聚晶金刚石高速研磨实验研究
聚晶金刚石的精密镜面磨削
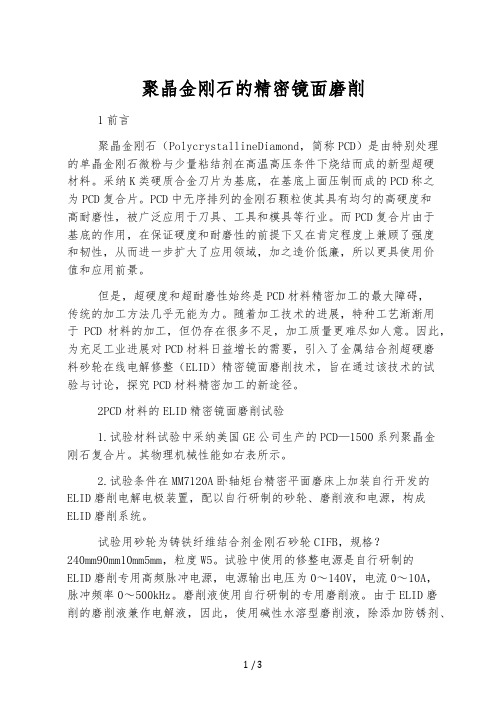
聚晶金刚石的精密镜面磨削1前言聚晶金刚石(PolycrystallineDiamond,简称PCD)是由特别处理的单晶金刚石微粉与少量粘结剂在高温高压条件下烧结而成的新型超硬材料。
采纳K类硬质合金刀片为基底,在基底上面压制而成的PCD称之为PCD复合片。
PCD中无序排列的金刚石颗粒使其具有均匀的高硬度和高耐磨性,被广泛应用于刀具、工具和模具等行业。
而PCD复合片由于基底的作用,在保证硬度和耐磨性的前提下又在肯定程度上兼顾了强度和韧性,从而进一步扩大了应用领域,加之造价低廉,所以更具使用价值和应用前景。
但是,超硬度和超耐磨性始终是PCD材料精密加工的最大障碍,传统的加工方法几乎无能为力。
随着加工技术的进展,特种工艺渐渐用于PCD材料的加工,但仍存在很多不足,加工质量更难尽如人意。
因此,为充足工业进展对PCD材料日益增长的需要,引入了金属结合剂超硬磨料砂轮在线电解修整(ELID)精密镜面磨削技术,旨在通过该技术的试验与讨论,探究PCD材料精密加工的新途径。
2PCD材料的ELID精密镜面磨削试验1.试验材料试验中采纳美国GE公司生产的PCD—1500系列聚晶金刚石复合片。
其物理机械性能如右表所示。
2.试验条件在MM7120A卧轴矩台精密平面磨床上加装自行开发的ELID磨削电解电极装置,配以自行研制的砂轮、磨削液和电源,构成ELID磨削系统。
试验用砂轮为铸铁纤维结合剂金刚石砂轮CIFB,规格?240mm90mm10mm5mm,粒度W5。
试验中使用的修整电源是自行研制的ELID磨削专用高频脉冲电源,电源输出电压为0~140V,电流0~10A,脉冲频率0~500kHz。
磨削液使用自行研制的专用磨削液。
由于ELID磨削的磨削液兼作电解液,因此,使用碱性水溶型磨削液,除添加防锈剂、钝化剂、极压添加剂和合成润滑剂外,尚需肯定数量的无机盐,以使磨削液具有电解本领。
3.试验过程应用ELID磨削装置对PCD复合片进行磨削试验时,首先对砂轮进行电火花精密整形,除去砂轮的圆度和圆柱度误差,使微细磨料尽可能等高地分布在砂轮表面上。
聚晶金刚石的精密镜面磨削

会发生抗刀现象。加工过程也证明了计算结果的可靠
性
5 结论
本文从 理论 上给 出了利 用飞刀 径 向进 给粗 加工 右
4 计算实例
一
旋蜗轮时飞刀左右侧 刃工作后角的计算方法 , 分析 并 讨论 了其影响因素的影 响规律 , 这些工作对于保 证蜗 轮齿面的加工质量 , 防止加工 中可能 出现的加工抗刀
周 曙光 关佳亮
徐 中耀
( 大连理 工 大学) 摘 要: 聚晶 金刚石 是一种应 用广 泛 的超 硬材料 . 密加 工极其 困难 。文章 介绍 了 E I 精 LD精密 镜面磨 削技 术 对聚 晶金 刚石 复合 片进 行的精密 磨削 实验 . 并对磨 削过程 和去 除机理 进行 了分析 。 关键 词 : 晶金 刚石 聚 超硬 材料 在线 电解 修 整( D 精 密镜 面磨削 ⅡJ ) 硬度 和耐磨 性的前 提下 又在 一定程 度上兼 顾 了强度 和 韧性 , 从而进 一步扩 大 了应 用领 域 , 之 造 价 低廉 , 加 所 以更具 使用价 值 和应用前 景 。 但 是 , 硬度 和超 耐磨 性 始终 是 P D材 料 精 密加 超 C 工 的最 大障碍 , 统 的加 工 方 法 几 乎无 能 为 力 。随着 传 加工 技 术 的 发 展 , 种 工 艺 逐 渐 用 于 P D 材 料 的 加 特 C 工, 但仍存 在许 多 不 足 , 工 质 量 更 难 尽 如 人 意 因 加 此, 为满 足工业 发 展对 P D材 料 日益 增 长 的 需 要 , C 引
模具等行业 。而 P D复台片由于基底的作用 , C 在保证
践 证 明, 口 ≥2、 ≥2且 。 ≤1。fe ≤1。 当 … 。口… 。 … 8、 ' T一 8 时, 不会发 生 飞刀 的切削加工抗 刀 和崩 刃现象 , 而且 飞
合成时间和温度对金刚石聚晶硬度和磨耗比影响的研究_王中

WANG Zhong
(Department of Management Engineering,Hunan Urban Construction College,Xiangtan 411103,China)
Abstract The polycrystalline diamond(PCD)was prepared with particle size of 5 μm diamond fine powder as raw materials and Co as adhesive by the cubic diamond press under different synthetic time and temperature. The microhardness and abrasion ratio were measured. The results show that the abrasion ratio and Vickers hardness of PCD first increase,then decrease with the increase of sintering time,and reach the maximum at the sintering time for 180 s. The abrasion ratio and Vickers hardness of PCD also increase at first,then decrease with the increase of sintering temperature,and reach the maximum at the sintering temperature of 1 550 ℃ . When sintering temperature is too low,the diamond grain becomes sharp ⁃ featured with big grain clearance,and when the sintering temperature is too high,the grain will grow abnormally. The reason why PCD sample appears different microhardness and abrasion ratio was analyzed by microstructure observation. Key words PCD;synthetic time;synthetic temperature;abrasion ratio
聚晶金刚石最佳磨削速度的试验研究

o t m r d n p e g u ig g id n CD i hc h o e t o ta d hg e t ce c a l e ra i d p mu g i ig s e d m e d r r ig P w ih t e lw s s n ih ret i y e r b e l e . i n n n n c q n z Ke wo d : oy rs U n imo d, d a n r d n h e , y r s p lcy t ie d a n a imo d g i i g w e l n
o n ̄nigsrc f C tem cai as gteepr et eusi aa T .R sac sl d a a t r i t d f eo D,h ehn scui xe m n r l n l ̄ n ua P c n h i st s y e rhr ut i i t t th e s: e e s n c e h e 1 1 1
材 料 的高 硬 度 、 高耐 磨 性 也 给其 加 工带 来 了 困难 , 目 前通 常 采 用 金 刚 石 砂 轮 磨 削 工 艺 加 工 P D 材 料 。 C
聚晶金刚石加工技术
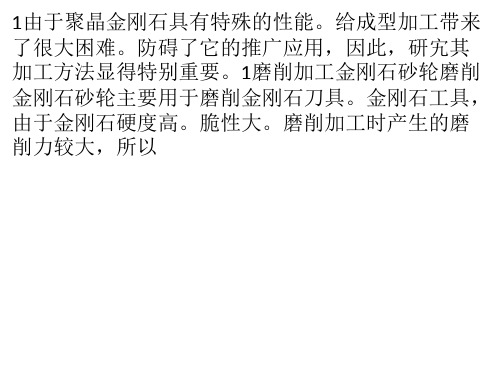
fahxs8e 超细用双电极分别 接正极和负极,磨轮旋转并以定压力从双电极的接 触面上擦过。使磨轮面敷上层金属粉,形成导电层。 与双电极之间产生接触式放电。从而电蚀结合剂。 使磨轮金刚石颗粒裸露突出。达到修锐的目的。经 大量试验及对数据的
统计分析得到经验公式及=0.014;71+3!125,式中, 为修整金刚石平均突出量;为贷格电1;为电极每次 进洽的叻深1;3激光加工激光加工聚晶金刚石的机 理是束能量密度极高的激光束照射到聚晶金刚石面 上。部分光能即被面吸收并转化成热能,照射斑点
提高。减少了金刚石工具使用过程中磨粒脱落,提 高其使用寿命。另方面。金属化的金刚石面,具有 了可焊性和导电性,这使得金刚石工具的制造工艺 有了很大改进。导电性使得金刚石面可电镀;可焊 性使得金刚石面与低熔点合金有良好的焊接性。如 加工金刚石刀具常用钎
焊,最近国内又研制了激光焊。与钎焊相比。激光 焊热影响区小,可降低应力和减少基体变形。对金 刚石性能没有影响;结合强度高。刀头不易脱落; 焊缝为细小柱状晶,不易产生裂纹。保证了产品质 量。金刚石溶于熔融硝盐浴中。将00工件置于熔融 的硝盐浴中。在溶解
要是磨耗磨削和破碎磨削。但聚晶金刚石本身特性 磨削加工工艺等都是影响磨削加工机理的因素,2金 孺盘削如工用铸铁磨盘纯铁磨盘对聚晶金刚石进行 研磨。研磨压力速度时间都对磨削量有重要影响。 研磨过程中热化学反应起主要作用。机械磨损起辅 助作用。这种方法适
用于聚晶金刚石半精加工和精加工。设备简单。成 本较低。2电火花加工1电火花线切,聚晶金刚石大 多用来制作机加工刀具。地质钻头以及拉丝磨具。 形状复杂多变,用电火花线切割机床进行成型加工 是目前种经济可行的良好途径。聚晶金刚石是由金 刚石颗粒与金属粉末
聚合而成,放电加工时。由于金刚石本身不导电, 在脉冲电压的作用下,首先使靠近电极的金属处高 温使,00中的金属熔化,部分金刚石石墨化。部分 金刚石脱落。如此反复进行。直到加工完毕。可, 材料的电加工性主要取决于金刚石的粒度及导电金 属相的含量。金刚石
聚晶金刚石表面抛光技术研究

聚晶金刚石表面抛光技术讨论用传统的机械抛光法对大面积PCD制品抛光,磨轮会先接触其因应力变形而显现的凸起,造成抛光时间长、局部厚度减薄等弊端。
对此,设计并运用了双摇杆摇摆夹具,使抛光表面在抛光过程能与磨轮端面自适应接触,本文重要阐述这种新工艺装备的特点和使用效果。
一、绪论PCD制品自20世纪70时代问世以来,以其优良的性能,在航空航天、国防、能源、汽车、地质钻探和线缆等高技术领域中得到日益广泛的应用。
尤其是大面积PCD制品的应用,使机械加工本领和水平向前迈进一大步,加工精度、加工表面质量不断提高,加工效率几十倍甚至上百倍提高。
大面积PCD制品多用于制造切削各种材料的刀具,为了良好断屑,提高被加工工件的精度和表面质量,大多数PCD制品的PCD面需要抛光,使其达到镜面(表面粗糙度Ra≦0.05m)。
尽管很多资料介绍PCD面电化学抛光、超声抛光等新技术,但在工业化的批量生产应用中,PCD面机械抛光仍占主导地位。
二、PCD面抛光参数选择PCD面机械抛光过程是聚晶金刚石磨耗与炭化过程,由于聚晶金刚石的硬度高,一般用金刚石抛光粉(膏)加铸铁盘或用磨轮进行抛光。
实践证明:用金刚石抛光粉(膏)加铸铁盘抛光的效率太低,大都采纳磨轮抛光(磨轮与工件被抛光表面接触面积大,被广泛采纳)。
PCD面抛光质量要求:(1)表面粗糙度Ra≦0.05m;(2)表面光泽一致,没有折光面;(3)没有未抛光到的边缘存在;(4)无光泽不均匀的环;(5)无划痕及污染。
为达到PCD面抛光质量要求,用磨轮实施机械抛光时,要合理选择磨轮宽度、浓度和粒度,磨轮和工件转速,抛光压力以及磨轮修整时机。
首先磨轮的粒度和浓度要选择合适,粒度过粗达不到工件抛光表面粗糙度要求;粒度过细,加工效率低,磨粒保持锋利的时间短,抛光时的摩擦力大,温上升。
磨轮宽度要选择合适,过窄,使用寿命短,磨轮修整频次高,工件被抛光表面与磨轮接触面小,抛光效率低;过宽,磨轮端面难于整平,磨轮内外圈的线速度差异大,磨轮内外消耗差异多,抛光中摩擦接触面积大,工件散热条件变差;磨轮工作层中含金刚砂浓度高,有利于缩短磨轮与被抛光表面接触吻合时间,但成本高,会使磨轮脱粒过快,有时造成被抛光表面划伤。
聚晶金刚石复合片磨削试验研究

,
A s at T epeio uf egidn s npl rs ln im n o ps e P D)w r cn utdb s gd mod bt c h rc insr c r igt t o o cyt l ed odcm oi ( C r s a n es y ai a t ee od c yui i n e n a
文章 编 号 :06— 5 X(07)6— 0 1 O 10 8 2 20 0 0 3 一 3
聚 晶晖 安 磊 胡 中伟
( 湖南大学国家高效磨削工程技术研究 中心 , 沙 40 8 ) 长 10 2
摘
要
本文采用金刚石砂轮对聚晶金刚石 ( C ) P D 复合片材料进 行 了精 密平 面磨削试验 , 究 了磨 削工艺参 数和砂 轮 研
特性对磨削力 的影 响规律 , 分析 了磨 削 P D材料去除机理 。研究发现 : C 随着砂轮 速度的增大 , 向磨削力 和法 向磨 削力 切 不 断减小 ; 随着磨削深度 的增加 , 向磨削力和法 向磨削力都增 加 , 切 相同粒度 的陶瓷结 合剂砂 轮 的磨 削力大 于树脂结合 剂砂轮的磨削力 ; 向磨削力 和法 向磨 削力都 随着工件进 给速度 的增加而增 大 ; 度号越 大 , 向磨 削力和法 向磨削力 切 粒 切 越大 。P D材料去除主要是通过磨粒 的机械磨耗 、 C 破碎作 用和热物理 、 热化学作用等方式 。 关键词 聚晶金刚石 ; 刚石砂轮 ; 金 磨削力 ; 磨削机理
P e a r sv e r rg na in,t e a —p y i sa d t e a —c e c l r c s . CD a b a i e w a ,fa me tt r o h r l h sc n h r l h mia o e s m m p
毕业论文毕业设计聚晶金刚石合成工艺

摘要本文在高温高压条件下,以粒度为5μm的金刚石微粉为原材料,采用液相烧结法制备了聚晶金刚石拉丝模坯,分别研究了烧结温度和烧结时间对其微观结构以及力学性能的影响,最后探讨了PCD拉丝模坯材料的烧结过程和机理。
结果表明:聚晶金刚石拉丝模坯的力学性能(磨耗比、维氏硬度)均随着烧结时间的增大先增加后降低,在烧结时间为180s时达到最大,烧结时间过短,其微观组织孔隙较大,烧结时间过长,金刚石石墨化严重;而在以烧结温度为变量的对比实验中发现,聚晶金刚石拉丝模坯的力学性能随着烧结温度的增加先变大后减小,在烧结温度为1550℃时达到最大,烧结温度过低,金刚石晶粒棱角分明,晶粒间隙较大,而烧结温度过高,晶粒发生异常生长。
所以,在压力为5.7GPa,温度为1550℃,烧结时间180s的条件下进行液相烧结得到的聚晶金刚石的力学性能最佳。
关键词:高温高压;聚晶金刚石;微结构;力学性能ABSTRACTIn this paper, the polycrystalline diamond was sintered under high temperature and high pressure with the diamond powders (5um) using liquid sintering method, and the effects of the sintering temperature and sintering time to the microstructure and the properties of the polycrystalline diamond were studied. The results showed that the mechanical properties (abrasion ratio, Vickers hardness) of polycrystalline diamond wire drawing die materials increased with the increasing of sintering time and sintering temperature firstly, and then decreases, and the mechanical properties (abrasion ratio, Vickers hardness) reached its maximum when the sintering time was 180s and 1550℃respectively, and the pores were more larger when the sintering time is too short, and the diamond graphitization more serious when the sintering time is too long;The grain angular and the grains gap was large when the sintering temperature was too low, while abnormal grain growth could be occurred when the sintering temperature was too high, Therefore, the polycrystalline diamonds with the most outstanding performance were sintered under the conditions of sintering time 180s, the pressure 5.7GPa, the temperature 1550℃. Keywords:High pressure and high temperature; Polycrystalline diamond; Microstructures; Mechanical properties目录1 绪论 (1)1.1拉丝模概述 (1)1.2拉丝模分类及发展状况 (2)1.3拉丝模的孔型结构 (6)1.4拉丝模的破坏及磨损研究 (8)1.4.1拉丝模的破坏形式 (8)1.4.2拉丝模的磨损 (10)1.5聚晶金刚石拉丝模坯材料的发展及研究现状 (14)1.6研究目的及意义 (17)2 实验过程及测试方法 (18)2.1实验材料及设备·································· (18)2.2PCD拉丝模的制备过程 (19)2.3实验测试方法与分析 (21)2.3.1扫描电镜及能谱分析 (21)2.3.2维氏硬度 (21)2.3.3磨耗比 (22)3 PCD拉丝模芯的合成工艺研究 (24)3.1烧结时间对力学性能的影响 (24)3.1.1烧结时间对显微维氏硬度的影响 (24)3.1.2烧结时间对磨耗比的影响 (26)3.2烧结温度对力学性能的影响 (27)3.2.1烧结温度对显微维氏硬度的影响 (28)3.2.2烧结温度对磨耗比的影响 (30)3.3PCD拉丝模坯的显微形貌及能谱分析 (31)3.3.1烧结时间对显微形貌的影响 (31)3.3.2烧结温度对显微形貌的影响 (32)3.3.3PCD拉丝模坯的能谱分析 (33)4PCD拉丝模坯高压烧结过程及机理 (35)4.1PCD拉丝模坯的烧结过程 (35)4.2PCD拉丝模坯的烧结机理 (36)5结论··································· (39)参考文献 (40)致谢 (42)1绪论1.1拉丝模概述拉丝模是拉制各种金属线材的重要工具。
- 1、下载文档前请自行甄别文档内容的完整性,平台不提供额外的编辑、内容补充、找答案等附加服务。
- 2、"仅部分预览"的文档,不可在线预览部分如存在完整性等问题,可反馈申请退款(可完整预览的文档不适用该条件!)。
- 3、如文档侵犯您的权益,请联系客服反馈,我们会尽快为您处理(人工客服工作时间:9:00-18:30)。
聚晶金刚石高速研磨实验研究许立福;刘涛;黄树涛;周丽【摘要】In this paper, both cases of with cooling jacket or not are comparatively studied. High-speed lapping experiments on the machining of PCD using resin bond diamond grinding wheel have been carried out. The effect of the lapping time, linear velocity and load pressure on material removal rate and lapping surface quality of PCD were evaluated.%通过实验对比研究了采用冷却套冷却和不冷却两种情况下,使用树脂结合剂金刚石砂轮高速研磨聚晶金刚石片时,研磨时间、研磨速度和研磨压力等工艺参数对聚晶金刚石片材料去除率及表面质量的影响规律.【期刊名称】《制造技术与机床》【年(卷),期】2012(000)012【总页数】4页(P173-175,178)【关键词】聚晶金刚石;高速研磨;金刚石砂轮【作者】许立福;刘涛;黄树涛;周丽【作者单位】沈阳理工大学机械工程学院,辽宁沈阳110159;沈阳理工大学机械工程学院,辽宁沈阳110159;沈阳理工大学机械工程学院,辽宁沈阳110159;沈阳理工大学机械工程学院,辽宁沈阳110159【正文语种】中文【中图分类】TG506.1聚晶金刚石(Polycrystalline Diamond简称PCD)是20世纪70年代以来发展起来的一种新型材料。
具有接近天然金刚石的硬度、耐磨性、化学性能稳定以及与硬质合金相当的抗冲击性[1]。
在现代工业、国防和高新技术等领域得到日益广泛的应用[2],其中用于制造各种切削刀具是聚晶金刚石最具潜力的应用领域[3-5]。
这些应用都需要对PCD表面进行光整加工,而研磨是获得高质量PCD表面的加工方法之一。
传统的研磨分为干研和湿研,干研时,研磨区温度高,工件表面易产生硬度软化层;湿研时,冷却液直接作用在研磨区,对研磨表面产生侵蚀,不易获得镜面,而且研磨速度低,耗时长,效率低。
本文针对PCD研磨加工过程中存在的问题,自制了高速研磨实验台及冷却套夹具对其进行研磨和冷却,避免冷却液对研磨区的直接作用。
研究冷却和不冷却两种情况下,研磨工艺参数对PCD片材料去除率和研磨表面质量的影响,为进一步提高PCD的加工效率奠定了实验基础,对促进PCD的广泛应用具有重要意义。
1 实验条件(1)高速研磨实验台:自行研制的金刚石膜超高速研磨实验台,电主轴驱动,100~24 000 r/min无级变速,配有坚固的防护罩;砂轮为B型树脂结合剂金刚石,粒度325#,直径255 mm,最高转速5 000 r/min(研磨线速度57.57 m/s)。
(2)试样材料:φ13 mm×2 mm的PCD圆片,PCD层及硬质合金层厚度各1 mm。
(3)聚晶金刚石材料去除率的测量方法采用称重法,称重仪器:梅特勒-托利多AB104-L分析天平,可读性0.1 mg,最大称重110 g。
(4)表面粗糙度测量:TR200粗糙度仪。
2 实验方案由于初始PCD圆片的表面中心有凹陷,先在高精度平面磨床(MG7132)上使用粒度为100#的金刚石砂轮对其进行粗加工取平,粗加工后试样表面粗糙度为Ra0.13 μm左右。
为避免直接冷却时因急冷产生的较大热应力和冷却液直接接触研磨区对工件及砂轮的腐蚀,自制了冷却套式研磨夹具,套内通入循环水对PCD 片的冷却。
高速研磨及冷却原理如图1所示。
采用单因素实验法,研究冷却和不冷却两种情况下,研磨时间、研磨线速度和研磨压力对聚晶金刚石材料去除率及研磨表面质量的影响。
实验过程中,通过改变砂轮转速来改变研磨线速度,通过调整弹簧上方的压力调整螺钉来改变研磨压力,实验参数见表1。
表1 实验参数砂轮转速/(r/min)对应研磨线速度/(m/s)研磨压力/N研磨时间/min 3 000 34.54 31 3 3 500 40.3 37.5 5 4 000 46.05 44 10 4 500 51.81 50.5 5 000 57.57 57每组实验之前首先对砂轮进行修整,使其达到最佳研磨状态。
PCD片的材料去除量和表面粗糙度分别在研磨3 min、5 min时各测量一次,之后每隔10 min测量一次。
3 实验结果分析3.1 研磨时间对材料去除率及表面粗糙度的影响当研磨压力37.5 N,砂轮转速5 000 r/min时,材料去除率随时间的变化曲线如图2所示。
可以看出,不冷却时,研磨开始阶段材料的去除率较大,随后迅速下降,20 min左右时,材料去除率开始趋于平稳。
冷却时,材料去除率随时间的增加逐渐增大,增大趋势较平稳,20 min左右时,材料去除率达到最大值,然后有所下降,并在一定的时间范围内趋于平稳状态。
图3所示为表面粗糙度随时间的变化曲线,在冷却和不冷却两种情况下,表面粗糙度值均随着研磨时间的增加,先迅速减小,然后趋于平稳。
两者的主要区别在于研磨的前15 min左右,不冷却时的表面粗糙度减小趋势比冷却时大。
不冷却时,试件表面粗糙度在5 min左右就能达到镜面(Ra≤0.05 μm);冷却时,约在10 min左右能达到镜面(Ra≤0.05 μm)。
在研磨15 min之后,冷却情况下的表面粗糙度值小于不冷却的情况,且两者的变化趋势基本一致。
出现上述现象的原因主要是,研磨开始阶段砂轮比较锋利,而且不冷却时的研磨区温度较高,高温一方面有利于提高材料去除率,同时也会加速砂轮的磨损,故材料去除率在研磨开始后很短的时间内达到比较大的值,表面粗糙度值也减小较快,然后趋于平稳。
冷却情况下开始时比较锋利的砂轮使得材料去除率较高,表面粗糙度值也减小较快,随着砂轮进入正常磨削阶段,材料去除率及表面粗糙度值趋于稳定。
3.2 研磨速度对材料去除率及表面粗糙度的影响图4为材料去除率与研磨速度的关系曲线(研磨压力44 N,采样时间间隔10 min)。
可以看出,在冷却和不冷却两种情况下,材料去除率均随研磨速度的提高而增加,冷却时的增大幅度更明显。
当研磨线速度低于46.05 m/s(即砂轮转速低于4 000 r/min)时,不冷却时的材料去除率较高。
而当研磨线速度高于46.05m/s时,冷却时的材料去除率较高。
图5为表面粗糙度与研磨速度的关系曲线(研磨压力44 N,采样时间间隔10 min),在冷却和不冷却两种情况下,表面粗糙度值均随研磨线速度的提高而减小。
在研磨线速度为34.54 m/s(转速为3 000 r/min),不冷却时的表面粗糙度值减小趋势较快,随着研磨线速度的提高,冷却时的表面粗糙度值明显小于不冷却时的情况。
这主要是因为在研磨线速度较低时,不冷却时的研磨区温度较高,有利于材料去除,而且开始时砂轮比较锋利,故材料去除率较高,表面粗糙度值减小也较快。
随着研磨线速度的提高,研磨区温度进一步升高,高温在提高材料去除率的同时也加剧了砂轮的磨损,砂轮磨损对去除率的抑制作用减弱了研磨线速度提高对去除率的促进作用,随着研磨线速度的提高,材料去除率的增大趋势减小。
在冷却情况下,研磨线速度较低时,研磨区温度较低,材料去除率较小,表面粗糙度值减小较慢,但砂轮的磨损小,能长时间保持锋利状态,随着研磨线速度的提高,材料去除率明显增大,表面粗糙度值也明显小于不冷却的情况。
3.3研磨压力对材料去除率及表面粗糙度的影响图6所示为PCD材料去除率随研磨压力的变化曲线(砂轮转速5 000 r/min,采样时间间隔10 min)。
从图6可以看出,冷却和不冷却两种情况下,材料去除率均随着研磨压力的增大而增加。
冷却时的材料去除率随研磨压力的增大幅度比不冷却时大。
当研磨压力小于40 N时,不冷却时的材料去除率较高。
而当研磨压力大于40 N时,冷却情况下的材料去除率较高。
图7所示为表面粗糙度随研磨压力的变化曲线(砂轮转速5 000 r/min,采样时间间隔10 min)。
从图7可以看出,冷却和不冷却两种情况下,表面粗糙度值均随研磨压力的增大而减小。
在研磨压力为31 N时,不冷却时的表面粗糙度值减小较快。
当研磨压力大于31 N时,冷却情况下的表面粗糙度值明显较小。
出现上述情况的主要原因是当研磨压力较小时,不冷却时的研磨区温度较高,有利于材料去除,材料去除率较高,表面粗糙度值减小较快。
随着研磨压力的增加,研磨区的温度进一步升高,高温加速了砂轮的磨损,在一定程度上抑制了材料去除率的增大,也使得表面粗糙度值减小变慢。
冷却情况下研磨区的大部分热量被冷却液带走,研磨区的温度不会过高,砂轮磨损慢,能较长时间保持锋利状态。
当研磨压力较小时温度对材料去除率的影响较小,材料去除率较低,表面粗糙度值减小较慢,随着研磨压力的增加,其材料去除率明显提高,表面粗糙度值明显减小。
4 结语通过实验研究了采用金刚石砂轮研磨聚晶金刚石时,研磨时间、研磨速度、研磨压力对材料去除率和表面粗糙度影响,得到如下结论:(1)PCD片的材料去除率随着研磨时间增加是先增大,后趋于平稳,研磨一定时间后又有所下降;随着研磨线速度和研磨压力的增大而增大。
当研磨线速度和研磨压力较小时,冷却时的材料去除率比不冷却时小;当研磨线速度和研磨压力较大时,冷却时的材料去除率比不冷却时大。
(2)PCD片研磨表面的粗糙度值随着研磨时间的增加、研磨线速度和研磨压力的增大而减小。
在研磨初始阶段及研磨线速度和载荷压力较小时,不冷却时的表面粗糙度值减小较快,随着研磨时间的增加及研磨线速度和研磨压力增加,冷却时的表面粗糙度值减小较快。
(3)采用冷却套冷却时的表面粗糙度值明显小于不冷却时的情况,说明设计的冷却套装置有利于聚晶金刚石的高速研磨加工。
参考文献[1]李颖,龙旭辉.金刚石聚晶的性能[J].郑州工业学校学报,2001(4).[2]王光祖.聚晶金刚石(PCD)在工业中应用[J].超硬材料与工程,1996(3).[3]邓福铭,陈启武.PCD超硬复合刀具材料及其应用[M].北京:化学工业出版社,2003.[4]白清顺,姚英学.Gracezhang,等.聚晶金刚石加工刀具在中国的研究与发展[J].机械工程师,2001(11).[5]刘进,胡娟.金刚石聚晶的性能特征及应用[J].磨料磨具通讯,2006(8).。