低毒脲醛树脂胶粘剂的合成
胶合板用低成本低毒脲醛树脂的研制
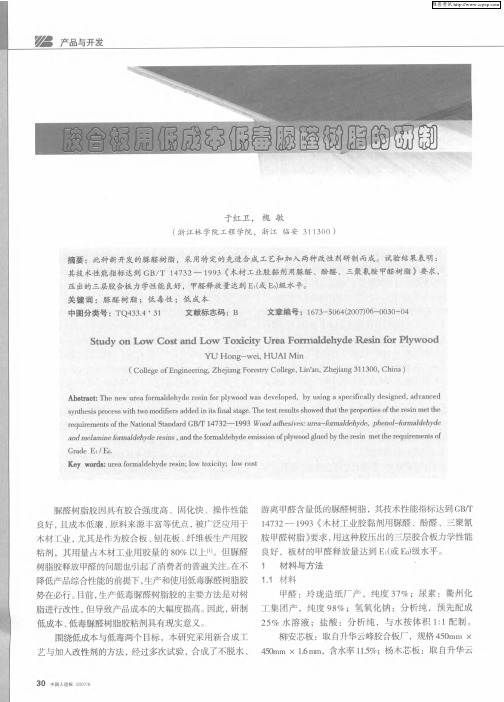
固体含量, % 5 0
4 3 . 2
4 2 . 5
4 1 . 4
3 9 . 6
储存期 / d
适用期 , h 游离甲醛
含量, %
≥6 0
≥4 0
.
≥6 0
≥4
0 . 2 4
≥6 0
≥4
0 . 1 8
≥6 0
≥4
乳白色 乳 白色
无杂质 无杂质
D H值 黏度 / s 7 . 2 2 3 7 . 3 2 l
无杂质
7 . 4 2 l
无杂质 无杂质
7 . 5 2 3 7 . 5 2 2
均匀液体 均匀液体 均匀液体 均匀液体 均匀液体
固体含量 , % 4 l
0 . 1 2
≥6 0
≥4
0 . 0 8
3 8
面粉 、淀粉作为多糖物质 ,在高温及催化剂的作用
从表 2可知 ,随着改性剂加入量的增加 ,固体含量
下可 以糊化 、部分醚化 ,形成烷 氧基 以及醛化淀粉 ,同 降低 ,游离 甲醛含量 明显减少 ,黏度也随着降低 ,但胶 时 由于形成 网状结 构分子 , 加上淀粉 自身有一定 的增稠 粘剂 的储存期与适用期都 比较长 ,可以满足胶合板生产 效果和粘接强度 ,可 以减少胶合板的透胶 ,提高预压性 要 求 。 . 2 改性剂 B 加入 墩对脲醛树脂性能的影响 能 ,达到较好 的胶合强度。氨水与 甲醛起化学 反应生成 3
4 2
4 2 . 5
4 4
4 5 . 6
p H 为酸 陛。 反应一定时间后加入第二批尿素 , 保温; 待反
应至终点 , 调p H为 7 . 0 左右 , 加入第三批尿素 , 使 甲醛与
低毒脲醛树脂的合成

低毒脲醛树脂的合成于红卫;傅深渊;槐敏;邵千钧;文桂峰;何礼平【期刊名称】《浙江农林大学学报》【年(卷),期】2002(019)002【摘要】采用了不同的改性剂与不同的合成工艺,研制用于胶合板制造的低毒脲醛树脂胶.结果表明:利用三聚氰胺和聚乙稀醇作为改性剂,结合特定的合成工艺,制得低毒脲醛(UF)树脂胶(游离甲醛含量≤3 g*kg-1),三层胶合板甲醛释放量为1.36mg*L-1.既讨论了影响树脂中游离甲醛含量的因素及制胶中出现的问题,又提出了解决的方法:树脂的摩尔比控制在1.3左右,聚乙烯醇和三聚氰胺的加入量分别为尿素总量的1.6%和2.5%;在加成反应阶段,树脂的pH值不应低于7.0;在缩聚反应阶段,温度控制在80~85 ℃,pH控制在4.0~4.2.表4参7【总页数】5页(P122-126)【作者】于红卫;傅深渊;槐敏;邵千钧;文桂峰;何礼平【作者单位】浙江林学院,工程学院,浙江,临安,311300;浙江林学院,工程学院,浙江,临安,311300;浙江林学院,工程学院,浙江,临安,311300;浙江林学院,工程学院,浙江,临安,311300;浙江林学院,工程学院,浙江,临安,311300;浙江林学院,工程学院,浙江,临安,311300【正文语种】中文【中图分类】TQ430.7+7【相关文献】1.低毒脲醛树脂胶的合成及胶液中游离甲醛的测定 [J], 开启余2.新型低毒耐水脲醛树脂胶的合成 [J], 开启余3.低温弱酸性三聚氰胺改性合成低毒耐水脲醛树脂的研究 [J], 何亚三;刘茜;陈燕仔;欧黎明4.低毒改性脲醛树脂合成工艺的研究 [J], 高翔; 张雄5.低毒改性脲醛树脂合成工艺的研究 [J], 高翔; 张雄因版权原因,仅展示原文概要,查看原文内容请购买。
脲醛树脂胶的生产配方流程

脲醛树脂胶的生产配方流程1.首先,将尿素和甲醛按一定比例加入水中搅拌溶解。
First, dissolve urea and formaldehyde in water in a certain proportion.2.然后加入碱液,并加热搅拌反应。
Then add alkali solution and heat and stir for reaction.3.在反应过程中控制温度和PH值。
Control the temperature and pH value during the reaction.4.待反应结束后,加入酸液进行中和。
After the reaction is completed, add acid to neutralize it.5.接着进行脲醛树脂的接枝改性。
Then proceed with graft modification of urea-formaldehyde resin.6.经过混合反应后,将脲醛树脂胶液进行脱泡处理。
After the mixed reaction, the urea-formaldehyde resin solution is treated to remove bubbles.7.然后采用真空脱泡,使树脂胶液中的气泡尽量减小。
Then use vacuum degassing to minimize air bubbles in the resin solution.8.将脲醛树脂胶液进行过滤以去除杂质。
Filter the urea-formaldehyde resin solution to remove impurities.9.继续加入稀释剂,调节树脂胶的粘度和固含量。
Continue to add diluent to adjust the viscosity and solid content of the resin.10.最后进行包装、贮存和运输。
脲醛胶生产工艺
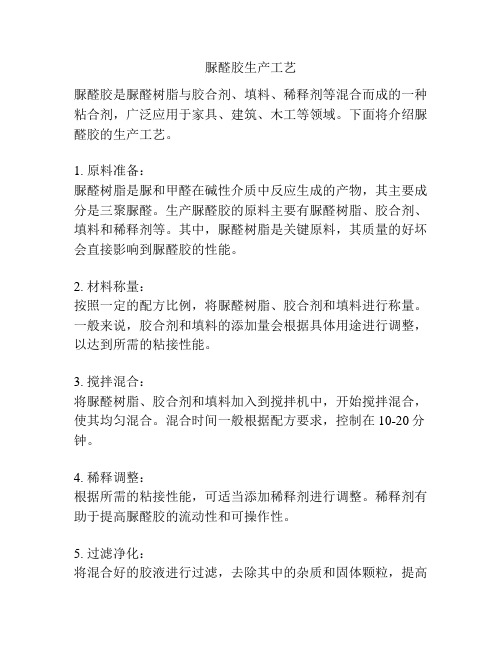
脲醛胶生产工艺脲醛胶是脲醛树脂与胶合剂、填料、稀释剂等混合而成的一种粘合剂,广泛应用于家具、建筑、木工等领域。
下面将介绍脲醛胶的生产工艺。
1. 原料准备:脲醛树脂是脲和甲醛在碱性介质中反应生成的产物,其主要成分是三聚脲醛。
生产脲醛胶的原料主要有脲醛树脂、胶合剂、填料和稀释剂等。
其中,脲醛树脂是关键原料,其质量的好坏会直接影响到脲醛胶的性能。
2. 材料称量:按照一定的配方比例,将脲醛树脂、胶合剂和填料进行称量。
一般来说,胶合剂和填料的添加量会根据具体用途进行调整,以达到所需的粘接性能。
3. 搅拌混合:将脲醛树脂、胶合剂和填料加入到搅拌机中,开始搅拌混合,使其均匀混合。
混合时间一般根据配方要求,控制在10-20分钟。
4. 稀释调整:根据所需的粘接性能,可适当添加稀释剂进行调整。
稀释剂有助于提高脲醛胶的流动性和可操作性。
5. 过滤净化:将混合好的胶液进行过滤,去除其中的杂质和固体颗粒,提高胶液的纯度。
6. 包装灌装:将过滤净化后的胶液进行包装灌装,以便于储存和销售。
包装时需要注意封口严实,以防胶液的挥发和污染。
7. 质量检验:对包装好的脲醛胶进行质量检验,检查其外观、黏度、凝胶时间等指标是否符合规定要求。
8. 成品库存:将合格的脲醛胶进行储存,标明生产日期和批次号,以便于追溯和管理。
以上是脲醛胶的生产工艺,通过科学合理的生产工艺,可以确保脲醛胶的质量和稳定性,满足不同行业对粘接剂的需求。
同时,对于环境保护和职业安全也需要加以关注,遵守相关的标准和规定,防止对环境和工人健康造成危害。
脲醛树脂胶粘剂制备原理
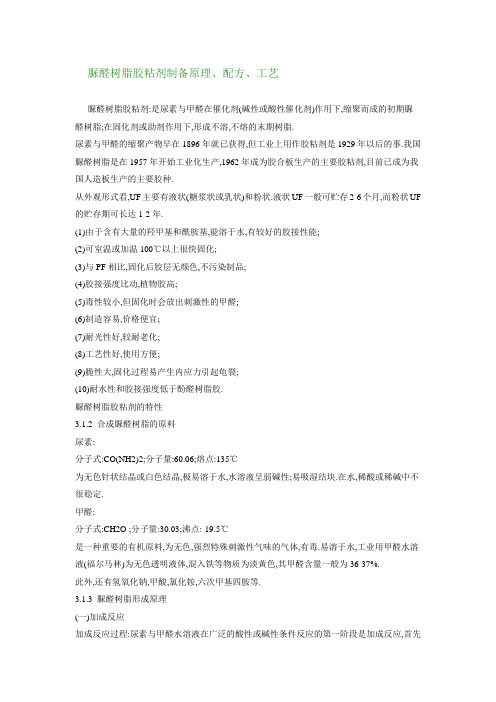
脲醛树脂胶粘剂制备原理、配方、工艺脲醛树脂胶粘剂:是尿素与甲醛在催化剂(碱性或酸性催化剂)作用下,缩聚而成的初期脲醛树脂;在固化剂或助剂作用下,形成不溶,不熔的末期树脂.尿素与甲醛的缩聚产物早在1896年就已获得,但工业上用作胶粘剂是1929年以后的事.我国脲醛树脂是在1957年开始工业化生产,1962年成为胶合板生产的主要胶粘剂,目前已成为我国人造板生产的主要胶种.从外观形式看,UF主要有液状(糖浆状或乳状)和粉状.液状UF一般可贮存2-6个月,而粉状UF 的贮存期可长达1-2年.(1)由于含有大量的羟甲基和酰胺基,能溶于水,有较好的胶接性能;(2)可室温或加温100℃以上很快固化;(3)与PF相比,固化后胶层无颜色,不污染制品;(4)胶接强度比动,植物胶高;(5)毒性较小,但固化时会放出刺激性的甲醛;(6)制造容易,价格便宜;(7)耐光性好,较耐老化;(8)工艺性好,使用方便;(9)脆性大,固化过程易产生内应力引起龟裂;(10)耐水性和胶接强度低于酚醛树脂胶.脲醛树脂胶粘剂的特性3.1.2 合成脲醛树脂的原料尿素:分子式:CO(NH2)2;分子量:60.06;熔点:135℃为无色针状结晶或白色结晶,极易溶于水,水溶液呈弱碱性;易吸湿结块.在水,稀酸或稀碱中不很稳定.甲醛:分子式:CH2O ;分子量:30.03;沸点:-19.5℃是一种重要的有机原料,为无色,强烈特殊刺激性气味的气体,有毒.易溶于水,工业用甲醛水溶液(福尔马林)为无色透明液体,混入铁等物质为淡黄色,其甲醛含量一般为36-37%.此外,还有氢氧化钠,甲酸,氯化铵,六次甲基四胺等.3.1.3 脲醛树脂形成原理(一)加成反应加成反应过程:尿素与甲醛水溶液在广泛的酸性或碱性条件反应的第一阶段是加成反应,首先生成一羟甲脲.一羟甲脲的生成:NH2CONH2 + CH2O NH2CONHCH2OH (3-1)二羟甲脲的生成:NH2CONHCH2OH + CH2O HOCH2NHCONHCH2OH(3-2)上述反应若尿素与甲醛为等摩尔比且在中性条件下进行,最终达到尿素,甲醛,一羟甲脲和二羟甲脲四个组分的平衡.但若尿素与甲醛的摩尔比大于1:1时,上述平衡组成就会发生变化,尤其是摩尔比大于1:2时,二羟甲脲进一步与甲醛加成生成三羟甲脲:HOCH2NHCONHCH2OH + CH2OHOCH2NHCON(CH2OH)2 (3-3)反应(3-1)和(3-2)可同时被酸(H+)和碱(OH-)所催化,但碱的催化效应较大.正反应和逆反应都能被催化到大致相同的程度,所以PH值的变化,平衡常数改变不大,但在实际的脲醛树脂的合成中,由于反应中间都在酸性条件下进行的,羟甲脲参加缩聚反应或生成不溶于水的次甲脲沉淀,这样平衡常常不能达到.加成反应机理:在酸性和碱性条件下,其加成反应可通过不同的反应机理进行,其反应历程和产物也有所不同.碱性条件下,加成反应生成较为稳定的初期产物羟甲脲.NH2CONH2 + OH-→NH2CONH- + H2ONH2CONH- + H2C+=O-→NH2CONHCH2O-NH2CONHCH2O- + H2O→NH2CONHCH2OH + OH-从反应动力学的角度来看,生成一羟甲脲,二羟甲脲和三羟甲脲的速度比为9:3:1,即其反应能力随引入羟甲基而依次降低.因此,生成一羟甲脲和二羟甲脲是决定脲醛树脂理化性能有意义的产物.酸性条件下,是甲醛受氢离子的作用,首先生成带正电荷的次甲醇:_CH2O + H2O HO—CH2—OHHO—CH2—OH + H+ +CH2OH +H2O带正电荷的次甲醇与尿素反应,生成不稳定的羟甲脲,它进而缩聚脱水,生成次甲基键连接的低分子缩聚物或次甲脲:NH2CONH2 + C+H2OH→NH2CON+H2CH2OHNH2CON+H2CH2OH→NH2CONHCH2OH + H+→NH2CONHC+H2 + H2ONH2CONHC+H2 + NH2CONH2→NH2CONHCH2N+H2CONH2→NH2CONHCH2NHCONH2 + H+ 或者NH2CONH2 + 2CH2O CH2NCONCH2 + 2H2OPH1%时就显示出影响了;含量越高,树脂在贮存期间的羟甲基含量下降越明显,贮存稳定性越差.不应超过0.8%.游离氨:能提高缩聚反应初期阶段及补加尿素再缩聚阶段的介质PH值;但当含量高于0.015%时,树脂的固化时间延长和贮存稳定性降低.不应超过0.015%.(四)反应温度和反应时间在反应体系中,反应温度和反应时间既有单独作用又有联合其它因素共同作用.反应温度:对反应速度,游离甲醛含量胶树脂贮存稳定性等的影响较为明显;过高(酸性介质),出现凝胶,易形成次甲脲沉淀;过低,反应时间过长,树脂聚合度低,粘度低等.应视各反应阶段的具体条件而定,酸性加成阶段,应为40-60℃,碱性加成阶段,应为80-95℃适宜.反应时间:关系到树脂的聚合度,游离甲醛含量,粘度及树脂的力学性能等;过短,反应不完全,固体含量低,粘度小,游离甲醛含量高,树脂机械强度低;过长,聚合度过高,粘度过高,树脂水混和性下降,贮存期短.应考虑反应时间与其它条件的共同作用.3.1.5 脲醛树脂的合成(一)原料计算所需尿素量为已知,按下式计算其它原料量:式中: ——所计算的原料量(Kg)——所计算原料的分子量——所计算原料的摩尔数——尿素纯度(%)——尿素量(Kg)——所计算原料的浓度(%)60.06——尿素分子量(二)胶接用脲醛树脂合成合成实例:甲酸:水1: 2甲醛水溶液1000尿素(1) 377.6尿素(2) 66.6尿素(3) 59.2六次甲基四胺 3.9聚乙烯醇11氢氧化钠适量甲酸适量(2)合成工艺甲醛水加入反应釜后加六次甲基四胺.用氢氧化钠调PH=7.8-8.2,加热升温并加入尿素(1)和聚乙烯醇(提高UF的耐老化性能,增加初粘性),在30-50min内升到88-92℃,并保温30min.用甲酸调PH=5.2-5.4,在温度88-92℃下保温30min.用甲酸调PH=4.7-4.9,反应20min后不断测定粘度,当粘度达到19-21s(涂-4杯,30℃).加尿素(2)并用氢氧化钠调PH=4.9-5.1,在温度为85-87℃下反应到粘度为25.5-28.5s.用氢氧化钠调PH=7.5-8.0,并冷却到温度为80℃,加尿素(3),在65℃下保持30min.冷却并调PH=7.0-7.6,在35℃下放料.(3)树脂质量指标包括外观,密度,固体含量,粘度,PH值,游离甲醛,固化时间,粘度变化率,贮存期,水混合性等.这些指标的测定按照标准(GB/T 14074.1-93——14074.18-93)进行测定.(4)应用:胶合板生产等.(三)浸渍用脲醛树脂合成合成实例:(1)合成工艺:用氢氧化钠调甲醛水溶液(155份)PH值为8.5-9.0,加尿素(占总尿素100份的57.5%).加热到55-60 ℃,停止加热,反应液自升到78-82 ℃,在此温度保持10-15min.用醋酸(醋酸:水=1:1)调PH值为4.5-4.6,在90-95 ℃保温20-30min.用氢氧化钠调PH值为8.7-9.2,同时降温到70-75 ℃,加余下的全部尿素.在60-65 ℃下保温35-40min.冷却到20-25 ℃,树脂液用120-200目/cm2筛网过滤.(2)树脂质量指标:固体含量,粘度,比重,PH值,游离甲醛,固化时间,渗透能力等.(3)应用:该树脂渗透能力强,用于浸渍纸,制造胶膜纸;也可作脲醛树脂与聚酯树脂的混合浸渍液的主要成份.3.1.6 脲醛树脂的调制脲醛树脂在加热加压条件下,虽然自身也能固化,但时间很长,固化后的产物,由于交联度低,固化不完全,胶接质量差.因此,在实际使用时都要加入固化剂(亦称促进剂,有时也有例外,如木材酸性较强时,可以不加)使UF迅速固化,保证胶接质量;其次,为了改变UF的某些性能(如增加初粘性,提高耐水性及耐老化性,降低游离醛等),还需加入某种助剂.以上过程称为UF的调制(简称为调胶).一般来说,UF的调制需要根据用途和需要进行.(一)固化剂UF的固化剂有酸和酸性盐两类.酸类固化剂有草酸,磷酸,苯磺酸,酒石酸,柠檬酸,无水苯甲酸等;酸性盐类有氯化铵,氧化锌,硫酸铁胺,盐酸苯胺等.不宜采用强酸固化剂,但强酸性盐(尤其是强酸铵盐,如氯化铵,硫酸铵)可行.以上这些固化剂的性质不同,效果不一,使用时应根据UF的理化性能,气温条件及胶接制品的要求等酌情应用.(1)单组分固化剂:如氯化铵,硫酸铵.使用最广的是氯化铵,其加入量一般为UF树脂量(固体含量)的0.2-2%.我们常加入1%的氯化铵(固体计),且有时还要将氯化铵调成水溶液(如20%). (2)多组分固化剂:如氯化铵与尿素,氯化铵与氨水,或氯化铵与六亚甲基四胺及尿素3组分混合物等.目的有两:一是为了延长树脂的适用时间,特别是夏季,由于室温较高,单独使用氯化铵(或硫酸铵)时,树脂的适用期往往不能满足要求;二是在冬季,采用常温固化方式时,为加速树脂固化,常使用氯化铵与浓盐酸合用,可使固化时间大大缩短.(3)潜伏性固化剂:是指在常态下呈化学惰性,在某种特定温度下起作用的固化剂.如酒石酸,草酸,有机酸盐等,但效果不太理想,国内目前正开始研究使用.(4)微胶囊固化剂:就是在固化剂的表面有一层保护膜——胶囊,在低温下由于表层胶囊的隔离,不起固化作用;而在高温或受压下,表层胶囊被破坏,胶囊内的固化剂即与UF接触,使之固化.目前国内还没有这种固化剂.注意:氯化铵对冷固化的UF来说,并不是很好的固化剂.这是因为铵盐在UF中释放酸速度与气温有关.且冬季施加氯化铵的量应比夏季多.还应注意的一点是:由于UF的固化过程中,主要变化有化学反应和水分和移动,此时还应考虑木材含水率,固化剂的性质,气温高低,空气湿度和风力大小等因素.固化剂的选择原则:(1)根据不同的用途要求和气候条件进行适当的选择.如胶合板用氯化铵固化剂,冬天一般加入量0.4-0.8%,春秋天加0.3-0.5%,夏天加0.2-0.3%,还要加一些延缓剂(如氨水,尿素等),因为温度愈高,湿度愈低,固化愈快,适用期愈短.(2)选择的固化剂,固化后的胶层PH值不宜过低或过高,一般胶层的PH值在4-5之间,其胶合性能最理想.PH值过低,胶层易老化,过高会造成固化不完全.(3)根据胶接制品的工艺要求选择.如较厚的刨花板生产,要求表层刨花中的胶固化时间要长,中(芯)层刨花中的胶固化时间要短,为了使表芯层胶液同时固化,就得在固化剂上做些文章.如表层刨花用胶的固化剂由氯化铵25份,氨水35份和水45份组成,加入量为树脂质量的5-6%,其固化时间为110-130s;芯层刨花用胶的固化剂为20%的氯化铵溶液,加入量为5-6%,其固化时间为35-45s,这样可使表芯层胶液达到同时固化.(二)助剂UF常用的助剂有填充剂,发泡剂,甲醛结合剂,防老化剂,耐水剂,增粘剂等.下面重点讲讲填充剂.(1)填充剂作用:降低成本,提高UF初粘性,减少UF渗透量,延长适用期,降低内应力,减少UF体积收缩率,提高耐老化性,降低游离甲醛含量等.要求:化学性质上应是不活泼的中性或近于中性的物质;能与水充分混合,水分蒸发后能转变为固体的物质;能与树脂混合,不产生分层沉淀;无副作用或副作用低(如保持胶的粘度,对固化时间,耐水性能,胶接强度及耐久性影响应尽可能小);原料易得,价格低廉,易加工成粉末(细度要求在100目以上).种类:淀粉类(常用的有面粉,淀粉,高梁粉,木薯粉等);蛋白质类(常用的有豆粉和血粉);纤维素类(常用的有树皮粉,花生壳粉,木粉,水解玉米芯粉等);矿石粉类(石英粉,白垩土粉,高岭土粉等) 用量:视UF的质量和人造板要求而定,一般来说,施加量在5-20%以内为宜.(2)其它助剂发泡剂:如血粉,拉开粉(烷基磺酸钠),用量0.5-1.0%(质量).甲醛结合剂:如尿素,三聚氰胺,含单宁的树皮粉,豆粉,面粉,聚乙酸乙烯乳液等,用量5-15%.防老化剂:如1-5%(用量)的聚乙烯醇或15-20%(用量)的聚乙酸乙烯酯乳液.耐水剂:苯酚,间苯二酚,三聚氰胺,硫脲等.三聚氰胺生产防水,防潮UF胶.增粘剂:聚乙烯醇,面粉,豆粉等,增加初粘性.(三)UF的调胶工艺主要根据人造板及木制品的工艺要求而定.如普通胶合板用胶调胶工艺:注:混合固化剂配方为:氯化铵25,尿素30,六亚甲基四胺45,水50(质量)3.1.7 脲醛树脂的改性(一)降低胶接制品释放的甲醛量胶接制品所释放的甲醛来源:(1)UF树脂中的游离甲醛;(2)树脂固化中分解的甲醛;(3)木材等被胶接材料所释放的甲醛.降低甲醛含量的途径:(1)从树脂合成配方入手:采用低摩尔比U/F;加入能与尿素,甲醛共聚的苯酚或三聚氰胺,双氰胺等;尿素分次加入;改变反应PH值等反应条件.(2)从调胶入手:加入甲醛结合剂(捕捉剂),如尿素,三聚氰胺,含单宁的树皮粉,豆粉,面粉,聚乙酸乙烯乳液等.(3)从制品后续处理入手:如封边,贴面;氨气处理等.(二)改善脲醛树脂的耐水性在UF中加入三聚氰胺或间苯二酚,可提高其耐水性能,并在较小程度上提高耐沸水性能;UF与PF或三聚氰胺树脂或聚醋酸乙烯酯乳液等混合,也可改善其耐水性.(三)改善脲醛树脂的胶接强度和耐久性从用UF胶合某些非木质材料如麦秆,棉秆,稻草等来说,有必要改善其胶接强度,可加入苯酚,间苯二酚,三聚氰胺等,可对UF起增强作用.对于改善UF的耐久性来说,可加入增塑剂(如橡胶乳),聚醋酸乙烯乳液,柠檬酸,填充剂等.。
低毒脲醛树脂胶粘剂的合成

有学 者研 究认 为 , 酸(H<3条 件 下 甲醛 与尿 强 p )
表 1 强酸下 ,/ u i . 对生成物中 盯 含■的影响 v l
释放 量 , 既要 降低 U R F A中 含 量 , 又要台 成 出在 使 用 条件 下不 易 分解 出 甲醛 结 构 的 胶粘 剂 , 有 可 能 才
从 根本 上解 决 u R F A胶接 制 品的 甲醛 释放 问题
2 结 果 与讨 论
21 强酸性 下 n/ 对生成 物 含 量的影 响 . F
质材 料时 , 些游 离 的 甲醛 从 被胶 合 的 材 料 内部 释 研 究 . 这
放 出来 , 染环 境 , 害人 类 健康 . 污 损 降低 U R 中 F FA F
含量 , 一个 重要而 紧迫 的任务 . 是
1 材料 与方 法
甲醛 : 分析 纯 , ( 甲醛 ) 70 ; 素 : 析 纯 , =3 .% 尿 分 ( 素)=9 .% .其 他 催 化 剂 和分 析 用 药 品 均 为 尿 99
采用单 因素 分 析 的 方 法 安 排 试 验 , 料 采 用 1 投
长期 以来 , 者们 对 降低 u 学
了大量 的研 究 -
中F F含 量 进 行
. 采用 的方 法 是 减 少 合 成过 程 中
甲醛 用量 、 甲醛 多次尿 素 和改 性 等 .这 些传 统方 分析纯 试剂 . 1次 法成 功地 降低 了 U R F A中游离 甲醛含 量 . F A胶 接 UR 这 制 品 中 散 发 的 甲醛 还 有 另 外 一 个 来 源 , 是 U R 次甲醛 3次 尿 素 的方 法 , 3次 投 料 是 在 每 次 投 料 就 FA
- 1、下载文档前请自行甄别文档内容的完整性,平台不提供额外的编辑、内容补充、找答案等附加服务。
- 2、"仅部分预览"的文档,不可在线预览部分如存在完整性等问题,可反馈申请退款(可完整预览的文档不适用该条件!)。
- 3、如文档侵犯您的权益,请联系客服反馈,我们会尽快为您处理(人工客服工作时间:9:00-18:30)。
低毒脲醛树脂胶粘剂的合成
摘要:本研究在脲醛树脂合成的过程中加入改性剂M和N,能极大地改善脲醛树脂的预压性和胶合强度。
通过正交实验优化改性剂的加入量,在保证成本低的前提下,改性剂M和N的加入量为0.68%和0.78% .合成的脲醛树脂中游离甲醛含量低于0.18%,压制胶合板胶合强度满足国家Ⅰ类标准,同时甲醛释放量达到E1级要求。
Abstract: Modifier M and N are added during UF resin synthesis in this study. They can reprove prepress and bonding strength of UF resin. Adding amount of modifier is by orthogonal matrix experiment. Adding amount of modifier is 0.7% and 0.8% respectively. Free-formaldehyde content is below 0.15% in UF resin made by in the experiment and bonding strength of plywood pressed by it can meet nation standard of Ⅰgrade. In the same time formaldehyde emission reach requirement of E1 grade.
关键词:脲醛树脂改性剂游离甲醛胶合强度甲醛释放量
keywords: UF resin modifier agent free-formaldehyde
bonding strength formaldehyde emission
前言
脲醛树脂胶粘剂是由尿素与甲醛在催化剂作用下合成的热固性树脂。
其原料来源丰富,合成工艺简单,胶合强度好,操作性能良好且成本低等优点而被广泛地应用于世界各国木材行业。
但是也有其严重缺点如耐水性差、贮存期短和甲醛释放,随着人们环保意识的提高,甲醛释放问题将限制脲醛树脂的应用。
本研究在利用改性剂来降低脲醛树脂中游离甲醛含量及木制品甲醛释放量,同时改善脲醛树脂压制胶合板预压性问题,并保证胶合制品的胶合强度,使其能满足实际生产的需要。
1 实验部分
1.1 实验原料
尿素、甲醛、三聚氰胺、六次甲基四胺、改性剂M和N、甲酸、NaOH
1.2 树脂合成及检测仪器
三口烧瓶(1000ml)恒温水浴锅、电动搅拌器、温度计、电子称、PHs-3C酸度计、涂-4杯、秒表、烘箱、分析天平(0.1mg)、万能力学实验机、分光光度计,干燥器、热压机等。
1.3 树脂合成合成工艺
脲醛树脂合成采用碱-酸-碱工艺,尿素分三次加入,三聚氰胺分两次加入。
将一定量的甲醛和六次甲基四胺加入三口烧瓶中,用NaOH调pH为7.5~8.0。
加热升温至40℃时加入第一批尿素和50%的三聚氰胺,继续升温至88~90℃,保温30min,用甲酸调pH值为6.5~6.7时加入改性剂M,调pH值为5.1~5.3,半个小时后不断测粘度,直至达到14~16s/30℃,加NaOH调pH6.2~6.3,在温度90℃左右加入三聚氰胺,保持10min 调pH值5.8,加入第二批尿素,升温至88,继续缩聚直至粘度到19~21s/30℃,加碱调pH 值7.5~8.0。
降温至60℃时加入第三批尿素,在此温度下保温30min,调pH值7.0 加入第四批尿素,冷却到50℃加入改性剂N,保温30~60min,调pH值7.5~8.0,降温至40℃出料。
1.4正交实验与胶合制品性能检测结果
1.4.1正交实验设计
由于此实验探讨改性剂的加入量对树脂及胶合制品性能的影响,所以采用正交实验。
正交实验以甲醛与尿素的摩尔比、改性剂M和N加入量为考察因素,以胶合强度和甲醛释放量为考察指标。
进行3因素、3水平L9(33)正交实验因素位级见表1。
表1 正交实验因素与水平
Table1 factors and levels of orthogonal matrix experiment
1.4压制胶合板实验
1.4.1实验材料
脲醛树脂(实验室自制)
杨木单板:本次实验所用的单板为杨木单板,单板名义厚度1.8~2.2mm,
幅面尺寸300m m×300mm,含水率8%~12%。
1.4.2 调胶
在脲醛树脂中依次加入一定比例的面粉、三聚氰胺和自配复合固化剂,搅拌均匀后即可使用。
1.4.3压板工艺参数确定
热压温度:105℃~110℃;热压时间:1~1.2min/mm单板;热压单位压力:1.0MPa
预压单位压力:1.0MPa;单板涂胶量:280~320g/m2
1.4.4胶合板湿胶合强度和甲醛释放量检测
胶合板湿强度的试件锯制及检测根据国家标准GB9846.12-88来进行。
甲醛释放量检测
干燥器法(1L):参照国家标准GB/T17657-2001进行检测。
2 结果与讨论
2.1 正交实验结果
正交实验设计表及胶合板湿胶合强度和甲醛释放量性能指标检测结果如表2所示。
湿胶合强度和甲醛释放量方差显著性分析如表35和4所示。
表2 正交实验及胶合强度和甲醛释放量检测结果
Table2 orthogonal matrix experiment and test results of bonding strength and
formaldehyde emission
0.2
0.4
0.6
0.8
1
1.2
a1
a2
a3
b1
b2
b3
c1
c2
c3
胶合强度(M P a )
2.2 分析讨论
考虑正交实验各因素对湿胶合强度的影响,从正交实验表2的各因素极差值可知,影响湿胶合强度因素的主次依次是:改性剂N →甲醛与尿素的摩尔比→改性剂M ;湿胶合强度指标值越大越好,因素的最佳组合为a 1b 2c 3。
各因素对甲醛释放量的影响,从正交实验表3-4的各因素极差值可知,影响甲醛释放量因素的主次依次是:改性剂N →甲醛与尿素的摩尔比→改性剂M ;甲醛释放量指标值越小越好,因素的最佳组合为a 3b 2c 1。
2.2.1甲醛与尿素的摩尔比对胶合板湿胶合强度、甲醛释放量的影响 从表3和4方差显著性分析看,甲醛与尿素的摩尔比对湿胶合强度性能影响显著,而对甲醛释放量不显著,这是由于摩尔比变化幅度小。
由图1和2可知,随着甲醛与尿素摩尔比的降低,胶合板的湿强度下降,而甲醛释放量也呈现下降趋势,这是由于。
综合考虑来说,在胶合制品强度满足国家标准时,制品甲醛释放量越低越好。
所以甲醛与尿素的摩尔比选择1.03:1。
2.2..2 改性剂M 的加入量对胶合板湿胶合强度、甲醛释放量的影响 从表3和4方差显著性分析看,改性剂M 对湿胶合强度和甲醛释放量的影响都不显著。
由图1和2可知,随着改性剂M 的加入量增加,胶合板的湿强度先增加,到0.7%时强度呈现最大值,之后强度下降;而甲醛释放量则是呈现先下降后上升趋势,在改性剂M 的加入量为0.7%时甲醛释放量值达到最低。
所以,综合湿胶合强度和甲醛释放量这两个指标来选择改性剂M 的加入量为甲醛量的0.7%。
2.2.3 改性剂N 的加入量对胶合板湿胶合强度、甲醛释放量的影响
从表3和4方差显著性分析看,改性剂N 对湿胶合强度和甲醛释放量的影响都显著。
由图1和2可知,随着改性剂N 的加入量增加,湿胶合强度和甲醛释放量都逐渐增加。
考虑到湿胶合强度和甲醛释放量满足国家标准,同时不使生产成本大幅度增加的情况下。
改性剂N 的加入量选择为甲醛量的0.8%。
3.结论
0.10.20.30.4
0.5
0.60.7a1a2a3b1b2b3c1c2
c3
甲醛释放量(m g /L )
1)甲醛与尿素的摩尔比对胶合板湿胶合强度影响显著,对甲醛释放量有一定的影响。
随着甲醛与尿素摩尔比的降低,湿胶合强度和甲醛释放量都下降。
2)改性剂M对胶合板湿胶合强度和甲醛释放量都有一定的影响。
随着改性剂M加入量的增加,湿胶合强度先增加后下降,而甲醛释放量则是先下降后上升趋势。
3)改性剂N对胶合板湿胶合强度和甲醛释放量的影响都显著。
随着改性剂N加入量的增加,湿胶合强度和甲醛释放量都呈现增加趋势。