加氢裂化飞温事故过程分析
加氢裂化装置典型事故处理(二)
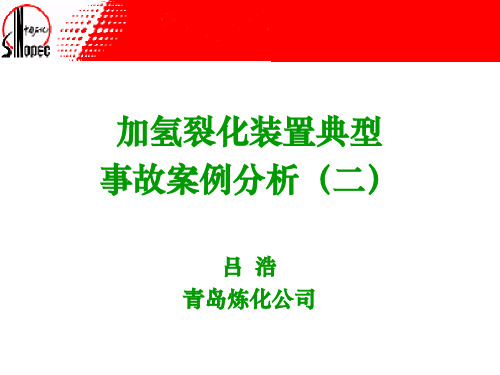
停电导致裂化反应器飞温
u 机组在1989r/min下运转15分钟后,裂化反应器四床 层TI1143温度开始上升,24:05最高达到470℃, 在场厂领导、技术部门、车间协商后决定立即启用 2.1MPa/min进行卸压,同时引入氮气进行置换。 u 停电前裂化反应温度CAT2为372℃,停电后22:17 裂化反应温度CAT2上升到391.7℃。但在24.:10循 氢机停机后,裂化反应器温度快速上升,停电前裂 化反应器四床中部温度TI1143B为373℃,24:00温 度为465℃,到24:58温度快速上升到了882℃。在 中压氮气引入反应系统后反应系统压力充至3.0MPa 后通过泄压阀进行泄压置换。
开工过程中飞温事故
三、事故教训 u 装置紧急泄压后,系统压力至0.1 MPa左右时,如果 反应器床层温度下降幅度不大(仍能大于300℃) ,则必须通过补入纯度99.99%的高纯氮气,边充边 放反应器床层降温至200℃后才可以重新恢复进料 。 u 循环机K102出口4.0MPa氮气日常生产中盲板要处于 通状态,三阀组双阀开,低点放空开,保证随时处 于备用状态。在紧急停工过程中及时联系化验对 4.0MPa氮气进行纯度分析,保证合格。 u 加强队反应器床层超温和循环机故障停运的反事故 处理能力培训工作。
停电导致裂化反应器飞温
此后精制裂化反应器各点温度逐步降低,9月5日 C1001开机前CAT1温度降至300℃,CAT2温度降至 326℃。 9月5日10:10左右,循氢机C1001再次启动,到11 :00左右,转速提至8000RPm,反应各点温度降低 速度加快,到9月5日20:00反应器各点温度都降到 了200℃以下。9月5日18:30装置启动P1001向反应 系统进低氮油进行了冲洗,到21:00停止冲洗。
加氢裂化反应器飞温的因素及控制措施
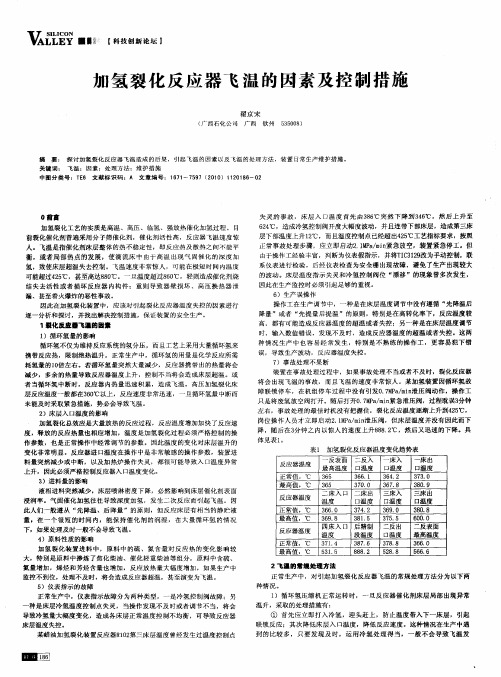
6 )生产 误操作
结 失去 活 性或 者 损 坏 反应 器 内构 件 ;重 则导 致 器 壁损 坏 、高压 换 热 器 泄
漏、甚 至着 火爆炸 的恶性 事故 。
因此在加 氢裂 化装 置 中,应 该对 引起裂 化反应 器温 度 失控 的因素 进行 逐一分 析和探 讨 ,并找 出解决控 制措 施 ,保 证装 置 的安 全生 产。
操作 工在 生产 调节 中, 一种是 在床 层温度 调 节 中没有 遵循 “ 降温 后 先
降量 ”或 者 “ 先提 量 后提 温 ”的原 则 ,特别 是在 高转 化 率下 ,反应 温度 较 高 ,都有 可 能造成 反 应器温 度 的超温 或 者失 控 ;另一 种 是在床 层温 度调 节
1曩 化反应 嚣飞 疆的 因素
可能超 过4 5 2 ℃,甚至 高达 80 。一旦温 度超过 80 8℃ 6 ℃,轻则造 成催化 剂烧
正常 事故 处理 步骤 ,应 立 即启 动2 1P/ J紧 急放 空 ,装置 紧 急停 工。但 . ̄a mn I 由于操 作工 经验丰 富 ,判断 为仪表假 指示 ,并将 TC 19 I32 改为手 动控 制 ,联 系 仪表 进行 检验 ,后经 仪表 检查 为安 全栅 出现 故 障,避 免 了生产 出现 较大 的波动 。床 层温 度 指示失 灵和 冷氢 控 制 阀位 “ 漂移 ”的现象 曾多次发 生 ,
一
反表面 二反入 一床入
一床 出 口温度 330 7.
上升 ,因此 必须严 格控 制反应 器入 口温度 变化 。
失 灵 的事 故 , 床层 入 口温 度 首先 由3 6C突 然 下 降到 3 6C, 然后 上 升 至 8" 4"
加氢事故案例
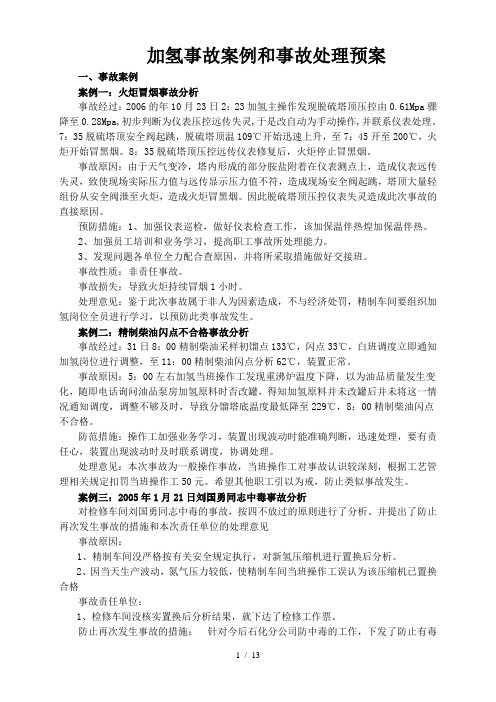
加氢事故案例和事故处理预案一、事故案例案例一:火炬冒烟事故分析事故经过:2006的年10月23日2:23加氢主操作发现脱硫塔顶压控由0.61Mpa骤降至0.28Mpa,初步判断为仪表压控远传失灵,于是改自动为手动操作,并联系仪表处理。
7:35脱硫塔顶安全阀起跳,脱硫塔顶温109℃开始迅速上升,至7:45开至200℃,火炬开始冒黑烟。
8:35脱硫塔顶压控远传仪表修复后,火炬停止冒黑烟。
事故原因:由于天气变冷,塔内形成的部分胺盐附着在仪表测点上,造成仪表远传失灵,致使现场实际压力值与远传显示压力值不符,造成现场安全阀起跳,塔顶大量轻组份从安全阀泄至火炬,造成火炬冒黑烟。
因此脱硫塔顶压控仪表失灵造成此次事故的直接原因。
预防措施:1、加强仪表巡检,做好仪表检查工作,该加保温伴热煌加保温伴热。
2、加强员工培训和业务学习,提高职工事故所处理能力。
3、发现问题各单位全力配合查原因,并将所采取措施做好交接班。
事故性质:非责任事故。
事故损失:导致火炬持续冒烟1小时。
处理意见:鉴于此次事故属于非人为因素造成,不与经济处罚,精制车间要组织加氢岗位全员进行学习,以预防此类事故发生。
案例二:精制柴油闪点不合格事故分析事故经过:31日8:00精制柴油采样初馏点133℃,闪点33℃,白班调度立即通知加氢岗位进行调整,至11:00精制柴油闪点分析62℃,装置正常。
事故原因:5:00左右加氢当班操作工发现重沸炉温度下降,以为油品质量发生变化,随即电话询问油品泵房加氢原料时否改罐,得知加氢原料并未改罐后并未将这一情况通知调度,调整不够及时,导致分馏塔底温度最低降至229℃,8:00精制柴油闪点不合格。
防范措施:操作工加强业务学习,装置出现波动时能准确判断,迅速处理,要有责任心,装置出现波动时及时联系调度,协调处理。
处理意见:本次事故为一般操作事故,当班操作工对事故认识较深刻,根据工艺管理相关规定扣罚当班操作工50元。
希望其他职工引以为戒,防止类似事故发生。
加氢裂化装置反应器飞温原因及处理对策

加氢裂化装置反应器飞温原因及处理对策摘要:加氢裂化装置反应器飞温原因较多,常见的有循环氢流量中断或减少、原料性质改变、床层径向温差较大。
为了提高加氢裂化装置反应器飞温处理效果,技术人员可从循环氢压缩机正常运转、对催化剂进行装填、硫化或钝化等方面着手,降低危险事故的发生率。
关键词:加氢裂化装置;反应器;飞温原因;处理对策飞温是反应器在非稳定操作条件下操作参数出现微扰动导致反应器温度升高的现象之一。
因加氢裂化装置活性较高,容易出现催化剂反应,增加了反应器的飞温速度,导致温度在短期内快速升高,催化剂烧结且失去活性,容易发生各类安全事故。
因此,为了保障加氢裂化装置及生产的安全,接下来本文就加氢裂化装置反应器飞温原因进行分析,提出相应的处理对策。
1加氢裂化装置反应器飞温原因1.1循环氢流量中断或减少反应器的床层放出的热量较多,需要通过循环氢携带,若出现循环氢流量中断或减少的情况,那么床层温度的能力就会失去。
从反应器温度控制方面分析,循环氢终端的影响相当重要,因为循氢机停运,无法往外携带热量,导致原料油和催化剂接触的滞留时间较长,和氢气在高温的反应器中容易继续发生反应且处于持续放热的状态,床层快速升温,必须第一时间采取有效的泄压方法[1]。
同时,还会出现个别床层入口冷氢量增加的问题,增加了其他床层入口氢气量被争夺的情况。
具体来说,循环氢压缩机停运发生的原因较多,常见的有干气密封泄漏量高连锁、冷高压分离器液位高联锁等。
1.2原料性质改变原料油的性质不同,若原料油的氮或含硫量智能机,又或者处理含烯烃量较多的原料时,精制催化剂所在的床层温升处于增加的趋势。
若精致床层的冷氢量较大,还会导致裂化床层入口冷氢降低。
因此,不仅要对加工减压蜡油进行考虑,掺炼焦化蜡油时,还要对混合原料油性质变化进行全面考虑。
针对采取尾油循环工艺装置,若循环油至反应系统流量发生变化,还会改变反应器进料性质。
1.3床层径向温差较大床层径向温差指的是在一个床层水平面上,不同位置的热电偶测量的最低和最高的温度差,可通过其反映不均匀的进料分配和催化剂装填问题,因而原料油在反应器横截面流量分布不够均匀,短路的问题比较常见[2]。
加氢裂化装置安全特点和常见事故分析

加氢裂化装置安全特点和常见事故分析摘要:对某公司五百万吨/年加氢裂化装置的工作原理进行了简单的阐述,并对该装置的安全特性、安全设计等方面进行了探讨,并对该装置的常见事故进行了归纳,并对该装置的运行和检修进行了分析。
关键词:加氢裂化;开工;安全一、装置的生产原理及简介加氢是指在高压条件下,碳氢和碳氢在催化上进行的催化分解和加氢,形成低分子的加氢工艺,以及加氢脱硫、脱氮和不饱和烃的加氢。
它的化学反应包括饱和,还原,裂化和异构。
碳氢化合物在加氢时的反应方向与深度与碳氢化合物组成、催化剂性能、运行环境有关。
加氢装置由反应、分馏、蒸汽发生三部分构成,利用 UOP单管双药全周期加氢裂解技术,实现了最大程度的中馏份,并将其用作洁净燃油的混合成分。
反应段为两组式串联全周期、预混氢、高温生产,并以湿法硫为原料进行硫化。
以低氮油钝化工艺对催化剂进行钝化,利用器外部再生技术对催化剂进行再生;分馏系统主要包括汽提塔、常压分馏塔和石脑油、航煤柴油等。
该设备的主要原材料是降压蜡和炼油,以液化石脑油、石脑油、航空煤油、轻柴油、重柴油等为主。
二、加氢裂化装置安全特点2.1临氢、易燃易爆氢是一种易扩散、燃烧和爆炸的气体。
氢是一种非常活跃的化学物质,它的火焰具有“不可见性”,它的燃烧非常迅速,如果是在空中,哪怕是一点点的火星,哪怕是剧烈的碰撞,都会引起它的爆炸。
2.2系统高温高压在此基础上,对加氢厂的加氢工艺进行了严格的实验研究,提出了高压15.89 MPa和382摄氏度的工艺要求,在生产过程中,必须保证液位的稳定性,避免了串压,不然会引起一场爆炸。
2.3有毒有害化学品多该设备含有大量有毒、有毒的化工原料,包括硫化剂、催化剂、碱液、液氨等,同时还会产生大量有毒的气体,如硫化氢、 CO、羰基镍、苯等,这些有毒的化合物中含有羰基镍和苯,硫化氢对神经系统的毒性很大,所以必须进行严格的监测。
能预防渗漏,熟悉危险化学品的特性和保护。
一旦发现问题,要立即进行处置,并向上级报告,避免事态进一步恶化。
辽阳石化炼油厂加氢裂化装置高压氢气烧伤致死事故1694
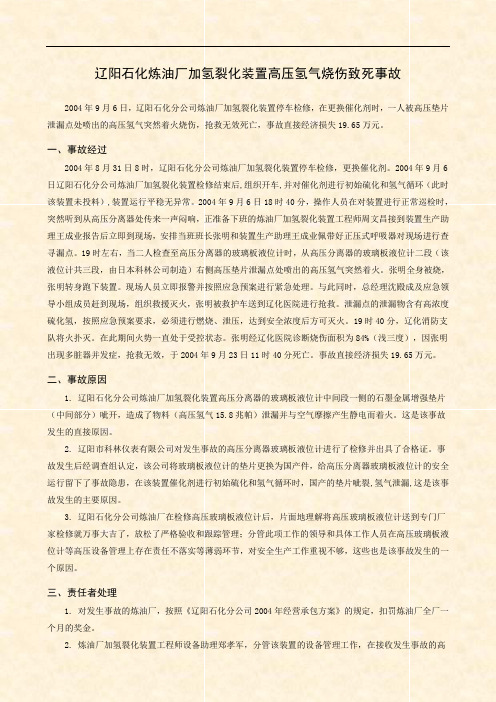
辽阳石化炼油厂加氢裂化装置高压氢气烧伤致死事故2004年9月6日,辽阳石化分公司炼油厂加氢裂化装置停车检修,在更换催化剂时,一人被高压垫片泄漏点处喷出的高压氢气突然着火烧伤,抢救无效死亡,事故直接经济损失19.65万元。
一、事故经过2004年8月31日8时,辽阳石化分公司炼油厂加氢裂化装置停车检修,更换催化剂。
2004年9月6日辽阳石化分公司炼油厂加氢裂化装置检修结束后,组织开车,并对催化剂进行初始硫化和氢气循环(此时该装置未投料),装置运行平稳无异常。
2004年9月6日18时40分,操作人员在对装置进行正常巡检时,突然听到从高压分离器处传来一声闷响,正准备下班的炼油厂加氢裂化装置工程师周文昌接到装置生产助理王成业报告后立即到现场,安排当班班长张明和装置生产助理王成业佩带好正压式呼吸器对现场进行查寻漏点。
19时左右,当二人检查至高压分离器的玻璃板液位计时,从高压分离器的玻璃板液位计二段(该液位计共三段,由日本科林公司制造)右侧高压垫片泄漏点处喷出的高压氢气突然着火。
张明全身被烧,张明转身跑下装置。
现场人员立即报警并按照应急预案进行紧急处理。
与此同时,总经理沈殿成及应急领导小组成员赶到现场,组织救援灭火,张明被救护车送到辽化医院进行抢救。
泄漏点的泄漏物含有高浓度硫化氢,按照应急预案要求,必须进行燃烧、泄压,达到安全浓度后方可灭火。
19时40分,辽化消防支队将火扑灭。
在此期间火势一直处于受控状态。
张明经辽化医院诊断烧伤面积为84%(浅三度),因张明出现多脏器并发症,抢救无效,于2004年9月23日11时40分死亡。
事故直接经济损失19.65万元。
二、事故原因1. 辽阳石化分公司炼油厂加氢裂化装置高压分离器的玻璃板液位计中间段一侧的石墨金属增强垫片(中间部分)呲开,造成了物料(高压氢气15.8兆帕)泄漏并与空气摩擦产生静电而着火。
这是该事故发生的直接原因。
2. 辽阳市科林仪表有限公司对发生事故的高压分离器玻璃板液位计进行了检修并出具了合格证。
加氢裂化事故案例
• 加氢裂化在高温(350425℃)、高压(10 18MPa)的临氢条件下运转,易发生故障;
• 如何减少装置故故障,确保长期案全运转,历来 是人们关注的焦点。
2
1. 设备本身的问题
18
表2. 生产管理问题造成的故障
厂家 操作 原料 蒸汽 助剂 器内 氢气
茂名 O O O O O
金陵 O
HD-C O O
三厂 O
DB-D O
0
DB-L O O
O
19
2.2 典型事例 2.2.1 茂名石化公司
(1)反应器催化剂床层有偏流现象,检修期间卸出催化剂 过程中,发现不正常的地方有烧焦了的灯头和电线, 系检查管理不严,装填催化剂作业时将安全灯遗留在 反应器内所致。
15
1.2.2 齐鲁石化公司
(1)高压放空管线固定卡子设计不良,调试启动紧 急卸压阀时,造成长距离管线从管架上坠地。
(2)反应器引入冷氢的分配系统设计欠佳,催化剂 床层温度分布不均匀,注入冷氢时造成同一截 面温差过大,第五床层温差高达52℃。
(3)制氢装置设计时也因对加热炉热膨胀考虑不周, 被迫停工改造。
7
1.1.2 茂名石化公司
(1)加氢高压热油循环泵开工后一直无法运转,致 使该装置一年未进行热油循环,能耗居高不下。
经查,该油泵系日本荏原制作所制造,采用美
国PACIFIC公司技术,首台产品即销往中国。
日方虽竭尽全力,但仍无法正常运转。一年后,
荏原制作所求助美方协助改造,才使油泵投入
使用。日方虽然做了赔偿,但远远不能弥补一
由于设备材质缺陷或选材不当而造成故障或事故 所占比例较大。其中可分为供货质量和设计质量 两大类。特别是供货质量引起的故障,应给予高 度重视设备故障居多。
加氢裂化装置事故处理讲解
反应系统事故 —— 全装置停电
• 加热炉熄火,烟道挡板、快开风门全开 • 关闭炉前所有瓦斯阀 • 打开放空阀,按紧急降压处理 • 引入补充氢气,继续冷却反应器 • 引入氮气
√ 手动7巴泄压
√ 当床层温度低于正常温度30 ℃时,逐渐恢复正常操作条件 • 当以上处理无效时,如反应器床层最高点温度很快达到428 ℃时,则21巴紧急放空 处理。
反应系统事故 —— 新鲜进料中断
• 加热炉熄火,留长明灯
• 停新氢压缩机
• 循环气继续循环
• 反应器降温至325℃改进低氮油
• 降温至200 ℃时停低氮油,气体循环待命
反应系统事故——原料油带水
• 现象
√ 炉出口温度下降 √ 反应器床层温度下降
√ 反应器出入口压差增大,系统差压上升
√ 生成油颜色变深 • 处理
√ 加强原料油脱水,严重时切换原料罐
√ 防止系统超压 √ 注意系统压差,如果上升很快而降不下来,可减少进油量和氢气量, 严重时可按停原料油处理 √ 因原料油带水引起炉出口、反应器床层温度下降时,炉出口温度不能 提高过多,以免原料油不带水时引起床层超温
• 事故原因:高压串低压,H2爆炸
• 损失巨大:死亡45人,58人受伤,厂房被炸毁,设备、仪 器损坏严重,人的身心安全健康受损。
案例2
• 1987年3月22日7时,英国格朗季蒙斯炼油厂加氢裂化装 置低压分离器因超压发生爆炸,并继而发生大火。事故造
成一人死亡,装置严重损坏。
1.2 飞温事故
• 案例1 • 中石油某加氢裂化装置2007年发生停电事故,循环氢压缩
加氢处理装置安全特点和常见事故分析(汪加海)
加氢处理装置安全特点和常见事故分析摘要:本文简要介绍了广州石化分公司210万吨/年加氢处理装置及其原理,论述了装置的安全特点和安全设计内容。
总结了加氢处理装置容易发生的事故,并列举和分析了国内外同类装置发生的相关事故,结合加氢处理装置开工以来生产实际运行状况,有针对性的提出防范事故的方法,为装置安全生产提供保障。
关键词:加氢处理、事故、安全、防范加氢处理是重质油深度加工的主要工艺之一,集炼油技术、高压技术和催化技术为一体。
加氢处理装置处于高温、高压、临氢、易燃、易爆、有毒介质操作环境,属甲类火灾危险装置。
从原料到产品在操作条件下均具有易燃易爆特性,装置所有区域均为爆炸危险区。
因此分析装置的安全特点,掌握装置的安全技术,了解容易发生的事故,对于确保装置顺利开工及正常生产是十分重要的。
1 装置的生产原理及简介加氢处理采用劣质蜡油加氢处理技术,加氢处理催化剂采用FRIPP的FF14(保护剂采用FZC系列)。
加氢处理过程是在较高压力下,烃类分子与氢气在催化剂表面进行也发生加氢脱硫、脱氮和不饱和烃的加氢反应,同时部份裂解和加氢反应生成较小分子的转化过程。
其化学反应包括饱和、还原、裂化和异构化。
烃类在加氢条件下的反应方向和深度,取决于烃的组成、催化剂的性能以及操作条件等因素。
加氢处理单元主要由反应、分馏等工段组成。
反应部分采用炉前混氢方案、热高分工艺流程。
催化剂的硫化采用湿法硫化。
催化剂再生采用器外再生方案;分馏部分采用汽提塔、常压分馏塔切割石脑油和柴油等馏分方案。
主要原料为常减压蜡油、焦化蜡油和溶剂脱沥青油等蜡油。
主要产品为粗石脑油、柴油和精制蜡油等。
2 加氢处理装置安全特点2.1 临氢、易燃易爆氢气具有易扩散、易燃烧、易爆炸的特点。
氢气的化学性质很活泼,氢气的火焰有“不可见性”,而且燃烧速度很快,在空气中,只要微小的明火甚至猛烈撞击就会发生爆炸。
其爆炸浓度范围为4.1%~75%。
闪点低于28℃的易燃液体、爆炸下限低于10% 的可燃气体为甲类。
加氢厂火灾事故分析怎么写
加氢厂火灾事故分析怎么写1. 事故背景加氢厂是炼油厂的重要设施,主要用于对石油裂化产物进行加氢处理,产生高质量的燃料和化工产品。
由于工作环境特殊,加氢厂容易发生火灾事故。
在实际生产中,加氢厂火灾可能由多种原因引起,如设备故障、操作失误、电气问题等。
2. 原因分析在进行事故分析时,需要对事故的原因进行详细的分析。
首先,对于加氢厂的设备运行状况需要进行全面的评估,检查设备是否存在损坏和老化情况。
其次,需要对操作人员的操作技能和规范程度进行评估,是否存在操作失误的可能性。
另外,还需要对加氢厂的消防设施进行检查,确保设施的完好性和可用性。
综合分析以上因素,可以找出引发事故的原因,从而采取相应的措施进行改进。
3. 应急预案对于加氢厂火灾事故,制定严谨的应急预案是非常重要的。
应急预案需要包括事故发生后的应急处置流程、人员和装备的调度安排、初期扑救措施和事故调查等内容。
另外,要对应急演练进行定期的训练和评估,确保一旦发生事故,能够快速、有效地应对。
4. 事故处理一旦发生加氢厂火灾事故,需要立即启动应急预案,迅速组织人员和装备进行处置。
首先,需要确保人员的安全,将受伤人员迅速转移到安全地带并进行救治。
其次,需要立即启动消防设施,采取控制和扑救火灾的措施,尽快将火势扑灭。
同时,要及时通知相关部门和上级领导,保持信息畅通,协调资源和人力,共同应对事故。
5. 教训总结经过一次次的事故处理和分析,需要总结相关的经验教训,为今后避免类似事故提供借鉴。
首先,要加强设备的维护和检查工作,确保设备的安全可靠。
其次,需要加强操作人员的技能培训和规范化管理,提高操作人员的应对能力。
另外,还需要加强消防设施的维护和更新,确保设施的完好性和可用性。
最后,要加强应急演练和培训,不断提高人员应对突发事件的能力和应对水平。
在实际生产中,加氢厂火灾事故可能对企业造成严重的损失,因此,预防和处理加氢厂火灾事故是非常重要的。
只有加强设备管理、加强人员培训、健全应急预案和经验总结,才能有效地防范和减少加氢厂火灾事故的发生。
- 1、下载文档前请自行甄别文档内容的完整性,平台不提供额外的编辑、内容补充、找答案等附加服务。
- 2、"仅部分预览"的文档,不可在线预览部分如存在完整性等问题,可反馈申请退款(可完整预览的文档不适用该条件!)。
- 3、如文档侵犯您的权益,请联系客服反馈,我们会尽快为您处理(人工客服工作时间:9:00-18:30)。
加氢裂化飞温事故过程分析————————————————————————————————作者: ————————————————————————————————日期:2010年3月5日蜡油加氢裂化装置事故开停工过程分析一装置停工原因1.106-K-102背压蒸汽压力达到4.3MPa,造成汽轮机出口背压蒸汽线上安全阀(放空口为一向下弯头)起跳,并且安全阀未能及时复位,现场大量蒸汽喷向地面并向四周扩散,操作人员无法靠近,不能准确判断具体的泄漏位置,同时避免对系统蒸汽供应产生影响,操作人员在109单元关闭进106装置的9.5MPa蒸汽手阀,循环氢压缩机K102停运,低速泄压阀启动,装置紧急停工。
二事故停、开工经过3月5日5:46装置紧急停工,K102停机,反应系统7bar紧急泄压。
泄压前后床层温度对比如下:R101A紧急泄压床层温度变化温度点5:46泄压开始温度6:24泄压结束温度泄压温降二床入口377.63 362.2 15.43 三床入口379.05 362.09 16.96四床入口381.7 357.424.3 五床入口374.3 352 22.3 六床入口364.7 352.3 12.4R101B紧急泄压床层温度变化温度点5:46泄压开始温度6:24泄压结束温度泄压温降二床入口374.88 362.05 12.83三床入口380.84 365.5215.32四床入口380.42 356.44 23.98五床入口375.95 354.84 21.11六床入口366.05 346.02 20.031.3月5日7:11时向反应系统补氢充压,同时通过7bar放空泄压。
在开K102之前R101A五床层温度升高约30℃,升至380℃,其他床层没有出现明显温升。
为了及时开启循环氢压缩机K102恢复生产,通过新氢压缩机K101三回一将系统压力升至1.8MPa,9:38时开循环氢压缩机转速升至1000rpm;37.5min后转速升至3100rpm,防喘振阀打开,循环氢量20000m3/h;30min后循环氢压缩机转速升至5300rpm,R101A第五床层温升得以控制;10min后(11:05时)循环氢压缩机转速升至6350rpm,R101A/B 第5、第6床层冷氢阀全开,此时R101A/B第六床层温度已快速升高,最终R101A列在11:14时出现下降拐点,而R101B则在此时飞速上升,在11:17时最高点温度达到800℃,3分钟后床层温度开始下降。
反应器床层继续循环降温至200℃,反应系统压力逐渐往10MPa控制。
分馏系统热油运短循环,吸收稳定三塔循环。
2.3月5日19:06时开进料泵,反应系统开始进料,装置进入正常开工程序。
3月6日15:00时柴油改入产品罐,15:36时重石改入产品罐;17:05时轻石、航煤改入产品罐。
三、开工正常后遗留的主要问题及处理建议3月6日下午柴油产品质量发黄,尾油硫含量505ppm(正常小于30),热低分油S:318ppm、N:141ppm(正常S:90;N:3-5)。
通过分别对E104A/B管程出口采样目测,发现R101A生成油颜色蓝而透明,R101B生成油颜色很黄,从而确定B系列高压换热器内漏,造成原料油泄漏至反应生成油中。
通过对E104B、E102B/D、E101B管壳程出入口温度数据分析,怀疑E101B的内漏可能性最大。
R101B高压换热器管壳程出入口最高点温度如下:E101B管程入口TI12505 590.5 E101B壳程入口TI12504 459.4 E101B管程出口TI12502 510 E101B壳程出口TI12506 550E102C/D管程入口TI12502510 E102C/D壳程入口TI12407308E102C/D管程出口TI12501 434E102C/D壳程出口TI12503477.9E104B管程入口TI12404356.6 E104B壳程入口TI12401 102.14E104B管程出口TI12403 349.68 E104B壳程出口TI12407308四经验教训1 、对装置催化剂的性能估计认识不足,未预想到系统压力1.8MPa左右,反应催化剂床层加氢反应激烈导致大量反应热产生,而此时由于K102正在升速过程中,短时间内没有冷氢可用无法带走反应热。
2、反应器床层发生超温事故或循环机故障停运事故,系统泄压要一泄到底,至0.1MPa左右,避免催化剂床层温度进一步升高。
在反应床层温度超温阶段将反应系统压力泄放至最低是非常有效的降温方式。
3、循环机开机程序过程共需要1.5h才能够带负荷运行。
延误了通过冷氢量来控制床层温度的时间。
4、装置紧急泄压后,系统压力至0.1 MPa左右时,如果反应器床层温度下降幅度不大(仍能大于300℃),则必须通过补入纯度99.99%的高纯氮气,边充边放反应器床层降温至200℃后才可以重新恢复进料。
5、循环机K102出口4.0MPa氮气日常生产中盲板要处于通状态,三阀组双阀开,低点放空开,保证随时处于备用状态。
在紧急停工过程中及时联系化验对4.0MPa 氮气进行纯度分析,保证合格。
6、加强队反应器床层超温和循环机故障停运的反事故处理能力培训工作。
附件一:PIC30401操作记录PIC30401操作记录M 2010-03-05 05:14:12 109DM1 10903P_3 PIC30401 MA Autoto Manual\parM 2010-03-05 05:14:17 109DM1 10903P_3 PIC30401 OUT 48.70to 47.70\parM 2010-03-05 05:14:17 109DM110903P_3 PIC30401 OUT 47.70 t o 46.70\parM 2010-03-05 05:14:20 109DM1 10903P_3 PIC30401 OUT 46.70 to 45.70\parM 2010-03-05 05:14:37 109DM1 10903P_3 PIC30401 OUT 45.70 to 44.70\parM 2010-03-05 05:14:37 109DM110903P_3 PIC30401 OUT 44.70 to 43.70\parM 2010-03-05 05:14:38 109DM1 10903P_3 PIC30401 OUT43.70 to 42.70\parM 2010-03-05 05:14:58 109DM1 10903P_3 PIC30401 OUT 42.70 to 41.70\parM 2010-03-05 05:14:58109DM1 10903P_3 PIC30401OUT 41.70to 40.70\parM 2010-03-05 05:15:01 109DM1 10903P_3 PIC30401 OUT 40.70to 39.70\parM 2010-03-05 05:15:01 109DM1 10903P_3 PIC30401 OUT 39.70 to 38.70\parM 2010-03-05 05:15:04 109DM1 10903P_3 PIC30401OUT 38.70 to 37.70\parM 2010-03-05 05:15:04 109DM1 10903P_3 PIC30401 OUT 37.70 to 36.70\parM 2010-03-05 05:15:11 109DM1 10903P_3 PIC30401 OUT 36.70 to 35.70\parM 2010-03-05 05:15:12 109DM1 10903P_3 PIC30401OUT 35.70to 34.70\parM 2010-03-05 05:15:13 109DM1 10903P_3 PIC30401 OUT 34.70 to 33.70\parM 2010-03-05 05:15:18 109DM1 10903P_3 PIC30401 OUT 33.70to 32.70\parM2010-03-05 05:15:19 109DM1 10903P_3 PIC30401 OUT 32.70 to 31.70\parM 2010-03-0505:15:20 109DM1 10903P_3 PIC30401 OUT 31.70 to 30.70\parM 2010-03-05 05:15:27 109DM1 10903P_3PIC30401 OUT 30.70to29.70\parM 2010-03-05 05:15:27 109DM1 10903P_3 PIC30401 OUT 29.70 to 28.70\parM 2010-03-05 05:15:28 109DM1 10903P_3 PIC30401 OUT 28.70 to 27.70\parM 2010-03-05 05:15:35 109DM1 10903P_3 PIC30401 OUT 27.70 to 26.70\parM 2010-03-05 05:15:35109DM1 10903P_3 PIC30401 OUT 26.70to 25.70\parM 2010-03-05 05:16:03 109DM1 10903P_3 PIC30401 OUT 25.70 to26.70\parM 2010-03-05 05:16:03 109DM1 10903P_3 PIC30401OUT 26.70 to 27.70\parM2010-03-05 05:16:04 109DM1 10903P_3 PIC30401 OUT 27.70 to 28.70\parM 2010-03-0505:16:04 109DM1 10903P_3 PIC30401 OUT 28.70 to29.70\parM 2010-03-05 05:16:04 109DM1 10903P_3 PIC30401 OUT 29.70 to 30.70\parM 2010-03-05 05:16:05 109DM1 10903P_3 PIC30401 OUT 30.70 to 31.70\parM 2010-03-05 05:16:05 109DM110903P_3 PIC30401OUT 31.70to 32.70\parM 2010-03-05 05:16:07 109DM1 10903P_3 PIC30401 OUT 32.70 to33.70\parM 2010-03-05 05:16:13 109DM1 10903P_3 PIC30401 OUT 33.70to 32.70\parM 2010-03-0505:16:31 109DM1 10903P_3PIC30401 MA Manual to Auto\parPIC30401趋势曲线图PIC30401控制流程简图附件2:1000002000003000004000005000006000009:00:009:10:309:21:009:31:309:42:009:52:3010:03:0010:13:3010:24:0010:34:3010:45:0010:55:3011:06:0011:16:3011:27:0011:37:3011:48:0011:58:30时间循环氢流量/N m 3/h1000200030004000500060007000转速/r p m循环氢流量循环氢压缩机转速(循环机转速与循环氢量的关系图)9:38 开循环氢压缩机,系统压力1.8MPa ,转速升至1000rp m; 37.5min 后转速逐渐升至3100rpm,循环氢20000m3/h 左右;30mi n后循环氢压缩机转速逐渐升至5300rp m,循环氢量40000m3左右。