第七章 成型零部件设计
成型零部件设计PPT课件

.
1
一、概述
1、成型零部件
塑料模具中与塑料接触并决定制品形状和尺寸的模具零部件 统称。
成型零部件包括:
凹模、凸模、型芯、型环、成型镶块等。
2、模腔
模具闭合后,由成型零部件组合在一起形成的闭 合空腔称模腔。制品的形状和尺寸实际上是由模腔决 定的。
2
一、概述
3、设计准则
根据制品的形状结构,生产能量和使用要求,并 考虑模块的使用寿命,合理的设计成型零件的结构形 式,准确地计算它的尺寸和公差,并保证它有足够的 强度,刚度。
9
镶拼组合式凹模
a.局部镶拼 问题:凹模型腔内壁六个凸
起圆弧不易加工。
加工方法: 钻铰6孔——装 芯棒——加工大孔——取 芯棒——装型芯
10
镶拼组合式凹模
b.底部镶拼式凹模 问题:底部凸台不易加工和铣削
11
镶拼组合式凹模
4)优缺点 优点:a.可降低整体加工难度。
b.容易保证形状尺寸精度及表面质量。 c.可改善热处理性能。 d.拼缝可排气。 e.各处可选用不同模具材料。 缺点:a.拼缝处容易益料。 b.装配精度要求高。 c.整体强度,刚度降低。 d.模具结构复杂,整体尺寸增大。
18
凸模和型芯
嵌入式凸模(型芯) 1)特点:将凸模或型芯单独加工,
然后嵌入到固定板中。 2)适用:主要用于小型制品或大型模
具中的小型芯。
19
凸模和型芯
安装方式
20
凸模和型芯
镶拼组合式凸模 特点:与镶拼凹模相似。将复杂转
化为简单形状 适用范围:内形复杂制品
21
镶拼组合式凸模
22
凸模和型芯
活动式凸模 瓣合式 侧向型芯 活动凸模 浮动凸模
压铸工艺及模具设计:第7章 成型零件和模架设计
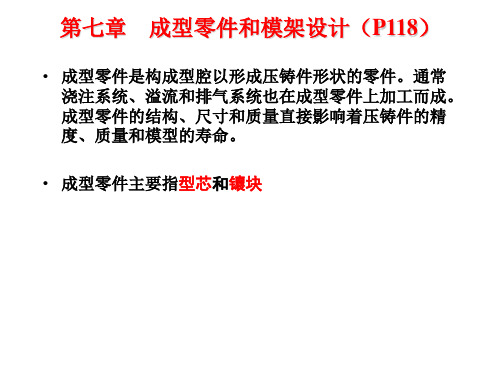
(一)主型芯的结构及固定形式 • 图7-6
(二)小型芯的结构及固定形式 • 图7-7,图7-8。
(二)小型芯的结构及固定形式
六、镶块和型芯的止转形式。
七、镶块和型芯的结构尺寸
(一)镶块壁厚尺寸
(二)整体镶块台阶尺寸
表7-8 整体镶块台阶尺寸推荐值
(三)组合式成型镶块固定部分长度
• 表7-9 组合式成型镶块固定部分长度推荐值
铸件实际尺寸的差与模具成型尺寸之比。即:
• A型-----室温下模具的成型尺寸(mm), • A实-----室温下压铸件的实际尺寸(mm)。
一、压铸件的收缩率 • (二)计算收缩率
• A’-----计算得到的模具成型零件的尺寸(mm), • A-----压铸件的公称尺寸(mm)。
常用压铸合金的计算收缩率腔尺寸(包括型腔深度尺寸) ②型芯尺寸(包括型芯高度尺寸)
③成型部分的中心距离和位置尺寸
(一)成型尺寸的分类及计算要点
成型尺寸计算的要点: • 因型腔磨损后尺寸增大,故计算型腔尺寸时应使得压
铸件外形接近于最小极限尺寸。
• 因型芯磨损后尺寸减小,故计算型腔尺寸时应使得压
铸件内形接近于最大极限尺寸。
• 1.壳体压铸件的成型尺寸分类
压铸件的①、②、③属于型腔尺寸;④、⑤、⑥属于 型芯尺寸;⑦、⑧属于中心距离、位置尺寸。另外, ②、⑤受到分型面的影响,高压、高速的金属液充填 型腔时,闭合的动、定模会出现微小的分离倾向,使 与分型面有关的尺寸略微增大。为消除这种影响,通 常将计算所得的公称尺寸减去0.05mm。
第七章 成型零件和模架设计(P118)
• 成型零件是构成型腔以形成压铸件形状的零件。通常 浇注系统、溢流和排气系统也在成型零件上加工而成。 成型零件的结构、尺寸和质量直接影响着压铸件的精 度、质量和模型的寿命。
第7章成型零件及模架设计详述

成型尺寸的计算要点如下: ①型腔磨损后尺寸增大,计算型腔尺寸时应使压铸件外 形接近于最小极限尺寸。 ②型芯磨损后尺寸减小,计算型芯尺寸时应使压铸件内 形接近于最大极限尺寸。 ③两个型芯或型腔之间的中心距离和位置尺寸与磨损量 无关,应使压铸件尺寸接近于最大和最小两个极限尺寸的 平均值。
2.成型尺寸标注形式及偏差分布的规定 上述三类成型尺寸,分别采用三种不同的计算方法。
镶块壁厚尺寸推荐值见表7-7。
2.整体镶块台阶尺寸 整体镶块台阶尺寸推荐值见表7-8
3.组合式成型镶块固定部分长度 组合式成型镶块固定部分长度推荐值见表7-9
4.圆形型芯结构尺寸 圆形型芯结构尺寸推荐值见表7-10
7.2成型零件成型尺寸的计算 7.2.1压铸件的收缩率 1.实际收缩率
压铸件的收缩率是指室温时,模具成型尺寸与压铸件对 应尺寸的相对变化率。又称为实际收缩率。即
L模 L铸 100%
L模
常用压铸合金的计算收缩率见表7-11。
2.计算收缩率(室温下压铸件尺寸与模具尺寸的相对差值) 设计模具时,计算成型零件成型尺寸所采用的收缩率为
计算收缩率。它包括了压铸件收缩值及模具成型零件在工作 温度时的膨胀值,即
计
L模 L铸 L铸
100%
L模 L铸(1%)
3.收缩率的确定 压铸件的收缩率应根据压铸件的结构特点、收缩条件
φ50的尺寸要换算成单向公差尺寸,其结果是: 49.900.22
计算结果如下表:
序号 类别
压铸件 尺寸
计算公式
模具尺寸
1
型 径向 腔
500.10 0.32
2
尺 深度
寸
2000.12
50.0500.055
20.04
第7章 成型零部件设计PPT课件

1.螺纹型芯与型环径向尺寸
螺纹型芯
※塑件可能产生的最大误差δ为各种误差的总和:
δ=δz+δc+δs+δj
式中
δz——成型零部件制造误差; δc——成型零部件的磨损量; δs——塑料的收缩率波动引起的塑件尺寸变化值; δj——由于配合间隙引起塑件尺寸误差; Δ——塑件的公差。
※塑件的公差Δ应大于或等于各种因素引起的积累误差之和δ,
即Δ≥δ
(4)中心距尺寸
影响模具中心距误差的因素:塑件收缩率,磨损量不会影响中 心距尺寸。
中心距误差表示方法:双向公差。塑件上中心距
Cs
1 2
,模具成
型零件的中心距为 Cm
1 2
z
,其平均值即为其基本尺寸。
塑件、模具中心距的关系:型芯与成型孔的磨损可认为是沿圆 周均匀磨损,不影响中心距,计算时仅考虑塑料收缩,而不考虑磨
对异形型芯为便于加工,可做成图7—13的结构,将 下面部分做成圆柱形 (a),甚至只将成型部分做成异形, 下面固定与配合部分均做成圆形(b)。
对于多个互相靠近的小型芯,用台肩固定时发生重叠 干涉,可将台肩相碰的一面磨去,将型芯固定板的台 阶孔加工成大孔,然后嵌入型芯。
二、螺纹型芯与螺纹型环
作用:分别用于成型塑件的内螺纹和外螺纹。 成型后塑件从螺纹型芯或螺纹型环上脱卸的方式: 强制脱卸、模内自动脱卸和模外手动脱卸。
成型其主体部分内表面的零件 称为主型芯
成型零部件结构设计
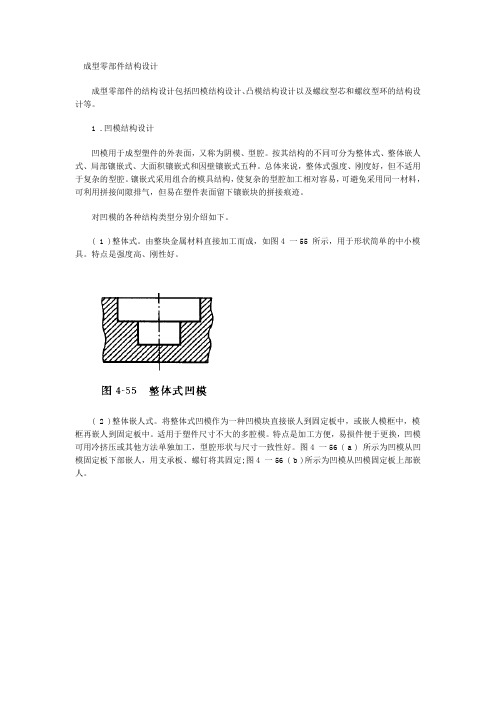
成型零部件结构设计成型零部件的结构设计包括凹模结构设计、凸模结构设计以及螺纹型芯和螺纹型环的结构设计等。
1 .凹模结构设计凹模用于成型塑件的外表面,又称为阴模、型腔。
按其结构的不同可分为整体式、整体嵌人式、局部镶嵌式、大面积镶嵌式和因壁镶嵌式五种。
总体来说,整体式强度、刚度好,但不适用于复杂的型腔。
镶嵌式采用组合的模具结构,使复杂的型腔加工相对容易,可避免采用同一材料,可利用拼接间隙排气,但易在塑件表面留下镶嵌块的拼接痕迹。
对凹模的各种结构类型分别介绍如下。
( 1 )整体式。
由整块金属材料直接加工而成,如图4 一55 所示,用于形状简单的中小模具。
特点是强度高、刚性好。
( 2 )整体嵌人式。
将整体式凹模作为一种凹模块直接嵌人到固定板中,或嵌人模框中,模框再嵌人到固定板中。
适用于塑件尺寸不大的多腔模。
特点是加工方便,易损件便于更换,凹模可用冷挤压或其他方法单独加工,型腔形状与尺寸一致性好。
图4 一56 ( a ) 所示为凹模从凹模固定板下部嵌人,用支承板、螺钉将其固定;图4 一56 ( b )所示为凹模从凹模固定板上部嵌人。
( 3 )局部镶嵌式。
当凹模局部形状复杂,或某一部分容易损坏需要经常更换,常采用局部镶嵌式结构。
如图4 一57 所示,其中,图4 一57 ( a )所示为嵌入圆销成型塑件表面直纹;图4 一57 ( b )所示为镶件成型塑件的沟槽;图4 一57 (。
)所示为镶件构成塑件圆环形筋槽;图4 一57 ( d )所示为镶件成型塑件底部复杂的构形。
( 4 )大面积镶嵌式。
对于底部或侧壁形状复杂的凹模,为了便于加工,保证精度,将凹模做成通孔式的,再镶上底,或将凹模壁做成镶嵌块。
适用于深腔或底部、侧壁难于加工的组合型模具型腔,但各个结合面的研磨、抛光增加了工时.图4 一58 ( a )所示为侧壁和底部大面积镶拼的凹模结构;图4 一58 ( b )所示为底部大面积镶嵌的结构,采用圆柱面配合。
( 5 )四壁镶嵌式。
第七章 成型零部件设计

第七章 成型零部件设计
§7.1 成型零部件的结构设计
2、组合式结构 这种结构是将型芯单独加工后,再镶入模板中。
通孔台肩式,凸模用台肩和模板连接,再用垫板、螺钉紧固;对于固定部分是圆柱面而型 芯有方向性的场合,可用销钉、键、“D”形定位。
图d 为底部大块镶嵌。
第七章 成型零部件设计
§7.1 成型零部件的结构设计
4)侧壁镶拼式凹模 这种结构便于加工和抛光,但一般很少采用,因为在成型时,熔融的塑料熔体 成型压力使螺钉和销钉产生变形。
第七章 成型零部件设计
§7.1 成型零部件的结构设计
5)四壁拼合式凹模 大型和形状复杂的凹模,可以把它的四壁和底板分别加工经研磨后压入模套中
第七章 成型零部件设计
§7.2成型零部件的工作尺寸计算
综上所述,制品可能产生的最大误差δ为上述各种误差的综合,即 δ=δz+δc+δs+δj+δf
δz——成型零件制造误差 δc——型腔使用过程中的总磨损量 δs——塑料收缩率波动引起塑件尺寸变化值 δj——因配合间隙变化引起塑件尺寸的变化值 δf——压制件水平溢边厚度波动引起的塑件高度尺寸变化。 各种误差累积后的误差值δ应小于或等于塑件的尺寸工差Δ,即:
第七章 成型零部件设计
§7.1 成型零部件的结构设计
3)底部镶拼式凹模 为了机械加工、研磨、抛光等方便,形状复杂的型腔底部可以设计成镶拼式
图a 底部台阶镶嵌,镶嵌形式简单,结合面在 磨平时应保证结合处的锐棱不影响脱模。
图b 圆柱面配合面不易楔入塑料。
第七章 成型零部件设计
§7.1 成型零部件的结构设计
第7章—成型零件与结构零件的设计(终).

①型腔较浅的小型单型腔模或型腔加工较简单的模具 ②压铸件形状简单、精度要求低的模具 ③生产批量小的模具 ④压铸机拉杆空间尺寸不大时
Page 5
2、组合式结构
型腔和型芯由整块材料制成,然后装入模板的模套内,再用 台肩或螺栓固定。
(a)
(b)
(c)
整体组合式型腔
Page 6
整体组合式型芯
Page 7
7.1.2 局部组合与完全组合式结构
1、局部组合式结构 ➢ 型腔或型芯由整块材料制成,局部镶有成型镶块。 2、完全组合式结构 ➢ 由多个镶拼件组合而成的成型空腔。
Page 8
局部组合式型腔的结构实例
Page 9
完全组合式结构
Page 10
7.1.3 组合式结构形式的特点
(1) 降低模具加工制造难度。 (2) 保证精度要求,提高了使用寿命。 (3) 提高设备利用率,减少工作量,提高生产效率,降低做
第7章 成型零件与结构零件的设计
第7章 成型零件与结构零件设计
7.1 成型零件的结构设计形式 7.2 成型尺寸的确定 7.3 成型零件的设计 7.4 模体的组合形式 7.5 模体主要结构件设计 7.6 模体结构零件的设计 7.7 加热与冷却系统的设计
Page 2Βιβλιοθήκη 7.1 成型零件结构设计7.1.1整体式与组合式结构 7.1.2局部组合与完全组合式结构 7.1.3组合式结构形式的特点 7.1.4小型芯的固定形式 7.1.5镶块固定形式和型芯的止转形式 7.1.6活动型芯的安装与定位 7.1.7成型零件的设计要点
Page 22
⑵分析成型零件受到冲击后的变化趋势 确定成型尺寸前,首先弄清各部位尺寸性质,方可确
定各部位尺寸及其公差取向。 ⑶消除相对位移或压射变形产生的尺寸误差
模具设计第七章成型零件结构设计

组合式
模具设计第七章成型零件结构设计
6.1 成型零部件结构设计
6.1.2 型芯的结构设计
1 .主型芯的结构设计
镶拼组合型芯 (溢料飞边与脱模方向)
模具设计第七章成型零件结构设计
6.1 成型零部件结构设计
6.1.2 型芯的结构设计
1 .主型芯的结构设计 镶拼组合型芯如图
镶拼组合型芯特点:与组合式基本相同(P143)
本章知识目标
1.掌握各种凹模和型芯的结构特点、适用范围装配要求; 2.掌握成型零件尺寸的计算方法; 3.会分析型腔壁厚和底板厚度受力情况,会运用公式和查表选择
数据确定型腔壁厚和底板厚度 4.掌握各结构零件作用、结构、安装形式、配合要求、材料的选 择和设计原则 。
模具设计第七章成型零件结构设计 2
6.1 成型零部件结构设计
模具设计第七章成型零件结构设计
6.1 成型零部件结构设计
6.1.1 凹模的结构设计
整体嵌入式型腔
通孔台肩式
若凹模镶件是回转体,而型腔是非回转体, 则需要用销钉或键定位 。
模具设计第七章成型零件结构设计
6.1 成型零部件结构设计
6.1.1 凹模的结构设计
整体嵌入式型腔
通孔无台肩式
盲孔式
装拆工艺 通孔
模具设计第七章成型零件结构设计
6.2 成型零部件的工作尺寸计算
6.2.1 计算成型零部件工作尺寸要考虑的要素
(3)、模具成型零件的磨损 c
模具成型零件的磨损
—— 型腔尺寸变大,型芯尺寸减小
➢造成磨损的原因:
①熔体流动冲刷 ②腐蚀性气体的锈蚀 ③脱模时的磨擦 ★(主要) ④由上述原因造成表面粗糙度增加而需重新打磨抛光
模具设计第七章成型零件结构设计 5
- 1、下载文档前请自行甄别文档内容的完整性,平台不提供额外的编辑、内容补充、找答案等附加服务。
- 2、"仅部分预览"的文档,不可在线预览部分如存在完整性等问题,可反馈申请退款(可完整预览的文档不适用该条件!)。
- 3、如文档侵犯您的权益,请联系客服反馈,我们会尽快为您处理(人工客服工作时间:9:00-18:30)。
0
第七章 成型零部件设计
2.型腔深度与型芯高度尺寸 (1)型腔深度 (1)型腔深度
按上述公差带标注原则, 按上述公差带标注原则,塑件高度尺寸为
+ 型腔深度尺寸为 H m 0 δ
z
H
0 s −∆
,
。
型腔底面和型芯端面均与塑件脱模方向垂直, 型腔底面和型芯端面均与塑件脱模方向垂直,磨损 很小, 很小,因此计算时磨损量 δ c 不予考虑, 不予考虑,则有
(7.1)
结论:塑件尺寸变化值δs与塑件尺寸成正比。对大尺 δs与塑件尺寸成正比 结论:塑件尺寸变化值δs与塑件尺寸成正比。 寸塑件,收缩率波动对塑件尺寸精度影响较大 影响较大。 寸塑件,收缩率波动对塑件尺寸精度影响较大。此时 ,只靠提高成型零件制造精度来减小塑件尺寸误差是 困难和不经济的, 困难和不经济的,应从工艺条件的稳定和选用收缩率 波动值小的塑料来提高塑件精度; 小尺寸塑件, 波动值小的塑料来提高塑件精度;对小尺寸塑件,收 缩率波动值的影响小 影响小, 缩率波动值的影响小,模具成型零件的公差及其磨损 量成为影响塑件精度的主要因素。 量成为影响塑件精度的主要因素。
2011-11-4
2
第七章 成型零部件设计
7.2.1 塑件、成型零件尺寸及公差标注的约定 塑件、
在计算前, 在计算前,对塑件尺寸和成型零部件的尺 寸偏差统一按“入体”原则标注。 寸偏差统一按“入体”原则标注。 1.对包容面(型腔和塑件内表面)尺寸采 对包容面(型腔和塑件内表面)尺寸采 用单向正偏差标注 基本尺寸为最小。例如图 标注, 1 用单向正偏差标注,基本尺寸为最小。例如图7.2.1-1 塑件内径、型腔尺寸。 为塑件公差,δz为 中,塑件内径、型腔尺寸。 (设∆为塑件公差,δz为 成型零件制造公差) 成型零件制造公差)
2 +δ z H m = [ H s + H s S cp − ∆]0 3
2011-11-4
19
第七章 成型零部件设计
(2)型芯高度 (2)型芯高度
同理可得型芯高度尺寸计算公式
hm = [hs + hs S cp + x ′∆]
对中、 对中、小型塑件则为
0 −δ z
7.11) (7.11)
2 0 hm = [ hs + hs S cp + ∆ ] −δ z 3
+δ z
3 Lm = Ls + Ls S cp − ∆ 4 0
(7.8) )
大尺寸和精度较低的塑件,δ z <Δ/3,δ c <Δ/6,上 大尺寸和精度较低的塑件, <Δ/3, <Δ/6, 式中Δ前面的系数x将减小,该系数值在1/2—3/4间 式中Δ前面的系数x将减小,该系数值在1/2—3/4间 1/2 变化。 变化。
2011-11-4
9
第七章 成型零部件设计
(4) 配合间隙引起的误差 配合间隙引起的误差原因,活动型芯的配合间隙, 配合间隙引起的误差原因,活动型芯的配合间隙, 的配合间隙 引起塑件孔的位置误差或中心距误差; 凹模与凸模 引起塑件孔的位置误差或中心距误差; 塑件孔的位置误差 分别安装于动模和定模时,合模导向机构中导柱和 分别安装于动模和定模时,合模导向机构中导柱和 导套的配合间隙,引起塑件的壁厚误差 塑件的壁厚误差。 导套的配合间隙,引起塑件的壁厚误差。
,可得型腔基本尺寸
1 Lm = Ls (1 + S cp ) − (∆ + δ z + δ c ) 2
据塑件公差来确定,成型零件制造公差 δ z 一般取 据塑件公差来确定,
1 1 ~ ∆ 3 6
δ z 和 δ c ,是影响塑件尺寸的主要因素,应根 是影响塑件尺寸的主要因素,
1 ;磨损量 δ c 一般取小于 6 ∆ ,故上式为
2011-11-4
3
第七章 成型零部件设计
2.对被包容面(型芯和塑件外表面)尺寸 对被包容面(型芯和塑件外表面) 采用单向负偏差标注,基本尺寸为最大, 单向负偏差标注 采用单向负偏差标注,基本尺寸为最大, 例如图7.2.1型芯尺寸和塑件外形尺寸。 例如图7.2.1-1中,型芯尺寸和塑件外形尺寸。 3.对中心距尺寸采用双向对称偏差标注, 对中心距尺寸采用双向对称偏差标注, ∆ 例如图7.2.1塑件间中心距为Cs± 例如图7.2.1-1中, 塑件间中心距为Cs± , 2 δz 型芯间的中心距为Cm± 型芯间的中心距为Cm± 。
2011-11-4 8
第七章 成型零部件设计
影响磨损量值的因素:成型塑件的材料、 影响磨损量值的因素:成型塑件的材料、成型 零部件的磨损性及生产纲领。 零部件的磨损性及生产纲领。 含玻璃纤维和石英粉等填料的塑件、 含玻璃纤维和石英粉等填料的塑件、型腔表面 耐磨性差的零部件取大值。设计时根据塑料材料、 耐磨性差的零部件取大值。设计时根据塑料材料、 成型零部件材料、 成型零部件材料、热处理及型腔表面状态和模具要 求的使用期限来确定最大磨损量, 求的使用期限来确定最大磨损量,中、小型塑件该 值一般取1 塑件公差,大型塑件则取小于1 值一般取1/6塑件公差,大型塑件则取小于1/6 塑件公差。 塑件公差。
2011-11-4 7
第七章 成型零部件设计
(2) 成型零部件的制造误差 包括:成型零部件的加工误差和安装、 包括:成型零部件的加工误差和安装、配合误 差。设计时一般应将成型零件的制造公差控制在塑 件相应公差的1 左右,通常取IT6 IT6— 件相应公差的1/3左右,通常取IT6—9级。 (3) 成型零部件的磨损 主要原因: 主要原因:塑料熔体在型腔中的流动以及脱模 时塑件与型腔的摩擦,以后者造成的磨损为主。 时塑件与型腔的摩擦,以后者造成的磨损为主。 简化计算, 简化计算,只考虑与塑件脱模方向平行的表面 的磨损, 的磨损,对垂直于脱模方向的表面的磨损则予以忽 略。
∆ ∆ Hm + − H s − S cp = H s − 2 2 2
2011-11-4 18
δz
第七章 成型零部件设计
整理后有: 整理后有:
H m = [ H s + H s S cp − x ′∆]
+δ z 0
(7.10) )
1 δ 对中、小型塑件, 对中、小型塑件, z = ∆ ,故得 3
Lm = Ls + Ls S cp − x∆
标注制造公差后得
(7.6) )
+δ z
Lm = Ls + Ls S cp − x∆
修正系数。 式中 x——修正系数。 修正系数
2011-11-4
[
]
0
(7.7) )
15
第七章 成型零部件设计
中、小型塑件, 小型塑件,
, δc , δ=∆/3, =∆/6,得 z
相关手册
2011-11-4
13
第七章 成型零部件设计
1.型腔与型芯径向尺寸 (1)型腔径向尺寸
∆ Ls,其公差值为Δ Ls,其公差值为Δ,则塑件平均尺寸为 Ls − ; 2
设塑料平均收缩率为Scp, 设塑料平均收缩率为Scp,塑件外形基本尺寸为 Scp
型腔基本尺寸为Lm,其制造公差为δz, 型腔基本尺寸为Lm,其制造公差为δz,则型腔平 Lm δz 均尺寸为Lm 均尺寸为Lm + δ z 。考虑平均收缩率及型腔磨损为
2011-11-4
10
第七章 成型零部件设计
为保证塑件精度须使上述各因素造成的误 差的总和小于塑件的公差值, 差的总和小于塑件的公差值,即 (7.2)
δz + δc + δs + δ j ≤ ∆
式中 δz——成型零部件制造误差; δz——成型零部件制造误差 成型零部件制造误差; δc——成型零部件的磨损量; δc——成型零部件的磨损量; 成型零部件的磨损量 δs——塑料的收缩率波动引起的塑件尺 δs——塑料的收缩率波动引起的塑件尺
1.平均值法 1.平均值法 按塑料收缩率、 按塑料收缩率、成型零件制造公差和磨损量均 为平均值时,制品获得的平均尺寸来计算。 为平均值时,制品获得的平均尺寸来计算。 平均收缩率法计算成型尺寸的思路及方法是: 平均收缩率法计算成型尺寸的思路及方法是:
2011-11-4 12
(7.3) )
第七章 成型零部件设计
寸变化值; 寸变化值; δj——由于配合间隙引起塑件尺寸误差 δj——由于配合间隙引起塑件尺寸误差; 由于配合间隙引起塑件尺寸误差; ∆——塑件的公差。 ——塑件的公差 塑件的公差。
2011-11-4 11
第七章 成型零部件设计
7.2.2 成型零部件工作尺寸的计算 根据式( ) 根据式(3.2)有: LM=LS+LSS
第七章 成型零部件设计
本章学习要求: 本章学习要求
2011-11-4
1
第七章 成型零部件设计
7.2 成型零部件的工作尺寸计算
成型零部件工作尺寸指成型零部件上直接决 定塑件形状的有关尺寸。主要包括型腔和型芯的 定塑件形状的有关尺寸。主要包括型腔和型芯的 径向尺寸(含长、宽尺寸 与高度尺寸 与高度尺寸, 径向尺寸 含长、宽尺寸)与高度尺寸,及中心距 含长 尺寸等 尺寸等。
2011-11-4
6
第七章 成型零部件设计
δ s = (S max − S min )Ls
式中 Smax——塑料的最大收缩率; Smax——塑料的最大收缩率; ——塑料的最大收缩率 Smin——塑料的最小收缩率; ——塑料的最小收缩率 Smin——塑料的最小收缩率; Ls——塑料的名义尺寸。 ——塑料的名义尺寸 Ls——塑料的名义尺寸。
标注制造偏差后则得
C m = [C s + C s S cp ] ±
δz
2
(7.13) 7.13)
21
2011-11-4