管式反应器课程设计
反应器设计课程设计

反应器设计课程设计一、教学目标本课程旨在通过学习反应器设计的基本原理和方法,使学生掌握化学反应器的设计和分析能力。
具体目标如下:1.掌握化学反应器的基本类型及其工作原理。
2.了解反应器设计的主要参数和计算方法。
3.理解反应器操作条件对反应结果的影响。
4.能够运用反应器设计的基本理论解决实际问题。
5.能够独立完成反应器设计的相关计算和分析。
6.能够阅读和理解反应器设计的英文文献。
情感态度价值观目标:1.培养学生的创新意识和科学精神。
2.增强学生对化学工程学科的兴趣和热情。
3.培养学生关注社会发展和环境保护的责任感。
二、教学内容本课程的教学内容主要包括以下几个部分:1.反应器类型的介绍和分析。
包括釜式反应器、管式反应器、固定床反应器、流动床反应器等。
2.反应器设计的基本参数和计算方法。
如反应器的体积、压力、温度、流量等。
3.反应器操作条件对反应结果的影响。
如温度、压力、搅拌速度等。
4.反应器设计的实例分析。
通过具体案例,使学生掌握反应器设计的过程和方法。
三、教学方法本课程将采用多种教学方法,以激发学生的学习兴趣和主动性。
1.讲授法:通过讲解反应器设计的基本原理和概念,使学生掌握相关知识。
2.讨论法:通过分组讨论,引导学生深入思考和理解反应器设计的实际问题。
3.案例分析法:通过分析具体案例,使学生学会运用所学知识解决实际问题。
4.实验法:通过实验操作,使学生了解反应器的工作原理和操作方法。
四、教学资源本课程将采用教材《化学反应器设计》为主要教学资源。
同时,还将利用参考书、多媒体资料、实验设备等辅助教学资源。
这些资源将有助于支持教学内容和教学方法的实施,丰富学生的学习体验。
五、教学评估为了全面、客观地评估学生的学习成果,本课程将采用以下评估方式:1.平时表现:通过课堂参与、提问、小组讨论等方式,评估学生的参与度和积极性。
2.作业:布置相关的反应器设计练习题,评估学生对知识的理解和运用能力。
3.考试:定期进行反应器设计相关的考试,评估学生的知识掌握和应用能力。
4-管式反应器
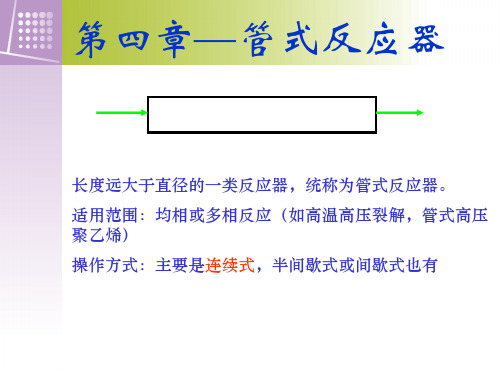
4.2 等温管式反应器的设计
1. 单一反应 2. 复合反应 3. 拟均相模型
原料以流量Q0从顶部连续加入,在底 部流出。反应器为定态操作,管式反应 Q0
器中,物料浓度随轴向位置而变,因此,
取微元体积dVr为控制体积
4.2 等温管式反应器的设计
Q0 进入量=排出量+反应量+累积量
Fi ( Fi dFi ) (i )dVr 0
4.5 变温管式反应器
1、管式反应器的热量衡算式
4.5 变温管式反应器
设流体在dVr中的温变为dT,取Tr为基准温度,则有:
dH A Hr Tr SdZ GCpt SdT
G为反应流体的质量速度 微元体积与环境交换的热量为
反应热 多个反应? ij rj H r j j 1
P为目的产物
a、E1<E2, E3>E4, 由低到高的温度序列 b、E1>E2, E3>E4, 保持高温 c、E1<E2, E3<E4, 保持低温 d、E1>E2, E3<E4, 由高到低的温度序列
例4.9
理想反应器的组合
理想反应器的组合
理想反应器的组合
理想反应器的组合
理想反应器的组合
本章小结
4.1 理想流动模型
B 全混流模型
1.基本假定: 径向混合和轴向混合都达到最大 2.特点: 反应物系的所有参数在径向上均一,轴向上也均一,即在 整个反应器内不存在温度和浓度差
根本区别:活塞流 无返混 全混流 返混程度最大
Plug flow reactor (PFR) Mixed flow reactor (MFR) 或 Continuous stirred tank Reactor(CSTR)
3-3平推流管式反应器-化学反应工程
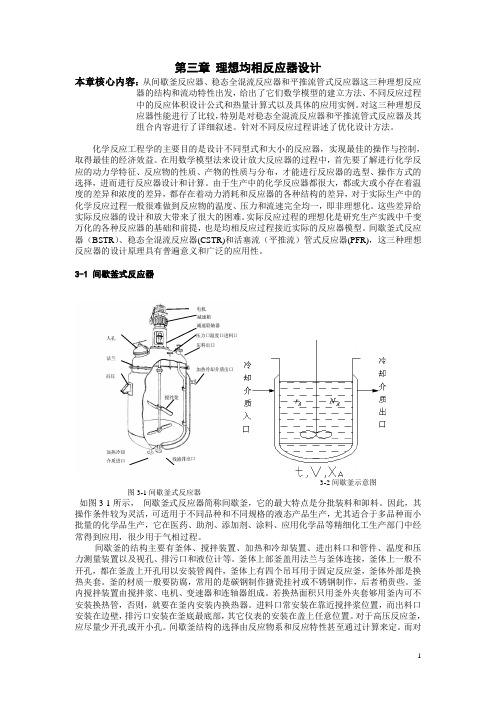
第三章理想均相反应器设计本章核心内容:从间歇釜反应器、稳态全混流反应器和平推流管式反应器这三种理想反应器的结构和流动特性出发,给出了它们数学模型的建立方法、不同反应过程中的反应体积设计公式和热量计算式以及具体的应用实例。
对这三种理想反应器性能进行了比较,特别是对稳态全混流反应器和平推流管式反应器及其组合内容进行了详细叙述。
针对不同反应过程讲述了优化设计方法。
化学反应工程学的主要目的是设计不同型式和大小的反应器,实现最佳的操作与控制,取得最佳的经济效益。
在用数学模型法来设计放大反应器的过程中,首先要了解进行化学反应的动力学特征、反应物的性质、产物的性质与分布,才能进行反应器的选型、操作方式的选择,进而进行反应器设计和计算。
由于生产中的化学反应器都很大,都或大或小存在着温度的差异和浓度的差异,都存在着动力消耗和反应器的各种结构的差异,对于实际生产中的化学反应过程一般很难做到反应物的温度、压力和流速完全均一,即非理想化。
这些差异给实际反应器的设计和放大带来了很大的困难。
实际反应过程的理想化是研究生产实践中千变万化的各种反应器的基础和前提,也是均相反应过程接近实际的反应器模型。
间歇釜式反应器(BSTR)、稳态全混流反应器(CSTR)和活塞流(平推流)管式反应器(PFR),这三种理想反应器的设计原理具有普遍意义和广泛的应用性。
3-1 间歇釜式反应器3-2间歇釜示意图图3-1间歇釜式反应器如图3-1所示,间歇釜式反应器简称间歇釜,它的最大特点是分批装料和卸料。
因此,其操作条件较为灵活,可适用于不同品种和不同规格的液态产品生产,尤其适合于多品种而小批量的化学品生产,它在医药、助剂、添加剂、涂料、应用化学品等精细化工生产部门中经常得到应用,很少用于气相过程。
间歇釜的结构主要有釜体、搅拌装置、加热和冷却装置、进出料口和管件、温度和压力测量装置以及视孔、排污口和液位计等。
釜体上部釜盖用法兰与釜体连接,釜体上一般不开孔,都在釜盖上开孔用以安装管阀件,釜体上有四个吊耳用于固定反应釜,釜体外部是换热夹套。
任务5连续管式反应器设计
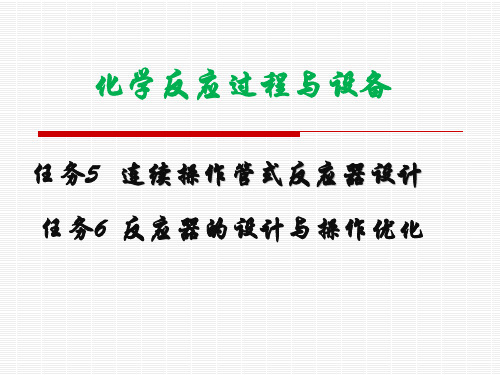
y A0
nA0 nt 0
为A组分占反应开始时总物
质的摩尔分数
恒温变容管式反应器计算公式
化学反应
速率方程
计算式
A
P(零级) -rA=k
VR xA
FA0
kA
A
P(一级) -rA=kCA
VR (1 A yA0 ) ln(1 xA ) A yA0 xA
换句话说,若反应器体积相同,连续操作管式反应 器所达到的转化率比连续操作釜式反应器更高。
27
1.间歇操作釜式反应器和连续操作管式反应器比较
对间歇操作釜式反应 器,其反应时间为:
对连续操作管式反应 器,其反应时间为:
m
CA0
xAf 0
dxA rA
p
VRp V0
xAf
CA0
特征:同一截面上不同径向位置的流体特性(T,CA) 是一致的。所有物料在反应器中的停留时间相同, 即 无返混.操作时,反应器内的状态只随轴向位置变, 不随时间变
2
一、 基础设计方程式
连续操作管式反应器具有以下特点: 1.在正常情况下,它是连续定态操作,故在反应
器的各处截面上,过程参数不随时间而变化; 2.反应器内浓度、温度等参数随轴向位置变化,
复合反应
反应器 的大小
影响
过程的 经济性
影响
产物分布 (选择性、收率等)
单一反应
复合反应
26
(一)简单反应的反应器生产能力的比较
简单反应是指只有一个反应方向的过程。其优化目 标只需考虑反应速率,而反应速率直接影响反应 器生成能力。
即:对简单反应,单位时间、单位体积反应器所能 得到的产物量,为达到给定生产任务所需反应器 体积最小为最好。
精细化工过程与设备教案第三章管式反应器
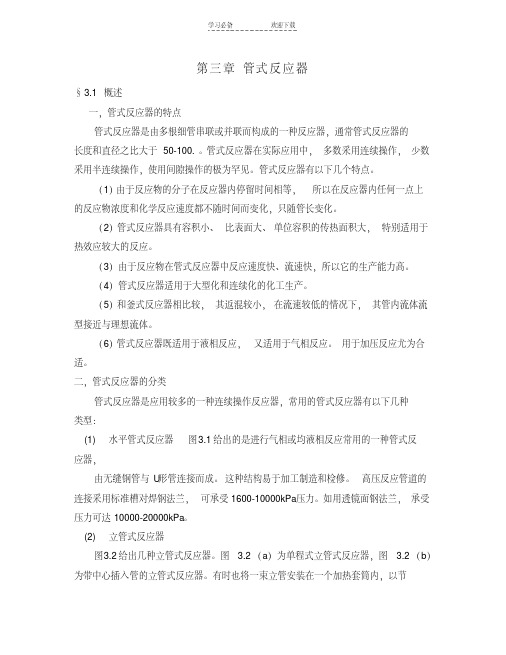
学习必备
欢迎下载
管径及排列方式,其工艺特性差异较大(见表)。 SRT 型炉是目前世界上大型乙烯装置中应用最多的炉型。中国的燕山石油化工
公司,扬子石油化工公司和齐鲁石油化工公司的 300kt 乙烯生产装置均采用此种裂 解炉。
超选择性裂解炉 简称 USC炉。每组四根管, 它是美国斯通-韦伯斯特公司在 70年代开发的一种炉 型,炉子的基本结构与 SRT炉大体相同, 但反应管由多组 W型变径管组成 (图 3.12 ), 每组四根管,前两根材质为 HK-40,后两根为 HP-40,全部离心浇铸和内部机械加工 平整,管径由小到大,一般为 50~ 83mm,长为 10~ 20m。按照生产能力的要求,每台 炉可装 16、24或32个管组,裂解产物离开反应管后迅速进入一种专用急冷锅炉 (USX), 每两组反应管配备一个急冷锅炉。 USC 炉的主要技术特性为 : ①采用多组小口径管并双面辐射加热,炉管比表面较 大。加热均匀且热强度高,从而实现了 0.3s 以下的短停留时间。②采用变径管以降 低过程的烃分压。短的停留时间和低的烃分压使裂解反应具有良好的选择性。 USC炉单台炉子乙烯年生产能力可达 40kt 。中国大庆石油化工总厂以及世界上 很多石油化工厂都采用它来生产乙烯及其相关产品。 林德-西拉斯裂解炉 简称 LSCC炉。 是林德公司和西拉斯公司在 70年代初合作研制而成的一种炉型。 炉子的基本结构与 SRT炉相似。可耐 1050℃高温。炉膛中央吊装构形特殊的反应管 (图 3.13 ),一般采用主要成分为含镍 20%、铬25%的 HK-40合金钢作为裂解反应管材料, 每组反应管是由 12根小口径管 (前 8根组成 4对平列管, 后 4根组成两对平列管) 以及 4根中口径管 (由 4根管组成两对平列管) 和一根大口径管组成, 管径为 6~15cm,管 总长 45~ 60m。裂解产物离开反应管后立即进入急冷锅炉骤冷。 急冷锅炉随裂解炉型 而有所不同。 LSCC 炉反应器的特点是原料入口处为小口径管双排双面辐射加热,物料能迅速 升温,缩短停留时间,后继的反应管则为单排双面辐射,管径采取逐管增大方式以 达到降低烃分压的目的。 物料在反应管中的停留时间为 0.2 ~ 0.4s 。短停留时间和低 烃分压使裂解反应具有较高的选择性,乙烯产率高。
管式反应器
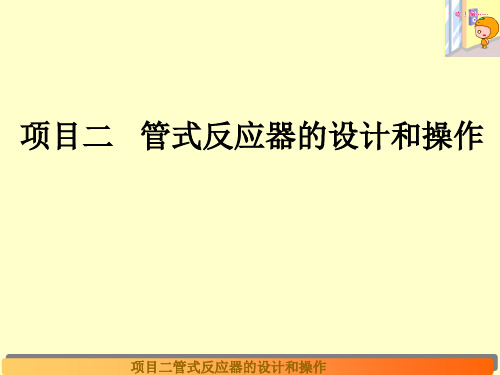
2.盘管式反应器
盘管式反应器
盘管式反应器是将管式反应器做成盘管的形式,设备紧凑, 节省空间,但检修和清刷管道比较麻烦。 盘管式反应器由许多水平盘管上下重叠串联而成。每一个 盘管是由许多半径不同的半圆形管子相连接成螺旋形式,螺 旋中央留出φ400 mm的空间,便于安装和检修。
项目二管式反应器的设计和操作
相关知识
一、平推流反应器
连续操作管式反应器可近似看成理想置换反应器,简称 PFR。反应物和产物都处于连续流动的状态,物料在反应器内 没有积累,系统中的浓度、温度、压力等参数在一定位置处是 定值,即不随时间而变。但在反应器中不同位置这些参数是不 同的。
操作过程:
反应器内的浓度变化:
项目二管式反应器的设计和操作
Vt V0 (1 y A0 A x A )
1 xA c A c A0 1 y A0 A x A
Ft F0 (1 y A0 A x A )
p A p A0 1 xA 1 y A0 A x A
1 xA y A y A0 1 y A 0 A x A
得:
xA VR dxA c A0 0 kc2 (1 x ) 2 V0 A0 A
VR xA V0 kcA0 (1 x A )
V0 x A VR V0 kcA0 (1 x A )
项目二管式反应器的设计和操作
求解方法:解析法、图解积分法、数值积分法
平推流反应器图解计算示意图
项目二管式反应器的设计和操作
解:由于 c A0 c B 0 ,并且是等摩尔反应
所以反应速率方程式为
(rA ) kcAcB kc
2 A
反应在理想间歇反应器内所需反应时间为
《化工反应原理与设备》课件—03管式反应器

结论:( 图3-8)
单 1、n>0:xA相同,则VPFR<VCSTR
个
vR相同时则XA(PFR)>XA(CSTR)
反 2、当xA低时VPFR/VCSTR→1
应
当xA高时VPFR/VCSTR ↓ 随xA↑,返混的影响↑
器
即过程要求的转化率越高,返混的影响越大
3、 xA一定时:n ↑ VPFR/VCSTR→ ↓
dxA (rA )
dc c A f
A
cA0 (rA )
等 解析法:
容
一级反应:
c
11 ln
k 1 xAf
1 ln cA0 k cAf
VR V0 c
二级反应: c
xAf
1( 1
kcA0 (1 xAf ) k cAf
1) cA0
等温管式反应器的计算
图解法:动力学方程无法用函数表达
等 温 等
c
,
程
Ft MCpdT (rA)(Hr )A,T KdA(T TS ) 0
物衡:
(rA )dVR FA0dxA
FtMCpdT FA0dxA(Hr )A,T KdA(T TS ) 0
变温管式反应器的计算
绝热操作即与外界没有热交换。则:KdA(T TS ) 0
绝
Ft MCpdT FA0dxA(Hr )A,T
解:对于二级反应
c
VR V0
x Af kcA0 (1 xAf )
0.9 3.283105 4 (1 0.9)
6.85104 s 19.04h
物料的处理量:
V0
FA0 c A0
2400 / 24 /146 4
0.171m3 / h
反应器体积: VR V0 C 0.171 19.04 3.26m3
管式反应器
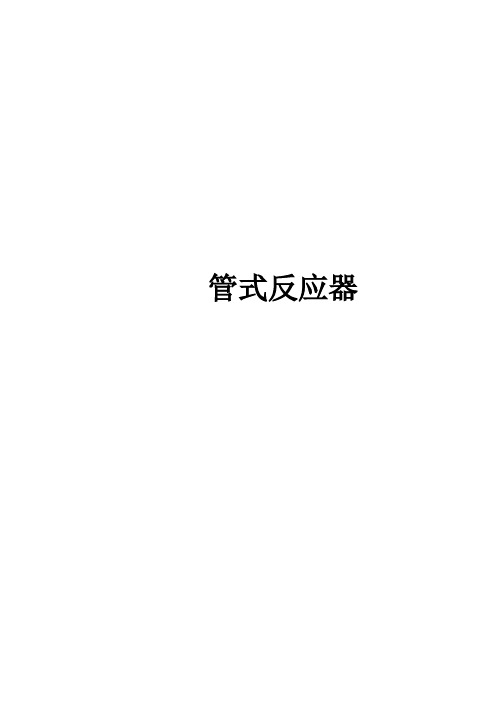
管式反应器1. 管式反应器的设计1.1 概述在整个工艺流程中反应器是最重要的一个设备,它的设计是否成功代表着整个工艺的是否成功,所以反应器的设计至关重要。
整个工艺中有两个反应器,都是管式反应器,这是我们在众多的反应器类型中挑选的最符合我们要求的反应器,我们现在拿第一个管式反应器作为例子进行设计,另一个反应器的设计数据见附表。
1.2反应器的设计1.2.1工艺计算a.选择反应器的类型两流体温度变化情况:热流体进口温度200℃,出口温度160℃。
冷流体(循环水)进口温度30℃,出口温度50℃。
该反应器用循环水冷却热的流体,因此初步确定选用管式反应器。
我们选择反应物走管程,这样有利于反应。
对于换热管,我们选择不锈钢管,尺寸为Φ16mm×3mm,若其流速太低,将会加快油层增长速度,使反应器的热流量下降,故管内流速取1.3m/s。
b.物性数据的确定(1)壳程(水)的定性的温度为:T=(30+50)/2=40℃查得水在40℃时的有关物性数据如下密度 ρ0=994.4kg/m3定压比热容C p=4.134KJ/Kg导热系数 λ0=0.601W/mºC粘度μ0=0.955mPa.s(2)管程(碳酸乙烯酯)的定性的温度为:T=(200+160)/2=180℃查得在70℃时的有关物性数据如下密度 ρi=1121.8kg/m3定压比热容C i=5.632KJ/Kg导热系数 λi=0.14W/mºC粘度μi=1.8mPa.sc.计算总传热系数热流量Q0= m0C oΔt o=153103.127×5.632×(200-160) =34491072.45kg/h=9593.45kw平均传热温差∆t m′=(Δt1-Δt2 )/ln (Δt1/Δt2) =[(200-160) -(50-30 )]/ ln[(200-160 )/ (50-30 )] =28.85℃水用量 W i =Q 0/( C i ∆t i )=34491072.45/[4.134×(50-30)]=416257.2kg/s管程传热系数:Re =d i u i ρi μi ⁄=0.02×1.3×1121.80.0018=21658.14i =0.023 λi d i(d i u i ρi μi ⁄)0.8(c p u i / λi )0.4=9850.4壳程传热系数: 假设壳程的传热系数0=300/(m 2•°C )污垢热阻si R =0.000344m 2•°C/W ,so R =0.000172m 2•°C/W管壁的导热系数=45 W/(m •°C ) K =1d o i di +bd 0d m 0+R SO +10+R si d o d i=10.0259850×0.02+0.0025×0.02545×0.0225+0.000172+1300+0.000344×0.0250.02=69.72 [w/(m.℃)] d.计算传热面积S′=Q ∆tk =9593.4528.85×69.72=17147.61m 2考虑15%的面积裕度,S=1.15×S ’=1.15×17147.61=114317.38(m2) e.工艺结构尺寸的计算 (1)管径和管内流速Φ16×3传热管(不锈钢),取管内流速i u =1.3m/s (2)管程速和传热管数 n s =V0.785×u×d i2=4162533600994.40.785×0.012×1.3=1139.40≈1140(根)L =S 3.14d 0n 0=2988.833.14×0.016×285=53m按单程设计,传热管过长,宜采用多管程结构。
- 1、下载文档前请自行甄别文档内容的完整性,平台不提供额外的编辑、内容补充、找答案等附加服务。
- 2、"仅部分预览"的文档,不可在线预览部分如存在完整性等问题,可反馈申请退款(可完整预览的文档不适用该条件!)。
- 3、如文档侵犯您的权益,请联系客服反馈,我们会尽快为您处理(人工客服工作时间:9:00-18:30)。
化学化工学院化工专业课程设计设计题目:管式反应器设计化工系化工专业课程设计——设计文档质量评分表(100分)评委签名: 日期:目录绪论 .........................................................错误!未定义书签。
1设计内容与方法介绍..........................................错误!未定义书签。
反应器设计概述............................................错误!未定义书签。
设计内容..................................................错误!未定义书签。
生产方法介绍..............................................错误!未定义书签。
反应器类型特点............................................错误!未定义书签。
反应器选择及操作条件说明..................................错误!未定义书签。
2工艺计算....................................................错误!未定义书签。
主要物性数据..............................................错误!未定义书签。
计算,确定管长,主副反应收率.............................错误!未定义书签。
管数计算..................................................错误!未定义书签。
3压降计算公式................................................错误!未定义书签。
4催化剂用量计算..............................................错误!未定义书签。
5换热面积计算................................................错误!未定义书签。
6反应器外径计算..............................................错误!未定义书签。
7壁厚计算....................................................错误!未定义书签。
8 筒体封头计算................................................错误!未定义书签。
9管板厚度计算................................................错误!未定义书签。
10设计结果汇总...............................................错误!未定义书签。
11设计小结...................................................错误!未定义书签。
绪论管式反应器一种呈管状、长径比很大的连续操作反应器。
这种反应器可以很长,如丙烯二聚的反应器管长以公里计。
反应器的结构可以是单管,也可以是多管并联,可以是空管,如管式裂解炉,也可以是在管内填充颗粒状催化剂的填充管,以进行多相催化反应,如列管式固定床反应器。
通常,反应物流处于湍流状态时,空管的长径比大于50,填充段长与粒径之比大于100(气体)或200(液体),物料的流动可近似地视为平推流。
管式反应器返混小,因而容积效率(单位容积生产能力)高,对要求转化率较高或有串联副反应的场合尤为适用。
此外,管式反应器可实现分段温度控制。
管式反应器在近40年里,由于其体积小,效率高的特点,在化工中的应用与发展十分迅速。
因此,对管式反应器的研究具有深远的意义。
我国自20世纪80年代引进这一先进技术后,由上海化工研究院、南华集团设计院和郑州工业大学在“七五”期间承担了管式反应器的国家攻关项目,四川大学在“八五”、“九五”、“十五”期间也承担了管式反应器的国家攻关项目和有关基础研究工作。
一些研究、设计院和高校大力协同,积极开展基础研究工作和承担工程项目,至今取得了很大的成绩,填补了这一领域的空白。
随着现代高科技的发展,我国研制的新型管式反应器也必将赶上世界先进水平,在化工界占有一席之地。
20世纪60年代美国TVA公司将管式反应器用于磷酸铵的气液固三项系统,省掉了传统的预中和工艺;70年代以来,许多国家在磷复合肥工业中相继开发了各种管式反应器以及相应的新流程,如德国UHDE公司、西班牙CROS公司。
目前世界上生产磷酸铵最简捷、能耗最低的流程是西班牙Aspindesa公司开发的生产粉状MAP的管式反应器喷雾流程。
如今的管式反应器的开发已扩展到磷酸铵以外的许多化肥生产领域,如硫基复合肥的中和段采用了短管型管式反应器,并且在扩大段形成了一个内循环反应过程以延长停留时间。
然而,随着科技的不断发展,新型的管式反应器将被不断地被研究出,为化工行业带来方便。
1设计内容与方法介绍反应器设计概述化学反应器是将反应物通过化学反应转化为产物的装置,是化工生产及相关工业生产的关键设备。
由于化学反应种类繁多,机理各异,因此,为了适应不同反应的需要,化学反应器的类型和结构也必然差异很大。
反应器的性能优良与否,不仅直接影响化学反应本身,而且影响原料的预处理和产物的分离,因而,反应器设计过程中需要考虑的工艺和工程因素应该是多方面的。
反应器的设计主要包括:1)反应器选型;2)确定合适的工艺条件;3)确定实现这些工艺条件所需的技术措施;4)确定反应器的结构尺寸;5)确定必要的控制手段。
在反应器设计时,除了通常说的要符合“合理、先进、安全、经济”的原则,在落实到具体问题时,要考虑到下列的设计要点:1)保证物料转化率和反应时间;2)满足物料和反应的热传递要求;3)设计适当的搅拌器和类似作用的机构;4)注意材质选用和机械加工要求。
设计内容在列管反应器中进行邻二甲苯(A)氧化制邻苯二甲酸酐(B),反应为连串—平行反应。
三个反应的速率方程为(-△Hr)B = 1285 kJ/kmol; (-△Hr)C=4561 kJ/kmol其中C是归并在一起的最终产物CO和CO2。
已知气体混合物的表观质量流速为G(5850 kg/m2·h),催化剂堆积密度为1300kg/m3,反应压力×105Pa,气体平均摩尔质量Mm = kg/kmol,入口处邻二甲苯的摩尔分数yA0,入口处氧的摩尔分数yO2,原料温度T(628K),比热容Cp=(kJ/kmol·K)。
反应热量通过管外冷流体强制循环移除,传热系数U=508kJ/(m2·h·K),且认为冷流体温度恒定,温度为Tc(613K)。
试对反应器进行设计,并进行床层压降校核。
催化剂粒径,床层空隙率参数自己选择。
催化剂耐受的最高温度为660 K。
产能:1万吨邻苯二甲酸酐/年每年生产周期按300天计生产方法介绍邻二甲苯氧化法610~640K主反应如上图,此外,由副反应还生成苯甲酸、顺丁烯二酸酐等。
该反应为强放热反应,因此选择适宜的催化剂(高活性和高选择性)和移出反应热以抑制深度氧化反应,是工业过程的关键。
工业生产方法一般是采用以五氧化二钒为主的钒系催化剂(见金属氧化物催化剂)进行邻二甲苯的气相氧化。
1974年,开发了高负荷表面涂层的钒系催化剂,催化剂载体是惰性的无孔瓷球、刚玉球和碳化硅球等。
选用环状载体制备催化剂。
这种新型催化剂可以减少因内扩散引起的深度氧化反应,从而提高了苯酐的收率、选择性和催化剂的负荷。
反应器多采用列管式固定床。
典型工艺过程是将过滤后的无尘空气经压缩、预热,与气化的邻二甲苯蒸气混合后进入反应器,反应热由管外循环的熔盐带出。
反应产物进入蒸汽发生器,被冷却的反应气经进一步冷却,回收粗苯酐。
尾气经水洗回收顺丁烯二酸酐后放空,或用催化燃烧法净化后再放空。
粗苯酐经减压精馏由塔顶分离出低沸点的顺丁烯二酸酐、甲基顺丁烯二酸酐及苯甲酸等,塔底物料经真空精馏,得到苯酐产品。
反应器类型特点反应器大致可以分为釜式反应器、管式反应器、固定床反应器、流化床反应器。
其中,固定床反应器又分为绝热式、多段绝热式、列管式、自热式反应器。
釜式反应器:反应器中物料浓度和温度处处相等,并且等于反应器出口物料的浓度和温度。
物料质点在反应器内停留时间又长又短,存在不同停留时间物料的混合,即返混程度最大。
适应范围广泛,投资少,投产容易。
但换热面积小,反应温度不易控制,停留时间不一致。
多大多数用于有液相参与的反应。
管式反应器:反应物的分子在反应器内停留时间相等,所以在反应器内任何一点上的反应物浓度和化学反应速度都不随时间变化,只随管长变化。
管式反应器具有容积小、比表面大、单位容积的传热面积大,特别适用于热效应较大的反应。
适用于大型化和连续化的化工生产。
管式反应器既适用于液相反应,又适用于气相反应。
用于加压反应尤为适用。
固定床反应器:返混小,流体同催化剂可进行有效解除,当反应伴有串联副反应时可得较高选择性。
催化剂机械损耗小。
结构简单。
主要用于气固相催化反应。
流化床反应器:流固相界面积大,有利于非均相反应的进行,提高了催化剂的利用率。
颗粒在床内混合激烈床层与内浸换热表面见的传热系数很高,全床热容量大,热稳定高。
但是催化剂颗粒间相互碰撞剧烈,造成催化剂的损失和除尘的困难。
绝热式固定床反应器:结构简单,床层横截面温度均匀。
单位体积内催化剂量大,即生产能力大。
但只适用于热效应不大的反应。
多段绝热式固定床反应器:热效应大,常把催化剂床层分成几段,段间采用间接冷却或原料气冷激。
列管固定床反应器:反应器由多根反应管并联构成,管数可达万根以上,具有良好的传热性能,单位床层体积具有较大的传热面积,可用于热效应中等或稍大的反应过程。
自热式反应器:结构较复杂,操作弹性小。
启动反应时常用电加热。
反应器选择及操作条件说明A反应器选择:本工艺反应为气固相反应,返混程度不高,为了很好的控制温度,使传热的面积更大,我们选择了列管式固定床形式。
它的优点有:①返混小,流体同催化剂可进行有效接触,当反应伴有串联副反应时可得较高选择性;②催化剂机械损耗小;③结构简单。
它的投资和操作费用介于绝热固定床和流化床之间,是气相氧化法生产邻苯二甲酸酐比较理想的反应设备。
B 操作条件说明:1. 反应方程式:C6H4CH3CH3 +3O2→C6H4C2O3 +3H2O该步骤中会有副反应发生,副反应产物为苯甲酸、顺丁烯二酸酐等。
进料状态:邻二甲苯是液态进料,经过邻二甲苯蒸发器后变为气体进入预混合器,空气经过空气压缩机进入预混合器。