真空树脂导入工艺和手糊工艺的比较
手糊产品设计及真空导入成型工艺在汽车领域的应用研究
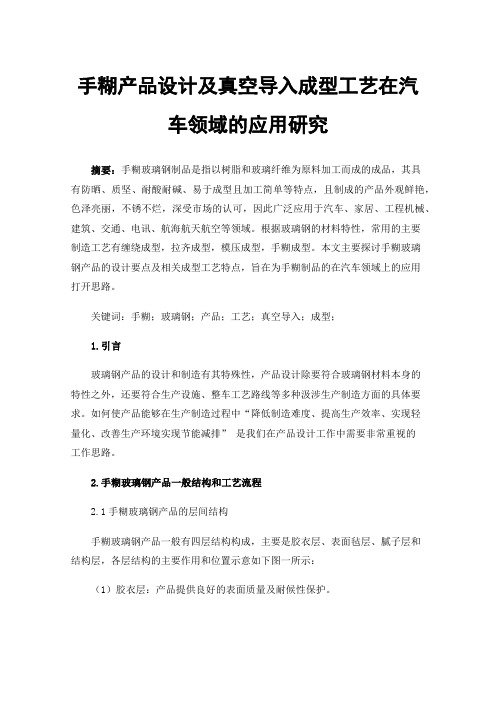
手糊产品设计及真空导入成型工艺在汽车领域的应用研究摘要:手糊玻璃钢制品是指以树脂和玻璃纤维为原料加工而成的成品,其具有防晒、质坚、耐酸耐碱、易于成型且加工简单等特点,且制成的产品外观鲜艳,色泽亮丽,不锈不烂,深受市场的认可,因此广泛应用于汽车、家居、工程机械、建筑、交通、电讯、航海航天航空等领域。
根据玻璃钢的材料特性,常用的主要制造工艺有缠绕成型,拉齐成型,模压成型,手糊成型。
本文主要探讨手糊玻璃钢产品的设计要点及相关成型工艺特点,旨在为手糊制品的在汽车领域上的应用打开思路。
关键词:手糊;玻璃钢;产品;工艺;真空导入;成型;1.引言玻璃钢产品的设计和制造有其特殊性,产品设计除要符合玻璃钢材料本身的特性之外,还要符合生产设施、整车工艺路线等多种汲涉生产制造方面的具体要求。
如何使产品能够在生产制造过程中“降低制造难度、提高生产效率、实现轻量化、改善生产环境实现节能减排” 是我们在产品设计工作中需要非常重视的工作思路。
2.手糊玻璃钢产品一般结构和工艺流程2.1手糊玻璃钢产品的层间结构手糊玻璃钢产品一般有四层结构构成,主要是胶衣层、表面毡层、腻子层和结构层,各层结构的主要作用和位置示意如下图一所示:(1)胶衣层:产品提供良好的表面质量及耐候性保护。
(2)表面毡(表面要求高的产品需要此层):减少表面气泡,隔离布纹,平整表面。
由于此层的树脂含量高,所以可以作为产品的防腐层。
(3)腻子层:提高结构层玻璃纤维的贴合能力,减少产品表面下层气泡。
(4)结构层:由树脂和玻璃钢纤维复合固化,是产品的受力主体。
可以根据功能需要,结构成可以细分为防腐层、防老化层、强度层等功能层。
各功能层采用不同特性的玻璃纤维材料铺设。
(图一)2.2手糊玻璃钢产品的成型过程简图如下图二所示:(图二)2.3手糊玻璃钢产品常用的原材料手糊成型玻璃钢的主要原材料有:①玻璃纤维制品:主要有表面毡、短切毡、方格布,主要作用是平整表面(使布纹不能透过胶衣层)、减少气泡;②树脂;③固化剂、促进剂;④填料;⑤颜料糊;⑥其他添加剂,如稀释剂、光稳定剂、阻燃剂等。
真空导入工艺和手糊工艺的比较-1

真空导入工艺和手糊工艺的比较手糊工艺(Handlay-up)是一种开模工艺,目前在玻璃纤维增强的聚酯复合材料中占65%。
它的优点是在模具的形状改变上有很大的自由度,模具价格低,适应性强、产品性能得到市场认可和投资少等。
所以特别适合于小公司,也适合于船舶及航空航天产业,这儿通常是一次性的大部件。
但该工艺也存在一系列问题,如可挥发有机物(VOC)排放超标、对操作人员的健康影响大、人员易流失、许用材料限制多、产品性能低,树脂浪费并且用量大等,尤其是产品质量不稳定,产品的玻纤和树脂比例、部件厚度、层材制造速率、层材的均匀性等都受操作人员的影响,要求操作人员有较好的技术、经验和素质。
手糊产品的树脂含量一般在50%-70%左右。
开模工艺的VOC排放超过500PPm,苯乙烯的挥发量高达使用量的35%-45%。
而各国规定都在50-100PPm。
目前国外大都改用环戊二烯(DCPD)或其它低苯乙烯释放树脂,但苯乙烯作为单体还没有好的替代品。
真空树脂导入工艺是近20年来发展的制造工艺,尤适合于大型产品的制造。
优点如下:(1)产品性能优良,成品率高。
在同样原材料的情况下,与手糊构件相比,真空树脂导入工艺成型构件的强度、刚度及其它的物理特性可提高30%-50%以上(表1)。
工艺稳定后成品率可接近100%。
表1典型聚酯玻璃钢性能比较增强材料无捻粗纱布双抽向织物无捻粗纱布双抽向织物成型工艺手糊手糊真空树脂扩散真空树脂扩散玻纤含量45506065 拉伸强度(MPa)273.2389383.5480 拉伸模量(GPa)13.518.517.921.9 压缩强度(MPa)200.4247215.2258 压缩模量(GPa)13.421.315.623.6 弯曲强度(MPa)230.3321325.7385 弯曲模量(GPa)13.41716.118.5 层间剪切强度(MPa)2030.73537.8 纵横剪切强度(MPa)48.8852.17 纵横剪切模量(GPa)1.621.84(2)产品质量稳定,重复性好。
玻璃钢制作工艺真空导入原理
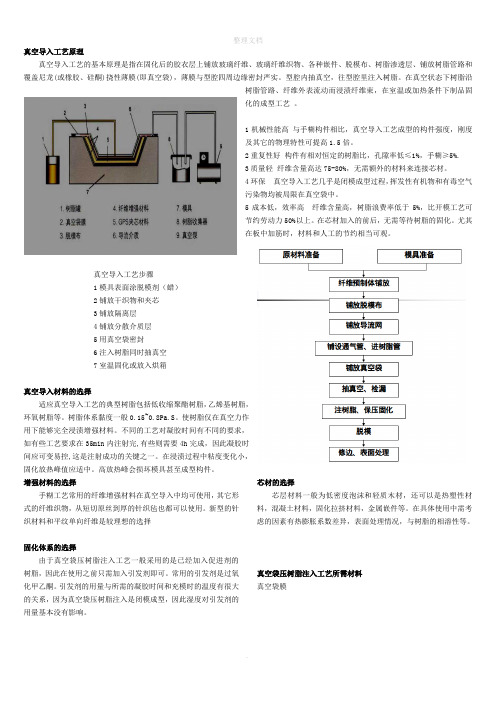
真空导入工艺原理真空导入工艺的基本原理是指在固化后的胶衣层上铺放玻璃纤维、玻璃纤维织物、各种嵌件、脱模布、树脂渗透层、铺放树脂管路和覆盖尼龙(或橡胶、硅酮)挠性薄膜(即真空袋),薄膜与型腔四周边缘密封严实。
型腔内抽真空,往型腔里注入树脂。
在真空状态下树脂沿树脂管路、纤维外表流动而浸渍纤维束,在室温或加热条件下制品固化的成型工艺。
1机械性能高与手糊构件相比,真空导入工艺成型的构件强度,刚度及其它的物理特性可提高1.5倍。
2重复性好构件有相对恒定的树脂比,孔隙率低≤1%,手糊≥5%.3质量轻纤维含量高达75-80%,无需额外的材料来连接芯材。
4环保真空导入工艺几乎是闭模成型过程,挥发性有机物和有毒空气污染物均被局限在真空袋中。
5成本低,效率高纤维含量高,树脂浪费率低于5%,比开模工艺可节约劳动力50%以上。
在芯材加入的前后,无需等待树脂的固化。
尤其在板中加筋时,材料和人工的节约相当可观。
真空导入工艺步骤1模具表面涂脱模剂(蜡)2铺放干织物和夹芯3铺放隔离层4铺放分散介质层5用真空袋密封6注入树脂同时抽真空7室温固化或放入烘箱真空导入材料的选择适应真空导入工艺的典型树脂包括低收缩聚酯树脂,乙烯基树脂,环氧树脂等。
树脂体系黏度一般0.15~0.8Pa.S。
使树脂仅在真空力作用下能够完全浸渍增强材料。
不同的工艺对凝胶时间有不同的要求,如有些工艺要求在35min内注射完,有些则需要4h完成,因此凝胶时间应可变易控,这是注射成功的关键之一。
在浸渍过程中粘度变化小,固化放热峰值应适中。
高放热峰会损坏模具甚至成型构件。
增强材料的选择手糊工艺常用的纤维增强材料在真空导入中均可使用,其它形式的纤维织物,从短切原丝到厚的针织毡也都可以使用。
新型的针织材料和平纹单向纤维是较理想的选择芯材的选择芯层材料一般为低密度泡沫和轻质木材,还可以是热塑性材料,混凝土材料,固化拉挤材料,金属嵌件等。
在具体使用中需考虑的因素有热膨胀系数差异,表面处理情况,与树脂的相溶性等。
玻璃钢制作工艺真空导入原理

真空导入工艺原理真空导入工艺的基本原理是指在固化后的胶衣层上铺放玻璃纤维、玻璃纤维织物、各种嵌件、脱模布、树脂渗透层、铺放树脂管路和覆盖尼龙(或橡胶、硅酮)挠性薄膜(即真空袋),薄膜与型腔四周边缘密封严实。
型腔内抽真空,往型腔里注入树脂。
在真空状态下树脂沿树脂管路、纤维外表流动而浸渍纤维束,在室温或加热条件下制品固化的成型工艺。
1机械性能高与手糊构件相比,真空导入工艺成型的构件强度,刚度及其它的物理特性可提高1.5倍。
2重复性好构件有相对恒定的树脂比,孔隙率低≤1%,手糊≥5%.3质量轻纤维含量高达75-80%,无需额外的材料来连接芯材。
4环保真空导入工艺几乎是闭模成型过程,挥发性有机物和有毒空气污染物均被局限在真空袋中。
5成本低,效率高纤维含量高,树脂浪费率低于5%,比开模工艺可节约劳动力50%以上。
在芯材加入的前后,无需等待树脂的固化。
尤其在板中加筋时,材料和人工的节约相当可观。
真空导入工艺步骤1模具表面涂脱模剂(蜡)2铺放干织物和夹芯3铺放隔离层4铺放分散介质层5用真空袋密封6注入树脂同时抽真空7室温固化或放入烘箱真空导入材料的选择。
增强材料的选择手糊工艺常用的纤维增强材料在真空导入中均可使用,其它形式的纤维织物,从短切原丝到厚的针织毡也都可以使用。
新型的针织材料和平纹单向纤维是较理想的选择芯材的选择芯层材料一般为低密度泡沫和轻质木材,还可以是热塑性材料,混凝土材料,固化拉挤材料,金属嵌件等。
在具体使用中需考虑的因素有热膨胀系数差异,表面处理情况,与树脂的相溶性等。
固化体系的选择由于真空袋压树脂注入工艺一般采用的是已经加入促进剂的树脂,因此在使用之前只需加入引发剂即可。
常用的引发剂是过氧化甲乙酮。
引发剂的用量与所需的凝胶时间和充模时的温度有很大的关系,因为真空袋压树脂注入是闭模成型,因此湿度对引发剂的用量基本没有影响。
真空袋压树脂注入工艺所需材料真空袋膜导流网脱模布中空螺旋管树脂进料管抽气管真空袋密封胶吸胶毡定位喷胶1.真空袋膜聚丙烯膜是最常用的真空袋膜,可以在形状复杂的模具上拉伸,无折叠和褶皱,真空效率高。
复合材料成型加工技术---
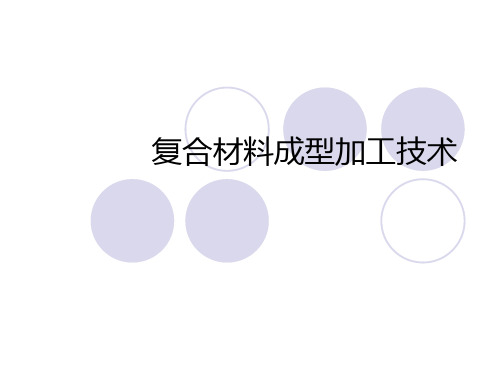
真空袋
1. 过程
制品毛坯 真空袋密封 抽真空 固化 制品
2. 特征 1)工艺简单,不需要专用设备; 2)压力较小,最大为0.1MPa,只适
用厚度1.5mm以下复合材料制品
压力袋成型
压力为0.25~0.5MPa
真空袋-热压罐成型
预浸料成型
预浸料成型(prepreg lay-up)
基本步骤:
设备:要求比RTM高,投资大
模压成型(Compression Molding)
将复合材料片材或模塑料放入金属对模中, 在温度和压力作用下,材料充满模腔,固 化成型,脱模制得产品的方法。
模具预热 模压料称量
涂刷脱模剂 预热
装模
压制 脱模
制品 检验 后处理
BMC模压 SMC、TMC模压 预浸料模压(层压)
多孔膜 密实膜 多孔织物
多孔膜
真空封装系统:透气、隔离、吸胶、透胶系统
适合加工高纤维含量(>60%)复合材料 简单和复杂构型构件均可以加工 高强度和高刚度复合材料均可以加工 劳动强度大,不适于大量加工 构件成本高 在航空和军事用先进复合材料上用途广泛
喷射成型(spray-up process)
包括:
干法缠绕: 预浸纱 湿法缠绕: 纤维纱 半干法缠绕: 纤维纱
加热软化 缠绕 浸胶 缠绕 浸胶 烘干 缠绕
非常适合制作管 状制品,如压力 容器、管道、火 箭发动机壳体、 喷管、化学品储 存罐等
配合CAD系统, 可以制作外形更 为复杂的构件
基本步骤
① 粗纱线轴放置在粗纱架上; ② 几根粗纱从导纱沟中穿过; ③ 固化剂和树脂在容器中混合后倒入树脂浸渍槽中; ④ 在卷绕滚筒上涂覆脱模剂、凝胶涂层,并将卷绕滚筒放
玻璃钢制作工艺真空导入原理

真空导入工艺原理真空导入工艺的基本原理是指在固化后的胶衣层上铺放玻璃纤维、玻璃纤维织物、各种嵌件、脱模布、树脂渗透层、铺放树脂管路和覆盖尼龙(或橡胶、硅酮)挠性薄膜(即真空袋),薄膜与型腔四周边缘密封严实。
型腔内抽真空,往型腔里注入树脂。
在真空状态下树脂沿树脂管路、纤维外表流动而浸渍纤维束,在室温或加热条件下制品固化的成型工艺。
1机械性能高与手糊构件相比,真空导入工艺成型的构件强度,刚度及其它的物理特性可提高1.5倍。
2重复性好构件有相对恒定的树脂比,孔隙率低≤1%,手糊≥5%.3质量轻纤维含量高达75-80%,无需额外的材料来连接芯材。
4环保真空导入工艺几乎是闭模成型过程,挥发性有机物和有毒空气污染物均被局限在真空袋中。
5成本低,效率高纤维含量高,树脂浪费率低于5%,比开模工艺可节约劳动力50%以上。
在芯材加入的前后,无需等待树脂的固化。
尤其在板中加筋时,材料和人工的节约相当可观。
真空导入工艺步骤1模具表面涂脱模剂(蜡)2铺放干织物和夹芯3铺放隔离层4铺放分散介质层5用真空袋密封6注入树脂同时抽真空7室温固化或放入烘箱真空导入材料的选择适应真空导入工艺的典型树脂包括低收缩聚酯树脂,乙烯基树脂,环氧树脂等。
树脂体系黏度一般0.15~0.8Pa.S。
使树脂仅在真空力作用下能够完全浸渍增强材料。
不同的工艺对凝胶时间有不同的要求,如有些工艺要求在35min内注射完,有些则需要4h完成,因此凝胶时间应可变易控,这是注射成功的关键之一。
在浸渍过程中粘度变化小,固化放热峰值应适中。
高放热峰会损坏模具甚至成型构件。
增强材料的选择手糊工艺常用的纤维增强材料在真空导入中均可使用,其它形式的纤维织物,从短切原丝到厚的针织毡也都可以使用。
新型的针织材料和平纹单向纤维是较理想的选择芯材的选择芯层材料一般为低密度泡沫和轻质木材,还可以是热塑性材料,混凝土材料,固化拉挤材料,金属嵌件等。
在具体使用中需考虑的因素有热膨胀系数差异,表面处理情况,与树脂的相溶性等。
GRP真空成型(真空导入)工艺与手糊(湿法)工艺结合新技术
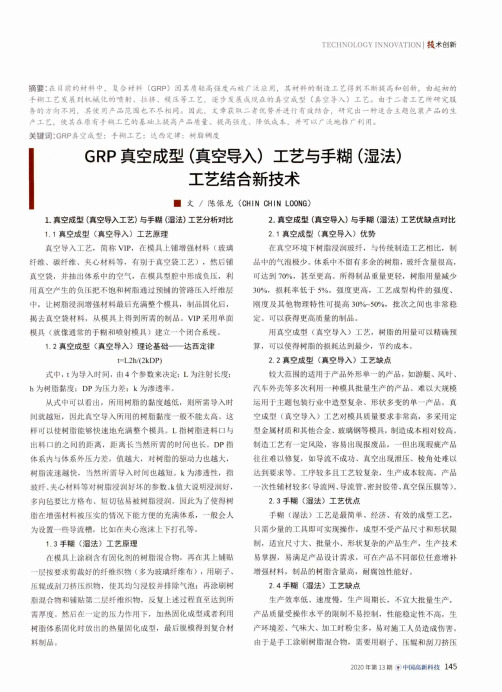
TECHNOLOGY INNOVATION |後术创新摘要:在目前的材料中,复合材料(G R P)因其质轻高强度而被广泛应用,其材料的制造工艺得到不断提高和创新,由起初的手糊工艺发展到机械化的喷射、拉挤、模压等工艺,逐步发展成现在的真空成型(真空导入)工艺。
由于二者工艺所研究服务的方向不同,其使用产品范围也不尽相同。
因此,文章获取二者优势并进行有效结合,研究出一种适合主题包装产品的生产工艺,使其在原有手糊工艺的基础上提高产品质量、提高强度、降低成本,并可以广泛地推广利用。
关键词:G RP真空成型:手糊工艺:达西定律:树脂裯度G R P真空成型(真空导入)工艺与手糊(湿法)工艺结合新技术■文/陈恨龙1.真空成型(真空导入工艺)与手糊(湿法)工艺分析对比1.1真空成型(真空导入)工艺原理真空导入工艺,简称VIP,在模具上铺增强材料(玻璃 纤维、碳纤维、夹心材料等,有别于真空袋工艺),然后铺 真空袋,并抽出体系中的空气,在模具型腔中形成负压,利 用真空产生的负压把不饱和树脂通过预铺的管路压入纤维层 中,让树脂浸润增强材料最后充满整个模具,制品固化后,揭去真空袋材料,从模具上得到所需的制品。
VIP采用单面 模具(就像通常的手糊和喷射模具)建立一个闭合系统。
1.2真空成型(真空导入)理论基础—达西定律t=L2h/(2kDP)式中,t为导入时间,由4个参数来决定;L为注射长度:h为树脂黏度;D P为压力差;k为渗透率。
从式中可以看出,所用树脂的黏度越低,则所需导入时 间就越短,因此真空导入所用的树脂黏度一般不能太高。
这 样可以使树脂能够快速地充满整个模具。
L指树脂进料口与 出料口的之间的距离,距离长当然所需的时间也长。
D P指 体系内与体系外压力差,值越大,对树脂的驱动力也越大,树脂流速越快,当然所需导入时间也越短。
k为渗透性,指 玻纤、夹心材料等对树脂浸润好坏的参数。
k值大说明浸润好, 多向毡要比方格布、短切毡易被树脂浸润。
VARI技术及其发展(华昌)

真空树脂扩散工艺的应用
真空树脂扩散工艺可一次成型面积达 200m2 、厚度为 3-150mm 、纤维含量达 6070%、孔隙率可达到1%-1.5%的制品。所 以该工艺是一种高质量低成本制造技术。适宜 制造船艇(达73m)、风机叶片、桥梁、汽车 部件及海洋基础工程等大中型制品。 在美国的低成本复合材料计划 (CAI 计划 ) 中,VARI 技术作为 CAI 复合材料低成本技术 体系中的一项重要技术。
压缩强度(MPa) 压缩模量(GPa)
弯曲强度(MPa)
弯曲模量(GPa) 层间剪切强度(MPa) 纵横剪切强度(MPa) 纵横剪切模量(GPa)
230.3
13.4 20 48.88 1.62
321
17 30.7
325.7
16.1 35 52.17 1.84
385
18.5 37.8
真空树脂扩散技术和手糊技术的比较
407
435
455
478
498
514
529
540
552
国产的织物铺层比西班牙织物的树脂导流性能稍差,
6) 不同厂家缝合和非缝合织物对 树脂流动性能的影响
800 700 600 500 400 300 200 100 0 0 5 10 15 —CDFM Inpre CD-CFM-CSM 分开 —CDFM 国产
同样的织物铺层在缝合后,对流动速度有不同影响。 但同为缝合织物,进口织物的浸润速度要快得多,
(3) 织物中的毛细管作用的影响研究
1)毛细管作用对树脂浸润性能的影响 研究了三种织物的毛细管现象对浸润速度的影 响。在相同溶液粘度下,三种织物浸润速度和高度 不同。闭模毡为夹芯结构,可以使树脂很快的流动, 并具有很高的浸润量,因此这类材料有很高的树脂 含量。双轴向织物在初始阶段的树脂流动速度低于 长丝毡,但其最终浸润高度却近于长丝毡。另外, 不同织物在不同的溶液中,上升速度和最终高度也 不尽相同。树脂粘度越大,浸润速度和浸润量减小。
- 1、下载文档前请自行甄别文档内容的完整性,平台不提供额外的编辑、内容补充、找答案等附加服务。
- 2、"仅部分预览"的文档,不可在线预览部分如存在完整性等问题,可反馈申请退款(可完整预览的文档不适用该条件!)。
- 3、如文档侵犯您的权益,请联系客服反馈,我们会尽快为您处理(人工客服工作时间:9:00-18:30)。
真空树脂导入工艺和手糊工艺的比较
目前用于风电机舱罩制造的材料主要为聚酯玻璃纤维复合材料,成型工艺主要为手糊工艺和真空树脂导入工艺,两者的优缺点比较如下:
手糊工艺(Hand lay-up)是一种开模工艺,目前在玻璃纤维增强的聚酯复合材料中占65%。
他的优点是在模具的形状改变上有很大的自由度,模具价格低,适应性强、产品性能得到市场认可和投资少等。
所以特别适合于小公司,也适合于船舶及航空航天产业,这儿通常是一次性的大部件。
但该工艺也存在一系列问题,如可挥发有机物(VOC)排放超标、对操作人员的健康影响大、人员易流失、许用材料限制多、产品性能低,树脂浪费并且用量大等,尤其是产品质量不稳定,产品的玻纤和树脂比例、部件厚度、层材制造速率、层材的均匀性等都受操作人员的影响,要求操作人员有较好的技术、经验和素质。
手糊产品的树脂含量一般在50%-70%左右。
开模工艺的VOC排放超过500PPm,苯乙烯的挥发量高达使用量的35%-45%。
而各国规定都在50-100PPm。
目前国外大都改用环戊二烯(DCPD)或其它低苯乙烯释放树脂,但苯乙烯作为单体还没有好的替代品。
[-page-]
真空树脂导入工艺是近20年来发展的低成本制造工艺,尤适合于大型产品的制造。
其优点如下:
(1)产品性能优良,成品率高。
在同样原材料的情况下,与手糊构件相比,真空树脂导入工艺成型构件的强度、刚度及其它的物理特性可提高30%-50%以上(表1)。
工艺稳定后成品率可接近100%。
(2)产品质量稳定,重复性好。
产品质量受操作人员影响小,不论是同一构件还是各构件间都存在高度的一致性。
产品的纤维用量在注入树脂前已按规定的量放入模具中,构件有相
对恒定的树脂比,一般在30%-45%,因此产品性能的均匀性和重复性比手糊工艺产品好得多,缺陷也少得多。
(3)抗疲劳性能提高,可减轻结构重量。
由于制品纤维含量高、孔隙率低、产品性能高,尤其是层间强度的提高,大大提高了产品的抗疲劳性能。
在强度或刚度要求相同的情况下,采用真空导入工艺制作的产品可减轻结构重量。
(4)环境友善。
真空树脂导入工艺是一种闭模工艺,挥发性有机物和有毒空气污染物均被局限于真空袋中。
仅在真空泵排气(可过滤)和打开树脂桶时有微量的挥发物。
VOC排放不超过5PPm的标准。
这也大大改善了操作人员的工作环境,稳定了劳动人员的队伍,也扩大了可用材料的范围。
(5)产品整体性好。
真空树脂导入工艺可同时成形加强筋、夹芯结构及其它嵌件,提高了产品的整体性,因此可制造风机机罩、船体和上层建筑等大型制品。
(6)减少原材料使用,减少用工。
在同样铺层时,树脂用量减少30%。
浪费少,树脂损耗率低于5%。
劳动生产率高,比手糊工艺可节约劳动力50%以上。
尤其在成型大型复杂几何形状的夹芯和加筋结构件时,材料和人工的节省更为可观。
如在航空工业的垂直舵制造中,使紧固件减少365个价格比传统方法减少75%,产品重量不变,性能更好。
(7)制品精度好。
真空树脂导入工艺产品的尺寸精度(厚度)优于手糊制品。
在同样的铺层下,一般真空树脂扩散技术产品的厚度为手糊制品的2/3 。
产品厚度偏差约为士10%,而手糊工艺一般为士20% 。
产品表面的平整度优于手糊产品。
真空树脂导入工艺的机罩产品内壁光滑,表面自然形成富树脂层,不需要另外加涂面漆(Top coat)。
减少了打磨和涂漆工序的人工和材料。
当然目前真空树脂导入工艺也有一定的缺点:
(1)准备工序时间较长而且较为复杂。
需要正确的铺层、铺设导流介质、导流管、有效的真空密封等。
因此对于小尺寸产品,其工艺时间反而超过手糊工艺。
(2)生产成本较高,并产生较多的废料。
如真空袋膜、导流介质、脱模布及导流管等辅助材料都是一次性使用,而且目前相当多的要依赖进口,故生产成本比手糊工艺高。
但产品越大,这个差别越小。
随着辅助材料的国产化,这一成本差别也越来越小。
当前研究可多次使用的辅助材料是本工艺的一个发展方向。
(3)工艺制造有一定的风险。
尤其是大型复杂结构产品,一旦在树脂灌注中失败,产品易报废。
因此要有较好的前期研究,严格的工艺控制和有效的补救措施,以保证工艺的成功。