OEE统计方法汇编
设备OEE计算方法介绍

(Overall Equipment Effectiveness), 即设备综合效率,其本质就是设备负荷时间内实际产量与理论产量的比值。
企业在进行OEE计算时常常遇到很多迷惑的问题,如工厂停水、停电、停气、停汽使设备不能工作,等待定单、等待排产计划、等待检查、等待上一道工序造成的停机,不知如何计算。
本文引入非设备因素停机的概念,修改了OEE的算法,使计算得到的OEE更能够真实反映设备维护的实际状况,让设备完全利用的情况由完全有效生产率这个指标来反映。
本文同时介绍了在不同情况下如何分析设备损失的PM分析流程。
1、 OEE表述和计算实例OEE= 时间开动率×性能开动率×合格品率其中,时间开动率 = 开动时间/负荷时间而,负荷时间 = 日历工作时间-计划停机时间开动时间 = 负荷时间–故障停机时间–设备调整初始化时间性能开动率 = 净开动率×速度开动率而,净开动率 = 加工数量×实际加工周期/开动时间速度开动率 = 理论加工周期/实际加工周期合格品率 = 合格品数量/ 加工数量在OEE公式里,时间开动率反映了设备的时间利用情况;性能开动率反映了设备的性能发挥情况;而合格品率则反映了设备的有效工作情况。
反过来,时间开动率度量了设备的故障、调整等项停机损失,性能开动率度量了设备短暂停机、空转、速度降低等项性能损失;合格品率度量了设备加工废品损失。
OEE还有另一种表述方法,更适用于流动生产线的评估, 即OEE= 时间开动率×性能开动率×合格品率而,时间开动率 = 开动时间/计划利用时间而,计划利用时间 = 日历工作时间-计划停机时间开动时间 = 计划利用时间–非计划停机时间性能开动率 = 完成的节拍数/计划节拍数其中,计划节拍数 = 开动时间/标准节拍时间合格品率 = 合格品数量/加工数量这与前述的OEE公式实际上是同一的。
计算:停机时间 = 115+12 = 127 min计划开动时间 = 910 – 127 = 783 min时间开动率 = 783/910 = 86%计划节拍数 = 开动时间/标准节拍时间 = 783/3 = 261性能开动率 = 203/261 = 77.7%合格品率 = 一次合格品数/完成产品数 = 152/203 = 74.9%于是得到OEE = 86% ×77.7%×74.9% = 50%2、 OEE的实质如果追究OEE的本质内涵,其实就是计算周期内用于加工的理论时间和负荷时间的百分比。
oee设备综合效率表格

oee设备综合效率表格篇一:oee设备综合效率二种叫法和计算公式并举例子oee (设备综合效率)是衡量设备综合性时间损失大小的指标,反应设备在负荷时间内有多少时间是有价值的开动时间。
叫法之一:oee=时间开动率x性能开动率x良品率即:(1)〔时间开动率〕:是衡量测定因故障、准备、调整等导致停止损失大小的指标。
时间开动率=(负荷时间一停止时间)/负荷时间*100%(2)〔性能开动率〕:是衡量因空转、小停工及速度降低等导致时间损失大小的指标。
性能开动率=(基准节拍*产量)/开动时间*100%(3)〔良品率〕:是衡量保证充分满足消费者质量要求的指标。
良品率二合格品件数/生产总件数*100%叫法之二:oee=时间利用率*设备性能率*产品合格率=(合格的产品*设计速度)/负荷时间1. 时间利用率=(负荷时间-停机损失)/负荷时间*100%=(有效)利用时间/负荷时间2. 设备性能率=(生产产品数*设计速度)/利用时间*100%3. 质量合格率=(生产产品数-不合格品)/生产产品数*100%其实:设计速度即基本节拍工厂/车间的设备综合效率=(1#设备综合效率*产量+2#设备综合效率*产量+…+n#设备综合效率*产量)+总产量叫法之三:oee=可使用率x工作表现率x品质率1. 可使用率:指实际运转时间与可用时间(负荷时间)之比。
(1)可用时间:指从一天(或一个月)的工作时间中,减去生产计划、计划保养,以及日常管理上必要的的停顿时间后所剩下的时间。
(2)停机时间(停止时间):指因故障、setup、调整、更换模具等所停止的时间。
(3)公式:可使用率=(可用时间-停机时间)/可用时间x100%2. 工作表現率包括速度运转率与纯运转率。
(1)速度运转率系指设备原有这能力(包括周期时间、循环数)对实际速度之比;纯运转率指在单位时间内设备有无以一定速度在运转,由此可以求得日报上无法出现的小故障损失。
(2)工作表现率二速度运转率x有效运转率=理想周期x 加工数量*(负荷时间-停止时间)3. 品质率:品质率系指实际制成之良品数量与加工数量的比率。
OEE计算方法

二、OEE计算详解 计算详解
1、设备综合效率的七大损失 、 负荷时间内分析 稼动时间(停止损失) 稼动时间(停止损失) : 1、故障损失 、 2、换模、换线调整 、换模、 3、刀具交换 、 4、开机、暖机 、开机、 净稼动时间(性能损失): ):5、 净稼动时间(性能损失): 、空转短停损失 6、速度下降 、 稼动时间(不良损失) 稼动时间(不良损失) :7、不良、手工修正 、不良、
3、针对PET线OEE计算 、针对 线 计算
(1)计划停工时间: )计划停工时间: 未排产时间: 未排产时间: A1 CIP时间 :A2 时间 计划保养时间: 计划保养时间 A3 换模时间: 换模时间 A4 计划停工时间 :B=A1+A2+A3+A4 为定期进行, 外其他设备不稼动, 注:CIP为定期进行,在此间除 为定期进行 在此间除UHT外其他设备不稼动,故算 外其他设备不稼动 计划停机时间中;如不算在计划停工时间, 的值在有CIP 计划停机时间中;如不算在计划停工时间,OEE的值在有 的值在有 或没有CIP时将会波动较大,不能真实反应设备综合效率。 时将会波率。
(8)设备综合效率 ) OEE=时间稼动率×性能稼动率× 品 时间稼动率×性能稼动率× 时间稼动率 设备综合效率:0EE=T × L × H × 100% 设备综合效率
三、 OEE计算统计表 计算统计表
四、 小结
1、时间稼动率度量了设备故障、调整等停机损失; 、时间稼动率度量了设备故障、调整等停机损失; 性能稼率度量了设备短暂停机、空转、 性能稼率度量了设备短暂停机、空转、速度降低等 性能损失;合格率度量了设备加工废品损失。 性能损失;合格率度量了设备加工废品损失。 2、OEE客观反映了设备维护状况 、 客观反映了设备维护状况 3、OEE是设备隐形损失分析工具 当设备综合效率 是设备隐形损失分析工具:当设备综合效率 、 是设备隐形损失分析工具 不高时,进行时间稼动、性能稼动等逐项分析,找 不高时,进行时间稼动、性能稼动等逐项分析, 出正因,进行改善。 出正因,进行改善。
OEE计算公式+统计数据

设备稼动率 (实际稼动时间 ÷理论可稼动时
间)
实际投 入工时
(H)
19266 8354
43.36%
8354
94.33%
19266 8354
43.36%
8354
投入数/良
备注:
品数数据来 源于<OPE汇
总表>
实际稼动工
时/实际投
入工时/实
际产出有效
工时数据来
源于<日生
产报表>
设备理论可
稼动时间=
月份
ห้องสมุดไป่ตู้
投入数量 (pcs)
良品数量 (pcs)
1月 12229867 11536936 2月 3月 4月 5月 6月 7月 8月 9月 10月 11月 12月 合计 12229867 11536936
产品合格率 (良品数÷投入
数)
94.33%
2020年OEE数据统计
设备理论 可稼动时
间(H)
实际稼 动时间
设备机台数
×计划排产
天数×
19.5H
OEE数据统计
实际产出有效工 时
(实际产出÷标 准产能)
性能效率 (有效产出工时÷
实际投入工时)
OEE (产品合格率×设 备稼动率×性能效
率)
备注
10310
123.41%
50.48%
10310
123.41%
50.48%
年度设备总效率(OEE)统计表
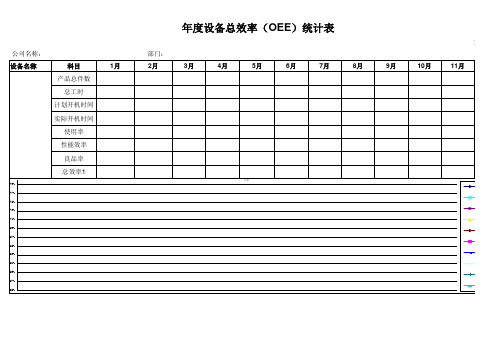
OEE是Overall Equipment Effectiveness(全局设备效率)的缩写;OEE=使用率X 性能效率 X良品率。 其中: 使用率=操作时间 / 计划工作时间 它是用来考虑停工所带来的损失,包括引起计划生产发生停工的任何事件,例如设备故障,原料短缺以及生产方法的改变等) 性能效率=(总产量/操作时间)/理想周期时间=(总产量 / 操作时间)/ 生产速率 (性能效率考虑生产速度上的损失。包括任何导致生产不能以最大速度运行的因素, 例如设备的磨损,材料的不合格以及操作人员的失误等) 良品率=良品/总产量 (质量指数考虑质量的损失,它用来反映没有满足质量要求的产品(包括返工的产品)) 利用OEE的一个最重要目的就是减少一般制造业所存在的六大损失:停机损失、换装调试损失、暂停机损失、减速损失、启动过程次品损失和生产正常运行时产生的次 品损失。
文件编号: 12月
总效率1 系列4 系列5 系列3 系列6 系列2 系列8 系列10 系列7 系列9
变等) 运行的因素,
运行时产生的次
公司名称: 设备名称
科目 产品总件数
总工时
计划开机时间
实际开机时间
使用率
性能效率
良品率
总效率1
79% 77% 75% 73% 71% 69% 67% 65% 63% 61% 59% 57% 55%
1月
年度设备总效率(OEE)统计表
部门:
2月3月4月Fra bibliotek5月6月
7月
8月
文件编号:
9月
10月
11月
月份
总效率 系列 系列 系列 系列 系列 系列 系列 系列 系列
设备OEE统计与算法

OEE会高于实际情况,OEE数据错误。
OEE的计算-案例三
Utilization Loss 停机损失
案例
故障
待料
换模
(分钟/周) (分钟/周) (分钟/周)
1
2
3
4
5
6
1000
1000
1000
1500
200
1000
600
600
600
600
600
600
1500
1500
设备OEE统计与算法分享
1
01
OEE的介绍
02
OEE的计算
03
OEE的六大损失
04
OEE的现场诊断
OEE的介绍-什么是OEE
设备综合效率(OEE)
[Overall Equipment Efficiency]
一般,每一个生产设备都有自己的最大理论产能,要实现这一产能必须保证没有任何
干扰和质量损耗。当然,实际生产中是不可能达到这一要求,由于许许多多的因素,
2300
3100
U%
51.9%
51.9%
51.9%
44.2%
64.3%
51.9%
不合格件 合格件
365
365
417
365
365
1006Leabharlann 0060006848
6000
6000
6000
总产出
A%
6365
6365
7265
6365
6365
6100
94.3%
94.3%
94.3%
94.3%
94.3%
OEE介绍和计算方法
OEE(Overall Equipment Effectiveness),即设备综合效率,其本质就是设备负荷时间内实际产量与理论产量的比值。
企业在进行OEE计算时常常遇到很多迷惑的问题,如工厂停水、停电、停气、停汽使设备不能工作,等待定单、等待排产计划、等待检查、等待上一道工序造成的停机,不知如何计算。
本文引入非设备因素停机的概念,修改了OEE的算法,使计算得到的OEE更能够真实反映设备维护的实际状况,让设备完全利用的情况由完全有效生产率这个指标来反映。
本文同时介绍了在不同情况下如何分析设备损失的PM分析流程。
1、 OEE表述和计算实例OEE= 时间开动率×性能开动率×合格品率其中,时间开动率 = 开动时间/负荷时间而,负荷时间 = 日历工作时间-计划停机时间开动时间 = 负荷时间–故障停机时间–设备调整初始化时间性能开动率 = 净开动率×速度开动率而,净开动率 = 加工数量×实际加工周期/开动时间速度开动率 = 理论加工周期/实际加工周期合格品率 = 合格品数量/ 加工数量在OEE公式里,时间开动率反映了设备的时间利用情况;性能开动率反映了设备的性能发挥情况;而合格品率则反映了设备的有效工作情况。
反过来,时间开动率度量了设备的故障、调整等项停机损失,性能开动率度量了设备短暂停机、空转、速度降低等项性能损失;合格品率度量了设备加工废品损失。
OEE还有另一种表述方法,更适用于流动生产线的评估, 即OEE= 时间开动率×性能开动率×合格品率而,时间开动率 = 开动时间/计划利用时间而,计划利用时间 = 日历工作时间-计划停机时间开动时间 = 计划利用时间–非计划停机时间性能开动率 = 完成的节拍数/计划节拍数其中,计划节拍数 = 开动时间/标准节拍时间合格品率 = 合格品数量/加工数量这与前述的OEE公式实际上是同一的。
计算:停机时间 = 115+12 = 127 min计划开动时间 = 910 – 127 = 783 min时间开动率 = 783/910 = 86%计划节拍数 = 开动时间/标准节拍时间 = 783/3 = 261性能开动率 = 203/261 = 77.7%合格品率 = 一次合格品数/完成产品数 = 152/203 = 74.9%于是得到 OEE = 86% ×77.7%×74.9% = 50%2、 OEE的实质如果追究OEE的本质内涵,其实就是计算周期内用于加工的理论时间和负荷时间的百分比。
oee计算国际标准
OEE(设备效率)的计算方法在国际上并没有统一的标准,但是通常来说,它通常是通过以下公式来计算的:
OEE = (周期时间内的总合格品数/ 周期时间内总开机时间) * 100%
具体到每个环节的OEE计算方法,可以根据设备在生产过程中的角色和作用进行适当调整。
例如,对于生产线上的某台设备,我们可以按照以下步骤来计算其OEE:
1. 确定设备的开机时间:这通常是从生产报告或设备日志中获取的,包括从开机到停机之间的所有时间。
2. 确定设备的总工作小时数:这可能是该设备在整个生产过程中工作的小时数。
3. 确定设备的总产量:这可能是通过查看生产报告或其他相关记录来确定的,包括合格品和不合格品的数量。
周期时间内的总合格品数= (某台设备生产合格品数+ 废品数) / 开机时间×总工作小时数
按照这个公式,我们可以得到某台设备的OEE:
OEE = (合格品数/ 开机时间) * (合格品数+ 废品数) / 总工作小时数×100%
注意,这里的废品数可能包括那些由于设备故障或生产过程中的其他问题而不能被用于最终产品的零件或产品。
总的来说,OEE是一个重要的指标,用于衡量设备的生产能力和效率。
它可以帮助我们了解设备的性能和生产能力,以及如何改进生产过程和提高产品质量。
在计算OEE时,我们需要确保数据的准确性和可靠性,以便我们能够获得准确的评估结果。
此外,不同的行业和不同的设备类型可能需要采用不同的OEE计算方法。
因此,在实际应用中,我们可能需要根据具体情况进行调整和修改。
OEE定义和计算方式汇总
OEE定义和计算方式汇总OEE是全称为Overall Equipment Effectiveness,中文名字叫做设备综合效能,是一种用于测量和评估设备性能的指标。
OEE的计算方式将设备的可用时间、性能效率和质量损失三个方面综合考虑,通过对设备的日常运行数据进行统计和分析,可以得出设备整体效率的量化指标。
OEE的计算方式如下:1. 设备的可用时间(Available Time):表示设备在规定时间段内应该可用的时间。
可用时间可以通过设备日历时间减去计划的停机时间和非计划的停机时间来计算。
可用时间=设备日历时间-计划停机时间-非计划停机时间2. 设备的性能效率(Performance Efficiency):表示设备在实际生产过程中的效率水平。
性能效率可以通过实际生产数量除以所需生产数量来计算。
性能效率=实际生产数量/所需生产数量3. 设备的质量损失(Quality Loss):表示设备生产过程中产生的质量损失。
质量损失可以通过实际良品数量除以实际生产数量来计算。
质量损失=实际良品数量/实际生产数量4.OEE的计算公式:OEE=可用时间×性能效率×质量损失OEE的计算结果可以是一个百分比值,表示设备整体的效率水平。
一般来说,高于85%的OEE被视为优秀,70%到85%的OEE被视为良好,低于70%的OEE被视为需要改进。
OEE的计算方式能够帮助企业发现设备运行中的问题和瓶颈,从而针对性地进行改进和优化。
通过准确地测量和评估设备的性能,企业能够找出并解决影响生产效率的因素,如设备故障、停机时间、性能不良等,从而提高设备的产能和生产效率。
除了OEE的计算方式,还有一些常见的OEE的改进方法包括:1.关键性能指标(KPIs)的设定和监控:设定关键性能指标,如设备的平均停机时间、停机次数、故障频率等,并定期监控这些指标的变化,从而及时发现并解决问题。
2.停机时间分析:对设备的停机时间进行分析,找出停机原因和停机时间的分布情况,从而确定采取适当的措施来减少停机时间。
OEE﹑MTBF﹑MTTR定定义及计算方法
7. 产品报 废或返修
品质 不良
性能 损失
5. 速度慢 6. 小停顿
计划停 机时间
当机时间
1. 设备故障 2. 模具故障 3. 换线调整 4. 暖机损失
•早会 •管理停止 •计划维护
时间稼动率=稼动时间 / 负荷时间 性能稼动率=净稼动时间 / 稼动时间=(理论周期*总产出量) / 稼动时间 良品率=价值稼动时间 / 净稼动时间= 良品数 / 总产出量 OEE=价值稼动时间/负荷时间=时间稼动率*性能稼动率*良品率
7. 产品报 废或返修
性能
损失 品质
不良 5. 速度慢 6. 小停顿
1. 设备故障 2. 模具故障 3. 换线调整 4. 暖机损失
•早会 •管理停止 •计划维护
时间稼动率=稼动时间 / 负荷时间 性能稼动率=净稼动时间 / 稼动时间=(理论周期*总产出量) / 稼动时间 良品率=价值稼动时间 / 净稼动时间= 良品数 / 总产出量 OEE1=价值稼动时间/负荷时间=时间稼动率*性能稼动率*良品率 OEE=OEE1 * 负荷时间 / 总投入时间
OEE定义及计算公式
1.5﹑ OEE计算公式
总投入时间
负荷时间
计划停 机时间
稼动时间
当机 时间
纯稼动时间
小停顿 损失
净稼动时间
速度 损失
5. 小停顿
价值稼动时间
品质 不良 7. 产品报
6. 速度慢
废或返修
•早会 •管理停止 •计划维护
1. 设备故障 2. 模具故障 3. 换线调整 4. 暖机损失
纯稼动率=纯稼动时间 / 稼动时间=(实际周期*总产出量) / 稼动时间 速度稼动率=净稼动时间 / 纯稼动时间=理论周期 / 实际周期
- 1、下载文档前请自行甄别文档内容的完整性,平台不提供额外的编辑、内容补充、找答案等附加服务。
- 2、"仅部分预览"的文档,不可在线预览部分如存在完整性等问题,可反馈申请退款(可完整预览的文档不适用该条件!)。
- 3、如文档侵犯您的权益,请联系客服反馈,我们会尽快为您处理(人工客服工作时间:9:00-18:30)。
维护、用餐等有 计划性的停机
计划性的停机时间,例如,班前班后15分钟,班中1小时吃饭时间、 周五周保养月保养时间等(以我厂为例:某天白班8小时,班前班后15分 钟,中午吃饭休息 1个小时,则可操作时间为 6.5个小时,即理论班产总 时间就是6.5个小时……
携手共赢
合作发展
再创辉煌
4
咸阳精密机械分公司设备能源科
合作发展
再创辉煌
9
咸阳精密机械分公司设备能源科
9
管理设备性能率的分析
净开动率= (加工数量×实际加工周期)/开动时间 速度开动率= 理论加工周期/实际加工周期
空转时间=加工数*(实际C/T-理论C/T)
速度损失/小停机=利用时间-加工数*实际C/T
净利用时间=利用时间-速度损失/小停机-空转时间 =利用时间-加工数*(实际C/T-理论C/T )-(利用时间-加工数*实际C/T) =利用时间-加工数*实际C/T+加工数*理论C/T –利用时间+加工数*实际C/T =加工数*理论CT
设备性能率=净利用时间/利用时间=加工数*理论CT/利用时间=加工数/利用时间*设计速度
携手共赢
合作发展
再创辉煌
10
咸阳精密机械分公司设备能源科
10
关于设备六大损失介绍 设备的六大损失
负荷时间 利用时间(运转时间) 净利用时间 速度损失 小停机、空转 停机时间 故障、调整
1、故障 2、切换、调整 3、启动、停机
携手共赢
合作发展
再创辉煌
7
咸阳精密机械分公司设备能源科
7
总结分析后的时间统计
日历总时间
正常出勤时间(所有上班时间)
节、假日
可操作时间(计算理论班产时间) 待料、待人 无动力 停机时间 故障、调整
计划性维护、用餐
负荷时间
利用时间(运转时间)
净利用时间
速度损失 小停机、空转
价值时间
废品时间
携手共赢
合作发展
4
何为可操作时间
可操作时间(计算理论班产时间) 负荷时间 待料、待人 无动力
“计算用理论班产总时间”
上面已经将理论班产总时间解释清楚,这个时间又分为两个部分:1)负荷时间;2)待料、 等人等时间。负荷时间下页讲。
待料、待人 无动力
计划外停机,无负荷停机……
携手共赢
合作发展
再创辉煌
5
咸阳精密机械分公司设备能源科
“OEE” OEE 是基于时间的衡量指标,我们的时间去哪了? 向时间要效率,首先建立这样的概念。
携手共赢
合作发展
再创辉煌
2
咸阳精密机械分公司设备能源科
2
何为“日历总时间”
日历总时间
正常出勤时间(所有生产时间) 节、假日
可利用时间
公司计划性停机
“何为日历总时间” 日历总时间是——用“从一个标准时间点到另一个标准时间点所经过的时间”来表示的时间, 例如:如1月有31天,每天有24小时等。 我们的日历总时间由两部分组成:1)正常出勤时间;2)节日、假日。
再创辉煌
8
咸阳精密机械分公司设备能源科
8
有关OEE的绩效指标
日历总时间
正常出勤时间(所有上班时间) 计划性活动 非生产时间 待料、待人 无动力 停机损失
公司计划性假期
可操作时间(计算理论班产时间)
负荷时间
利用时间(运转时间)
时间利用率
净利用时间
性能损失
设备性能率 产品合格率
价值时间
缺陷损失
携手共赢
5
关于狭义OEE的损失
负荷时间 利用时间(运转时间) 净利用时间 速度损失 小停机、空转 停机时间 故障、调整
1、故障 2、切换、调整 3、启动、停机
4、速度损失、小停机 5、空转
6、质量缺陷损失
价值时间
废品时间
定义损失(统计)
1、故障:未预料到的大于10分钟的设备故障停机(维修纪录) 2、切换:从换产开始(上一种产品生产结束)到下一种产品按要求生产出来(生产操作纪录) 调整:频繁的检测、调节、清理等以降低问题(例:质量缺陷)的发生(生产操作纪录) 3、启动:设备恢复后,重新开始生产至达到要求所经历的时间(生产操作纪录) 停机:从正常生产至设备完全停止所经历的时间,例如:热处理设备停机(生产操作纪录)
节、假日
实际放假时间:春节、周末、高温假……
携手共赢
合作发展
再创辉煌
3
咸阳精密机械分公司设备能源科
3
何为所有生产时间
正常出勤时间(所有生产时间) 可操作时间(计算理论班产时间) 维护、用餐等有 计划性的停机
“何为正常出勤时间” 正常出勤时间要分两部分理解:1)人的出勤时间;2)设备的出勤时间。例如:我厂员工 三班倒,员工每天正常出勤8小时,但对于设备出勤则是24小时(首先接受这样的概念)。 正常出勤时间由两部分组成:1)可操作时间(理论生产时间);2)计划性停机时间。 理论班产量核定:理论产量是指在各种条件最优化时,忽略各种操作误差、损耗所得出的 产量,注意实际班产量只能无限接近理论班产量,但绝不会高于班产量。注:有些不确定的损 耗时间(例如:工作期间喝水、如厕等)都要包含到理论班产总时间内。
4、速度损失、小停机 5、空转
6、质量缺陷损失
价值时间
携手共赢
合作发展
再创辉煌6
关于狭义OEE的损失
负荷时间 利用时间(运转时间) 净利用时间 空 转 速度损失 小停机 停机时间 故障、调整
负荷时间 利用时间(运转时间) 净利用时间 空 转 速度损失 小停机 停机时间 故障、调整
价值时间
空 转
废品时间
价值时间
废品时间
定义损失(统计) 4、速度:运行的操作速度低于该品种生产时的标准设计速度 5、小停机:未预料到的小于10分钟的设备停机(喝水、上厕所) 空转:实际CT与理论CT的时间差(空转时间+理论CT=实际 CT),包括人的动作,测量,通过人机协作统计、标准作业研究 人的动作可以减少空转 注:用左图净利用时间-空转时间=右图净利用时间 速度损失+小停机= 运转时间-(实际加工总数量*实际CT)= 右图净利用时间(包括空转时间) 空转时间= 实际加工总数量*(实际CT-理论CT)= 计算实际加工速度时人员辅助动作时间
咸阳精密机械分公司设备能源科
赵军强
(2014年度)
携手共赢
合作发展
再创辉煌
1
咸阳精密机械分公司设备能源科
1
OEE的时间分析
日历总时间
正常出勤时间(所有上班时间) 可操作时间(计算理论班产时间) 负荷时间 利用时间(运转时间) 净利用时间 价值时间 废品时间 速度损失 小停机、空转 停机时间 故障、调整 待料、待人 无动力 计划性维护、用餐 节、假日