炼厂蒸汽系统优化技术应用
炼油厂应用热管式蒸汽发生器

余热回收工程一、锅炉烟气余热回收简介:工业燃油、燃气、燃煤锅炉设计制造时,为了防止锅炉尾部受热面腐蚀和堵灰,标准状态排烟温度一般不低于180℃,最高可达250℃,高温烟气排放不但造成大量热能浪费,同时也污染环境。
热管余热回收器可将烟气热量回收,回收的热量根据需要加热水用作锅炉补水和生活用水,或加热空气用作锅炉助燃风或干燥物料。
节省燃料费用,降低生产成本,减少废气排放,节能环保一举两得。
改造投资3-10个回收,经济效益显著。
(一)气—气式热管换热器(1)热管空气预热器系列应用场合:从烟气中吸收余热,加热助燃空气,以降低燃料消耗,改善燃烧工况,从而达到节能的目的;也可从烟气中吸收余热,用于加热其他气体介质如煤气等。
设备优点:*因为属气/气换热,两侧皆用翅片管,传热效率高,为普通空预器的5-8倍;*因为烟气在管外换热,有利于除灰;*因每支热管都是独立的传热元件,拆卸方便,且允许自由膨胀;*通过设计,可调节壁温,有利于避开露点腐蚀结构型式:有两种常用的结构型式,即:热管垂直放置型,烟气和空气反向水平流动,见图1;热管倾斜放置型,烟气和空气反向垂直上下流动,见图2。
(二)气—液式热管换热器应用场合:从烟气中吸收热量,用来加热给水,被加热后的水可以返回锅炉(作为省煤器),也可单独使用(作为热水器),从而提高能源利用率,达到节能的目的。
设备优点:*烟气侧为翅片管,水侧为光管,传热效率高;*通过合理设计,可提高壁温,避开露点腐蚀;*可有效防止因管壁损坏而造成冷热流体的掺混;结构型式:根据水侧加热方式的不同,有两种常用的结构型式:水箱整体加热式(多采用热管立式放置)和水套对流加热式(多采用热管倾斜放置),如图3所示(三)气—汽式热管换热器应用场合:应用热管作为传热元件,吸收较高温度的烟气余热用来产生蒸汽,所产生的蒸汽可以并倂入蒸汽管网(需达到管网压力),也可用于发电(汽量较大且热源稳定)或其他目的。
对钢厂,石化厂及工业窑炉而言,这是一种最受欢迎的余热利用形式。
管网模拟技术在蒸汽系统优化上的应用
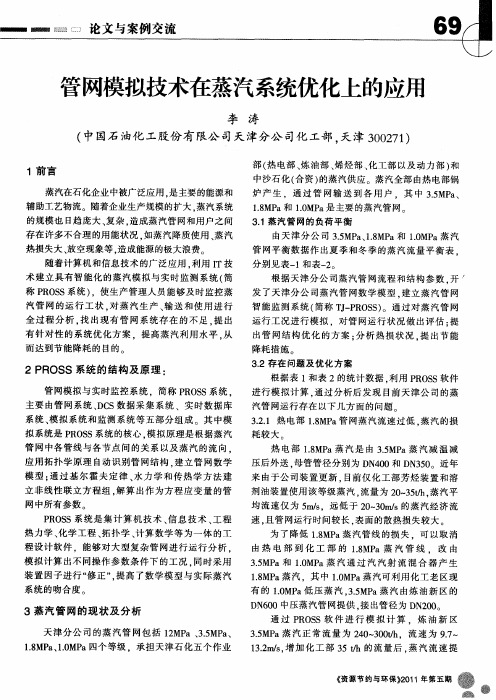
6 # 9
/
管网模拟技术在蒸汽系统优化上的应用
李 涛
( 中国石油化 工股份有 限公 司天津分公 司化工部 , 天津 3 07 ) 02 1
1前 言
蒸汽 在石化企业 中被广泛应用 . 主要 的能 源和 是
部 ( 电部 、 热 炼油 部 、 烃部 、 工 部 以及 动 力部 ) 烯 化 和 中沙石 化 ( 资 ) 合 的蒸 汽供应 。蒸汽 全部 由热 电部锅
炉 产 生 ,通 过 管 网输 送 到 各 用 户 ,其 中 3 MP 、 . a 5
辅 助工艺物流 。随着企业生产 规模 的扩 大 . 蒸汽 系统 的规 模也 日趋庞 大 、 复杂 , 造成 蒸汽 管 网和用 户之 间 存在 许多 不合理 的用 能状 况 , 蒸汽 降质 使用 、 汽 如 蒸 热损失 大 、 放空现象等 , 造成能源 的极 大浪费
出管 网结 构 优 化 的方 案 ; 析 热损 状 况 , 出节 能 分 提
降耗措 施
32存在 问题 及优 化 方案 .
2P OS 系统 的 结构 及 原 理 : R S
管 网模 拟与 实时监 控 系统 ,简 称 P O S系统 . R S 主 要 由管 网系统 、 C D S数 据 采 集 系统 、实 时数 据 库 系 统 、 拟系 统 和监 测 系统 等 五部 分组 成 其 中模 模
拟 系统是 P O S系统 的核心 . 拟原 理是 根 据蒸 汽 R S 模
根 据表 1 和表 2的统 计数 据 . 利用 P O S软件 RS 进 行模 拟 计算 , 过分 析后 发 现 目前 天 津公 司的蒸 通 汽 管 网运行存 在 以下几 方 面的 问题
321 热 电部 1 MP .. . a管 网蒸 汽 流速 过低 . 汽 的损 8 蒸 耗较 大 。 热 电 部 1 MP . a蒸 汽 是 由 35 a蒸 汽 减 温 减 8 . MP
浅析石化装置蒸汽管网的优化和节能技术
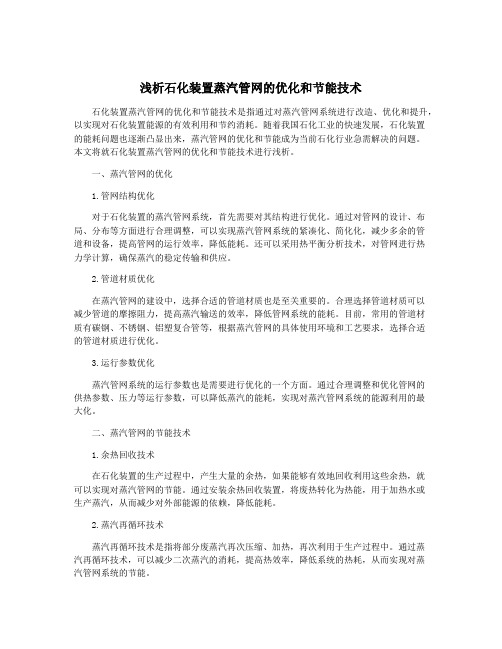
浅析石化装置蒸汽管网的优化和节能技术石化装置蒸汽管网的优化和节能技术是指通过对蒸汽管网系统进行改造、优化和提升,以实现对石化装置能源的有效利用和节约消耗。
随着我国石化工业的快速发展,石化装置的能耗问题也逐渐凸显出来,蒸汽管网的优化和节能成为当前石化行业急需解决的问题。
本文将就石化装置蒸汽管网的优化和节能技术进行浅析。
一、蒸汽管网的优化1.管网结构优化对于石化装置的蒸汽管网系统,首先需要对其结构进行优化。
通过对管网的设计、布局、分布等方面进行合理调整,可以实现蒸汽管网系统的紧凑化、简化化,减少多余的管道和设备,提高管网的运行效率,降低能耗。
还可以采用热平衡分析技术,对管网进行热力学计算,确保蒸汽的稳定传输和供应。
2.管道材质优化在蒸汽管网的建设中,选择合适的管道材质也是至关重要的。
合理选择管道材质可以减少管道的摩擦阻力,提高蒸汽输送的效率,降低管网系统的能耗。
目前,常用的管道材质有碳钢、不锈钢、铝塑复合管等,根据蒸汽管网的具体使用环境和工艺要求,选择合适的管道材质进行优化。
3.运行参数优化蒸汽管网系统的运行参数也是需要进行优化的一个方面。
通过合理调整和优化管网的供热参数、压力等运行参数,可以降低蒸汽的能耗,实现对蒸汽管网系统的能源利用的最大化。
二、蒸汽管网的节能技术1.余热回收技术在石化装置的生产过程中,产生大量的余热,如果能够有效地回收利用这些余热,就可以实现对蒸汽管网的节能。
通过安装余热回收装置,将废热转化为热能,用于加热水或生产蒸汽,从而减少对外部能源的依赖,降低能耗。
2.蒸汽再循环技术蒸汽再循环技术是指将部分废蒸汽再次压缩、加热,再次利用于生产过程中。
通过蒸汽再循环技术,可以减少二次蒸汽的消耗,提高热效率,降低系统的热耗,从而实现对蒸汽管网系统的节能。
3.管道绝热技术管道绝热是一种有效的节能措施,可以减少管道传热损失,提高管网系统的热效率。
通过采用优质的绝热材料对管道进行绝热处理,可以降低热损失,减少供热能力,实现对管网的节能。
炼油生产过程能量系统优化实施指南
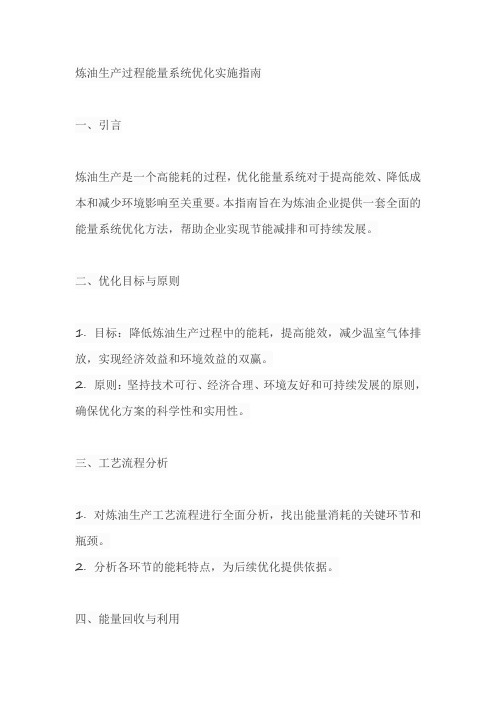
炼油生产过程能量系统优化实施指南一、引言炼油生产是一个高能耗的过程,优化能量系统对于提高能效、降低成本和减少环境影响至关重要。
本指南旨在为炼油企业提供一套全面的能量系统优化方法,帮助企业实现节能减排和可持续发展。
二、优化目标与原则1. 目标:降低炼油生产过程中的能耗,提高能效,减少温室气体排放,实现经济效益和环境效益的双赢。
2. 原则:坚持技术可行、经济合理、环境友好和可持续发展的原则,确保优化方案的科学性和实用性。
三、工艺流程分析1. 对炼油生产工艺流程进行全面分析,找出能量消耗的关键环节和瓶颈。
2. 分析各环节的能耗特点,为后续优化提供依据。
四、能量回收与利用1. 针对各环节的热量输出,采取有效的回收措施,提高能量的利用率。
2. 优化蒸汽系统,减少蒸汽的消耗和损失。
3. 实施余热回收,将余热用于加热、工艺或发电等用途。
五、热能整合与改进1. 对各工艺环节的热能需求进行整合,实现热能共享。
2. 改进换热器等设备,提高传热效率。
3. 优化热力系统,降低不必要的热量损失。
六、节能技术应用1. 采用先进的节能技术和设备,如高效电动机、变频器等。
2. 应用智能控制技术,实现能源的优化调度和精细管理。
3. 实施能源审计和管理体系,强化能源管理意识和能力。
七、系统集成与优化1. 将各工艺环节的能量系统集成起来,进行整体优化。
2. 优化物料平衡和能量平衡,提高系统运行效率。
3. 引入仿真技术,对能量系统进行模拟和优化。
八、实施计划与监控1. 制定详细的实施计划,明确各阶段的任务和目标。
2. 对实施过程进行严格监控,确保优化方案的有效执行。
3. 建立数据监测与采集系统,实时掌握能源消耗和优化效果。
九、经济效益评估1. 对优化方案进行经济效益评估,分析投资回报率等指标。
2. 对比优化前后的能耗数据,计算节能减排的经济效益。
3. 综合评估环境和社会效益,为企业决策提供依据。
十、持续改进与建议1. 对优化过程中遇到的问题进行总结分析,不断改进和完善方案。
炼厂优化加工的思路和对策

34炼厂优化加工的思路和对策郑文刚(中国石油化工集团公司炼油事业部,北京100728)收稿日期:2018–06–09。
作者简介:郑文刚,硕士,高级工程师,1998年毕业于浙江大学化学工程专业,长期从事炼油总流程优化、加工过程模拟与优化工作,曾获中国石化突出贡献专家,中国石化科技进步二等奖。
摘 要:优化是炼油提高盈利能力,增强竞争力的有力手段。
本文讨论了当前炼厂在原油采购、石脑油和重油加工、柴汽比、氢气平衡、燃料平衡、蒸汽动力系统等方面面临的主要问题。
在此基础上,提出了原油和氢气降本、石脑油和重油增效、柴汽比结构优化、燃料和蒸汽动力系统全局优化等方面的思路和对策。
关键词:炼厂优化 原油加工 重油加工 柴汽比 氢气优化 燃料和蒸汽动力系统目前,我国炼油行业经过快速发展,面临产能过剩,柴油消费见顶,市场竞争剧烈的局面。
同时,产品质量升级步伐加快、节能环保要求日趋严格,炼厂只有综合运用各种优化手段,挖潜增效,才能提高竞争能力。
1 炼厂生产过程中存在的主要问题目前,不同炼厂在生产过程中存在的问题不同,综合大部分炼厂情况,共性问题如下。
1.1 原油性质波动大,不利于装置稳定、优化运行大部分炼厂缺乏原油调合设施,由于原油品种多,且到厂不均匀,造成原油性质波动大,对长周期稳定和优化运行不利。
1.2 加工高含硫原油存在瓶颈部分炼厂由于设备材质未升级,常减压、催化裂化硫含量设防值低,造成原油选择困难,炼厂不得不采购低硫中间基调和高含硫中间基、环烷基原油,导致原油成本偏高。
部分低硫渣油进延迟焦化或渣油加氢加工,降低了炼厂的效益。
1.3 重油加工不优化由于满足渣油加氢进料要求的原油可选范围有限,在生产实际中,为了保证装置长周期运行,掺渣率往往低于设计值,造成部分渣油进焦化,损失效益。
和渣油加氢配套的重油催化生产运行方案不优化,造成催化剂金属污染失活、水热失活严重,产品分布不理想。
大部分常减压装置都没有达到减压深拔的标准,导致延迟焦化进料残炭约20%,减压渣油TBP 切割点只有540~545℃,重蜡油进延迟焦化生焦,损失效益。
炼厂能量系统优化过程简介

炼厂能量系统优化过程简介[摘要]上一部分介绍了炼厂能量系统优化方法,这部分介绍能量系统优化过程。
一、合理利用能量的基本原则二、炼油工艺过程简介三、炼厂能量系统优化过程一、合理利用能量的基本原则炼厂的工艺过程都使用能量,合理用能的原则实质是按照能源的品质来使用,按照用户所需要的数量和能量品质等级供给能量,能尽其用。
简单说就是用的准、用的好、用的省,而不是无原则地少用和不用,集中于“优用”。
1.能量的有效利用节能和有效用能实质就是要减少能量的降级使用而造成的能量损失。
所有的炼油工艺过程都是在一定的热力学能势差(温度差、压力差、电势差和化学能势差)推动下进行,无推动力显然是无法推动过程进行的。
由于任何热力学能势差都会导致使用后的能量降级,所以有效利用能量的关键,就是在技术及经济条件许可的前提下,采取一切可能的措施,减少能量降级的发生,做到能量的合理有效利用。
(1)按需按质用能。
就是根据用能设备对需求的能级要求,选择适当的能级供给能量,按照输入的能级确定其使用范围。
按需按质的核心都是要避免能量品质的无谓降级,实现能级匹配合理。
(2)能量的逐级多次利用。
炼油工艺过程中使用的能源主要是电力和化石燃料这种高能级能源。
为了防止能量的浪费,应根据用能设备对输入能的不同能级要求,使能量的能级合理匹配逐次下降,对能量进行有效的、多次、多效、梯级使用。
(3)优化热能推动力。
如果以增加热能推动力来强化传热过程,是可以减少设备投资,但是却造成了能量降级大,增加了运行费用。
比如,增大传热温差,可以强化传热速率,减小换热面积,降低了设备投资费用,但却导致传热佣损失增加。
各种工艺过程的能量有效利用都要经过技术经济分析对比,决定最经济合理的热能推动力。
其实,能量的充分利用就是要减少排弃损失。
虽然各种工艺过程有些排弃的能量品质不高,但它们都是由投入系统的高等级能量使用后降级来的,这些用能过程。
蒸汽动力系统运行优化软件的工业应用
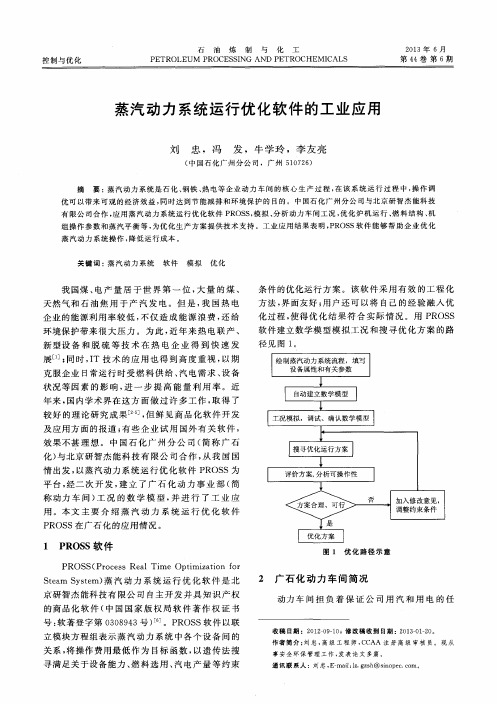
立模 块方 程组 表示 蒸 汽 动 力 系统 中各 个 设 备 间 的
收稿 日期 :2 0 1 2 — 0 9 — 1 0 ;修 改 稿 收 到 日期 :2 0 1 3 - 0 1 — 2 0 。
作者简介 : 刘忠, 高 级工程 师, C C AA 注 册 高 级 审 核 员 。现 从
事 安全 环保 管理 工 作 , 发 表 论 文 多篇 。
1 P R O S S软 件
PR O S S( Pr o c e s s Re a l Ti me O pt i mi z a t i o n f o r
图 1 优 化 路 径 示 意
S t e a m S y s t e m) 蒸 汽 动 力 系 统 运 行 优 化 软 件 是 北
( 中 国 石 化 广 州 分 公 司 ,广 州 5 ] 0 7 2 6 )
摘
要: 蒸汽动力系统是石化 、 钢铁 、 热 电等 企 业 动 力 车 间 的 核 心 生 产 过 程 , 在该 系统运 行过程 中 , 操 作 调
优 可 以带 来 可 观 的 经济 效 益 , 同时 达 到 节 能 减 排 和环 境 保 护 的 目的 。中 国石 化 广 州分 公 司 与北 京研 智杰 能科 技 有 限公 司合 作 , 应 用 蒸 汽 动 力 系统 运 行 优 化 软件 P R OS S , 模拟 、 分 析动力车间工况 , 优化 炉机运行 、 燃料结构 、 机 组 操 作 参 数 和蒸 汽 平衡 等 , 为 优 化 生 产 方 案 提 供 技 术 支 持 。工 业应 用 结 果 表 明 , P R O S S软 件 能 够 帮 助 企 业 优 化 蒸 汽 动力 系 统 操 作 , 降低 运 行 成 本 。
径见 图 1 。
全厂蒸汽动力系统运行优化
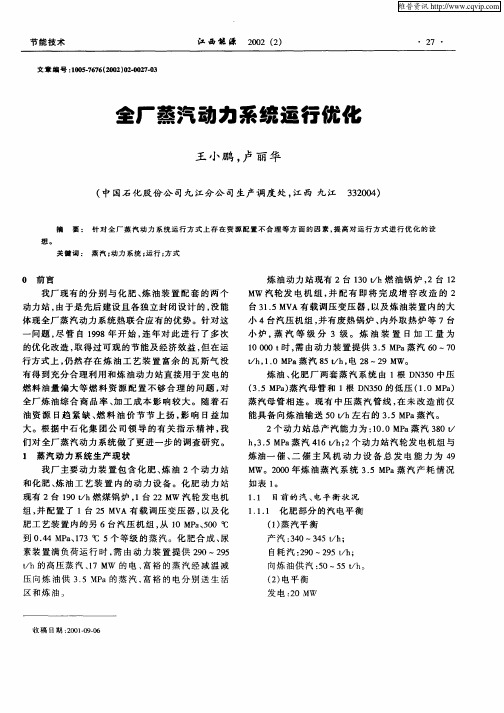
的 优 化 改 造 , 得 过 可 观 的 节 能 及 经 济 效 益 , 在 运 取 但 行 方 式 上 , 然 存 在 炼 油 工 艺 装 置 富 余 的 瓦 斯 气 没 仍 有 得 到 充 分 合 理 利 用 和 炼 油 动 力 站 直 接 用 于 发 电 的 燃料油量偏大 等燃料 资 源配 置不 够合理 的 问题 , 对 全 厂 炼 油 综 合 商 品 率 、 工 成 本 影 响 较 大 。随 着 石 加 油 资 源 日趋 紧 缺 、 料 油 价 节 节 上 扬 , 响 日益 加 燃 影 大 。根 据 中石 化 集 团 公 司 领 导 的 有 关 指 示 精 神 , 我
我 厂 现 有 的分 别 与 化 肥 、 油 装 置 配 套 的 两 个 炼 动 力 站 , 于 是 先 后 建 设 且 各 独 立 封 闭 设 计 的 , 能 由 没 体 现 全 厂 蒸 汽 动 力 系统 热 联 合 应 有 的 优 势 。 针对 这
一
小 4台汽 压 机 组 , 有 废 热 锅 炉 、 并 内外 取 热 炉 等 7台 小 炉 , 汽 等 级 分 3级 。 炼 油 装 置 日加 工 量 为 蒸
th的高 压 蒸 汽 、7 M 的 电 、 裕 的蒸 汽 经 减 温 减 / 1 W 富 压 向 炼 油 供 3 5 MP . a的 蒸 汽 , 裕 的 电 分 别 送 生 活 富
区和 炼 油
收稿 日期 :O 10 —6 2 O .90
维普资讯
炼 油 、 肥 厂 两 套 蒸 汽 系 统 由 1根 D 30中压 化 N5
( . a 蒸 汽 母 管 和 1 D 3 0的 低 压 ( . a 3 5 MP ) 根 N5 10 MP )
蒸 汽 母 管相 连 。 现 有 中 压 蒸 汽 管 线 , 未 改 造 前 仅 在
- 1、下载文档前请自行甄别文档内容的完整性,平台不提供额外的编辑、内容补充、找答案等附加服务。
- 2、"仅部分预览"的文档,不可在线预览部分如存在完整性等问题,可反馈申请退款(可完整预览的文档不适用该条件!)。
- 3、如文档侵犯您的权益,请联系客服反馈,我们会尽快为您处理(人工客服工作时间:9:00-18:30)。
炼厂蒸汽系统优化技术应用
作者:周卫锋赵士昌
来源:《科学与财富》2017年第35期
摘要:节约蒸汽,是炼厂节能的重点,从大的方向调整优化是见效最快的方式,某炼厂由于公用配套与炼油能力不相匹配,是该厂能耗高的主要原因,通过利用模型对全厂蒸汽系统优化,改造蒸汽流向、去除不必要的管线、专线消除瓶颈等措施,使该厂达到了系统节能的目的,经济效益617万元。
关键词:蒸汽;模型;优化;运行
某中石化炼厂是以加工胜利油田纯梁和现河混合原油为主的220万吨/年规模炼厂。
该厂公用工程、辅助设施系统本是为550万吨/年加工能力所配套,但是由于历史的原因,加工规模没有达到设计值,所以造成了能耗高,布局不合理等问题,2015年4月,该厂与石化盈科合作,采用英国PIL公司蒸汽动力系统离线优化软件Site-int,设计蒸汽动力系统的优化运行方案,2015年9月对蒸汽动力系统进行优化调度和量化管理,通过模型测算预计年经济效益580万,在2016年4月至6月经过实施改造,通过10个月的观察与计算,达到了预期经济效益。
1.改造前蒸汽系统介绍
该厂有两套动力系统,分别为一动力(动力东锅炉)和二动力(动力西锅炉),两个动力站相隔2000米,向全厂提供生产过程所需的中、低压蒸汽和高、低压除盐水。
一动力站于1990年建成,有3台DG35/39-9型中温中压燃油燃气锅炉,单台额定蒸发35t/h,总产汽能力105t/h;配2台3MW B3-35/10的背压式汽轮发电机组,两台75t/h除氧器;换热站有两台汽水换热器和一台U型换热器,负责老区冬季供暖。
二动力设备配置为:2台额定蒸发量为60t/h 的水煤浆流化悬浮高效洁净燃烧锅炉,配1台C12-3.43/0.981-Ⅵ型12MW 的抽汽凝汽式汽轮发电机组。
该厂有三个压力等级管网,分别为3.5MPa中压蒸汽、1.0MPa低压蒸汽和0.4MPa低低压蒸汽。
由于该厂是由加工能力100万吨/年逐步扩建改造至220万吨/年,蒸汽系统没有进行相应的优化和改造,造成了全厂蒸汽的设备、管线整体布局不合理、蒸汽系统调节手段缺少、蒸汽管网维护和运行存在困难等诸多问题,导致很多装置汽耗率比设计值高,全厂的能耗指标高。
蒸汽管网的供汽量和用汽量的计量相差很大。
蒸汽系统整体运行效率低、运行成本高,经济效益差。
全厂提供蒸汽的装置主要有两处,动力西锅炉和重催的CO余热锅炉。
2015年冬季动力水煤浆锅炉在26吨/时左右,重催锅炉约89吨/时左右,(夏季动力锅炉不运行)为全厂提供
3.5MPa蒸汽,重催所产3.5MPa蒸汽一方面为气压机提供蒸汽动力,其余与动力的3.5MPa蒸汽送往管网,经过由125线、219线送到1.5公里外地东锅炉汽轮发电机和加氢循环氢机,其余中压蒸汽用于焦化气压机的汽轮机。
2.蒸汽系统的优化
2015年初,该厂与石化盈科合作,通过前期调研,设计优化方案、实施等,利用Site-int 软件进行计算与评估。
2015年9月完成了Site-int系统初步建模,2015年10月~11月,根据蒸汽动力系统运行情况制定了不同运行方案,包括汽轮机移机方案、中压蒸汽管网停用方案、低压蒸汽管网降压操作方案,凝结水热量回收方案和蒸汽动力系统优化方案等。
2016年4月-6月对蒸汽系统进行了实施优化。
2.1
3.5MPa蒸汽的优化
由于西锅炉的水煤浆炉(60t/h)产汽后送往东锅炉3MW机组背压发电,背压后的低压汽再由一动力厂送出供全厂。
中压蒸汽供汽管线长度超过1150m,两条管线125线与219线双线运行,主要是给东锅炉的汽轮发电机、减温减压器、加氢循环氢机供蒸汽,但是由于双线运行,管线保温不佳,温降与压降都很大(60℃与0.6MPa),而且加氢循环氢机与汽轮机调整时双方相互抢量,造成蒸汽压力不稳,对设备运行造成影响,因此造成很大的能量损失。
由于加氢循环氢机不需要太大的蒸汽流量,因此停用了219线,现停用后,125线变为加氢专线,为加氢循环氢压机平稳运行提供了条件。
关闭219线后,与双线同时运行相比,热量损失减少约1875MJ/h,折合蒸汽0.81t/h,年经济效益66.7万元。
2.2 1.0MPa蒸汽的优化
1.0MPa蒸汽低压管网原来有两条管线在运行,1#线、2#线运行,2#线主要是为生产装置运行,1#线是主要是伴热或者不重要装置使用,存在管线长、蒸汽用量小、流速低、凝结水多的问题。
由于低压管网产汽点呈东西两侧分布,东部的一动力、加氢装置的产汽与西部的重催、焦化、柴油加氢的产汽,除了供附近的装置外,还一起往中心的用户(新硫磺、焦化、常减压)使用,蒸汽在管网流动过程中形成对峙,对峙的管线蒸汽流动方向常发生变化,流速低,易结水,所以中心用户的蒸汽有很大的波动。
2.2.1消除瓶颈,降低管网运行压力
一是消除常减压车间瓶颈,减压塔抽真空蒸汽对压力存在着压力要求,不能低于0.9公斤,我们利用热泵,将3.5MPa蒸汽引入常减压装置,与较低的1.0MPa合进,提高抽真空蒸汽的压力。
二是消除酸水汽提瓶颈,硫磺车间的酸水汽提装置对1.0MPa蒸汽压力有要求,否则酸水就会不合格,经调研,焦化距离硫磺较近(仅有800米的距离),因此利用焦化的气压
机的背压蒸汽做为酸水汽提的专用蒸汽,酸水汽提用不了,可以回到全厂蒸汽管网。
由于其余使用1.0MPa蒸汽的装置对蒸汽品质要求不高,于是降低运行压力由原来的0.9MPA降为现在的0.70MPa。
低压蒸汽管网运行压力降低后,可多回收蒸汽做功冬季约694kW.h/h,夏季约417kW.h/h,年经济效益282万元。
2.2.2整合管网,停用1#1.0MPa蒸汽管线。
1#管线为建厂前期所建,现保温材料破损严重,保温不佳,管段温降较大,导致进入装置蒸汽温度偏低,管网过于复杂,很多管段平时不用,阀门处于关闭状态,但由于操作和阀门自身的原因,阀门关闭不严,造成热损失,于是将在1#线的用户都迁至2#蒸汽线运行,停用1#线,解决了蒸汽在管网流动过程中形成对峙问题,用户的蒸汽波动大的问题得以解决。
关停后可减少凝结水生成量0.58t/h,减少散热损失1.6GJ/h,合计折合节省低压蒸汽1.27t/h,年经济效益131.9万元。
2.2.3增加1.0MPa蒸汽的操作弹性
为了解决1.0MPa蒸汽的操作弹性的问题,在硫磺车间增设螺杆发电机替代减温减压器为溶剂再生装置提供0.4MPa蒸汽,多余的1.0MPa蒸汽可以发电,解决了秋冬季节、春冬季节蒸汽放空的问题,使多余的蒸汽得以利用。
2016年7月至2017年1月共发电49.2万KWH,合计32.47万元,解决了1.0MPa浪费问题。
3.优化后的效果
通过实施全厂蒸汽优化改造,调整三个管网的运行,2016年冬季水煤浆锅炉产汽21吨/时,重催锅炉产汽82吨/时左右,比2015年冬季降低了20吨/时;2016年夏季重催CO锅炉产汽82吨时,比2015年夏季降低了5吨/时,季节交替时减少1.0MPa蒸汽放空15天,约10吨/时,回收电量49.2万KWh,约32.47万元,大大降低了蒸汽的使用。
通过全厂蒸汽优化改造年经济效益617.87余万元。
以上数据表明,利用Site-int软件优化蒸汽系统预测与实际运行效果是一致的,蒸汽优化取得了成功。