气体辅助注射成型原理及应用
气体辅助注射成型技术原理及应用

气体辅助注射成型技术原理及应用
气体辅助注射成型技术的应用
● 管状和棒状零件,如门把手、转椅支座、吊 钩、扶手、导轨、衣架等。这是因为,管状结 构设计使现存的厚截面适于产生气体管道,利 用气体的穿透作用形成中空,从而可消除表面 成型缺陷,节省材料并缩短成型周期。
气体辅助注射成型技术原理及应用
在进行模具设计之前,利用MoldFlow MPI 5.0对设计方案进行了模拟。 分析模型如图8所示,在该分析模型中确定了浇口及进气口位置。在模拟中, 设定预注射量为70%,熔体温度为230℃,注射时间为3s,延迟时间为1.5s, 气体压力为20MPa。
气体辅助注射成型技术原理及应用
● 可通过气体的穿透减轻制品重量,节省原材料 用量,并缩短成型周期,提高生产率。
● 该技术可适用于热塑性塑料、一般工程塑料及 其合金以及其他用于注射成型的材料。
气体辅助注射成型技术原理及应用
气体辅助注射成型技术的缺点是:
●需要增加供气和回收装置及气体压力控制单元, 从而增加了设备投资;对注射机的注射量和注射 压力的精度要求有所提高;制品中接触气体的表 面与贴紧模壁的表面会产生不同的光泽;制品质 量对工艺参数更加敏感,增加了对工艺控制的精 度要求。
气体辅助注射成型CAE分析的主要作用是:
1.分析产品的成型工艺性 2.评价模具的设计是否合理 3.优化成型工艺参数 4.预测制品可能出现的缺陷
气体辅助注射成型技术原理及应用
下面以成型把手为例,介绍气体辅助注射成型 CAE分析的过程。
如图7所示的把手材料为ABS,手柄位置壁厚为14mm。由于是外观件,对 其成型要求很高。
气辅成型原理
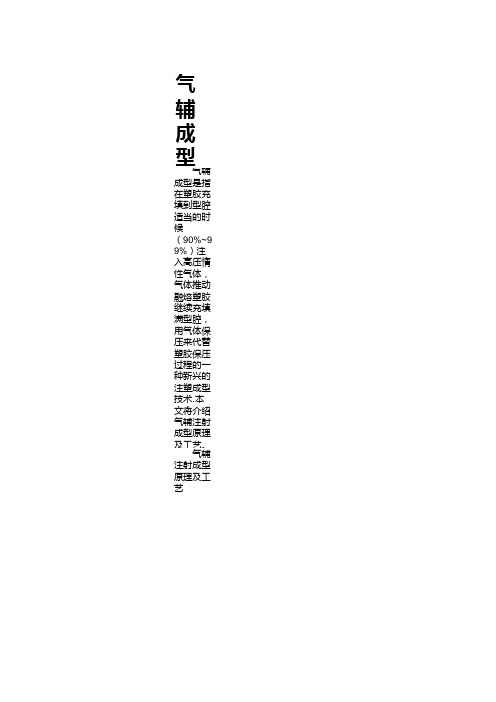
气辅成型 气辅成型是指在塑胶充填到型腔适当的时候(90%~99%)注入高压惰性气 气辅注射成型原理及工艺 气辅成型(GIM)是指在塑胶充填到型腔适当的时候(90%~99%)注入高 要点: 1、计量管理。
2、利用气辅控制器把高压氮气直接压入到模腔内熔胶里。
3、使塑件内部膨胀而造成中空。
一、气辅成型的优点 1、降低产品的残余应力,使产品不变形。
2、解决和消除产品表面缩痕问题,应用于厚度变化大的产品。
3、降低注塑机的锁模力,减少成型机的损耗。
4、提高注塑机的工作寿命。
5、节省塑胶原材料,节省率可达百分之三十。
6、缩短产品生产成型周期时间,提高生产效率。
7、降低模腔内的压力,使模具的损耗减少和提高模具的使用寿命。
8、对某些塑胶产品,模具可采用铝合金属材料。
9、简化产品的繁复设计。
二、气辅成型过程 • 合模 • 射座前进 • 熔胶充填 • 气体注入 • 预塑计量(气体保压) • 射座后退(排气卸压) • 冷却定型 • 开模 • 顶出制件 三、气体辅助注塑周期 1、注塑期 以定量的塑化塑料充填到模腔内。
(保证在充气期间,气体不会把产品表面 2、充气期 可以注塑期中或后,不同时间注入气体。
气体注入的压力必需大于注塑压力 3、气体保压期 当产品内部被气体充填后,气体作用于产品中空部分的压力就是保压压力, 4、脱模期 随着冷却周期的完成,模具的气体压力降至大气压力,产品由模腔内顶出。
四、气辅成型所需的条件 • 注塑成型机 • 气体的来源(氮气发生器) • 输送气体的管道 • 控制氮气有效流动的设备(氮气控制台) • 带有气道设置的成型模具(气辅模具) 五、成型条件的设定 1、注塑机的设定 o 原材料的烘干温度与传统成型一致 o 料筒的塑化温度比传统注塑偏高 o 模温要求较严,冷却水路布置要使冷却效果均衡 o 注塑压力与传统注塑基本一致 o 注塑速度一般采用高速填充 2、氮气设备的设定 a、氮气发生器的压力一般设定在30MPA左右 b、氮气控制台要素的设定(延迟时间、气体压入时间、气体保持时间、气90%~99%)注入高压惰性气体,气体推动融熔塑胶继续充填满型腔,用气体保压来代替塑胶保压过程的一种新兴的注塑成当的时候(90%~99%)注入高压惰性气体,气体推动融熔塑胶继续充填满型腔,用气体保压来代替塑胶保压过程的一种新兴模腔内熔胶里。
气辅注塑

1)封闭式气体注射(SEALED INJECTION GAS)方法: * 是把气体直接注入模腔内,使塑料成品中空的方法。无需采用活阀,只是 通过简单模具加工,把气辅气嘴装在模具中。 * 在同一模具上,可有单一或多个注入气体的地方,这视乎同产品的需要, 慕求令产品有良好效果和提供产品设计有较大的灵活性。
太小会使气体流动失去控制 7.冷却要尽量均匀,内外壁温差要尽量小
8.在流道上放置合理流道半径的截流块,辅助注塑设备按工艺需求大致应有以下几类: 1、氮气机:主要用于氮气的制造 2、氮气增压器:主要是将氮气的气压加大,以便于氮气的注入 3、气辅控制器:主要用于控制氮气注入量、气压、时间及排气的控制,是
• 降低生产成本
– 由于减少了壁厚,因此降低了零件成品的总重量. – 由于壁厚较小,因此缩短了冷却时间和循环时间. – 由于降低了锁模力和注塑保压压力,能源消耗成本降低. – 由于零件的集成化,从而降低了装配成本.
• 降低投资成本
– 由于注射压力较低,因此可以降低注塑机的锁模压力,可使用吨位较小的注塑 机.
整个气辅设备的控制中心 4、气辅配件:主要有气针、气管及各种接头等,用于气辅设备与模具的连
接
因各种设备加在一起,占用的空间较大,现有很大一部分已采用一体化的气 辅系统。
END
同传统注射成型工艺相比.应用气体辅助注塑技术,有以下优点:
• 自由设计
– 综合功能较为复杂的塑胶零件可以整装为单一的组件. – 可以在同一零件上结合厚壁和薄壁部分. – 使用空心的"加强筋"部分可以提高其强度.
• 提高零件质量
– 由于减小了微收缩,因此扭曲和变形就减少了. – 消除缩痕. – 由于注射点的数量减少,所以波纹和熔接线也相应减少.
注塑成型过程中气体辅助成型技术的应用前景探讨
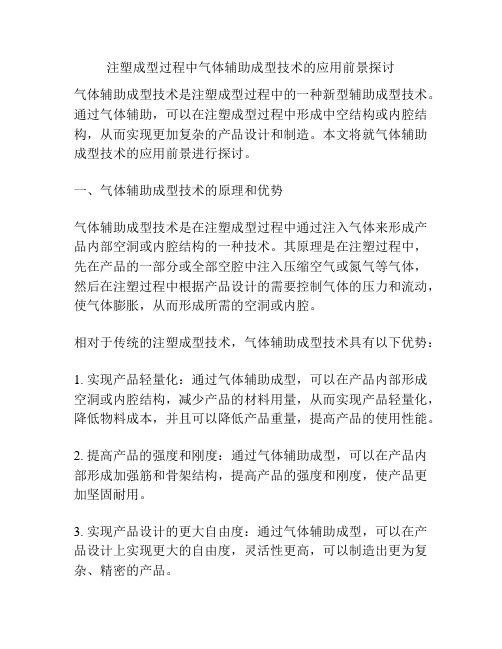
注塑成型过程中气体辅助成型技术的应用前景探讨气体辅助成型技术是注塑成型过程中的一种新型辅助成型技术。
通过气体辅助,可以在注塑成型过程中形成中空结构或内腔结构,从而实现更加复杂的产品设计和制造。
本文将就气体辅助成型技术的应用前景进行探讨。
一、气体辅助成型技术的原理和优势气体辅助成型技术是在注塑成型过程中通过注入气体来形成产品内部空洞或内腔结构的一种技术。
其原理是在注塑过程中,先在产品的一部分或全部空腔中注入压缩空气或氮气等气体,然后在注塑过程中根据产品设计的需要控制气体的压力和流动,使气体膨胀,从而形成所需的空洞或内腔。
相对于传统的注塑成型技术,气体辅助成型技术具有以下优势:1. 实现产品轻量化:通过气体辅助成型,可以在产品内部形成空洞或内腔结构,减少产品的材料用量,从而实现产品轻量化,降低物料成本,并且可以降低产品重量,提高产品的使用性能。
2. 提高产品的强度和刚度:通过气体辅助成型,可以在产品内部形成加强筋和骨架结构,提高产品的强度和刚度,使产品更加坚固耐用。
3. 实现产品设计的更大自由度:通过气体辅助成型,可以在产品设计上实现更大的自由度,灵活性更高,可以制造出更为复杂、精密的产品。
4. 提高生产效率:由于气体辅助成型可以一次性实现多个镶嵌件的成型,因此可以提高生产效率,降低生产成本。
5. 减少废品率:气体辅助成型能够减少由于变形、翘曲等问题导致的废品率,提高产品的成形质量。
二、气体辅助成型技术的应用前景随着工业自动化水平的提高和人们对产品质量和性能要求的提高,气体辅助成型技术在注塑成型中的应用前景越来越广阔。
以下是其应用前景的具体探讨:1. 制造电子产品组件在电子产品制造过程中,一些组件需要在内部形成空洞或内腔结构,以容纳电路板和电子元器件。
传统注塑成型很难实现这种内部空洞的制造,而气体辅助成型技术能够轻松地实现这种需求。
因此,气体辅助成型技术在制造电子产品组件方面有着广阔的应用前景。
2. 制造汽车零部件汽车行业是注塑成型的重要应用领域之一,而气体辅助成型技术正好满足了汽车零部件制造上的一些需求。
气体辅助注塑工艺原理及优点
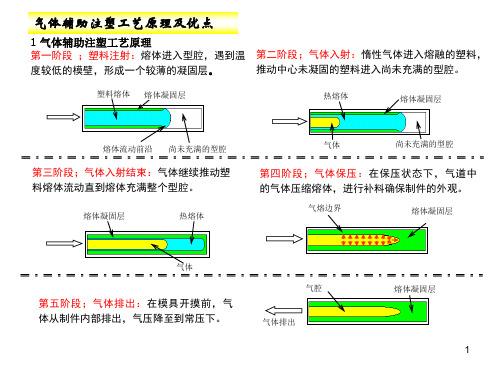
图4自封闭气辅射嘴
图5主动式气辅射嘴
7
(2) 气针进气方式 气针进气方式即在模具的某个特定位置,安装排气装置-气针。当塑料注入型腔后, 即将气针包裹在塑料内部;此时高压气体排出,气针在塑料内部按气道形成一个延展的 封闭空间-气腔,并保持一定压力,直至冷却,在模具打开之前,气腔内的气体依靠气 针由控制装置排出塑料内部。
全系统包含进口螺杆空气压缩机、蓄能型压缩空气冷冻干燥机、压缩空气 过滤器三大部分构成,系统一体化设计生产。系统过滤后颗粒精度≤0.01µm、过 滤后除油精度≤0.001mg/m3。其特点系统简单,系统压缩空气品质极高,保护措 施严密,可靠性高;操作方便,维护工作量小;系统加载多点保护及报警装置, 严密监控,保证压缩空气品质
图1
图2
4
2.板类制品
气辅注塑成型技术的主要应用之一就是板类制件的成型。因为气体总是沿 着阻力最小的方向前进,容易在较厚的部位进行穿透,因此,在板类制品设计时常 将加强筋作为气道,气道一般设在制品的边缘或壁的转角处。对制品的设计也就是 对加强筋和肋板的设计,即气道的设计。基本原则如下: (1).在设计制作加强筋时,应避免设计又细又密的加强筋。 (2).“手指”效应是大平面制件容易产生的主要问题。 (3).当制件仅由一个气针进气而形成多个加强筋或肋板(气道)时,气道不能形 成回 路。
9
3. 气辅模具设计方面对气辅成型的影响 (1)模具型腔的设计应尽量保证流动平衡以减小气体的不均匀穿透,保证流动平衡也是 普通注射成型模具的一条设计原则,但对气辅成型制品来说这一点更重要。图7对比了管 状型腔中平衡与非平衡方式充填时气体穿透的情况,箭头处是熔体和气体的入口处。
图7 流动是否平衡对气体穿透的影响 10
13
注塑成型中的气体辅助技术应用
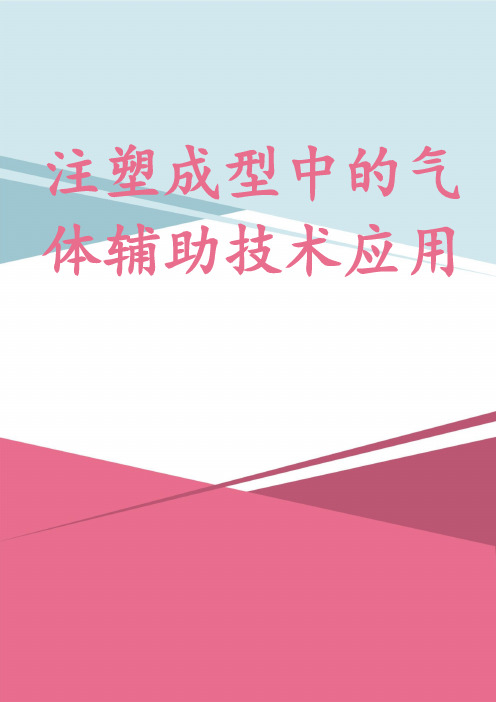
注塑成型中的气体辅助技术应用注塑成型中的气体辅助技术应用注塑成型是一种常用的塑料加工方法,通过将熔化的塑料注入模具中,经过冷却固化后得到所需的塑料制品。
然而,在注塑成型过程中,常常会出现一些问题,如缺陷、翘曲等。
为了解决这些问题,气体辅助技术在注塑成型中得到了广泛的应用。
气体辅助技术是指在注塑成型过程中,通过向模具中注入气体,利用气体的性质对塑料进行辅助成型的一种方法。
在注塑成型过程中,通过在模具中注入气体,可以改善产品表面质量,减少翘曲和缩水等缺陷,提高产品的整体性能。
首先,气体辅助技术可以改善产品的表面质量。
在注塑成型中,由于塑料的热胀冷缩和浇注冷却的不均匀性,常常会出现产品表面的缺陷,如气泡、痕迹等。
通过在模具中注入气体,可以使塑料在充填过程中更加均匀,减少气泡的产生,从而改善产品的表面质量,使其更加光滑。
其次,气体辅助技术可以减少产品的翘曲和缩水。
在注塑成型中,由于塑料的收缩性质,产品往往会出现翘曲和缩水等问题。
通过在模具中注入气体,可以产生一定的气压,使塑料在冷却固化过程中更加均匀,减少翘曲和缩水的可能性,从而提高产品的几何稳定性和尺寸精度。
最后,气体辅助技术可以改善产品的整体性能。
在注塑成型中,由于塑料的结晶性质,产品往往会出现内部应力集中的问题,从而影响产品的强度和韧性。
通过在模具中注入气体,可以使塑料在充填过程中形成空腔结构,减少内部应力的集中,提高产品的整体性能,使其更加坚固耐用。
综上所述,气体辅助技术在注塑成型中的应用可以改善产品的表面质量,减少翘曲和缩水,提高产品的整体性能。
随着技术的不断发展,气体辅助技术在注塑成型中的应用前景更加广阔,将为塑料制品的生产提供更多的可能性。
气辅成型
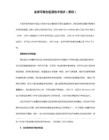
设计模具时要考虑气体喷口的设计及位置。
在初期应用中会经历一条学习曲线。
材料选择范围广
大多数热塑性材料都能应用气体辅助注射成型。例如聚丙烯、聚酰胺和PBT树脂等晶体材料是比较理想的材料,因为它们都具有精确的熔点、较低的粘稠度、气体容易穿透。要依据对产品性能的要求,诸如刚性、强度、特殊条件下的表现、耐化学腐蚀等来选择原材料。
气体辅助射出成型工艺范例:
汽车部件
车门把手
车门硬件模块
外后视镜外壳
外饰件
油门踏板臂
乘客扶手
玻璃刮水器臂
空气滤清器外壳
格栅
打印机/传真机嵌版
计算机边框
计算机服务器嵌版
打印机嵌版
娱乐设施
高尔夫球杆杆身
篮板
高尔夫车顶板
雪地机动车保险杆
其他
用具的把手
医疗分析仪器罩
淋浴房基座
电视机柜
洗衣机波轮
平板架
电动工具把手
马桶座
自动售货机罩
水冷机嵌板
随着越来越多的产品设计者、工程技术人员、工具商和模塑商开始熟悉气体辅助注射成型工艺,唯一的问题是如何创造性地运用这一工艺。正如一贯的做法,在一个新产品的开发过程中,每一位成员都应该在开发过程中尽可能早的阶段参加进来。这样,各方的意见和经验能够交汇,有助于大幅缩短新品开发的周期并降低成本。
气体辅助注射成型技术原理及应用.

气体辅助注射成型技术原理及应用气体辅助注射成型(Gas-Assisted Injection Molding, GAIM)技术最早可追溯到20世纪70年代,该技术在20世纪80年代末得到了完善并实现了商品化。
从20世纪90年代开始,作为一项成功的技术,气体辅助注射成型技术在美、日、欧等发达国家和地区得到了广泛应用。
目前该技术主要被应用在家电、汽车、家具、日常用品、办公用品等加工领域中。
气体辅助注射成型技术的工艺过程气体辅助注射成型技术的工艺过程是:先向模具型腔中注入塑料熔体,再向塑料熔体中注入压缩气体。
借助气体的作用,推动塑料熔体充填到模具型腔的各个部分,使塑件最后形成中空断面而保持完整外形。
在成型后的制品中,由气体形成的中空部分被称为气道。
由于具有廉价、易得且不与塑料熔体发生反应的优点,因此一般所使用的压缩气体为氮气。
气体辅助注塑成型周期可分为以下六个阶段。
(1)塑料充模阶段这一阶段与普通注塑成型基本相同,只是普通注塑成型时塑料熔体是充满整个型腔,而气体辅助注塑成型时塑料熔体只充满局部型腔,其余部分要靠气体补充。
(2)切换延迟阶段这一阶段是塑料熔体注射结束到气体注射开始时的时间,这一阶段非常短暂。
(3)气体注射阶段此阶段是从气体开始注射至整个型腔被充满的时间,这一阶段也比较短,但对制品质量的影响极为重要,如控制不好,会产生空穴、吹穿、注射不足和气体向较薄的部分渗透等缺陷。
(4)保压阶段熔体内气体压力保持不变或略有上升使气体在塑料内部继续穿透,以补偿塑料冷却引起的收缩(5)气体释放阶段使气体入口压力降到零。
(6)冷却开模阶段将制品冷却到具有一定刚度和强度后开模取出制品。
根据具体工艺过程的不同,气体辅助注射成型可分为标准成型法、副腔成型法、熔体回流法和活动型芯法四种。
1、标准成型法标准成型法是先向模具型腔中注入经准确计量的塑料熔体(如图1a所示),再通过浇口和流道注入压缩气体。
气体在型腔中塑料熔体的包围下沿阻力最小的方向扩散前进,对塑料熔体进行穿透和排空(如图1b所示),最后推动塑料熔体充满整个模具型腔并进行保压冷却(如图1c所示),待塑料制品冷却到具有一定刚度和强度后,开模将其顶出(如图1d所示)。
- 1、下载文档前请自行甄别文档内容的完整性,平台不提供额外的编辑、内容补充、找答案等附加服务。
- 2、"仅部分预览"的文档,不可在线预览部分如存在完整性等问题,可反馈申请退款(可完整预览的文档不适用该条件!)。
- 3、如文档侵犯您的权益,请联系客服反馈,我们会尽快为您处理(人工客服工作时间:9:00-18:30)。
一、气体辅助注射成型概述——Jack Avery气体辅助注射成型过程首先是向模腔内进行树脂的欠料注射,然后将气体导入熔融物料当中,气体沿着阻力最小方向流向制品的低压和高温区域。
当气体在制品中流动时,它通过置换熔融物料而掏空厚壁截面。
这些置换出来的物料充填制品的其余部分(图1-3)。
当填充过程完成以后,由气体继续提供保压压力,解决物料冷却过程中体积收缩的问题。
气体辅助注射成型主要有以下两种基本类型:恒体积和恒压力。
体积恒定时,汽缸内已经加压的气体在注射之前就已经预先确定好注射体积,由活塞推动气体进入制品。
气体的压力取决于制品中的体积与汽缸体积之比。
气体的压力、停留时间以及活塞运动速度直接影响着制品外观。
如图1-4所示为恒体积成型中一个注射周期内的压力变化曲线。
对于每一注射周期,在注射之前都必须重新建立压力。
压气时间图1-4 恒体积系统的气体压力曲线图[源自:Innovation inPolymer Processing:Molding,Stevenson,J.F.(Ed.)]另外一种类型是恒压力成型。
我们通过空气压缩机将氮气(N2)装入储存罐中预先加压,储存罐向一毓的阀门提供恒定压力。
压力曲线可以通过调节气压和开启相应阀门来实现。
图1-5所示为成型周期内,气体压力可以保持恒定。
时间p氮气压力p p p p 3图1-5 恒压力系统的气体压力曲线图[源自:Innovation inPolymer Processing :Molding,Stevenson ,J.F.(Ed.)]气体辅助注射成型的实现主要有两个选择,二者的区别在于气体注入位置的不同。
气体注射既可以通过喷嘴来实现,也可以直接注进模腔——从分流道进入或者直接进入制品(如图1-6、图1-7和图1-8)。
最主要的不同是由喷嘴进气的方式要求所有气道都从喷嘴外开始。
而采取气体直接注射到模具中的方式时,气体通道可以独立地设置在浇口位置。
对于这种方式,注射之前物料可以实现正常的填充。
气体辅助注射成型加工的基本方式有许多种。
这里介绍其中两种:一是采用多个喷嘴的形式;另一是在熔融物料中使液体蒸发产生气体从而形成气体通道。
多喷嘴的气体辅助注射成型方法与结构发泡成型方法一样都是用于成型大件制品。
采用这种方式可以缩短气体流动距离,降低气体注射压力和模腔所受压力。
多个喷嘴气体辅助注射成型方式常用于同一模板上的多个模具的情况。
不过单个模具也可拥有一个或者多个气体喷嘴,这取决于制品形状大小以及气体流动距离的要求。
由于会受到流动平衡和填充方式的制约,单个喷嘴的气体辅助注射成型方式对于在一个成型周期内成型多个形状不同、质量不同的制品是非常困难的。
多喷嘴气体辅助注射方式则可以解决这个问题。
它允许向多个模腔中充入不同体积的物料和不同压力的气体。
现在已经有人设计出了一种可以同时控制6个气体喷嘴进行工作的机器。
它的控制系统允许6个不同的模具同时安装在拥有多个喷嘴的机器模板上。
图1-11为同时成型一个9kg和一个2.3kg制品的示意图。
有些模腔可以同时有多个喷嘴,而其他模腔则只有一个喷嘴。
机器可通过编写程序来实现对不同的模腔中注入不同要求的物料和气体。
这样我们可以将机器的工作能力提高50%甚至更高。
这项技术现在主要用于质量2.3kg以上大型制品的生产当中。
HELGA(Hettinga 液态气体辅助注射成型)与前一种用N2来辅助成型的方法有很大区别,如图1-12所示。
成型所需的一部分物料先被注入模腔中,随后采用共注射的方式注入更多包含专门液体的物料。
液体与熔融物料接触以后转化为气体形成中空结构。
当液体停止流动时,注射过程也随之结束。
气体包含在制品里面,它提供的压力可以使制品的缩痕降到最低。
制品冷却以后,即使制品受热其内部的气体不会活动。
HELGA成型方法与采用气体喷嘴的成型方法效果相当,它在应用过程中最大的一个优点就是制品不用开设进气孔,而其他一些气体辅助性成型方式在完成制品成型以后,都必须采取另外一个工序来封口。
许多公司都拥有气体辅助注射成型的专利权。
这些专利的内容包括将气体注入熔体的各种技术、气体喷嘴的设计及先后顺序等。
表1-1列出了提供这项专利技术的主要供应商名单。
建议你在决定使用其中某项技术之前,先对这些专利技术做一个全面了解,看看你所用的与其中哪一项相近。
这些技术所用的设备在全球范围都可以获得。
表1-2列出了一些具有全球供应能力的供应商名单。
表1-1气体辅助注射成型技术供应商名单气体辅助注射成型的适用范围气体辅助注射成型技术用在哪里,原因何在呢?设计人员发现气体辅助注射成型最大的优点就是制品由于中空结构使刚性增加而不用增加质量,有时甚至还能减轻。
以下是气体辅助注射成型制品的两个主要类型:——封闭式气道——开放式气道封闭式气道制品主要由一个厚壁截面和气体穿行的通道组成。
比如门把手、扶手、框架结构、中空管等都属于此类结构。
因为气体的扩散有一条设定好的清晰路线,而且制品没有薄壁部分,所以这种制品是最容易加工成型的。
开放式气道制品主要是薄壁元件,类似于传统的加强筋结构制品。
因为气体可能会穿透制品的薄壁部分(有时趋向于指形),因此开放式气道制品的设计与制造都相对较困难。
气体辅助注射成型方法的优点为什么人们对于气体辅助注射成型的兴趣如此之大呢?其主要的原因在于这种方法出现时所许诺的种种优点。
以下是气体辅助注射成型其他成型方式相比所具有的一些优势:制品残余应力降低翘曲变形较小减少/消除缩痕更大的设计自由度制品综合性能提高与结构发泡相比,制品外观质量得到改善(也就是减少/消除修整过程)中空制品且有以下特点制品更加易于填充物料流动距离更长刚度与质量之比更大与实心制品相比成型周期缩短合模力吨位要求降低注射压力降低气道取代热流道系统从而使模具成本降低上述即为气体辅助注射成型所拥有的优点。
因此,很多公司都积极地对这项技术研究拓展新的应用领域。
同其他所有的成型技术一样,必须通过所生产的制品来得到对技术的完整评价,也就是通过制品的特征和产量,来确定我们所选择的是最经济的成型加工方法。
勉强去适应某种成型方法一般并不能得到最好的结果。
气体辅助注射成型方法的缺点气体辅助注射成型肯定存在一些缺点,否则,在25年的时间里它早已在更加广阔的领域得到应用了。
首先是专利使用权限制。
表1-1列出了一些已经被申请专利保护的技术。
虽然专利情况在不断地变化,但现在如果要使用Cinpres Ltd. , Gain Technologies和Nitrojection等公司的技术仍然需要得到专利许可。
为了使用HELGA或者Johnson Controls多喷嘴成型技术而购买的设备则包括了专利使用权在内。
另外一个问题是附加的成本。
即使没有专利使用权的要求,气体辅助注射成型的专用设备也会要求$30000~$85000的附加费用。
这些附加费用是使用气体辅助注射成型技术的前提。
根据专利使用权的费用和生产制品的产量,每个制品的成本费用增加可从少到每件几分多至数额非常巨大。
导致成本增加的另一个原因是气体的使用。
除了HELGA加工方法外,一般气体辅助注射成型技术都因为氮气来源充足而将其作为首选的注射用气体。
在气体辅助注射成型的早期发展阶段,高压气缸氮气常作为气体来源。
这是因为氮气的用量很少,汽缸能够放在靠近机器的地方,而且成本低廉。
随着气体辅助注射成型制品产量的增加,与氮气使用相关的诸如成本、供应和安全等问题引起了人们的注意。
高压氮气的来源可以通过采用大型低温液氮容器或者采用现场氮气发生器来得到。
表1-3为Bauer Gas Systems Inc进行的一项研究。
研究用的氮气流速为13cfm(360L/min),工作时间为24小时/天,7天/周,50周/年。
这项研究表明采用现场氮气发生器的成本回收期为半年左右,而采用液氮的成本回收周期要一年左右。
不管怎样我们必须承认,氮气的使用的确使生产成本增加,而且收益率也因此受到极大的压缩。
表1-3氮气费用研究汽缸/液体/膜分离器汽缸液体膜分离器(现场)花费($)/(100cf/3m3) 2.89 1.45 1.57花费($)/h 22.54 11.31 1.36花费($)/年第1年189336.00 95004.00 89742.00第2年378672.00 190008.00 101148.00第3年568008.00 285012.00 112572.00第5年946680.00 475020.00 135420.00①来源:Bauer Compressors,Inc。
②膜分离器产量425L/min。
③第1年花费包括全部发生器费用$78300。
气体喷嘴的设计以及位置选择也是潜在的问题。
采用从制品内和从流道内方式进行气体注射时,喷嘴位置的选择是个很棘手的问题。
在气体流入之前,物料必须先包裹在喷嘴外部,否则就会发生气体泄漏现象。
要保证高生产率,就必须保证喷嘴结构设计正确、位置选择正确。
如果喷嘴设计不当就会在气体流入和排气阶段出现这样或那样的问题。
同时也会导致喷嘴在维护和更换过程的困难,从而使生产率降低,生产成本增加。
材料大多数热塑性塑料都可用于气体辅助注射成型加工,表1-4列出一些常用材料。
对于结晶型物料如聚苯乙烯、尼龙和对苯二甲酸酯等,由于它们有明显的熔融温度并且黏度低,所以气体在其中的流动相对来说很容易。
我们在选择材料时,必须考虑到制品的刚性、强度、使用温度以及耐腐蚀性等。
研究表明,随着材料黏度的增加气道的壁厚也相应增加。
GE Plastics 用PC和PBT做实验证明了这一点。
材料的黏度可以通过调整加工过程中的工作温度来改变。
温度升高,物料黏度降低,气道壁厚随之变薄。
很多材料供应商也在进行气体辅助注射成型的研究,因此他们能够提供采用这种加工方法时一些特殊材料的特性参数。
表1-4气体辅助注射成型所用原料气体辅助注射成型还可以用于一些热固性材料的成型加工。
Battenfeld的研究表明层流热固性材料完全能够采用气体辅助注射成型,而非层流的热固性材料则不能。
其中最主要的原因是,当非层流物料凝固成型时,熔体与模腔内壁间的黏附力非常小。
结果,处于流动前锋的物料不能向模腔内壁分散而形成一个没有压缩的低压区域,使加压气体从这个区域流走。
Battenfeld对非层流材料进行研究时发现气体在此处并没有形成气泡,而是直接穿透流动前锋或进入物料与模腔的接触面。
人们正在研究其他一些热固性材料是否适用气体辅助注射成型,包括苯酚甲醛(PF)、脲甲醛(UF)、三聚氰胺甲醛、三聚氰胺甲醛、三聚氰胺苯酚甲醛、不饱和聚酯和环氧树脂。
一般来说,物料加入矿质填充剂后表现出来的是层流性质,那样便可以采用气体辅助注射成型进行加工,而物料加入有机填料后则表现出固态/剪切流的性质,不利于气体辅助注射成型。