OEE计算公式表教程文件
OEE计算公式范文

OEE计算公式范文OEE(Overall Equipment Effectiveness)是一种衡量设备综合效益的指标,常用于衡量生产线设备的运行效率和生产能力。
OEE的计算公式是:OEE = Availability × Performance × Quality其中,Availability(可用性)衡量设备在计划生产时间内真正可用的比例,Performance(性能率)衡量设备在可用时间内达到理论最高速度的比例,Quality(质量率)衡量设备生产出合格产品的比例。
具体计算公式如下:Availability = (计划生产时间 - 停机时间) / 计划生产时间Performance = (实际生产数量 / (计划生产时间 - 停机时间))/ 理论最高速度Quality = (合格产品数量 / 实际生产数量)OEE是一个综合指标,通过倍数相乘的方式,将设备的可用性、性能和质量三个方面综合考虑在内,从而得出设备的综合效益。
以下是对OEE计算公式的详细解释:1. Availability(可用性):可用性反映了设备是否按照计划进行生产的能力。
计算公式中的计划生产时间是指设备在一定周期内的累计时间,停机时间指设备由于故障、修理、更换等原因无法运行的时间。
可用性的计算结果通常为一个0到1之间的小数,1表示设备全天候稳定运行,0表示设备无法正常运行。
2. Performance(性能率):性能率反映了设备是否能够以最高速度进行生产。
实际生产数量指设备在可用时间内真实完成的产品数量,计划生产时间减去停机时间表示设备的可用时间。
理论最高速度是指设备在理想状态下的最高生产能力,通常以单位时间内的产品产量表示。
性能率的计算结果通常为一个0到1之间的小数,1表示设备以最高速度运行,0表示设备无法达到最高速度。
3. Quality(质量率):质量率反映了设备生产出合格产品的能力。
合格产品数量指设备在可用时间内生产的合格产品数量,实际生产数量是指设备在可用时间内真实完成的产品数量。
OEE计算公式+统计数据

设备稼动率 (实际稼动时间 ÷理论可稼动时
间)
实际投 入工时
(H)
19266 8354
43.36%
8354
94.33%
19266 8354
43.36%
8354
投入数/良
备注:
品数数据来 源于<OPE汇
总表>
实际稼动工
时/实际投
入工时/实
际产出有效
工时数据来
源于<日生
产报表>
设备理论可
稼动时间=
月份
ห้องสมุดไป่ตู้
投入数量 (pcs)
良品数量 (pcs)
1月 12229867 11536936 2月 3月 4月 5月 6月 7月 8月 9月 10月 11月 12月 合计 12229867 11536936
产品合格率 (良品数÷投入
数)
94.33%
2020年OEE数据统计
设备理论 可稼动时
间(H)
实际稼 动时间
设备机台数
×计划排产
天数×
19.5H
OEE数据统计
实际产出有效工 时
(实际产出÷标 准产能)
性能效率 (有效产出工时÷
实际投入工时)
OEE (产品合格率×设 备稼动率×性能效
率)
备注
10310
123.41%
50.48%
10310
123.41%
50.48%
2.OEE计算规则

0.083333333
正常损失 换型(模)
设备故障
模治具故障
异常损失 工艺异常
Байду номын сангаас
异常等待
其他损失
开机 时间
产能损失时间 合理产 不良品工时 能时间 合格品工时
1号下午安排保养4H 4H
3号下午试做4H
4H
换型5次,每次1H =1H/次*5
当月累计故障5H 5H
当月累计故障3H 3H
当月累计工艺异常4H 4H
当月累计待料2H 2H
吃饭 两餐,两个30分钟 =1H/D*26D
26
计划停机时间
开机点检 开机点检15分钟 首末件 检测15分钟
=0.25H/D*26D =0.25H/D*26D
6.5 6.5
53.5
F
2.广义OEE: =A/(A+B+C+D+E+F)
日 历 时 间
上 班 时 间
计 划 开 机 时 间
计划保养
新产品试做
当月累计其他损失1H 1H
当月累计产能损失10H10H
不良品折合工时5H 5H
合理产能时间
=30*24-以上
4 4 55 5 3 4 15 2 1 10 10 55 197.5 198
E
D 1.狭义OEE: =A/(A+B+C+D+E)
C B A
27.4% 69.1%
84.9%
说明 此表为对某机台30天内的各项时 间数据进行模拟,再推算出各项指 标
OEE定义依据分母时间范围不同 而不同,企业最初建议先选择狭义 OEE进行计算,即重点控制现场异 常、缩短换模时间
OA_OEE计算公式汇总_v2_0714 (2)

换大卷的时间=n*15,n为换大卷的次数,15是换卷时间的单位为分钟(换卷时间可以按精整机台维护),换卷的次数是根据班次内机台日志的BCT停机次数(只考虑计算次数,不考虑实际的时间)来统计。
成品长度=铝卷重量/2.71/铝卷实际宽度/铝卷的实际厚度(指每小卷)
成品长度:成品重量对应的长度,一轴的长度,一个小卷的长度
壁厚、铝卷宽度的单位为毫米,铝卷重量单位公斤,670是套筒外径,单位是毫米
铝卷重量是指出口重量,直接从系统中抓取
标准速度:同一各道次标准速度不同,手工在机台轧制前选择,同时默认值取前一个道次的标准速度。
BCT:标准换卷时间,每个机台有一个BCT
2、Shop OEE运算
Shop OEE=Avail.*Speed.E*uality
=[(480-停机时间)/(480-计划停机)]*[实际速度/标准速度]*[成品重量/(来料重量-计划损失重量)]
注:BCT(换卷时间)不属于停机时间,BCT采用机台标准BCT
停机时间:不包括标准BCT的实际停机时间
计划停机时间:待料、计划检修两种情况,根据停机编码判断是否为计划停机时间
有效运行时间=长度/标准速度+BCT(针对一个铝卷)
*[成品重量/(成品重量+成品报废重量+中间大卷废品重量)]/[(480-计划停机时间)]
注:BCT(换卷时间)不属于停机时间,BCT采用机台标准BCT
停机时间:不包括标准BCT的实际停机时间
计划停机时间:计划检修和放假两种情况,根据停机编码中的是计划还是非计划原因来判断。
每轴有效运行时间=成品长度/标准速度+6
2、Shop OEE运算
Shop OEE=Avail.*Speed.E*Quality
OEE计算公式
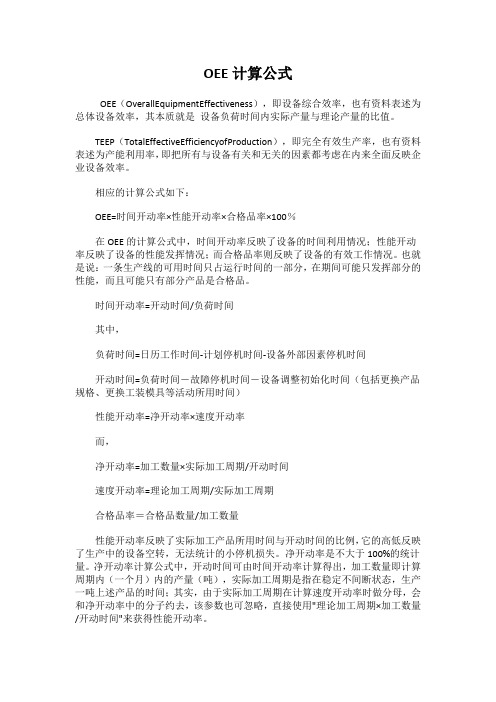
OEE计算公式OEE(OverallEquipmentEffectiveness),即设备综合效率,也有资料表述为总体设备效率,其本质就是设备负荷时间内实际产量与理论产量的比值。
TEEP(TotalEffectiveEfficiencyofProduction),即完全有效生产率,也有资料表述为产能利用率,即把所有与设备有关和无关的因素都考虑在内来全面反映企业设备效率。
相应的计算公式如下:OEE=时间开动率×性能开动率×合格品率×100%在OEE的计算公式中,时间开动率反映了设备的时间利用情况;性能开动率反映了设备的性能发挥情况;而合格品率则反映了设备的有效工作情况。
也就是说:一条生产线的可用时间只占运行时间的一部分,在期间可能只发挥部分的性能,而且可能只有部分产品是合格品。
时间开动率=开动时间/负荷时间其中,负荷时间=日历工作时间-计划停机时间-设备外部因素停机时间开动时间=负荷时间-故障停机时间-设备调整初始化时间(包括更换产品规格、更换工装模具等活动所用时间)性能开动率=净开动率×速度开动率而,净开动率=加工数量×实际加工周期/开动时间速度开动率=理论加工周期/实际加工周期合格品率=合格品数量/加工数量性能开动率反映了实际加工产品所用时间与开动时间的比例,它的高低反映了生产中的设备空转,无法统计的小停机损失。
净开动率是不大于100%的统计量。
净开动率计算公式中,开动时间可由时间开动率计算得出,加工数量即计算周期内(一个月)内的产量(吨),实际加工周期是指在稳定不间断状态,生产一吨上述产品的时间;其实,由于实际加工周期在计算速度开动率时做分母,会和净开动率中的分子约去,该参数也可忽略,直接使用"理论加工周期×加工数量/开动时间"来获得性能开动率。
原则上,理论加工周期不大于实际加工周期,即速度开动率是不大于100%的统计结果。
OEE介绍及计算方法

OEE定义及计算公式
五﹑速度损失定义
速度损失时间分为两部分﹕ 1﹑速度降低 2﹑空转和小停顿 分别定义如下﹕ • 速度降低
机器操作中与理论速度的差异造成的损 失时间。 • 空转和小停顿损失
制程中由于小的停顿(比如断料)导致的 生产损失。
稼动时间(=负荷时间-停机时间)
时间稼动率 =
出勤时间
性能稼动率 = 理论周期*加工数量
稼动时间
为了区分速度降低﹑小停顿对性能稼动率的影响﹐将性能稼动率 拆分为纯稼动率和速度稼动率﹐分别表达速度降低的影响和小停顿的 影响。
OEE定义及计算公式
纯稼动率是指设备在稼动时间内﹐以一定速度保持稳定﹑连续运 转的程度。以一定之速度运转这并不是与理论速度比快或慢﹐即 使本身速度比较慢﹐但要看是否能在长时间内保持安定的速度运 转。所以可以衡量因小停顿引起的损失﹐或在每日报表上看不出 来之微缺损失。
性能 稼动 率
纯稼动率 =(实际周期时间×加工数量)/稼动时间×100%
=×
速度稼动率 =理论周期/实际周期×100%
速度稼动率是指速度的差﹐对设备应具备的能力﹐与实 际速度比率。也就是判断是否以规定的速度进行运转。如 果设备的速度降低﹐会有多少损失。
良品数
良品率 = 总产出量
OEE定义及计算公式
= 时间稼动率 ×性能稼动率 ×良品率
OEE三大
设 备
模换暖 具线机
空速 转度
不 良
要素对应 故 故 调 损 与 降
件
的损失 障 障 整 失 小 低
停
顿
综合设备效率是从上述的时间性﹑性能﹑良率观察后得到的使 用有效率﹐来整体性进行设备评估的标准。
oee计算公式 excel
oee计算公式 excel(原创版)目录1.OEE 的定义和意义2.OEE 计算公式的构成3.如何在 Excel 中使用 OEE 计算公式4.OEE 计算公式的实际应用案例正文一、OEE 的定义和意义OEE(Overall Equipment Effectiveness,整体设备效率)是一种衡量生产设备效率的指标,它反映了生产设备的利用率、性能和质量。
OEE 的计算公式通常包括三个部分:生产时间、故障时间和计划停机时间。
通过计算 OEE,企业可以了解设备的运行状况,找出存在的问题,从而提高生产效率。
二、OEE 计算公式的构成OEE 的计算公式如下:OEE = (生产时间 / (生产时间 + 故障时间 + 计划停机时间)) x 100%其中,生产时间是设备正常运行的时间,故障时间是设备因故障停机的时间,计划停机时间是设备按照计划停机的时间。
百分比越高,说明设备的效率越高。
三、如何在 Excel 中使用 OEE 计算公式在 Excel 中,可以使用以下步骤计算 OEE:1.在 A1、B1、C1 单元格分别输入“生产时间”、“故障时间”和“计划停机时间”。
2.在 D1 单元格输入以下公式:`=IF(SUM(A1:C1)=0,0,SUM(A1:C1)/(A1+B1+C1)*100)`这个公式将计算 OEE 的百分比。
四、OEE 计算公式的实际应用案例假设一个企业有 10 台设备,每天工作 8 小时。
在计算 OEE 时,需要记录每台设备每天的生产时间、故障时间和计划停机时间。
将这些数据输入 Excel 后,可以使用上述公式计算每台设备每天的 OEE。
OEE的计算公式
OEE的计算公式(不考虑设备加工周期的差异)OEE= 时间开动率×性能开动率×合格品率其中,时间开动率= 开动时间/负荷时间而,负荷时间= 日历工作时间-计划停机时间开动时间= 负荷时间–故障停机时间–设备调整初始化时间(包括更换产品规格、更换工装模具、更换刀具等活动所用时间)性能开动率= 净开动率×速度开动率而,净开动率= 加工数量×实际加工周期/开动时间速度开动率= 理论加工周期/实际加工周期合格品率= 合格品数量/ 加工数量在OEE公式里,时间开动率反映了设备的时间利用情况;性能开动率反映了设备的性能发挥情况;而合格品率则反映了设备的有效工作情况。
反过来,时间开动率度量了设备的故障、调整等项停机损失,性能开动率度量了设备短暂停机、空转、速度降低等项性能损失;合格品率度量了设备加工废品损失。
例1: 设某设备1天工作时间为8h, 班前计划停机20min, 故障停机20min, 更换产品型号设备调整40min, 产品的理论加工周期为0.5min/件, 实际加工周期为0.8min/件,一天共加工产品400件, 有8件废品, 求这台设备的OEE。
计算:负荷时间= 480-20 = 460 min开动时间= 460 –20 –40 = 400 min时间开动率= 400/460 = 87%速度开动率= 0.5/0.8 = 62.5%净开动率= 400×0.8/400 = 80%性能开动率= 62.5%×80% = 50%合格品率= (400-8)/400 = 98% 于是得到OEE = 87%×50%×98% = 42.6%。
有些企业还可以根据生产的实际, 用便于统计的数据来推算TPM例2.设备负荷时间a = 100h,非计划停机10h,则实际开动时间为b = 90h;在开动时间内,计划生产c = 1000个单元产品,但实际生产了d = 900个单元;在生产的e = 900个单元中,仅有f = 800个一次合格的单元。
设备综合效率OEE计算公式和方法实例
设备综合效率OEE计算公式和方法实例影响设备综合效率的主要原因是停机损失、速度损失和废品损失。
它们分别由时间开动率、性开动率和合格品率反映出来,故得到下面设备综合效率公式:设备综合效率=时间开动率×性能开动率×合格品率这里,负荷时间为规定的作业时间除去每天的停机时间,即负荷时间=总工作时间-计划停机时间工作时间则是负荷时间除去那些非计划停机时间,如故障停机、设备调整和更换刀具、工夹具停机等。
【例1】若总工作时间为8h,班前计划停机时间是20min,而故障停机为20min,安装工夹具时间为20min,调整设备时间为20min。
于是负荷时间=480-20=460min开动时间=460-20-20=400min时间开动率=速度开动率×净开动率这里,理论加工周期是按照标准的加工进给速度计算得到的,而实际的加工周期一般要比理论加工周期长。
开动时间即是设备实际用于加工的时间,也就是工作时间减去计划停机和非计划停机所得时间,或是负荷时间减去非计划停机所得时间。
从计算上看,用简化了的公式也可以得到同样的结果。
之所以用速度开动率和净开动率共同表示性能开动率,是因为从计算过程更容易看出性能开动率的损失原因。
【例2】有400件零件加工,理论加工周期为0.5min,实际加工周期为0.8min。
则净开动率=0.8×400/400=80%速度开动率=0.5/0.8=62.5%性能开动率=80%×62.5%=50%【例3】如果仍延用上面的例子,假如设备合格品率为98%,则设备综合效率(全效率)=87%×50%×98%=42. 6%我们把上面的公式和例子总结成以下的序列,得到(A)每天工作时间=60×8=480min。
(B)每天计划停机时间(生产、维修计划、早晨会议等)=20min。
(C)每天负荷时间=A-B=460min。
(D)每天停机损失=60min(其中故障停机=20min,安装准备=20min,调整=20min)。
OEE的计算公式
OEE的计算公式OEE(Overall Equipment Effectiveness,设备综合效能)是一种用于衡量设备生产效率的标准指标,它综合评估了设备的开机时间、速度损失和质量损失。
OEE的计算公式如下:OEE = Availability × Performance × Quality其中Availability(可用性)表示设备在计划生产时间内处于正常运行状态的时间占比,即设备实际运行时间与计划生产时间的比率。
Performance(性能率)表示设备在正常运行状态下的产能利用率,即设备实际运行速度与设计速度的比率。
Quality(质量合格率)表示设备生产的合格产品的比例,即合格产品数量与总产出数量的比率。
1.可用性计算方法:可用性=实际运行时间/计划生产时间实际运行时间是设备实际处于正常运行状态的时间,不包括停机、换模、维修等非运行时间。
计划生产时间是设备在一段时间内的总计划生产时间,通常为24小时、一个班次或一个生产周期。
2.性能率计算方法:性能率=实际运行速度/设计速度实际运行速度是设备在正常生产运行状态下的实际生产速度。
设计速度是设备设计或规划时预期的最高生产速度。
3.质量合格率计算方法:质量合格率=合格产品数量/总产出数量合格产品数量是设备生产过程中符合质量标准的产品数量。
总产出数量是设备在一段时间内的总产出数量,包括合格产品和不合格产品的总和。
根据以上三个指标的计算结果,将它们乘积即可得到OEE的值。
OEE 的值在0到1之间,可通过乘以100转换为百分比。
OEE的计算公式能够全面评价设备的生产效率,并反映出设备在运行过程中的各种损失。
通过监测和分析OEE的数值,企业可以了解设备性能的实际状况,找出潜在问题和改进机会,并采取相应的措施提高生产效率和质量水平。
- 1、下载文档前请自行甄别文档内容的完整性,平台不提供额外的编辑、内容补充、找答案等附加服务。
- 2、"仅部分预览"的文档,不可在线预览部分如存在完整性等问题,可反馈申请退款(可完整预览的文档不适用该条件!)。
- 3、如文档侵犯您的权益,请联系客服反馈,我们会尽快为您处理(人工客服工作时间:9:00-18:30)。
17
16
17
#DIV/0! #DIV/0!
#DIV/0! #DIV/0!
#DIV/0! #DIV/0!
#DIV/0! #DIV/0!
#DIV/0! #DIV/0!
0
0
0
0
0
0
0
0
0
0
0
0
0
0
0
0
0
0
0
0
0
0
0
0
0
0
0
0
0
0
0
0
0
0
0
0
0
0
0
当 机 时 间
品质异常处理
人员请假
其他
稼动时间
0
0
0
0
0
0
T/T(理论节拍) 总产出
总不良数
0
0
0
0
0
备注: 公式自动计算
手动填写
7
8
9
10
11
12
13
14
15
7
8
9
10
11
12
13
14
15
#DIV/0! #DIV/0! #DIV/0! #DIV/0! #DIV/0! #DIV/0! #DIV/0! #DIV/0! #DIV/0!
#DIV/0! #DIV/0! #DIV/0! #DIV/0! #DIV/0! #DIV/0! #DIV/0! #DIV/0! #DIV/0!
0
0
0
0
0
0
00Leabharlann 0000
0
0
0
0
0
0
0
0
0
0
0
0
0
0
0
0
0
0
0
0
0
0
0
0
OEE(%) OEE1(%) 时间稼动率(%) 性能稼动率(%) 成品率(%)
16
#DIV/0! #DIV/0! #DIV/0! #DIV/0! #DIV/0! #DIV/0! #DIV/0! #DIV/0! #DIV/0!
#DIV/0! #DIV/0! #DIV/0! #DIV/0! #DIV/0! #DIV/0! #DIV/0! #DIV/0! #DIV/0!
#DIV/0! #DIV/0! #DIV/0! #DIV/0! #DIV/0! #DIV/0! #DIV/0! #DIV/0! #DIV/0!
#DIV/0! #DIV/0! #DIV/0! #DIV/0! #DIV/0! #DIV/0!
#DIV/0! #DIV/0! #DIV/0! #DIV/0! #DIV/0! #DIV/0!
#DIV/0! #DIV/0! #DIV/0! #DIV/0! #DIV/0! #DIV/0!
#DIV/0! #DIV/0! #DIV/0! #DIV/0! #DIV/0! #DIV/0!
110.0%
100.0%
90.0%
80.0%
70.0%
60.0%
50.0%
1
2
3
4
5
6
生产线别
OEE(%)
OEE1(%)
时间稼动率(%)
性能稼动率(%)
成品率(%)
总工时(分钟)
计划 停机 时间
休息 打扫 培训 计划停止
负荷时间
换模换线
机械故障
搬运
当
机
量检设备
时
材料异常
间
1
2
3
4
5
6
#DIV/0! #DIV/0! #DIV/0! #DIV/0! #DIV/0! #DIV/0!