离子注入和快速退火工艺处理
半导体工艺与制造技术习题答案(第四章 离子注入)
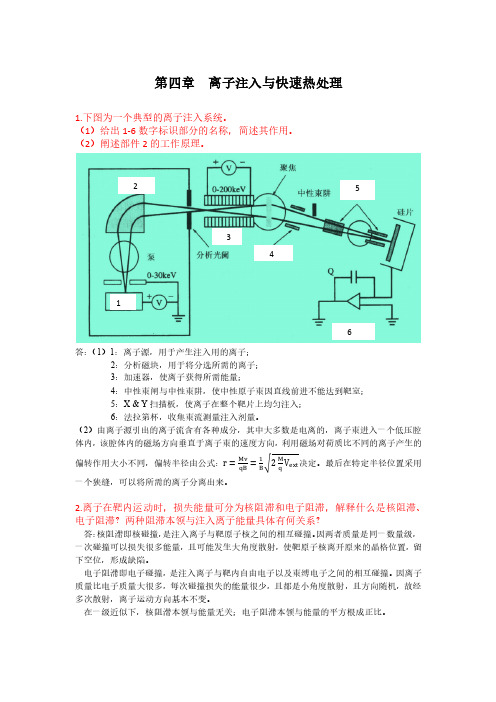
第四章 离子注入与快速热处理1.下图为一个典型的离子注入系统。
(1)给出1-6数字标识部分的名称,简述其作用。
(2)阐述部件2的工作原理。
答:(1)1:离子源,用于产生注入用的离子;2:分析磁块,用于将分选所需的离子;3:加速器,使离子获得所需能量;4:中性束闸与中性束阱,使中性原子束因直线前进不能达到靶室; 5:X & Y 扫描板,使离子在整个靶片上均匀注入;6:法拉第杯,收集束流测量注入剂量。
(2)由离子源引出的离子流含有各种成分,其中大多数是电离的,离子束进入一个低压腔体内,该腔体内的磁场方向垂直于离子束的速度方向,利用磁场对荷质比不同的离子产生的偏转作用大小不同,偏转半径由公式:决定。
最后在特定半径位置采用一个狭缝,可以将所需的离子分离出来。
2.离子在靶内运动时,损失能量可分为核阻滞和电子阻滞,解释什么是核阻滞、电子阻滞?两种阻滞本领与注入离子能量具体有何关系?答:核阻滞即核碰撞,是注入离子与靶原子核之间的相互碰撞。
因两者质量是同一数量级,一次碰撞可以损失很多能量,且可能发生大角度散射,使靶原子核离开原来的晶格位置,留下空位,形成缺陷。
电子阻滞即电子碰撞,是注入离子与靶内自由电子以及束缚电子之间的相互碰撞。
因离子质量比电子质量大很多,每次碰撞损失的能量很少,且都是小角度散射,且方向随机,故经多次散射,离子运动方向基本不变。
在一级近似下,核阻滞本领与能量无关;电子阻滞本领与能量的平方根成正比。
1 2 3 4 563.什么是离子注入横向效应?同等能量注入时,As和B哪种横向效应更大?为什么?答:离子注入的横向效应是指,注入过程中,除了垂直方向外,离子还向横向掩膜下部分进行移动,导致实际注入区域大于掩膜窗口的效应。
B的横向效应更大,因为在能量一定的情况下,轻离子比重离子的射程要深且标准差更大。
4.热退火用于消除离子注入造成的损伤,温度要低于杂质热扩散的温度,然而,杂质纵向分布仍会出现高斯展宽与拖尾现象,解释其原因。
离子注入工艺流程
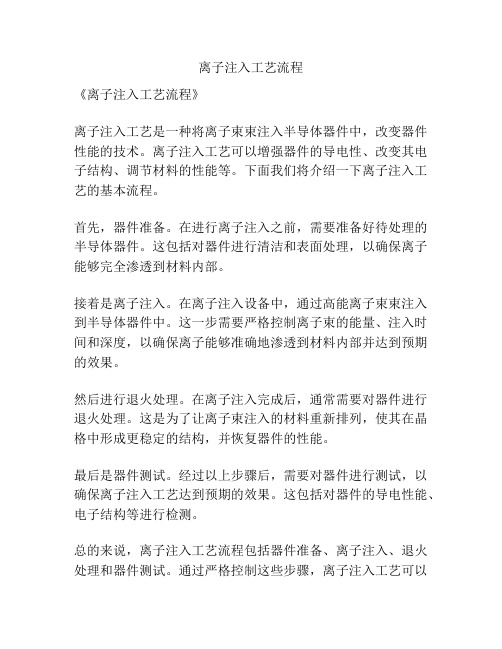
离子注入工艺流程
《离子注入工艺流程》
离子注入工艺是一种将离子束束注入半导体器件中,改变器件性能的技术。
离子注入工艺可以增强器件的导电性、改变其电子结构、调节材料的性能等。
下面我们将介绍一下离子注入工艺的基本流程。
首先,器件准备。
在进行离子注入之前,需要准备好待处理的半导体器件。
这包括对器件进行清洁和表面处理,以确保离子能够完全渗透到材料内部。
接着是离子注入。
在离子注入设备中,通过高能离子束束注入到半导体器件中。
这一步需要严格控制离子束的能量、注入时间和深度,以确保离子能够准确地渗透到材料内部并达到预期的效果。
然后进行退火处理。
在离子注入完成后,通常需要对器件进行退火处理。
这是为了让离子束注入的材料重新排列,使其在晶格中形成更稳定的结构,并恢复器件的性能。
最后是器件测试。
经过以上步骤后,需要对器件进行测试,以确保离子注入工艺达到预期的效果。
这包括对器件的导电性能、电子结构等进行检测。
总的来说,离子注入工艺流程包括器件准备、离子注入、退火处理和器件测试。
通过严格控制这些步骤,离子注入工艺可以
有效地改善半导体器件的性能,为半导体工业的发展提供重要支持。
【doc】离子注入工艺简介
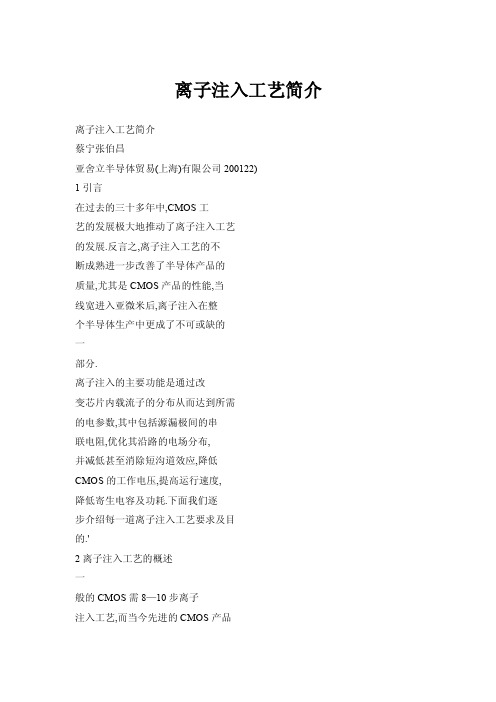
离子注入工艺简介离子注入工艺简介蔡宁张伯昌亚舍立半导体贸易(上海)有限公司200122)1引言在过去的三十多年中,CMOS工艺的发展极大地推动了离子注入工艺的发展.反言之,离子注入工艺的不断成熟进一步改善了半导体产品的质量,尤其是CMOS产品的性能,当线宽进入亚微米后,离子注入在整个半导体生产中更成了不可或缺的一部分.离子注入的主要功能是通过改变芯片内载流子的分布从而达到所需的电参数,其中包括源漏极间的串联电阻,优化其沿路的电场分布,并减低甚至消除短沟道效应,降低CMOS的工作电压,提高运行速度,降低寄生电容及功耗.下面我们逐步介绍每一道离子注入工艺要求及目的.'2离子注入工艺的概述一般的CMOS需8—10步离子注入工艺,而当今先进的CMOS产品更需20多步离子注入.根据在场效应管的位置,离子注入工艺可分为三大块:1)沟道区及井区(Channe1 andWel1)掺杂;2)多晶硅(Poly)注入:3)源漏区(SourceDrain)注入.2.1沟道及井区掺杂沟道区及井区的掺杂主要有阈值电压调节(V+Adjust)注入,反穿通(Anti-punchthrough)注入,埋层(BuriedLayer)注入,井问绝缘注入(Channe1Stop),井区反型(RetrogradeWel1)注入及吸收(Gettering)注入.这部分注入工艺的能量比较宽,但剂量属中低范围,所以此部分注入工艺基本上使用中束流及高能注入机.2.1.1阈值电压调节注入工艺(V.Adjust)阈值电压调节注入工艺是半导体工业中使用最早的离子注入技术工艺.由于在CMOS中N型井与P型井共存,它们的功能电压会有不同,V+ 注入是将所需的元素掺杂在门下方的沟道区内,改变电荷而得到所需的工作电压,使这两种井区共用一个闸门电压.高性能产品的N井区里传统的硼掺杂逐渐被铟(indium)注入所代替,其目的是使载子浓度分布更陡,以提高开关速度并降低功耗.2.1.2反击通注入工艺(Ant1一Dunchthr0ugh)该注入工艺的功能是防止源漏两极在沟道下面导通,因PN结深与载流子浓度成反比,如果沟道下部载流子浓度很低,在细线宽情况下源漏之间的PN结就会靠很近而容易被击通,增加此区域的载流子浓度就是为了降低耗尽层的厚度,使源漏不会在沟道下面导通,所以此注入要比阈值电压调节注入要更深一些.2.1.3井间绝缘注入工艺(Channel Stop)井间绝缘的注入是将杂质掺在用于隔开井区的绝缘栏的下方,此目的是为了提高井间寄生场效应管的阈值电压,使在正常的工作情形下此寄生三极管不会被导通而起到绝缘的效果.2.1.4埋层注入工艺(BuriedLayer)该工艺是要降低井区底部的电阻,以防芯片在运行中出现死循环(Latch—up)现象.井区内二个寄生的三极管(NPN&PNP)在一定的条件下可变成一个PNPN可控硅而形成自锁,埋层注入可降低PNP--极管的输出电阻,抬高死循环引发电流而彻底消除死循环现象.2.1.5吸取注入工艺(Gettering)它是在CM0S离子注入中能量最高的工艺,其目的是利用所注入的元素的化学特性和注后所形成的缺陷的物理特性来吸收井区里的其它杂质(如:重金属等)及晶格缺陷,以提高井区内,尤其是沟道区内的材料质量来提升产品性能.离子注入晶体后与原子核碰撞的可能性是和离子本身的能量成反比,所以在高能注入的条件下,有些轻元素如硼及磷,因注入而产生的缺陷分布与注入元素的分布极为接近,利用这—特性离子注入就可在所需的地方将晶格破坏,此外利用硼与磷的化学特性也可将重金属元素吸收.2.1.6反型井区注入工艺(RetrogradeWel1)在早期此工艺由炉管扩散或注入后驱动扩散而完成,但其不能在井区内形成优化的载流子分布,高性能的芯片要求硅片表面的载流子浓度低,而在硅片深度的某些部位要浓,这样既能提高芯片的运行速度,又能达到以上所述的反穿通,抑制死循环及吸取污染杂质的效果.由于在扩散时载流子的浓度是从硅片表面逐步向硅片内部降低的连续分布,这样的分布势必影响到硅片表面载流子的移动集虞电?蠢用2o年9居●■率而降低芯片的运营速度,为提高芯片的功能离子注入就成了必不可少的手段,新一代的CMOS技术已全部使用离子注入方式,当今的CMOS技术更采用双井反型工艺(Twin Retrogradewel1),它综合了以上所讨论的阈值电压调节注入,反穿通注入,井问绝缘注入,及埋层注入,构成一个完整的反型井层注入工艺链. 亚舍立科技(Axcelis)公司的高能注入机的设计,可提供连续注入(ChainImplant)技术,即将这些注入工艺步骤在一次装片中连续注入,这样既可提高产量,降低成本,还可提高产品性能,降低在硅片上的尘粒总数量.2.2多晶硅注入此注入工艺是为了降低多晶硅的电阻,是CMOS注入工艺中注入剂量最大的工艺.有的制成在长多晶硅的同时已掺入所需的元素,假如长多晶硅时没有掺杂,则要做多晶硅注入,再进行退火,注入后的元素在退火时在多晶硅中的扩散率与单晶硅相比会高出二个数量级,因此掺杂后的多晶硅的阻值与非掺杂的多晶硅相比会有大幅度的下降.此工艺因剂量很大,能量较低,在生产中一般都采用大束流离子注入机. 2.3源漏区注入工艺源漏区注入主要包括大角度晕环(Halo)注入,延伸(Extension)注入,源漏(Source—drain)及非晶体化(Pre-amorphouse)注入,此部分工艺技术要求越来越高,并与注入后的退火工艺有着密切的联系. 该部分的注入工艺其能量相对较低, 但剂量属中高范围,一般采用中束流及大束流注入机.2.3.1大角度注入工艺(Halo)Halo是大角度(>20度)四方向的中剂量离子注入工艺,它的主要功能是防止源漏相通,降低延伸区的结深及缩短沟道长度,有利于提高芯片的性能,一般在延伸注入工艺之后注入.为了使载流子分布更陡,以更有效的防止短沟道效应,最新的掺杂技术是用锑来替代砷,用铟来替代硼.2.3.2延伸注工艺(Extension)它先前也称作低剂量掺杂(LDD),它是在CMOS中注入能量最低的工艺,其作用是优化源漏问的电场分布,降低最高电场,在高阻与电阻区之间起一个衔接作用.其剂量随着沟道缩短而增加.线宽的变窄要求延伸区的结深越来越浅,晕环注入可对此有帮助.但还不够,尤其对n+井区,唯一可用的注入元素是质量很轻的硼,或稍高的BF,并在退火时由于存在过渡性扩散(TED),硼在退火时的扩散率很高,这就更要求注入的能量要非常低,所以如何在延伸区形成浅结是近年来注入工业界的最大课题.2.3.3源漏注入工艺(source-drain)源漏注入的剂量很大,是降低场效应管串型电阻的重要一环.与延伸注入工艺一样,现在源漏注入最大挑战是如何形成具有一定导电率的浅结,这是一个离子注入与快速退火的工艺优化问题,但最基本的要求是低能量注入.因其要求的剂量很大,这对离子注入机的生产率是一大考验,如何设计出在低能时能产生高电流是每个离子注入厂家的努力方向.2.3.4非晶体化注入工艺((pre-amorphouse)在源漏区还有一种注入工艺被有些厂家所采用,它就是非晶体化注入工艺,其注入元素主要有锗(Ge)和硅(Si),其中锗的使用比较广泛一些,因为其原子重量大,容易达到非晶体化效果,并能降低源漏区的接触电阻.非晶体化的目的主要是防止下—步注入的沟道效应,并可降低在退火时其掺杂元素激活的激活能.其不利之处在于难于消除在晶体与非晶体界面层的缺陷因而增加源漏区的漏电.3总结离子注入工艺的优化就是选择所需的掺杂元素和注入的能量,剂量及角度的过程,当今的离子注入工艺无论是从能量还是剂量涵盖很广,所以对设备的要求可大致分为高能,大束流及中束流.设备的合理选择及搭配就是要既能满足工艺要求,又能达到高效低成本的目的.亚舍立科技(Axcelis)公司是当今全球唯—提供整合注入相关工艺配套的半导体设备商,产品种类包括光刻胶定型机,去胶机,快速退火炉及全套离子注入系统,包括具有低能量功能的大束流注入机,中束流注入机及高能注入机,并可为用户提供整套设备和工艺服务.-■集成电路应用2oo2年9月。
sic加工过程中的高温离子注入法的原理
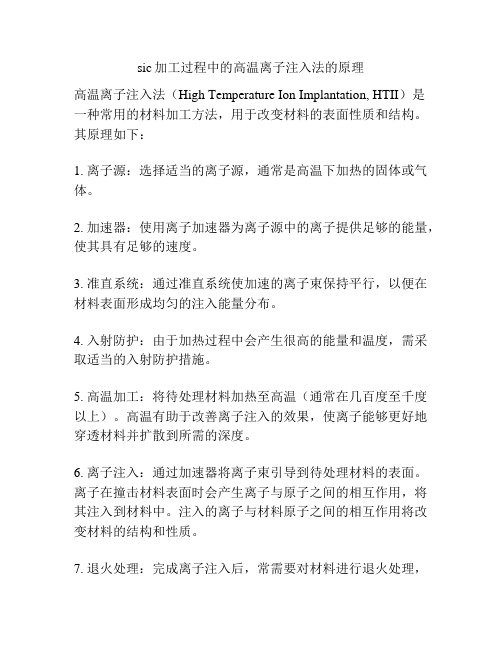
sic加工过程中的高温离子注入法的原理
高温离子注入法(High Temperature Ion Implantation, HTII)是
一种常用的材料加工方法,用于改变材料的表面性质和结构。
其原理如下:
1. 离子源:选择适当的离子源,通常是高温下加热的固体或气体。
2. 加速器:使用离子加速器为离子源中的离子提供足够的能量,使其具有足够的速度。
3. 准直系统:通过准直系统使加速的离子束保持平行,以便在材料表面形成均匀的注入能量分布。
4. 入射防护:由于加热过程中会产生很高的能量和温度,需采取适当的入射防护措施。
5. 高温加工:将待处理材料加热至高温(通常在几百度至千度以上)。
高温有助于改善离子注入的效果,使离子能够更好地穿透材料并扩散到所需的深度。
6. 离子注入:通过加速器将离子束引导到待处理材料的表面。
离子在撞击材料表面时会产生离子与原子之间的相互作用,将其注入到材料中。
注入的离子与材料原子之间的相互作用将改变材料的结构和性质。
7. 退火处理:完成离子注入后,常需要对材料进行退火处理,
以消除应力和恢复材料的结构和性能。
通过高温离子注入法,可以实现对材料的改性和改良,如改变材料的化学成分、增强材料的硬度、改善表面光滑度等。
八大半导体工艺顺序剖析

八大半导体工艺顺序剖析八大半导体工艺顺序剖析在现代科技领域中,半导体材料和器件扮演着重要的角色。
作为电子设备的基础和核心组件,半导体工艺是半导体制造过程中不可或缺的环节。
有关八大半导体工艺顺序的剖析将会有助于我们深入了解半导体制造的工作流程。
本文将从简单到复杂,逐步介绍这八大工艺的相关内容。
1. 排版工艺(Photolithography)排版工艺是半导体制造过程中的首要步骤。
它使用光刻技术,将设计好的电路图案转移到硅晶圆上。
排版工艺需要使用光刻胶、掩膜和曝光设备等工具,通过逐层叠加和显影的过程,将电路图案转移到硅晶圆上。
2. 清洗工艺(Cleaning)清洗工艺在排版工艺之后进行,用于去除光刻胶和其他污染物。
清洗工艺可以采用化学溶液或高纯度的溶剂,保证硅晶圆表面的干净和纯净。
3. 高分辨率电子束刻蚀(High-Resolution Electron BeamLithography)高分辨率电子束刻蚀是一种先进的制造技术。
它使用电子束在硅晶圆表面进行刻蚀,以高精度和高分辨率地制作微小的电路图案。
4. 电子束曝光系统(Electron Beam Exposure Systems)电子束曝光系统是用于制造高分辨率电子束刻蚀的设备。
它具有高能量电子束发射器和复杂的控制系统,能够精确控制电子束的位置和强度,实现微米级别的精细曝光。
5. 高能量离子注入(High-Energy Ion Implantation)高能量离子注入是半导体器件制造中的一项重要工艺。
通过将高能量离子注入到硅晶圆表面,可以改变硅晶圆的电学性质,实现电路中的控制和测量。
6. 薄膜制备与沉积(Film Deposition)薄膜制备与沉积是制造半导体器件的关键工艺之一。
这个工艺将薄膜材料沉积在硅晶圆表面,包括化学气相沉积、物理气相沉积和溅射等方法。
这些薄膜能够提供电介质、导电材料或阻挡层等功能。
7. 设备和工艺完善(Equipment and Process Optimization)设备和工艺完善的步骤是优化半导体制造工艺的关键。
5.6 离子注入的损伤与退火[7页]
![5.6 离子注入的损伤与退火[7页]](https://img.taocdn.com/s3/m/69f7c02e2b160b4e777fcf09.png)
行处理。注入硅片的火通常在通入Ar或N2的快速热处理机中进行。
快速热退火 RTA
特点:快速的升温和 短暂的持续时间能够 在晶格缺陷修复,激 活杂质和最小化杂质 再分布三者之间取得
优化。
离子注入机的组成及工作原理 离子注入的损伤与退火
§5.6 离子注入损伤与退火工艺
一、退火的作用:
消除晶损伤 ➢ 撞离错位的硅原子重新回到
晶格位置。 激活杂质 ➢ 杂质取代硅原子占据晶格点
,成为施、受主杂质。
二、退火的方法:
高温热退火: 用高温炉把硅片加热至800-1000℃ 并保持30分钟 特点:方法简单,设备兼容,但高温长时间易导致杂质的再扩散
集成电路制造工艺
--离子注入机的损伤与退火
单位:江苏信息职业技术学院 微电子教研室
本章 要点
第五章 掺杂
扩散的基本原理 扩散方法
扩散层的质量参数与检测 离子注入的基本原理
离子注入机的组成及工作原理 离子注入的损伤与退火
本章 要点
第五章 掺杂
扩散的基本原理 扩散方法
扩散层的质量参数与检测 离子注入的基本原理
半导体八大工艺顺序
半导体八大工艺顺序半导体八大工艺顺序,是指半导体制造过程中的八个主要工艺步骤。
这些工艺步骤包括晶圆清洗、光刻、沉积、刻蚀、扩散、离子注入、退火和包封。
下面将逐一介绍这些工艺步骤的顺序及其作用。
1. 晶圆清洗晶圆清洗是半导体制造过程中的第一步。
在这一步骤中,晶圆将被放入化学溶液中进行清洗,以去除表面的杂质和污染物。
这样可以确保后续工艺步骤的顺利进行,同时也可以提高器件的质量和性能。
2. 光刻光刻是半导体制造中的关键工艺步骤之一。
在这一步骤中,将使用光刻胶覆盖在晶圆表面上,并通过光刻机将图形投射到光刻胶上。
然后,利用化学溶液将未曝光的光刻胶去除,从而形成所需的图形。
3. 沉积沉积是指在晶圆表面上沉积一层薄膜的工艺步骤。
这一层薄膜可以用于改变晶圆表面的性质,增加其导电性或绝缘性。
常用的沉积方法包括化学气相沉积和物理气相沉积。
4. 刻蚀刻蚀是将多余的材料从晶圆表面去除的工艺步骤。
在这一步骤中,利用化学溶液或等离子刻蚀机将不需要的材料去除,从而形成所需的图形和结构。
5. 扩散扩散是将杂质或掺杂物diffused 到晶圆中的工艺步骤。
这一步骤可以改变晶圆的电学性质,并形成PN 结等器件结构。
常用的扩散方法包括固体扩散和液相扩散。
6. 离子注入离子注入是将离子注入到晶圆中的工艺步骤。
这可以改变晶圆的导电性和掺杂浓度,从而形成电子器件的结构。
离子注入通常在扩散之前进行。
7. 退火退火是将晶圆加热至一定温度并保持一段时间的工艺步骤。
这可以帮助晶圆中的杂质扩散和掺杂物活化,从而提高器件的性能和稳定性。
8. 包封包封是将晶圆封装在外部保护材料中的工艺步骤。
这可以保护晶圆不受外部环境的影响,同时也可以方便晶圆的安装和使用。
半导体制造过程中的八大工艺顺序是一个复杂而精密的过程。
每个工艺步骤都起着至关重要的作用,只有严格按照顺序进行,才能生产出高质量的半导体器件。
希望通过本文的介绍,读者对半导体制造过程有了更深入的了解。
离子注入退火的作用
离子注入退火的作用离子注入退火是一种常见的材料处理方法,其作用是通过注入离子并进行退火处理,来改善材料的性能。
离子注入退火可以用于改善材料的导电性、硬度、化学稳定性和抗腐蚀性等方面的性能。
离子注入是指将离子束注入到材料表面或内部,以改变材料的化学组成和结构。
离子注入通常通过离子源产生离子束,并通过加速电场将离子束加速到高能量,然后通过聚焦系统将离子束聚焦到所需位置。
离子束中的离子通过与材料原子的相互作用,改变了材料的晶格结构和化学组成。
离子注入退火的主要目的是通过加热材料来改变其结构和性能。
退火是指将材料加热到一定温度,保持一段时间后再冷却到室温。
退火过程中,材料的晶格结构会发生重排和再结晶,从而改变材料的物理和化学性质。
离子注入退火可以改善材料的导电性。
通过注入特定的离子,可以改变材料的电子结构,增加电子的迁移率,从而提高材料的导电性。
这在半导体工业中非常重要,因为半导体器件的性能很大程度上取决于材料的导电性能。
离子注入退火还可以改善材料的硬度。
通过注入高能量的离子并进行退火处理,可以在材料中形成大量的缺陷和位错,从而增加材料的硬度。
这对于一些需要高硬度的应用非常关键,比如切削工具和汽车发动机零件等。
离子注入退火还可以提高材料的化学稳定性和抗腐蚀性。
通过改变材料的化学组成和晶格结构,可以增强材料的抗腐蚀能力,使其能够在恶劣的环境下长时间保持稳定。
这对于一些需要在高温、高压或腐蚀性环境中使用的材料非常重要。
离子注入退火是一种常见的材料处理方法,通过注入离子并进行退火处理,可以改善材料的导电性、硬度、化学稳定性和抗腐蚀性等方面的性能。
离子注入退火在半导体工业、材料科学和工程领域中有着广泛的应用前景。
通过不断研究和发展,离子注入退火技术将进一步推动材料科学和工程的发展,为我们创造更加先进和高性能的材料。
硅集成电路基本工艺流程简介
硅集成电路基本工艺流程简介近年来,日新月异的硅集成电路工艺技术迅猛发展,一些新技术、新工艺也在不断地产生,然而,无论怎样,硅集成电路制造的基本工艺还是不变的。
以下是关于这些基本工艺的简单介绍。
IC制造工艺的基本原理和过程IC基本制造工艺包括:基片外延生长、掩模制造、曝光、氧化、刻蚀、扩散、离子注入及金属层形成。
一、硅片制备(切、磨、抛)1、晶体的生长(单晶硅材料的制备):1) 粗硅制备: SiO2+2H2=Si+2H2O99%经过提纯:>99.999999%2) 提拉法基本原理是将构成晶体的原料放在坩埚中加热熔化,在熔体表面接籽晶提拉熔体,在受控条件下,使籽晶和熔体的交界面上不断进行原子或分子的重新排列,随降温逐渐凝固而生长出单晶体.2、晶体切片:切成厚度约几百微米的薄片二、晶圆处理制程主要工作为在硅晶圆上制作电路与电子元件,是整个集成电路制造过程中所需技术最复杂、资金投入最多的过程。
功能设计à模块设计à电路设计à版图设计à制作光罩其工艺流程如下:1、表面清洗晶圆表面附着一层大约2um的Al2O3和甘油混合液保护之,在制作前必须进行化学刻蚀和表面清洗。
2、初次氧化有热氧化法生成SiO2 缓冲层,用来减小后续中Si3N4对晶圆的应力氧化技术干法氧化Si(固) + O2 àSiO2(固)湿法氧化Si(固) +2H2O àSiO2(固) + 2H23、CVD法沉积一层Si3N4。
CVD法通常分为常压CVD、低压CVD 、热CVD、电浆增强CVD及外延生长法(LPE)。
着重介绍外延生长法(LPE):该法可以在平面或非平面衬底上生长出十分完善的和单晶衬底的原子排列同样的单晶薄膜的结构。
在外延工艺中,可根据需要控制外延层的导电类型、电阻率、厚度,而且这些参数不依赖于衬底情况。
4、图形转换(光刻与刻蚀)光刻是将设计在掩模版上的图形转移到半导体晶片上,是整个集成电路制造流程中的关键工序,着重介绍如下:1)目的:按照平面晶体管和集成电路的设计要求,在SiO2或金属蒸发层上面刻蚀出与掩模板完全对应的几何图形,以实现选择性扩散和金属膜布线。
离子注入介绍
掺杂,曝光,刻蚀,镀膜,退火,净化,改性,打孔,切割,等。不同 的用途需要不同的离子能量E,
E<10Kev 刻蚀,镀膜 E:10~50Kev 曝光 E>50Kev 注入掺杂
概述
离子注入工艺是IC制造中占主导的掺杂技术
离子注入:将杂质离化,通过电场加速,将这些离化的杂质直接 打入晶元中,达到掺杂的目的
共晶合金LMIS
通常用来对各种半导体进行离子注入掺杂的元素,因为熔点高或蒸气压高而无法制成单体LMIS。
根据冶金学原理,由两种或者多种金属组成的合金,其熔点会大大低于组成这种合金的单体金属 的熔点,从而可大大降低合金中金属处于液态时的蒸气压。
例如,金和硅的熔点分别为1063℃和1404℃,他们在此温度的蒸气压分别为1e-3Torr和1e-1Torr。 当以适当的组分组成合金时,其熔点降为370℃,在此温度下,金和硅的蒸气压分别仅为1e22Torr和1e-19Torr。这就满足了LMIS的要求。
加速方式: 先加速后分析 前后加速,中间分析 第二种方式比较常见
聚焦系统和中性束偏移器
5.偏转扫描系统
用来使离子束沿X,Y方向在一定面积内进行扫描 静电光栅扫描,适于中低束流机 机械扫描,适于强束流机
离子束电流的测量
法拉第杯:捕获进入的电荷,测量离子电流 注入剂量:
当一个离子的荷电量为m时,注入剂量为:
两种质量分析器的对比:
在E×B质量分析器中,所需离子不改变方向,但在输出的离子束中容易含有中性粒子,磁质量分析 器则相反,所需离子需要改变方向,但其优点是中性粒子束不能通过。
离子加速器
产生高压静电场,用来对离子 加速。该加速能量是决定离子 注入深度的一个重要参量,一 般需要<1e-6Torr的真空环境
- 1、下载文档前请自行甄别文档内容的完整性,平台不提供额外的编辑、内容补充、找答案等附加服务。
- 2、"仅部分预览"的文档,不可在线预览部分如存在完整性等问题,可反馈申请退款(可完整预览的文档不适用该条件!)。
- 3、如文档侵犯您的权益,请联系客服反馈,我们会尽快为您处理(人工客服工作时间:9:00-18:30)。
11 高能量与大电流注入
注入机能量可高达1.5-5MeV,且已用作多种新型用途。主要利用其能将杂质掺入半导体内深达好几个微米的能力而不需要借助高温下长时间的扩散。也可用于制作低电阻埋层。例如,CMOS器件中距离表面深达1.5到3um的埋层。
衬底定位时有意偏离晶向情况下的杂质分布。离子束从<111>轴偏离7度入射。
指数型尾区与离子注入沟道效应有关,当入射离子对准一个主要的晶向
并被导向在各排列晶体原子之间时,沟道效应就会发生。图为沿<110>方向观测金刚石晶格的示意图。离子沿<110>方向入射,因为它与靶原子较远,使它在和核碰撞时不会损伤大量能量。对沟道离子来说,唯一的能量损伤机制是电子阻止,因此沟道离子的射程可以比在非晶硅靶中大得多。
2.8 离子注入主要参数:
离子注入的几何说明:
α:离子束注入面
∑ :表面
β:模拟的平面
θ:离子束方向与y轴方向的夹角
φ:离子束与模拟平面之间的夹角
参数说明:
Species:注入的杂质种类
Energy:注入能量(KeV)
Dose:注入剂量,单位cm-2
Tilt:离子束注入的纵向角度,默认值是7º
Rotation:离子束与模拟平面之间的夹角,默认值是30º
快速热退火(RTA)是一种采用各种能源、退火时间范围很宽(100s到纳秒)的退火工艺。RTA可以在最小的杂质再分布情况下完全激活杂质。
退火:将注入离子的硅片在一定温度和真空或氮、氩等高纯气体的保护下,经过适当时间的热处理,
部分或全部消除硅片中的损伤,少数载流子的寿命及迁移率也会不同程度的得到恢复,
电激活掺入的杂质
10 倾斜角度离子注入
当器件缩小到亚微米尺寸时,将杂质分布垂直方向也缩写是很重要的。现代器件结构如轻掺杂漏极(LDD),需要在纵向和横向上精确控制杂质分布。垂直于表面的离子速度决定注入分布的投影射程。如果硅芯片相对于离子束倾斜了一个很大的角度,则等效离子能量将大为减少。
在倾斜角度离子注入时,需考虑硅芯片上掩蔽图案的阴影效应。较小的倾斜角度导致一个小阴影区。如高为0.5um的掩蔽层,离子束的入射角为7度,将导致一个61nm的阴影区。可能是器件产生一个预想不到的串联电阻。
扩散效应:
8 快速热退火
一个具有瞬间光加热的快速热退火系统
表为传统炉管与RTA技术的比较。为获得较短的工艺时间,需在温度和工艺的不均匀性、温度测量与控制、硅芯片的应力与产率间作取舍。
快速热退火
9注入相关工艺-多次注入及掩蔽
在许多应用中,除了简单的高斯分布外其它的杂质分布也是需要的。例如硅内预先注入惰性离子,使表面变成非晶。此方法使杂质分布能准确地控制,且近乎百分百的杂质在低温下激活。在此情况下,深层的非晶体层是必须,为了得到这种区域,必须要做一系列不同能量与剂量的注入(多次注入)。
多次注入如下图所示,用于形成一平坦的杂质分布。
为了要在半导体衬底中预先选择的区域里形成p-n结,注入时需要一层合适的掩蔽层。此层要阻止一定比例的入射离子其最小厚度可从离子的射程参数来求得。在某一深度d之后的注入量对回忆式积分可得:
穿越深度d的剂量的百分比可由穿透系数T求得:
一旦得到了T,对任一恒定的Rp和σp来说,都可以求得掩蔽层厚度d,对SiO2、Si3N4与抗蚀剂来说,要阻挡99.99%的入射离子(T=10-4)所需的d值如下图所示。图中内插图显示了在掩蔽材料内的注入物的分布。
离子能量随距离的平均损耗可由上述两种阻止机制的叠加而得:
如果一个离子在停下来之前,所经过的总距离为R,则
E0为初始离子能量,R为射程。
核阻止过程可以看成是一个入射离子硬球与衬底核硬球之间的弹性碰撞M1转移给M2的能量为:
电子中止能力与入射离子的速度成正比:
其中系数ke是原子质量和原子序数的弱相关函数。硅的ke值107(eV)1/2/cm。砷化镓的ke值为3×107(eV)1/2/cm
离子注入和快速退火工艺
离子注入是一种将带电的且具有能量的粒子注入衬底硅的过程。注入能量介于1keV到1MeV之间,注入深度平均可达10nm~10um,离子剂量变动范围从用于阈值电压调整的1012/cm3到形成绝缘层的1018/cm3。相对于扩散工艺,离子注入的主要好处在于能更准确地控制杂质掺杂、可重复性和较低的工艺温度。
轻离子的树枝状的无序区不同于重离子。轻离子(11B+)大多数的能量损伤起因于电子碰撞,这并不导致晶格损伤。离子的能量会减低至交叉点能量,而在那里核阻止会成为主导。因此,晶格无序发生在离子最终的位置附近。如下图(a)所示。
重离子的能量损失主要是原子核碰撞,因此预期有大量的损伤。如下图(b)所示。
要估计将单晶转变为非晶材料所需的能量,可以利用一个判据,即认为注入量应该与融化材料所需的能量密度(1021keV/cm3)在数量级上相同。对于100keV的砷离子来说,形成非晶硅所需的剂量为
表示。因为这种形式的分布也会参数某些横向注入。
2 离子中止
使荷能离子进入半导体衬底后静止有两种机制。
一是离子能量传给衬底原子核,是入射离子偏转,也使原子核从格点移出。设E是离子位于其运动路径上某点x处的能量,定义核原子中止能力:
二是入射离子与衬底原子的电子云相互作用,通过库仑作用,离子与电子碰撞失去能量,电子则被激发至高能级或脱离原子。定义电子中止能力:
离子中止两种机制:一是离子能量传给衬底原子核,是入射离子偏转,也使原子核从格点移出。二是入射离子与衬底原子的电子云相互作用,通过库仑作用,离子与电子碰撞失去能量,电子则被激发至高能级或脱离原子。
硅中电子中止能力如虚线所示,交叉能量点是Sn(E)=Se(E)。一旦Sn(E)和Se(E)已知,可计算处射程范围。可以用下述近似方程式来求得投影射程与投影偏差:
大电流注入机(10-20mA)工作在25-30keV范围下,通常用于扩散技术中的预置处理。因为其总量能够精确控制。在预置后,掺杂剂可以用高温扩散步骤再分布,同时顺便将表面区的注入损伤修补。另一用途就是MOS器件的阈值电压调整,精确控制的杂质量经栅极氧化层注入沟道区。
目前,已有能量范围介于150-200keV的大电流离子注入。主要用途是制作高品质硅层,通过向硅层中注入氧来生成二氧化硅从而使该硅层与衬底绝缘。这种氧注入隔离(SIMOX)是一种绝缘层上硅(SOI)的关键技术。
聚焦系统:用来将加速后的离子聚集成直径为数毫米的离子束。
偏转扫描系统:用来实现离子束x、y方向的一定面积内进行扫描。
工作室:放置样品的地方,其位置可调。
13 离子注入主要解决的问题
1)纯度
2)深度
3)浓度
4)均匀性
5)稳定性
14 离子注入优缺点
优点:
1)可在较低的温度下,将各种杂质掺入到不同的半导体中;
3、先注入大量硅或锗原子以破坏硅芯片表面,可在硅芯片表面产生一个随机层[图(c)],这种方法需使用昂贵的离子注入机。
5 注入损伤与退火
离子注入中,与原子核碰撞后转移足够的能量给晶格,使基质原子离开晶格位置而造成注入损伤(晶格无序)。这些离位的在也许获得入射能量的大部分,接着如骨牌效应导致邻近原子的相继移位而形成一个沿着离子路径的树枝状的无序区。当单位体积内移位的原子数接近半导体的原子密度时,单晶材料便成为非晶材料。
6 退火
由于离子注入所造成的损伤区及畸形团,使迁移率和寿命等半导体参数受到影响。此外,大部分的离子在被注入时并不位于置换位置。为激活被注入的离子并恢复迁移率与其它材料参数,必须在适当的时间与温度下将半导体退火。
传统退火炉使用类似热氧化的整批式开放炉管系统。需要长时间和高温来消除注入损伤。但会造成大量杂质扩散而无法符合浅结及窄杂质分布的需求。
高能的离子由于与衬底中电子和原子核的碰撞而失去能量,最后停在晶格内某一深度。平均深度由于调整加速能量来控制。杂质剂量可由注入时监控离子电流来控制。主要副作用是离子碰撞引起的半导体晶格断裂或损伤。因此,后续的退化处理用来去除这些损伤。
1离子分布
一个离子在停止前所经过的总距离,称为射程R。此距离在入射轴方向上的投影称为投影射程Rp。投影射程的统计涨落称为投影偏差σp。沿着入射轴的垂直的方向上亦有一统计涨落,称为横向偏差σ┷。
分为普通热退火、硼的退火特性、磷的退火特性、扩散效应、快速退火
普通热退火:退火时间通常为15--30min,使用通常的扩散炉,在真空或氮、氩等气体的保护下对衬底作退火处理。缺点:清除缺陷不完全,注入杂质激活不高,退火温度高、时间长,导致杂质再分布。
7 硼与磷的传统退火
退火的特性与掺杂种类及所含剂量有关
3离子注入的沟道效应
前述高斯分布的投影射程及投影的标准偏差能很好地说明非晶硅或小晶粒多晶硅衬底的注入离子分布。只要离子束方向偏离低指数晶向<111>,硅和砷化镓中的分布状态就如在非晶半导体中一样。在此情况下,靠近峰值处的实际杂质分布,可用“高斯分布函数”来表示,即使延伸到低于峰值一至两个数量级处也一样,这表示在下图中。然而即使只偏离<111>晶向7度,仍会有一个随距离而成指数级exp(-x/λ)变化的尾区,其中λ的典型的数量级为0.1um。
4离子进入的角度及通道
<100><110><111>
沟道效应降低的技巧
1、覆盖一层非晶体的表面层、将硅芯片转向或在硅芯片表面制造一个损伤的表层。常用的覆盖层非晶体材料只是一层薄的氧化层[图(a)],此层可使离子束的方向随机化,使离子以不同角度进入硅芯片而不直接进入硅晶体沟道。
2、将硅芯片偏离主平面5-10度,也能有防止离子进入沟道的效果[图(b)]。此方法大部分的注入机器将硅芯片倾斜7度并从平边扭转22度以防止沟道效应。
下图显示了离子分布,沿着入射轴所注入的杂质分布可以用一个高斯分布函数来近似: