DCS控制系统在化工生产中的应用分析
DCS系统在化工工艺中的应用

DCS系统在化工工艺中的应用DCS系统(分散控制系统,Distributed Control System)是一种以计算机为核心,采用分布式控制、多机联网的工业自动化控制系统。
它广泛应用于化工工艺中,以提高生产效率、降低成本、提升产品质量。
本文将重点探讨DCS系统在化工工艺中的应用。
一、DCS系统在生产过程中的优势DCS系统在化工工艺中的应用有许多优势。
首先,DCS系统能够实现对整个生产过程进行集中控制和监控。
通过集中控制,可以实现对各个控制环节的协调配合,提高生产效率。
其次,DCS系统具有较高的可扩展性,可以根据实际生产需求进行扩展和升级。
这样一来,不仅能够适应不断变化的生产需求,还能够降低系统更新的成本。
此外,DCS系统还可以实现远程监控和远程操作,无论何时何地,都能够对生产过程进行实时监控和及时干预,提高工作效率和安全性。
二、DCS系统在化工工艺中的具体应用1. 温度控制在化工生产中,温度是一个重要的参数。
DCS系统可以通过传感器实时采集温度数据,并将数据传输到控制中心进行分析和处理。
通过设定合理的温度控制策略,DCS系统可以实现对温度的准确控制,保证化工过程的稳定性和产品质量。
2. 压力控制化工工艺中,压力是另一个关键指标。
DCS系统可以通过连接压力传感器,实时监测压力变化,并将数据传输到控制中心进行处理。
运用DCS系统,可根据设定的控制算法,实现对压力的精确控制,确保系统的稳定运行。
3. 流量控制在化工过程中,液体或气体的流量也是非常重要的一个参数。
DCS 系统能够通过流量传感器实时监测流量变化,并通过相应的控制策略对流量进行调节。
合理的流量控制有助于提高工艺效率和产品质量。
4. 浓度控制化学反应中,溶液的浓度是一个重要的控制参数。
DCS系统可以通过浓度传感器实时监测溶液浓度的变化,并根据设定的控制算法对浓度进行调节。
通过精确控制浓度,可以提高产品的一致性和合格率。
5. 安全监测化工工艺存在着一定的安全风险,如温度、压力超限等。
化工生产中DCS控制系统的运用分析

化工生产中DCS控制系统的运用分析作者:崔玉洪来源:《科技创新导报》 2013年第15期崔玉洪(青海省格尔木市青海盐湖海虹化工股份有限公司 816000)摘?要:从20世纪80年代以后,普通的仪表逐步被DCS控制系统代替,变成了当今化工生产中重要的控制系统,特别是现在网络和计算机技术的不断发展,使得DCS控制系统在性能和功能方面都有了非常大的提升。
该文主要对化工生产中DCS控制系统的运用情况进行探讨分析。
关键词:化工生产 DCS控制系统运用分析中图分类号:TQ056;TP273 文献标识码:A 文章编号:1674-098X(2013)05(c)-0117-01 1 DCS控制系统功能简介1.1 对系统状况进行实时显示在控制系统中,建立O/I的系统服务,收集现场控制点的数据,在操作员站上显示出单回路控制画面、流程画面、声音、数据等方面的变化,从而更好的体现出系统的整体运行概况。
1.2 对相关作业参数进行调整操作员根据操作员站上显示的各种数据,迅速的对生产过程中的各种运行参数做出调整,比如液位参数、流量、温度、压力等方面的参数。
1.3 对运行故障进行报警DCS控制系统通过创建自动报警功能,可以对系统的状态、硬件设备状态、开关量、模拟量等方面的信息进行实时的监控,可以根据不同的报警点、报警时间、报警显示状况等方面的内容来判断出系统出现故障的位置。
例如当搅拌电动机运转异常的时候,操作界面的屏幕就会从绿色逐步变成红色,且伴随有声音提示和灯光的闪烁,以便告知操作员迅速的对系统运行问题进行解决。
1.4 对运行状态进行监督DCS控制系统还具有分析处理报警信息、查看历史参数、阅览操作记录等方面的功能。
可以对操作员的误操作和实际操作情况进行监督。
当出现事故的时候,可以使用分析历史数据和实时数据的方法,来找出故障的原因,从而及时的采取相关措施,杜绝相关故障再次出现,降低损失。
2 在化工生产中使用DCS控制系统2.1 控制反应器的反应温度的应用在整个化工生产过程中,反应器控制是最重要的一个部分,它的生产控制水平的高低对生产安全和产品质量有非常大的影响。
DCS控制系统在化工生产和消防应急处理系统中的应用

DCS控制系统在化工生产和消防应急处理系统中的应用近年来,计算机技术发展迅速,DCS控制系统实现了更新换代,在包括化工企业在内的产业经济发展中发挥了积极作用。
在化工产业中,DCS系统的应用可以减少化工企业成本、增加产品收益、扩大生产规模,化工企业通过采用DCS控制系统可以优化产品设备功能,实现化工生产的智能化和便捷化。
另外,在化工生产中,DCS控制系统的应用,通过自动化功能启动消防系统,能够帮助化工企业更高效地做好消防应急处理工作,提高化工企业消防安全和火灾事故扑救能力,快速控制火情,争取消防救援时间,避免火灾事故扩大,有力地保障了化工企业生产安全。
1 DCS控制系统概述DCS,即集散控制系统,亦称“分散控制系统”或“分布式计算机控制系统”,是一种功能十分强大的计算机网络集成技术,它依据控制分散、操作和管理集中的基本设计理念,主要由控制体系、运行体系、计划体系、管理体系几部分构成,有着集中管理和分散控制的典型特征,具备监督功能、参数调整功能、实时性功能和预警调整功能。
可靠性是DCS系统得以高质量发展和广泛应用的重要保障,提高DCS系统可靠性,应采用可靠性更高的硬件设备和生产工艺,同时在软件设计上采用冗余技术,并实现系统的容错技术、故障自诊断、自动处理技术。
DCS控制系统应用范围广,可以广泛应用于生产现场、工作车间以及生产设施和服务器等方面。
目前,DCS系统呈现出以下发展趋势:第一,系统功能向开放式方向发展,赋予用户更大的系统集成自主权,系统之间实现了高度兼容,达到最佳的系统集成;第二,仪表技术向数字化、智能化、网络化方向发展,过程控制的功能实现了真正意义上的“全数字”、“全分散”控制,整个系统的安装、使用和维护工作更加方便快捷;第三,工控软件正向先进控制方向发展。
广泛应用各种先进控制与优化技术,确保DCS系统更加高效、直接,向标准化、网络化、智能化和开放性方向发展。
1.1 可控网络可控网络结构主要分为三层,其中:上层是综合信息处理并做出控制反应;中层主要监控化工生产和操作,并基于上层操作处理信息数据,以实现有效监控的目的;下层包括收集信息、调节闭环、执行程序,主要用于控制生产对象、收集数据信息,下层所采集的数据信息将会及时报告到上层[1]。
DCS控制系统在化工企业中的应用

DCS控制系统在化工企业中的应用DCS(Distributed Control System)控制系统是一种分布式控制系统,它由许多控制器、传感器和执行器等组成,并通过高速数据传输网络连接在一起,形成一个分层的、功能模块化的实时控制系统。
DCS控制系统在制造业中广泛应用,而在化工企业中尤为重要。
本文将介绍DCS控制系统在化工企业中的应用。
DCS控制系统及其优势DCS控制系统是基于计算机的物理过程控制系统,它具有许多优势,包括:•可靠性高。
DCS的硬件、软件、通讯等部件都经过严格的测试和设计,保证其稳定性和可靠性。
•灵活性好。
DCS控制系统的核心是计算机,可以对系统进行灵活的配置和调整。
•具有强大的数据管理和处理能力。
DCS可以记录系统数据和运行状态,并为后期的优化和维护提供支持。
•可以与其他系统无缝连接,实现信息共享和协同作业。
例如,它可以与ERP系统相连接,实现工厂信息的实时更新和数据共享。
总之,DCS控制系统可以通过提高生产效率、降低生产成本、提高产品质量、降低能源消耗等方面的改进,将企业的生产水平提高到新的高度。
化工企业中的DCS系统应用在化工企业的生产中,DCS控制系统的应用是不可或缺的。
本节将介绍化工企业中DCS控制系统的具体应用。
原料配制对于液体、固体和气体等不同状态的原材料进行混合和配制,是化工企业生产过程的基础。
在化工生产中,通常会有多个原材料生成一个混合物,此时,控制系统需要根据所使用的原材料、混合体的比例以及不同原材料在加入混合器后,所产生的影响进行控制。
DCS系统可以对每个组分的流量、温度等进行精确控制,并通过实时数据记录来监测混合物的配制精度和效率。
温度控制化工产品通常需要在一定的温度条件下完成反应或产生化学反应,DCS控制系统可以根据工艺要求自动控制反应器的温度,也可以调节供热和供冷等方式来控制温度,从而确保反应的有效性和生产的效率。
压力控制在化工生产中,通常会使用高压或低压来进行反应生产。
DCS系统在化工工艺控制中的应用

DCS系统在化工工艺控制中的应用化工工艺控制是指通过对化工生产过程中的温度、压力、液位、流量等参数进行监测和控制,以确保生产过程的安全性、稳定性和高效性。
而随着信息技术的发展,分散控制系统(DCS)在化工工艺控制中扮演着至关重要的角色。
本文将介绍DCS系统在化工工艺控制中的应用,探讨其在提升生产效率、确保产品质量和实现智能化管理方面的优势。
一、DCS系统概述DCS系统是一种将生产控制技术与计算机技术相结合的集散式过程控制系统。
它由多个分布在工厂不同区域的控制器和各种感知设备、执行器组成,通过通信网络进行数据交换和控制指令传递。
DCS系统具有开放性、灵活性和可靠性强的特点,适用于各类化工工艺过程的控制。
二、DCS系统在化工工艺中的应用1. 生产过程监测与控制DCS系统通过对温度、压力、液位、流量等参数进行实时监测和控制,可以及时发现和解决生产过程中的异常情况,确保生产过程的安全性和稳定性。
同时,DCS系统还能够自动调整和控制参数,提高生产过程的效率和精度。
2. 质量控制与优化DCS系统可以对关键工艺参数进行精确控制,提高产品的质量一致性和稳定性。
通过实时监测和控制,可以及时调整工艺参数,减少工艺变异,提高产品品质。
此外,DCS系统还可以通过数据分析和优化算法,实现工艺参数的优化和调整,进一步提高产品质量。
3. 故障诊断与维护DCS系统具有自动故障诊断功能,可以对生产设备和系统进行实时监测和分析,及时发现设备故障和异常状态。
通过故障诊断,可以快速定位故障原因,并采取相应的维修措施,减少停机时间,提高生产效率。
4. 能耗管理与优化DCS系统可以对能源消耗进行全面监测和控制,实现能源的合理配置和利用。
通过对能源数据的收集和分析,可以识别能耗高峰和能耗异常,采取相应的控制措施进行优化调整,降低能源消耗,提高能源利用效率。
5. 智能化管理与远程监控DCS系统支持远程监控和管理,可以实现对生产过程的远程控制和监测。
DCS系统在石油化工中的应用
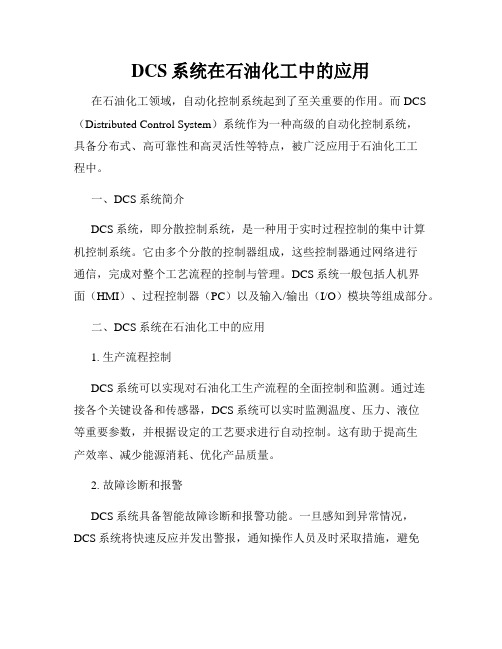
DCS系统在石油化工中的应用在石油化工领域,自动化控制系统起到了至关重要的作用。
而DCS (Distributed Control System)系统作为一种高级的自动化控制系统,具备分布式、高可靠性和高灵活性等特点,被广泛应用于石油化工工程中。
一、DCS系统简介DCS系统,即分散控制系统,是一种用于实时过程控制的集中计算机控制系统。
它由多个分散的控制器组成,这些控制器通过网络进行通信,完成对整个工艺流程的控制与管理。
DCS系统一般包括人机界面(HMI)、过程控制器(PC)以及输入/输出(I/O)模块等组成部分。
二、DCS系统在石油化工中的应用1. 生产流程控制DCS系统可以实现对石油化工生产流程的全面控制和监测。
通过连接各个关键设备和传感器,DCS系统可以实时监测温度、压力、液位等重要参数,并根据设定的工艺要求进行自动控制。
这有助于提高生产效率、减少能源消耗、优化产品质量。
2. 故障诊断和报警DCS系统具备智能故障诊断和报警功能。
一旦感知到异常情况,DCS系统将快速反应并发出警报,通知操作人员及时采取措施,避免设备故障或生产事故发生。
这种自动化监测和报警功能可以保障工厂的安全运行。
3. 数据采集与处理DCS系统可以对石油化工生产中产生的大量数据进行采集和处理。
通过数据的历史存储和实时监测,DCS系统可以为运营和管理层提供有价值的信息,帮助制定更好的生产策略和决策,提高管理水平和生产效益。
4. 远程监控与操作DCS系统还支持远程监控与操作。
操作人员可以通过远程终端与DCS系统进行连接,随时随地实时监测生产数据、追踪工艺变化,并进行远程控制和调整。
这种功能可以提高工作灵活性和生产效率,减少操作人员的工作强度。
5. 系统集成与扩展DCS系统可以与其他相关软硬件进行集成,实现更高级别的自动化控制和管理。
例如,可以集成与ERP(Enterprise Resource Planning)系统,实现产销一体化的全面管理;可以集成与MES(Manufacturing Execution System)系统,实现生产过程的跟踪与优化。
DCS系统在化工工程中的应用案例
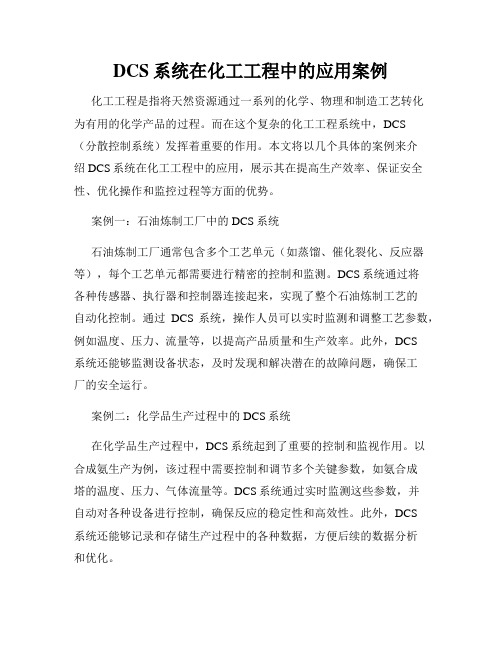
DCS系统在化工工程中的应用案例化工工程是指将天然资源通过一系列的化学、物理和制造工艺转化为有用的化学产品的过程。
而在这个复杂的化工工程系统中,DCS(分散控制系统)发挥着重要的作用。
本文将以几个具体的案例来介绍DCS系统在化工工程中的应用,展示其在提高生产效率、保证安全性、优化操作和监控过程等方面的优势。
案例一:石油炼制工厂中的DCS系统石油炼制工厂通常包含多个工艺单元(如蒸馏、催化裂化、反应器等),每个工艺单元都需要进行精密的控制和监测。
DCS系统通过将各种传感器、执行器和控制器连接起来,实现了整个石油炼制工艺的自动化控制。
通过DCS系统,操作人员可以实时监测和调整工艺参数,例如温度、压力、流量等,以提高产品质量和生产效率。
此外,DCS系统还能够监测设备状态,及时发现和解决潜在的故障问题,确保工厂的安全运行。
案例二:化学品生产过程中的DCS系统在化学品生产过程中,DCS系统起到了重要的控制和监视作用。
以合成氨生产为例,该过程中需要控制和调节多个关键参数,如氨合成塔的温度、压力、气体流量等。
DCS系统通过实时监测这些参数,并自动对各种设备进行控制,确保反应的稳定性和高效性。
此外,DCS系统还能够记录和存储生产过程中的各种数据,方便后续的数据分析和优化。
案例三:DCS系统在制药工业中的应用制药工业对产品质量和生产环境的要求非常高。
DCS系统在制药工业中的应用广泛,可以实现对生产过程的精细控制和监控。
例如,在药物配方和混合工艺中,DCS系统能够控制精确的原料投放和混合过程,以确保产品的一致性和效果。
此外,DCS系统还可以监测生产过程中的温度、湿度、压力等关键参数,及时报警并采取相应的措施以保证生产的安全和稳定。
总结:DCS系统在化工工程中扮演着至关重要的角色。
通过整合和优化工艺控制、监测、数据记录和报警系统,DCS系统有效提高了生产效率,降低了生产成本,保证了生产的安全性和一致性。
随着科技的不断进步,DCS系统在化工工程中的应用还将不断发展和完善,为化工产业的发展带来更多的机遇和挑战。
DCS控制系统在化工生产和消防应急处理系统中的应用

DCS控制系统在化工生产和消防应急处理系统中的应用摘要:DCS控制系统也称为散射控制系统。
工艺控制水平和工艺控制水平均为DCS控制系统类型,DCS控制系统也是一种与网络通信相结合的多级计算机系统,DCS控制系统是结合内容各个方面的最新科学成果,包括:it技术、技术该系统的特点是安全性高、控制功能强、动态可扩展性强、可定期升级等深受现代人喜爱,所有大型石油化工企业都采用该系统,DCS控制系统的应用前景广阔。
本文对DCS控制系统在化工生产和消防应急处理系统中的应用进行分析,以供参考。
关键词:DCS 控制系统;化工企业;化工生产;消防应急处理引言随着信息技术的普及,信息技术控制越来越多地用于社会各个部门。
在化学工业中,由于特殊的生产条件,原料的进入和使用条件通常非常严格。
DCS是一种计算机控制的自动化系统。
在目前化学生产和使用的情况下,DCS不仅可以提供更精确的原料添加技术,而且可以大大提高化学工业的生产效率。
同时DCS控制系统也能保证化工生产的安全DCS自动控制系统在化工领域的应用,不仅在一定程度上提高了化工行业的利益,也促进了化工行业的发展。
1 DCS系统简介集散控制系统(Distributed-Control-System)简称为DCS系统。
该控制系统是计算机技术与网络技术相结合的产物,包括从第三方设备和电信设备采集多种信号。
这些技术使加工工业的管理更加高效和科学。
在我国,分布式设置控制系统(DCS)也被称为一种新的计算机控制系统,与集中式控制系统相比,可以看作是一种新的计算机控制系统。
DCS设计是基于一个由持续、优化和集中控制系统控制的中央控制系统。
在电气、化学等行业。
并随着DCS控制系统的进一步发展,将进一步发展和广泛应用于其他领域。
2 DCS系统的结构通信结构也是DCS控制系统的一部分,该系统分为三个主要层次:过程控制、内部控制和数据管理。
这些数据主要由不同的网络和计算机组成。
信息管理层直接参与系统信息和参数,可以调度特定的生产指令。
- 1、下载文档前请自行甄别文档内容的完整性,平台不提供额外的编辑、内容补充、找答案等附加服务。
- 2、"仅部分预览"的文档,不可在线预览部分如存在完整性等问题,可反馈申请退款(可完整预览的文档不适用该条件!)。
- 3、如文档侵犯您的权益,请联系客服反馈,我们会尽快为您处理(人工客服工作时间:9:00-18:30)。
DCS控制系统在化工生产中的应用分析
作者:翟英丽
来源:《中国化工贸易·下旬刊》2018年第03期
摘要:DCS 控制系统作为一种集实时显示、参数调整、状态监督以及故障报警等功能于一身的系统,将其运用于化工生产中,能让企业花费最小的成本来创造最大的价值以及利润。
本文主要是从DCS控制系统的功能和结构出发,分析其使用过程中存在的问题,并对其在化工生产中的应用情况展开讨论,寻求提升的相关措施。
关键词:DCS控制系统;化工生产;操作
DCS 在我国化工生产中得到了广泛的应用,该系统主要构成包括微处理器、图形显示、网络通信、自动化控制系统、计算机系统构成。
其中微处理器为该系统的基础,能够对整个生产过程进行监控、操作和管理,是一种综合性的控制系统。
DCS 具有较强的功能,从而广泛引用。
包括采集和控制模拟量数据、控制开关量顺序、混合控制开关量、模拟量的数据等。
此外,DCS 系统具有人机界面,容易安装和使用,后期维护较为方便,可随时进行升级换代,这是DCS 系统的一大优势。
目前,在我国化工生产中,没有可以替代DCS 的系统,相关生产设备随着DCS 系统的升级需要进行改造扩容。
因此,DCS 系统在我国化工生产中具有重要的地位。
1 集散控制系统的主要构成
DCS的控制站:在集散控制系统中,控制站是一个完整的、可以独立运行的计算机,在实际的操作过程中可以在不联网的情况下完成操作控制,并且保证整个系统的运行。
控制站是一个独立的计算机,主要包括现场输入和输出设备,包括信号的变换、信号的调理等。
控制站在变换信号的过程中需要用到隔离技术防止其他信号的干扰,这对于整个控制站来讲有着重要的作用。
DCS的操作站:DCS 系统在建立初期,操作站具有操作员功能、工程师功能和通信功能。
其中,工程师功能包括对系统的组态、维护以及通用系统的功能。
DCS 系统操作站也是计算机,有着人机界面以及其他外围设备。
DCS 系统可以完成数据的组织和存储,可以确保人员的操作。
DCS的数据通信网络:DCS 的数据通信网络需要与生产工程的管理网连接,与高级控制计算机站相连接,同时上述控制站和操作站都是通信网络的环节。
DCS 的网络是其最重要的生命线,能够将整个系统连接到一起,其整个系统的稳定性、实时性都受到通信网络的影响。
因此,逐步实现生产工厂的发展,将其与整个工厂的网络技术融合,促进网络系统的开放性,保证其扁平化结构,不断地提高数据通信网络的专业水平。
2 DCS系统使用过程中存在的问题
2.1 DCS系统型号选择的问题
DCS 系统具有可以通用的特点,众多厂家可以参与生产并使用,因此众多设计院并没有标明DCS 系统的型号,仅仅规定了控制回路数、I/O 点数、人际界面要求以及其他相关数据等,尚未表明与整个企业网络之间的关系等,因此,为了保证公平竞争,在明确相关国际标准时需要重视我国DCS 系统的相关数据和标准。
2.2 DCS系统服务问题
DCS 系统是一种技术含量相对较高的系统,其服务问题也是生产厂家需要注意的问题。
生产厂家需要做好相关服务工作,与用户之间做好沟通问题,保证该系统在应用过程中可以进行正常稳定地运行,并且在发生问题之后可以做好售后问题,尽快地将问题解决,从而提升生产厂商的社会声誉,提升自身的经济效益。
3 提升DCS系统应用水平的策略
3.1 提升控制算法的水平
在使用DCS 系统的过程中需要不断地改进DCS 系统的控制算法,可以使用分离的控制算法来对控制积分进行分离,同时可以采用微分、滤波以及微分先行的方式来进行微分计算。
另外,在对算法进行控制,改进大林算法时可以使用离散的控制算法等。
因此,在使用的过程中可以根据不同的算法来进行控制,同时需要不断地提升该控制系统的算法水平,从而能够提升其自动化水平。
3.2 优化DCS的控制系统
控制系统是整个系统运行的关键,需要逐渐优化控制系统,才能够保证DCS 系统可以不断的优化发展。
在使用的过程中可以根据实际情况来增设前馈控制,将其与反馈控制不断地融合。
根据控制系统的实际关联情况来设置解耦控制,根据系统的安全性来选择性地进行控制,根据对象的情况来设置补偿设置等。
在实际应用的过程中,需要根据各项指标的情况来进行控制优化。
3.3 充分应用计算机的功能
计算机的控制系统需要根据相关模型来计算指标,例如热量、温度等控制。
一些难以测算的变量可以根据一些容易测量的过程变量来进行测算,这些技术都需要通过计算机的测量技术来实现。
另外,在使用计算机的过程中可以优化生产过程,通过数学模型来发现系统中的问题,从而做到整体的优化。
4 结束语
我国的化工生产中广泛应用了DCS 系统,能够提升当前化工管理、生产的效率和质量,可以解决用户对自动化、智能化、稳定性、开放性等要求。
我国的DCS 系统生产已经相对成熟,可以在多项化工生产中得到应用。
同时在使用过程中需要不断地总结经验,规范地使用DCS系统,避免使用过程中发生问题,从而提高我国化工生产的效率,为智能化化工生产提供可靠稳定的平台。
参考文献:
[1]帕孜来·马合木提,杨华伟.基于DCS的电锅炉温度控制系统设计[J].实验技术与管理,2016,33(03):82-85.
[2]张桢,牛玉刚.DCS与现场总线综述[J].电气自动化, 2013,35(01):4-6+46.。