OEE之解析
OEE是全员生产维护的核心

OEE是全员生产维护的核心公众号内回复“设备维修”四个字,赠送机修手册(共8卷)全员生产性维护 6大损失和综合设备效率 6大损失和综合设备效率(OEE)的概念在TPM中广泛应用。
6大损失可以划分为三个范畴:可用性、性能和质量,这三个范畴是OEE的基础,如图6-4所示。
可用性:需要修理时的非计划停机导致的故障损失。
任何超过10分钟的非计划停机通常被认为是故障。
它们可能是电气的、机械的、液压的、气动的等。
当在产品之间换型时,会发生换型和调整损失。
换型时间通常定义为从上一批的最后一个产品完成到下一批的第一个合格产品完成的时间。
不过,要注意,让设备全速生产可能需要很长的时间,在这期间需要频繁地调整,相应的调整时间也要记录。
性能:如果停机时间少于10分钟,则定义它们为小停机和空转或闲置。
有一系列原因可以导致此类损失,比如崩刃、添加冷却水、卡料、去除碎屑、小的调整等。
数据收集以后,可能会发现小停机是最大的损失。
因为小停机很频繁,持续时间短,记录困难,所以经常被忽略。
活动抽样法对此大有帮助。
另一个方法是让操作员在靠近工作场所方便的地方用“正”字记录小停机发生的次数,随机抽样20个实际小停机样本进行分析,就可获得小停机时间的平均状况。
机器没有按照设计速度运转则产生(降低的)速度损失。
典型的原因是流量限制、CNC设备的程序错误、工具磨损、喂料机构和传送带问题等。
质量:零件缺陷会导致报废或者返工,任何导致机器不能按照产品规格生产的问题都可以导致损失。
在换型的时候,机器启动和停止也会产生报废或者返工。
这些损失按照数量来计量。
注意,有些系统中将机器从启动到达到全速运行的时间也归纳并到这个类别,而不是作为换型损失的一部分。
综合设备效率 OEE=时间开动率×性能开动率×合格品率,最终结果用百分比的形式表示。
举例:一个班次9小时。
工作时间是8小时—因为计划性维护和会议时间占用1个小时。
故障停机20分钟,换型时间40分钟,标准的机器加工周期是1分钟。
有关OEE的定义和利用(精)

定义
总体利用率 = 有价值操作时间 [生产合格产品的时间] 总可用小时 [=每年8760小时]
=
总可用 小时
计划装料时间 计划 装料 时间
OEE X
总可用小时 [=每年8760小时] 有价值 操作 时间
13th March 2002
定义
总设备效用 = OEE 指数 =
有价值操作时间 [生产合格产品的时间] 计划装料时间
减低速度
性能
次要停机 处理次品
OEE
由次品和返工导致的损失 在生产初始阶段和稳定生产期间出现的损失
质量合格率
起始期次品使 产量减少
13th Ma工期
损失的定量分析
计划装料时间
总时间 – 组织性停工期 装料率 = 总时间
停工损失
计划装料时间 - 停工期 设备的可用性= 计划装料时间
• 机器的初始设置和调整 • 电力失效 • 电力管制
非计划的设备停工期
13th March 2002
速度或生产性能损失
降低的速度
• • • • • 设备降低的功能 工具降低的功能 小中断 材料问题 与加工相关的 • • • • •
空转时间
无操作员 无材料 等待指令 填文档延迟 安排时间延迟
工程时间
总 可用 小时
计划 装料 时间
有价值 操作 时间
13th March 2002
OEE
定义和为问题范围定优先级 以及改进操作
详细信息
由间歇性和功能降低的机器失效 导致的损失 在机器设置、调换和调整期间的停机损失
监视改进操作, 策略研究
“六大损失”
停机
性能指示器
可用性
设置和调整
设备综合效率OEE的分析与改善!太实用了!
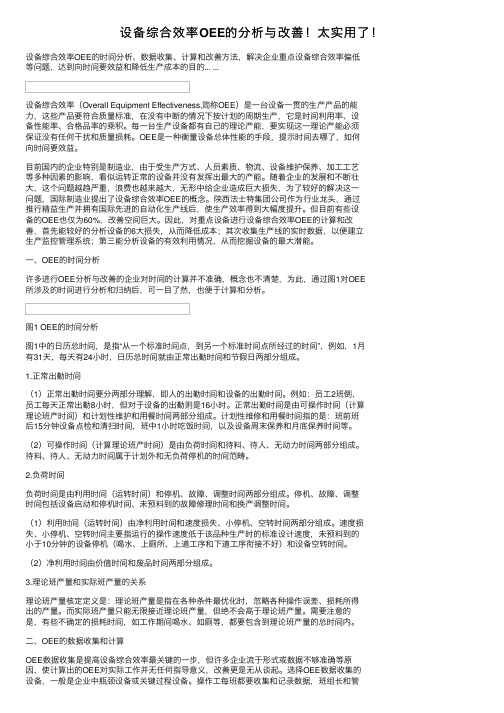
设备综合效率OEE的分析与改善!太实⽤了!设备综合效率OEE的时间分析、数据收集、计算和改善⽅法,解决企业重点设备综合效率偏低等问题,达到向时间要效益和降低⽣产成本的⽬的... ...设备综合效率(Overall Equipment Effectiveness,简称OEE)是⼀台设备⼀贯的⽣产产品的能⼒,这些产品要符合质量标准,在没有中断的情况下按计划的周期⽣产,它是时间利⽤率、设备性能率、合格品率的乘积。
每⼀台⽣产设备都有⾃⼰的理论产能,要实现这⼀理论产能必须保证没有任何⼲扰和质量损耗。
OEE是⼀种衡量设备总体性能的⼿段,提⽰时间去哪了,如何向时间要效益。
⽬前国内的企业特别是制造业,由于受⽣产⽅式、⼈员素质、物流、设备维护保养、加⼯⼯艺等多种因素的影响,看似运转正常的设备并没有发挥出最⼤的产能。
随着企业的发展和不断壮⼤,这个问题越趋严重,浪费也越来越⼤,⽆形中给企业造成巨⼤损失,为了较好的解决这⼀问题,国际制造业提出了设备综合效率OEE的概念。
陕西法⼠特集团公司作为⾏业龙头,通过推⾏精益⽣产并拥有国际先进的⾃动化⽣产线后,使⽣产效率得到⼤幅度提升。
但⽬前有些设备的OEE也仅为60%,改善空间巨⼤。
因此,对重点设备进⾏设备综合效率OEE的计算和改善,⾸先能较好的分析设备的6⼤损失,从⽽降低成本;其次收集⽣产线的实时数据,以便建⽴⽣产监控管理系统;第三能分析设备的有效利⽤情况,从⽽挖掘设备的最⼤潜能。
⼀、OEE的时间分析许多进⾏OEE分析与改善的企业对时间的计算并不准确,概念也不清楚,为此,通过图1对OEE所涉及的时间进⾏分析和归纳后,可⼀⽬了然,也便于计算和分析。
图1 OEE的时间分析图1中的⽇历总时间,是指“从⼀个标准时间点,到另⼀个标准时间点所经过的时间”,例如,1⽉有31天,每天有24⼩时,⽇历总时间就由正常出勤时间和节假⽇两部分组成。
1.正常出勤时间(1)正常出勤时间要分两部分理解,即⼈的出勤时间和设备的出勤时间。
《OEE分析与管理》

100%
5.OEE分析图可与六大损失关系趋势
OEE 100% F F E D C B A F F F E
D
F
E D
好!
E
D C B A
E
D C
B
E
D
C B A
C
B
C
B
OEE
A
A
A:故障损失
B:换品种、调整损失
C:开关机损失 D:空转、小停机 E:速度降低损失
A
50%
F:缺陷和返工损失
月
35
采用“损失树”的方法显示每个损失的趋势
OEE %
85%
60%
时间利用率 %
性能利用率 %
质量合格率 %
65%
75%
70%
90%
85%
90%
换品种、调整
故障
开、停机
小停机
速度降低
返工
不良品
分钟 设置调整 清洁
分钟 A类 B类 C类 D类 E类
产品数 开机
次数 A类 B类 C类 D类 E类
数量/ 分钟 设备A 设备B 设备C 设备D 设备E
外加工件或其它零部件迟延交货所引起之待料
突发故障引起之停止时间 模具、工具之交换、调整、试加工之时间。 运转时间-(加工数× C.T) 基准加工速度与实际加工速度之差。加工数×(实际C.T基准C.T) 正常生产时作出不良品之时间。选别、修理不良品而致设 备停止有效稼动之时间 生产开始时,自故障小停止至回复运转时,条件之设定、 试加工等制作不良品之时间 实际产生附加价值的时间 生产良品所花的时间
60 60 70 70 36400 56560 36575 56768 175 208 4320 4320 3590 3180 730 1140 10 25 0 0 0 0 0 0 10 25 0 0 0 0 720 1115 197.5 304.02857 90 119 87 135 20 50 0 0 523 811 2.5 3.0 2.5 3.0 0 0 520 808
浅谈OEE
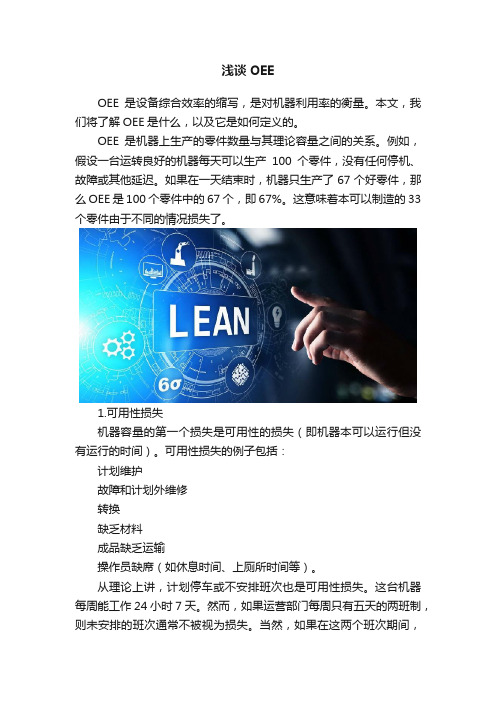
浅谈OEEOEE是设备综合效率的缩写,是对机器利用率的衡量。
本文,我们将了解OEE是什么,以及它是如何定义的。
OEE是机器上生产的零件数量与其理论容量之间的关系。
例如,假设一台运转良好的机器每天可以生产100个零件,没有任何停机、故障或其他延迟。
如果在一天结束时,机器只生产了67个好零件,那么OEE是100个零件中的67个,即67%。
这意味着本可以制造的33个零件由于不同的情况损失了。
1.可用性损失机器容量的第一个损失是可用性的损失(即机器本可以运行但没有运行的时间)。
可用性损失的例子包括:计划维护故障和计划外维修转换缺乏材料成品缺乏运输操作员缺席(如休息时间、上厕所时间等)。
从理论上讲,计划停车或不安排班次也是可用性损失。
这台机器每周能工作24小时7天。
然而,如果运营部门每周只有五天的两班制,则未安排的班次通常不被视为损失。
当然,如果在这两个班次期间,客户的需求远远超过机器的容量,则完全可以将未计划的班次也包括在损失中。
在任何情况下,如果不包括这些计划停靠站,则仍应将其视为潜在容量。
2.速度损失下一大类是速度损失。
这台机器确实运转了,但由于某种原因,生产零件的速度比预期的要慢。
速度损失的原因有:缺乏维护机器磨损机器上的操作不正确机器设置错误,设置速度低于可能的速度轻微怠速(理论上这是可用性损失,但更容易确定为速度损失)。
3.质量损失最后,还有质量损失。
机器正在运转,速度很快,但生产的产品不符合规格。
简而言之,这台机器正在产生废物。
产生废物可能有三个原因:报废产品(产品根本无法回收)返工产品(产品必须返工才能使用)。
虽然从理论上讲,机器的能力并没有完全浪费在这个零件上,但在现实中,返工通常需要比一开始就做好更多的工作。
因此,返工通常被视为完全损失。
启动损失(在生产爬坡期间,生产零件,但取决于系统,可能因质量问题或作为常规爬坡程序的一部分而报废)。
总结以下是一台机器的示例,该机器本可以生产100个零件,但由于机器停止生产而损失了18个零件,由于速度较慢而损失了10个零件,还有5个零件被报废。
OEE分析与改善
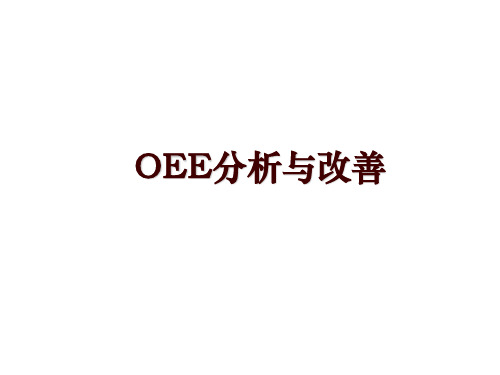
即:OEE = 时间稼动率 X 性能稼动率 X 良品率
然而,在现在的制造业中,看似良好运作的生产车间实际上并 没有以最好的状态进行工作,设备和操作人员的价值存在很大 的改善空间,这无形中为企业带来了巨大的损失。
为了解决这一问题,国际制造业提出了全局设备效率(OEE)的 概念。
OEE的定义
一般,每一个生产设备都有自己的最大理论产能,要实现 这一产能必须保证没有任何干扰和质量损耗。当然,实际生产 中是不可能达到这一要求,由于许许多多的因素,车间设备存 在着大量的失效: 例如设备的故障,调整以及设备的完全更换 之外,当设备的表现非常低时,可能会影响生产率,产生次品, 返工等。
OEE分析与改善
目录
➢ 1、OEE的定义 ➢ 2、OEE的计算 ➢ 3、OEE的六大损失 ➢ 4、OEE的改善
OEE的定义
随着市场竞争的日益激烈,制造行业要想持续的获得高的经济 效益,必须最大化的挖掘和改善所有可提升的空间。
生产车间的生产效率显得极其重要,在某些方面,它甚至成为 企业是否可以赢利的决定性因素。
运转时间 / 开动时间 * 100%
良品率:
(940 - 30) / 940 * 100% = 96.81% (生产总数 – 报废品数)/ 生产总数 * 100%
OEE = 79.75% * 73.44% * 96.81% = 56.70%
OEE的六大损失
损失类型
故障 开停机 切换
OEE概念

总时间损失
1
为什么在衡量OEE? ? 为什么在衡量
河水与暗礁的比喻
精益生产的目的是要降低库存(河水水位),指出产生生产停顿的潜在 原因(暗礁),清除之使企业能以更强的竞争力即更低水位运作
通过使企业的库存强制减少 到某个既定目标,企业可以 降低水位,主动使暗礁浮出 水面,从而可以清除礁石或 降低暗礁高度
OEE(整体设备效能)
OEE概念ห้องสมุดไป่ตู้
0
OEE是什么?
• OEE代表整体设备效能(Overall Equipment Effectiveness) • 这是一种严格的机器总体性能的衡量手段,揭示时间浪费存在于哪里 • 统计各种时间浪费目的在于实现改进
OEE所涵盖的其 他时间损失
传统效率衡量方式 只计算了部分时间 损失
• OEE要作为一系列一体化的综合关键业绩指标中的一部 分来运用而不能孤立使用,否则将造成生产批次规模加大 或有质量缺陷的产品 • OEE必须与精益原则相符,要确保对OEE的计算不会导 致浪费合理化、制度化,例如,绝不要允许给换线留出 时间
计划内停工* 机器故障 换线 计划外停工 速度降低 损坏 质量缺陷
时间运 行效率 = 性能运 行效率 = 机器实际运行时间 24小时-计划停机时间 赚得时间 机器实际运行时间 生产的合格产品数 合格品率 = 生产的合格产品数+损耗数
总体设备效能( 总体设备效能(OEE) = 时间运行效率 性能运行效率 x 合格品率 ) 时间运行效率x
* 计划内停工排除在OEE计算之外
3
OEE的计算
OEE = 时间运行效率 性能运行效率 x 合格品率 时间运行效率x
其中:时间运行效率 时间开动率 时间开动率=开动率 其中:时间运行效率=时间开动率 开动率 性能运行效率=性能开动率 机械效率 性能运行效率 性能开动率=机械效率 性能开动率
OEE的定义

OEE的定义随着市场竞争的日趋激烈,生产企业要想持续获得理想的效益,其中一个重要环节就是要持续提升其生产效率——在具有“制造大国”之称的中国的今天,效率已成为众多企业是否可以赢利的关键甚至是决定性因素。
然而,中国目前大部分生产企业,特别是民营生产企业,其表面上看似良好运作的生产车间实际上并没有以最好的状态进行工作,设备和操作人员的价值存在很大的改善空间,这无形中为企业造成了巨大的损失。
为了解决这一问题,国际制造业提出了全局设备效率(OEE)的概念。
全局设备效率OEE是一种简单实用的生产管理工具,在欧美的制造业和中国的跨国企业中已得到广泛的应用,全局设备效率指数已成为衡量企业生产效率的重要标准,也是TPM (Total Productive Maintenance)实施的重要手法之一。
OEE是Overall Equipment Effectiveness(全局设备效率)的缩写。
一般,每一个生产设备都有自己的理论产能,要实现这一理论产能必须保证没有任何干扰和质量损耗。
OEE就是用来表现实际的生产能力相对于理论产能的比率,它是一个独立的测量工具。
OEE是由可用率,表现性以及质量指数三个关键要素组成:OEE = 可用率 * 表现指数 * 质量指数可用率=操作时间/计划工作时间它是用来评价停工所带来的损失,包括引起计划生产发生停工的任何事件,例如设备故障,原材料短缺以及生产方法的改变等。
表现指数=理想周期时间/(操作时间/总产量)=(总产量/操作时间)/生产速率表现性是用来评价生产速度上的损失。
包括任何导致生产不能以最大速度运行的因素,例如设备的磨损,材料的不合格以及操作人员的失误等。
质量指数=良品/总产量质量指数是用来评价质量的损失,它用来反映没有满足质量要求的产品(包括返工的产品)。
例如:某设备某天工作时间为8H,班前计划停机10MIN,故障停机30MIN,设备调整35MIN,产品的理论加工周期为1min/件,一天共加工产品400件,有20件废品,求这台设备的OEE。
- 1、下载文档前请自行甄别文档内容的完整性,平台不提供额外的编辑、内容补充、找答案等附加服务。
- 2、"仅部分预览"的文档,不可在线预览部分如存在完整性等问题,可反馈申请退款(可完整预览的文档不适用该条件!)。
- 3、如文档侵犯您的权益,请联系客服反馈,我们会尽快为您处理(人工客服工作时间:9:00-18:30)。
一.OEE的認識
1.1. 英文全名:Overall equipment effectiveness,即指全面設備生產效率
二.OEE簡化后的計算公式
2.1. OEE=良品數*理論加工週期時間/(總可用時間-計劃停止時間,如保養開會等-無訂單無排程的時間)
2.2. OEE=時間開動率*凈嫁動率*速度嫁動率*良率
'=(開動時間/負荷時間)*(實際加工數量*實際加工週期時間/開動時間)*(理論加工週期時間/實際加工週2.2.1. 時間開動率管控的目的:減少故障停機,換模的時間,增加總嫁動率
2.2.2. 凈嫁動率管控的意義在於:減少短暫停機的損失
2.2.
3. 速度嫁動率管控的目的在於:增加設備的速度達成率,縮小實際週期時間與理論週期時間的差距,增加設
2.2.1. 負荷時間管控的目的在於:減少計劃休止的時間,增加設備實際的開動時間
三. OEE的衍伸
3.1. TEEP.其英文全名為:Total Effective Equipment Performance,即全面生產效率
3.2. TEEP.的計算公式為:設備利用率*OEE
3.2.1. 設備利用率=(日曆工作時間-計劃停止時間(如無訂單)-非設備因素停止時間)/日曆工作時間
以上可以看出TEEP是for特殊使用者者使用的,與制程的狀態無關係,但是也是損失的一部份
程的時間)
加工週期時間/實際加工週期時間)*良品數/實際加工數量週期時間的差距,增加設備的OEE
間)/日曆工作時間。