汽车直线制动仿真计算与优化
制动系统的优化设计与仿真分析
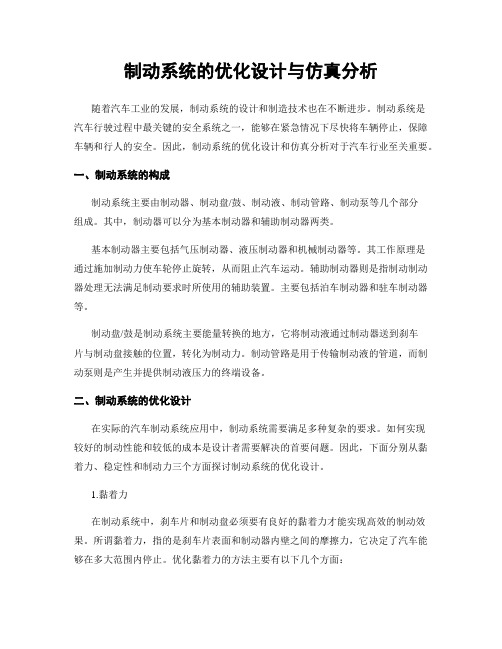
制动系统的优化设计与仿真分析随着汽车工业的发展,制动系统的设计和制造技术也在不断进步。
制动系统是汽车行驶过程中最关键的安全系统之一,能够在紧急情况下尽快将车辆停止,保障车辆和行人的安全。
因此,制动系统的优化设计和仿真分析对于汽车行业至关重要。
一、制动系统的构成制动系统主要由制动器、制动盘/鼓、制动液、制动管路、制动泵等几个部分组成。
其中,制动器可以分为基本制动器和辅助制动器两类。
基本制动器主要包括气压制动器、液压制动器和机械制动器等。
其工作原理是通过施加制动力使车轮停止旋转,从而阻止汽车运动。
辅助制动器则是指制动制动器处理无法满足制动要求时所使用的辅助装置。
主要包括泊车制动器和驻车制动器等。
制动盘/鼓是制动系统主要能量转换的地方,它将制动液通过制动器送到刹车片与制动盘接触的位置,转化为制动力。
制动管路是用于传输制动液的管道,而制动泵则是产生并提供制动液压力的终端设备。
二、制动系统的优化设计在实际的汽车制动系统应用中,制动系统需要满足多种复杂的要求。
如何实现较好的制动性能和较低的成本是设计者需要解决的首要问题。
因此,下面分别从黏着力、稳定性和制动力三个方面探讨制动系统的优化设计。
1.黏着力在制动系统中,刹车片和制动盘必须要有良好的黏着力才能实现高效的制动效果。
所谓黏着力,指的是刹车片表面和制动器内壁之间的摩擦力,它决定了汽车能够在多大范围内停止。
优化黏着力的方法主要有以下几个方面:(1)选择合适的材料。
选择合适的刹车片材料可以改善制动器与制动盘之间的黏着力,从而提高制动性能。
目前主流的刹车片材料有金属、有机和陶瓷等,不同材料的优缺点也不同。
(2)改善制动盘表面。
制动盘表面会因为使用而损耗,会影响刹车片与制动盘之间的黏着力。
对制动盘进行适当的处理或涂层处理可以改善黏着性能。
(3)优化刹车片结构。
刹车片的厚度和面积也会影响制动性能。
适当增加刹车片的面积或者采用具有弹性可调的刹车片结构可以增强黏着性能。
汽车刹车系统动力学仿真优化研究
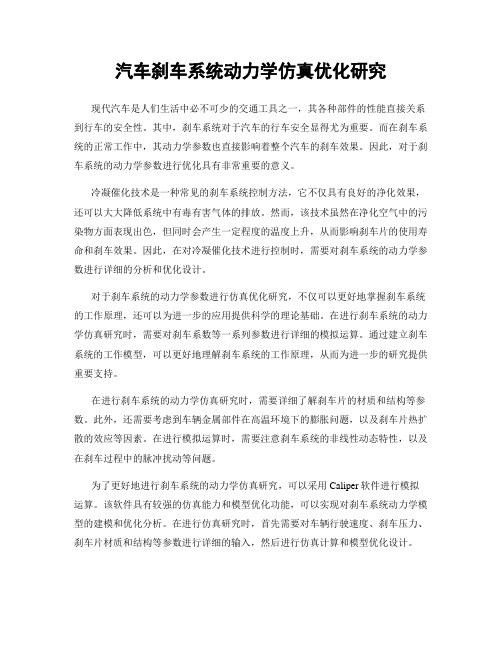
汽车刹车系统动力学仿真优化研究现代汽车是人们生活中必不可少的交通工具之一,其各种部件的性能直接关系到行车的安全性。
其中,刹车系统对于汽车的行车安全显得尤为重要。
而在刹车系统的正常工作中,其动力学参数也直接影响着整个汽车的刹车效果。
因此,对于刹车系统的动力学参数进行优化具有非常重要的意义。
冷凝催化技术是一种常见的刹车系统控制方法,它不仅具有良好的净化效果,还可以大大降低系统中有毒有害气体的排放。
然而,该技术虽然在净化空气中的污染物方面表现出色,但同时会产生一定程度的温度上升,从而影响刹车片的使用寿命和刹车效果。
因此,在对冷凝催化技术进行控制时,需要对刹车系统的动力学参数进行详细的分析和优化设计。
对于刹车系统的动力学参数进行仿真优化研究,不仅可以更好地掌握刹车系统的工作原理,还可以为进一步的应用提供科学的理论基础。
在进行刹车系统的动力学仿真研究时,需要对刹车系数等一系列参数进行详细的模拟运算。
通过建立刹车系统的工作模型,可以更好地理解刹车系统的工作原理,从而为进一步的研究提供重要支持。
在进行刹车系统的动力学仿真研究时,需要详细了解刹车片的材质和结构等参数。
此外,还需要考虑到车辆金属部件在高温环境下的膨胀问题,以及刹车片热扩散的效应等因素。
在进行模拟运算时,需要注意刹车系统的非线性动态特性,以及在刹车过程中的脉冲扰动等问题。
为了更好地进行刹车系统的动力学仿真研究,可以采用Caliper软件进行模拟运算。
该软件具有较强的仿真能力和模型优化功能,可以实现对刹车系统动力学模型的建模和优化分析。
在进行仿真研究时,首先需要对车辆行驶速度、刹车压力、刹车片材质和结构等参数进行详细的输入,然后进行仿真计算和模型优化设计。
在实际行车过程中,刹车系统的刹车力度和刹车力持续时间都是影响刹车效果的重要因素。
因此,在进行刹车系统的动力学仿真研究时,需要特别考虑这些因素。
同时,为了更好地控制刹车系统的动力学参数,可以采用模型预测控制方法,实现对刹车系统的精确控制。
乘用车制动感觉仿真分析与优化研究

MANUFACTURING AND PROCESS I卸造与工艺乘用车制动感觉仿真分析与优化研究张涵1徐伟21.上汽通用五菱汽车股份有限公司广西柳州市5450072.武汉理工大学机电学院湖北省武汉市430070摘要:针对乘用车的制动感觉在车辆制动性能中愈发备受重视,本文对汽车制动中制动系统所需制动液总体积和制动踏板行程进行了分析,提出建立制动踏板感觉的仿真模型来分析乘用车制动踏板感觉。
分别对制动器、制 动软管、制动主缸进行了模型建立,得到制动踏板位移、制动减速度和制动踏板力的关系曲线。
并针对某款车型的制动系统进行了制动感觉试验来验证模型的合理性,同时对其制动感觉进行了优化与优化结果验证。
结果表明,制动踏板感觉仿真模型切合实际,增大前制动轮缸缸径、前有效制动半径和后有效制动半径可以减小制动踏板力,并达到优化制动感觉的效果。
关键词:制动感觉;仿真模型;制动踏板力;制动踏板位移1引言据中国汽车工业协会统计,2017年全年 乘用车销量约为2420.91辆,稳居全球第一。
伴随着汽车行业的蓬勃发展,消费者对车辆 安全性中的制动性能也更加重视,而其中制 动感觉尤为如此。
根据JD Pow-e r的反馈,对汽车制动感觉方面反映最多的问题主要有 制动不够力、制动偏软、刹车不够灵敏等[1]。
因而对汽车制动感觉的研究是提高乘用车的 制动性能的一个重要方向。
侯俊、过学迅应用UG对盘式制动器进 行建模,并用ANSYS软件对制动器总成有限元模型进行了有限元分析'孟建德、张立军和余卓平等开发构建了乘用车制动踏板感 觉试验台架来研究关健因素对制动踏板感觉 的影响[3]。
国外对制动感觉研究则较为成熟,Rena、Paul等通过对制动卡钳内的制动块的 材料进行研究,通过理论和实验证明了制动 块的材料确实能够在一定程度上对乘用车的 制动感觉产生影响[4]。
David、M ark等人通 过对制动系统中的制动软管进行了研究,发 现制动软管的膨胀量会引起制动液的体积增 加,从而会对乘用车的制动感觉产生影响[5]。
汽车性能仿真计算实验实验报告

汽车性能仿真计算实验实验报告实验⼀汽车动⼒性仿真计算实验⽬的1.掌握汽车动⼒性评价指标和评价⽅法2.学会使⽤matlab 对汽车动⼒性指标进⾏计算实验内容1.学习汽车动⼒性理论2.编写计算程序3.绘制汽车动⼒性图形实验设备硬件环境:汽车虚拟仿真实验室软件环境:matlab2016a 及以上版本实验步骤1.学习汽车动⼒性理论2.编写计算程序3.绘制汽车动⼒性图形实验报告1. 运⽤matlab 解决《汽车理论》第⼀章习题1.31)绘制汽车驱动⼒与⾏驶阻⼒平衡图汽车驱动⼒Ft=ri i T to g tq η⾏驶阻⼒F f +F w +F i +F j =G ?f +2D 21.12A C a u +G ?i+dt dum δ发动机转速与汽车⾏驶速度之间的关系式为:0g i nr 0.377ua i ?= 由本题的已知条件,即可求得汽车驱动⼒和⾏驶阻⼒与车速的关系,编程即可得到汽车驱动⼒与⾏驶阻⼒平衡图。
2)求汽车最⾼车速,最⼤爬坡度及克服该坡度时相应的附着率①由1)得驱动⼒与⾏驶阻⼒平衡图,汽车的最⾼车速出现在5档时汽车的驱动⼒曲线与⾏驶阻⼒曲线的交点处,Ua max =99.08m/s 2。
②汽车的爬坡能⼒,指汽车在良好路⾯上克服w f F F +后的余⼒全部⽤来(等速)克服坡度阻⼒时能爬上的坡度,此时0=dt du,因此有()w f t i F F F F +-=,可得到汽车爬坡度与车速的关系式:()+-=G F F F i w f t arcsin tan ;⽽汽车最⼤爬坡度为Ⅰ档时的最⼤爬坡度。
利⽤MATLAB 计算可得,352.0max =i 。
③如是前轮驱动,1?C =qb hg q L L -;相应的附着率1?C 为1.20,不合理,舍去。
如是后轮驱动,2?C =qa hg q L L+;相应的附着率2?C 为0.50。
3)绘制汽车⾏驶加速度倒数曲线,求加速时间利⽤MATLAB 画出汽车的⾏驶加速度图和汽车的加速度倒数曲线图:忽略原地起步时的离合器打滑过程,假设在初时刻时,汽车已具有Ⅱ档的最低车速。
关于汽车制动系统性能分析及优化设计探讨

MANUFACTURING AND PROCESS | 制造与工艺关于汽车制动系统性能分析及优化设计探讨郝孟军 梅容芳 宫涛 刘福华 刘良 周彬宜宾职业技术学院 四川省宜宾市 644003摘 要: 我国汽车产业发展的速度在不断的加快,同时得到了我国有关部门的重视,在这种情况下,汽车产业的安全问题也是人们非常重视的问题。
在汽车的安全系统中,汽车制动系统是非常关键的作用。
汽车制动系统的主要作用是要确保车辆在进行制动的过程中有比较稳定的减速过程。
本文对汽车制动系统的性能进行了深入的分析,并提出相应的优化设计。
关键词:汽车制动系统 性能分析 优化设计1 引言汽车制动系统的作用主要是在制动时对车辆进行可靠的减速,同时确保车辆在制动过程中不受地面坡度的干扰,使车辆能够平稳地行驶。
汽车制动系统中最常见的制动方法是电子制动以及气动动力制动。
在本文中,主要分析汽车的制动系统工作原理,分析了制动系统的主要功能,并提出了相应的优化设计。
2 汽车制动系统的主要工作原理2.1 电子制动系统的工作原理一般来说,汽车的电子制动系统的原理主要包括以下几点:如果车辆在进行行驶时,需要进行紧急制动,驾驶员需要用力通过制动踏板进行制动信号的发送,信号经三环调速系统有效调节后通过机电制动系统,同时,确保直流无刷力矩发动机直接接收输出铠装的电压,然后运用旋转发动机轴把需要输出的转速信号传输到传动机构中,通过减速以及扭矩把转速信号转换成螺杆的位移,在这个制动过程中,汽车机电制动系统的工作过程是非常速度的,只有0.1s。
2.2 汽车气动制动系统的工作原理目前,许多车辆主要采用气动制动系统。
为了更好的提升气压制动系统的安全性,应总结和分析气压制动系统的工作原理和特点,提升气制动系统的工作效率。
当驾驶员安全驾驶时,汽车空气制动系统不使用汽车空气制动系统。
在此过程中,车辆的气动制动系统是处于待机的状态,气动制动系统的气动阀和快速释放阀完全失效,车辆气动制动系统的前后制动气室与室外空气的气压是处于相同的状态,但气室没有与储气罐中的压缩空气进行有效地连接,当车辆遇到紧急的情况时,需要进行紧急制动,司机需要做好车辆气动制动系统的制动阀,能够及时的踩下车辆的制动踏板。
汽车制动系统的设计及仿真

汽车制动系统的设计及仿真任务书1.设计的主要任务及目标汽车制动器是制动系中最重要的一个部件,是制动系统中用以产生阻碍汽车运动或运动趋势的力的部件。
凡是利用固定元件与旋转元件工作表面的摩擦而产生制动力矩的制动器都成为摩擦制动器。
摩擦制动器可分为鼓式和盘式两大类。
前者的摩擦副中的旋转元件为制动鼓,其工作表面为圆柱面;后者的旋转元件则为圆盘状的制动盘,以端面为工作表面。
2.设计的基本要求和内容(1)了解汽车制动系统的工作过程。
(2)熟悉汽车制动系统的设计过程和设计参数。
(3)结合汽车制动性能要求设计汽车制动器。
(4)结合三维建模软件,并实现制动器的运动仿真。
3.主要参考文献[1] 王望予.汽车设计[M].北京:机械工业出版社,2004[2] 余志生.汽车理论[M].北京:机械工业出版社,2003[3] 陈家瑞.汽车构造[M].北京:机械工业出版社,2003[4] 林秉华.最新汽车设计实用手册[M],黑龙江:黑龙江出版社,2005[5] 张尉林.汽车制动系统的分析与设计[M].北京:机械工业出社,20024.进度安排注:一式4份,系部、指导教师各1份、学生2份:[毕业设计]及答辩评分表各一份汽车制动系统的设计及仿真摘要:汽车的制动系是汽车行车安全的保证,许多制动法规对制动系提出了许多详细而具体的要求,这是我们设计的出发点。
从制动器的功用及设计的要求出发,依据给定的设计参数,进行了方案论证。
对各种形式的制动器的优缺点进行了比较后,选择了浮动钳盘的形式。
这样,制动系有较高的制动效能和较高的效能因素稳定性。
随后,对盘式制动器的具体结构的设计过程进行了详尽的阐述。
选择了简单液压驱动机构和双管路系统,选用了间隙自动调节装置。
在设计计算部分,选择了几个结构参数,计算了制动系的主要参数,盘式制动器相关零件的设计计算。
关键词: 制动器,同步附着系数,制动盘,制动钳Automobile brake system design and simulationAbstracts:The braking system in a vehicle guaranteed the safety of driving .Many rules and regulations have been made for the braking system in detail, which is the starting of our design.Firstly, I demonstrate the project on the base of the function of the brake, And analysis their strong point and shortcomings .I choose the form of front-disked. In this way, the braking system have higher braking efficiency and high stability of the performance factors. Subsequently, the specific structure of the disc brake design was elaborated in detail.I designed the hydraulic drive system and two-pipe system and selected clearance automatic adjusting device.In the calculate part .I chosen several structural parameters, calculated the main parameters of the braking system drive mechanism.Key words:disc brakes,synchronous attachment coefficient,brake disc,brake caliper目录1 绪论 (1)1.1 课题研究的目的及意义 (1)1.2制动系统研究现状 (1)1.3课题设计思路 (3)2制动系统概述 (4)2.1制动系的类型 (4)2.2汽车制动系统组成 (4)2.3 制动器的组成 (5)2.4 制动器的要求 (5)2.5 制动器的种类 (7)3 汽车参数计算 (14)3.1汽车的基本参数 (14)3.2 制动系的主要参数及其选择 (15)3.3 盘式制动器的结构参数与摩擦系数的确定 (16)3.4 制动衬块的设计计算 (18)3.5 摩擦衬块磨损特性的计算 (19)4 制动器主要零件的结构设计 (21)4.2 制动钳 (21)4.4 摩擦材料 (21)4.5 盘式制动器间隙的调整方法及相应机构 (22)4.6 制动驱动机构的结构型式选择与设计计算 (22)结论 (25)参考文献 (26)致谢 (27)附录 (28)1 绪论1.1 课题研究的目的及意义汽车的设计与生产涉及到许多领域,其独有的安全性、经济性、舒适性等众多指标,也对设计提出了更高的要求。
轿车制动性能仿真分析与计算
进行轿车制动性能的仿真分析和计算通常涉及以下步骤和考虑因素:
步骤一:建立轿车制动系统模型
1. 车辆参数收集:收集轿车相关参数,如质量、车轮半径、制动器类型等。
2. 制动系统建模:建立轿车制动系统的数学模型,包括制动盘、刹车片、制动液、制动缸等组成部分。
步骤二:制动力计算
1. 制动力分析:根据制动器和车速等参数计算制动力的大小。
2. 摩擦系数考虑:考虑轮胎与地面的摩擦系数,影响制动力的传递效果。
步骤三:制动距离仿真
1. 刹车距离计算:利用制动力和车辆动力学方程计算制动过程中的制动距离。
2. 不同情况考虑:考虑干燥、潮湿、结冰路面等不同路况对制动距离的影响。
步骤四:热力学分析
1. 制动系统热平衡:考虑制动过程中制动系统的热平衡问题,防止制动器过热失效。
2. 材料特性影响:考虑制动盘和刹车片材料的热特性对制动性能的影响。
步骤五:模拟验证与优化
1. 仿真验证:运用仿真软件(如ADAMS、Simulink等)进行制动性能的仿真验证。
2. 性能优化:根据仿真结果对制动系统进行优化设计,提高制动性能。
以上步骤涉及到多个领域的知识,包括车辆动力学、制动系统设计、热力学等。
在实际工程中,通常需要借助专业的仿真软件和工程计算工具来进行轿车制动性能的分析与计算。
基于Modelica的电动汽车制动系统建模仿真与参数优化
基于Modelica的电动汽车制动系统建模仿真与参数优化随着社会的发展,电动汽车已经成为一个必然趋势,并且成为了解决环境问题的重要手段。
然而,电动汽车的制动系统与传统汽车的制动系统有很大的不同,需要重新对制动系统进行建模和优化。
基于Modelica语言,我们可以建立一个电动汽车的制动系统模型,并对其进行仿真和优化。
在这个模型中,我们把制动系统分成了三个部分,即制动器、电机和控制器。
制动器部分使用Modelica.Mechanics.Rotational子库中的元件进行建模。
我们把制动器建模成了一个摩擦片和转子的组合体。
当制动器处于制动状态时,摩擦片会和转子发生摩擦,从而减速汽车。
电机部分主要建模电机的动力学特性,使用Modelica.Electrical.Machines库进行建模。
我们采用了一个直流电机,并根据电机参数建立动力学模型,包括转矩-转速曲线等。
在制动时,电机接通再反向运转,产生负功率,从而带动轮胎减速。
控制器部分主要控制制动系统的动作,采用了Modelica.Blocks中的元件进行建模。
控制器部分的主要功能是根据汽车速度和制动踏板的行程,计算制动器的力矩,从而控制汽车制动。
在建立完毕制动系统的模型之后,我们可以使用仿真软件对制动系统进行仿真测试。
通过仿真测试,我们可以观测到制动系统是否能够正常运作,并且可以得到控制参数的优化方案。
我们可以通过调整控制器部分的参数来达到最佳制动效果。
例如,通过改变制动器的力矩大小,我们可以调整制动系统的制动能力。
如果力矩太小,制动效果不佳;如果力矩太大,会导致轮胎打滑。
因此,我们需要进行参数优化,以达到最佳制动效果。
在最终的仿真测试结果中,我们得到了一个能够良好运作的电动汽车制动系统模型,该模型的制动系统具有良好的稳定性和可靠性,并能够通过控制器的参数优化实现最佳制动效果。
基于Modelica的电动汽车制动系统建模仿真与参数优化可以帮助我们更好地了解电动汽车的特性,并且优化它们的制动性能。
基于Modelica的电动汽车制动系统建模仿真与参数优化
modeling language—Modelica is established.A testing method based on VBOX一3i data logger is proposed.The simulation results agree with the test results and the accuracy of the m odel is verif ied.Based on the m odel,the parameters of vacuum assist brake system are optimized by orthogonal experiment method. The optimized parameters can reduce energ y consumption of the vacuum assist brake system by approx.14.2%.
【摘要 】基于多领域统一建模语言 Modelica建立 了电动汽车整车模 型及真空助力制动系统模型,提出了基于车辆数据 采 集 系统 VBOX一3i的 测试 方 法 ,并 通 过对 电动 中 巴车 的 实车 路 况测 试 验 证 了仿 真模 型 的 准确 性 。在 此 基础 上 ,利 用 正交 试
基金项 目:F-东省 战略性新兴产业核 心技术攻关项 目(编号 :2011A010802003)、东莞 市重大科技专项 (编号 :2011215155)。
2016 ̄ 第2期
一33—
不同车速下汽车的制动性能仿真分析
1制动距离仿真分析制动距离是指汽车在一定的初速度下,从驾驶员急踩制动踏板开始,到汽车完全停住为止所驶过的距离,它是重要的衡量汽车制动性能的指标之一。
汽车制动距离主要受车速和制动力大小的影响,一旦车轮发生了制动抱死,轮胎与地面之间的附着系数将比其间的峰值附着系数有所减小,从而增加制动距离,而制动距离过大,很容易导致各类交通事故。
有资料显示,每增加0.1m 的制动距离,交通事故的发生率就会大大提高,而交通事故的发生率又和车速存在直接关系。
基于此,本文十分有必要对车速与制动距离之间的关系开展研究。
本文是对装有ABS 汽车在基于逻辑门限值,PID 和模糊控制三种不同控制算法的车速与制动距离的关系研究。
图1-图6给出了在初始速度60km/h 、80km/h 和100km/h 下,三种不同控制算法的制动距离和制动时间变化曲线。
由图1-图6可以得出在初始速度60km/h 、80km/h 和100km/h 下,基于逻辑门限值控制算法,PID 控制算法和模糊控制算法的制动距离和制动时间数值。
归纳为表1。
由表1可以得出:①在相同控制算法情况下,车速对制动距离和制动时间存在较大影响。
比如,基于门限值控制算法控制下,车速为60km/h 时,制动时间为1.75s ,车速为80km/h 时为2.22s ,较车速为60km/h 增加了0.47s ,车速为100km/h 时为2.18s ,较车速为60km/h 增加了0.955s 。
在制动距离上,车速为60km/h 时,制动距离为16.28m ,车速为80km/h 时,制动距离为为27.23m ,较车速为60km/h 增加了10.95m ,车速为100km/h 时为39.84m ,较车速为60km/h 增加了近一倍,增加了15.20m 。
由此可见,制动距离增加速率远远大于车速的增加速率。
更能充分说明了,即使装有ABS 的汽车,在高速行驶时,也是非常危险的。
②在相同初始车速的情况下,基于门限值控制的制动时间和制动距离相比PID 控制和模糊控制都最大。
- 1、下载文档前请自行甄别文档内容的完整性,平台不提供额外的编辑、内容补充、找答案等附加服务。
- 2、"仅部分预览"的文档,不可在线预览部分如存在完整性等问题,可反馈申请退款(可完整预览的文档不适用该条件!)。
- 3、如文档侵犯您的权益,请联系客服反馈,我们会尽快为您处理(人工客服工作时间:9:00-18:30)。
传统制动系统的建模及仿真优化1.1 汽车直线制动仿真计算理论基础汽车直线制动时,对两轮接地点分别取距(图1-1),可得地面法向反作用力为1()g z G b zh F L+=(1-1) 2()g z G a zh F L -= (1-2) 式中,j z g=,1z F 、2z F 分别为路面对前后车轮的法向作用力;G 为汽车重量;a 、b 分别为质心至前后轴的距离;j 为汽车减速度;g h 为汽车质心高度;L 为汽车的轴距。
汽车理论制动力分配关系为1(2)2r f gGb F F h =+ (1-3) 式中,r F 为汽车后轴制动力;f F 为汽车前轴制动力。
1.1.1 制动力分配比制动力分配比β为ff r F F F β=+ (1-4)1.1.2 直线制动的最佳制动力分配 设汽车前轮刚要抱死或者汽车前、后轮同时刚要抱死的减速度为du zg dt=,则 1u G du F Gz g dtββ== 式中,z 为制动强度。
根据汽车理论,可知前、后轴的利用附着系数为1()f g zb zh Lβϕ=+ (1-5)(1)1()r g z a zh L βϕ-=- (1-6) 前后轴的附着效率为f f gb LE h L ϕβ=- (1-7)(1)r r ga LE h L ϕβ=-+ (1-8)由于后轮先抱死容易发生后轴侧滑,是一种不稳定工况,故r f ψϕϕ≤≤,由式(1-5)和式(1-6)可以得出制动力分配比的极限关系为min min 1g g h h a b L Iz LIz ϕϕβϕϕ⎛⎫⎛⎫+-≤≤+ ⎪ ⎪⎝⎭⎝⎭ (1-9) 式中,min z 为整车应达到的最小制动强度。
利用不等式(1-9),可以确定0.2()0.8ϕ≤≤湿滑路面(干燥路面)的极限条件下,满载工况制动力分配比的允许范围。
1.2 优化设计1.2.1 设计变量将制动力分配比β作为设计变量,根据车辆制动系统设计经验可以取初值为00.4x =。
1.2.2 目标函数附着系数在制动强度(z=0.2~0.8)范围内,应尽可能接近防止车轮抱死需要的附着系数,此时地面的附着条件发挥得越充分,汽车轴间制动力分配越好。
在实际设计时,可以分别在满载与空载的利用附着系数与制动强度的差值平方和前乘以相应的权值。
所以,当制动强度z 在0.2~0.8范围变化时,根据汽车满载时前轴和后轴的实际附着系数,利用曲线与理想曲线间差值平方和为最小建立目标函数,即0.8220.2min ()()()f r z F z z βϕϕ=⎡⎤=-+-⎣⎦∑ (6-10)1.2.3 约束条件由于汽车在任何载荷情况下都要满足ECE 制动法规要求,根据ECE 制动法规和GB 12676—1999《汽车制动系统 结构、性能和试验方法》,对汽车制动力分配要求如下所述。
对于ϕ=0.2~0.8之间的各种车辆,要求制动强度为z ≥0.1+0.85(ϕ-0.2)当z>0.2时,有10.070.85f z c ϕ+⎛⎫=- ⎪⎝⎭当0.3<z<0.45时,有2(0.05)r c z ϕ=-+另外,要求前轴利用附着系数在后轴利用附着系数的上方,即3r f c ϕϕ=-制动力分配系数的范围为0.40.6β≤≤1.3 实例仿真分析早期的汽车配备的都是无调节装置的制动系统。
本文则是通过对早期货车的制动系统前后制动力分配进行优化。
货车的原始相关数据见表1-1。
表1-1 赛车的原始相关数据根据以上理论分析,在MATLAB 中编写以下程序进行优化设计。
先建立未优化前的主函数,进行求解计算并绘制制动力分配图,具体程序如下: clear allclcl=3.950;a=2.95;b=l-a;h=1.170;G=9290*9.8;z=0.2:0.1:0.8;beta=0.4;%前后制动力分配比fai0=(l*beta-b)/h;%同步附着系数faif=beta.*z.*l./(b+z.*h);%前轴利用附着系数fair=(1-beta).*z.*l./(a-z.*h);%后轴利用附着系数Ef=b./(1-beta-faif.*h);%前轴制动效率Er=a./(1-(1-beta)+fair.*h);%后轴制动效率f1=0.1:10:40000;f2=0.5*(G/h*sqrt(b^2+4*h*l*f1/G)-(G*b/h+2*f1));%I 曲线ff2=(1-beta)./beta.*f1;%实际制动力分配曲线plot(f1,f2,f1,ff2)%绘制制动力分配曲线图grid onfai=0.7;%路面附着系数v=80;%制动初速度am=fai0*9.8;%最大制动减速度计算s=v*(0.1+0.3/2)/3.6+v^2/(25.92*am);%制动距离计算fprintf('汽车最大制动力分配比beta=%3.3f \n',beta)fprintf('汽车最大减速度am=%3.2f m/s2 \n',am)fprintf('汽车同步附着系数fai0=%3.3f \n',fai0)fprintf('汽车车速为80km/h 的制动距离distance=%3.3f \n',s)其次再建立优化函数:首先应建立目标函数zhidong_m.m:function m=zhidong_m(x);l=3.950;a=2.95;b=l-a;h=1.170;G=9290*9.8;%汽车的原始相关数据z=0.2:0.05:0.8;ii=length(z);for i=1:iifaif=x.*z.*l./(b=z.*h);fair=(1-x).*z.*l./(a-z.*h);dm=(faif-z).^2+(fair-z).^2;endm=max(dm);然后根据约束条件建立约束函数zhidong_y.m:function[c,ceq]=zhidong_y(x);for z=0.2:0.05:0.8;l=3.950;a=2.95;b=l-a;h=1.170;G=9290*9.8;faif=x.*z.*l./(b+z.*h);fair=(1-x).*z.*l./(a-z.*h);ceq=[];if z>0.3&z<0.45c(1)=fair-z-0.05;endc(2)=fair-(z+0.07)/0.85;c(3)=0.85*(faif-0.2)+0.1-z;c(4)=0.85*(fair-0.2)+0.1-z;c(5)=fair-faif;end最后建立优化设计的主函数zhidongyouhua.m,进行求解计算并绘制制动力分配图,具体程序如下:clear allclclb=0.4;ub=0.6;x0=0.4;%制动力分配比初值l=3.950;a=2.95;b=l-a;h=1.170;G=9290*9.8;[beta,y]=fmincon('zhidong_m',x0,[],[],[],[],lb,ub,'zhidong_y')z=0.2:0.1:0.8;x=beta;%前后制动力分配比fai0=(1*beta-b)/h;%同步附着系数faif=x.*z.*l./(b+z.*h);%前轴利用附着系数fair=(1-x).*z.*l./(a-z.*h);%后轴利用附着系数Ef=b./(1-*beta-faif.*h);%前轴制动效率Er=a./(1-*(1-beta)+fair.*h);%后轴制动效率f1=0.1:10:2000;f2=0.5*(G/h*sqrt(b-^2+4*h*l*f1/G)-(G*b/h+2*f1));%I曲线ff2=(1-beta)./beta.*f1;%实际制动力分配曲线plot(f1,f2,f1,ff2)%绘制制动力分配曲线图grid onfai=0.7;%路面附着系数v=80;%制动初速度am=fai0*9.8;%最大制动减速度计算s=v*(0.1+0.3/2)/3.6+v^2/(25.92*am);%制动距离计算fprintf('汽车最大制动力分配比beta=%3.3f \n',beta)fprintf('汽车最大减速度am=%3.2f m/s2 \n',am)fprintf('汽车同步附着系数fai0=%3.3f \n',fai0)fprintf('汽车车速为80km/h的制动距离distance=%3.3f \n',s)通过上述仿真得出,对制动系统优化前的数据为:汽车最大制动力分配比beta=0.400汽车最大减速度am=4.86 m/s2汽车同步附着系数fai0=0.496汽车车速为80km/h的制动距离distance=56.380。
而仿真优化后得到的结果为:汽车最大制动力分配比beta=0.490汽车最大减速度am=6.16 m/s2汽车同步附着系数fai0=0.629汽车车速为80km/h的制动距离distance=45.608。
由上述仿真结果可知,优化结果比较令人满意,制动距离缩短了10米。
利用绘制功能可以很容易得到图1-2、1-3。
图1-2图1-3对比图1-2、1-3后可以看出,优化后 曲线能够在更大范围内位于I曲线下方,比优化前更能保证前轮先抱死,属于一种稳定工况。