旋转弯曲疲劳标准
曲轴弯曲疲劳试验标准

曲轴是内燃机的重要部件之一,它承受着发动机高速旋转和往复运动带来的巨大压力和应力。
为了确保曲轴的可靠性和耐久性,需要进行曲轴弯曲疲劳试验。
曲轴弯曲疲劳试验标准是指对曲轴进行弯曲加载,并在一定的试验条件下进行疲劳寿命测试的规范和要求。
下面将详细介绍曲轴弯曲疲劳试验的标准。
一、试验目的曲轴弯曲疲劳试验的主要目的是评估曲轴在长期使用过程中的弯曲疲劳寿命,为曲轴的设计和制造提供依据。
通过试验,可以确定曲轴的疲劳强度和疲劳寿命,为改进曲轴的设计和材料选择提供参考。
二、试验方法1. 试验样品的选择:根据实际情况选择代表性的曲轴样品进行试验。
样品的选择应符合相关标准和规范要求。
2. 试验设备的准备:确保试验设备的准确性和可靠性。
试验设备应能够提供符合要求的弯曲加载条件。
3. 试验参数的确定:根据曲轴的实际使用情况和相关标准,确定试验参数,如载荷幅值、载荷频率、试验温度等。
4. 试验过程的控制:按照设定的试验参数进行试验,并对试验过程进行实时监测和记录。
确保试验过程的准确性和可重复性。
5. 试验结果的评估:通过试验结果的评估,确定曲轴的疲劳强度和疲劳寿命,并与相关标准进行比较和分析。
三、试验标准1. 载荷幅值:根据曲轴的设计要求和使用条件确定载荷幅值。
载荷幅值应能够真实模拟曲轴在实际使用中承受的载荷变化。
2. 载荷频率:根据曲轴的使用情况和相关标准,确定载荷频率。
载荷频率应能够真实模拟曲轴在实际使用中的工作状态。
3. 试验温度:根据曲轴的使用条件和材料特性,确定试验温度。
试验温度应能够真实模拟曲轴在实际使用中的工作温度。
4. 试验次数:确定试验次数时,应考虑曲轴的设计寿命和安全系数。
试验次数应能够真实模拟曲轴在实际使用中的寿命。
5. 试验结果评估:根据试验结果评估曲轴的疲劳强度和疲劳寿命,并与相关标准进行比较和分析。
评估结果应符合相关标准的要求。
四、试验报告完成试验后,应编制试验报告,报告内容应包括试验目的、试验方法、试验过程、试验结果和评估等。
旋转纯弯曲疲劳试验机检定方法
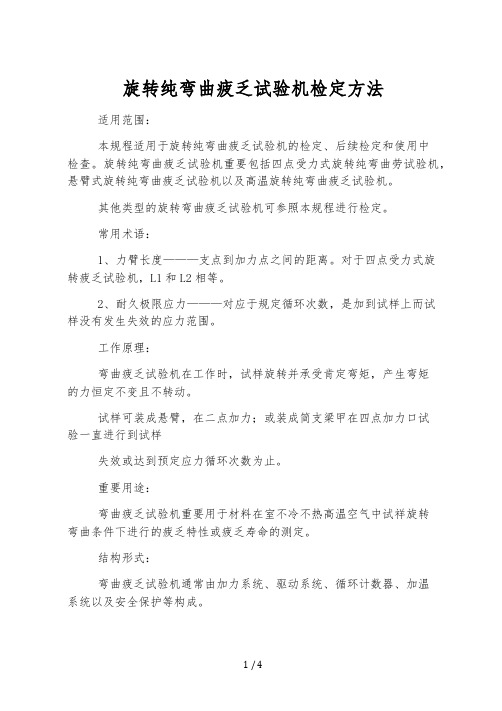
旋转纯弯曲疲乏试验机检定方法适用范围:本规程适用于旋转纯弯曲疲乏试验机的检定、后续检定和使用中检查。
旋转纯弯曲疲乏试验机重要包括四点受力式旋转纯弯曲劳试验机,悬臂式旋转纯弯曲疲乏试验机以及高温旋转纯弯曲疲乏试验机。
其他类型的旋转弯曲疲乏试验机可参照本规程进行检定。
常用术语:1、力臂长度———支点到加力点之间的距离。
对于四点受力式旋转疲乏试验机,L1和L2相等。
2、耐久极限应力———对应于规定循环次数,是加到试样上而试样没有发生失效的应力范围。
工作原理:弯曲疲乏试验机在工作时,试样旋转并承受肯定弯矩,产生弯矩的力恒定不变且不转动。
试样可装成悬臂,在二点加力;或装成简支梁甲在四点加力口试验一直进行到试样失效或达到预定应力循环次数为止。
重要用途:弯曲疲乏试验机重要用于材料在室不冷不热高温空气中试祥旋转弯曲条件下进行的疲乏特性或疲乏寿命的测定。
结构形式:弯曲疲乏试验机通常由加力系统、驱动系统、循环计数器、加温系统以及安全保护等构成。
计量性能要求:1、加力系统A、左,右夹头土轴同轴度弯曲疲乏试验机夹紧试样时,左、右夹头主轴同轴度为0.02mm。
B、左、右夹头高度差弯曲疲乏试验机夹紧试样时,左、右夹头的高度差不应超过0.1mm。
C、主轴箱动态径向跳动量弯曲疲乏试验机夹紧试样(不加祛码)运转时。
土轴箱施力部位的动态径向跳动量不超过0.06mm。
D、力加载机构①力臂弯曲疲乏试验机力臂长度的扣对误差不超过0.3%。
②初始弯矩弯曲疲乏试验机的初始弯矩应尽可能小,初始弯矩不应大于疲乏试验机zui大弯矩的}10%。
③弯矩重复性和对误差弯曲疲乏试验机从zui大弯矩的10%开始,至疲乏试验机zui大弯矩,其弯矩示值相对误差不大于1%。
④弯矩示值相对误差弯曲疲乏试验机从zui大弯炬的10%开始,至疲乏试验机zui大弯矩,其弯矩示值相对误差的zui大允许值为1%。
⑤左、右弯矩相对误差左右两边施加弯矩的疲乏试验机,其左、右弯矩应相等,左、右弯矩相对误差不应超过单边弯矩标称值的1%。
iso 1143金属材料旋转弯曲疲劳试验方法

iso 1143金属材料旋转弯曲疲劳试验方法
ISO 1143是一项关于金属材料旋转弯曲疲劳试验方法的国际标准。
该标准的目的是确定金属材料在旋转弯曲载荷下的疲劳强度和寿命。
金属材料旋转弯曲疲劳试验是一种常用的测试方法,用于评估金属材料在不断施加旋转弯曲载荷下的耐久性能。
这种试验方法可以模拟材料在实际使用过程中受到的循环载荷,如摩擦、振动和机械应力等。
根据ISO 1143标准,进行金属材料旋转弯曲疲劳试验的基本步骤如下:
1. 根据试验要求,选择适合的试验设备和样品。
确保样品具有规定的几何形状和尺寸。
2. 在试验设备上安装好样品,并根据标准规定的试验频率和幅值施加旋转弯曲载荷。
载荷的施加应符合标准的要求,并确保载荷的稳定性和准确性。
3. 进行预先设定的试验循环数或持续时间。
循环数和持续时间的设定应根据材料的特性和试验要求确定。
4. 在试验过程中,记录样品的应变和载荷数据。
这些数据可以用于分析材料的疲劳性能和寿命。
5. 在试验完成后,对样品进行质量评估和疲劳寿命分析。
根据需要,可以对样品进行断口分析、金相观察和硬度测试等。
通过ISO 1143金属材料旋转弯曲疲劳试验方法的应用,我们可以评估金属材料在循环载荷下的耐久性能,并为设计和生产过程提供相关数据参考。
这可以帮助我们选择合适的材料,预测材料的使用寿命,优化产品设计,以及改进相关工艺和制造过程。
齿轮用渗碳钢弯曲疲劳试验浅析
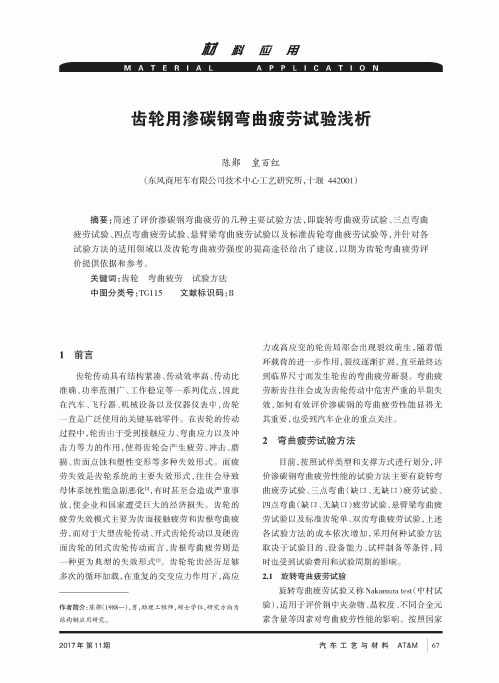
齿轮用渗碳钢弯曲疲劳试验浅析陈郧皇百红(东风商用车有限公司技术中心工艺研究所,十堰442001)摘要:简述了评价渗碳钢弯曲疲劳的几种主要试验方法,即旋转弯曲疲劳试验、三点弯曲 疲劳试验、四点弯曲疲劳试验、悬臂梁弯曲疲劳试验以及标准齿轮弯曲疲劳试验等,并针对各试验方法的适用领域以及齿轮弯曲疲劳强度的提高途径给出了建议,以期为齿轮弯曲疲劳评价提供依据和参考。
关键词:齿轮弯曲疲劳试验方法中图分类号:TG115 文献标识码:B^ ---1—1刖@齿轮传动具有结构紧凑、传动效率高、传动比 准确、功率范围广、工作稳定等一系列优点,因此 在汽车、飞行器、机械设备以及仪器仪表中,齿轮 一直是广泛使用的关键基础零件。
在齿轮的传动 过程中,轮齿由于受到接触应力、弯曲应力以及冲 击力等力的作用,使得齿轮会产生疲劳、冲击、磨 损、齿面点蚀和塑性变形等多种失效形式。
而疲 劳失效是齿轮系统的主要失效形式,往往会导致 母体系统性能急剧恶化有时甚至会造成严重事故,使企业和国家遭受巨大的经济损失。
齿轮的 疲劳失效模式主要为齿面接触疲劳和齿根弯曲疲 劳,而对于大型齿轮传动、开式齿轮传动以及硬齿 面齿轮的闭式齿轮传动而言,齿根弯曲疲劳则是 一种更为典型的失效形式+。
齿轮轮齿经历足够 多次的循环加载,在重复的交变应力作用下,高应作者简介:陈郧(1988—),男,助理工程师,硕士学位,研究方向为 结构钢应用研究。
力或高应变的轮齿局部会出现裂纹萌生,随着循 环载荷的进一步作用,裂纹逐渐扩展,直至最终达 到临界尺寸而发生轮齿的弯曲疲劳断裂。
弯曲疲 劳断齿往往会成为齿轮传动中危害严重的早期失 效,如何有效评价渗碳钢的弯曲疲劳性能显得尤其重要,也受到汽车企业的重点关注。
2弯曲疲劳试验方法目前,按照试样类型和支撑方式进行划分,评 价渗碳钢弯曲疲劳性能的试验方法主要有旋转弯 曲疲劳试验、三点弯曲(缺口、无缺口)疲劳试验、四点弯曲(缺口、无缺口)疲劳试验、悬臂梁弯曲疲 劳试验以及标准齿轮单、双齿弯曲疲劳试验,上述 各试验方法的成本依次增加,采用何种试验方法 取决于试验目的、设备能力、试样制备等条件,同时也受到试验费用和试验周期的影响。
疲劳试验标准

疲劳试验标准疲劳试验是指在特定载荷或应力作用下,材料或构件在一定条件下进行循环加载,以模拟实际工作中的疲劳破坏情况,从而评定材料或构件的疲劳性能。
疲劳试验标准是对疲劳试验进行规范和标准化的要求,其制定的目的是为了保证试验结果的准确性和可比性,为材料和构件的设计、生产和使用提供依据。
一、疲劳试验标准的分类。
根据不同的试验对象和试验目的,疲劳试验标准可以分为金属材料疲劳试验标准、混凝土疲劳试验标准、复合材料疲劳试验标准等。
其中,金属材料疲劳试验标准是最为常见和重要的一类,其主要包括拉伸-压缩疲劳试验、弯曲疲劳试验、扭转疲劳试验等内容。
二、疲劳试验标准的要求。
1. 试验条件的确定,包括载荷类型、频率、试样尺寸、环境条件等。
2. 试验方法的规范,包括试验过程的控制、数据采集和处理方法等。
3. 试验结果的评定,包括疲劳寿命、疲劳极限、疲劳裂纹扩展速率等指标的评定方法。
4. 试验设备和仪器的要求,包括试验机、应变计、测力传感器等设备的选用和校准要求。
5. 试验报告的内容,包括试验目的、试验方法、试验结果和分析等内容的详细记录。
三、疲劳试验标准的意义。
疲劳试验标准的制定和执行对于材料和构件的设计、生产和使用具有重要意义。
首先,它可以评定材料的疲劳性能,为材料的选用提供依据;其次,它可以评定构件的耐久性能,为构件的设计和改进提供依据;最后,它可以评定材料和构件在特定工况下的寿命,为工程结构的安全评定提供依据。
四、疲劳试验标准的发展趋势。
随着材料科学和试验技术的不断发展,疲劳试验标准也在不断更新和完善。
未来,疲劳试验标准将更加注重多尺度、多尺寸、多工况的综合试验方法,更加注重试验数据的数字化、标准化和信息化管理,以适应材料和构件疲劳性能评定的新需求。
总之,疲劳试验标准是对疲劳试验进行规范和标准化的要求,其制定的目的是为了保证试验结果的准确性和可比性,为材料和构件的设计、生产和使用提供依据。
随着材料科学和试验技术的不断发展,疲劳试验标准也在不断更新和完善,以适应新的需求和挑战。
铸件疲劳 标准
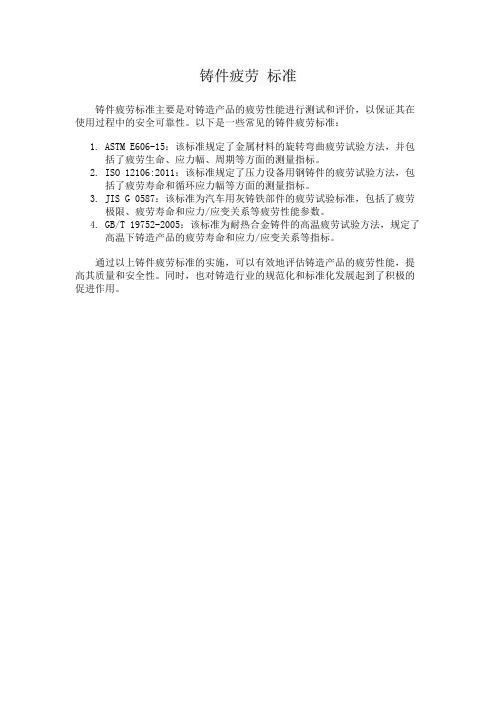
铸件疲劳标准
铸件疲劳标准主要是对铸造产品的疲劳性能进行测试和评价,以保证其在使用过程中的安全可靠性。
以下是一些常见的铸件疲劳标准:
1.ASTM E606-15:该标准规定了金属材料的旋转弯曲疲劳试验方法,并包
括了疲劳生命、应力幅、周期等方面的测量指标。
2.ISO 12106:2011:该标准规定了压力设备用钢铸件的疲劳试验方法,包
括了疲劳寿命和循环应力幅等方面的测量指标。
3.JIS G 0587:该标准为汽车用灰铸铁部件的疲劳试验标准,包括了疲劳
极限、疲劳寿命和应力/应变关系等疲劳性能参数。
4.GB/T 19752-2005:该标准为耐热合金铸件的高温疲劳试验方法,规定了
高温下铸造产品的疲劳寿命和应力/应变关系等指标。
通过以上铸件疲劳标准的实施,可以有效地评估铸造产品的疲劳性能,提高其质量和安全性。
同时,也对铸造行业的规范化和标准化发展起到了积极的促进作用。
金属材料的疲劳极限标准

金属材料的疲劳极限标准1. 引言1.1 疲劳极限的定义疲劳极限是指金属材料在受到交变应力作用下所能承受的疲劳载荷的极限值。
疲劳极限与金属材料的抗疲劳性能密切相关,是评价金属材料抗疲劳性能的重要指标之一。
疲劳极限通常用应力水平表示,即在特定的应力幅值下,金属材料经过一定次数的循环载荷后出现裂纹和破坏的应力值。
疲劳极限是金属材料在实际工程中使用时需要考虑的重要参数,对于确保金属部件在长期使用过程中不会因为疲劳破坏而影响工作安全具有重要意义。
疲劳极限的测定需要进行大量的实验研究和数据分析,以确保结果的准确性和可靠性。
金属材料的疲劳极限还受到多种因素的影响,如材料的化学成分、热处理工艺、表面处理等,需要综合考虑这些因素才能准确评估金属材料的疲劳性能。
1.2 金属材料的疲劳极限金属材料的疲劳极限是指在连续循环加载下,金属材料所能承受的最大变形次数或载荷幅度。
对于金属材料来说,疲劳极限是一项至关重要的性能指标,它直接影响着材料在实际工程中的可靠性和安全性。
金属材料的疲劳极限可以通过实验测试来确定,通常采用旋转弯曲、拉伸、扭转等不同加载方式进行试验。
通过对金属材料进行疲劳测试,可以得到不同载荷条件下的疲劳曲线,从而确定材料的疲劳性能和疲劳寿命。
金属材料的疲劳极限受多种因素影响,包括材料的化学成分、晶粒结构、微观缺陷等。
对于不同类型的金属材料,其疲劳极限标准也有所不同,因此在工程设计和材料选择过程中,需要根据具体的应用要求来确定合适的金属材料及其疲劳极限要求。
疲劳极限的重要性在于可以帮助工程师评估材料的使用寿命和安全性,从而设计出更加可靠和耐久的工程结构。
研究金属材料的疲劳极限标准对于提高材料的抗疲劳性能和延长材料的使用寿命具有重要意义。
2. 正文2.1 金属材料的疲劳损伤金属材料在受到循环载荷作用时,会产生疲劳损伤。
这种损伤是由于金属内部的微观缺陷在受力的作用下逐渐扩展,最终导致材料的破坏。
疲劳损伤的形式主要有裂纹的扩展和表面损伤两种。
金属材料疲劳试验旋转弯曲方法

金属材料疲劳试验旋转弯曲方法金属材料疲劳试验旋转弯曲方法是一种常用的疲劳试验方法,旨在评估金属材料在不同应力水平下的疲劳寿命和破坏机理。
本文将介绍旋转弯曲试验的原理、实验装置、实验步骤和一些应注意的问题。
旋转弯曲试验的原理是通过在金属试样上施加交变弯曲载荷,使其产生疲劳破坏。
与拉伸、压缩等加载方式相比,弯曲加载更接近实际工作条件下的应力状态,因此旋转弯曲试验更加符合实际应用。
通过控制试样的几何尺寸和加载条件,可以得到金属材料在一定应力水平下的疲劳寿命和疲劳曲线。
实验装置的主要组成部分包括试样夹持装置、负载装置和数据采集系统。
试样夹持装置通常采用夹具或夹具+滚动装置的方式,以确保试样在加载过程中不产生滑动。
负载装置通过电机驱动试样产生旋转弯曲载荷,可利用电机的控制系统调节载荷大小和频率。
数据采集系统用来记录试验过程中的试样应变和载荷变化,以便后续分析。
旋转弯曲试验的实验步骤如下:1.准备试样:根据实验要求,根据标准规范或自定义设计制作试样。
试样的几何形状和尺寸要符合实验要求,通常为长条形或圆柱形。
2.安装试样:将试样固定在试样夹持装置中,并确保试样的几何形状和尺寸不会发生变形或损坏。
3.设置实验参数:根据实验目的和要求,设置加载频率、载荷幅值和载荷比等参数,可以在实验中逐步增加载荷或设置不同的载荷比,以得到不同应力水平下的疲劳寿命和曲线。
4.开始实验:启动负载装置,使试样产生旋转弯曲载荷。
在实验过程中,连续记录试样的应变和载荷变化,并查看试样的破坏情况。
5.终止实验:当试样出现破坏或达到预设的实验次数时,停止负载装置,结束实验。
记录试样的破坏形态和位置,以便进一步分析。
在进行旋转弯曲试验时,还需要注意以下几个问题:1.试样的几何尺寸和材料特性应符合实验要求,避免试样在实验加载过程中出现松动、变形或损坏的情况。
2.实验过程中要及时记录试样的应变和载荷变化,以便后续分析。
可以使用应变计、力传感器等装置进行实时监测和数据采集。
- 1、下载文档前请自行甄别文档内容的完整性,平台不提供额外的编辑、内容补充、找答案等附加服务。
- 2、"仅部分预览"的文档,不可在线预览部分如存在完整性等问题,可反馈申请退款(可完整预览的文档不适用该条件!)。
- 3、如文档侵犯您的权益,请联系客服反馈,我们会尽快为您处理(人工客服工作时间:9:00-18:30)。
旋转弯曲疲劳标准
旋转弯曲疲劳标准是指在工程领域中,对于材料或结构在旋转弯曲
载荷下的疲劳性能进行评估和标准化的一种方法。
旋转弯曲疲劳是指
材料或结构在受到交替或周期性旋转弯曲载荷作用下,逐渐失去强度
和耐久性的现象。
这种疲劳现象在许多工程领域中都是非常重要的,
因为它可能导致材料或结构的失效和损坏。
旋转弯曲疲劳标准的制定是为了保证工程材料和结构在使用过程中
的可靠性和安全性。
通过对材料或结构在旋转弯曲载荷下的疲劳性能
进行评估,可以确定其使用寿命和安全边界,从而指导工程设计和材
料选择。
旋转弯曲疲劳标准的制定通常包括以下几个方面的内容:
首先是载荷的定义和描述。
旋转弯曲载荷是指材料或结构在旋转或
弯曲过程中所受到的力或力矩。
在制定疲劳标准时,需要明确载荷的
大小、方向和作用方式,以便进行准确的评估和比较。
其次是疲劳寿命的评估方法。
疲劳寿命是指材料或结构在旋转弯曲
载荷下能够承受的循环次数或时间。
评估疲劳寿命的方法通常包括实
验测试和数值模拟两种。
实验测试是通过对材料或结构进行循环加载,观察其失效情况来评估疲劳寿命。
数值模拟则是通过建立数学模型,
利用计算机仿真技术来预测材料或结构的疲劳寿命。
此外,还需要确定疲劳强度和安全系数。
疲劳强度是指材料或结构
在旋转弯曲载荷下能够承受的最大应力或应变。
安全系数是指在设计
和使用过程中,将实际载荷与疲劳强度之间的比值,用于保证材料或结构的安全性和可靠性。
确定疲劳强度和安全系数的方法通常是基于统计学和概率论的理论,结合实验数据和工程经验进行分析和计算。
最后,还需要制定相应的测试方法和评估标准。
测试方法是指对材料或结构进行实验测试的具体步骤和要求。
评估标准是指根据测试结果,对材料或结构的疲劳性能进行评估和分类的依据。
测试方法和评估标准的制定需要考虑到实际工程应用的需求和条件,以及相关国际和行业标准的要求。
总之,旋转弯曲疲劳标准的制定对于保证工程材料和结构的可靠性和安全性具有重要意义。
通过对材料或结构在旋转弯曲载荷下的疲劳性能进行评估和标准化,可以为工程设计和材料选择提供科学依据,从而提高工程的质量和可持续发展能力。