疲劳试验简介
金属疲劳试验方法

金属疲劳试验方法
金属疲劳试验是一种对金属材料进行疲劳性能评估的方法。
它可以用来测试材料在循环加载下的疲劳寿命以及疲劳行为。
常用的金属疲劳试验方法包括:
1. 疲劳弯曲试验:将金属试样固定在两个支撑点上,通过加载作用使其产生弯曲变形,并进行循环加载,记录试样的破坏次数或使用寿命。
2. 疲劳拉伸试验:将金属试样固定于试验机上,通过加载作用使其产生拉伸变形,并进行循环加载,记录试样的破坏次数或使用寿命。
3. 疲劳扭转试验:将金属试样固定在两个夹具上,通过加载作用使其产生扭转变形,并进行循环加载,记录试样的破坏次数或使用寿命。
4. 疲劳冲击试验:将金属试样固定在冲击机上,通过冲击作用使其产生变形,并进行循环冲击加载,记录试样的破坏次数或使用寿命。
这些试验方法可以通过变化加载幅值、加载频率、试样几何形状等参数的方式,来评估金属材料在不同加载条件下的疲劳性能。
重症肌无力疲劳试验标准

重症肌无力疲劳试验标准
重症肌无力(Myasthenia gravis,MG)疲劳试验是一种帮助诊断和评估MG疾病严重程度的常用方法。
下面是一些常见的重症肌无力疲劳试验标准:
1. 末梢肌疲劳试验(Peripheral Muscle Fatigability Test):通过检查患者的末梢肌肌力变化来评估肌无力。
这可以通过要求患者保持重复肌肉运动(如握力测试)或持续进行特定动作(如闭眼眼球运动)来完成。
在MG患者中,肌肉疲劳的程度更快、更显著。
2. 简单疲劳试验(Simple Fatigability Test):这个试验要求患者保持特定的肌肉活动一段时间,例如伸直手臂或举起双腿。
如果在持续活动后肌肉力量明显下降,则可能是MG症状。
3. 跳跃疲劳试验(Tensilon Test):这是一项常用的诊断肌无力的试验。
在试验中,将琼脂球碱(Tensilon)注射患者体内后观察症状变化。
如果肌无力症状显著改善,则可能是MG。
4. 静脉疲劳试验(Intravenous Fatigability Test):在这个试验中,患者经历一系列静脉注射及活动,以检测肌肉疲劳及其恢复情况。
需要注意的是,以上试验仅为常见的评估MG疲劳程度的方法之一,具体的试验方法和标准可能会根据个体情况和医生的判断而略有不同。
因此,在进行任何疲劳试验之前,请务必咨询医生以获得准确的诊断。
试验六疲劳试验示范

实验六疲劳试验(示范)一、实验目的1、了解测定材料疲劳极限的方法。
2、观察疲劳破坏的现象。
二、实验设备疲劳试验机有各种类型,用来在不同受力形式下和不同条件下进行试验。
常用的是旋转弯曲疲劳试验机,有纯弯曲和悬臂弯曲两种型式。
本试验采用纯弯曲式疲劳试验机,其构造示意图如图26(A)所示。
试件4的两端被夹紧在两个空心轴1中,两空心轴与试件构成一个整体杆,支持于两个滚珠轴承3上。
电动机5通过软轴6使这个整体杆转动。
横杆8挂在滚珠轴承2上,处于静止状态。
在横杆中央的砝码盘上放置砝码9,使试样中段受纯弯曲(图26—B),最大弯曲正应力为(A)纯弯曲疲劳试验机示意图(B)试件弯矩图图26 纯弯曲式疲劳试验机三、试件本实验需用一组8~13根材料和尺寸均相同的光滑小试件,直径为d=6~lOmm,表而须磨光,无锈蚀或伤痕,圆角处要光滑过度。
四、实验原理疲劳破坏与静力破坏有本质的不同。
当交变应力小于材料的静强度极限σb时,材料就可产生疲劳裂纹或完全断裂。
即使是塑性材料,断裂时也无显著的塑性变形。
在疲劳破坏的断口上,一般呈现两个区域,即光滑区和粗粒状区。
材料断裂前所经历的循环次数称为疲劳寿命N,试件所受应力愈小,则疲劳寿命愈长。
对钢和铸铁等黑色金属,如果在某一交变应力下经受107次循环仍不破坏,则实际上可以承受无限次循环而不会发生破坏。
所以,对这些金属以试件能承107循环所对应的最大应力σ值作为疲劳极限σ-1。
maX五、实验步骤1、试件准备取8~13根试件,检查试件表面加工质量,如有锈蚀或擦伤,用细砂纸或砂布沿试件轴向抛光加以消除。
测量试件的直径。
2、装夹试件安装试件时必须很仔细,避免灰尘和杂质进入空心轴的锥孔中。
将试件牢固夹紧,使试件与试验机的转轴保持良好的同心度。
试件安装好后用手慢慢旋转试验机的转轴,用百分表在试件上测得的径向跳动量应不大于0.03mm。
然后空载运转,试件的径向跳动量应不大于0.06mm。
3、进行试验第一根试件的交变应力的最大值约取材料强度极限的60%,即σlmax=0.6而砝码重量P1二0.6σbπd3/16a。
结构疲劳试验

• 1852-1869年德国人沃勒(A.Wöhler)为研究机车车 辆开始以15次/分的频1 率s对b 车辆部件进行拉钢伸疲劳 试疲劳验试,以验后机又进用行试旋样转以弯7s曲2s 次疲/分劳的试频验率,在他旋的转功弯绩曲是
指绘出成一应些力金与属循存环在周疲次劳极关限系,的并- 曲将s线疲r-持劳,久试极又验限 称结果为
起落架因飞机起落而 反复受载
2.疲劳试验的内容
研究性疲劳试验一般研究以下内容:
1. 应力随荷载重复次数变化情况; 2. 开裂荷载及开裂情况;
鉴定性疲劳试验
3. 裂缝的宽度、长度、间距及其随荷载重复次数的变化;
4. 最大绕度及其变化;
5. 疲劳极限;
6. 疲劳破坏特征。
疲劳破坏特征
破坏时应力低于sb (抗拉强度),甚至 ss(屈服强度) 即使是塑性材料,也呈现脆性断裂 断口通常呈现光滑与粗粒状两个区域
• 2)受压区混凝土破坏。这是一种脆性破坏,此时受拉主 筋处的最大裂缝宽度未达到1.5mm,且挠度小于跨度的 1/50。配筋过多或混凝土强度太低的梁,出现此种标志。
• 3)受拉主筋拉断。这是另一种更为危险的脆性破坏,它 发生于配筋过少或预应力过高的梁
6.疲劳试验的观测
1.疲劳强度
科研性试验是以疲劳极限强度和疲劳极限荷载作为最大的 疲劳承载能力。构件达到疲劳破坏时的荷载上限值和应力 最大值分别为疲劳极限荷载和疲劳极限强度。
为了得到给定疲劳应力比值(值)条件下的疲劳极限强度 和疲劳极限荷载,一般采取的办法是:
根据构件实际承载能力,取定最大应力值s max,作疲劳试验, 求得破坏时荷载作用次数n,从 s与mnax双对数直线关系中 求得控制疲劳次数下的疲劳极限强度,作为标准疲劳极限 强度。它的统计值作为设计验算时疲劳强度取值的基本依 据。
疲劳试验
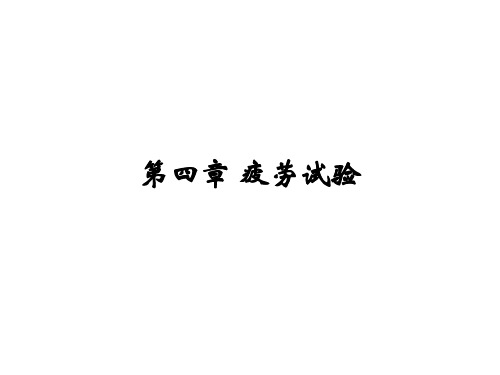
第一步 采用升降法测定条件疲劳极限, 第二步 用成组法测定σ一N曲线有限寿命段上各 点的数据, 第三步 绘制σ一N曲线。 二、不同应力状态下的疲劳极限 根据大量的实验结果,弯曲与拉压、扭转疲劳 极限之间的关系: 钢:σ-1p=0.85σ-1,铸铁σ-1p=0.65σ-1 铜及轻合金:τ-1=0.55σ-1,铸铁τ-1=0.8σ-1 σ-1>σ-1p>τ-1
(2)σmax~σm 图 y轴上的边界点为σ-1和 -σ-1,x轴则同前图。 σmax=σb ,利用不同的 应力比r来作图。若为韧性 材料σmax=σ0.2 (3)公式法 上两图中的曲线可用数学 公式表示 可以很方便利用 σb ,σ-1, σ0.2和r,求得σr。
第二节 疲劳抗力指标及其测定 一、疲劳极限的测定
一、变动载荷和循环应力
1、变动载荷 大小、方向或者大小和方向均随时间而变化。 变化分为周期性,无规则性。相对应的应力,称为循环 应力。 (P94-图5-1) 2、循环应力 (1)循环应力的特性 平均应力 σm=1/2(σmax+σmin) 应力幅 σa=1/2(σmax-σmin) 应力循环对称系数 γ=σmin/σmax (2)循环应力的种类(P95-图5-2) 对称;脉动;不对称循环应力。
第四节 低周疲劳与热疲劳
疲劳寿命为102-105次的疲劳断裂,称为低周 疲劳。
一、低周疲劳的特点
1、局部产生宏观变形,应力与应变之间呈非 线性。 总应变△εt=△εe+△εp
2、裂纹成核期短,有多个裂纹源。 3、断口呈韧窝状、轮胎花样状。 4、疲劳寿命取决于塑性应变幅。
二、金属的循环硬化与循环软化
(二)疲劳极限
1、对称疲劳极限 97 循环载荷,r=-1。 σ-1,τ-1,σ-1p(对称拉压)
疲劳试验

• 疲劳:结构物或构件在重复荷载作用下达 到破坏时的应力比其静力强度要低的多。 结构疲劳试验的目的就是要了解在重复荷 载作用下结构的性能和其变化规律。 • 为什么对结构构件 —— 特别是钢筋混凝土 构件的疲劳性能的研究比较重视?
一、疲劳试验项目
结构疲劳试验按试验目的的不同可分为研究性疲 劳试验和检验性疲劳试验两类。 研究性疲劳试验一般包括以下内容:开裂荷载和 开裂情况;裂缝的宽度、长度、间距及其随荷载 重复次数的变化;最大挠度及其变化;疲劳极限; 疲劳破坏特征。 检验性疲劳试验一般包括以下内容:抗裂性能; 开裂荷载、裂缝宽度及开展情况;最大挠度的变 化情况。
(2)疲劳试验的应变测量 动态或静动态应变仪测量。 裂缝测量:裂缝的开始出现和微裂缝的宽度很重要。 目前利用光学仪器或应变传感器电测。
(3)疲劳试验的挠度测量
(4)疲劳试验的安装 疲劳试验需要连续进行时间很长,振动荷载很大,试件安装及试验过程中需 要充分注意安全措施。 (1)试件安装时,严格对中,保证平稳,尽可能不用分配梁,如需多点加载 可用多个脉冲千斤顶。要在砂浆找平层的强度足够时才能做试验。 (2)试验过程中,要经常巡视,发现隐患,立刻排除。 (3)注意安全防护,设置支架等保护措施。
二、疲劳试验荷载
(一)疲劳试验荷载取值: 疲劳试验的上限荷载Qmax是根据构件在最大标准 荷载最不利组合下产生的弯矩计算而得,荷载下限 根据疲劳试验设备的要求而定。
(二)疲劳试验荷载速度 荷载频率不应使构件和荷载架发生共振,同时 应使构件在试验时与实际工作时的受力状态一致, 为此荷载频率与构件固有频率应满足一定条件:
【思 考 题】
1.列举几个建筑工程中需要考虑振动问题的方面? 2.结构动载试验主要包括哪三类情况? 3.测振系统由哪几部分组成?画出仪器组成框图, 并说明各部分的作用?什么是压电效应? 4.动载试验中产生动荷载的方法有哪几种? 5.何为结构的动力反应与动力特性?它们有何区别? 6.结构动力特性试验测定方法有哪三种?简述共振 法的测定原理? 7.光线示波器的工作原理?
车轮疲劳试验
车轮疲劳试验简介车轮疲劳试验是一种通过模拟车辆长时间运行状态下的负载情况,评估车轮在使用过程中的耐久性能和寿命的试验方法。
通过该试验可以确定车轮的安全性和可靠性,为车辆设计和制造提供重要参考依据。
试验目的车轮是汽车重要的组成部分之一,其承受着来自路面、悬挂系统等多方面的力量。
长时间运行后,车轮可能出现疲劳裂纹、变形等问题,严重影响行驶安全。
因此,进行车轮疲劳试验旨在评估和验证车轮在长时间使用中的耐久性能和寿命。
试验流程1.准备工作:确定试验样品、选择适当的试验设备和仪器。
2.载荷设定:根据实际使用情况、道路条件等因素,确定合适的载荷大小和类型。
3.车速设定:根据实际使用情况、道路条件等因素,确定合适的车速范围。
4.试验开始:将样品安装到试验设备上,并设置载荷和车速参数。
5.试验监测:使用传感器和监测设备对试验过程中的载荷、变形、温度等进行实时监测和记录。
6.试验终止:根据实际需求,确定试验的终止条件,如达到一定的试验时间或者出现破坏等情况。
7.结果分析:对试验结果进行数据处理和分析,评估车轮的耐久性能和寿命。
试验参数1.载荷:根据实际使用情况和设计要求,确定合适的载荷大小。
常用的载荷类型包括静态载荷、动态载荷和复合载荷等。
2.车速:根据实际使用情况和设计要求,确定合适的车速范围。
常用的车速范围为0-120公里/小时。
3.试验时间:根据实际需求确定试验时间,通常为数小时至数十小时不等。
试验设备1.车轮疲劳试验机:用于模拟车辆在长时间运行状态下对车轮施加各种负载,并记录相关数据。
常见的设备有旋转式疲劳试验机、振动式疲劳试验机等。
2.数据采集系统:用于实时监测和记录试验过程中的载荷、变形、温度等数据。
常见的设备有传感器、数据采集卡等。
试验结果分析1.车轮疲劳寿命:根据试验结果,通过统计分析和可靠性评估等方法,确定车轮的疲劳寿命。
2.车轮变形:通过试验结果中的变形数据,评估车轮在长时间使用中可能出现的变形情况。
拉伸疲劳试验
拉伸疲劳试验的原理、方法和应用一、什么是拉伸疲劳试验拉伸疲劳试验是一种材料力学试验,用于测定材料或结构件在交变拉伸载荷作用下的疲劳性能。
疲劳是指材料或结构件在应力远低于材料的屈服强度或断裂强度的若干个循环下发生的突然断裂现象。
疲劳是导致许多机械零部件失效的主要原因之一,因此,了解和评估材料的疲劳性能对于保证机械设备的安全和可靠运行具有重要意义。
拉伸疲劳试验通常分为高周疲劳试验和低周疲劳试验两种。
高周疲劳试验是指在较高的循环频率(一般为10~1000 Hz)下进行的拉伸疲劳试验,主要用于测定材料的高周疲劳强度和有限寿命疲劳强度。
低周疲劳试验是指在较低的循环频率(一般为0.01~10 Hz)下进行的拉伸疲劳试验,主要用于测定材料的低周疲劳强度和塑性应变能力。
二、拉伸疲劳试验的原理拉伸疲劳试验的基本原理是在规定的循环应力或应变条件下,对试样进行反复加载,直到试样发生断裂或达到预定的循环次数为止。
在试验过程中,记录并分析试样的应力-应变曲线、应力-循环次数曲线、应变-循环次数曲线等数据,以得到材料的疲劳特性值。
拉伸疲劳试验中常用的参数有以下几个:应力比(R):指最小应力与最大应力之比,即R=σmin/σmax。
应力比反映了循环载荷的对称性,当R=0时,表示循环载荷为完全正向(拉-拉);当R=-1时,表示循环载荷为完全反向(拉-压);当R介于0和-1之间时,表示循环载荷为交变(拉-压)。
应力幅(Δσ):指最大应力与最小应力之差的一半,即Δσ=(σmax-σmin)/2。
应力幅反映了循环载荷的大小,一般认为,应力幅越大,材料越容易发生疲劳。
平均应力(σm):指最大应力与最小应力之和的一半,即σm=(σmax+σmin)/2。
平均应力反映了循环载荷的偏心程度,一般认为,平均应力越大,材料越容易发生疲劳。
应变比(εr):指最小应变与最大应变之比,即εr=εmin/εmax。
应变比与应力比类似,也反映了循环载荷的对称性。
疲劳试验简介
疲劳试验(fatigue test)利用金属试样或模拟机件在各种环境下,经受交变载荷循环作用而测定其疲劳性能判据,并研究其断裂过程的试验,即为金属疲劳试验。
1829年德国人阿尔贝特为解决矿山卷扬机服役过程中钢索经常发生突然断裂,首先以10次/分的频率进行疲劳试验。
1852~1869年德国人沃勒hler)为研究机车车辆,开始以15次/分的频率对车辆部件进行拉伸疲劳试验,以后又用试样以72次/分的频率在旋转弯曲疲劳试验机进行旋转弯曲疲劳试验,他的功绩是指出一些金属存在疲劳极限,并将疲劳试验结果绘成应力与循环周次关系的S-N曲线(图1),又称为W hler曲线。
1849年英国人古德曼首先考虑了平均应力不为零时非对称载荷下的疲劳问题,并提出耐久图,为金属制件的寿命估算和安全可靠服役奠定理论基础。
1946年德国人魏布尔对大量疲劳试验数据进行统计分析研究,提出对数疲劳寿命一般符合正态分布(高斯分布),阐明疲劳测试技术中应采用数理统计。
60年代初,从断裂力学观点分析金属疲劳问题,进一步扩大了疲劳研究内容。
近年来,由于电液伺服闭环控制疲劳试验机的出现以及近代无损检验技术、现代化仪器仪表等新技术的采用,促进了金属疲劳测试技术的发展。
今后应着重各种不同条件(特别是接近服役条件)下金属及其制件的疲劳测试技术的研究。
试验种类和判据金属疲劳试验种类很多,通常可分为高周疲劳、低周疲劳、热疲劳、冲击疲劳、腐蚀疲劳、接触疲劳、声致疲劳、真空疲劳、高温疲劳、常温疲劳、低温疲劳、旋转弯曲疲劳、平面弯曲疲劳、轴向加载疲劳、扭转疲劳、复合应力疲劳等。
应根据金属制件的服役(工作)条件来选择适宜的疲劳试验方法,测试条件要尽量接近服役条件。
进行金属疲劳试验的目的在于测定金属的疲劳强度(抗力),由于试验条件不同,表征金属疲劳强度的判据(指标)也不一样。
高周疲劳:高周疲劳时,金属疲劳强度判据是疲劳极限 (或条件疲劳极限)即金属经受“无限”多次(或规定周次)应力循环而不断裂的最大应力,以σr表示,其中γ为应力比,即循环中最小与最大应力之比。
零部件疲劳试验
断裂力学试验
基于断裂力学原理,通过 控制裂纹扩展速率或测量 临界应力强度因子来评估 零部件的疲劳性能。
02
零部件疲劳试验方法
应力疲劳试验
总结词
通过在试样上施加交变应力来模拟实际工作状态,以检测试样在交变应力作用下 的疲劳性能。
详细描述
应力疲劳试验是在试样上施加交变应力,使试样在一定周期内反复承受拉伸和压 缩,以模拟实际工作状态。该试验方法适用于各种材料和零部件,如金属、塑料 、橡胶等,是评估材料和零部件疲劳性能的重要手段。
使用和维护建议
根据试验结果和失效分析,提出合 理的使用和维护建议,降低使用过 程中对零部件的损伤和失效风险。
06
零部件疲劳试验的应用与 发展趋势
应用领域
汽车工业
零部件疲劳试验在汽车工业中应用广泛,主要用 于测试发动机、传动系统、悬挂系统等关键部件 的疲劳性能,以确保车辆的安全性和可靠性。
轨道交通
03
零部件疲劳试验设备与材 料
试验设备
疲劳试验机
用于施加循环载荷,模 拟零部件在实际使用中
的受力情况。
数据采集系统
用于实时监测和记录试 验过程中的应变、位移
等数据。
环境箱
用于模拟不同温度、湿度等 环境条件,以评估零部件在
不同环境下的疲劳性能。
振动台
用于模拟实际使用中的 振动情况,加速疲劳裂
纹的萌生和扩展。
应力分析
分析试验过程中零部件所承受的应力分布和变化情况,评估应力 对疲劳寿命的影响。
损伤累积
评估零部件在循环载荷下的损伤累积情况,分析损伤累积与疲劳 失效的关系。
失效分析
失效模式
分析试验中观察到的失效模式,如裂纹、断裂、磨损等,了解失效 的具体表现形式。
- 1、下载文档前请自行甄别文档内容的完整性,平台不提供额外的编辑、内容补充、找答案等附加服务。
- 2、"仅部分预览"的文档,不可在线预览部分如存在完整性等问题,可反馈申请退款(可完整预览的文档不适用该条件!)。
- 3、如文档侵犯您的权益,请联系客服反馈,我们会尽快为您处理(人工客服工作时间:9:00-18:30)。
疲劳试验(fatigue test)利用金属试样或模拟机件在各种环境下,经受交变载荷循环作用而测定其疲劳性能判据,并研究其断裂过程的试验,即为金属疲劳试验。
1829年德国人阿尔贝特(J.Albert)为解决矿山卷扬机服役过程中钢索经常发生突然断裂,首先以10次/分的频率进行疲劳试验。
1852~1869年德国人沃勒(A.W hler)为研究机车车辆,开始以15次/分的频率对车辆部件进行拉伸疲劳试验,以后又用试样以72次/分的频率在旋转弯曲疲劳试验机进行旋转弯曲疲劳试验,他的功绩是指出一些金属存在疲劳极限,并将疲劳试验结果绘成应力与循环周次关系的S-N曲线(图1),又称为W hler曲线。
1849年英国人古德曼(J.Goodman)首先考虑了平均应力不为零时非对称载荷下的疲劳问题,并提出耐久图,为金属制件的寿命估算和安全可靠服役奠定理论基础。
1946年德国人魏布尔(W.Weibull)对大量疲劳试验数据进行统计分析研究,提出对数疲劳寿命一般符合正态分布(高斯分布),阐明疲劳测试技术中应采用数理统计。
60年代初,从断裂力学观点分析金属疲劳问题,进一步扩大了疲劳研究内容。
近年来,由于电液伺服闭环控制疲劳试验机的出现以及近代无损检验技术、现代化仪器仪表等新技术的采用,促进了金属疲劳测试技术的发展。
今后应着重各种不同条件(特别是接近服役条件)下金属及其制件的疲劳测试技术的研究。
试验种类和判据
金属疲劳试验种类很多,通常可分为高周疲劳、低周疲劳、热疲劳、冲击疲劳、腐蚀疲劳、接触疲劳、声致疲劳、真空疲劳、高温疲劳、常温疲劳、低温疲劳、旋转弯曲疲劳、平面弯曲疲劳、轴向加载疲劳、扭转疲劳、复合应力疲劳等。
应根据金属制件的服役(工作)条件来选择适宜的疲劳试验方法,测试条件要尽量接近服役条件。
进行金属疲劳试验的目的在于测定金属的疲劳强度(抗力),由于试验条件不同,表征金属疲劳强度的判据(指标)也不一样。
高周疲劳:高周疲劳时,金属疲劳强度判据是疲劳极限(或条件疲劳极限)即金属经受“无限”多次(或规定周次)应力循环而不断裂的最大应力,以σr表示,其中γ为应力比,即循环中
最小与最大应力之比。
在对称循环应力下γ=-1,疲劳极限表示为σ-1。
工程金属材料的疲劳极限与抗拉强度σb成正比,比值约为0.5,对疲劳试验时选取第一个循环应力具有参考价值。
金属疲劳试验时,应力随时间一般呈正弦波形变化(图2),但有时也采用三角形、矩形等应力波形。
金属疲劳试验时最广泛采用的是旋转弯曲疲劳试验和轴向加载疲劳试验。
循环应力类型见图2。
金属在疲劳极限下实际所通过的最大循环次数称为试验基数。
钢铁及钛合金等,基数一般为107;对于有色金属、特殊钢及在高温、腐蚀等试验条件下,基数一般为108。
一些金属存在疲劳极限,对应地在S-N曲线上出现水平部分。
一些金属不存在疲劳极限,其S-N曲线无水平部分;随循环周次增加,金属所能承受的应力不断减小,因此将对应于规定周次的应力称为条件疲劳极限。
金属疲劳极限一般根据10个以上相同试样的疲劳试验结果所绘制的S-N曲线求得,或用升降法求得。
金属疲劳强度是一种对金属外在缺陷、内在缺陷、显微组织和环境条件非常敏感的性能,通过疲劳试验所测定的试验数据一般都很分散,即S-N曲线通常都是一个带,由此求出的疲劳极限乃是一组试样的统计平均值。
不对称循环应力疲劳:在不对称循环应力下,一般采用在规定耐久期下表示极限循环应力σ与平均应力σm的耐久图(图3),表示疲劳试验结果。
低周疲劳:对于高应力大应变下的低周疲劳(周次一般为102~105),通常是进行恒应变控制低周疲劳试验。
应首先将试验结果绘成低周疲劳寿命曲线(图4),然后从相关直线的截距和斜率求得下列表征金属低周疲劳性能的判据:疲劳强度系数σ媕、疲劳塑性系数ε媕、
疲劳强度指数b、疲劳塑性指数c。
循环应变硬化指数n’、循环强度系数k’等判据可从循环应力-应变曲线求得。
影响疲劳试验的因素:金属疲劳试验结果受很多因素影响,如试验条件(试样的尺寸、形状和表面状态,试验机类型,载荷特征,频率、温度及介质等)、冶金因素(晶粒度、显微组织、冶金缺陷等)、操作技术(试样安装情况、加载同心度等)。
为了保证金属疲劳试验结果的可靠性和可比性,必须设法避免上述各种因素的影响,严格控制疲劳测试相关条件的一致性。
此外,残余应力也是影响疲劳强度的一个重要因素,一般是残余压应力有利,残余拉应力有害。
为了减小残余应力对疲劳试验结果的影响,样坯应经适当热处理外,疲劳试样的机械切削加工应采用多段、分级、逐步减小加工量的方法,精加工时以横磨削、纵抛光为宜。
疲劳断口:金属疲劳裂纹通常在表面层应力集中处(滑移带、夹杂、析出微粒、划痕、缺口、冶金缺陷等)萌生、而后扩展至断裂。
金属疲劳断裂表面的外观形貌称之为疲劳断口。
一般分为三区:即疲劳源(萌生疲劳裂纹的核心策源地);疲劳裂纹扩展区(扩展过程中留下呈同心弧线的贝壳状形貌,光亮平滑,颗粒细有时呈瓷状);终断区(剩余截面不足以支承峰值应力因过载荷而静断,呈暗灰色纤维状或晶粒状)。
在电子显微镜或光学显微镜高倍放大下,在金属疲劳扩展区可显示出垂直裂纹扩展方向而大致平行的疲劳条痕,每根条痕标志每一循环终了疲劳裂纹的位置,因此条痕间距可作为局部疲劳裂纹扩展率的度量。