管式反应器
管式反应器原理
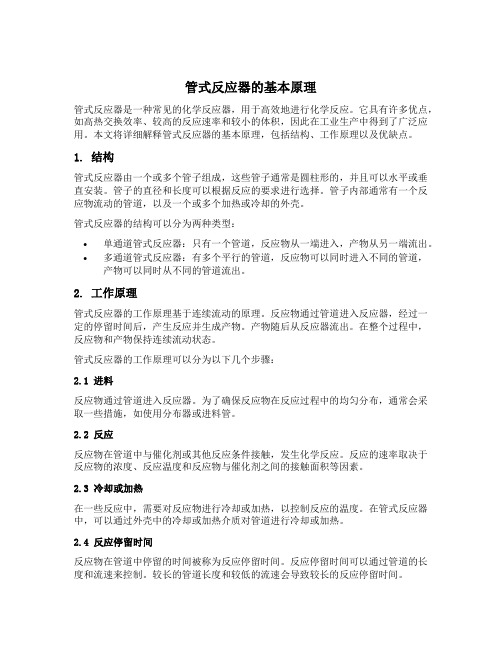
管式反应器的基本原理管式反应器是一种常见的化学反应器,用于高效地进行化学反应。
它具有许多优点,如高热交换效率、较高的反应速率和较小的体积,因此在工业生产中得到了广泛应用。
本文将详细解释管式反应器的基本原理,包括结构、工作原理以及优缺点。
1. 结构管式反应器由一个或多个管子组成,这些管子通常是圆柱形的,并且可以水平或垂直安装。
管子的直径和长度可以根据反应的要求进行选择。
管子内部通常有一个反应物流动的管道,以及一个或多个加热或冷却的外壳。
管式反应器的结构可以分为两种类型:•单通道管式反应器:只有一个管道,反应物从一端进入,产物从另一端流出。
•多通道管式反应器:有多个平行的管道,反应物可以同时进入不同的管道,产物可以同时从不同的管道流出。
2. 工作原理管式反应器的工作原理基于连续流动的原理。
反应物通过管道进入反应器,经过一定的停留时间后,产生反应并生成产物。
产物随后从反应器流出。
在整个过程中,反应物和产物保持连续流动状态。
管式反应器的工作原理可以分为以下几个步骤:2.1 进料反应物通过管道进入反应器。
为了确保反应物在反应过程中的均匀分布,通常会采取一些措施,如使用分布器或进料管。
2.2 反应反应物在管道中与催化剂或其他反应条件接触,发生化学反应。
反应的速率取决于反应物的浓度、反应温度和反应物与催化剂之间的接触面积等因素。
2.3 冷却或加热在一些反应中,需要对反应物进行冷却或加热,以控制反应的温度。
在管式反应器中,可以通过外壳中的冷却或加热介质对管道进行冷却或加热。
2.4 反应停留时间反应物在管道中停留的时间被称为反应停留时间。
反应停留时间可以通过管道的长度和流速来控制。
较长的管道长度和较低的流速会导致较长的反应停留时间。
2.5 产物收集产物在反应过程中生成,并从管道中流出。
在一些反应中,产物可能需要经过进一步的处理,如冷却、分离或纯化。
3. 优缺点管式反应器相比其他类型的反应器具有许多优点,但也存在一些缺点。
管式反应器结构、流程及仪表介绍

管式反应器结构、流程及仪表介绍全文共四篇示例,供您参考第一篇示例:管式反应器是一种常见的化工设备,用于在一定条件下进行化学反应。
它的结构、流程和仪表的设计及运用对于生产过程起着至关重要的作用。
下面我们将介绍一份关于管式反应器结构、流程及仪表方面的详细内容。
一、管式反应器的结构管式反应器通常由反应器主体、加热装置、搅拌装置和控制系统组成。
其中反应器主体是由管道、容器和支撑构件构成的,通常采用不锈钢或碳钢材料制造,以确保其具有良好的耐压性、耐腐蚀性和密封性能。
加热装置主要包括外部加热方式和内部加热方式,以确保反应物在适当的温度下进行化学反应。
搅拌装置则能够保证反应物在反应器内充分混合,使反应过程更加均匀。
控制系统则通过传感器、执行器和控制器来监控和调节反应器的各项参数,从而确保反应过程的安全、稳定和高效。
二、管式反应器的流程管式反应器的流程通常包括加料、反应、卸料和清洗等步骤。
需要将反应物通过管道加入反应器主体中,然后通过加热装置使反应物达到所需的温度。
在反应过程中,搅拌装置将反应物进行充分混合和反应,直至达到反应末态。
接着,对反应产物进行卸料处理和清洗反应器,清除残留物和污垢,为下一轮的生产做好准备。
三、管式反应器的仪表介绍管式反应器的仪表通常包括温度传感器、压力传感器、液位传感器、流量计和控制器等。
温度传感器用于实时监测反应器内部的温度变化,确保反应温度的稳定性。
压力传感器用于监测反应器内部的压力变化,保证反应过程的安全性。
液位传感器用于监测反应物的液位变化,确保反应器内反应物的稳定供应和控制。
流量计用于测量反应物的流量,控制反应物的进出流程。
控制器则根据传感器所得的数据来对反应器进行自动控制,以确保反应过程的精准性和稳定性。
总结:管式反应器作为一种重要的化工设备,在化学生产过程中扮演着不可替代的角色。
正确的结构设计、合理的操作流程以及精准的仪表控制,对于保证生产过程的安全、高效和稳定至关重要。
管式反应器.
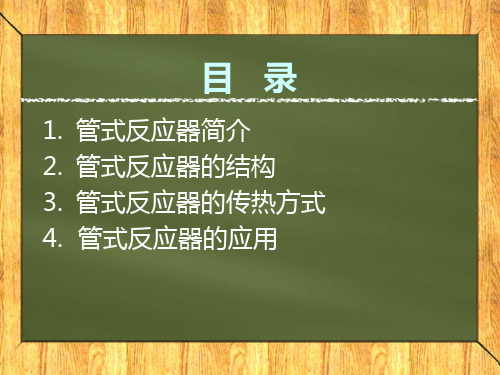
流程说明
一、 来自界区的烯烃在液位控制下进入D201 烯烃原料罐,经烯烃回收单元回收的烯烃也 送入D201,混合后的烯烃经进料泵 P200A/B 送进反应器系统。
二、来自界区的催化剂在流量控制下,进入 第一个环管反应器 R201。来自界区的氢气在 流量控制下,分两路分别进入R201和R202。
三、两个环管反应器内浆液的温度是通过 其反应器夹套中闭路循环的脱盐水系统 来控制的。
管式反应器传热方式
烟道气加热: 当反应的温度要求较高时,一般利用煤气, 天然气,石油加工废气或燃料油等燃烧 时产生的高温烟道气作为热源通过辐射 传热直接:聚丙烯的生产 环管聚丙烯通过催化剂的引发,在一 定温度和压力下烯烃单体聚合成聚烯烃, 聚合后的浆液经蒸汽加热后,高压闪蒸, 分离出的烯烃经烯烃回收系统回收循环 使用,聚合物粉末部分送入下一工段。
目 录
1. 2. 3. 4. 管式反应器简介 管式反应器的结构 管式反应器的传热方式 管式反应器的应用
管式反应器简介
在化工生产中,常常把反应器长度远大于其直 径即高径比大于100的一类反应器统称为管式反 应器。管式反应器是化工生产中应用较多的一种 连续操作反应器,在20 世纪40 年代起开始开发 应用。主要特点:比表面积大,容积小,返混少, 且能承受较高的压力,反应操作易于控制,但反 应器的压降较大,动力消耗大。 应用举例:乙酸裂解制乙烯酮,乙烯高压 聚合,对苯二甲酸酯化,椰子油加氢制脂肪醇等。
3.盘管式反应器 将管式反应器做成 盘管的形式,设备紧 凑,节省空间,但检 修和清刷管道比较麻 烦。
5
4. U形管式反应器
如图所示,U形管式反 应器的管内设有多孔挡 板或搅拌装置,以强化 传热与传质过程。U形 管的直径大,物料停留 时间长,可应用于反应 速率较慢的反应。
管式反应器
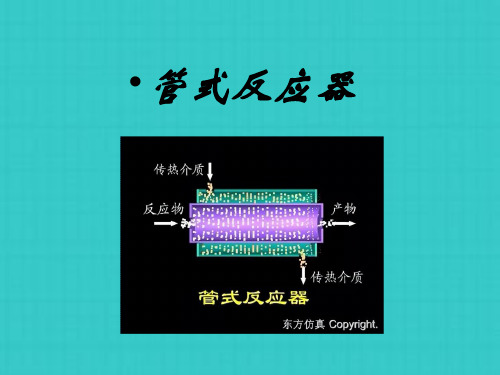
(5)多管并联管式反应器
多管并联结构的管式 反应器一般用于气固 相反应,例如气相氯 化氢和乙炔在多管并 联装有固相催化剂的 反应器中反应制氯乙 烯,气相氮和氢混合 物在多管并联装有固 相铁催化剂的反应器 中合成氨。
管式反应器的加热或冷却可采用各种方式
(1)管或夹套传热,如图3.1、3.2(a)、3.2(b)等所示的反应 器,均可用套管或夹套传热结构。
管式反应器的分类
管式反应器是应用较多的一种连续操作 反应器,常用的管式反应器有以下几种 类型:
(1)水平管式反应器 图3.1给出的是进行气相或均 液相反应常用的一种管式反应器, 由无缝钢管与U形管连接而成。这种结构易于 加工制造和检修。高压反应管道的连接采用标准 槽对焊钢法兰,可承受1600-10000kPa压力。如 用透镜面钢法兰,承受压力可达10000-20000kPa。 图3.1
图3.8 弯管
管式反应器的结构
三,密封环 套管式反应器的密封环为透镜环。
透镜环有两种形状。一种是圆柱形的, 另一种是带接管的T形透镜环,如图3.9. 圆柱形透镜环用反应器内管同一材质制 成。带接管的T形透镜环是安装测温、测 压元件用的。
图3.9 带接管的T形透镜环
管式反应器的结构
四,管件 反应器的连接必须按规定的紧固力矩进行。所以对法兰、
炉型 目前国际上应用较广的管式裂解炉有短停留时间炉、 超选择性炉、林德- 西拉斯炉、超短停留时间炉。从而实现了 0.3s以下的短停留时间。
一,管式裂解炉
应加用热管 均式匀反且应热器强短一度停流高化,留床从时造而粒实间器现炉生了产0. 球粒状磷酸二铵的工艺流程图如下: SRT-Ⅰ型由是等径鲁管姆组成斯;公司在60和70年代开发的炉 (晶2种)颗型管粒式(由反晶S应种R器T料)具仓有下,容星有积形小加三、料种比器表加:面即入大流S、化R单T床-位,Ⅰ容流积、化的床S传出R热T料-面由1积振Ⅱ大动,输特送别机适进用行于控热制效。应较大的反应。 裂解产及物S离R开T反-Ⅲ应管型后(立即图进3入.急1冷1)锅炉,骤炉冷,管以比中止表反面应。较大, 而内后壁者 粘其的结中造,粒从S过而RT程影-是响Ⅱ在生又氨产化的可粒连分化续机进为中行高进。行选,择存在性返(料H比S大)和、产高品生粒度不均匀、氨逸出率较大等缺点,而且造粒物料极易在氨化粒化机 它包括产直能管、力弯管(、H密C)封两环、种法。兰及SR紧T固-件Ⅰ、型温度由补等偿器径、管传热组夹套及联络管和机架等几部分。 管 管式式反反成应 应;器 器的 可S加 用RT热 于-或 气Ⅱ冷 相及却、可 均S采 液RT用 相-各 、Ⅲ种 非则方 均式 液为相前、气细液后相、粗气的固相变、径固相等反应。 反应管管管,径为四2股~7平in(行1in进等于料2.以强化前期加热,缩短 反管应式器 反停出应留口器与的时一加间短热管或和以冷后螺却纹可期连采降接用,各低并种烃把方物式分料压出口,内从径缩而至提Ø7高选 反应器择机性架用。桥按梁钢照焊生接成产整能体。力的要求,每台炉可装 图3.11 三种SRT炉的反应管排列方式 裂(3)解短炉路1管6电、悬流吊加2在4热或辐,射将3室2低个中电央压管。、组大电,流增的电加源乙直接烯通产到管率壁。上,裂使解电能转变为热能。 用于烃产类物裂解离制开乙烯反及应其相管关后产品迅的速一种进生入产设一备种,为专目用前世急界冷上大型石油化工厂所普遍采用。 管4-带式接反锅管应炉的器T一(形种U透S呈X镜管)环状,;、由长径于比三很大种的反连续应操管作反采应用器。了不同 每一个的盘管管是径由及许多排半列径不方同式的半,圆其形管工子艺相连特接性成螺差旋异形式较,大螺旋中央留出Φ400mm的空间,便于安装和检修。
管式反应器结构、流程及仪表介绍
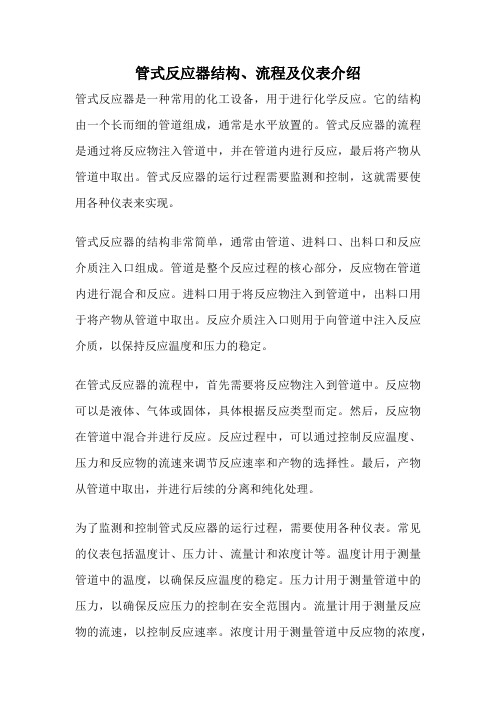
管式反应器结构、流程及仪表介绍管式反应器是一种常用的化工设备,用于进行化学反应。
它的结构由一个长而细的管道组成,通常是水平放置的。
管式反应器的流程是通过将反应物注入管道中,并在管道内进行反应,最后将产物从管道中取出。
管式反应器的运行过程需要监测和控制,这就需要使用各种仪表来实现。
管式反应器的结构非常简单,通常由管道、进料口、出料口和反应介质注入口组成。
管道是整个反应过程的核心部分,反应物在管道内进行混合和反应。
进料口用于将反应物注入到管道中,出料口用于将产物从管道中取出。
反应介质注入口则用于向管道中注入反应介质,以保持反应温度和压力的稳定。
在管式反应器的流程中,首先需要将反应物注入到管道中。
反应物可以是液体、气体或固体,具体根据反应类型而定。
然后,反应物在管道中混合并进行反应。
反应过程中,可以通过控制反应温度、压力和反应物的流速来调节反应速率和产物的选择性。
最后,产物从管道中取出,并进行后续的分离和纯化处理。
为了监测和控制管式反应器的运行过程,需要使用各种仪表。
常见的仪表包括温度计、压力计、流量计和浓度计等。
温度计用于测量管道中的温度,以确保反应温度的稳定。
压力计用于测量管道中的压力,以确保反应压力的控制在安全范围内。
流量计用于测量反应物的流速,以控制反应速率。
浓度计用于测量管道中反应物的浓度,以控制产物的选择性。
管式反应器是一种常用的化工设备,用于进行化学反应。
它的结构简单,流程清晰,并通过使用各种仪表来实现监测和控制。
通过合理的操作和控制,管式反应器可以实现高效的化学反应,并产生优质的化学产品。
第四章管式反应器

流体相中的反应物需向面体催化剂表面上传递,生成的反应产 物又需作反方向传递。 与化学反应进行的同时必然产生一定的热效应,于是固体催化 剂与流体间还存在着热量传递。 那么,固体催化剂上反应组分的浓度与流体相将是不同的;固 体催化剂的温度也与流体的温度不同。 如果两者间的传质和传热的速率很大,则两者的浓度及温度的 差异将很小。虽为多相催化反应,若忽略这些差异,则在动力 学表征上与均相反应并无两样。所以,根据这种简化假定而建 立的模型称为拟均相模型。 拟均相模型:忽略相间传递对反应的影响的模型。
已不足以描述整个反应过程,需分别对各关键组分作 物料衡算,以获得管式反应器的设计方程组。 如果在反应器中存在K个独立反应,就需要确定K个 组分来描述反应系统的状态,因此就需要可建立 K个 物料衡算方程。 dFi
Vr 0, Fi Fi 0 , i 1,2,K 同单一反应一样,只要将i组分的摩尔流量与转化速 率变化为转化率的函数,就可积分求出反应器体积。 实际反应过程中更关心反应的收率与选择性。
即所有流体粒子均以相同速度从进口向出口运动,就像一个活
塞一样有序地向前移动,故称之为活塞流。
3
活塞流假设( Plug (Piston) Flow Reactor 简称PFR )
返混(Back mixing) :在反应器中停留时间不同的流体粒子之间的
混合。返混又称逆向混合。 所谓逆向混合指的是时间概念上的逆向,既然活塞流假设径向流速 分布均匀,那么在同一横截面上所有流体粒子的停留时间必然相同, 自然不存在逆向混合。 活塞流模型还假设在流体流动的方向上即轴向上不存在流体的返混, 就整个反应器而言,如符合活塞流假设,则同一时刻进入反应器的 流体粒子必定在另一时刻里同时离开,即所有流体粒子在反应器内 的停留时间相同。(间歇反应器也是如此,因此间歇反应器中也不 存在返混) 活塞流反应器虽然不存在返混,但由于流体的主体流动和发生化学 反应的结果,各个横截面上反应物料的浓度和温度则可以是各不相 同的 。
第四章管式反应器_反应工程上课简版

4.3 管式与釜式反应器反应体积的比较
图分析比较
(a)1/-RA随xA的增大呈单调上升 (b)1/-RA随xA的增大呈单调上升
(c)1/-RA具有极小值
4.3 管式与釜式反应器反应体积的比较
比较管式与釜式反应器的收率
(a) 选择性随转化率的增加而减小 (b) 选择性随转化率的增加而增大
习题
4.7 拟设计一等温反应器进行下列液相反应:
A B R, rR k1C AC B
2 2 A S , rS k2C A
目的产物为R,且R与B极难分离。试问: (1)目的产物瞬时选择性表达式? (2)在原料配比上有何要求? (3)若采用活塞流反应器,应采用什么样的加料方式? (4)如用半间歇反应器,应采用什么样的加料方式?
4.4 循环反应器
Vr (1 )Q0c A0 X Af
1
X Af
dX A ( A )
0, XA0 0
, X A0 X Af
当ψ ≥25时,即可认为反应器达到了 全混状态。
4.5 变温管式反应器
活塞流反应器的热量衡算
活塞流反应器的热量衡算示意图 控制体:反应体积为dVr的微元段,微元段长度为dZ, 转化率的变化为dxA、温度变化为dT。
管式反应器的热量衡算
------管式反应器轴向温度分布方程
dT GwA0 (H r )Tr dX A U Gcpt 4 (TC T ) dZ MA dZ dt
------管式反应器中反应温度与转化率的关系
绝热管式反应器
wA0 (H r )Tr dT dX A M Ac pt
Q0C A0 X Af
A
多釜串联全混流反应器体积:
管式反应器

(1)水平管式反应器 图3.1给出的是进行 气相或均液相反应常用的一种管式反应 器,由无缝钢管与U形管连接而成。这 种结构易于加工制造和检修。高压反应 管道的连接采用标准槽对焊钢法兰,可 承受1600-10000kPa压力。如用透镜面 钢法兰,承受压力可达10000-20000kPa
(2)立管式反应器
图3.2给出几种立管式反应 器。图3.2(a)为单程式 立管式反应器,图3.2(b )为带中心插入管的立管 式反应器。有时也将一束 立管安装在一个加热套筒 内,以节省安装面积,如 图3.2(c)所示。 立管式反应器被应用于 液相氨化反应、液相加氢 反应、液相氧化反应等工 艺中。
(a)单程式
(b)中心插入管式
管 式 反 应 器 的 特 点
(4)管式反应器适用于大型化和连续 化的化工生产。 (5)和釜式反应器相比较,其返混较 小,在流速较低的情况下,其管内流 体流型接近与理想流体。 (6)管式反应器既适用于液相反应, 又适用于气相反应。用于加压反应尤 为合适。
此外,管式反应器可实现分段温度控 制。其主要缺点是,反应速率很低时 所需管道过长,工业上不易实现。
邻硝基氯苯胺化
图3.16 用管式反应器生产邻硝基苯胺的工艺流程图 1-高压计量泵;2-混合器;3-预热器; 4-高压管式反应器;5-减压阀;6-氨蒸发器; 7-脱氨塔;8-脱氨塔釜
邻硝基氯苯胺化
图3.16即是用管式反应器生产邻硝基苯胺的 流程图,用高压计量泵分别将已配好的浓氨水 和熔融的邻硝基氯苯按15:1的物质的量之比 连续送入管式反应器中,管式反应器可采用短 路电流或道生油加热,反应物料在管道中呈湍 流状态,控制反应温度在225-230℃,物料在 反应管道中的停留时间约20分钟。通过减压阀 后已降为常压的反应物料,经脱氨装置回收过 量的氨,再经冷却结晶和离心过滤,即得到成 品邻硝基苯胺。
- 1、下载文档前请自行甄别文档内容的完整性,平台不提供额外的编辑、内容补充、找答案等附加服务。
- 2、"仅部分预览"的文档,不可在线预览部分如存在完整性等问题,可反馈申请退款(可完整预览的文档不适用该条件!)。
- 3、如文档侵犯您的权益,请联系客服反馈,我们会尽快为您处理(人工客服工作时间:9:00-18:30)。
管式反应器
• 一种呈管状、长径比很大的连续操作反应器。这种反应器 可以很长,如丙烯二聚的反应器管长以公里计。反应器的 结构可以是单管,也可以是多管并联;可以是空管,如管 式裂解炉,也可以是在管内填充颗粒状催化剂的填充管, 以进行多相催化反应,如列管式固定床反应器。通常,反 应物流处于湍流状态时,空管的长径比大于50;填充段长 与粒径之比大于100(气体)或200(液体),物料的流动可 近似地视为平推流(见流动模型)
(1)水平管式反应器 由单管(直管或盘管) 连续或多根平行排列的 管子组成。一般设有套管或壳管式换热装置。 操作时,物料自一端连续加入,在管中连续 反应,从另一端连续流出,便达到了要求的 转化。
(2) 立管式反应器 (a) 单程式立管式反应器; (b) 夹套式立管式反应器,其特点是将一束立 管安装在一个加热套筒内,以节省地面。 立管式反应器被应用于液相氨化反应、液 相加氢反应、液相氧化反应等工艺中。
(3) 盘管式反应器 >盘管式反应器是将管式反应器做成盘管的形 式,设备紧凑, 节省空间,但检修和清刷管道比较麻烦。>盘 管式反应器由许多水平盘管上下重叠串联而 成。每一个盘管是由许多半径不同的半圆形 管子相连接成螺旋形式,螺旋中央留出直径 400 mm的空间,便于安装和检修。
(4) U 形管式反应器 上图是一种内部设有搅拌和电阻加热装置的U 形管式反应器。U形管式反应器的管内设有挡 板或搅拌装置,以强化传热与传质过程。 U形管的直径大,物料停留时间增长,可以应 用于反应速率较慢的反应。