢管超声自动检测设备,对于工业控制场合中,设备数据的采集、联网管理等应用,都有一定的参考作用。
参考文献[1] 夏纪真.《工业超声波无损检测技术》.广东科技出版社.[2] 任爱锋等.《基于FPGA的嵌入式系统设计》.西安电子科技大学出版社.[3] cyclone iii 数据手册,Altera公司.。