模具问题改善与建议
模具加工改善方案

模具加工改善方案在制造业领域中,模具加工是一个非常重要的环节。
模具的精度和质量直接决定了最终产品的质量和成本。
因此,模具加工及其改善方案是制造业中必不可少的一环。
在本文中,我们将介绍几种模具加工的常见问题,并探讨一些改善方案。
常见问题及其解决方案1. 模具加工精度不高模具加工精度不高是模具加工中常见的问题之一。
通常情况下,造成这个问题的原因有很多,比如模具材料、加工设备、操作技能等等。
下面我们将介绍一些解决方案。
1.1 优化模具材料模具材料是影响模具精度的重要因素之一。
在选择模具材料时,应充分考虑模具的复杂度、尺寸以及所需的精度等要求。
一般情况下,硬度高、材料强度好、变形小、腐蚀性低的材料是较为理想的选项。
常见的模具材料有:工具钢、硬质合金、精密合金、高速钢等。
1.2 优化加工设备在模具加工过程中,加工设备的精度和稳定性也非常重要。
一般来说,数字化控制数控机床是一个很好的解决方案。
这种机床能够根据制定的程序精确的加工模具。
另外,机床应该经常进行维护和保养,以确保其正常运转。
1.3 增强操作技能操作技能对于模具加工精度有很大的影响。
对于操作人员来说,应当接受专业的培训和指导,以便更好地操作加工设备和模具。
同时,操作人员也应该具备一定的材料知识和加工经验,能够理解和分析加工过程中的问题,制定合适的措施。
2. 模具使用寿命短模具使用寿命短,往往会导致模具加工成本增加,影响生产效率。
造成这个问题的原因有很多,例如模具材料、模具设计、模具维护等等。
下面我们将介绍一些解决方案。
2.1 优化模具材料选择适合的模具材料,是延长模具寿命的一个关键因素。
在选择模具材料时,应充分考虑模具所承受的压力、温度、摩擦力等等因素,选择适合的材料,并对模具进行定制化的加工。
2.2 优化模具设计在模具设计方面,应该充分考虑模具所需要承受的力和应力,并对模具结构进行相应的优化。
设计时,应该避免尖锐角度、薄壁边缘和过度细节等问题。
另外,应根据模具材料和加工过程等因素设计出合适的冷却系统。
模具加工工艺改善方案

模具加工工艺改善方案模具是制造业中常用的一种设备,主要是用于制作各种指定形状产品的硅胶模具和金属模具,以及各种塑料模具、橡胶模具等。
模具加工成为了一种重要的制造技术。
针对目前一些模具加工过程中存在的一些问题,本文提出了一些改善方案。
一. 提高模具加工精度模具加工的精度直接关系到最终的产品的质量,要想获得高精度的模具,需要从以下几个方面进行改善:•选择优质刀具:刀具是模具加工中起关键作用的一种设备,合理的选择刀具可以大大提升加工效率和精度。
•保证加工环境的洁净:加工环境中的杂质或者灰尘等微小颗粒都会对模具加工精度带来影响,因此需要保持加工环境的优美和洁净。
•配置高精度数控加工机床:数控加工技术在模具加工中应用广泛,合理选择高品质的数控加工机床可以大大提高加工精度。
二. 提高模具加工效率模具加工效率的提高可以更快地完成产品的加工,提前完成生产计划,减少生产成本。
以下是提高模具加工效率的一些方法:•优化加工方案:通过分析加工工艺,合理调整加工策略和流程,以减少加工时间,提高加工效率。
•提高加工速度:一些材料的加工速度比较慢,需要根据不同的材料,调整加工速度,以提高加工效率。
•限制加工干扰:对于一些加工中容易出现干扰的部位或者死角,需要采用相应的加工工艺,以避免加工干扰。
三. 降低模具加工成本模具加工成本的降低是企业持续发展的重要因素之一。
降低模具加工成本需要从以下几个方面入手:•合理降低材料成本:通过合理选择材料种类、批量采购等方式,将材料成本控制在一个较低的水平上。
•减少加工时间:在保证加工质量的基础上,缩短加工时间,降低人工和设备使用成本。
•优化工艺流程:对加工过程中的每一个环节进行优化,将加工流程简化,减少加工损耗和废品产生,降低成本。
四. 完善模具加工质量管理对于模具加工工艺,加强质量管理是非常重要的一环。
只有保证了质量,企业才能长期稳定发展。
以下是完善模具加工质量管理的具体措施:•强化质量意识:对企业员工加强质量意识培训,建立严谨的质量文化。
模具车间改善方案

模具车间改善方案背景模具车间是制造业中非常重要的一个环节。
它负责生产各种模具,以保障后续产品的生产。
然而,模具车间的管理和生产状况往往存在一些问题,如生产效率低、质量不稳定、设备老化等。
因此,为了提高生产效率和质量,本文将提出一些模具车间改善方案。
问题分析生产效率低模具车间生产效率低主要有以下原因:1.物料准备不充分当生产物料没有及时准备,或者准备不充分时,会影响生产进度,导致生产效率低。
2.流程不合理流程不合理也是造成生产效率低的原因之一。
比如,优化模具加工流程、改善人员作业流程等都能带来生产效率的提升。
3.设备老化设备老化也是导致生产效率低的原因之一。
设备老化不仅会导致设备效率低下,而且还会影响生产质量。
质量不稳定模具车间质量不稳定主要有以下原因:1.操作不规范操作不规范或误操作是导致质量不稳定的主要原因之一。
操作人员应该明确操作流程和规范操作程序,防止出现误操作。
2.设备老化设备老化不仅会导致生产效率低下,也会导致质量不稳定。
因此,及时更换老化设备是很必要的。
3.配件材料不匹配材料和配件不匹配会导致制造模具的质量不稳定,可能会影响后续产品的生产。
改善方案1.管理优化物料管理物料管理是模具车间管理中至关重要的一个环节。
为了增强物料管理,可以使用物料管理系统进行管理和追踪物料。
同时,可以增加物料储备,保证物料的充足性。
流程优化流程优化是提高生产效率的重要手段。
可以对模具加工流程进行优化,减少工艺流程环节,缩短生产周期。
2.设备改善选购先进设备选购先进设备不仅可以增强生产的效率,而且能更好地保证生产的质量。
选择性能更好的设备,能够减少设备老化带来的影响。
定期维护定期维护既能够避免设备故障产生,又可以延长设备的使用寿命,提高设备的稳定性。
3.操作规范化建立作业规程建立作业规程是非常重要的,能够引导操作人员规范操作,降低误操作率。
提高员工技能培训和提升员工的技能水平,能够提高员工的工作效率和素质,减少人为错误。
模具改善计划方案

模具改善计划方案背景模具是工业生产中必不可少的工具,它用于塑造各种材料,制造出零件和产品。
但是,不可避免地,模具也会存在磨损、变形、断裂等问题,这些问题将会给生产带来延误、降低生产效率等问题。
因此,及时对模具进行改善和修复显得尤为重要。
目的本文目的在于提出一种可行的模具改善计划方案,以提高模具的使用效率、延长其使用寿命及减少生产中可能出现的问题。
计划方案1. 改善保养制度制定适当的模具保养制度至关重要。
定期检查模具的磨损程度,清洁其表面,及时补充润滑油,以降低磨损和保护模具表面。
另外,还应安排专人进行模具的定期保养和检查。
2. 模具设计的改进模具设计的改进可以从以下几个方面进行:a. 提高材料的质量选用更好的模具材料,可以提高模具的强度和硬度,从根本上降低模具磨损的概率。
b. 优化模具结构优化模具的结构可以降低模具的磨损程度。
如添加一些防磨损零件、减小松动和更换容易磨损的零件等措施。
c. 加强模具的防腐蚀能力模具长期使用可能会受到环境的侵蚀,尤其是在潮湿的环境里容易生锈。
因此,加强模具的防腐蚀能力,对延长模具使用寿命有非常大的帮助。
3. 加强维修管理及时对模具进行维修及更换是保证模具长期使用的重要措施。
要根据模具的使用年限和实际情况,设定相应的检查和维修频率。
定期对模具进行全面维修,如拆除模具零部件,进行清洗、保养、检查磨损,更换损坏部件等,以保证模具在使用过程中的稳定性和精度。
结论通过以上几种改善措施,可以使模具使用寿命得到延长,降低了维修成本,并大大提高了产量,从而取得更好的经济效益。
因此,要制定好模具改善计划,注重模具维修管理的细节,以达到更好的生产效果。
模具改善方案怎么写
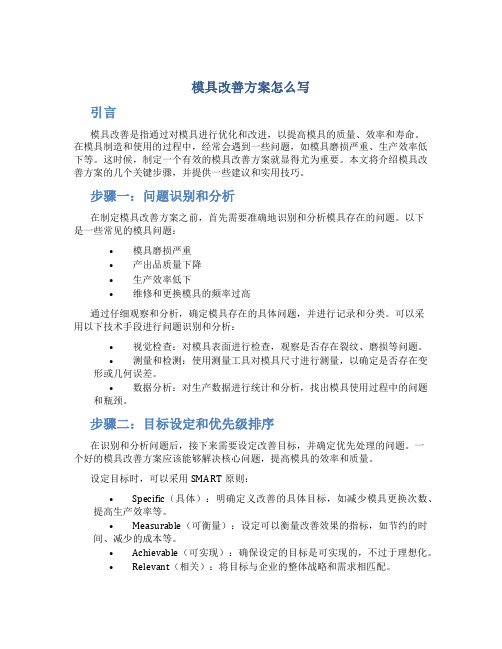
模具改善方案怎么写引言模具改善是指通过对模具进行优化和改进,以提高模具的质量、效率和寿命。
在模具制造和使用的过程中,经常会遇到一些问题,如模具磨损严重、生产效率低下等。
这时候,制定一个有效的模具改善方案就显得尤为重要。
本文将介绍模具改善方案的几个关键步骤,并提供一些建议和实用技巧。
步骤一:问题识别和分析在制定模具改善方案之前,首先需要准确地识别和分析模具存在的问题。
以下是一些常见的模具问题:•模具磨损严重•产出品质量下降•生产效率低下•维修和更换模具的频率过高通过仔细观察和分析,确定模具存在的具体问题,并进行记录和分类。
可以采用以下技术手段进行问题识别和分析:•视觉检查:对模具表面进行检查,观察是否存在裂纹、磨损等问题。
•测量和检测:使用测量工具对模具尺寸进行测量,以确定是否存在变形或几何误差。
•数据分析:对生产数据进行统计和分析,找出模具使用过程中的问题和瓶颈。
步骤二:目标设定和优先级排序在识别和分析问题后,接下来需要设定改善目标,并确定优先处理的问题。
一个好的模具改善方案应该能够解决核心问题,提高模具的效率和质量。
设定目标时,可以采用SMART原则:•Specific(具体):明确定义改善的具体目标,如减少模具更换次数、提高生产效率等。
•Measurable(可衡量):设定可以衡量改善效果的指标,如节约的时间、减少的成本等。
•Achievable(可实现):确保设定的目标是可实现的,不过于理想化。
•Relevant(相关):将目标与企业的整体战略和需求相匹配。
•Time-bound(有时间限制):设定一个明确的时间范围,使目标有明确的约束。
确定优先级时,可以根据问题的严重性、影响范围和可改善的效果等因素进行排序。
步骤三:寻找解决方案在设定目标之后,需要寻找适合的解决方案。
以下是几种常见的模具改善方案:•材料改进:选择更耐磨、耐腐蚀的材料,以延长模具的使用寿命。
•结构优化:通过对模具结构进行改进,提高模具的刚性和稳定性,减少变形和磨损。
模具改善报告怎么写
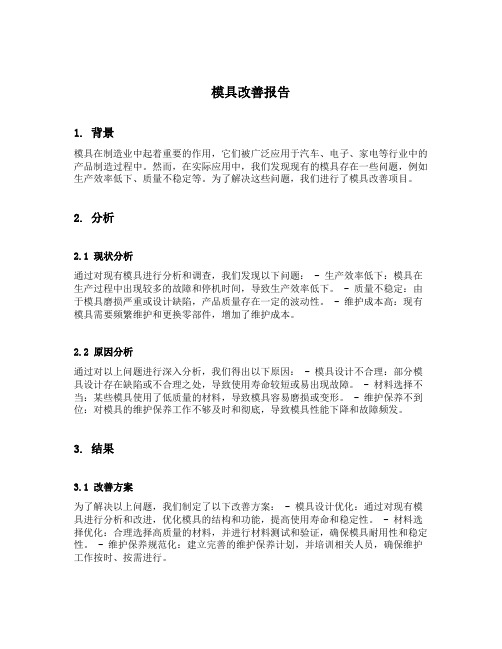
模具改善报告1. 背景模具在制造业中起着重要的作用,它们被广泛应用于汽车、电子、家电等行业中的产品制造过程中。
然而,在实际应用中,我们发现现有的模具存在一些问题,例如生产效率低下、质量不稳定等。
为了解决这些问题,我们进行了模具改善项目。
2. 分析2.1 现状分析通过对现有模具进行分析和调查,我们发现以下问题: - 生产效率低下:模具在生产过程中出现较多的故障和停机时间,导致生产效率低下。
- 质量不稳定:由于模具磨损严重或设计缺陷,产品质量存在一定的波动性。
- 维护成本高:现有模具需要频繁维护和更换零部件,增加了维护成本。
2.2 原因分析通过对以上问题进行深入分析,我们得出以下原因: - 模具设计不合理:部分模具设计存在缺陷或不合理之处,导致使用寿命较短或易出现故障。
- 材料选择不当:某些模具使用了低质量的材料,导致模具容易磨损或变形。
- 维护保养不到位:对模具的维护保养工作不够及时和彻底,导致模具性能下降和故障频发。
3. 结果3.1 改善方案为了解决以上问题,我们制定了以下改善方案: - 模具设计优化:通过对现有模具进行分析和改进,优化模具的结构和功能,提高使用寿命和稳定性。
- 材料选择优化:合理选择高质量的材料,并进行材料测试和验证,确保模具耐用性和稳定性。
- 维护保养规范化:建立完善的维护保养计划,并培训相关人员,确保维护工作按时、按需进行。
3.2 改善效果经过实施改善方案后,我们得到了以下改善效果: - 生产效率提升:故障率降低,停机时间减少,生产效率得到显著提升。
- 质量稳定性提高:通过优化设计和材料选择,产品质量波动性大幅降低。
- 维护成本降低:规范维护保养工作,减少维护次数和更换零部件的频率,降低了维护成本。
4. 建议为了进一步提高模具改善效果,我们提出以下建议: - 持续改进:对现有的改善方案进行持续评估和优化,以适应市场和技术的变化。
- 技术创新:关注新技术的发展趋势,引入先进的模具制造技术和设备,提升模具品质和生产效率。
模具溢料改善措施

模具溢料改善措施
模具溢料是指在注塑成型过程中,塑料熔体从模具的分型面或其他缝隙中溢出的现象。
以下是一些改善模具溢料的措施:
1. 调整注射参数:适当降低注射速度、注射压力和熔体温度,以减少熔体在模具中的流动速度和压力,降低溢料的风险。
2. 优化模具设计:检查模具的分型面、型腔和型芯的设计是否合理,确保其匹配良好,减少缝隙和间隙,防止熔体溢出。
3. 清洁模具:保持模具的清洁,定期清理分型面和模具缝隙中的杂质和污垢,以确保模具的密封性能。
4. 调整模具闭合力度:确保模具的闭合力度适当,过紧或过松都会导致溢料问题。
可以通过调整模具的锁紧装置或调整模具的合模高度来解决。
5. 使用排气系统:在模具中设置适当的排气系统,以排除熔体中的气体,减少气泡和局部高压区域,从而降低溢料的可能性。
6. 检查模具磨损:定期检查模具的磨损情况,特别是分型面和模具缝隙处的磨损情况。
如有必要,进行模具修复或更换磨损部件。
7. 选择合适的材料:根据产品要求和工艺条件,选择适合的塑料材料,一些材
料具有更好的流动性和低黏度,有助于减少溢料问题。
8. 培训操作人员:对操作人员进行培训,提高他们的技能水平和操作规范,以确保正确的注塑操作和模具维护。
通过以上措施的综合应用,可以有效改善模具溢料问题,提高注塑成型的质量和效率。
模具修理改善方案

模具修理改善方案背景模具是工业生产中常用的设备,用于制造各种零部件和产品。
模具在使用过程中,由于摩擦、磨损、腐蚀等原因,会出现各种问题,需要进行修理和改善。
本文将提供一些模具修理改善方案,旨在提高模具的使用寿命和效率。
修理前的准备在进行模具修理之前,需要进行一些准备工作。
1.审查模具问题,确定需要进行哪些修理措施。
2.准备好必要的工具和材料。
3.确保修理工作场所干净整洁,以避免杂物和灰尘对模具造成二次污染。
4.穿戴好防护装备,如手套、防护服、护目镜等。
修理改善方案磨损修理模具在长期使用过程中会出现各种程度的磨损,从轻微划痕到严重磨损都有可能。
磨损会导致模具精度下降,加工品质变差,甚至严重影响产品的使用寿命。
以下是一些磨损修理的建议:•轻微划痕:使用砂纸或磨具修复。
•表面磨损:利用加工设备重新打磨表面。
•深刻磨损:采用电火花加工、等离子喷涂等技术进行修复。
腐蚀修理模具在长时间存放或使用过程中可能会受到酸、碱、氧化等化学腐蚀,导致表面产生腐蚀痕迹甚至损毁模具。
以下是一些腐蚀修理的建议:•表面轻微腐蚀:用磨具打磨表面,涂上防腐涂料。
•表面严重腐蚀:采用冷却剂、机械除锈等方式进行清洗,再进行表面打磨、喷涂防腐涂料。
•深层腐蚀:采用金属纤维激光、等离子欧姆增材制造等技术进行修复。
空气孔修补模具在制造过程中需要设置空气孔,以使气体能够顺畅地流过并减少铝及镁合金的气泡。
在长期使用中,由于各种原因(如腐蚀、摩擦等),空气孔可能会堵塞或失效,导致产品质量下降。
以下是一些空气孔修补建议:•使用专门的钻头将被堵住的孔钻通。
•使用新的模具修复,重新开孔。
模具优化除了修理和更换损坏的部件外,我们还可以尝试进行模具优化。
模具的优化可以提高模具制造精度、提高产品质量、减少生产成本等。
以下是一些模具优化的建议:•合理的模具结构布局,根据使用需求设计适合的空气孔和排气槽等。
•采用模拟分析工具对模具进行优化分析,以预测模具性能并提前发现潜在问题。
- 1、下载文档前请自行甄别文档内容的完整性,平台不提供额外的编辑、内容补充、找答案等附加服务。
- 2、"仅部分预览"的文档,不可在线预览部分如存在完整性等问题,可反馈申请退款(可完整预览的文档不适用该条件!)。
- 3、如文档侵犯您的权益,请联系客服反馈,我们会尽快为您处理(人工客服工作时间:9:00-18:30)。
建議事項
2.沖床課目前以單手按鍵操作.單手用鉗子夾板.此一 作業方式.非常危險.且紅外線作用.似乎調得過高 或過低.導致手拿鉗子.還可越過電眼作業.現場幹 部卻無視此一危險舉動! 建議(此建議曾與現場幹部溝通.但無法達成共識) 恢復同時按兩個鍵.才能作動沖床.另外將電眼重新 設定高度.確保能有效的發揮功用! (此一改變雖會短暫影響產能.但工安問題.不得不重 視;另一問題.就針對沖床作業時.會遇到大排板.導 致無法平擺於模具上作業.故才使用鉗子固定.此一 做法.可使用可調整式的支撐架.改善此一現象!
模具問題改善與製程建議
報告人:熊 大 仁 2008.4月
現況分析
1.目前模具的拆/組.簡易維修.研磨等.皆由製造部作 業;另入庫管理.發外送修則由資材主導作業;多頭 馬車之故.模具相關作業.則易出現灰色地帶! 2.目前模具內修.分別日/夜各一員.均未受過正統模 具拆/組.研磨之訓練.且無保養的觀念;此外.模具使 用次數.權由資材統計.而現場作業員及幹部.都無 法馬上了解作業模具的使用壽命;之故.易導致模具 維修時或組裝時.因模板不平整.而受損.壽命減短. 且無法在第一時間做好預防的工作! 3.沖床作業人員對品質的觀念薄弱.依賴性高.工安意 識低! 4.模具的拆/組.均以手動作業.效率性差!
改善問題的三大層面
1.從組織面著手:獨立為組.專責模具.納編為沖 床課管理! 2.從技術面著手:建立基本操作模式 3.教育訓練著手:提升人員專業素質.重新建立 品質觀念及工安觀念!
一.從組織面著手
建檔及入庫 A.組織現況: (隸屬於資材) 研磨/維修/架模 (隸屬於製造) 發外模具跟催 (隸屬於資材生管)
建議事項
5.每批首次量產的品號.可於正式投量產前(例 如:此訂單為1000PNL).生管可提前1~2天先 行投產18PNL試跑生產線.若於各製程發現 異常時.可將損失降至最低! P.S樣品與量產 有時會改排板數.故製程條件亦不能延用!! 建議 請生管於安排排程時.納入考量.倘若製程條 件不同時.有利於內部生技有緩衝的時間找 出問題或重抓條件.才不至於延遲交期!
建議事項
3.目前拆/組模具.皆使用手動旋開/鎖緊.造成 很多不必要的工時浪費! 建議 於維修工作台.使用角鐵做成一個ㄇ字型.固 定於兩端.再從左上方的空氣接頭處.拉出兩 個供應口.可供應兩條氣動槍(Air Gun).並將 氣動槍置於ㄇ字型上方.於拆/組模具時.將大 大提高拆/組模速度!
建議事項
4.模具維修目前統計:日/夜班最頻繁且高居第一位的現象 斷 針! 分析造成斷針的現象.有下列幾種可能性:a.孔塞(現場幹部因 依賴沖床作業後.尚有一道通孔檢驗.故對作業中已經孔塞 的模具.仍然照沖不誤)若長期孔塞不加以清除退屑孔中的 廢料.易使孔徑變大.靠近模邊的退屑孔.甚至引起崩模現 象!.b.維修人員為了挽救曝偏的孔位.刻意將沖針的直徑縮 小(如1m/m改成0.95 or 0.9m/m)如此造成沖針與原本的孔 徑不符.於沖床200t/160t強大的作動下.與板材互動後.易產 生斷裂.c.沖針壽命到期! 建議 加強幹部重新對品質的重視及對模具基本常識與日常保養的 認知!
建議事項
1.沖床課作業用之鼓風機.其功效只能將部分 粉塵及板邊廢料吹離.但真正附著於模具上. 下板的顆粒廢料.卻無法有效的吹走.故打.壓 痕仍持續地增加公司成本! 建議: 改採用腳踏方式的空氣吹嘴.可固定於模具旁 邊.上.下模皆使用此近距離吹嘴;另將雞毛袒 子改用短毛刷.並於50次自檢時.使用酒精 (清潔劑)擦拭上.下模板!
模具組維修簡易流程圖
開出領模單 沖床模具故障 開出送修單 判定由廠內/廠外維修
廠內
拆模
更換維修/研磨
簡易保養
組裝
記錄/建檔
入庫/現場
廠外
重啟/更換全沖針
入廠
品保量測/試沖驗收
記錄/建檔
入庫/現場
二.從技術面著手
1.建立模具管制表:表單隨模具走.沖型次數由沖床作業員作業 完後.填寫次數再由治具組統計.並登錄於電腦(防止管制卡 遺失);另達2萬punch時.則由治具課負責保養.無論維修或 研磨.都必須將原因及問題點紀錄於管制卡上.並做備份! 2.建立模具於每次入庫前保養:必需清除退屑孔中的廢料.再上 薄油(WD-4潤滑油)=>擦拭(看的到摸不著)=>入庫! 3.架模深度的斷取:架模人員不能延續上一模具的深度做基礎. 需視實際模具高度.重新將沖床高度升高.再做微調升降.每 次調整以1~2格做微調.至適當深度時.再先以紙張做第一次 試沖.並從紙張上了解模具刀鋒狀況;另當上.下模處於分開 狀態時.機台務必設定為寸動.且速度需降慢.才不至於傷到 導柱跟導套;若不小心傷到.嚴重時.需整套模具報廢! 4.每年兩次針對沖床做水平校正.分上.下半年度.各一次! 5.針對治具課的維修人員.先進行專業培訓.進而要求維修速度!
三.從教育訓練著手
1.模具維修人員:需至模具廠實際操作.拆/組裝與研磨.換沖針. 以及了解模具的形成與結構.受訓時間:約2~3個月.日/夜班 各一員種子(穩定性高的人員.組長可優先考慮).另未經(模 具廠或種子教官)受訓之人員.則不許私下拆/組裝模具! 2.加強沖床現場作業人員及幹部對SIP的認識與判定.勿過度 依賴品保單位的巡檢人員以及通孔檢驗程序;並於作業前. 現場幹部務必要求.檢視沖床電眼.是否故障或忘記開啟.加 強工安意識! 3.建立50punch做自主檢查(建議加裝蜂鳴器).(無論單.雙面板. 均需做正反兩面檢查.清潔上.下玉).發現異狀時.則立即停 工.反應給組.課長.同時請模具人員進行維修! 4.首件改由現場自行檢驗.幹部審核.(核對留底樣板即可.除首 次量產交由品保審核)方能有效的.在第一時間.立即掌控品 質問題!
B.組織異動後:
研模/維修/保養/建檔及入庫/發外跟催 (隸屬於製造部沖床課模具組)
p.S更改組織結構.並非增加一組站.只是將現 有單位及人員獨立出來.專責模具項目!
沖床課組織圖
課 長
沖床組長/白班
模具組長/白班
沖床組長/夜班
領班
領班
領班/白
領班/夜(歸夜班沖床組長管)
領班
領班
初擬:(維修人員x4).(倉管人員x2).(發外跟催/規格確 認x1)