气体辅助注塑
气辅注塑的缺陷及解决方法

气辅注塑的缺陷及解决方法一、引言气辅注塑是一种常用的塑料加工技术,通过注塑机将熔融的塑料材料注入模具中,利用注塑机的高压将塑料材料压实成型。
在这个过程中,气辅注塑存在一些缺陷,本文将重点讨论这些缺陷及其解决方法。
二、缺陷一:翘曲变形在气辅注塑过程中,塑料材料在注射模具中冷却固化,如果冷却速度不均匀或受到外力作用,就容易出现翘曲变形的情况。
这种翘曲变形不仅会影响产品的外观质量,还会导致产品尺寸不准确。
解决方法:1.优化模具设计,增加冷却系统,确保塑料材料能够均匀冷却,避免翘曲变形的发生。
2.调整注射工艺参数,控制注射温度和压力,使塑料材料充分流动,减少翘曲变形的可能性。
3.合理安排模具的开模顺序,避免产品在模具中停留时间过长,减少翘曲变形的机会。
三、缺陷二:气泡气辅注塑过程中,由于塑料材料的熔融状态和注射速度,有可能在产品内部产生气泡。
这些气泡不仅会影响产品的外观质量,还可能导致产品的强度下降。
解决方法:1.优化模具设计,增加通气孔,确保气体能够顺利排出,减少气泡的产生。
2.调整注射工艺参数,控制注射速度和压力,使塑料材料充分流动,减少气泡的形成。
3.采用真空辅助注塑技术,利用负压吸附气泡,确保产品的内部质量。
四、缺陷三:热缩变形在气辅注塑过程中,由于热胀冷缩的原理,塑料材料在冷却固化后会发生一定程度的热缩变形。
这种热缩变形不仅会影响产品的尺寸精度,还可能导致产品的装配困难。
解决方法:1.优化模具设计,增加冷却系统,加强对塑料材料的冷却,减少热缩变形。
2.调整注射工艺参数,控制注射温度和压力,使塑料材料充分流动,并在冷却过程中尽量减少热缩变形的发生。
3.采用后处理工艺,如热处理或压力调整,对产品进行形状稳定化处理,减少热缩变形的影响。
五、缺陷四:尺寸偏差在气辅注塑过程中,由于材料的收缩率和模具的磨损等因素,产品的尺寸往往会有一定的偏差。
这种尺寸偏差不仅会影响产品的装配性能,还可能导致产品无法正常工作。
气体辅助注射成型

他工业承载零件等方面。 /
6.10.2.RIM成型设备
是一组带有轴向活塞泵的计量装置. 主要组成:组分储存槽、过滤器、轴向柱塞泵、
电动机以及带有混合头的液压系统。 RIM成型设备要求有很高的灵活性和计量精度。 近年来,采用电脑对计量装置、工艺操作程序和
⑸.固化定型
制品的固化是通过化学交联反应等物理变化完 成.。
对化学交联反应固化,反应温度必须超过达到完 全转换成聚合物网络结构的玻璃化温度Tg。
模具应具有换热功能,起到散发热量的作用,以 控制模具的最高温度低于树脂热分解温度 。/
制品的脱模必须使其取得足够的强度才可进行, 这主要由材料的固化时间决定的,而固化时间受 制品的配方和制品尺寸影响。
其作用:是分别独立贮存两种原料,防止贮存时 发生化学反应,同时用惰性气体保护,防止空气 中的水分进入贮罐与原料发生反应。/
②计量和输送系统(液压系统)由泵、阀及辅件组 成的控制液体物料的管路系统和控制分配缸工 作的油路系统所组成,
其作用:是使两组分物料能按准确的比例进行分 别输送。
③混合系统(即混合头),使两组分物料实现高速 均匀混合,并加速混合液从喷嘴流道注射到模 具中。/
1)需要供气装置和进气喷嘴,增加了设备的 投资。
2)在注入气体和不注入气体部分,制品表面 光泽有差异。
3)对注射机的注射量和注射压力的精度有更 高的要求。
4)制品质量对模具温度和保压时间等工艺参 数更加敏感。 /
根据产品结构的不同可分为两类:
一类是厚壁、偏壁、管状制件, 如手柄、方向盘、衣架、马桶、座垫等制件; 另一类是大型平板制件, 如仪表盘、踏板、保险杠及桌面等。/
气辅注塑原理
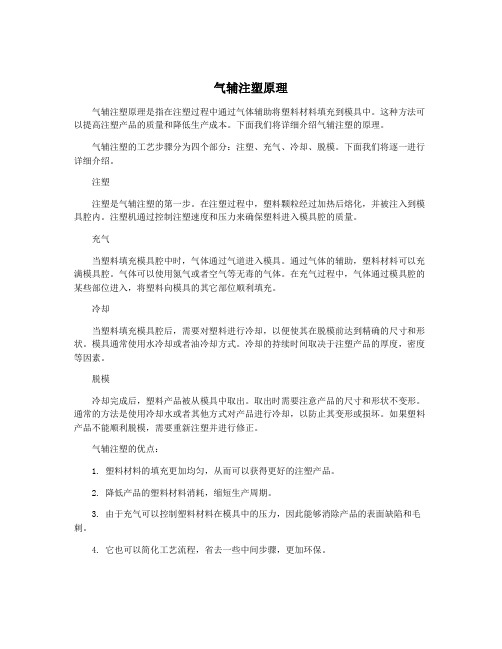
气辅注塑原理气辅注塑原理是指在注塑过程中通过气体辅助将塑料材料填充到模具中。
这种方法可以提高注塑产品的质量和降低生产成本。
下面我们将详细介绍气辅注塑的原理。
气辅注塑的工艺步骤分为四个部分:注塑、充气、冷却、脱模。
下面我们将逐一进行详细介绍。
注塑注塑是气辅注塑的第一步。
在注塑过程中,塑料颗粒经过加热后熔化,并被注入到模具腔内。
注塑机通过控制注塑速度和压力来确保塑料进入模具腔的质量。
充气当塑料填充模具腔中时,气体通过气道进入模具。
通过气体的辅助,塑料材料可以充满模具腔。
气体可以使用氮气或者空气等无毒的气体。
在充气过程中,气体通过模具腔的某些部位进入,将塑料向模具的其它部位顺利填充。
冷却当塑料填充模具腔后,需要对塑料进行冷却,以便使其在脱模前达到精确的尺寸和形状。
模具通常使用水冷却或者油冷却方式。
冷却的持续时间取决于注塑产品的厚度,密度等因素。
脱模冷却完成后,塑料产品被从模具中取出。
取出时需要注意产品的尺寸和形状不变形。
通常的方法是使用冷却水或者其他方式对产品进行冷却,以防止其变形或损坏。
如果塑料产品不能顺利脱模,需要重新注塑并进行修正。
气辅注塑的优点:1. 塑料材料的填充更加均匀,从而可以获得更好的注塑产品。
2. 降低产品的塑料材料消耗,缩短生产周期。
3. 由于充气可以控制塑料材料在模具中的压力,因此能够消除产品的表面缺陷和毛刺。
4. 它也可以简化工艺流程,省去一些中间步骤,更加环保。
气辅注塑是一种高效、环保、节能的注塑工艺。
它可以提高生产效率,降低生产成本,同时还能有效改善产品的质量和外观。
近年来,气辅注塑工艺广泛应用于各个领域。
它可以用于制造电子产品、医疗器械、汽车零配件、家用电器等。
它的灵活性和可塑性极高,满足了市场对产品多样化、品质一致化、成本低价化等需求。
在汽车零配件的制造中,气辅注塑的运用已成为一种趋势。
由于汽车零配件的尺寸和数量大,所以制造成本非常高。
而这里正是气辅注塑的优势所在。
利用气辅注塑工艺,能够更好的控制塑料材料在模具中的填充,从而提高产品的密度、强度和耐用性。
气体辅助注塑工艺原理及优点.
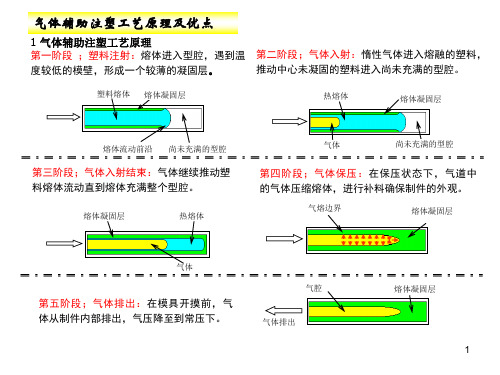
1 气体辅助注塑工艺原理 第一阶段 ;塑料注射:熔体进入型腔,遇到温 第二阶段;气体入射:惰性气体进入熔融的塑料,
度较低的模壁,形成一个较薄的凝固层。
推动中心未凝固的塑料进入尚未充满的型腔。
塑料熔体 熔体凝固层
热熔体
熔体凝固层
熔体流动前沿 尚未充满的型腔
第三阶段;气体入射结束:气体继续推动塑 料熔体流动直到熔体充满整个型腔。
射嘴进气方式,即使用专用的自封闭式或主动式气辅射嘴,在塑料注射结束后,将 高压气体依靠射嘴直接进入塑料内部,按气道形成一个延展的封闭空间-气腔并保持一 定压力,直至冷却,在模具打开之前,通过座台后退使射嘴与制品料道强行分离,使气 体排出制品。
图4自封闭气辅射嘴
图5主动式气辅射嘴 7
(2) 气针进气方式 气针进气方式即在模具的某个特定位置,安装排气装置-气针。当塑料注入型腔后,
2
气辅技术应用
气体辅助注射可以应用在除特别柔软的塑料以外的任何热塑性塑料和部分热 固性塑料。
根据气辅成型制品的结构形状不同,大致分为3类: (1).棒类制品,类似把手之类大壁厚制件; (2).板类制品,容易产生翘曲变形和局部表面收缩的大平面制件; (3).特殊制品,由传统注塑技术难以一次成型的特殊结构的制件。
(5).气道截面尺寸变化应平缓过渡,以免引起收缩不均。 (6).气道入口不应设置在外观面或制件承受机械外力处。
(7).进气口位置应接近浇口,以保证气体与熔体流动方向一致,但两者距离应>30mm, 以避免类制品
气辅注塑成型技术的主要应用之一就是板类制件的成型。因为气体总是沿 着阻力最小的方向前进,容易在较厚的部位进行穿透,因此,在板类制品设计时常 将加强筋作为气道,气道一般设在制品的边缘或壁的转角处。对制品的设计也就是 对加强筋和肋板的设计,即气道的设计。基本原则如下: (1).在设计制作加强筋时,应避免设计又细又密的加强筋。 (2).“手指”效应是大平面制件容易产生的主要问题。 (3).当制件仅由一个气针进气而形成多个加强筋或肋板(气道)时,气道不能形 成回 路。 (4).为避免熔体聚集产生凹陷,气道末端的外形应采用圆角过渡。 (5).采用多点进气时,气道之间的距离不能太近。 (6).气道布置尽量均匀,尽量延伸至制品末端。
气辅注塑加工工艺与一般注塑工艺
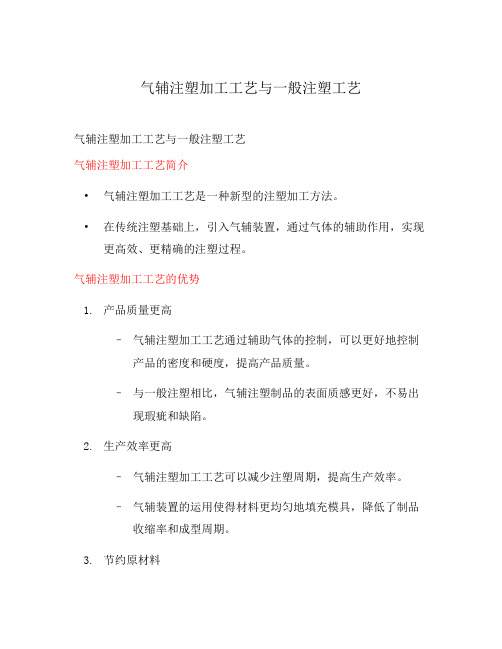
气辅注塑加工工艺与一般注塑工艺气辅注塑加工工艺与一般注塑工艺气辅注塑加工工艺简介•气辅注塑加工工艺是一种新型的注塑加工方法。
•在传统注塑基础上,引入气辅装置,通过气体的辅助作用,实现更高效、更精确的注塑过程。
气辅注塑加工工艺的优势1.产品质量更高–气辅注塑加工工艺通过辅助气体的控制,可以更好地控制产品的密度和硬度,提高产品质量。
–与一般注塑相比,气辅注塑制品的表面质感更好,不易出现瑕疵和缺陷。
2.生产效率更高–气辅注塑加工工艺可以减少注塑周期,提高生产效率。
–气辅装置的运用使得材料更均匀地填充模具,降低了制品收缩率和成型周期。
3.节约原材料–气辅注塑加工工艺由于材料分布更均匀,减少了材料的浪费。
–相比较于一般注塑,气辅注塑制品在制造时所需的原材料用量更少。
4.环保节能–气辅注塑加工工艺不需要额外的加热或冷却设备,节约了能源。
–通过优化制程,减少了废品率,降低了对环境的负面影响。
气辅注塑加工工艺的应用领域•电子产品:手机壳、电池壳、硬盘壳等。
•汽车配件:车灯壳、仪表板、车门把手等。
•家居用品:儿童玩具、家具配件、文具等。
一般注塑工艺的特点与局限性•一般注塑工艺在制品的表面平整度和精度方面有一定的局限性。
•一般注塑制造过程中,因为材料无法完全填充到模具中的每个角落,易产生瑕疵和缺陷。
结语气辅注塑加工工艺相对于一般注塑工艺具有众多优势,无论是产品质量、生产效率还是原材料的节约都占有明显的优势。
在如今注塑加工行业日益竞争激烈的背景下,气辅注塑加工工艺的应用前景非常广阔。
希望本文能对读者对气辅注塑加工工艺与一般注塑工艺有更深入的了解。
气辅注塑加工工艺的工作原理1.注塑过程中,将塑料颗粒加热融化。
2.融化的塑料通过注塑机的螺杆被注入模具腔中。
3.气辅装置通过喷嘴向注入的塑料中喷入压缩空气。
4.压缩空气通过气门控制,辅助塑料充填模具,使得塑料更加均匀地填充到模具的每个角落。
5.注塑机冷却塑料,然后开模取出制品。
气辅注塑的工艺流程
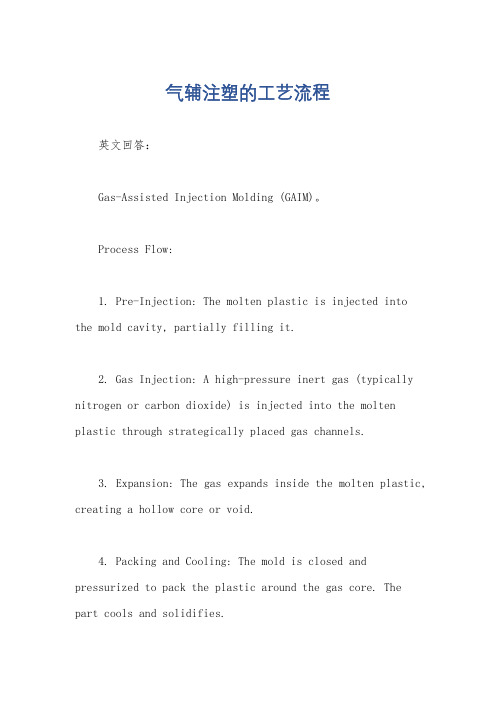
气辅注塑的工艺流程英文回答:Gas-Assisted Injection Molding (GAIM)。
Process Flow:1. Pre-Injection: The molten plastic is injected into the mold cavity, partially filling it.2. Gas Injection: A high-pressure inert gas (typically nitrogen or carbon dioxide) is injected into the molten plastic through strategically placed gas channels.3. Expansion: The gas expands inside the molten plastic, creating a hollow core or void.4. Packing and Cooling: The mold is closed and pressurized to pack the plastic around the gas core. Thepart cools and solidifies.5. Demolding: The part is ejected from the mold.Benefits of GAIM:Reduced material usage and weight.Improved part strength and stiffness.Reduced cycle time.Enhanced surface finish.Increased design flexibility.中文回答:气辅注塑成型工艺流程:1. 预注塑,将熔融塑料注入模腔,部分填充模腔。
2. 气体射入,通过放置在关键位置的气体通道,将高压惰性气体(通常为氮气或二氧化碳)注入熔融塑料中。
气体辅助注塑成型技术简介

气体辅助注塑成型技术简介气体辅助注塑成型技术简介类型:气体辅助注塑成型是欧美近期发展出来的一种先进的注塑工艺,它的工作流程是首先向模腔内进行树脂的欠料注射,然后利用精确的自动化控制系统,把经过高压压缩的氮气导入熔融物料当中,使塑件内部膨胀而造成中空,气体沿着阻力{TodayHot}最小方向流向制品的低压和高温区域。
当气体在制品中流动时,它通过置换熔融物料而掏空厚壁截面,这些置换出来的物料充填制品的其余部分。
当填充过程完成以后,由气体继续提供保压压力,解决物料冷却过程中体积收缩的问题。
气体辅助注塑成型优点为什么人们对于气体辅助注射成型的兴趣如此之大呢?其主要的原因在于这种方法出现时所许诺的种种优点。
成型者希望以低制造成本生产高质量的产品。
在不降低质量的前提下用现代注塑机和成型技术可以缩短生产周期。
通过使用气体辅助注射成型的方法,制品质量得到提高,而且降低了模具的成本。
使用气体辅助注射成型技术时,它的优点和费用的节约是非常显着的。
1、减少产品变形:低的注射压力使内应力降低,使翘曲变形降到最低;2、减少锁模压力:低的注射压力使合模力降低,可以使用小吨位机台;3、提高产品精度:低的残余应力同样提高了尺寸公差和产品的稳定性;4、减少塑胶原料:成品的肉厚部分是中空的,减少塑料最多可达40%;5、缩短成型周期:与实心制品相比成型周期缩短,不到发泡成型一半;6、提高设计自由:气体辅助注射成型使结构完整性和设计自由度提高;7、厚薄一次成型:对一些壁厚差异大的制品通过气辅技术可一次成型;8、提高模具寿命:降低模腔内压力,使模具损耗减少,提高工作寿命;9、降低模具成本:减少射入点,气道取代热流道从而使模具成本降低;10、消除凹陷缩水:沿筋板和根部气道增加了刚度,不必考虑缩痕问题。
第一阶段:按照一般的注塑成型工艺把一定量的熔融塑胶注射入模穴;第二阶段:在熔融塑胶尚未充满模腔之前,将高压氮气射入模穴的中央;第三阶段:高压气体推动制品中央尚未冷却的熔融塑胶,一直到模穴末端,最后{HotTag}填满模腔;第四阶段:塑胶件的中空部分继续保持高压,压力迫使塑料向外紧贴模具,直到冷却下来;第五阶段:塑料制品冷却定型后,排除制品内部的高压气体,然后开模取出制品。
气辅注塑工艺的应用和工艺过程
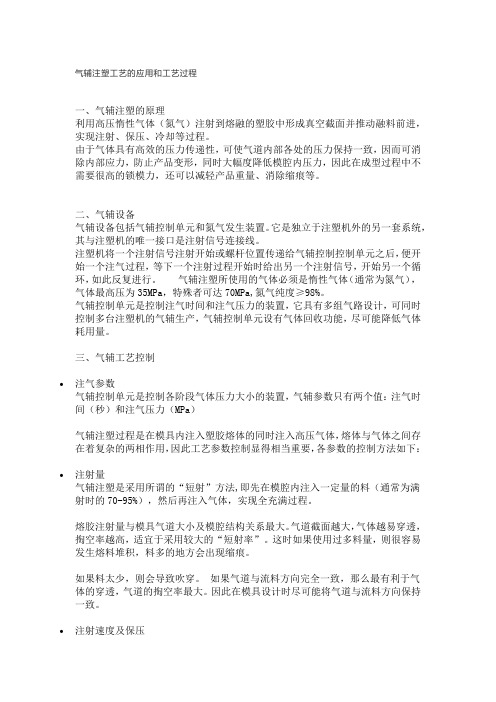
气辅注塑工艺的应用和工艺过程一、气辅注塑的原理利用高压惰性气体(氮气)注射到熔融的塑胶中形成真空截面并推动融料前进,实现注射、保压、冷却等过程。
由于气体具有高效的压力传递性,可使气道内部各处的压力保持一致,因而可消除内部应力,防止产品变形,同时大幅度降低模腔内压力,因此在成型过程中不需要很高的锁模力,还可以减轻产品重量、消除缩痕等。
二、气辅设备气辅设备包括气辅控制单元和氮气发生装置。
它是独立于注塑机外的另一套系统,其与注塑机的唯一接口是注射信号连接线。
注塑机将一个注射信号注射开始或螺杆位置传递给气辅控制控制单元之后,便开始一个注气过程,等下一个注射过程开始时给出另一个注射信号,开始另一个循环,如此反复进行。
气辅注塑所使用的气体必须是惰性气体(通常为氮气),气体最高压为35MPa,特殊者可达70MPa,氮气纯度≥98%。
气辅控制单元是控制注气时间和注气压力的装置,它具有多组气路设计,可同时控制多台注塑机的气辅生产,气辅控制单元设有气体回收功能,尽可能降低气体耗用量。
三、气辅工艺控制•注气参数气辅控制单元是控制各阶段气体压力大小的装置,气辅参数只有两个值:注气时间(秒)和注气压力(MPa)气辅注塑过程是在模具内注入塑胶熔体的同时注入高压气体,熔体与气体之间存在着复杂的两相作用,因此工艺参数控制显得相当重要,各参数的控制方法如下:•注射量气辅注塑是采用所谓的“短射”方法,即先在模腔内注入一定量的料(通常为满射时的70-95%),然后再注入气体,实现全充满过程。
熔胶注射量与模具气道大小及模腔结构关系最大。
气道截面越大,气体越易穿透,掏空率越高,适宜于采用较大的“短射率”。
这时如果使用过多料量,则很容易发生熔料堆积,料多的地方会出现缩痕。
如果料太少,则会导致吹穿。
如果气道与流料方向完全一致,那么最有利于气体的穿透,气道的掏空率最大。
因此在模具设计时尽可能将气道与流料方向保持一致。
•注射速度及保压在保证制品表现不出现缺陷的情况下,尽可能使用较高的注射速度,使熔料尽快充填模腔,这时熔料温度仍保持较高,有利于气体的穿透及充模。
- 1、下载文档前请自行甄别文档内容的完整性,平台不提供额外的编辑、内容补充、找答案等附加服务。
- 2、"仅部分预览"的文档,不可在线预览部分如存在完整性等问题,可反馈申请退款(可完整预览的文档不适用该条件!)。
- 3、如文档侵犯您的权益,请联系客服反馈,我们会尽快为您处理(人工客服工作时间:9:00-18:30)。
1气体辅助注塑成型是通过把高压气体引入到制件的厚壁部位,在注塑件内部产生中空截面,完全充填过程、实现气体保压、消除制品缩痕的一项新颖的塑料成型技术。
传统注塑工艺不能将厚壁和薄壁结合在一起成型,而且制件残余应力大,易翘曲变形,表面时有缩痕。
新发展的气辅技术通过把厚壁的内部掏空,成功地生产出厚壁、偏壁制品,而且制品外观表面性质优异,内应力低。
轻质高强。
现已开发成功气辅产品结构和模具设计包括浇注系统、进气方式和气道分布设计技术,气辅注塑工艺设计技术,气辅注塑工艺设计技术,气辅注塑过程计算机仿真技术,气辅注塑产品缺陷诊断与排除技术,气辅工艺专用料技术。
电视机、家电、汽车、家具、日常用品、办公用品、玩具等为塑料成型开辟了全新的应用领域,气辅注塑技术特别适用于管道状制品、厚壁、偏壁(不同厚度截面组成的制件)和大型扁平结构零件。
气体辅助装置:包括氮气发生和增压系统,压力控制单元和进气元件。
投资约40--200万元(视规模和对设备要求的档次不同而不同)。
气辅工艺能完全与传统注塑工艺(注塑成型机)衔接。
减轻制品重量(省料)可高40%,缩短成型周期(省时达30%,消除缩痕,提高成品率;降低注塑压力达60%,可用小吨位注塑机生产大制件,降低操作成本;模具寿命延长、制造成本降低,还可采用如粗根、厚筋、连接板等更稳固的结构,增加了模具设计自由度。
通常6-18个月可收回增加的设备成本(具体经济效益随制件而议)。
2气体辅助注塑系统,这个先进的系统和技术,是把氮气经由分段压力控制系统直接注射入模腔内的塑化塑料裹,使塑件内部膨胀而造成中空,但仍然保持产品表面的外形完整无缺。
应用气体辅助注塑技术,有以下优点:1)节省塑胶原料,节省率可高达50%。
2)缩短产品生产周期时间。
3)降低注塑机的锁模压力,可高达60%。
4)提高注塑机的工作寿命。
5)降低模腔内的压力,使模具的损耗减少和提高模具的工作寿命。
6)对某些塑胶产品,模具可采用铝质金属材料。
7)降低产品的内应力。
8)解决和消除产品表面缩痕问题。
9)简化产品繁琐的设计。
10)降低注塑机的耗电量。
11)降低注塑机和开发模具的投资成本。
12)降低生产成本。
气体辅助注塑技术,可应用于各种塑胶产品上,如电视机或音响外壳、汽车塑料产品、家私、浴室、橱具、家庭电器和日常用品、各类型塑胶盒和玩具等等。
气体辅助注塑技术在注塑行业中必定被受广泛应用。
材料选择基本上所有用于注塑的热塑性塑料(加强或不加强),及一般工程塑料(如pps,pai,pes)皆适用于气体辅助注塑。
电脑辅助模拟分析1)防止困气和保证气体充填平均。
2)防止气体破成品表面。
3)困气体是有挤压特性,并在保压阶段时起了一定重要作用,因此,借助电脑辅助模拟分析,能保证塑料分布和模具充填作更准确的预测。
注塑机系统设备要求基本上,气体辅助注塑系统可配合全球不同牌子的注塑机,只要是这些注塑机是配备有:1)弹弓射咀,以防止高压气体跑进到注塑机的螺杆里。
2)注塑机的螺杆行程配备电子尺行程开关,以触发讯号给气辅主系统,从而把高压氮气注射进模腔内。
3塑胶制品在人们生产生活中已密不可分,这种供需关系也推动注塑业的迅猛发展.着眼未来石油的稀有性,控制成本是商家必争课题.由于注塑制品被各个行业广泛采用,对塑件精密度的要求也成了业内的难题。
氮气辅助射出作为高新技术,在业界还没得到广泛认知.下面着重介绍一下氮气辅助射出的优越性.传统射出是将溶融塑料通过机械能高压注射到模腔内成型.但在注射,保压,冷却,收缩过程中产生的应力,和塑件壁厚收缩不一,使塑件变形曲翘,因此影响塑件精度.氮气辅助射出也叫氮气保压,它是将氮气高压缩(高最可达350bar)引入模腔(塑件)内部,来接替传统的射出保压.明确点说就是注塑机只需要完成注射模腔所需75%-95%的计量,余下的保压由氮气来完成.由于氮气在塑件内部形成一个中空的氮气高压气泡,并通过气体的特性均匀将压力向外扩张,所以它的应力是不变的.记住气泡永远都只会在中部,同时根据塑件的形状自动充满壁厚较厚的位置.经过冷却后在开模前排气释放压力,这样所得的结果,保压力平均(没有了注射应力),收缩应力平均.由此得到塑件的稳定的高精度尺寸.上述的动作同时能得到更多的帮助:1.在大幅度降低应力下,塑件尺寸得到精确保障;2.由于只需要注射75-95%的计量,因此,塑件本身的重量减轻,根据塑件外形而定,可以得到节省35%或以上的原料;3. 我们说过,在塑件的内部形成中空,通过圆的作用,塑件结构得到加强;4.由于它是经过高压成形,外观上的缩水痕迹也明显不见了;5.肉厚中空了,冷却时间减少了约35%,成形周期也随之改变;6,因为气体形状的随意性,产品设计限制减少,不再期望抽芯或二次成型加工;7氮气是在塑件内部形成的压力.因此锁模压力降低.要模具尺寸允许,您可以在较小的机台上生产,由此降低设备损耗.以上技术被广泛应用于汽车,音响,电视,电脑,打印机,家具,餐具,保健器材,箱包等行业,国际国内企业都已采用并获认可,知名的如SONY,台湾奇美,光电,京瓷,三星;海尔,奂鑫,华博,荣成等.有的为了精度,有的为了省料,都有绝对优势!一、前言气辅注塑工艺是国外八十年代研究成功,九十年代才得到实际应用的一项实用型注塑新工艺,其原理是利用高压隋性气体注射到熔融的塑料中形成真空截面并推动熔料前进,实现注射、保压、冷却等过程。
由于气体具有高效的压力传递性,可使气道内部各处的压力保持一致,因而可消除内部应力,防止制品变形,同时可大幅度降低模腔内的压力,因此在成型过程中不需要很高的锁模力,除此之外,气辅注塑还具有减轻制品重量、消除缩痕、提高生产效率、提高制品设计自由度等优点。
近年来,在家电、汽车、家具等行业,气辅注塑得到越来越广泛的应用,前景看好。
科龙集团于98年引进一套气辅设备用于生产电冰箱、空调器的注塑件。
二、气辅设备气辅设备包括气辅控制单元和氮气发生装置。
它是独立于注塑机外的另一套系统,其与注塑机的唯一接口是注射信号连接线。
注塑机将一个注射信号注射开始或螺杆位置传递给气辅控制单元之后,便开始一个注气过程,等下一个注射过程开始时给出另一个注射信号,开始另一个循环,如此反复进行。
气辅注塑所使用的气体必须是隋性气体(通常为氮气),气体最高压力为35MPa,特殊者可达70MPa,氮气纯度≥98%。
气辅控制单元是控制注气时间和注气压力的装置,它具有多组气路设计,可同时控制多台注塑机的气辅生产,气辅控制单元设有气体回收功能,尽可能降低气体耗用量。
今后气辅设备的发展趋势是将气辅控制单元内置于注塑机内,作为注塑机的一项新功能。
三、气辅工艺控制1.注气参数气辅控制单元是控制各阶段气体压力大小的装置,气辅参数只有两个值:注气时间(秒)和注气压力(MPa)。
2.气辅注塑过程是在模具内注入塑胶熔体的同时注入高压气体,熔体与气体之间存在着复杂的两相作用,因此工艺参数控制显得相当重要,下面就讨论一下各参数的控制方法:a.注射量气辅注塑是采用所谓的“短射”方法(short size),即先在模腔内注入一定量的料(通常为满射时的70-95%),然后再注入气体,实现全充满过程。
熔胶注射量与模具气道大小及模腔结构关系最大。
气道截面越大,气体越易穿透,掏空率越高,适宜于采用较大的“短射率”。
这时如果使用过多料量,则很容易发生熔料堆积,料多的地方会出现缩痕。
如果料太少,则会导致吹穿。
如果气道与流料方向完全一致,那么最有利于气体的穿透,气道的掏空率最大。
因此在模具设计时尽可能将气道与流料方向保持一致。
b.注射速度及保压在保证制品表现不出现缺陷的情况下,尽可能使用较高的注射速度,使熔料尽快充填模腔,这时熔料温度仍保持较高,有利于气体的穿透及充模。
气体在推动熔料充满模腔后仍保持一定的压力,相当于传统注塑中的保压阶段,因此一般讲气辅注塑工艺可省却用注塑机来保压的过程。
但有些制品由于结构原因仍需使用一定的注塑保压来保证产品表现的质量。
但不可使用高的保压,因为保压过高会使气针封死,腔内气体不能回收,开模时极易产生吹爆。
保压高亦会使气体穿透受阻,加大注塑保压有可能使制品表现出现更大缩痕。
c.气体压力及注气速度气体压力与材料的流动性关系最大。
流动性好的材料(如PP)采用较低的注气压力。
几种材料推荐压力如下:塑料种类熔纸(g/10min) 使用气压(MPa)PP 20~30 8~10HIPS 2~10 15~20ABS 1~520~25气体压力大,易于穿透,但容易吹穿;气体压力小,可能出现充模不足,填不满或制品表面有缩痕;注气速度高,可在熔料温度较高的情况下充满模腔。
对流程长或气道小的模具,提高注气速度有利于熔胶的充模,可改善产品表面的质量,但注气速度太快则有可能出现吹穿,对气道粗大的制品则可能会产生表面流痕、气纹。
d.延迟时间延迟时间是注塑机射胶开始到气辅控制单元开始注气时的时间段,可以理解为反映射胶和注气“同步性”的参数。
延迟时间短,即在熔胶还处于较高温度的情况下开始注气,显然有利于气体穿透及充模,但延迟时间太短,气体容易发散,掏空形状不佳,掏空率亦不够。
四、气辅模具气辅模具与传统注塑模具无多大差别,只增加了进气元件(称为气针),并增加气道的设计。
所谓“气道”可简单理解为气体的通道,即气体进入后所流经的部分,气道有些是制品的一部分,有些是为引导气流而专门设计的胶位。
气针是气辅模具很关键的部件,它直接影响工艺的稳定和产品质量。
气针的核心部分是由众多细小缝隙组成的圆柱体,缝隙大小直接影响出气量。
缝隙大,则出气量也大,对注塑充模有利,但缝隙太大会被熔胶堵塞,出气量反而下降。
五、气辅应用实例气辅注塑最适宜于具有粗大柱孔或厚筋的制品以及胶位粗大内部有孔穴的制品(如手柄类、衣架类),国内几间大型电视机厂家都采用气辅注塑工艺生产电视机前框,可节省原材料10%~20%并大幅度降低锁模力。
冰箱顶盖板是大型平板注塑件,质量要求高,其模具采用直浇口入胶,在传统注塑时极易产生变形,影响冰箱的装配。
采用气辅后,变形量得到有效控制,拱曲变形量由原来的1.7~2 mm减少到0.5mm以下。
空调器的横向风板是一长条型结构,截面形状“不规则”,由于表面不允许有熔接痕,模具采取单点水口入胶,料流程长,用传统注塑极易产生变形、缩痕,装在空调器上会影响风向电机的转动,严重者甚至会烧毁电机,因此改善变形量显得尤为重要。
采用气辅工艺后此问题迎刃而解,变形量由原来的3~4mm降为1 mm以内。
手柄则是另一类型的制品,在气辅出现前它是由两件制品装配而成,需要做两付模具而且装配后强度不够,整体也不够美观。
采取气辅后可“合二为一”,省略一付模具及装配工序。
六、总结气辅注塑是近年兴起的一项新工艺,在国外已得到广泛应用,在国内尚处于初始阶段,目前大型家电厂已陆续开始应用这项新工艺,相信随着各厂商对气辅工艺认识的加深,这项新工艺会应用得越来越普遍。