电镀络合废水处理工艺流程
电镀废水处理过程详解及规范
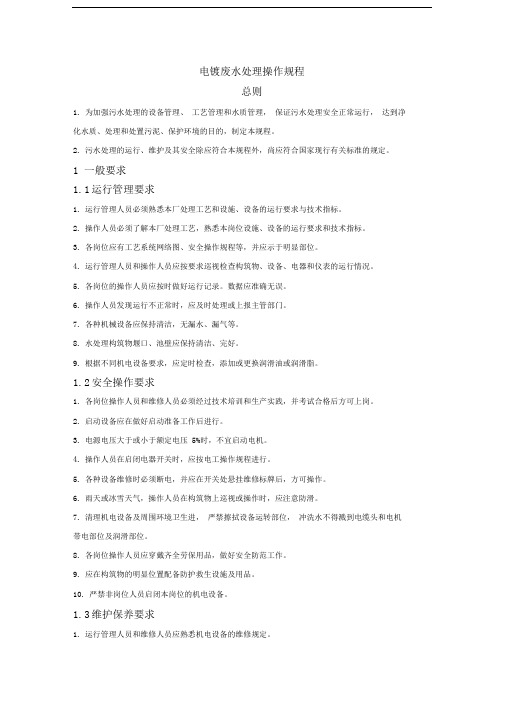
电镀废水处理操作规程总则1.为加强污水处理的设备管理、工艺管理和水质管理,保证污水处理安全正常运行,达到净化水质、处理和处置污泥、保护环境的目的,制定本规程。
2.污水处理的运行、维护及其安全除应符合本规程外,尚应符合国家现行有关标准的规定。
1 一般要求1.1运行管理要求1.运行管理人员必须熟悉本厂处理工艺和设施、设备的运行要求与技术指标。
2.操作人员必须了解本厂处理工艺,熟悉本岗位设施、设备的运行要求和技术指标。
3.各岗位应有工艺系统网络图、安全操作规程等,并应示于明显部位。
4.运行管理人员和操作人员应按要求巡视检查构筑物、设备、电器和仪表的运行情况。
5.各岗位的操作人员应按时做好运行记录。
数据应准确无误。
6.操作人员发现运行不正常时,应及时处理或上报主管部门。
7.各种机械设备应保持清洁,无漏水、漏气等。
8.水处理构筑物堰口、池壁应保持清洁、完好。
9.根据不同机电设备要求,应定时检查,添加或更换润滑油或润滑脂。
1.2安全操作要求1.各岗位操作人员和维修人员必须经过技术培训和生产实践,并考试合格后方可上岗。
2.启动设备应在做好启动准备工作后进行。
3.电源电压大于或小于额定电压5%时,不宜启动电机。
4.操作人员在启闭电器开关时,应按电工操作规程进行。
5.各种设备维修时必须断电,并应在开关处悬挂维修标牌后,方可操作。
6.雨天或冰雪天气,操作人员在构筑物上巡视或操作时,应注意防滑。
7.清理机电设备及周围环境卫生进,严禁擦拭设备运转部位,冲洗水不得溅到电缆头和电机带电部位及润滑部位。
8.各岗位操作人员应穿戴齐全劳保用品,做好安全防范工作。
9.应在构筑物的明显位置配备防护救生设施及用品。
10.严禁非岗位人员启闭本岗位的机电设备。
1.3维护保养要求1.运行管理人员和维修人员应熟悉机电设备的维修规定。
2.应对构筑物的结构及各种闸阀、护栏、爬梯、管道等定期进行检查、维修及防腐处理,并及时更换被损坏的照明设备。
3.应经常检查和紧固各种设备连接件,定期更换联轴器的易损件。
电镀废水处理工艺技术方案说明
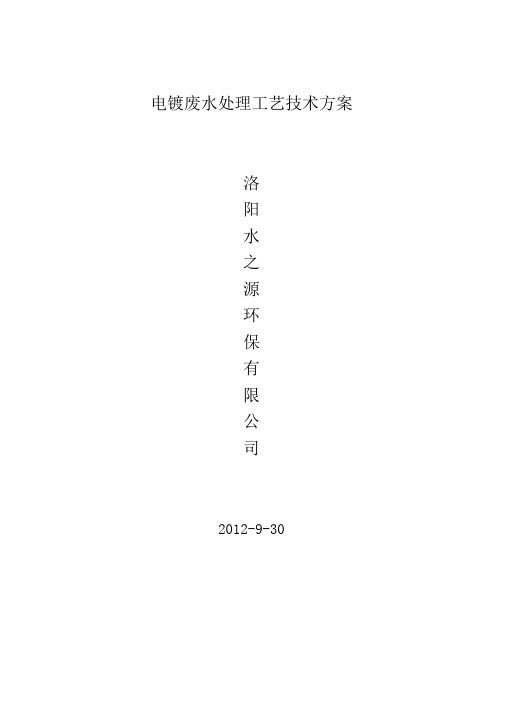
电镀废水处理工艺技术方案洛阳水之源环保有限公司2012-9-30项目提出甲方意将已处理后的电镀废水做深度处理,深度处理后的废水再利用,处理后的浓缩水回流到源水池再度提取水中的稀有金属。
由于原水水源中部分指标超标,不能达到饮用水标准,需进行处理,经调研特提出利用洛阳水之源环保有限公司提供的工艺技术和设备以求达到用水标准。
工艺技术方案一、设计思路在本着充分利用客户方原有设施和最大程度的节省投资,本着对客户负责、对我们自己负责的前提下,同时根据甲方提供水质报告、工艺技术及实际情况和要求特提出以下设计方案。
二、工艺方案及工艺流程由于原水水质中铁,硫酸盐,氯化物,镍等多项指标超标•工艺选择采用预处理加双膜工艺。
由于原水水质报告中铁,超标,这会对工艺中反渗透膜造成极大的不利,使得反渗透膜快速衰减,造成水通量下降和降低出水品质。
为防止此类问题的发生,我们预处理中增加了錳沙过滤装置及超滤装置,同时又有活性炭吸附装置。
超滤膜用于反渗透预处理时,运行压力0.1 —0.2MPa,可以使出水浊度小于0.2NTU,SDI小于3;可以100%勺去除水中残留滋生的细菌和近于100%胶体,尤其是胶体硅,在SDI小于1时超滤能去除水中所有的Fe、Al氧化物;能耗可减少30%以上。
最大程度上减少了对反渗透膜的危害,它还可以减少反渗透膜的清洗次数,降低维护费用,延长反渗透膜组件的使用寿命。
极大地降低了客户方的运行成本。
工艺方案技术参数:1、原水:已处理后的工业废水2、出水水质:GB5749-2006生活饮用水卫生标准3、产水量:10t/h 一套。
工艺流程【已处理的工业废水】-【废水收集池】-【提升泵】-【多介质过滤(反冲)】宀【碳滤装置】宀【微滤过滤】宀【精密过滤】f【超滤】f【投加阻垢剂及杀菌剂】f【中间水箱】T【保安过滤】T【高压泵】f【反渗透】f【净水池】f【用户】工艺配置设备报价本系统报价***万元.含税及设备厂房内的安装调试及产品水的第一次水质化验费用,不含运费•厂房面积不大于100平方米•工艺说明本工艺设计操作系统具有手动和自动两种操作方式,具有手动/ 自动切换功能;可实现无人值守功能,具有缺水自动断电停机保护功能;1.多介质过滤器的主要作用是吸附原水中的余氯、重金属、沉淀物等其他有害杂质,减小余氯;2.药剂投加主要使原水中的胶体原水中钙、镁离子部分减少形成沉积,破坏朗格利尔指数,同时使得水中超标的铁和锰形成沉积,减轻后置的工作负担,延长滤膜的使用寿命. 配置配有PE加药箱,搅拌泵,PSF进口计量泵等。
电镀废水AOMBR处理工艺详解

电镀废水A2/O-M B R处理工艺详解现代电镀网讯:常见的电镀废水处理工艺通常是采用传统化学处理法对不同种类的废水进行分类处理;从而达到回收重金属且使废水达标排放的目的〔1;2;3〕..然而;随着电镀污染物排放标准发布稿GB21900—2008的发布;N、P、COD等污染物的排放标准更加严格;仅仅采用传统化学处理并不能很好地达到排放标准的要求..MBR是一种新兴的污水处理工艺;具有处理效果好;占地面积省;抗冲击负荷能力强等诸多优点..将MBR用于工业污水的处理国内外近年来研究较多;并已经有了实际应用;实践证明采用化学处理结合MBR的新工艺处理工业污水效果很好〔4;5;6〕..某电镀工业园每天产生大量电镀废水;因其电镀产品种类较多;所产生的废水水质也较复杂..设计采用化学处理结合A2/O-MBR的新工艺对园区的络合废水及前处理废水进行处理;将传统化学处理作为生化段的预处理工艺;后接A2/O-MBR工艺以强化去除COD及脱氮除磷的效果..工程建成调试完成后经过几个月的连续监测表明;经过本工艺处理后的出水水质优良;且本工艺具备较强的抗冲击负荷能力..1废水水量及水质情况1.1设计进水水量及水质本工艺处理的对象为园区内车间排放的电镀前处理废水及络合废水;项目前期对车间排放废水进行水量调查及取样分析得到前处理废水设计水量为750m3/ d;设计进水水质:pH为4~8;水中所含污染物主要为COD、氨氮和总磷;分别为6 00、20、5mg/L;络合废水设计水量为250m3/d;设计进水水质:pH为6~8;所含污染物主要为COD、总铜、总镍、总锌、氨氮和总磷;分别为300、60~120、20、20~60、200、20mg/L..1.2生化系统进水水质要求上述两类废水显然都达不到生化进水要求;必须经过各自的预处理后方能进入A2/O-MBR系统..因此设计首先采用传统工艺对废水进行分类预处理;经过预处理的生化进水所要求的水质指标如下:COD300mg/L左右;氨氮30~35mg/L;总磷3~6mg/L;SS不超过50mg/L;总铜、总镍、总锌均低于0.5mg/L..1.3设计出水水质设计出水水质以电镀污染物排放标准发布稿GB21900—2008规定的表2的排放标准为依据;具体指标如表1所示..2处理工艺2.1工艺选择MBR反应器具有处理效果好;占地面积小;抗冲击负荷能力强等优良特性;综合考虑;决定采用化学处理结合A2/O-MBR的工艺..化学处理作为A2/O-MBR工艺的预处理;主要目的是去除绝大部分重金属;降低对活性污泥的毒害..由于络合废水含有较高的氨氮;为了减轻A2/O-MBR工艺的脱氮负荷;采用吹脱的方式对废水进行处理..厌氧池的作用主要是水解酸化以提高废水的可生化性..经过预处理的废水经pH回调后送入生化处理系统..预处理过程如下:络合废水首先采用双氧水破络;然后进行加碱混凝沉淀处理;沉淀后出水进行氨氮吹脱处理..前处理水由于含有油类物质;先做混凝气浮;再进行加碱混凝沉淀..具体的处理流程如图1所示..图1A2/O-MBR工艺流程由图1可见;经预处理后的混合废水先进入pH回调池;加酸将废水的pH调节为9~9.5..经pH回调后的废水进入厌氧池;厌氧池设计较大;总的停留时间较长;在起到水解酸化作用的同时也起到了生化调节池的作用..厌氧池后接两级沉淀池;沉淀厌氧活性污泥回流;上清液进入缺氧池..缺氧池DO较低;主要完成反硝化的作用..缺氧池出水进入好氧池;好氧池末端连接MBR池..此工段主要完成硝化反应;MBR池可以截留几乎所有活性污泥;使出水水质澄清;且使得硝化细菌得以大量增殖;加强了硝化的效果..MBR池出水进入清水池后排放..MBR池硝化液回流入缺氧池;并另设回流管使部分污泥回流入厌氧池..2.2主要构筑物参数及设备选型1生化pH回调池..由于经过物化预处理后的电镀废水呈碱性;不能直接进入生化系统;因此在厌氧池前设置一个pH回调池;通过pH自动控制系统控制H2SO4加入量;使废水的pH维持在9.5~10..处理水量62.5m3/h;尺寸为2.2m×2.2m×2.5m;钢砼结构;地上2.5m..2厌氧池..厌氧池4格串联;单格尺寸为12.0m×3.85m×6m;总停留时间为2 1h..每个厌氧池均在对角线的位置设有两个潜水搅拌器;池间过流孔上下交错布置;以改善池内的水力条件;更好地起到水解酸化及水质调节的作用..钢砼结构;地上2.5m;地下3.5m..3沉淀池..尺寸为28.85m×3.5m×6m;设计停留时间11.5h;钢砼结构;地上2. 5m;地下3.5m..4缺氧池..尺寸为4.5m×17m×6m;设计停留时间8h;对角线的位置设有两个潜水搅拌器;钢砼结构;地上2.5m;地下3.5m..5好氧池..并排4格;单池尺寸为11m×2.85m×6m;曝气使DO维持在2~4mg /L;钢砼结构;地上2.5m;地下3.5m..6MBR池..4个;连接在好氧池末端;单池尺寸为8m×2.85m×3.4m;曝气使DO 维持在2~4mg/L;钢砼结构;地上2.5m;地下0.9m..7MBR膜组件..采用PVDF帘式中空膜组件;总面积为6000m2..8好氧池风机..2个;1用1备;设计风量为20m3/min..9MBR电磁阀、真空罐及自吸泵..设4个电磁阀、2个水环式真空泵及4个自吸泵;通过自控系统控制电磁阀、真空泵及自吸泵的启闭;实现每个MBR池每出水4min后停12min继续出水..自吸泵Q≥15m3/h;H≥10m;根据真空罐内的液位控制自吸泵开启数量..10硝化液回流泵..2个;1用1备..Q≥100m3/h;H≥15m..进水管由MBR池底接出;通过调节出水管阀门调节回流比;正常运行中回流比设为200%..11污泥回流泵..2个;可同时开启..Q≥10m3/h;H≥10m..12自动控制系统..1套;可设置为全自动模式及手动模式;用于控制MBR池的出水..3系统调试运行3.1系统的启动及调试本工程于2011年3月建成并开始调试;由于厌氧池调试耗时较长;整个调试过程持续近8个月..生化系统调试首先进行污泥培养;种泥来自附近一个市政污水厂..养泥过程中硝化液回流系统及曝气系统正常开启;使缺氧池和好氧池中污泥形成循环;每日监测MBR池中的MLSS、SVI、COD、氨氮、总磷等指标;于缺氧池中投加葡萄糖、尿素和磷酸二氢钾使COD、氨氮、总磷分别补充到400、20、4 mg/L..由于条件适宜;养泥过程中污泥量增加很快..连续运行两周后开始驯化;此时MBR池中MLSS达到3000mg/L;SV30已达到约25%;SVI为85mL/g;沉降污泥絮体呈淡黄色;污泥的各项指标均达到比较好的状态..驯化开始后逐步将化学处理部分的出水导入厌氧池;并通过厌氧池进入缺氧池中;在进水的同时开启MBR的出水装置;保证每日进出水量平衡;以维持池中水量的稳定..驯化过程中每日监测4次进水中重金属含量;确保进水重金属含量符合设计要求;以保障生化系统的安全运行..每日监测MBR池中MLSS、SVI、COD、氨氮、总磷等指标以及出水的COD、氨氮、总磷含量;通过出水水质情况来考察活性污泥对污水的适应性..同时继续于缺氧池中投加葡萄糖补充COD;而不再补充N、P..考虑到正常运行时的进水水质情况及控制成本;葡萄糖投加量控制在使COD补充到300mg/L..从养泥开始到完成驯化MBR池内MLSS变化情况如图2所示..图2MBR池内MLSS随时间变化情况由图2可见;驯化开始后MBR池内MLSS增速放慢;趋于停滞;随后又有一定的下降;说明池内的部分微生物因为不适应处理水质遭到淘汰;一段时间后又呈稳定缓慢上升趋势;并最终稳定在3500mg/L左右;说明此时基本完成驯化..在保证活性污泥性状及出水水质稳定的前提下;经过了大约30d完成驯化;此时停止人工投加营养物..驯化初期MBR出水水质尚可;COD达标;氨氮和总磷超标..随着驯化的继续进行;出水氨氮仍然偏高;甚至比驯化初期更高一些;而总磷有一定程度的降低..分析原因可能是:1由于硝化细菌的生长周期较长;此时还未大量增殖;池内硝化作用强度不够;从而导致氨氮去除速率慢..2驯化初期进的工业污水较少;经过稀释后对活性污泥微生物的毒性大大降低..但是随着驯化过程的继续;工业污水进水比例增加;池中重金属的积累使得部分微生物无法适应而遭淘汰;其中可能包含具有硝化功能的微生物;使得活性污泥的硝化能力降低;出水氨氮高..3工业污水的引入所造成的冲击使得池内微生物总量减少;且污泥活性有一定降低;生物增长速度放慢;对N、P等的需求自然也就降低;从而使得出水的氨氮和总磷含量偏高..驯化阶段MBR出水的COD、氨氮、总磷变化情况如图3所示..图3驯化阶段MBR出水COD、氨氮、总磷变化情况由图3可见;到驯化后期;随着活性污泥微生物逐渐适应水质;污泥量有所增加;MBR出水的各项指标也趋于正常;基本达到排放标准要求..好氧池驯化完成后开始逐步将部分回流硝化液分流至厌氧池前端;开启沉淀池污泥回流系统;开始厌氧污泥的培养驯化过程;此过程持续近6个月后整个生化系统开始进入正常运行阶段..整个调试过程均未排泥;到调试末期污泥稳定在3500mg/L左右;相对于处理市政污水的MBR;其污泥浓度不高;分析原因是由于进水含有微量重金属;含盐量较高;COD本身较低;不利于反应器内污泥浓度的提高;然而从出水效果来看;低负荷运行状态的MBR出水水质仍然很好..3.2工艺运行效果厌氧池开始调试后即每天对生化系统进出水进行日常水质监测..运行中控制好进水水质在设计范围内;DO控制为2~4mg/L;硝化液回流比200%;MLSS稳定在3500mg/L左右..从监测结果来看;系统出水水质良好、运行稳定、抗冲击负荷能力较强;经本工艺处理后出水水质达到甚至优于电镀污染物排放标准发布稿G B21900—2008中的要求..随着厌氧池调试进程的推进;出水水质有进一步提高;具体进出水水质情况如表2所示..4工程投资与运行费用本工程总投资550万元;其中MBR膜组件费用为85万元..化学预处理部分运行费用如下:药剂费2.08元/m3;电费1.80元/m3;人工费0.36元/m3;折旧及设备维护费0.30元/m3;生化部分运行费用如下:电费1.20元/m3;折旧及设备维护费1.16元/m3;总运行费用为6.9元/m3..5结论1采用传统化学沉淀法和A2/O-MBR相结合的工艺处理电镀废水效果好;在生化段进水COD250~350mg/L;氨氮45~60mg/L;总磷2.0~3.0mg/L;总铜、总镍、总锌均低于0.5mg/L;DO控制为2~4mg/L;硝化液回流比200%;MLSS在3500mg/L 左右的运行条件下;MBR出水水质良好且稳定;达到电镀污染物排放标准发布稿G B21900—2008中的排放要求..2由于电镀污水水质的特殊性;A2/O-MBR进水含有微量重金属;盐度较高;COD 较低;本工艺正常运行状态的污泥质量浓度相对不高;稳定在3500mg/L左右;但这并没有对处理效果产生不利影响..整个处理系统具有较强的抗冲击负荷能力; MBR的使用对于出水水质的提高具有重要的作用..3电镀废水中所含重金属等有毒物质对活性污泥毒害很大;因此需要在生化系统之前采用传统化学沉淀法对废水进行预处理;使其对活性污泥的毒害降到最低..。
常见工业废水处理方法

常见工业废水处理方法目录一、表面处理废水 (2)1.磨光、抛光废水 (2)2.除油脱脂废水 (2)3.酸洗磷化废水 (2)4.铝的阳极氧化废水 (3)二、电镀废水 (3)1.含氰废水 (3)2.含铬废水 (4)3.综合重金属废水 (4)4.多种电镀废水综合处理 (5)三、线路板废水 (5)1.络合含铜废水(铜氨络合废水) (6)2.油墨废水 (6)3.线路板综合废水 (6)4. 多种线路板废水综合处理 (6)四、常见有机类污染物废水的处理技术 (7)1.生活污水 (7)2.印染废水 (7)3.印刷油墨废水 (7)附件1造纸工业废水处理中的预处理 (8)1.格栅、筛网 (8)2.纤维回收系统 (9)3.调节 (10)4、结论 (10)常见的工业废水主要分布在电子、塑胶、电镀、五金、印刷、食品、印染等行业。
从废水的排放量和对环境污染的危害程度来看,电镀、线路板、表面处理等以无机类污染物为主的废水和食品、印染、印刷及生活污水等以有机类污染物为主的废水是处理的重点。
本文主要介绍几种比较典型的工业废水的处理技术。
一、表面处理废水1.磨光、抛光废水在对零件进行磨光与抛光过程中,由于磨料及抛光剂等存在,废水中主要污染物为COD、BOD、SS。
一般可参考以下处理工艺流程进行处理:废水→调节池→混凝反应池→沉淀池→水解酸化池→好氧池→二沉池→过滤→排放2.除油脱脂废水常见的脱脂工艺有:有机溶剂脱脂、化学脱脂、电化学脱脂、超声波脱脂。
除有机溶剂脱脂外,其它脱脂工艺中由于含碱性物质、表面活性剂、缓蚀剂等组成的脱脂剂,废水中主要的污染物为pH、SS、COD、BOD、石油类、色度等。
一般可以参考以下处理工艺进行处理:废水→隔油池→调节池→气浮设备→厌氧或水解酸化→好氧生化→沉淀→过滤或吸附→排放该类废水一般含有乳化油,在进行气浮前应投加CaCl2破乳剂,将乳化油破除,有利于用气浮设备去除。
当废水中COD浓度高时,可先采用厌氧生化处理,如不高,则可只采用好氧生化处理。
电镀废水处理工艺方案1
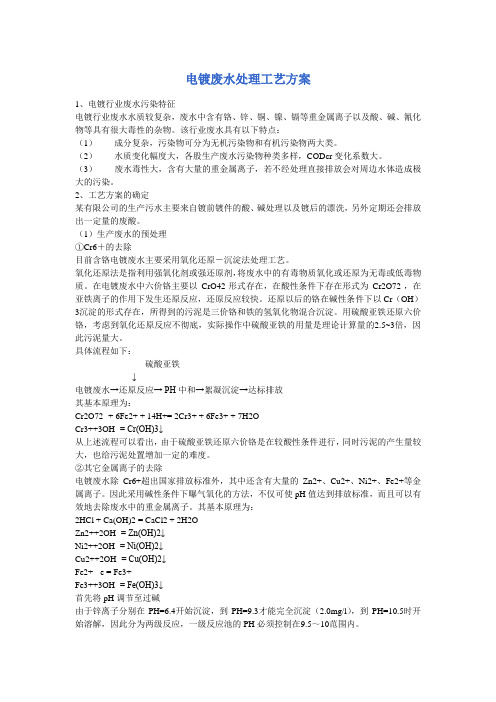
电镀废水处理工艺方案1、电镀行业废水污染特征电镀行业废水水质较复杂,废水中含有铬、锌、铜、镍、镉等重金属离子以及酸、碱、氰化物等具有很大毒性的杂物。
该行业废水具有以下特点:(1)成分复杂,污染物可分为无机污染物和有机污染物两大类。
(2)水质变化幅度大,各股生产废水污染物种类多样,CODcr变化系数大。
(3)废水毒性大,含有大量的重金属离子,若不经处理直接排放会对周边水体造成极大的污染。
2、工艺方案的确定某有限公司的生产污水主要来自镀前镀件的酸、碱处理以及镀后的漂洗,另外定期还会排放出一定量的废酸。
(1)生产废水的预处理①Cr6+的去除目前含铬电镀废水主要采用氧化还原-沉淀法处理工艺。
氧化还原法是指利用强氧化剂或强还原剂,将废水中的有毒物质氧化或还原为无毒或低毒物质。
在电镀废水中六价铬主要以CrO42-形式存在,在酸性条件下存在形式为Cr2O72-,在亚铁离子的作用下发生还原反应,还原反应较快。
还原以后的铬在碱性条件下以Cr(OH)3沉淀的形式存在,所得到的污泥是三价铬和铁的氢氧化物混合沉淀。
用硫酸亚铁还原六价铬,考虑到氧化还原反应不彻底,实际操作中硫酸亚铁的用量是理论计算量的2.5~3倍,因此污泥量大。
具体流程如下:硫酸亚铁↓电镀废水→还原反应→ PH中和→絮凝沉淀→达标排放其基本原理为:Cr2O72- + 6Fe2+ + 14H+= 2Cr3+ + 6Fe3+ + 7H2OCr3++3OH- = Cr(OH)3↓从上述流程可以看出,由于硫酸亚铁还原六价铬是在较酸性条件进行,同时污泥的产生量较大,也给污泥处置增加一定的难度。
②其它金属离子的去除电镀废水除Cr6+超出国家排放标准外,其中还含有大量的Zn2+、Cu2+、Ni2+、Fe2+等金属离子。
因此采用碱性条件下曝气氧化的方法,不仅可使pH值达到排放标准,而且可以有效地去除废水中的重金属离子。
其基本原理为:2HCl + Ca(OH)2 = CaCl2 + 2H2OZn2++2OH- = Zn(OH)2↓Ni2++2OH- = Ni(OH)2↓Cu2++2OH- = Cu(OH)2↓Fe2+ - e = Fe3+Fe3++3OH- = Fe(OH)3↓首先将pH调节至过碱由于锌离子分别在PH=6.4开始沉淀,到PH=9.3才能完全沉淀(2.0mg/l),到PH=10.5时开始溶解,因此分为两级反应,一级反应池的PH必须控制在9.5~10范围内。
电镀废水处理新工艺介绍
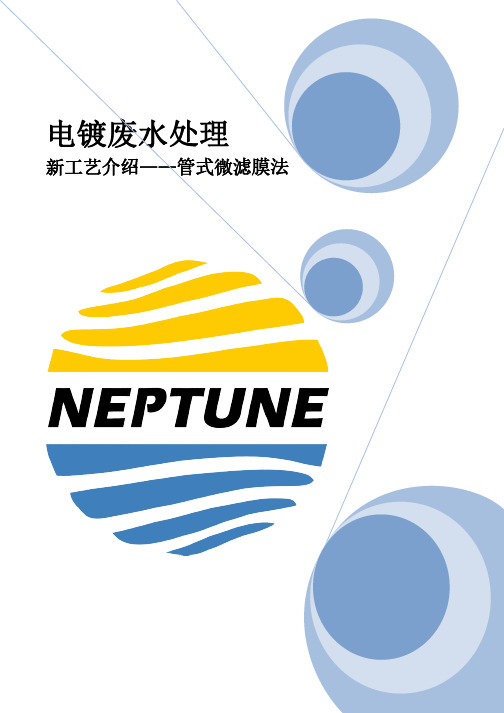
电镀废水处理新工艺介绍——管式微滤膜法一、概述电镀废水就其总量来说,比如造纸、印染、化工、等行业的水量小,污染面窄,但由于电镀厂点分布广,废水中所含高毒物质的种类多,其危害性是很大的。
未经处理达标的电镀废水排入河道、池塘,渗入地下,不但会危害环境,而且会污染饮用水和工业用水。
电镀废水中含有铬锌、铜、镉,铅、镍等重金属离子以及酸、碱氰化物等具有很大毒性的杂物。
有的还属于致癌和致畸变的剧毒物质.因此必须认真地加以处理.以免对人们造成危害。
电镀废水的成分非常复杂,除含氰(CN)-废水和酸碱废水外,重金属废水是电镀业潜在危害性极大的废水类别。
多数废水为含铬(Cr)、镍(Ni)、含镉(Cd)、铜(Cu)、锌(Zn)废水,而含金(Au)和银(Ag)贵重金属废水直接回收。
随着电镀工业的快速发展和环保要求的日益提高,目前,电镀废水治理已开始进入清洁生产工艺>清洁生产工艺、总量控制阶段,但是进步的资源回收利用和闭路循环将是发展的主要方向。
所以现所提出的微滤+反渗透处理回收电镀废水技术,将会被更多企业采用。
电镀是利用化学和电化学方法在金属或在其它材料表面镀上各种金属。
广泛应用于机器制造、轻工、电子等行业。
为提高镀件的质量,电镀生产中使用的电镀添加剂种类和数量越来越多,成分也越来越复杂,这些添加剂含有与重金属离子络合作用较强的成分,如:酒石酸、EDTA、焦磷酸盐、柠檬酸和氨等,在采用传统化学沉淀法处理电镀废水过程中,重金属离子就不能完全形成氢氧化物沉淀,其中的重金属离子含量极容易超过国家废水排放标准。
利用NT-Micro管式微滤膜+反渗透膜双膜法处理电镀废水,是电镀废水最高效的处理方式。
他具有占地小,运行成本低,运行稳定等特点。
电镀含镍、含铜废水循环系统是NT-Micro膜公司专门针对电镀生产过程中产生的大量含镍、铜等贵重金属废水的回收利用而设计研发的,该系统是以膜科技为核心,按照“废水分流,分别处理,清水回用,金属回收”的原则进行综合设计,实现电镀废水以及贵重金属资源的循环利用。
电镀废水处理工艺流程

电镀废水处理工艺流程电镀废水是指在电镀生产过程中所排放的含有重金属离子、有机物和其他有害物质的废水。
由于其含有大量的有毒物质,如果直接排放到环境中,将会对周围的土壤、水源和生态环境造成严重的污染。
因此,对电镀废水进行有效的处理是非常重要的。
下面将介绍电镀废水处理的工艺流程。
首先,电镀废水处理的第一步是预处理。
预处理的主要目的是去除废水中的悬浮物、沉淀物和油污等杂质,以保护后续处理设备的正常运行。
预处理过程通常包括格栅过滤、沉淀池沉淀、过滤等操作,有效去除废水中的大颗粒杂质。
接下来是化学处理。
在预处理后的电镀废水中,仍然含有大量的重金属离子和有机物。
化学处理的主要目的是利用化学方法将废水中的有害物质转化成无害的物质,或者将其沉淀下来。
常用的化学处理方法包括中和沉淀、氧化还原、络合沉淀等。
随后是生物处理。
生物处理是利用微生物对废水中的有机物进行降解和转化的过程。
通过生物处理,可以有效地降低废水中有机物的含量,减少废水对环境的污染。
生物处理通常包括好氧生物处理和厌氧生物处理两种方式。
最后是深度处理。
深度处理是为了进一步提高废水的处理效果,通常采用高级氧化、膜分离、离子交换等技术,以达到对废水中残留有机物和重金属离子的高效去除。
综上所述,电镀废水处理工艺流程包括预处理、化学处理、生物处理和深度处理四个步骤。
通过这些处理步骤,可以有效地将电镀废水中的有害物质去除或转化,达到排放标准,保护环境和人类健康。
在实际操作中,需要根据废水的具体成分和特性,选择合适的处理工艺和设备,以确保废水处理的效果和经济性。
电镀废水处理流程专业讲解

一般清洗水 处理系统
电镀废水分类处理工艺
?含氰废水的处理
? 采用碱性氯化法, 两级破氰。
含氰废水 pH 调节池I
一级破氰
pH 调节池II
二级破氰
一般清洗水 处理系统
电镀废水分类处理工艺
?混排废水处理系统:
混排废水
一级破氰
二级破氰
含铬废水池
电镀废水分类处理工艺
?生化处理系统的特点:
1、有效去除COD。 2、采用“投药式活性污泥法”,防止污泥膨胀。
主要污染物处理技术—COD的去除
主要是镀件清洗、除油、除蜡造成的COD。 ? 常见的处理方法有: 1.化学氧化法; 2.气浮法; 3.生物处理法;
主要污染物处理技术—COD的去除
?化学氧化法 Fenton 氧化法:
是产生强氧化性的羟基自由基 (·OH),从而直接 氧化有机物,达到去除效果。 其它氧化法: 漂白水氧化法、 漂白粉氧化法、 双氧水氧化法、
主要污染物处理技术——COD的去除
Fenton氧化法原理
Fe2+ + H2O2 → Fe2+ + OH- + ·OH Fe2+ + ·OH → Fe3+ + OHFe3+ + H2O2 → Fe2+ + H+ + HO2· HO2·+ H2O2 → O2 + H2O + ·OH RH + ·OH → R·+ H2O R·+ Fe3+ → R+ + Fe2+ R+ + O2 → ROO+ →······→ CO2 + H2O
- 1、下载文档前请自行甄别文档内容的完整性,平台不提供额外的编辑、内容补充、找答案等附加服务。
- 2、"仅部分预览"的文档,不可在线预览部分如存在完整性等问题,可反馈申请退款(可完整预览的文档不适用该条件!)。
- 3、如文档侵犯您的权益,请联系客服反馈,我们会尽快为您处理(人工客服工作时间:9:00-18:30)。
电镀络合废水处理工艺流程
一、废水收集
电镀络合废水主要来源于电镀生产过程中的清洗、漂洗、钝化等环节,具有浓度高、成分复杂、含多种重金属离子等特点。
为确保废水处理效果,需要将不同生产环节的废水分类收集,避免不同类型废水相互混合,影响后续处理效果。
同时,应设置合理的收集系统,确保废水顺畅、稳定地进入处理设备。
二、预处理
预处理的目的是去除废水中的大颗粒物质、悬浮物和部分有机物,为后续处理创造有利条件。
预处理一般包括过滤、中和、化学氧化等方法。
根据电镀络合废水的特点,可采用化学氧化法,通过投加氧化剂,如高锰酸钾、双氧水等,将有毒有害物质转化为无毒或低毒物质。
三、混凝沉淀
混凝沉淀是电镀络合废水处理的重要环节,通过投加混凝剂,使废水中的悬浮物、重金属离子等物质凝聚成大颗粒,便于后续分离。
常用的混凝剂包括聚合氯化铝(PAC)、聚合硫酸铁(PFS)等。
在混凝沉淀过程中,应控制好混凝剂的投加量、搅拌速度和反应时间,确保混凝效果。
四、泥水分离
经过混凝沉淀后的废水需要进行泥水分离,将废水中的悬浮物和大颗粒物质分离出来。
常用的泥水分离方法包括重力沉降、离心分离和气浮等。
根据电镀络合废水的特点,可采用重力沉降和离心分离相
结合的方法,提高分离效果。
分离出的污泥可进行进一步处理,如浓缩、脱水等。
五、活性炭吸附
活性炭吸附是电镀络合废水处理中的重要环节,可以有效去除废水中的有机物、重金属离子等有害物质。
活性炭具有高比表面积、多孔结构等特点,能够吸附大量的有害物质。
为确保处理效果,应根据废水的浓度和特点,选择合适的活性炭种类和投加量。
同时,需要定期更换活性炭,防止吸附饱和。
六、生物处理
生物处理是利用微生物降解有机物的能力,对电镀络合废水中的有害物质进行分解和转化。
常用的生物处理方法包括活性污泥法、生物膜法等。
在选择生物处理方法时,应根据废水的浓度、流量和特点,选择合适的微生物种类和生长条件。
同时,需要控制好溶解氧、温度、pH等环境因素,促进微生物的生长和代谢。
七、二次处理
经过生物处理后的电镀络合废水仍可能含有一定的有害物质,需要进行二次处理。
二次处理的方法可根据废水的特点和环境要求选择,常用的方法包括高级氧化、电化学氧化等。
高级氧化通过投加氧化剂或利用催化剂等方法,将废水中的有机物和重金属离子彻底氧化分解;电化学氧化通过电解作用,使废水中的有害物质在阳极上发生氧化反应而被去除。
八、排放或回收利用
经过二次处理后的电镀络合废水可达到国家排放标准或回收利用要求,可根据实际情况选择排放或回收利用。
如需排放,应按照相关规定设置排放口,并监测废水中的各项指标;如需回收利用,应根据实际需求进行进一步处理和浓缩,提高废水回用率。