高炉冶炼过程的物理化学
高炉内生成铁的原理是什么
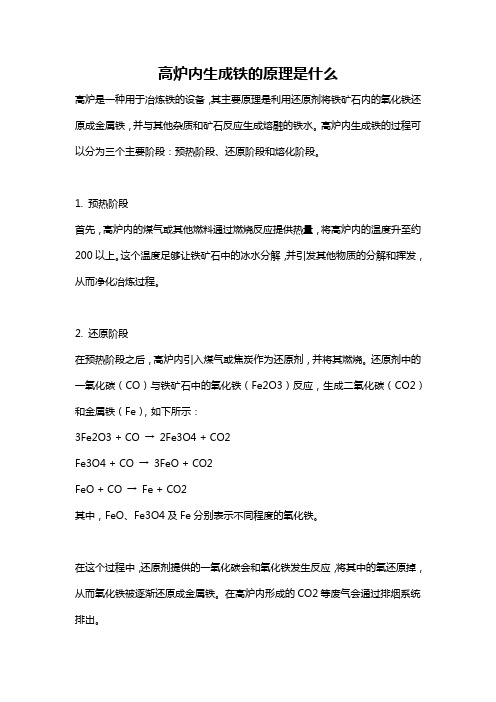
高炉内生成铁的原理是什么高炉是一种用于冶炼铁的设备,其主要原理是利用还原剂将铁矿石内的氧化铁还原成金属铁,并与其他杂质和矿石反应生成熔融的铁水。
高炉内生成铁的过程可以分为三个主要阶段:预热阶段、还原阶段和熔化阶段。
1. 预热阶段首先,高炉内的煤气或其他燃料通过燃烧反应提供热量,将高炉内的温度升至约200以上。
这个温度足够让铁矿石中的冰水分解,并引发其他物质的分解和挥发,从而净化冶炼过程。
2. 还原阶段在预热阶段之后,高炉内引入煤气或焦炭作为还原剂,并将其燃烧。
还原剂中的一氧化碳(CO)与铁矿石中的氧化铁(Fe2O3)反应,生成二氧化碳(CO2)和金属铁(Fe),如下所示:3Fe2O3 + CO →2Fe3O4 + CO2Fe3O4 + CO →3FeO + CO2FeO + CO →Fe + CO2其中,FeO、Fe3O4及Fe分别表示不同程度的氧化铁。
在这个过程中,还原剂提供的一氧化碳会和氧化铁发生反应,将其中的氧还原掉,从而氧化铁被逐渐还原成金属铁。
在高炉内形成的CO2等废气会通过排烟系统排出。
3. 熔化阶段在还原过程中,金属铁会逐渐与其他杂质、矿石和渣球反应,形成熔融的铁水。
铁水会下沉并从高炉底部的出铁口流出,而留下的渣球则会从高炉顶部排出。
高炉内生成铁的原理涉及到多种物理和化学过程,其中还包括矿石的分解、还原反应、熔化和脱渣等。
为了保持高炉的有效工作,还需注意控制气氛、燃料的使用和废气处理等方面。
高炉内的反应过程是与温度、压力、矿石和还原剂的性质以及高炉结构等多个因素相关的复杂过程。
为了提高冶炼效率、降低成本和减少对环境的影响,工程师和研究人员一直在致力于优化高炉的设计和操作。
铁冶金学——第四章 高炉内物理化学反应2
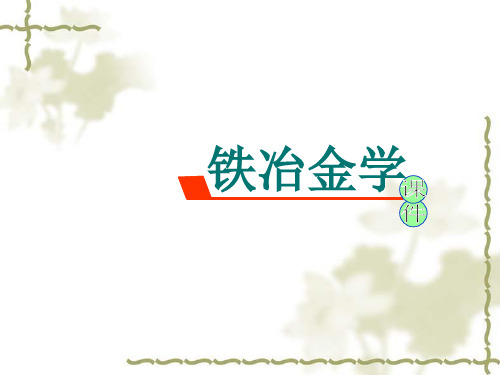
4.1 高炉炼铁还原热力学
4.3 造渣与脱硫
4.1 高炉炼铁还原热力学
4.3.3 高炉渣组成和性质及其对冶炼的影响 一、高炉渣的组成
高炉中凡没有或不能进入生铁的熔融物质都全部转入炉渣。
由表6-1可见,高炉渣主要由SiO2、Al2O3、CaO、MgO四种 组分组成。在用普通矿冶炼炼钢生铁的情况下,它们之和
4.3 造渣与脱硫
4.1 高炉炼铁还原热力学
三、炉渣性质及其对冶炼的影响 炉渣的性质及其化学成分密切相关,其中碱度对渣的性质 有很大影响。直接影响高炉冶炼的炉渣性质有熔化温度、 熔化性温度、粘度、稳定性和脱硫性能等。一般希望高炉 渣具有适宜的熔化性,较小的粘度,良好的稳定性和较高 的脱硫能力。炉渣的这些性质在冶金热力学和动力学中已 经讲过了,这里着重讨论它们对高炉冶炼的影响。
质基本稳定,变化不大。经风口区再氧化的铁及其它元素
在这里又可能还原到铁水中,使渣中FeO含量降低。铁水穿 过渣层和渣铁界面发生的脱硫反应使渣中CaS有所增加。一 般所说的高炉渣系指终渣。终渣对控制生铁成分,保证生
铁质量有重要影响。终渣应是预期的理想炉渣。若有不当,
应在实践中通过配料调整,使其达到适宜成分。
4.3 造渣与脱硫
4.1 高炉炼铁还原热力学
4.3.2 高炉造渣过程和软熔带的形成 现代高炉多用熔剂性熟料冶炼,基本上不直接加入熔剂。 由于在烧结(或球团)生产过程中熔剂已事先矿化成渣, 这就大大改善了高内造渣过程。 高炉渣按其形成过程有初渣、中间渣和终渣之分。 初渣是指在高炉的适当温度区域(软熔带,图6-2)刚开始 出现的液相炉渣;中间渣是指在处于滴落过程中成分、温 度在不断变化的炉渣(国外称炉腹渣);终渣是指已经下 达炉缸,并周期的从炉内排出的炉渣。
炼铁工艺05高炉冶炼过程的物理化学

高炉冶炼主要是以 CO 和 C 作为还原剂,还原区域的温度一般不大于 1500℃, 在此条件下,CaO、A1203 和 MgO 在高炉冶炼过程中不可能被还原。
氧化物中的金属(或非金属)和氧亲和力的大小,也可用氧化物的分解压力 大小来表示,即氧化物的分解压力越小,元素和氧的亲和力越大,该氧化物越稳 定。
用 H2 还原铁氧化物高炉在不喷吹燃料条件下,煤气中 H2 量一般在 1.8-2.5% 范围内,主要是鼓风中水分被 C 还原产生的。在喷吹煤粉、天然气等燃料时,煤 气中 H2 浓度显著增加。H2 和氧的亲和力很强,可夺取铁氧化物中的氧而作为还原 剂。
所以固体碳还原铁氧化物反应,只表示最终结果,反应的实质仍是 CO 在起 作用,最终消耗的是碳素。
反应 FeO 十 C=Fe 十 CO 的进行,决定于 C02 十 C=2CO 反应的速度。实验指 出:C02 与 C 作用达到平衡,其速度是很慢的。650 ℃时,大约需要 12h;800 ℃ 时需要 9h;温度愈低,用固体碳进行还原愈难。由于高炉内煤气流速很高,在 温度大于 700-730℃时,C02 十 C=2CO 反应有可能达到平衡,即 FeO 可用 C 进行 还原。但因碳的气化反应速度很慢,C 还原 FeO 的作用很小。只有在 800~850 ℃ 时,FeO 被 C 还原才较明显;激烈地进行反应则在 1100℃以上。
高炉冶炼的理化过程
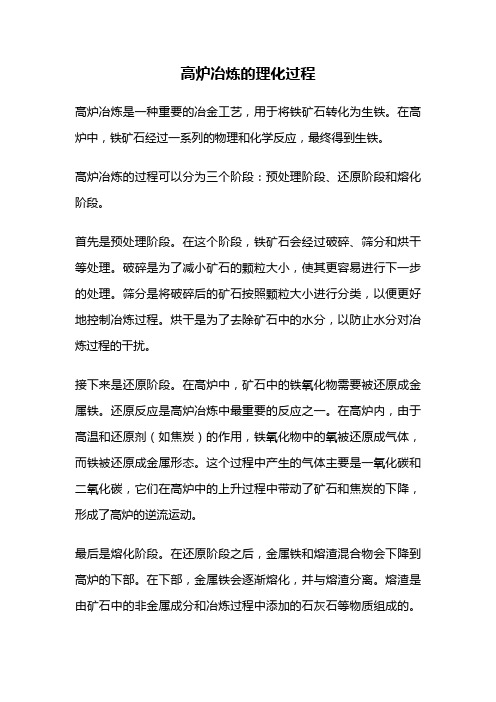
高炉冶炼的理化过程高炉冶炼是一种重要的冶金工艺,用于将铁矿石转化为生铁。
在高炉中,铁矿石经过一系列的物理和化学反应,最终得到生铁。
高炉冶炼的过程可以分为三个阶段:预处理阶段、还原阶段和熔化阶段。
首先是预处理阶段。
在这个阶段,铁矿石会经过破碎、筛分和烘干等处理。
破碎是为了减小矿石的颗粒大小,使其更容易进行下一步的处理。
筛分是将破碎后的矿石按照颗粒大小进行分类,以便更好地控制冶炼过程。
烘干是为了去除矿石中的水分,以防止水分对冶炼过程的干扰。
接下来是还原阶段。
在高炉中,矿石中的铁氧化物需要被还原成金属铁。
还原反应是高炉冶炼中最重要的反应之一。
在高炉内,由于高温和还原剂(如焦炭)的作用,铁氧化物中的氧被还原成气体,而铁被还原成金属形态。
这个过程中产生的气体主要是一氧化碳和二氧化碳,它们在高炉中的上升过程中带动了矿石和焦炭的下降,形成了高炉的逆流运动。
最后是熔化阶段。
在还原阶段之后,金属铁和熔渣混合物会下降到高炉的下部。
在下部,金属铁会逐渐熔化,并与熔渣分离。
熔渣是由矿石中的非金属成分和冶炼过程中添加的石灰石等物质组成的。
熔渣的主要作用是吸收和分离金属铁中的杂质,使得最终得到的生铁质量更纯净。
在熔化阶段,高炉内部温度极高,达到了1500摄氏度以上,这使得金属铁能够熔化,而熔渣则保持在液态状态。
总结起来,高炉冶炼的理化过程包括预处理、还原和熔化三个阶段。
通过这些过程,铁矿石中的铁氧化物被还原成金属铁,并与熔渣分离,最终得到生铁。
高炉冶炼是一种复杂的物理和化学过程,需要严格控制温度、压力和流动等参数,以确保冶炼过程的顺利进行。
这种冶炼工艺在现代工业中仍然具有重要的地位,为人们提供了大量的铁合金和其他铁制品。
2.高炉炼铁过程的物理化学变化2010

实际rd更小,0.4-0.6 rd↓0.1,焦比50Kg↓ 措施:高风温,喷吹,精料
不同rd下还原剂的耗C量
2.2.3 气固相还原反应的动力学
研究目的 发展间接还原,提高冶炼效率,降低燃料消耗 研究历史 二部理论
1926年苏联学者Байков提出: MO=M+1/2O2 O2+CO(或H2)=CO2(或H2O) 存在的问题:
分解
结晶水 强烈分解温度:400℃~600℃。 影响:一般不影响高炉过程,有20%可能进入高温 区(800℃) H2O+C=H 2+CO
碳酸盐
来源: MnCO3,FeCO3,MgCO3,CaCO3 影响:MnCO3,FeCO3,MgCO3分解对高炉影响不大 CaCO350%~70%进入高温区分解,耗碳 CO2十C=2CO
1—4Fe3O4十O2=6 Fe2O3 2—6 FeO十O2=2 Fe3O4 3—2 CO十O2=2 CO2 4—2Fe十O2=2FeO 5一C十O2=CO2 6—2C十O2=2CO 7—2H2十O2=2H2O 8—3/2Fe十O2=1/2 Fe3O4 Fe2O3最不稳定, Fe3O4次之,FeO最稳定 小于950K时,还原能力CO>H2>C,高于此温度情况相反 标准状态下,FeO不能被CO和H2还原
2.2 还原过程
2.2.1 铁的氧化物及其特性
Fe: 温度911℃:α -Fe 体 心立方 温度>911℃ β -Fe 面心立方(不锈钢) γ -Fe 体心立方 浮土体:Fe++缺位的晶体, 以 FexO表示, O=23.16- 25.60%, 温度<570℃时, FexO将分解为Fe3O4+Fe Fe3O4: 理论含O量27.64%, 温度高于800℃时,也有溶 解O2,或Fe++缺位的现象。 Fe2O3 理论含O量为30.06%, >1457℃时 , Fe2O3→ Fe3O4十O2 (体积增大)
铁冶金学——第四章 高炉内物理化学反应1
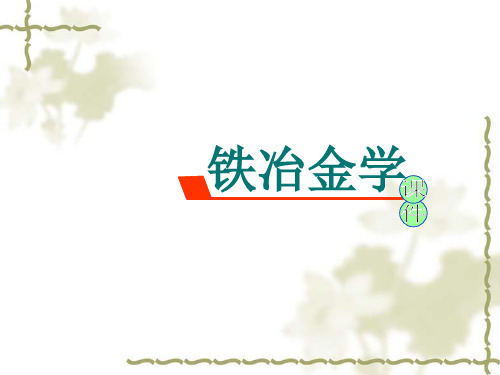
式中:、——分别为B和Me与1molO2结合成氧化物的标准 生成自由能。
4.1.1 氧化物还原的一般原理
4.1 高炉炼铁还原热力学
图4-1例举了高炉中常见氧化物的标准生成自由能变化 (对1molO2而言)及其与温度的关系,可用它来判断 还原反应的方向和难易,并选择适宜的温度条件。图41中的各条线称为氧势线。氧势线位置愈低的氧化物, 其值愈小,愈难还原。凡是在铁氧势线以下的物质单质 都可用来还原铁氧化物。例如Si就可还原FeO。如果两 直线有交点,则交点温度即为开始还原温度。高于交点 温度,则是下面的单质能还原上面的氧化物;低于交点 温度,则反应逆向进行。如两直线在图中无交点,那么 下面的单质能还原上面的氧化物。
4.1 高炉炼铁还原热力学
4.1.2 铁氧化物的还原的一般规律
高炉下部铁氧化物的直接还原反应的进行取决于碳 的气化反应(4-13)和(4-15)的发展(即气化反 应的迟早和速率)。而碳的气化反应的发展则决定 于温度和焦炭本身的反应性。焦炭反应性愈好,碳 的气化反应可提前在较低的温度下进行,则直接还 原反应发展的早,进行的快,高炉内直接还原区扩 大。相反,焦炭反应性较差时,碳的气化反应需要 在更高的温度下进行,则直接还原反应发展的晚, 进行得慢,即直接还原区向高温区收缩。一般希望 适当扩大间接还原区,缩小直接还原区。因此,使 用反应性较差的焦炭反而有利。
4.1.1 氧化物还原的一般原理
4.1 高炉炼铁还原热力学
然而,还原剂的选择还必须适应大规模工业生 产的需要和经济效益的要求。显然在高炉中不 能用比铁昂贵的Al、Mg、Ca、Si、Mn来作为 还原剂。它们作为还原剂是不经济的。
C、CO和H2是高炉炼铁适宜的还原剂。它们由 原料带来,兼有热能和化学能的双重职能,焦
一 炉料在炉内的物理化学变化 §2.5 高炉冶炼基本原理

(4)喷吹燃料后,喷吹料柱压差普遍升 高,随喷吹量的增加而增加,下部压差增 加较多。
(5)喷吹后生铁含硫量降低,质量提高。
高炉喷吹燃料后,炉渣脱硫能力提高, 允许适当降低生铁含硅量。因此,喷吹更 适于冶炼低硫低硅生铁。
5 富氧鼓风
富氧鼓风工艺流程 1—冷风管;2—流量孔板;3—氧气插入管;4、8—压力表;5、10—截止阀; 6—氧气流量孔板;7—电磁快速切断阀;9—电动流量调节阀;11—放风阀
的F大于零。
显然,某处的F=0时,则该处的炉料 处于悬料状态。
因此,炉料不顺行的现象,不仅可能 在高炉上部或下部出现,也可能在某一截 面上的某一区域出现。
通常情况下,当炉型、原料和操作操 作制度一定时,Q有效变化不大,因此,F的 大小主要受到△P的影响。
△P是煤气流通过高炉料柱时的压力 损失,也即克服摩擦阻力和局部阻力而造 成的压力损失,可近似地看作上升煤气对 下降炉料的浮力。
焦炭作回旋运动;
主要发生碳素的燃烧,产生炉缸煤气,燃烧
释放的热量由炉缸煤气传递 。
(5) 炉缸区 炉缸区内汇集渣铁,进行最后的渣铁反应。
七 炉料下降条件
在高炉冶炼过程中,炉料在炉内的运 动是一个固体散状料的缓慢移动床。炉料 均匀而有节奏地顺利下降,是高炉顺行的 重要标志。
炉料下降的必要条件之一是高炉内必 须不断产生使其下降的自由空间。
量增多,气体粘度减小,煤气渗透能力提高。
(3)炉缸冷化,顶温升高,有热滞后现象。
炉缸冷化是指风口前理论燃烧温度(风口 前燃料燃烧产生的热量全部用于加热燃烧产物所
能达到的温度)降低。
热滞后现象是指高炉增加喷吹量后,由于
入炉总燃料量增加,炉温本应升高。但在喷吹之
初,炉缸温度不升反而暂时下降,过一段时间后, 炉缸温度才上升的一种现象。
炉料在高炉中的化学反应

【本章学习要点】本章学习炉料在高炉内的物理化学变化,高炉内铁氧化物的还原反应,高炉内非铁元素的还原,生铁的生成与渗碳过程,高炉炉渣的成分与作用,硫的分布情况,炉渣脱硫反应及其条件,高炉内燃烧反应的作用,影响燃烧带大小的因素,炉料和煤气运动情况。
第一节炉料在炉内的物理化学变化炉料从炉顶装入高炉后,自上而下运动。
被上升的煤气流加热,发生了吸附水的蒸发、结晶水的分解、碳酸盐的分解、焦炭中挥发分的挥发等反应。
图3-1 炉内的状况一、高炉炉内的状况通过国内外高炉解剖研究得到如图3—1所示的典型炉内状况。
按炉料物理状态,高炉内大致可分为五个区域或称五个带:1)炉料仍保持装料前块状状态的块状带;2)矿石从开始软化到完全软化的软熔带;3)已熔化的铁水和炉渣沿焦炭之间的缝隙下降的滴落带;4)由于鼓风动能的作用,焦炭作回旋运动的风口带;5)风口以下,贮存渣铁完成必要渣铁反应的渣铁带。
高炉解剖肯定了软熔带的存在。
软熔带的形状和位置对高炉内的热交换,还原过程和透气性有着极大的影响。
二、水分的蒸发与结晶水的分解在高炉炉料中,水以吸附水与结晶水两种形式存在。
1.吸附水吸附水也称物理水,以游离状态存在于炉料中。
常压操作时,吸附水一般在105℃以下即蒸发,高炉炉顶温度常在250℃左右,炉内煤气流速很快,因此吸附水在高炉上部就会蒸发完。
蒸发时消耗的热量是高炉煤气的余热。
所以不会增加焦炭的消耗。
相反,由于吸附水蒸发吸热,使煤气的温度降低,体积缩小,煤气流速降低,一方面减少了炉尘的吹出量,另一方面对装料设备和炉顶金属结构的维护还带来好处。
2.结晶水结晶水也称化合水,以化合物形态存在于炉料中。
高炉炉料中的结晶水一般存在于褐铁矿(nFe203·mH20)和高岭土(A123·2Si02·2H20)中,结晶水在高炉内大量分解的温度在400~600℃,分解反应如下:这些反应都是吸热反应,消耗高炉内的热量。
三、挥发物的挥发挥发物的挥发,包括燃料挥发物的挥发和高炉内其他物质的挥发。