反应釜温度过程控制课程设计
反应釜温度控制系统设计
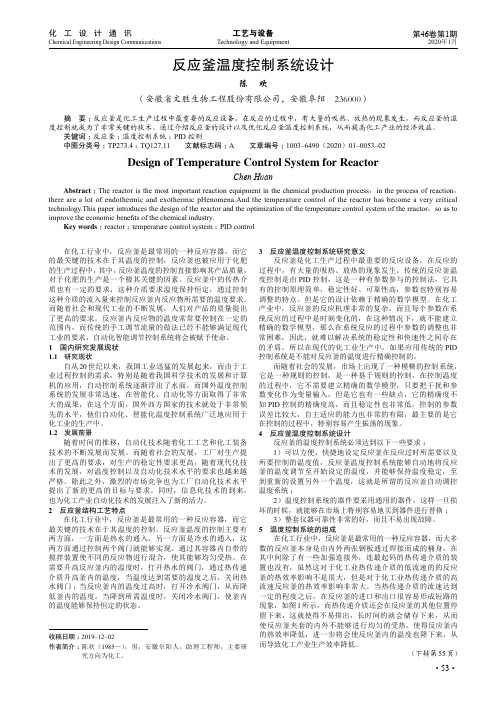
在化工行业中,反应釜是最常用的一种反应容器,而它的最关键的技术在于其温度的控制,反应釜也被应用于化肥的生产过程中,其中,反应釜温度的控制直接影响其产品质量,对于化肥的生产是一个极其关键的因素。
反应釜中的传热介质也有一定的要求,这种介质要求温度保持恒定,通过控制这种介质的流入量来控制反应釜内反应物所需要的温度要求。
而随着社会和现代工业的不断发展,人们对产品的质量提出了更高的要求。
反应釜内反应物的温度常常要控制在一定的范围内,而传统的手工调节流量的做法已经不能够满足现代工业的要求,自动化智能调节控制系统将会被赋予使命。
1 国内研究发展现状1.1 研究现状自从20世纪以来,我国工业迅猛的发展起来,而由于工业过程控制的需求,特别是随着我国科学技术的发展和计算机的应用,自动控制系统逐渐浮出了水面。
而国外温度控制系统的发展非常迅速,在智能化、自动化等方面取得了非常大的成果,在这个方面,国外西方国家的技术就处于非常领先的水平,他们自动化、智能化温度控制系统广泛地应用于化工业的生产中。
1.2 发展前景随着时间的推移,自动化技术随着化工工艺和化工装备技术的不断发展而发展。
而随着社会的发展,工厂对生产提出了更高的要求,对生产的稳定性要求更高,随着现代化技术的发展,对温度控制以及自动化技术水平的要求也越来越严格。
除此之外,激烈的市场竞争也为工厂自动化技术水平提出了新的更高的目标与要求。
同时,信息化技术的到来,也为化工产业自动化技术的发展注入了新的活力。
2 反应釜结构工艺特点在化工行业中,反应釜是最常用的一种反应容器,而它最关键的技术在于其温度的控制。
反应釜温度的控制主要有两方面,一方面是热水的通入,另一方面是冷水的通入,这两方面通过控制两个阀门就能够实现。
通过其容器内自带的搅拌装置使不同的反应物进行混合,使其能够均匀受热。
在需要升高反应釜内的温度时,打开热水的阀门,通过热传递介质升高釜内的温度,当温度达到需要的温度之后,关闭热水阀门;当反应釜内的温度过高时,打开冷水阀门,从而降低釜内的温度,当降到所需温度时,关闭冷水阀门,使釜内的温度能够保持恒定的状态。
反应釜温度过程控制课程设计
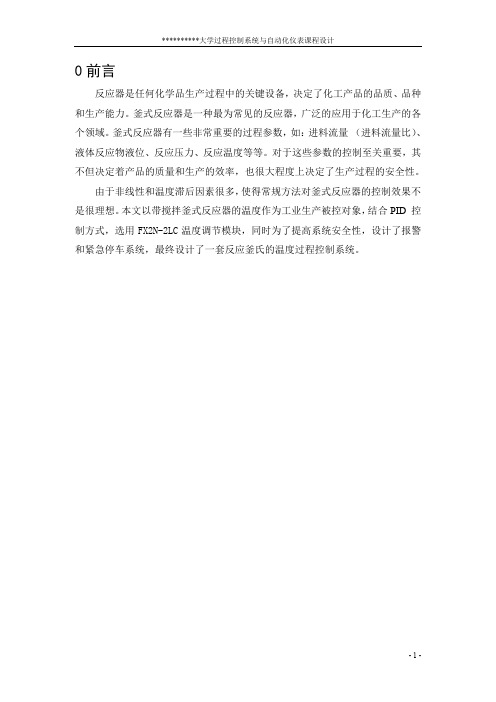
0前言反应器是任何化学品生产过程中的关键设备,决定了化工产品的品质、品种和生产能力。
釜式反应器是一种最为常见的反应器,广泛的应用于化工生产的各个领域。
釜式反应器有一些非常重要的过程参数,如:进料流量(进料流量比)、液体反应物液位、反应压力、反应温度等等。
对于这些参数的控制至关重要,其不但决定着产品的质量和生产的效率,也很大程度上决定了生产过程的安全性。
由于非线性和温度滞后因素很多,使得常规方法对釜式反应器的控制效果不是很理想。
本文以带搅拌釜式反应器的温度作为工业生产被控对象,结合PID 控制方式,选用FX2N-2LC温度调节模块,同时为了提高系统安全性,设计了报警和紧急停车系统,最终设计了一套反应釜氏的温度过程控制系统。
1系统工艺过程及被控对象特性选取1.1 被控对象的工艺过程本设计以工业常见的带搅拌釜式反应器(CSTR)为过程系统被控对象。
反应器为标准3盆头釜,反应釜直径1000mm,釜底到上端盖法兰高度1376mm,反应器总容积0.903m,耐压2.5MPa。
为安全起见,要求反应器在系统开、停车全过程中压力不超过1.5MPa。
反应器压力报警上限组态值为1.2MPa。
反应器的工艺流程如图1-1所示。
图1-1 釜式反应器工艺流程图该装置主要参数如表1-1所示。
各个阀门的设备参数如表1-2所示,其中,D g为阀门公称直径、K v为国际标准流通能力。
表1-1 主要测控参数表表1-2 设备参数表由图1-1可以看出,该被控对象的反应过程为反应物A与反应物B在催化剂C的作用下,在反应温度70±1.0℃发生反应,生成产物D。
反应初期用热水诱发,当反应开始后由冷却水通过蛇管与夹套进行冷却。
图1中,各参数含意如下:F4、F5 和F6 分别反应物A、B和催化剂 C 的进料流量,V4、V5 和V6 分别是A、B和C的进料阀。
A为反应器内主产物D重量百分比浓度,反应温度为T1,液位为L4。
反应器出口浆液流量为F9,由出口阀V9控制其流量。
反应釜(过程设备设计)课程设计

辽宁工业大学专业课课程设计(论文)题目:院(系)机械工程与自动化学院专业班级:学号:学生姓名:指导教师:教师职称:起止时间: 13.12.16----14.01.10专业课课程设计(论文)任务书目录前言 (3)1反应釜用途及特征 (3)2反应釜常见类型 (3)3搅拌反应釜 (4)第1章机械设计 (6)1.1确定筒体的直径和高度 (6)1.1.1筒体的直径 (6)1.1.2筒体的高度 (6)1.2确定夹套的直径和高度 (7)1.2.1夹套的直径 (7)1.2.2夹套的高度 (7)1.3确定夹套及筒体材料和设计壁厚 (8)1.3.1确定夹套的材料和设计壁厚 (8)1.3.2确定筒体的材料和壁厚 (9)1.4水压实验及强度较核 (11)1.4.1内筒体水压实验压力 (11)1.4.2夹套水压实验压力 (12)1.4.3内筒水压实验时壁内应力 (12)1.4.4夹套水压实验时壁内应力 (12)第二章传热计算 (14)2.1夹套内的液体向筒体的外壁传热 (14)2.2筒外壁和内壁的传热 (14)2.3较核外壁温度 (16)第三章搅拌釜密封、搅拌传动装备及附属的计算与选择 (17)3.1选择釜体法兰 (17)3.2搅拌轴、搅拌器及传动装置的设计 (17)3.2.1选择搅拌器、搅拌轴和联轴器 (17)3.2.2功率计算 (18)3.2.3搅拌轴直径计算 (18)3.2.4选择搅拌传动装置和密封装置 (19)3.2.5轴封装置 (20)3.3开孔补强 (21)3.3.1氨水进口补强: (21)3.3.2人孔补强: (22)3.3.3温度计补强: (24)3.3.4补强措施 (25)3.4容器支座的选用 (25)3.4.1反应釜的总重量计算 (26)3.5人孔、温度计与工艺接管选择 (27)3.5.1人孔的选择 (27)3.5.2温度计的选择 (28)3.5.3工艺接管的选择 (28)结束语 (30)参考文献 (31)前言1反应釜用途及特征反应釜的广义理解即有物理或化学反应的不锈钢容器,通过对容器的结构设计与参数配置,实现工艺要求的加热、蒸发、冷却及低高速的混配功能。
基于化学反应釜过程控制系统_水温控制
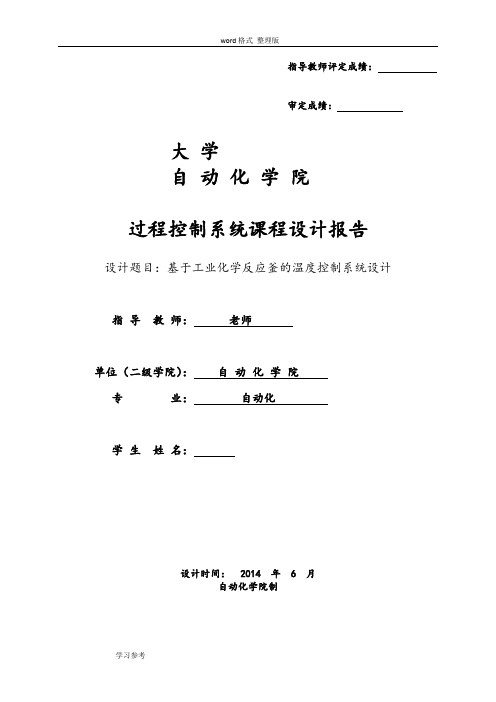
指导教师评定成绩:审定成绩:大学自动化学院过程控制系统课程设计报告设计题目:基于工业化学反应釜的温度控制系统设计指导教师:老师单位(二级学院):自动化学院专业:自动化学生姓名:设计时间: 2014 年 6 月自动化学院制基于过程控制反应釜温度控制系统设计摘要:温度是化学反应釜生产过程中对反应过程影响最重要的的因素之一,温度的控制精度、系统响应速度及稳定度是衡量温度系统性能指标的关键因素,准确地控制反应釜内原料在不同温度下进行化学反应具有重要意义。
首先,本系统对反应釜的温度进行分析,得出了冷剂流量对反应釜内温度的传递函数。
其次,通过单片机,利用继电器、DS18B20温度传感器、LCD液晶显示屏等设计了对反应釜进行加热与降温来实现反应釜温度控制的具体电路和实时系统,对实际化学反应过程中的温度变化进行模拟,并利用经典控制理论中的PID算法得到反应时的最优控制,并给出了详细的分析步骤和控制算法。
最后,通过组态软件对整个化学反应过程进行实时监控的模拟。
关键词:温度控制 PID 单片机组态王一、背景及国内外研究现状1.1 问题研究背景在化工生产过程中, 连续反应釜是一种常用的、重要的反应容器。
其化学反应机理较为复杂, 受到外界条件、原料纯度、催化剂的类型等诸多因素的影响,所以难以建立精确的数学模型, 致使整套设备的自动化水平较低。
而且在反应釜中进行的反应一般属于放热反应, 反应放热量大, 传热效果却不理想, 因此反应釜内温度一般具有大滞后、非线性等特征。
针对反应釜内温度变化的特点, 设计良好的温度控制系统是保证产品质量的关键。
在我国,尽管大中城市的科学技术和工业自动化的发展比较快,但是在众多的小城市与农村地区由于经济不够发达,政府扶持力度不够,存在许多不太安全的小规模化工生产项目,给人们的人生安全与财产安全带来了一定的威胁。
所以,如何更安全的进行化工生产已经成为了政府和各种研究机构亟待解决和完善的事。
1.2 国内外研究现状目前关于反应釜温度控制系统设计问题国内外都有一些研究,并且已经基本满足了工业需求。
夹套式反应器温度串级控制课程设计
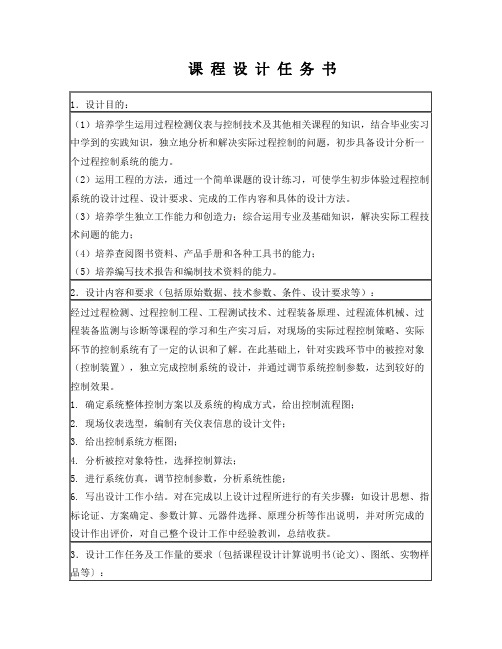
课程设计任务书中北大学课程设计说明书学院:机械与动力工程学院专业:过程装备与控制工程题目:夹套式反应器温度串级控制系统设计指导教师:吕海峰职称: 副教授目录1、概述 11.1化学反应器基本介绍 11.2夹套式反应器控制要求 22、被控对象特性研究 32.1建立动态数学模型 32.2被控变量与控制变量的选择 62.3夹套式反应器扰动变量 63、控制系统方案确定 73.1主回路的设计 83.2副回路的设计 84、过程检测仪表的选型 94.1测温检测元件及变送器 94.2主、副控制器正、反作用的选择 124.3控制系统方框图 135、系统仿真,分析系统性能 135.1各个环节传函及参数确定 135.2控制系统的仿真及参数整定 145.3 系统性能分析 176、课程设计总结 187、参考文献 191 概述1.1化学反应器的基本介绍反应器(或称反应釜)是化工生产中常用的典型设备,种类很多。
化学反应器在结构、物料流程、反应机理、传热、传质等方面存在差异,使自控的难易程度相差很大,自控方案差别也比较大。
化学反应器可以按进出物料状况、流程的进行方式、结构形式、传热情况四个方面分类:一、按反应器进出物料状况可分为间歇式和连续式反应器通常将半连续和间歇生产方式称为间歇生产过程。
间歇式反应器是将反应物料分次获一次加入反应器中,经过一定反应时间后取出反应中所有的物料,然后重新加料在进行反应。
间歇式反应器通常适用于小批量、多品种、多功能、高附加值、技术密集型产品的生产,这类生产反应时间长活对反应过程的反应温度有严格程序要求。
连续反应器则是物料连续加入,化学反应连续不断地进行,产品不断的取出,是工业生产最常用的一种。
一些大型的、基本化工产品的反应器都采用连续的形式。
二、从物料流程的进行方式可分为单程与循环两类物料在通过反应器后不再进行循环的流程称为单程,当反应的转化率和产率都较高时,可采用单程的排列。
如果反应速度较慢,祸首化学平衡的限制,物料一次通过反应器转化不完全,则必须在产品进行分离后,把没有反应的物料与新鲜物料混合后,再送送入反应器进行反应。
电子技术课程设计--化学反应釜温度电子控制器设计与实验
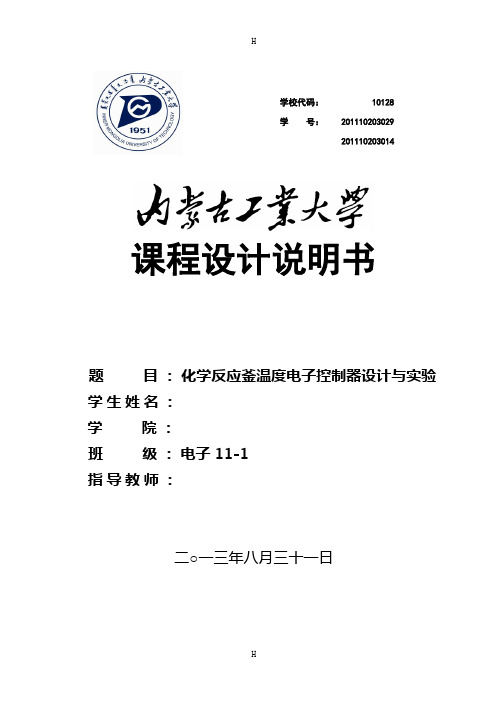
学校代码: 10128学号: 201110203029201110203014 课程设计说明书题目:化学反应釜温度电子控制器设计与实验学生姓名:学院:班级:电子11-1指导教师:二○一三年八月三十一日摘要本次设计旨在将模拟电子技术与数字电子技术相结合,运用放大电路、滤波电路、门电路、逻辑分析电路、组合逻辑电路、时序逻辑电路的相关知识,解决集成电路、数模和数模转换、数字电路中的若干实际问题,制作一个针对化学反应釜温度和反应次数的控制器,控制器有高、低温报警功能(V CC=5V,P OM=1W)、报警和反应次数的计数显示功能,并且可显示反应时间、设定启停温度、存储报警和反应次数,同时可提供控制器5V/2A直流电源电路。
本设计经multisim和实测验证均可达到预期要求。
关键词:控制电路;温度信号;报警;显示;AbstractThe design aims at combining the analog electronic technology and digital electronic technology, with using the amplification circuit, filter circuit, circuit, logic circuit, combinational logic circuit and sequential logic circuit knowledge ,to solve the integrated circuits, analog and digital to analog conversion, some actual problems in digital circuit .To produce a chemical reaction kettle temperature and reaction times of the controller, the controller has the high and low temperature alarm function (VCC = 5 v, POM = 1 w) count display, alarm and reaction times, and it can display the reaction time, temperature, storage alarm set start-stop and reaction times, at the same time can provide controller 5 v / 2 a dc power supply circuit. This design through the multisim and validation of all can meet the expected requirements.Key words: control circuit; Temperature signal; Call the police; Display; Storage;目录一、设计任务概述 (1)二、设计方案论证及方框图 (1)1、题目要求简析 (1)2、电路分块 (1)3、电路结构方框图 (2)4、设计方案比对 (2)三、电路组成及工作原理 (3)(一)、信息采集电路 (4)(二)、信号处理电路 (4)(三)、状态表示电路 (5)1、计时显示部分 (5)2、报警电路及报警计数电路 (6)3、工作状态控制电路 (7)四电路元器件选择与实际测量 (8)模拟电子技术部分 (8)(1)放大、滤波部分测量 (8)(2)比较器部分测量 (10)数字电子技术部分: (11)(1)计时显示部分测量 (11)(2)高、低温报警计数部分测量 (13)(3)工作状态控制部分测量 (14)参考文献 (17)设计所需仪器设备及元器件清单 (18)一、设计任务概述设计并制作一个针对化学反应釜温度和反应次数的控制器,也适用于大中小工业生产领域。
反应釜温控系统课程设计
反应釜温控系统课程设计一、课程目标知识目标:1. 学生能理解反应釜的基本原理和温度控制的重要性。
2. 学生能掌握反应釜温度控制系统的组成、工作原理及各部分功能。
3. 学生能了解温度传感器、控制器、执行器等关键部件的类型及选用原则。
技能目标:1. 学生能运用所学知识分析反应釜温度控制系统的故障原因并进行排查。
2. 学生能设计简单的反应釜温度控制方案,包括参数设置、设备选型等。
3. 学生能通过实验操作,验证温度控制系统的稳定性和可靠性。
情感态度价值观目标:1. 学生培养对化学反应过程的兴趣,增强对化学工程领域的认识。
2. 学生树立安全意识,认识到温度控制在化学反应过程中的重要性。
3. 学生培养团队协作精神,提高沟通与表达能力,为未来从事相关工作奠定基础。
分析课程性质、学生特点和教学要求,本课程目标旨在使学生在理解反应釜温控系统基本原理的基础上,掌握实际操作和设计能力,同时培养安全意识、团队协作和沟通能力,为未来从事化学工程及相关领域工作打下坚实基础。
通过本课程的学习,学生将能够具备解决实际问题的能力,为我国化学工业的发展贡献力量。
二、教学内容1. 反应釜基本原理及温度控制概述- 介绍反应釜的作用、类型及在化工生产中的应用。
- 阐述温度控制在反应釜操作中的重要性。
2. 反应釜温度控制系统组成与工作原理- 分析温度控制系统的组成部分,包括温度传感器、控制器、执行器等。
- 讲解各部分的工作原理及相互关系。
3. 温度传感器及其选用- 介绍常见温度传感器的类型、特点及应用场景。
- 分析温度传感器的选用原则,包括精度、响应时间等方面。
4. 温度控制器原理与操作- 阐述温度控制器的原理,包括PID控制算法。
- 指导学生操作温度控制器,实现反应釜温度的精确控制。
5. 反应釜温度控制方案设计- 分析反应釜温度控制方案的设计原则,包括设备选型、参数设置等。
- 指导学生设计简单的反应釜温度控制方案。
6. 实验操作与故障排查- 安排实验操作环节,让学生动手验证温度控制系统的稳定性和可靠性。
反应釜设计课程设计
反应釜设计课程设计
反应釜设计课程设计应包括以下内容:
1. 引言:介绍反应釜的基本概念、用途和重要性。
2. 反应釜的基本原理和设计要求:介绍反应釜的工作原理、反应釜设计的基本要求,包括反应条件、反应物的特性、反应速率等。
3. 反应釜的材料选择:介绍不同材料的优缺点,选择适合特定反应条件的反应釜材料。
4. 反应釜的容积和尺寸设计:根据反应物的量和反应速率,确定反应釜的容积和尺寸,包括直径、高度等。
5. 反应釜的加热和冷却系统设计:介绍不同的加热和冷却方法,选择适合的系统,包括传热介质的选择、传热面积的确定等。
6. 反应釜的搅拌系统设计:介绍不同的搅拌方式和搅拌器的选择,包括搅拌速度、搅拌器形状等。
7. 反应釜的安全措施设计:介绍反应釜的安全操作规程、安全设备的选择和安装,包括压力控制、温度控制、泄压装置等。
8. 反应釜的操作和维护:介绍反应釜的操作步骤、常见故障及解决方法,以及定期维护和保养。
9. 实例分析:通过实际的反应釜设计案例,进行分析和讨论,包括
设计过程、问题解决思路等。
10. 课程总结:对整个课程进行总结并展望未来的发展方向。
以上是反应釜设计课程设计的基本内容,可以根据具体情况进行调整和补充。
课程设计应注重理论与实践相结合,通过实际案例和实验操作提高学生的实际操作能力和问题解决能力。
反应釜的设计课程设计
反应釜的设计课程设计一、课程目标知识目标:1. 让学生理解反应釜的基本结构及其在化学工业中的应用。
2. 掌握反应釜设计中涉及的关键参数,如温度、压力、搅拌速度等。
3. 学习反应釜的材料选择原则及其对反应过程的影响。
技能目标:1. 培养学生运用所学知识进行反应釜初步设计的能力,包括选型、计算和材料选择。
2. 提高学生通过实验、图表分析等手段解决实际问题的能力。
3. 学会使用专业软件或工具对反应釜设计进行模拟和优化。
情感态度价值观目标:1. 培养学生对化学工程学科的兴趣,激发其创新意识和探索精神。
2. 增强学生的环保意识,使其在设计过程中充分考虑安全、环保和节能等因素。
3. 培养学生的团队协作精神和沟通能力,使其在项目实施过程中能够有效分工与协作。
本课程针对高中化学或物理学科,结合学生年级特点,以提高学生的实践操作能力和创新思维为核心。
课程设计注重理论知识与实践应用的结合,鼓励学生通过实验和案例分析,掌握反应釜设计的基本原理和方法。
通过本课程的学习,期望学生能够达到上述目标,为未来进一步学习相关专业打下坚实基础。
二、教学内容1. 反应釜的基本概念与结构- 介绍反应釜的定义、分类及其在化学工业中的应用。
- 分析反应釜的主要组成部分,如釜体、搅拌装置、加热和冷却系统等。
2. 反应釜设计原理与关键参数- 探讨反应釜设计的基本原则,包括材料选择、热力学和动力学考虑。
- 讲解温度、压力、搅拌速度等关键参数对反应过程的影响。
3. 反应釜设计方法与步骤- 引导学生了解反应釜设计的流程,包括需求分析、选型、计算、材料选择等。
- 指导学生运用相关公式和图表进行反应釜设计计算。
4. 反应釜设计实践案例分析- 分析典型反应釜设计案例,让学生了解实际工程中的应用。
- 组织学生进行小组讨论,分析案例中的设计优缺点。
5. 反应釜设计模拟与优化- 引导学生使用专业软件或工具进行反应釜设计的模拟和优化。
- 指导学生通过调整设计参数,提高反应釜的性能和安全性。
反应釜温控方案
反应釜温控方案要搞定反应釜的温控,咱得这么来。
一、了解反应釜和温度要求。
首先得把咱这个反应釜摸透咯。
就像了解自己的宠物一样,知道它啥习性。
得知道这个反应釜是干啥用的,里面进行的反应是喜欢热乎点还是凉快些,能承受的最高温和最低温是多少。
比如说有些反应像个急性子,温度稍微不对就容易出乱子;有些就像慢性子,温度有点波动还能凑合。
这时候就得找资料或者问问之前用过这反应釜的老手,把准确的温度范围确定好。
二、温控设备的选择。
1. 加热设备。
如果反应釜需要加热,那选择可不少。
像电加热棒就像个小火炉,往反应釜里一放,电能转化成热能,简单直接。
不过要注意功率得选合适的,功率小了像小火苗给大象取暖,半天没效果;功率大了,又容易一下把反应釜给热过头,就像火太大把饭烧焦了。
还有蒸汽加热,这就像是给反应釜蒸桑拿。
蒸汽通过管道进去,热量就慢慢传进去了。
但是得保证蒸汽的供应稳定,要是一会儿有一会儿没有,反应釜里的反应就像坐过山车,忽冷忽热的。
2. 冷却设备。
要是反应过程中会产生热量需要冷却,那冷却水管就像给反应釜冲凉水澡。
不过要注意水流速度,水流慢了,冷却效果不好,就像夏天用涓涓细流洗脸,不凉快;水流太快了,又可能对反应釜造成一些冲击啥的,就像拿高压水枪去冲娇嫩的花朵。
还有些制冷机组,那可是个大空调,专门给反应釜制冷的。
不过这玩意儿成本比较高,就像买个豪车,得考虑自己的钱包能不能承受得住。
三、温度监测。
1. 温度计。
普通的玻璃温度计就像个老实巴交的小兵,便宜又简单。
但是读数不太方便,得凑近了看,而且容易碎,就像个脆弱的小瓷人。
热电偶温度计就高级一些,能把温度信号变成电信号,然后传输到控制系统那里。
就像个小间谍,偷偷把温度情报送出去。
它的精度也比较高,不过也得定期检查校准,不然小间谍也可能传递错误情报呢。
2. 温度传感器。
除了热电偶,还有热电阻传感器之类的。
这些传感器就像一群小侦探,分布在反应釜的各个关键位置,把不同地方的温度都监测到。
- 1、下载文档前请自行甄别文档内容的完整性,平台不提供额外的编辑、内容补充、找答案等附加服务。
- 2、"仅部分预览"的文档,不可在线预览部分如存在完整性等问题,可反馈申请退款(可完整预览的文档不适用该条件!)。
- 3、如文档侵犯您的权益,请联系客服反馈,我们会尽快为您处理(人工客服工作时间:9:00-18:30)。
过程控制系统课程课题:反应釜温度控制系统系另I」:电气与控制工程学院专业:自动化_____________姓名: ________ 彭俊峰_____________学号:__________________指导教师: _______ 李晓辉_____________河南城建学院2016年6月15日反应器是任何化学品生产过程中的关键设备,决定了化工产品的品质、品种和生产能力。
釜式反应器是一种最为常见的反应器,广泛的应用于化工生产的各个领域。
釜式反应器有一些非常重要的过程参数,如:进料流量(进料流量比)、液体反应物液位、反应压力、反应温度等等。
对于这些参数的控制至关重要,其不但决定着产品的质量和生产的效率,也很大程度上决定了生产过程的安全性。
由于非线性和温度滞后因素很多,使得常规方法对釜式反应器的控制效果不是很理想。
本文以带搅拌釜式反应器的温度作为工业生产被控对象,结合PID 控制方式,选用FX2N-PLC 调节模块,同时为了提高系统安全性,设计了报警和紧急停车系统,最终设计了一套反应釜氏的温度过程控制系统。
1系统工艺过程及被控对象特性选取被控对象的工艺过程本设计以工业常见的带搅拌釜式反应器(CSTR)为过程系统被控对象。
反应器为标准3盆头釜,反应釜直径1000mm,釜底到上端盖法兰高度1376mm, 反应器总容积,耐压。
为安全起见,要求反应器在系统开、停车全过程中压力不超过。
反应器压力报警上限组态值为。
反应器的工艺流程如图1-1所示。
S8QA a珑厲娜口图1-1釜式反应器工艺流程图该装置主要参数如表1-1所示。
各个阀门的设备参数如表1-2所示,其中,D g为阀门公称直径、K v为国际标准流通能力。
表1-1主要测控参数表表1-2设备参数表由图1-1可以看出,该被控对象的反应过程为反应物A与反应物B在催化剂C的作用下,在反应温度70±C发生反应,生成产物D。
反应初期用热水诱发,当反应开始后由冷却水通过蛇管与夹套进行冷却。
图1中,各参数含意如下:F4、F5和F6分别反应物A、B和催化剂C的进料流量,V4、V5和V6分别是A、B和C的进料阀。
A为反应器内主产物D重量百分比浓度,反应温度为T1,液位为L4。
反应器出口浆液流量为F9,由出口阀V9控制其流量。
出口泵及出口泵开关为S5反应器出口为混合液,由产物D与未反应的A、B以及催化剂C组成。
F7为夹套冷却水入口流量,由阀V7进行控制。
F8为蛇管冷却水入口流量, 由阀V8 进行控制。
此外,在反应初期,需要由反应器夹套加热热水来触发反应。
该热水由开关阀S6引入。
反应器搅拌电机开关为S&被控对象特性描述本设计中的被控对象主要是反应釜的温度部分。
由于被控对象有其特殊特性,直接影响着操纵变量和控制方案的选取,因此对于被控变量的特性分析显得尤为重要。
下面就针对反应釜反应温度分析和描述。
该反应属于放热反应,放热反应属于非自衡的危险过程,反应温度高将导致反应速度加快,释放出热量导致反应温度进一步升高,温度迅速升高的同时,反应压力也会迅速加大,从而有可能导致火灾或者爆炸事故。
因此有必要对反应温度加以控制,其主要手段是控制夹套以及蛇管冷却水的流量。
冷却水流量的变化随阀门的开关变化较快、时间常数较小。
当冷却水压力下降时(这种干扰在现场时有发生),即使阀位不变,冷却水流量也会下降,冷却水带走的热量减少,反应器中物料温度会上升。
反应温度和反应转化率的变化属于时间常数较大的高阶特性。
由于温度变化的滞后,用常规控制器进行调节效果不佳。
2 仪表的选取温度控制系统主要由温度传感器、温度调节仪、执行装置、被控对象四个部分组成,其系统结构图如图所示。
图2-1 温度控制系统结构图过程检测与变送器的选取过程检测是生产过程自动控制系统的重要组成部分。
过程检测装置及时而准确的把被控参数检测出来,并变成调节、控制装置可识别的方式,作为过程控制装置判断生产过程的依据。
根据工业的要求,为了具有较高的精度,采用热电阻温度计。
热电阻温度计广泛应用于-200~600C范围内的温度测量。
用于制造热电阻的材料,要求电阻率、电阻温度系数要大,热容量、热惯性要小,电阻与温度的关系最好近于线性,另外,材料的物理化学性质要稳定,复现性好,易提纯,同时价格便宜。
热电阻的选取可以根据表2-1确定:表2-1工业常用热电阻由表2-1,根据釜内温度的一般变化范围选用铂电阻,为提高检测精度采用三线制的接法,如图2-2所示。
采用三线制是为了消除连接导线电阻引起的测量误差。
这是因为测量热电阻的电路一般是不平衡电桥。
热电阻作为电桥的一个桥臂电阻,其连接导线(从热电阻到中控室)也成为桥臂电阻的一部分,这一部分电阻是未知的且随环境温度变化,造成测量误差。
采用三线制,将导线一根接到电桥的电源端,其余两根分别接到热电阻所在的桥臂及与其相邻的桥臂上,这样消除了导线线路电阻带来的测量误差。
所以工业上一般都采用三线制接法。
温度变送器我们选择DDZ-川型温度变送器如图2-3所示。
图2-2热电阻三线直接法图2-3变送器的测量接线示意图其特点:(1)采用线性集成放大电路,使仪表的精确性、可靠性、稳定性以及其他指标均符合国家规定的标准。
(2)采用了通用模块和专用模块相结合的设计方法,使用灵活、方便。
(3)在与热电阻的接入单元中,采用了线性化电路,从而保证了变送器的输出信号与被测温度呈线性关系,大大方便了变送与系统的配接。
(4)采用了统一的24V DC 集中供电,变送器内无电源,实现了“三线制”的接线方式。
(5)采取了安全火花防爆措施,适用于具有爆炸危险场合中的温度或直流毫伏信号的检测。
执行器的选取执行器是过程控制系统的重要组成部分,其特性好坏直接影响系统的控制质量。
它接受控制器输出的控制信号,并将其转换为直线位移和角位移,操纵控制机构,自动改变操作变量,从而实现对过程变量的自动控制。
本设计采用气动薄膜调节阀,其工作原理:当气室输入了〜信号压力之后,薄膜产生推力,使推力盘向下移动,压缩弹簧,带动推杆、阀杆、阀芯向下移动,阀芯离开了阀座,从而使压缩空气流通。
当信号压力维持一定时,阀门就维持在一定的开度上。
气动薄膜调节阀的结构可以分为两部分,上面是执行机构,下面是调节机构它主要由膜片、弹簧、推杆、阀芯、阀座等零部件组成。
当来自控制器的信号压力通入到薄膜气室时,在膜片上产生一个推力,并推动推杆部件向下移动,使阀芯和阀座之间的空隙减小,流体受到的阻力增大,流量减小。
推杆下移的同时,弹簧受压产生反作用力,直到弹簧的反作用力与信号压力在膜片上产生的推力相平衡为止,此时,阀芯与阀座之间的流通面积不再改变,流体的流量稳定。
出于安全的原因,在此次设计中使用VBD 气动端面密封蝶阀,VBD 气动端面密封蝶阀是一种重量轻,结构简单的后座式端面密封蝶阀。
阀体、阀板均用钢板焊接或铸造加工而成。
适用于低压状态的空气或其他气体的流量、压力控制。
气动执行器分气开和气关两种形式,有压力信号时阀关,无压力信号时阀开为气关式执行器;反之,则为气开式。
它的选择首先应根据调节器输出信号为零时使生产处于安全状态的原则确定;其次,还应考虑是否有利于节能、是否有利于开车、停车等进行选择。
最后,气开、气关的选择主要是考虑在不同生产工艺条件下安全生产的要求。
考虑的原则是:信号压力中断时,应保证设备和工作人员的安全。
根据工业的要求,本设计选择了气关方式。
调节阀的尺寸主要是指调节阀的开度和口径,他们的选择对系统的正常运行影响很大。
若调节阀口径选择过小,当系统受到较大扰动时,调节阀既是运行在全开状态,也会使系统出现暂时失控现象;若口径选择过大,则在运行中阀门会经常处于小开度状态,容易造成流体对阀芯和阀座的频繁冲蚀,甚至使调节阀失灵。
因此,结合本设计的工业要求,调节阀开度应处于15%〜85%之间。
调节阀是控制系统非常重要的一个环节,它接受控制器的输出信号,改变操纵变量,执行最终控制任务。
控制阀的流量特性是指流体通过阀门的相对流量与相对开度之间的函数关系,如下式中所示。
Q Q max f l L(2-1)其中Q Q max ――相对流量。
即控制阀在某一开度下的流量与最大流量之比;lL――相对开度。
即控制阀在某一开度下的行程与全行程之比。
常用的理想流量特性的控制阀有:线性型、对数(等百分比)型和快开型等。
其理想流量特性如图2-5所示。
图2 -5控制阀理想流量特性而在实际工作时,阀两端的压降会随流量而变化,这时的流量特性称为工作特性。
设管路系统的总压差为厶P T,由液体提升高度引起的压差为厶P h,阀两端的压降为△ P v,管路其他部分的压降为厶R。
工程中通常采用经验法来选择调节阀的流量特性。
表2-1给出了理想流量特性的经验,本方案将依据这个表来选取理想流量特性。
然而当控制系统中某一环节出现故障或意外时,应考虑人身、设备装置的安全;考虑介质性质;还要考虑减少经济损失等。
表2-1控制阀理想流量特性经验选择表控制器仪表的选择采用模拟控制器:DDZ —III型调节器,DDZ ―川基型控制器框图如图控制器的输入信号为1〜5V的测量信号。
设定信号有内设定和外设定两种。
内设定信号为1〜5V,外设定信号为4〜20mA。
测量信号和设定信号通过输入电路进行减法运算,输出偏差到比例积分微分电路进行比例积分微分运算后,由输出电路转换为4〜20mA 信号输出。
手动电路和保持电路附于比例积分微分电路之中,手动电路可实现软手动和硬手动两种操作,当处于手动状态时,用手指按下软手动操作键,使控制器输出积分式上升或下降,当手指离开操作键时,控制器的输出值保持在手指离开前瞬间的数值上,当控制器处于硬手动状态时,移动硬手动操作杆,能使控制器的输出快速改变到需要的数值,只要操作杆不动,就保持这一数值不变。
由于有保持电路,使自动与软手动相互切换,硬手动只能切换到软手动,都是无平衡无扰动切换,只有软手动和自动切换到硬手动需要事先平衡才能实现无扰动切换。
3.控制方案的整体设定控制方式的选择采用单回路控制方式,将反应温度T1 取一阶微分,得到温度变化率,再与升温速率设定值C /s作比较,将偏差作为控制器的输入。
控制系统框图如图3-1 所示:图3-1 控制系统框图传递函数框图如图3-2所示:图3-2传递函数框图系统的开环传递函数为:G(s) G c(S)G°(S)G v(S)G m(s)(3-1) 闭环传递函数为:W(s) G c (S)G°(S)G V(S)1 G c(S)G°(S)G v(S)G m(s)(3-2)阀门特性及控制器选择阀门V8选线性阀。
对于釜式反应器,在升温阶段65C以下由夹套冷却水阀控制冷却水流量来实现对反应温度的控制。
根据反馈控制的基本原理,要使系统能够正常工作,构成系统开环传递函数静态增益的乘积必须为正。