埋地钢管外防腐层直接检测技术与方法
埋地管道外腐蚀直接评价方法
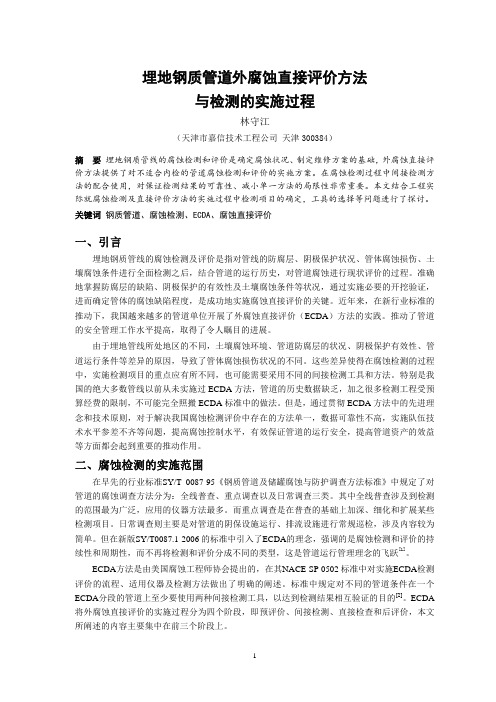
埋地钢质管道外腐蚀直接评价方法与检测的实施过程林守江(天津市嘉信技术工程公司 天津300384)摘 要 埋地钢质管线的腐蚀检测和评价是确定腐蚀状况、制定维修方案的基础,外腐蚀直接评价方法提供了对不适合内检的管道腐蚀检测和评价的实施方案。
在腐蚀检测过程中间接检测方法的配合使用,对保证检测结果的可靠性、减小单一方法的局限性非常重要。
本文结合工程实际就腐蚀检测及直接评价方法的实施过程中检测项目的确定,工具的选择等问题进行了探讨。
关键词钢质管道、腐蚀检测、ECDA、腐蚀直接评价一、引言埋地钢质管线的腐蚀检测及评价是指对管线的防腐层、阴极保护状况、管体腐蚀损伤、土壤腐蚀条件进行全面检测之后,结合管道的运行历史,对管道腐蚀进行现状评价的过程。
准确地掌握防腐层的缺陷、阴极保护的有效性及土壤腐蚀条件等状况,通过实施必要的开挖验证,进而确定管体的腐蚀缺陷程度,是成功地实施腐蚀直接评价的关键。
近年来,在新行业标准的推动下,我国越来越多的管道单位开展了外腐蚀直接评价(ECDA)方法的实践。
推动了管道的安全管理工作水平提高,取得了令人瞩目的进展。
由于埋地管线所处地区的不同,土壤腐蚀环境、管道防腐层的状况、阴极保护有效性、管道运行条件等差异的原因,导致了管体腐蚀损伤状况的不同。
这些差异使得在腐蚀检测的过程中,实施检测项目的重点应有所不同,也可能需要采用不同的间接检测工具和方法。
特别是我国的绝大多数管线以前从未实施过ECDA方法,管道的历史数据缺乏,加之很多检测工程受预算经费的限制,不可能完全照搬ECDA标准中的做法。
但是,通过贯彻ECDA方法中的先进理念和技术原则,对于解决我国腐蚀检测评价中存在的方法单一,数据可靠性不高,实施队伍技术水平参差不齐等问题,提高腐蚀控制水平,有效保证管道的运行安全,提高管道资产的效益等方面都会起到重要的推动作用。
二、腐蚀检测的实施范围在早先的行业标准SY/T 0087-95《钢质管道及储罐腐蚀与防护调查方法标准》中规定了对管道的腐蚀调查方法分为:全线普查、重点调查以及日常调查三类。
埋地管道防腐层检测
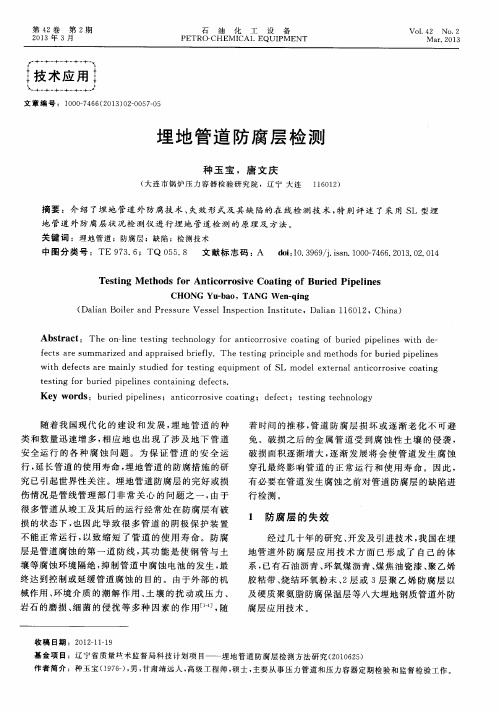
关 键 词 :埋地管道 ;防腐层 ;缺 陷;检测技术
中图分 类号 :TE 9 7 3 . 6 ;TQ 0 5 5 . 8 文献 标 志码 : A d 0 i : 1 0 . 3 9 6 9 / j . i s s n . 1 0 0 0 - 7 4 6 6 . 2 0 1 3 . 0 2 . 0 1 4
Te s t i n g Me t ho d s f o r An t i c o r r o s i v e Co a t i n g o f Bu r i e d Pi p e l i n e s
CH ONG Yu - b a o,TAN G W e n— qi ng
第4 2卷
第 2期
石
油
化
工
设
备
Vo1 . 42 NO. 2
Ma r .2 O1 3
2 0 1 3年 3月
P ETR( ) I CHEM I CAL EQUI P M ENT
, 一. “ ” ” ” ” “ 、
: 技术应用j
+ + + . . + + + .
文章 编 号 :1 0 0 0 — 7 4 6 6 ( 2 0 1 3 ) 0 2 — 0 0 5 7 — 0 5
埋 地 管 道 防腐 层 检 测
种 玉 宝 ,唐 文庆
( 大 连 市 锅 炉压 力容 器 检 验 研 究 院 ,辽 宁 大 连 1 1 6 0 1 2 )
摘 要 :介 绍 了埋 地 管道 外防 腐技 术 、 失效形 式及 其缺 陷的在 线检 测技 术 , 特 别 评述 了采 用 S L型 埋
f e c t s a r e s umm a r i z e d a n d a pp r a i s e d b r i e f l y .The t e s t i n g p r i nc i pl e a nd me t ho d s f o r b ur i e d p i pe l i ne s wi t h d e f e c t s a r e ma i n l y s t u di e d f o r t e s t i ng e q ui pme nt o f SL mo de l e x t e r na l a nt i c o r r os i v e c o a t i n g t e s t i n g f o r bu r i e d p i pe l i ne s c o nt a i ni n g de f e c t s .
埋地钢管外防腐层直接检测技术与方法实用版

YF-ED-J7487可按资料类型定义编号埋地钢管外防腐层直接检测技术与方法实用版In Order To Ensure The Effective And Safe Operation Of The Department Work Or Production, Relevant Personnel Shall Follow The Procedures In Handling Business Or Operating Equipment.(示范文稿)二零XX年XX月XX日埋地钢管外防腐层直接检测技术与方法实用版提示:该操作规程文档适合使用于工作中为保证本部门的工作或生产能够有效、安全、稳定地运转而制定的,相关人员在办理业务或操作设备时必须遵循的程序或步骤。
下载后可以对文件进行定制修改,请根据实际需要调整使用。
摘要:根据多年检测地下管道外防腐层的实践经验,系统地论述了地下管道外防腐层检测前沿的几种理论方法。
通过对这些理论方法和检测技术的分析,以期能对我国油气等埋地管网腐蚀评价的技术规范制定、实际管道腐蚀检测的实施、埋地管网腐蚀评价起到指导和借鉴作用。
关键词:外防腐层直接检测和评价;交流电流法;直流电压法1埋地钢管的腐蚀类型①管道内腐蚀这类腐蚀影响因素相对来说比较单一,主要受所输送介质和其中杂质的物理化学特性的影响,所发生的腐蚀也主要以电化学腐蚀为主。
例如:如果所运输的天然气的湿度和含硫较高时,管道内就容易发生电化学腐蚀。
对于这类腐蚀的机理研究比较成熟,管道内腐蚀所造成的结果也基本上可预知,因此处理方法也规范。
比如通过除湿和脱硫,或增加缓蚀剂就可消除或减缓内腐蚀的发生。
近年来随着管道业主对管道运行管理的加强以及对输送介质的严格要求,内腐蚀在很大程度上得到了控制。
目前国内外长输油气管道腐蚀控制主要发展方向是在外防腐方面,因而管道检测也重点针对因外腐蚀造成的涂层缺陷及管道缺陷。
②管道外腐蚀管道外腐蚀的原因包括外防腐层的外力破损,外防腐层的质量缺陷,钢管的质量缺陷,管道埋设的土壤环境腐蚀。
埋地管道防腐层检测技术
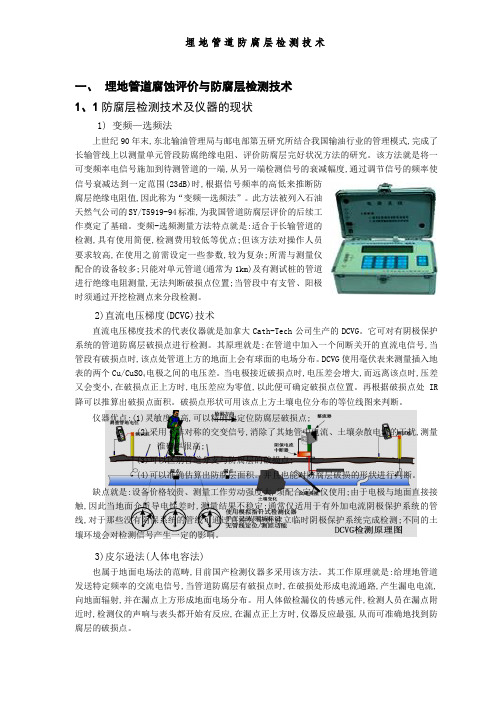
一、埋地管道腐蚀评价与防腐层检测技术1、1防腐层检测技术及仪器的现状1) 变频—选频法上世纪90年末,东北输油管理局与邮电部第五研究所结合我国输油行业的管理模式,完成了长输管线上以测量单元管段防腐绝缘电阻、评价防腐层完好状况方法的研究。
该方法就是将一可变频率电信号施加到待测管道的一端,从另一端检测信号的衰减幅度,通过调节信号的频率使信号衰减达到一定范围(23dB)时,根据信号频率的高低来推断防腐层绝缘电阻值,因此称为“变频—选频法”。
此方法被列入石油天然气公司的SY/T5919-94标准,为我国管道防腐层评价的后续工作奠定了基础。
变频-选频测量方法特点就是:适合于长输管道的检测,具有使用简便,检测费用较低等优点;但该方法对操作人员要求较高,在使用之前需设定一些参数,较为复杂;所需与测量仪配合的设备较多;只能对单元管道(通常为1km)及有测试桩的管道进行绝缘电阻测量,无法判断破损点位置;当管段中有支管、阳极时须通过开挖检测点来分段检测。
2)直流电压梯度(DCVG)技术直流电压梯度技术的代表仪器就是加拿大Cath-Tech公司生产的DCVG。
它可对有阴极保护系统的管道防腐层破损点进行检测。
其原理就是:在管道中加入一个间断关开的直流电信号,当管段有破损点时,该点处管道上方的地面上会有球面的电场分布。
DCVG使用毫伏表来测量插入地表的两个Cu/CuSO4电极之间的电压差。
当电极接近破损点时,电压差会增大,而远离该点时,压差又会变小,在破损点正上方时,电压差应为零值,以此便可确定破损点位置。
再根据破损点处IR 降可以推算出破损点面积。
破损点形状可用该点上方土壤电位分布的等位线图来判断。
仪器优点:(1)灵敏度很高,可以精确地定位防腐层破损点;(2)采用了非对称的交变信号,消除了其她管中电流、土壤杂散电流的干扰,测量准确率很高;(3)可以区别管道分支与防腐层的破损点;(4)可以准确估算出防腐层面积。
并且也能对防腐层破损的形状进行判断。
埋地钢管的防腐方法

埋地钢管的防腐方法1.层状涂覆法层状涂覆法是将一层或多层防腐材料涂覆在钢管表面,以提供物理屏障和防腐保护。
常用的防腐材料包括沥青、聚合物涂料、环氧涂料等。
这些防腐材料具有良好的粘附性和耐腐蚀性,可以有效地抵御土壤中的湿气和化学物质的侵蚀。
2.粘合剂防腐法粘合剂防腐法是将一层粘合层涂覆在钢管表面,然后将防腐层粘贴在粘合层上。
常用的粘合层材料有煤焦油、聚苯乙烯等,而防腐层材料可以是玻璃钢、高密度聚乙烯等。
粘合剂防腐法具有良好的粘附性和耐腐蚀性,能够有效地保护钢管不受土壤侵蚀。
3.管道内防腐管道内防腐是通过在钢管内部涂覆防腐层来保护钢管。
常用的管道内防腐材料有环氧陶瓷涂料、环氧玻璃钢等。
这些材料可以有效地抵御水、酸、碱等化学物质的腐蚀,保护钢管内壁的完整性。
4.阴极保护法阴极保护是一种通过外加电流的方式,使钢管成为阴极而降低其腐蚀速度的方法。
常见的阴极保护方法有电流阳极保护和牺牲阳极保护。
电流阳极保护是把阳极材料(如铅、铝、铅锌合金等)安装在钢管附近,通过外加电流将钢管保护起来;牺牲阳极保护是将一些较容易腐蚀的材料(如锌、铝、镁等)与钢管连接,构成一个电化学电池,使这些材料遭受腐蚀,从而保护钢管。
5.外壳防护法外壳防护法是通过在钢管表面加装外壳来保护钢管。
常见的外壳材料有塑料、玻璃钢、聚乙烯等。
外壳能够有效地抵御土壤中的湿气和化学物质的侵蚀,提供额外的物理保护层,延长钢管的使用寿命。
总之,埋地钢管的防腐方法多种多样,可以根据具体情况选择适当的防腐措施。
通过合理使用这些防腐方法,可以延长钢管的使用寿命,减少维修和更换的需求,提高工程的可靠性和经济效益。
埋地钢管外防腐系统检测和评价技术的研究与应用
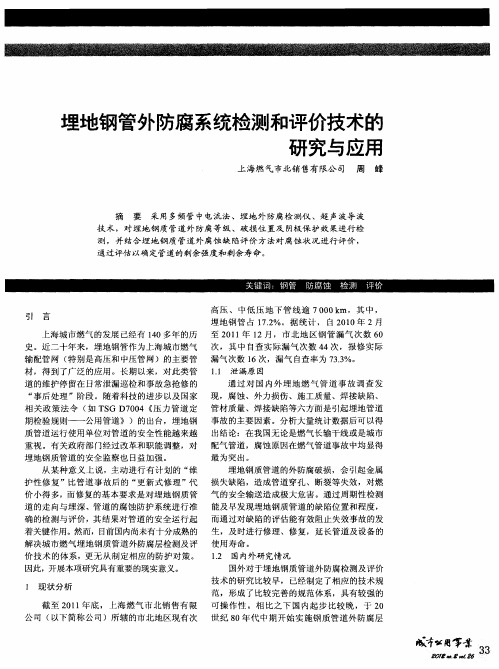
1 国内外研 究情 况 . 2 国外对于埋地钢质管道外防腐检测及评价 技术的研究 比较早 ,已经制定 了相应 的技术规
范,形成 了比较完善的规范体系 ,具有较强 的 截 至 2 1 年 底 ,上海燃气 市 北销 售有 限 可操作 性 。相 比之 下 国 内起 步 比较 晚 ,于 2 01 0 公司 ( 以下简称公司 )所辖 的市北地 区现 有次 世 纪 8 年代 中期 开始实 施钢质管 道外 防腐层 0
护性修 复 ”比管道 事故后 的 “ 更新式修 理”代 损 失缺 陷,造 成管道 穿孔 、断裂等失效 ,对燃
价小得 多,而修复 的基 本要求是对埋 地钢质管 气 的安全输送 造成极大危害 。通过周期性检测 道 的走 向与埋 深、管 道的腐蚀防护系统进 行准 能及 早发现埋地钢质管道的缺 陷位置和程度 , 确的检测与评 价,其 结果对管道 的安全运 行起 而通 过对缺陷的评估能有效阻止失效事故 的发 着关键 作用。然而 ,目前 国内尚未有十分成熟的 生,及 时进行修理、修复 ,延长管道及设备 的 解决城市燃气埋地钢 质管道外防腐层检测及评 使用寿命 。 价技术 的体系 ,更无 从制定相应 的防护对策 。 因此 , 开展本项研究具有重要的现实意义。
埋地钢管外防腐系统检测和评价技术的 研 究与应用
上 海燃 气 市北销 售有 限公 司 周 峰
摘 要 采 用多频 管 中电流法 、埋地 外 防腐检 测仪 、超 声 波导波 技 术 ,对 埋地钢 质管 道外 防腐等 级 、破损 位 置及 阴极保 护 效果进行 检
测 ,并结合 埋地 钢质 管道外 腐蚀缺 陷评价 方 法对 腐蚀 状 况进 行评价 ,
定。
2 . 检 测 方 式 2
2 . 外 防腐系统 间接检测 .1 2
埋地管道检测方案
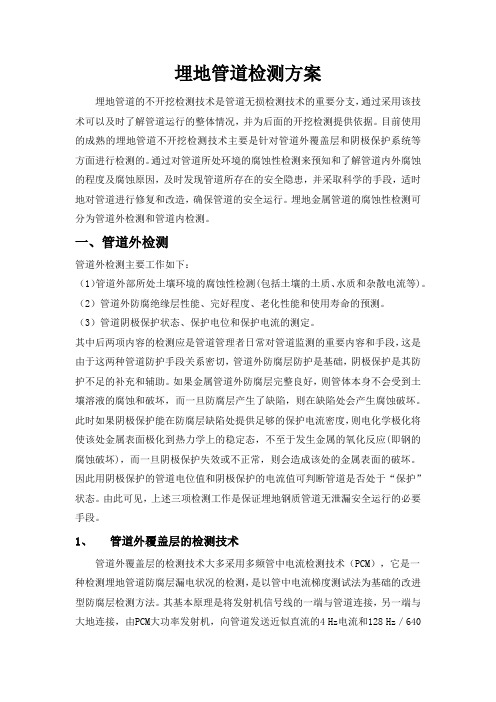
埋地管道检测方案埋地管道的不开挖检测技术是管道无损检测技术的重要分支,通过采用该技术可以及时了解管道运行的整体情况,并为后面的开挖检测提供依据。
目前使用的成熟的埋地管道不开挖检测技术主要是针对管道外覆盖层和阴极保护系统等方面进行检测的。
通过对管道所处环境的腐蚀性检测来预知和了解管道内外腐蚀的程度及腐蚀原因,及时发现管道所存在的安全隐患,并采取科学的手段,适时地对管道进行修复和改造,确保管道的安全运行。
埋地金属管道的腐蚀性检测可分为管道外检测和管道内检测。
一、管道外检测管道外检测主要工作如下:(1)管道外部所处土壤环境的腐蚀性检测(包括土壤的土质、水质和杂散电流等)。
(2)管道外防腐绝缘层性能、完好程度、老化性能和使用寿命的预测。
(3)管道阴极保护状态、保护电位和保护电流的测定。
其中后两项内容的检测应是管道管理者日常对管道监测的重要内容和手段,这是由于这两种管道防护手段关系密切,管道外防腐层防护是基础,阴极保护是其防护不足的补充和辅助。
如果金属管道外防腐层完整良好,则管体本身不会受到土壤溶液的腐蚀和破坏,而一旦防腐层产生了缺陷,则在缺陷处会产生腐蚀破坏。
此时如果阴极保护能在防腐层缺陷处提供足够的保护电流密度,则电化学极化将使该处金属表面极化到热力学上的稳定态,不至于发生金属的氧化反应(即钢的腐蚀破坏),而一旦阴极保护失效或不正常,则会造成该处的金属表面的破坏。
因此用阴极保护的管道电位值和阴极保护的电流值可判断管道是否处于“保护”状态。
由此可见,上述三项检测工作是保证埋地钢质管道无泄漏安全运行的必要手段。
1、管道外覆盖层的检测技术管道外覆盖层的检测技术大多采用多频管中电流检测技术(PCM),它是一种检测埋地管道防腐层漏电状况的检测,是以管中电流梯度测试法为基础的改进型防腐层检测方法。
其基本原理是将发射机信号线的一端与管道连接,另一端与大地连接,由PCM大功率发射机,向管道发送近似直流的4 Hz电流和128 Hz/640Hz定位电流,便携式接收机能准确地探测到经管道传送的这种特殊信号,跟踪和采集该信号,输入到微机,便能测绘出管道上各处的电流强度。
埋地钢制管道的防腐要求

燃气埋地钢制管道的防腐与检测运行部白群星一、钢管防腐规范1、《埋地钢制管道聚乙烯防腐》GB/T23257-2009;2、《钢制管道聚乙烯胶粘带防腐层技术标准》SY/T0414-2007;3、《埋地钢制管道环氧煤沥青防腐层技术标准》SY/T0447-2014;4、《钢制管道熔结环氧粉末外涂层技术规范》SY/T0315-2013;二、埋地钢制管道的防腐应用1、环氧粉末防腐(SY/T0315-2013)(1)环氧粉末(环氧树脂)是一种热固性(第一次加热时可以软化流动,加热到一定温度,产生化学反应一交联固化而变硬,这种变化是不可逆的,此后,再次加热时,已不能再变软流动了。
)、无毒涂料,固化后形成高分子量交联结构涂层,具有优良的化学防腐性能和较高的机械性能,尤其耐磨性和附着力最佳。
该涂料为100%固体,无溶剂,无污染,粉末利用率可达95%以上,是埋地钢质管道的优质防腐涂料。
(2)采用环氧粉末涂敷打底聚乙烯PE及粘剂缠绕或包覆形成的三层PE工艺,是目前国内外普遍采用的钢管道防腐工艺,也是目前国内西气东输及油田输油、气,城市供气、供水所采用的管道防腐工艺。
(3)经过环氧粉末涂覆的钢管可用于工作温度为-30℃——80℃的埋地或者水下环境;我公司2002年铺设的一门站——襄都路段508钢管采用的单层环氧粉末,加强级防腐。
河北省天然气公司铺设的京石邯线508管道同样采用的环氧粉末防腐(是否为单层、加强不确定)。
单层环氧粉末外涂层厚度序号涂层等级最小厚度μm1普通级3002加强级400双层环氧粉末外涂层厚度最小厚度μm序号涂层等级内层外层总厚度1普通级2503506002加强级300500800(4)电火花检漏涂层完全固化且低于100℃时,采用电火花检测,检测电压——最小涂层厚度(μm)×5V/μm。
2、挤压聚乙烯防腐层(GB/T23257-2009)(1)分为长期工作温度不超过50℃(常温N型)、长期工作温度不超过70℃(高温H型);(2)2PE:胶黏剂+聚乙烯;3PE:环氧粉末+胶黏剂+聚乙烯(3)防腐层厚度(4)防腐层检测:防腐层的漏电应采用在线电火花检漏仪进行连续检查,检漏电压为25kv,无漏电为合格。
- 1、下载文档前请自行甄别文档内容的完整性,平台不提供额外的编辑、内容补充、找答案等附加服务。
- 2、"仅部分预览"的文档,不可在线预览部分如存在完整性等问题,可反馈申请退款(可完整预览的文档不适用该条件!)。
- 3、如文档侵犯您的权益,请联系客服反馈,我们会尽快为您处理(人工客服工作时间:9:00-18:30)。
埋地钢管外防腐层直接检测技术与方法摘要:根据多年检测地下管道外防腐层的实践经验,系统地论述了地下管道外防腐层检测前沿的几种理论方法。
通过对这些理论方法和检测技术的分析,以期能对我国油气等埋地管网腐蚀评价的技术规范制定、实际管道腐蚀检测的实施、埋地管网腐蚀评价起到指导和借鉴作用。
关键词:外防腐层直接检测和评价;交流电流法;直流电压法1埋地钢管的腐蚀类型①管道内腐蚀这类腐蚀影响因素相对来说比较单一,主要受所输送介质和其中杂质的物理化学特性的影响,所发生的腐蚀也主要以电化学腐蚀为主。
例如:如果所运输的天然气的湿度和含硫较高时,管道内就容易发生电化学腐蚀。
对于这类腐蚀的机理研究比较成熟,管道内腐蚀所造成的结果也基本上可预知,因此处理方法也规范。
比如通过除湿和脱硫,或增加缓蚀剂就可消除或减缓内腐蚀的发生。
近年来随着管道业主对管道运行管理的加强以及对输送介质的严格要求,内腐蚀在很大程度上得到了控制。
目前国内外长输油气管道腐蚀控制主要发展方向是在外防腐方面,因而管道检测也重点针对因外腐蚀造成的涂层缺陷及管道缺陷。
②管道外腐蚀管道外腐蚀的原因包括外防腐层的外力破损,外防腐层的质量缺陷,钢管的质量缺陷,管道埋设的土壤环境腐蚀。
③管道的应力腐蚀破裂管道在拉应力和特定的腐蚀环境下产生的低应力脆性破裂现象称为应力腐蚀破裂(stresscorrosioncracking,scc),它不仅能影响到管道内腐蚀,也能影响到管道外腐蚀。
关于应力腐蚀,有资料表明,截至1993年底,国内某输气公司的输气干线共发生硫化物应力腐蚀事故78起,其中某分公司的输气干线共发生硫化物应力腐蚀破裂事故28起,仅1979年8月至1987年3月间就发生12次硫化物应力腐蚀的爆管事故,经济损失超过700×104元。
据国外某国11家公司对1985年至1995年间油气管道事故的统计,应力腐蚀破裂占17%。
该国某公司自1977年以来,天然气和液体管道系统发生应力腐蚀破坏事故22起,其中包括12起破裂和10起泄漏事故。
这些应力腐蚀为近中性应力腐蚀,是由于聚乙烯外防护层剥离和管道与水分接触造成的。
2埋地钢管的防腐措施目前管道的腐蚀防护采用了双重措施,即外防腐层和阴极保护。
外防腐层是第一道屏障,对埋地钢管腐蚀起到约95%以上的防护作用,一旦发生局部破损或剥离,就必须保证阴极保护(cathodicprotection,cp)电流的畅通,达到防护效果。
随着防腐涂层性能的降低,cp的作用会逐渐增加,但是无论如何发挥cp的作用,它都不可能替代防腐涂层对管道的保护作用。
而且使用cp应注意它的负作用,cp仅在极化电位-(~)v这样一个很窄的电位带上起作用,一旦电位超出这个范围,就会造成阳极溶解或引起应力腐蚀破裂。
3外防腐层破损的直接检测和评价外防腐层破损直接检测和评价技术ecda(externalcorrosiondirectassessment)是在对埋地钢管不开挖的前提下,采用专用设备和检测方法在地面非接触性地对外防腐层破损缺陷定位,从而对管道的腐蚀状况和管道运行的安全风险进行评估。
国外对这个领域的研究比较早,已经制定了相应的技术规范,从而形成了比较完善的知识体系,比如国际防腐蚀工程师协会(nace)标准rp0502—2002和美国天然气协会(ingaa)对ecda作了详细的要求和规定,因此具有很强的可操作性。
国内实施管道外防腐层检测技术始于20世纪80年代中期,随着改革开放,国外的检测设备大量引进。
但是对于其理论方法和技术规范鲜有论述,致使引进的先进设备并没有发挥应有的效能。
笔者认为对理论方法和技术规范的消化引进更重要,它是我们引进设备的基础,也是再创新的基础。
虽然我国也制定了相应的腐蚀控制的标准,cjj95—2003《城镇燃气埋地钢质管道腐蚀控制技术规程》、sy/t0063—1999《管道防腐层检漏试验方法》,但这些标准只涉及到了防腐层施工和埋设前的质量保证,对埋地管道外防腐层破损直接检测和评价技术没有详细规定,而这方面却又是生产运行中急需解决的问题。
3.1外防腐层破损直接检测和评价的步骤按照国际防腐蚀工程师协会(nace)标准rp0502—2002的要求,ecda的总体技术要求是对于腐蚀已经发生、正在发生和将要发生的敏感管段能做出预测。
在实际应用时,为达到此目标,要进行如下4个操作步骤。
①预评价(pre.assessment)收集敏感管道的历史资料及管道特征,并对这些资料进行评估。
在所搜集的管道资料的基础上,制定ecda的可行性方案,按相似条件的管段划分不同的区域,在这些区域内采用的检测仪器要相同,以保证结果的可比性。
②非接触测量(indirectinspection)采用2种或2种以上的地面外防腐层破损检测技术,比如:密间隔电位法(closeintervalpotentialsurvey,cips)、直流电压梯度法(directcurrentvoltagegradient,dcvg)、交流电压梯度法(alternatingcurrentvoltagegradient,acvg)、交流电流衰减法(acattenuation),用以检测管道的腐蚀行为和查找外防腐层的破损点。
系统地分析以上方法所取得的数据,得出高风险区域的开挖修复的准确信息。
③直接开挖验证(directexamination)选定开挖的现场,实际识别出破损点,并决定是修复还是更换管道。
④后评价(postassessment)对ecda的以上3个步骤做出总结,建立起评价模型,以便指导将来的管道安全维护。
3.2外防腐层破损的检测方法3.2.1交流电流法交流电流法在国际上通常被称为皮尔逊检测法(pearsonsurvey)。
其基本原理是:当用一个信号发射机把特定频率的交流信号通过导线施加在金属管道上时,这种特定频率的交流信号就会沿管道向前传播,并在无穷远处与发射机的地线形成回路。
如果管道的外防腐层完好,由于管道电阻的原因,管道中交流信号是沿程均匀衰减的;如果管道的外防腐层有破损或绝缘不好,在外防腐层破损点便会有电流泄漏入土壤中,这样如果沿程测量管道中的电流信号,在破损点附近,就会有一个管中电流的陡降;同时在管道破损点和土壤之间也会形成电压差,且在接近破损点的部位电压差最大,用仪器在埋设管道的地面上可检测到这种电流或电位异常,即可发现管道外防腐层破损点。
特别指出的是,皮尔逊检测是一种检测方法和基本原理,不是具体的某种设备,把基于以上原理的检测设备与一种检测方法混为一谈是不恰当的。
皮尔逊检测法最大的特点是向管道施加特定频率的交流信号,然后在防腐层破损点检测到电流或者电压的异常。
基于以上原理,不同的厂家开发出各具特色的产品,这些产品的区别主要在于采用的信号频率不同和接收天线数目和布局不同,目前主流的检测设备有以下两种。
①c-扫描设备该设备接收机采用5根垂直阵列天线,提高了管道定位精度,具有自动识别干扰信号并提示的能力。
c-扫描采用的交流信号是单一的交流信号。
该设备能够方便地确定被测管道位置或防腐层缺陷位置。
在测试过程中自动记录、处理和储存检测数据,现场显示各种检测曲线,可现场评判防腐层性能,并具备数据结果存储和进一步分析评价的能力。
其缺点是设备价格昂贵,稍高的信号频率易受外界电磁杂波的干扰,并且一旦受到干扰,由于设备只有一种频率,很难避开干扰。
另外,c-扫描没有测量破损点电压异常的附件。
②管中电流法测绘设备管中电流法测绘设备(pipecurrentmapping,pcm)的最大特点是施加“准直流”的4hz交流信号作为防腐层破损检测的测绘信号,并有128/640hz的定位信号。
接收机天线采用经典的双水平天线和单竖直天线,既可按峰值(双水平天线)也可按零值(单竖直天线)定位。
pcm能够通过a字架测量破损点的跨步电压(setvoltage)异常。
pcm具有数据存储功能,数据可以用国内开发出的相应评价软件分析。
pcm具有较大的市场占有率。
pcm的缺点是发射机不带电源,在野外操作不方便。
与pcm类似的产品还有德国ferrophonel/g1设备。
其最大的特点是接收机能够直接接收阴极保护的信号,因此对有阴极保护的管道定位十分方便。
它把交流信号作为防腐层破损检测的测绘信号,并有42/10khz的定位信号,接收机天线也是采用经典的双水平天线和单竖直天线,既可按峰值(双水平天线)也可按零值(单竖直天线)定位。
它也能够通过a字架测量破损点的跨步电压异常。
其优点是价格低,缺点是数据不能存储。
基于皮尔逊检测法的设备,由于接收机轻便,检测速度较快,自带信号发射机,可以检测没有阴极保护(cp)的管道,因此目前国内仍较普遍使用,受现场检测人员的欢迎。
但是这些设备使用局限性也很大:操作者的经验技能特别重要,没有现场经验的人不易查找到涂层缺陷的位置,或者是常给出不存在的缺陷信息;很难指示涂层剥离但管道不漏铁的破损点;不能指示cp效率,易受地电场干扰。
3.2.2直流电压法外防腐层破损检测和管道腐蚀状态评价的另一个前沿研究领域就是直流电压梯度法(dcvg),其特点是利用现有的阴极保护直流信号或临时向管道施加直流信号,然后在防腐层破损点检测到管对地极化电压的异常,从而确定破损点和破损程度。
而采用密间隔电位法(cips)全面测量,有助于评估管道整体阴极保护的情况。
这两种技术的结合(dcvg+cips)代表了这一领域的发展方向,也符合国际防腐蚀工程师协会(nace)标准rp0502—2002的基本要求。
①密间隔电位测量法密间隔电位法cips主要用于测定cp系统的效果,间接反映防腐涂层状况。
cips法沿管道以间隔~采集数据,绘制连续的开/关管地电位曲线图,反映管道全线阴极保护电位情况。
当防腐层某处存在缺陷时,该处电流密度增大,使保护电位正向偏移,当这种偏移达到一定数量,在地表就可检测到,当电位(铜/硫酸铜参比电极)低于-850mv时,管道就会发生腐蚀。
cips法不能检出涂层破损的准确位置,实际上是一种管地电位检测技术并非涂层缺陷检测技术,涂层状况是通过电位分析获得的,因此通常要与dcvg配合使用。
用cips判定cp 不足或过保护具有独到之处。
②直流电压梯度法直流电压梯度法(dcvg)是由johnmulvaney在澳大利亚首先提出,最初应用在通信电缆外护套破损的确定,而后广泛地应用在埋地钢管外防腐层破损的直接检测和评价领域,至今已经有逾30a历史。
其基本原理是当把一个直流信号(比如阴极保护信号)施加到带防腐层的管道上,就能在管道的防腐层破损点裸露的管体和大地之间,由于土壤的电阻作用,建立起电压梯度,即土壤的电压降δu。
依据土壤的电压降占管道对地电压的百分比来计算涂层缺陷的大小和破损点的严重程度,越靠近管道的破损点电压的梯度越大,流失的电流也越大。