聚晶金刚石涂层的元素含量
金刚石聚晶的堆积密度

金刚石聚晶的堆积密度1.引言1.1 概述金刚石聚晶的堆积密度是指在固定容器或结构中,金刚石颗粒的紧密程度。
金刚石作为一种重要的宝石和工业材料,其堆积密度对于其性能和应用具有重要的影响。
金刚石是一种由碳元素组成的矿物,拥有优异的物理和化学性质。
它具有极高的硬度和强度,是目前已知的最坚硬的物质之一。
由于其硬度和耐磨性,金刚石被广泛应用于宝石加工、石油钻探、切割工具等领域。
金刚石聚晶是指将金刚石颗粒通过特定的工艺方法进行堆积和固结而形成的一种材料。
聚晶的过程中,金刚石颗粒之间通过化学键或物理键相互吸附和结合,形成了一个坚固的结构。
聚晶可以增加金刚石的密度和坚固性,使其更具实用性。
金刚石聚晶的堆积密度受多种因素的影响。
其中,金刚石颗粒的形状和大小、颗粒间的间隙大小以及聚晶工艺等因素都会对堆积密度产生影响。
较为紧密的堆积密度可以提高金刚石材料的坚固性和耐磨性,使其在工业领域中的应用更加广泛。
金刚石聚晶的堆积密度在各个领域都具有重要的应用价值。
在宝石加工中,通过增加金刚石的堆积密度,可以提高宝石的光泽和折射率,使其更具观赏价值。
而在工业领域,金刚石聚晶的堆积密度可以增加切削工具的锋利度和使用寿命,提高生产效率。
总之,金刚石聚晶的堆积密度是金刚石材料重要的性质之一,对于其性能和应用具有重要意义。
进一步研究金刚石聚晶堆积密度的影响因素和应用价值,将有助于推动金刚石材料的发展和应用。
1.2 文章结构文章结构部分的内容可以写成:本文主要分为三个部分:引言、正文和结论。
在引言部分,我们将概述金刚石聚晶的堆积密度的重要性以及研究的目的。
首先,我们将介绍金刚石的特性,特别是与其堆积密度相关的特性。
然后,我们将解释聚晶的概念,并概述其在金刚石领域中的应用。
通过这些介绍,读者将对金刚石聚晶的堆积密度有一个初步的了解。
在正文部分,我们将更详细地介绍金刚石的特性,包括其物理和化学特性。
我们将讨论金刚石晶体的结构和形成过程,并探讨它们在堆积过程中的堆积方式和影响因素。
pcd是什么材料

pcd是什么材料PCD是多晶金刚石(Polycrystalline Diamond)的缩写,是一种由金刚石微粉和金属结合剂通过高温高压烧结而成的超硬材料。
PCD具有极高的硬度、耐磨性和热导性,因而被广泛应用于刀具、磨具、车削刀具、铣刀、钻头等领域。
PCD材料是由金刚石微粉和金属结合剂混合而成的,经过高温高压烧结而成的一种超硬材料。
金刚石微粉作为主要成分,赋予了PCD极高的硬度和耐磨性,而金属结合剂则起到了固化和连接金刚石微粉的作用。
PCD的硬度仅次于天然金刚石,但相对于单晶金刚石而言,PCD更具有韧性和耐磨性,因此在实际应用中更加耐用和稳定。
PCD材料的硬度主要来源于其中的金刚石微粉,金刚石是自然界中最坚硬的物质之一,其摩氏硬度高达10级,是其他材料无法比拟的。
而PCD材料中的金刚石微粉经过高温高压烧结后,其硬度更是得到了进一步的提升,使得PCD具有了出色的耐磨性和切削性能。
因此,PCD被广泛应用于刀具、磨具等领域,用于加工各类硬质材料。
除了硬度和耐磨性之外,PCD材料还具有优异的热导性能。
金刚石是一种优良的热导体,因此PCD材料具有良好的散热性能,可以有效减少加工过程中的热量积聚,提高刀具的使用寿命和加工质量。
这使得PCD材料在高速切削和高效加工领域有着广泛的应用前景。
在实际应用中,PCD材料已经成为了现代制造业中不可或缺的材料之一。
其在航空航天、汽车制造、机械加工等领域都有着重要的应用价值。
例如,PCD刀具可以用于加工铝合金、铜合金、纤维增强复合材料等难加工材料,具有较高的切削效率和表面质量。
此外,PCD磨具也被广泛应用于精密磨削、超精密加工等领域,为工件加工提供了高效、精确的加工解决方案。
总的来说,PCD是一种具有极高硬度、耐磨性和热导性的超硬材料,其在现代制造业中有着广泛的应用前景。
随着制造技术的不断进步和创新,PCD材料在未来将会有更加广阔的发展空间,为工业制造领域带来更多的创新和突破。
聚晶金刚石

聚晶金刚石(PCD)刀具的开发与应用1 引言高速切削已成为现代制造技术的一个主要发展方向。
由于高速切削刀具的开发与应用直接影响高速切削的加工效率和加工质量,因此具有非常重要的意义。
刀具技术的革新,除了刀具本身的几何形状、切削角度等的革新和改进外,刀具切削刃材质的开发和革新也是提高切削效率、降低切削成本的一个关键因素。
20世纪70年代中期以来,美国、德国、日本等工业发达国家先后开发聚晶金刚石(PCD)刀具并将其用于非金属材料和有色金属材料的高速切削加工,使生产效率获得大幅度提高,切削费用成倍下降,因此被广泛应用于汽车、航空、航天以建材等工业领域。
2 PCD复合片的开发聚晶金刚石(PCD)复合片是由粒度为微米级的金刚石颗粒与Co、Ni 等金属粉末均匀混合后,在高压高温下,在碳化钨(WC)基材上烧结而成的一种刀坯新材料。
PCD 复合片不仅具有金刚石高硬度、高耐磨性、高导热性、低摩擦系数、低热膨胀系数等优越性能,同时还具有硬质合金良好的强度和韧性。
PCD 复合片还具有导电性,因此可用线切割机切割成所需刀头,将刀头焊接在刀体上,经过刃表1公司名称国别牌号金刚石平均粒径(%26micro;m)GE 美国Compax-1600Compax-1300Compax-1500Compax-17005102540Element six (原De Beers) 英国Syndite-CTC002Syndite-CTB002Synd ite-CTB010Syndite-CTB025Syndite-CTH02522102525住友电工日本DA-200DA-150DA-100DA-900.5520+0.550日本韩国CFCMCC21025东名日本TDC-FMTDC-98F2MTDC-GMTDC-SMTDC-HMTDC-SATDC-EpMTDC-EM113710162036+16磨制成PCD 刀具。
目前国内外已有不少PCD 复合片的生产企业,主要生产厂商及产品牌号见表1。
PCD﹑PCBN刀具材料及刀具涂层
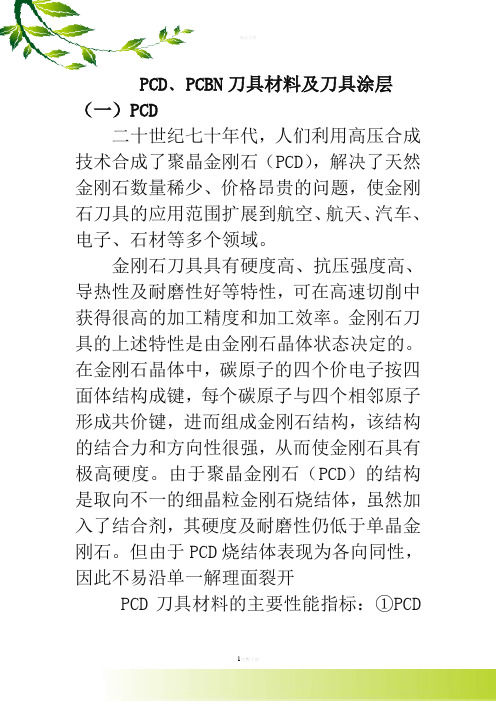
PCD﹑PCBN刀具材料及刀具涂层(一)PCD二十世纪七十年代,人们利用高压合成技术合成了聚晶金刚石(PCD),解决了天然金刚石数量稀少、价格昂贵的问题,使金刚石刀具的应用范围扩展到航空、航天、汽车、电子、石材等多个领域。
金刚石刀具具有硬度高、抗压强度高、导热性及耐磨性好等特性,可在高速切削中获得很高的加工精度和加工效率。
金刚石刀具的上述特性是由金刚石晶体状态决定的。
在金刚石晶体中,碳原子的四个价电子按四面体结构成键,每个碳原子与四个相邻原子形成共价键,进而组成金刚石结构,该结构的结合力和方向性很强,从而使金刚石具有极高硬度。
由于聚晶金刚石(PCD)的结构是取向不一的细晶粒金刚石烧结体,虽然加入了结合剂,其硬度及耐磨性仍低于单晶金刚石。
但由于PCD烧结体表现为各向同性,因此不易沿单一解理面裂开PCD刀具材料的主要性能指标:①PCD的硬度可达8000HV,为硬质合金的80~120倍;②PCD的导热系数为700W/mK,为硬质合金的1.5~9倍,甚至高于PCBN和铜,因此PCD刀具热量传递迅速;③PCD的摩擦系数一般仅为0.1~0.3(硬质合金的摩擦系数为0.4~1),因此PCD刀具可显著减小切削力;④PCD的热膨胀系数仅为0.9×10 -6~1.18×10 -6,仅相当于硬质合金的1/5,因此PCD刀具热变形小,加工精度高;⑤PCD 刀具与有色金属和非金属材料间的亲和力很小,在加工过程中切屑不易粘结在刀尖上形成积屑瘤。
PCD刀具的应用: 工业发达国家对PCD刀具的研究开展较早,其应用已比较成熟。
自1953年在瑞典首次合成人造金刚石以来,对PCD刀具切削性能的研究获得了大量成果,PCD刀具的应用范围及使用量迅速扩大。
目前,国际上著名的人造金刚石复合片生产商主要有英国De Beers公司、美国GE公司、日本住友电工株式会社等。
据报道,1995年一季度仅日本的PCD刀具产量即达10.7万把。
图层金刚石

三、涂层金刚石的发展研究现状
(2)硬质合金基体中的Co具有催石墨化的作用;
(3)金刚石与WC-Co硬质合金热膨胀系数不匹配导致 涂层内存在较大的残余应力。
选择合适的厚度是金刚石涂层刀具合理性价比的关键。
CVD金刚石薄膜太薄,磨损快,刀具使用寿命不高; CVD金刚石薄膜太厚,与硬质合金基体的粘附性变差 且制造成本增加。
但材料添加了硬质耐磨 颗粒作为强化剂,这无 疑增加了这些材料加工 难度,这些硬质颗粒会 造成刀具过早磨损产生 大量切削热。
一、涂层金刚石刀具出现的历史背景
因此,多数刀具用户认为, 普通刀具已经不能满足需 求,而迫切需要一种耐磨 性更高、能稳定实现高精、 高效、寿命更长的超硬刀 具。
金刚石涂层刀具因其具有 十分接近天然金刚石的硬 度和耐磨性、高的弹性模 量、极高的热导率、良好 的自润滑性和化学稳定性 等优异性能,成为加工难 加工材料的理想刀具。
三、涂层金刚石的发展研究现状
典型的硬质合金表面预处理方法主要有:
(1)除去或钝化刀具表面层的粘结相Co; (2)施加过渡层; (3)机械处理等。 在实际应用中,为了更好地提高金刚石薄膜与硬质合 金基体的结合强度,往往同时综合采用多种表面预处 理方法。
广东工业大学匡同春等人发表了《CVD金刚石涂层硬质
石的热膨胀系数最为接近,因此一直被认为是CVD金 刚石涂层较为理想的基体材料。 缺点:由于Si3N4陶瓷本身脆性大,抗冲击性能差,一
二、涂层金刚石刀具的含义及其组成
般认为,Si3N4基金
刚石涂层刀具仅宜 用于精加工,而不 宜进行冲击切削加工。
(2) WC系硬质合金
二、涂层金刚石刀具的含义及其组成
四、涂层金刚石刀具的发展前景展望
聚晶金刚石

主要用于研磨,一般配制成研磨液来使用。
也有可能制作刀具,切割时不容易产生崩裂。
谢谢观看
微粉粒度图
聚晶金刚石微粉粒度图D50值也就是中值粒径(Median)
优点
优异的磨削性能:高去除率和韧性,具有自锐性; 与单晶金刚石比较起来,更不容易产生表面划伤; 更适合用来研磨表面由不同硬度材料构成的工件。
应用领域
作为精密磨料,用于蓝宝石、磁头、硬盘、硬质玻璃和晶体、陶瓷以及硬质合金的超精密研磨和抛光,如用 于LED蓝宝石的减薄。
聚晶金刚石
利用独特的定向爆破法由石墨制得的金刚石
01 基本介绍
04 应用领域
聚晶金刚石(PCD)(微粉)是利用独特的定向爆破法由石墨制得,高爆速炸药定向爆破的冲击波使金属飞片 加速飞行,撞击石墨片从而导致石墨转化为聚晶金刚石。
基本介绍
其结构与天然的金刚石极为相似,通过不饱和键结合而成,具有很好的韧性。 制作工艺 聚晶金刚石
金刚石的成分
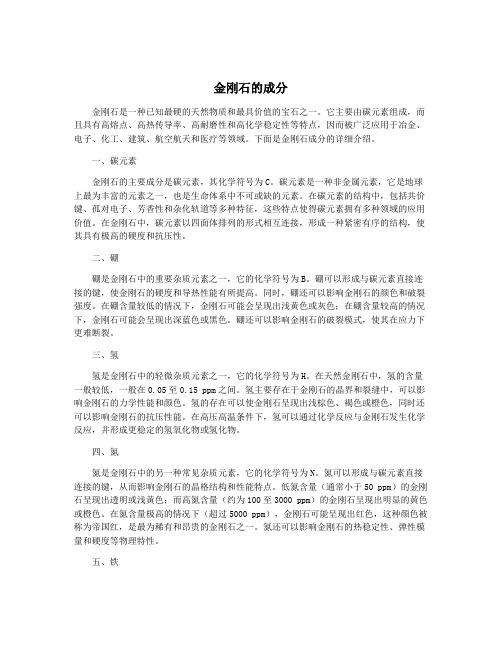
金刚石的成分金刚石是一种已知最硬的天然物质和最具价值的宝石之一。
它主要由碳元素组成,而且具有高熔点、高热传导率、高耐磨性和高化学稳定性等特点,因而被广泛应用于冶金、电子、化工、建筑、航空航天和医疗等领域。
下面是金刚石成分的详细介绍。
一、碳元素金刚石的主要成分是碳元素,其化学符号为C。
碳元素是一种非金属元素,它是地球上最为丰富的元素之一,也是生命体系中不可或缺的元素。
在碳元素的结构中,包括共价键、孤对电子、芳香性和杂化轨道等多种特征,这些特点使得碳元素拥有多种领域的应用价值。
在金刚石中,碳元素以四面体排列的形式相互连接,形成一种紧密有序的结构,使其具有极高的硬度和抗压性。
二、硼硼是金刚石中的重要杂质元素之一,它的化学符号为B。
硼可以形成与碳元素直接连接的键,使金刚石的硬度和导热性能有所提高。
同时,硼还可以影响金刚石的颜色和破裂强度。
在硼含量较低的情况下,金刚石可能会呈现出浅黄色或灰色;在硼含量较高的情况下,金刚石可能会呈现出深蓝色或黑色。
硼还可以影响金刚石的破裂模式,使其在应力下更难断裂。
三、氢氢是金刚石中的轻微杂质元素之一,它的化学符号为H。
在天然金刚石中,氢的含量一般较低,一般在0.05至0.15 ppm之间。
氢主要存在于金刚石的晶界和裂缝中,可以影响金刚石的力学性能和颜色。
氢的存在可以使金刚石呈现出浅棕色、褐色或橙色,同时还可以影响金刚石的抗压性能。
在高压高温条件下,氢可以通过化学反应与金刚石发生化学反应,并形成更稳定的氢氧化物或氢化物。
四、氮氮是金刚石中的另一种常见杂质元素,它的化学符号为N。
氮可以形成与碳元素直接连接的键,从而影响金刚石的晶格结构和性能特点。
低氮含量(通常小于50 ppm)的金刚石呈现出透明或浅黄色;而高氮含量(约为100至3000 ppm)的金刚石呈现出明显的黄色或橙色。
在氮含量极高的情况下(超过5000 ppm),金刚石可能呈现出红色,这种颜色被称为帝国红,是最为稀有和昂贵的金刚石之一。
拉丝模具的几种常见材质概述

拉丝模具的几种常见材质概述经历了几十年的发展,已出现了很多新型拉丝模材质。
按照材料种类,可将拉丝模分为合金钢模、硬质合金模、天然金刚石模、聚晶金刚石模、CVD金刚石模和陶瓷模等多种。
近年来新型材料的开发极大的丰富了拉丝模具的应用范围并提高了拉丝模的使用寿命。
(1)合金钢模是早期的拉丝模制造材料。
用来制造合金钢模的材料主要是碳素工具钢和合金工具钢。
但是由于合金钢模的硬度和耐磨性差、寿命短,不能适应现代生产的需要,所以合金钢模很快被淘汰,在目前的生产加工中已几乎看不到合金钢模。
(2)硬质合金模由硬质合金制成。
硬质合金属于钨钴类合金,其主要成分是碳化钨和钴。
碳化钨是合金的“骨架”,主要起坚硬耐磨作用;钴是粘结金属,是合金韧性的来源。
因此,硬质合金模与合金钢模相比具有以下特性:耐磨性高、抛光性好、粘附性小、摩擦系数小、能量消耗低、抗蚀性能高,这些特性使得硬质合金拉丝模具有广泛的加工适应性,成为当今应用最多的拉丝模模具。
(3)天然金刚石是碳的同素异性体,用它制作的模具具有硬度高、耐磨性好等特点。
但天然金刚石的脆性较大,较难加工,一般用于制造直径1.2mm以下的拉丝模。
此外,天然金刚石价格昂贵,货源紧缺,因此天然金刚石模并不是人们最终所寻求的即经济又实用的拉丝工具。
(4)聚晶金刚石是用经过认真挑选的质量优良的人造金刚石单晶体加上少量硅、钛等结合剂,在高温高压的条件下聚合而成。
聚晶金刚石的硬度很高,并有很好的耐磨性,与其它材料相比它具有自己独特的优点:由于天然金刚石的各向异性,在拉丝过程中,当整个孔的周围都处在工作状态下时,天然金刚石在孔的某一位置将发生择优磨损;而聚晶金刚石属于多晶体、具有各向同性的特点,从而避免了模孔磨损不均匀和模孔不圆的现象发生。
与硬质合金相比,聚晶金刚石的抗拉强度仅为常用硬质合金的70%,但比硬质合金硬250%,这样,使得聚晶金刚石模比硬质合金模有更多的优点。
用聚晶金刚石制成的拉丝模耐磨性能好,内孔磨损均匀,抗冲击能力强,拉丝效率高,而且价格比天然金刚石便宜许多。
- 1、下载文档前请自行甄别文档内容的完整性,平台不提供额外的编辑、内容补充、找答案等附加服务。
- 2、"仅部分预览"的文档,不可在线预览部分如存在完整性等问题,可反馈申请退款(可完整预览的文档不适用该条件!)。
- 3、如文档侵犯您的权益,请联系客服反馈,我们会尽快为您处理(人工客服工作时间:9:00-18:30)。
聚晶金刚石涂层的元素含量
聚晶金刚石涂层是一种具有高硬度、高耐磨性和高耐腐蚀性的表面涂层材料,广泛应用于刀具、模具、机械零件等领域。
其优异的性能主要归功于其特殊的元素含量。
本文将从聚晶金刚石涂层的元素含量入手,探讨其特点和应用。
一、碳元素
聚晶金刚石涂层主要由碳元素构成。
碳元素是构成金刚石晶格的主要元素,具有极高的硬度和热稳定性。
在涂层制备过程中,通过热解石墨等方法,将碳元素沉积在基体表面,形成金刚石晶体。
这些金刚石晶体之间通过共价键相互连接,使得涂层具有极高的硬度和耐磨性。
二、金属元素
聚晶金刚石涂层中通常还含有金属元素。
金属元素的添加可以改善涂层的性能,并调节涂层的组织结构和性能。
常见的金属元素包括钛、铬、铝、钼等。
这些金属元素可以与碳元素形成合金化合物,增强涂层的硬度和耐磨性。
此外,金属元素还可以提高涂层的抗腐蚀性能和热稳定性,使其能够在恶劣环境下长时间工作。
三、氮元素
氮元素是聚晶金刚石涂层中的重要添加元素之一。
氮元素可以与碳元素形成碳氮键,增加涂层的硬度和耐磨性。
此外,氮元素还可以
提高涂层的热稳定性和抗氧化性能,使其能够在高温环境下长时间使用。
另外,氮元素还可以调节涂层的晶格结构,使其具有更好的机械性能和导热性能。
四、硅元素
硅元素是聚晶金刚石涂层中的重要添加元素之一。
硅元素可以与碳元素形成硅碳键,增加涂层的硬度和耐磨性。
此外,硅元素还可以提高涂层的抗腐蚀性能和热稳定性,使其能够在恶劣环境下长时间工作。
另外,硅元素还可以调节涂层的晶格结构,使其具有更好的机械性能和导热性能。
五、其他元素
除了上述几种主要元素外,聚晶金刚石涂层中还可能含有其他元素,如氧、氢、氩等。
这些元素的添加可以改善涂层的性能和结构,使其具有更好的机械性能、导热性能和抗腐蚀性能。
总结:
聚晶金刚石涂层的元素含量对其性能具有重要影响。
碳元素是构成金刚石晶格的主要元素,金属元素的添加可以改善涂层的性能,氮元素和硅元素可以增加涂层的硬度和耐磨性。
此外,其他元素的添加也可以改善涂层的性能和结构。
在实际应用中,根据不同的需求可以调节聚晶金刚石涂层的元素含量,以获得最佳的性能和效果。
聚晶金刚石涂层的元素含量研究仍在不断深入,相信将来会有更多
的元素被应用于聚晶金刚石涂层中,为各个领域的应用提供更好的解决方案。