水玻璃型壳的缺陷及防止措施
水玻璃型壳熔模铸造制壳工艺过程控制

水玻璃型壳熔模铸造制壳工艺过程控制作者:董丽华来源:《中国科技纵横》2018年第21期摘要:近年来,随着中国的铸造业发展迅速。
其中由于熔模铸造可以做到少切削,不切削,复杂件成型率高,生产工艺水平越来越高,其市场也越来越大。
而大部分的铸件生产任然采用的是水玻璃工艺,这种工艺最大的问题就是不稳定性,所以对水玻璃制壳质量控制要求和生产管理要点的讨论就显得很有必要。
实践证明,通过加强关键工序的控制和质量因素的综合控制,产品质量和成品率会有了显著的提高。
关键词:水玻璃;熔模铸造;制壳;工艺;控制中图分类号:TG249.5 文献标识码:A 文章编号:1671-2064(2018)21-0086-02由于水玻璃粘结剂的价格低廉,制壳周期短,因此在我国广泛采用水玻璃工艺精密铸造。
但是,与传统砂型铸造相比,水玻璃壳型铸造成本高,工艺复杂,生产周期长。
型壳是影响铸件质量的重要因素之一。
如何控制其质量具有重要意义。
本文结合生产实践,对壳的原材料控制和管理和制壳工艺的改善,改善型壳强度及稳定性,从而提高铸件质量及其成品率。
1 原材料的选择与控制1.1 水玻璃硅酸钠的水溶液俗称水玻璃,南方一般被称为水玻璃,北方一般被称为泡化碱。
硅酸钠的形态可分为液体、固体和水淬三种形态。
水玻璃可分为钾水玻璃和钠水玻璃。
熔模铸造中一般采用的是钠水玻璃。
水玻璃中二氧化硅和氧化钠(或氧化钾)的摩尔比通常称为模数(M)。
硅酸钠是水分散体系中的无色、浅色透明或半透明粘稠液体。
固体硅酸钠是一种无色和浅色的透明或半透明玻璃。
硅酸钠在的凝固与石灰非常相似。
主要通过碳化、脱水、固化三个工序来实现。
随着二氧化硅含量的增加,游离水蒸发,硅胶脱水成固体SiO2并固化。
由于空气中CO2浓度低,碳化反应和固化过程非常缓慢。
1.2 水玻璃的特性熔模铸造生产时水玻璃应为液态,纯净的水玻璃是一种外观显无色透明的粘滞性溶液,含有杂质时则显青灰色或者淡黄色。
水玻璃溶液显碱性,一般高、中模数的水玻璃的PH值为11~13。
铸件常见缺陷及防止方法
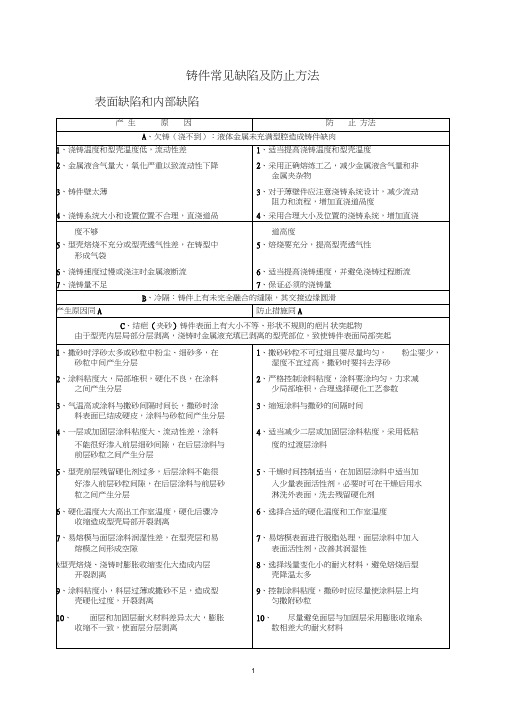
铸件常见缺陷及防止方法表面缺陷和内部缺陷
T 、跑火:钢水穿透型壳,在铸件上形成不规则的多余金属突起 尺寸和粗糙度超差
1、 拉长:铸件几何尺寸超出图样规定范围
2、 变形:铸件平面度、平行度、同轴度以及各单元的相对位置超出图样规定范围
3、 表面粗糙度差:铸件表面粗糙度超出图样规定范围
1、 2、 3铸件结构和浇铸系统设计不合理,在铸件冷
却过程中收缩受阻,产生的热应力和相变应 力超过在弹性状态的铸件材料的强度而断裂
清理过程中有残余应力铸件受外力作用断裂 钢水质量不高,杂质多 1、 2、 3改进铸件结构,减小壁厚差,增设加强肋
等。
合理设计浇铸系统,减少铸造应力
铸件生产过程中应避免受剧烈撞击 改进熔练工艺,提高钢水质量,减少杂质。
CO2水玻璃砂夹砂缺陷的解决措施

CO2水玻璃砂夹砂缺陷的解决措施摘要:本文从夹砂形成的机理出发,结合CO2水玻璃砂的生产实际,对发生的夹砂缺陷,系统分析其产生的原因,提出了防止夹砂的措施,在生产上收到了较好的效果。
关键词:CO2水玻璃砂夹砂防止措施前言我公司用CO2水玻璃砂生产铁路货车用摇枕、侧架等铸钢件。
2001年,在生产过程中,在摇枕、侧架铸件上出现了严重的夹砂缺陷,其部位在内浇口引入型腔的平面及侧面,导致铸件报废上百件,造成很大的经济损失,高达几十万元之多。
针对出现的夹砂缺陷,分析问题的原因,采取预防措施。
2002年以来,从2月到3月,连续生产两个月,生产的铸件基本上杜绝了夹砂缺陷的发生,取得了良好的经济效益。
一、CO2水玻璃砂产生夹砂的分析:1、夹砂形成机理:当砂型中浇入金属液,在型腔尚未充满和金属液尚未凝固时,一方面,金属液对型腔表面砂层热作用,砂型表面层温度急剧上升,因而表面层受热急剧膨胀,产生热应力;另一方面,砂型表面层产生的水蒸气通人砂型内部时,被冷却而凝聚在表面干燥层的下面,成为水分饱和凝聚薄层。
此层热温强度很低,仅为正常状态湿强度的几分之一。
由于石英膨胀热应力的作用,迫使表面层有沿着水分凝聚层滑动而拱起的趋势。
此时,金属液尚未充满,金属液的压力作用迟于表面层的拱起开裂。
砂型开裂后,当金属液从破裂处侵入冷却凝固后,就形成夹砂。
2、水玻璃砂不易形成夹砂的机理:水玻璃型砂,在低温时,由于铸型的刚体性质,不能吸收膨胀,产生的应力就大;相反,在具有大膨胀量的高温下,由于铸型显示出粘弹性的性质,在某种程度上可以吸收膨胀,所以应力小。
因为水玻璃砂具有这种加热后,开始时膨胀,但是随后就收缩的特性,故不易产生夹砂。
3、夹砂形成的原因分析:CO2水玻璃砂不易形成夹砂,为什么产生夹砂呢?从夹砂形成的机理可以看出,在以石英砂颗粒为骨干的铸造条件下,型腔表面砂层的热膨胀和铸型内的水分迁移是形成夹砂的外因。
砂层膨胀造成的热应力是表面拱起的动力,砂层的容让变形能力和层与层之间的连接强度是表面拱起破裂的阻力。
铸件常见缺陷及防止方法

一、表面缺陷和内部缺陷
产生原因
防止方法
A、欠铸(浇不到):液体金属未充满型腔造成铸件缺肉
1、浇铸温度和型壳温度低,流动性差
2、金属液含气量大,氧化严重以致流动性下降
3、铸件壁太薄
4、浇铸系统大小和设置位置不合理,直浇道高度不够
5、型壳焙烧不充分或型壳透气性差,在铸型中形成气袋
6、浇铸速度过慢或浇注时金属液断流
2、壳烧不充分,没排除蜡残余及壳中发气杂质
3、冷壳浇铸,型壳受潮
4、钢水含气多,脱氧不良
5、浇铸系统设计不合理,浇铸时卷入气体
1、改善壳透气性,
2、充分焙烧型壳
3、热壳浇铸,防止受潮
4、改进脱氧方法
5、改进浇铸系统结构
N、多孔性气孔和针孔:铸件上的细小、分散或密集的孔眼
1、炉料不干净,
2、钢水脱氧不良,镇静时间不够,含气量高
1、水玻璃型壳热水脱蜡时,脱蜡液碱性偏大,模料皂化,造成型壳内层局部酥软煮烂
2、面层涂料粘度过大,局部堆积,硬化不透,热水脱蜡时,局部面层涂料层不规则脱落
3、模料熔失不充分,焙烧不彻底,使皂化物和其它有害杂质沉积在型壳内表面某个部位
4、水玻璃型壳的水玻璃模数高、密度大、硬化不充分,造成型壳局部钠盐集聚
5、改进涂料配方,适当增加层数,必要时可采用一些局部强化措施
H、铁刺:铸件表面上出现许多分散或密集的小突刺
1、面层涂料中粉料量少,粘度低
2、面层涂料相对易熔模的涂挂性差
3、面层涂料配制时搅拌时间不充分,涂挂时面层涂料中的粉料趋向撒砂砂粒分布
4、表面层撒砂砂粒较大
1、适当增加面层涂料中粉料加入量,提高粘度
2、严格控制涂料粘度,涂料要涂均匀,力求减少局部堆积,合理选择硬化工艺参数
铸造缺陷分类及介绍
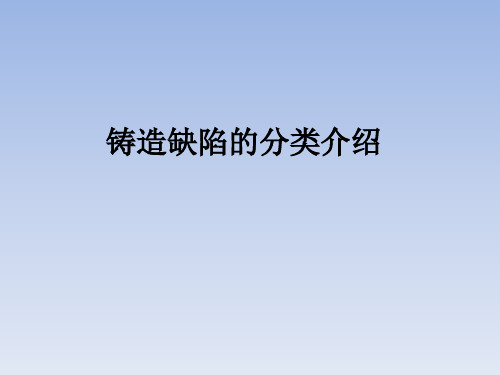
一:蜡模缺陷
1:鼓包及产生原因 和防止方法
鼓包
序号
1
缺陷原因
模料中搅入了气体
防止方法
配制料时应避裹入过多气体
2
起模太早,被压缩的气泡膨胀
适当延长保压时间
3
熔模没有及时冷却,或 不充分
冷却
从压型中取出的熔模应及时冷却,并 控制冷却时间。
4
制模室温度过高
严格控制制模室温度
1
一:蜡模缺陷
2:裂纹及产生原因 和防止方法
裂纹
序号
1
缺陷原因
起模时间过长,熔模收缩受阻
防止方法
控制熔模在压型中的冷却时间
2
模料收缩率大或太脆
改用收缩率小、韧性好的模料
3
压型设计不正确或起模操作不当
改进压型设计,增大圆角或起模斜度, 起模时用力要均匀。
4
压型温度过低,使熔模冷却太快
提高压型的工作温度
5
压注时模料温度偏高
4
5
选择热裂倾向小的合金或钢种
14
二:铸件表面缺陷
7:冷裂及产生原因 和防止方法
冷裂
序号
1
缺陷原因
铸件结构不合理
防止方法
改进铸件结构和浇注系统设计,减小 收缩应力
避免撞击和抛甩铸件
2
浇注系统设计不合理
3
铸件在搬运和清砂过程中受撞击
矫正前退火,并改进矫正操作
4
铸件在矫正时操作不当或未退火
减少型壳层数,并改善退让性
6:热裂及产生原因 和防止方法
热裂
序号
1
缺陷原因
铸型温度低,冷却速度过快
防止方法
提高铸型温度,减缓铸件冷却速度
水玻璃类防腐蚀工程表面起皮、起砂-施工通病防治
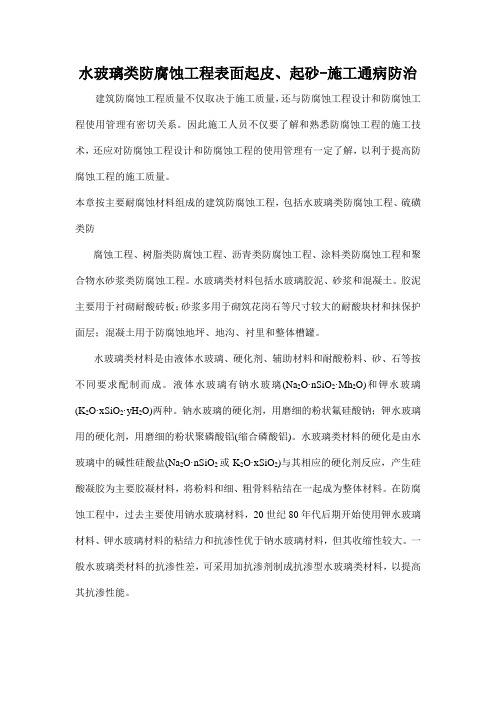
水玻璃类防腐蚀工程表面起皮、起砂-施工通病防治建筑防腐蚀工程质量不仅取决于施工质量,还与防腐蚀工程设计和防腐蚀工程使用管理有密切关系。
因此施工人员不仅要了解和熟悉防腐蚀工程的施工技术,还应对防腐蚀工程设计和防腐蚀工程的使用管理有一定了解,以利于提高防腐蚀工程的施工质量。
本章按主要耐腐蚀材料组成的建筑防腐蚀工程,包括水玻璃类防腐蚀工程、硫磺类防腐蚀工程、树脂类防腐蚀工程、沥青类防腐蚀工程、涂料类防腐蚀工程和聚合物水砂浆类防腐蚀工程。
水玻璃类材料包括水玻璃胶泥、砂浆和混凝土。
胶泥主要用于衬砌耐酸砖板;砂浆多用于砌筑花岗石等尺寸较大的耐酸块材和抹保护面层;混凝土用于防腐蚀地坪、地沟、衬里和整体槽罐。
水玻璃类材料是由液体水玻璃、硬化剂、辅助材料和耐酸粉料、砂、石等按不同要求配制而成。
液体水玻璃有钠水玻璃(Na2O·nSiO2·Mh2O)和钾水玻璃(K2O·xSiO2·yH2O)两种。
钠水玻璃的硬化剂,用磨细的粉状氟硅酸钠;钾水玻璃用的硬化剂,用磨细的粉状聚磷酸铝(缩合磷酸铝)。
水玻璃类材料的硬化是由水玻璃中的碱性硅酸盐(Na2O·nSiO2或K2O·xSiO2)与其相应的硬化剂反应,产生硅酸凝胶为主要胶凝材料,将粉料和细、粗骨料粘结在一起成为整体材料。
在防腐蚀工程中,过去主要使用钠水玻璃材料,20世纪80年代后期开始使用钾水玻璃材料、钾水玻璃材料的粘结力和抗渗性优于钠水玻璃材料,但其收缩性较大。
一般水玻璃类材料的抗渗性差,可采用加抗渗剂制成抗渗型水玻璃类材料,以提高其抗渗性能。
钠和钾水玻璃材料在技术性能上虽有不同,但在防腐蚀工程中出现的质量通病和防治措施基本相同,在本节中综合介绍。
1.现象表面不光滑、起皮、起砂,用脚搓动或用硬物刮划表面时,有粉或砂粒脱落。
2.原因分析(1)水玻璃的模数低,密度小,产生硅酸凝胶少,强度不够。
(2)硬化剂用量不够。
水玻璃型壳缺陷
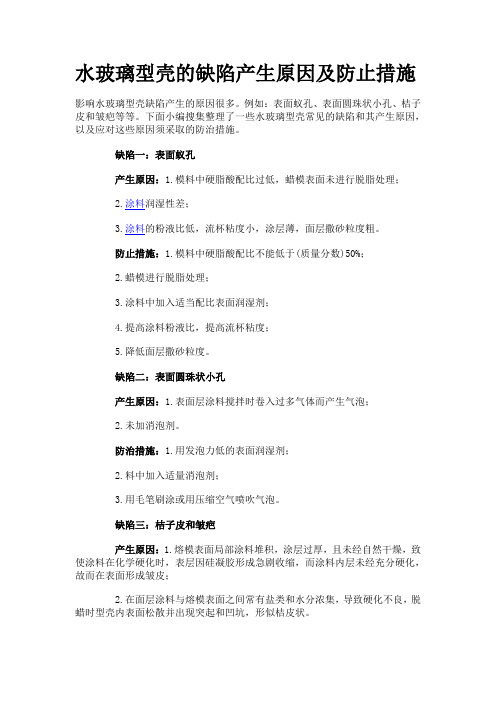
水玻璃型壳的缺陷产生原因及防止措施影响水玻璃型壳缺陷产生的原因很多。
例如:表面蚁孔、表面圆珠状小孔、桔子皮和皱疤等等。
下面小编搜集整理了一些水玻璃型壳常见的缺陷和其产生原因,以及应对这些原因须采取的防治措施。
缺陷一:表面蚁孔产生原因:1.模料中硬脂酸配比过低,蜡模表面未进行脱脂处理;2.涂料润湿性差;3.涂料的粉液比低,流杯粘度小,涂层薄,面层撒砂粒度粗。
防止措施:1.模料中硬脂酸配比不能低于(质量分数)50%;2.蜡模进行脱脂处理;3.涂料中加入适当配比表面润湿剂;4.提高涂料粉液比,提高流杯粘度;5.降低面层撒砂粒度。
缺陷二:表面圆珠状小孔产生原因:1.表面层涂料搅拌时卷入过多气体而产生气泡;2.未加消泡剂。
防治措施:1.用发泡力低的表面润湿剂;2.料中加入适量消泡剂;3.用毛笔刷涂或用压缩空气喷吹气泡。
缺陷三:桔子皮和皱疤产生原因:1.熔模表面局部涂料堆积,涂层过厚,且未经自然干燥,致使涂料在化学硬化时,表层因硅凝胶形成急剧收缩,而涂料内层未经充分硬化,故而在表面形成皱皮;2.在面层涂料与熔模表面之间常有盐类和水分浓集,导致硬化不良,脱蜡时型壳内表面松散并出现突起和凹坑,形似桔皮状。
防止措施:1.表面层涂料粘度不要太高,增加涂料流动性;2.避免蜡模表面及局部涂料堆积,应使涂料分布均匀;3.表面层浸涂料撒砂后,先经一定时间的自然干燥后,再进行化学硬化;4.表面层的化学硬化要充分。
缺陷四:型壳分层和鼓胀产生原因:1.涂料撒砂后,表面有浮砂;2.表面层撒砂的粒度过细,砂中粉尘过多或砂粒受潮含水分过多;3.型壳表面层化学硬化后风干时间过短,残留硬化剂过多;4.涂料粘度过大涂层过厚,涂层中间未硬化。
防治措施:1.表面层撒砂要干燥,无粉尘,(水的质量分数小于0.3%);2.表面层撒砂粒度不要太细,并防止浮砂堆积;3.表面层涂料粘度不宜太大,防止涂料堆积,涂层要充分硬化;4.表面层硬化后的干燥时间要充分,残留硬化剂要少。
水玻璃造型浇铸安全操作要点
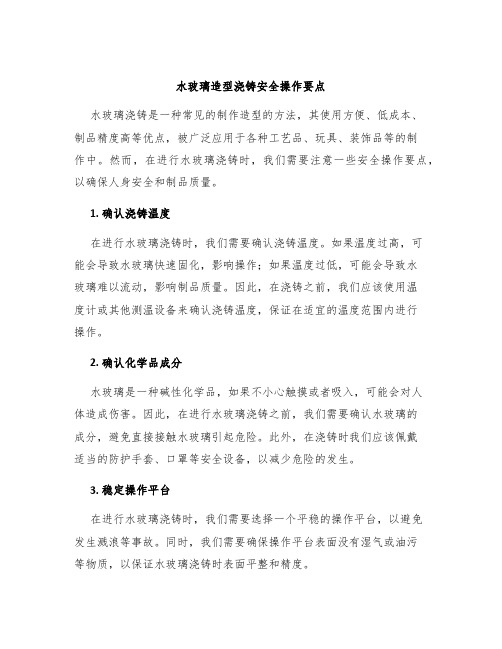
水玻璃造型浇铸安全操作要点水玻璃浇铸是一种常见的制作造型的方法,其使用方便、低成本、制品精度高等优点,被广泛应用于各种工艺品、玩具、装饰品等的制作中。
然而,在进行水玻璃浇铸时,我们需要注意一些安全操作要点,以确保人身安全和制品质量。
1. 确认浇铸温度在进行水玻璃浇铸时,我们需要确认浇铸温度。
如果温度过高,可能会导致水玻璃快速固化,影响操作;如果温度过低,可能会导致水玻璃难以流动,影响制品质量。
因此,在浇铸之前,我们应该使用温度计或其他测温设备来确认浇铸温度,保证在适宜的温度范围内进行操作。
2. 确认化学品成分水玻璃是一种碱性化学品,如果不小心触摸或者吸入,可能会对人体造成伤害。
因此,在进行水玻璃浇铸之前,我们需要确认水玻璃的成分,避免直接接触水玻璃引起危险。
此外,在浇铸时我们应该佩戴适当的防护手套、口罩等安全设备,以减少危险的发生。
3. 稳定操作平台在进行水玻璃浇铸时,我们需要选择一个平稳的操作平台,以避免发生溅浪等事故。
同时,我们需要确保操作平台表面没有湿气或油污等物质,以保证水玻璃浇铸时表面平整和精度。
4. 防止高温烫伤在进行水玻璃浇铸时,我们需要注意防止高温烫伤。
由于水玻璃浇铸时用的是高温液体,如果不小心触摸到液体,可能会导致皮肤烫伤。
因此,在进行水玻璃浇铸时,我们应该穿上适当的隔热服装,以降低烫伤的风险。
5. 保持工作区域干燥在进行水玻璃浇铸时,我们需要保持工作区域干燥。
由于水玻璃浇铸时需要注入液体,如果工作区域有积水或者潮湿,可能会导致水玻璃浇铸出现质量问题。
因此,在进行水玻璃浇铸时,我们需要选择一个干燥的工作区域,以确保制品质量。
6. 正确清洗设备和工具在进行水玻璃浇铸时,我们需要正确清洗设备和工具。
由于水玻璃是一种化学物品,容易污染设备和工具,如果不及时清洗,则可能影响下次的使用和浇铸质量。
因此,在进行水玻璃浇铸时,我们需要使用清洁水和清洁剂对设备和工具进行彻底的清洗。
水玻璃浇铸是一种简单、高效的制作造型的方法,但在进行水玻璃浇铸时,我们需要注意以上安全操作要点,以确保安全和制品质量。
- 1、下载文档前请自行甄别文档内容的完整性,平台不提供额外的编辑、内容补充、找答案等附加服务。
- 2、"仅部分预览"的文档,不可在线预览部分如存在完整性等问题,可反馈申请退款(可完整预览的文档不适用该条件!)。
- 3、如文档侵犯您的权益,请联系客服反馈,我们会尽快为您处理(人工客服工作时间:9:00-18:30)。
5.以氯化铝和氯化镁硬化的型壳在浸第二层涂料前须进行冲水,晾干,以增强层间结合
型壳裂纹
1.浸涂料后未能撒上砂粒的部位易产生裂纹
2.涂料粘度过低,粉料加入量少,涂层过薄
3.涂层未经充分硬化
4.脱蜡水温度低,脱蜡时间过长
5.水玻璃模数低,密度小
6.型壳层数不足
3.脱蜡水温度低,脱蜡时间过长
4.焙烧时型壳受挤压或温度过高
1.控制涂料粉液比和粘度
2.避免涂料局部堆积
3.控制硬化剂浓度、温度和硬化时间等工艺参数
4.缩短脱蜡时间,适当提高脱蜡水温度(95-98℃)
表面析出物(茸毛状析出物、瘤状、鹿角状析出物)
1.氯化铵硬化的型壳,脱蜡后干燥时,型壳内在硬化反应时生成的盐分及残留的氯化铵硬化剂,随水分蒸发扩散迁移到型壳表面上来,并沿析出孔道堆集生长成茸毛状物质,其中4∕5是氯化钠,约1∕5是氯化铵
表面圆珠状小孔
1.表面层涂料搅拌时卷入过多气体而产生气泡
2.未加消泡剂
1.用发泡力低的表面润湿剂
2.料中加入适量消泡剂
3.用毛笔刷涂或用压缩空气喷吹气泡
桔子皮和皱疤
1.熔模表面局部涂料堆积,涂层过厚,且未经自然干燥,致使涂料在化学硬化时,表层因硅凝胶形成急剧收缩,而涂料内层未经充分硬化,故而在表面形成皱皮
2.氯化铝硬化的型壳(尤其是聚含氯化铝硬化),硬化反应时产生铝胶氢氧化铝,通常氢氧化铝以弥散状态分布于型壳中,若硬化时间不足,在脱蜡时脱蜡水的PH值高,就可能使残留的氯化铝析出难溶的氢氧化铝附于型壳内外表面上,形成析出物
1.型壳脱蜡后存放时间不要太长,应及时焙烧浇注
2.水玻璃密度不宜过大
3.涂料粘度不要过高
2.在面层涂料与熔模表面之间常有盐类和水分浓集,导致硬化不良,脱蜡时型壳内表面松散并出现突起和凹坑,形似桔皮状
1.表面层涂料粘度不要太高,增加涂料流动性
2.避免蜡模表面及局部涂料堆积,应使涂料分布均匀
3.表面层浸涂料撒砂后,先经一定时间的自然干燥后,再进行化学硬化
4.表面层的化学硬化要充分
型壳分层和鼓胀
水玻璃型壳的缺陷及防止措施
水玻璃型壳的缺陷及防止措施缺陷名称产生原因防止措施表面蚁孔1.模料中硬脂酸配比过低,蜡模表面未进行脱脂处理2.涂料润湿性差3.涂料的粉液比低,流杯粘度小,涂层薄,面层撒砂粒度粗1.模料中硬脂酸配比不能低于(质量分数)50% 2.蜡模进行脱脂处理3.
水玻璃型壳的缺陷及防止措施
1.涂料撒砂后,表面有浮砂
2.表面层撒砂的粒度过细,砂中粉尘过多或砂粒受潮含水分过多
3.型壳表面层化学硬化后风干时间过短,残留硬化剂过多
4.涂料粘度过大涂层过厚,涂层中间未硬化
1.表面层撒砂要干燥,无粉尘,(水的质量分数小于0.3%)
2.表面层撒砂粒度不要太细,并防止浮砂堆积
3.表面层涂料粘度不宜太大,防止涂料堆积,涂层要充分硬化
4.氯化铝硬化剂的PH值要适当,硬化时间要充足
5.脱蜡水应保持酸性
1.控制水玻璃的模数、密度及涂料粉液比和粘度
2.控制硬化剂的浓度、温度及硬化时间等工艺参数
3.提高脱蜡水温度至95-98℃,缩短脱蜡时间
4.适当增加型壳层数
5.大件型壳在制壳时可用铁丝加固,以增加高温强度
型壳变形(高温)
型壳变形大多在脱蜡、焙烧或浇注时产生
1.涂料的粘度过大,涂层过厚,涂料堆积
2.硬化剂浓度低,温度低,硬化时间太短,硬化不足
缺陷名称
产生原因
防止措施
表蚁孔
1.模料中硬脂酸配比过低,蜡模表面未进行脱脂处理
2.涂料润湿性差
3.涂料的粉液比低,流杯粘度小,涂层薄,面层撒砂粒度粗
1.模料中硬脂酸配比不能低于(质量分数)50%
2.蜡模进行脱脂处理
3.涂料中加入适当配比表面润湿剂
4.提高涂料粉液比,提高流杯粘度
5.降低面层撒砂粒度