基于汽车制动性试验系统的开发
基于虚拟仪器的汽车制动性测试系统的研究与开发

是将传感器采集到 的信号经数据采集卡 , 传到笔记
本 电脑 中进 行分 析 和显示 , 其 原理 图如 图 1 所示。
—
一
一
一
一
L a b V I E W 为开发平 台。L a b V I E w 是集 开发 、 调
试 和运 行 于一 体 的功能 强 大 的虚 拟 仪器 开发 工具 软
I一 一 一 一 一 一 一 一 一 一 一 一 一 一 一 一 一 一 一 一 一 一 一 一 一 L 一 一 一 一 一 一 一 一 一 一 一。
图 1 测试 系 统 的 原 理 图
2 . 1 系统 的硬件 部 分
硬件 部分 主要 由 D AQC A R D—AI 一1 6 E一4数 据采集卡b ] 、 S C一 2 0 4 0 数据保持卡 ] 、 光 电传感器 、 踏板 力传 感器 、 动态应变仪、 电压 转换 器 、 蓄 电池 和
第2 3卷第 3期
2 0 1 3年 6月
北华航天工业学 院学报
J o u r n a l o f No r t h Ch i n a I n s t i t u t e o f Ae r o s o a c e E n g i n e e r i n  ̄
Vo 1 . 2 3 NO. 3
汽 车 制 动 性 能 测 试 系 统 是 以 图形 化 编程 工 具
卡将采集到的数据传给笔记本 电脑 , 然后运行相应 的程序 , 就 可 以得 到检测 的结果 , 进 而分 析汽 车 的制 动性 能 J 。
2 系统 的组成
该 测 试 系 统是 由硬 件部 分 和 软件 部 分 组成 的 ,
件系统 , 很好地发挥 了虚拟仪器的数据采集 、 处理、 分析和显示的功能。能够实现传感器信号 、 滤波效 果 显示 、 传感 器 标 定 、 速 度 和 制 动 减 速度 显 示 、 制 动
汽车制动系统的设计开题报告
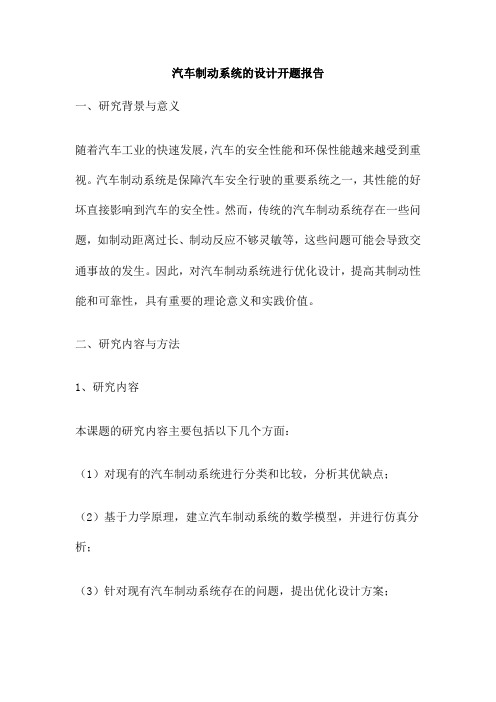
汽车制动系统的设计开题报告一、研究背景与意义随着汽车工业的快速发展,汽车的安全性能和环保性能越来越受到重视。
汽车制动系统是保障汽车安全行驶的重要系统之一,其性能的好坏直接影响到汽车的安全性。
然而,传统的汽车制动系统存在一些问题,如制动距离过长、制动反应不够灵敏等,这些问题可能会导致交通事故的发生。
因此,对汽车制动系统进行优化设计,提高其制动性能和可靠性,具有重要的理论意义和实践价值。
二、研究内容与方法1、研究内容本课题的研究内容主要包括以下几个方面:(1)对现有的汽车制动系统进行分类和比较,分析其优缺点;(2)基于力学原理,建立汽车制动系统的数学模型,并进行仿真分析;(3)针对现有汽车制动系统存在的问题,提出优化设计方案;(4)对优化后的汽车制动系统进行实验验证,分析其性能和可靠性。
2、研究方法本课题将采用理论分析、数值模拟和实验验证相结合的方法进行研究。
具体来说,我们将:(1)收集和整理现有的汽车制动系统相关资料,对其分类和比较进行分析;(2)基于力学原理,建立汽车制动系统的数学模型,并利用数值模拟方法对不同类型汽车制动系统的性能进行仿真分析;(3)针对现有汽车制动系统存在的问题,提出优化设计方案,并进行详细的理论分析和仿真计算;(4)对优化后的汽车制动系统进行实验验证,分析其性能和可靠性。
三、预期成果与价值(1)对现有的汽车制动系统进行分类和比较,明确各种制动系统的优缺点;(2)建立汽车制动系统的数学模型,并利用数值模拟方法对其性能进行评估;(3)提出优化设计方案,提高汽车制动系统的性能和可靠性;(4)对优化后的汽车制动系统进行实验验证,分析其性能和可靠性。
本课题的研究成果将具有重要的理论意义和实践价值。
通过对现有汽车制动系统的分类和比较,可以为汽车制造商和消费者提供更加全面的技术参考。
建立的汽车制动系统的数学模型和优化设计方案,可以为汽车制造商提供更加详细的设计指导和技术支持。
通过实验验证和分析,可以证明优化后的汽车制动系统在提高汽车安全性和可靠性方面具有显著的优势。
汽车制动实验报告心得

汽车制动实验报告心得1. 引言汽车制动系统是汽车安全性能最重要的部分之一,也是驾驶员操作最频繁的一个系统。
汽车制动实验旨在通过对制动系统的测试,了解车辆制动性能和制动过程中的一些关键指标,从而确保车辆行驶的安全性。
在本次实验中,我们使用了制动试验台进行了一系列的测试,从中获得了许多有益的信息。
2. 实验目的本次实验的目的是测量并分析汽车制动系统的性能,主要包括制动距离、制动时间、制动力分布等指标。
通过对实验结果的分析,能够帮助我们更好地理解制动系统的工作原理和性能特点。
3. 实验过程在实验过程中,我们首先使用了制动力计,通过测量前轮制动力和后轮制动力的分布情况,得到了车辆在制动过程中的动态响应。
然后,在制动试验台上使用了制动距离测量装置,测量了车辆在不同速度下的制动距离和制动时间。
4. 实验结果通过实验测量,我们得到了一系列有关制动系统性能的数据。
其中,最重要的是制动距离和制动时间。
通过对这些数据的分析,我们可以得出一些有用的结论。
首先,制动距离与车辆速度呈正相关关系。
随着车辆速度的增加,制动距离也会增加。
这是因为制动过程需要消耗一定的时间来将车辆的动能转化为制动能量,因此车辆在高速行驶时需要更长的制动距离来停下来。
其次,制动时间与制动压力呈正相关关系。
在相同速度下,当制动压力增加时,制动时间会减小。
这是因为制动压力的增加会加速制动系统的响应速度,使得制动时间缩短。
此外,通过前后轮制动力分布的测量,我们可以得出车辆的制动力分配情况。
通过调整制动系统的参数,可以实现不同的制动力分配方式,以满足不同道路条件和驾驶员的需求。
5. 实验心得通过参与汽车制动实验,我学到了很多关于汽车制动系统的知识。
首先,我深刻认识到汽车制动系统对于行车安全的重要性。
一辆好的汽车制动系统可以在紧急情况下快速停车,避免意外发生。
其次,我了解到制动系统的性能与很多因素有关,包括车辆质量、制动盘和刹车片的磨损程度、制动液的温度等。
汽车制动性能检测系统的设计与分析

该检测系统主要 由机械和电气两部分组成。 机 械部分主要包括双板式称重 台和单轴反力式滚筒 制动试验台, 电气部分采用工业 计算机测控系统 , 是本文介绍的重点. 制动力检测采用的制动试验台 由框架 、 驱动装置 、 滚筒装置、 举升装置、 测量装置、 控制装置等组成 , 中滚筒的圆周表面覆盖一定厚 其
维普资讯
第 2 卷 第 5期 6 2 0 年 1 月 06 O
西 安 工 业 大 学 学 报
J OURNAL ’ OF XIAN TECHNOLOGI CAL UNI VERS TY I
V0. 6 No 5 1 2 .
输出( 、 电平 ) 高 低 状态发生 改变 , 从而 给计算机一 个可靠的开始和结束检测信号.
A
提示信息和制动力检测值及判断结果 , 并通过网络 将结果传送给上位计算机.
工 ‘— 灯 阵
开 关
__■ ■■■ ■■■_。■ 。■■一
量输 _ ^
入 卡
lD E
Oc.2 0 t 06
文章编号 : 10—742 0)54 5 4 005 1 (0 60—3— 0
汽车春 霞
( 西安工业大学 机 电工程学院 , 西安 7 0 3 ) 1 0 2
摘 要 : 介绍一种汽车制动性能检测 系统的结构及工作原理 , 并对制动性能测试方法和测试 结果进行 了分析研 究. 结果表明, 由于受到轴荷、 滚筒夹角及滚筒表面附着系数等因素的影响,
况很相似, 使测试结果更接近实 际情况, 平板式 但 制动试验台对传感器 、 检定工具 、 测试方法等有较 严格的要求 , 使得造价升高 、 测试难度增加. 本文介 绍的这种汽车制动性 能检测系统采用反力 式滚筒
毕业设计论文-汽车制动实验台动力系统设计

汽车制动实验台动力系统设计目录第一章绪论 (4)1.1选题背景 (4)1.1.1 选题的目的和意义 (4)1.1.2 国内外汽车试验制动台的发展的现状: (6)1.1.3 台架制动实验台的特点及发展前景 (8)1.2本课题的研究工作 (9)第二章传动方案选择及论证 (10)2.1传动方案的设计与论证 (10)2.1.1传动方案的要求 (10)2.1.2 传动方案的拟定 (11)2.2传动方案的内容与工作制动试验台原理 (11)2.2.1传动方案的内容 (11)2.2.2制动实验台的工作原理 (12)第三章制动实验台结构设计计算 (13)3.1引言: (13)3.2滚筒选择 (13)3.2.1 滚筒直径的选择 (13)3.2.2 滚筒长度的选择 (13)3.2.3 滚简转速的选择 (13)3.2.4 车轮与滚筒间附着系数的选择 (14)3.2.5 安置角对测试车轮稳定性的影响 (14)3.2.6 滚筒中心距L的选择 (15)3.3车轮的选择与计算 (15)3.3.1车轮直径计算 (15)3.3.2车轮所需转速计算 (15)3.4滚筒的计算 (15)3.4.1滚筒质量计算 (15)3.4.2滚筒转动惯量计算 (16)3.4.3滚筒功率计算 (16)3.5电动机的选择 (16)3.6.齿轮传动计算 (18)3.6.1 车速为100km/h时的齿轮传动 (19)3.6.2齿轮传动分析 (26)3.7轴设计 (28)3.7.1确定轴的最小直径 (29)3.7.2从动轴设计 (30)3.7.3主动轴设计 (30)3.8轴承和轴承座设计 (31)3.81 选择轴承型号 (31)3.82 轴承座型号 (32)3.9主从滚筒间齿轮传动设计 (32)3.10汽车制动实验台框架参数设计 (32)3.10.1 槽钢的选择 (33)3.10.2 制动试验台框架结构参数 (34)3.11带传动设计 (34)3.12电磁离合器地选择 (35)3.12.1.按计算扭矩选择电磁离合器 (35)3.12.2 牙嵌式电磁离合器的结构与工作原理 (35)3.13本章小结 (36)第四章结论和建议 (38)4.1本论文的结论 (38)致谢 (39)参考文献 (40)附录 (41)制动器和制动测试试验的概况 (41)A P RIMER ON B RAKES AND B RAKE T ESTING (47)第一章绪论1.1 选题背景汽车制动性能的检测,作为机动车安全检测中最重要项目之一,一直是大家关注的焦点。
最新汽车制动性实验报告
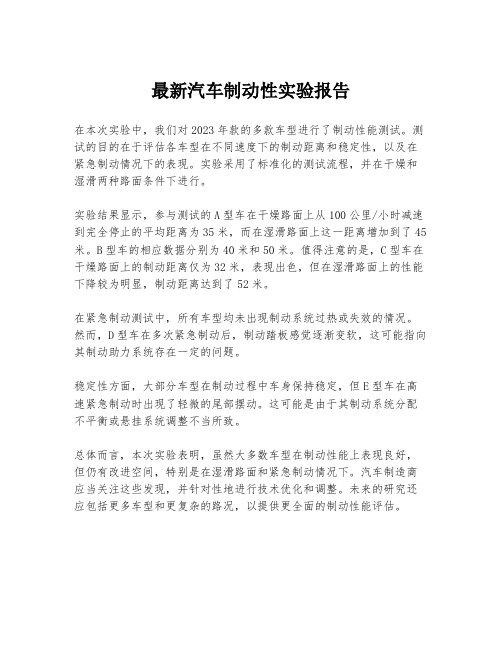
最新汽车制动性实验报告
在本次实验中,我们对2023年款的多款车型进行了制动性能测试。
测试的目的在于评估各车型在不同速度下的制动距离和稳定性,以及在紧急制动情况下的表现。
实验采用了标准化的测试流程,并在干燥和湿滑两种路面条件下进行。
实验结果显示,参与测试的A型车在干燥路面上从100公里/小时减速到完全停止的平均距离为35米,而在湿滑路面上这一距离增加到了45米。
B型车的相应数据分别为40米和50米。
值得注意的是,C型车在干燥路面上的制动距离仅为32米,表现出色,但在湿滑路面上的性能下降较为明显,制动距离达到了52米。
在紧急制动测试中,所有车型均未出现制动系统过热或失效的情况。
然而,D型车在多次紧急制动后,制动踏板感觉逐渐变软,这可能指向其制动助力系统存在一定的问题。
稳定性方面,大部分车型在制动过程中车身保持稳定,但E型车在高速紧急制动时出现了轻微的尾部摆动。
这可能是由于其制动系统分配不平衡或悬挂系统调整不当所致。
总体而言,本次实验表明,虽然大多数车型在制动性能上表现良好,但仍有改进空间,特别是在湿滑路面和紧急制动情况下。
汽车制造商应当关注这些发现,并针对性地进行技术优化和调整。
未来的研究还应包括更多车型和更复杂的路况,以提供更全面的制动性能评估。
车辆制动系统开发方案
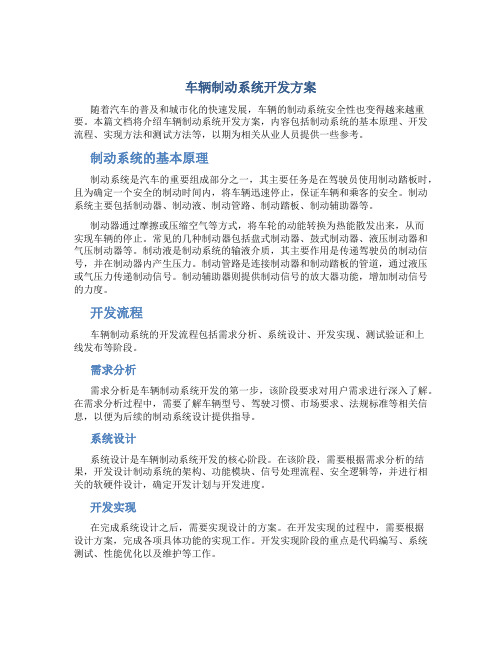
车辆制动系统开发方案随着汽车的普及和城市化的快速发展,车辆的制动系统安全性也变得越来越重要。
本篇文档将介绍车辆制动系统开发方案,内容包括制动系统的基本原理、开发流程、实现方法和测试方法等,以期为相关从业人员提供一些参考。
制动系统的基本原理制动系统是汽车的重要组成部分之一,其主要任务是在驾驶员使用制动踏板时,且为确定一个安全的制动时间内,将车辆迅速停止,保证车辆和乘客的安全。
制动系统主要包括制动器、制动液、制动管路、制动踏板、制动辅助器等。
制动器通过摩擦或压缩空气等方式,将车轮的动能转换为热能散发出来,从而实现车辆的停止。
常见的几种制动器包括盘式制动器、鼓式制动器、液压制动器和气压制动器等。
制动液是制动系统的输液介质,其主要作用是传递驾驶员的制动信号,并在制动器内产生压力。
制动管路是连接制动器和制动踏板的管道,通过液压或气压力传递制动信号。
制动辅助器则提供制动信号的放大器功能,增加制动信号的力度。
开发流程车辆制动系统的开发流程包括需求分析、系统设计、开发实现、测试验证和上线发布等阶段。
需求分析需求分析是车辆制动系统开发的第一步,该阶段要求对用户需求进行深入了解。
在需求分析过程中,需要了解车辆型号、驾驶习惯、市场要求、法规标准等相关信息,以便为后续的制动系统设计提供指导。
系统设计系统设计是车辆制动系统开发的核心阶段。
在该阶段,需要根据需求分析的结果,开发设计制动系统的架构、功能模块、信号处理流程、安全逻辑等,并进行相关的软硬件设计,确定开发计划与开发进度。
开发实现在完成系统设计之后,需要实现设计的方案。
在开发实现的过程中,需要根据设计方案,完成各项具体功能的实现工作。
开发实现阶段的重点是代码编写、系统测试、性能优化以及维护等工作。
测试验证测试验证是车辆制动系统开发的重要环节。
该阶段需要对开发实现阶段的所有功能进行测试,对测试结果进行分析评估,确定是否满足系统要求。
本阶段需要进行全方位的测试,包括单元测试、模块测试、性能测试、压力测试、安全测试、稳定性测试等。
汽车制动性实验报告(一)2024

汽车制动性实验报告(一)引言概述:
汽车制动性是指汽车在行驶过程中受到外力作用后能够迅速减速并停下来的性能。
为了验证汽车的制动性能,进行了一系列的制动实验。
本文将详细介绍汽车制动性实验的过程和结果。
正文:
1. 制动能力测试
- 布置实验设备和测量仪器
- 选择合适的测试路段和条件
- 测定汽车在各种速度下的制动距离
- 记录制动距离与刹车力的关系曲线
- 分析不同车速下的制动性能差异
2. 制动灵敏度测试
- 选取不同施加刹车力的实验组
- 测试汽车对不同刹车力大小的响应时间
- 分析制动灵敏度与刹车力之间的关系
- 比较不同车辆的制动灵敏度表现
3. 制动平衡测试
- 利用制动力测试仪测定四个车轮的制动力
- 分析制动力的分布情况
- 检测车辆在制动过程中的左右平衡性
- 针对不平衡情况提出调整建议
4. 制动热衰变测试
- 使用测温仪测量制动器片和制动盘的温度
- 进行连续制动实验并记录温度变化
- 分析制动热衰变的过程和速率
- 探讨制动器的热衰变对制动性能的影响
5. 制动安全性测试
- 模拟紧急制动情况,观察车辆的反应
- 测试ABS(防抱死刹车系统)的效果
- 比较不同车辆的制动安全性能
- 分析制动性能的改善方向和建议
总结:
通过上述五个方面的实验研究,我们对汽车的制动性能进行了全面的评估。
制动能力、灵敏度、平衡性、热衰变和安全性都是衡量汽车制动性的重要指标。
本次实验结果表明,该车辆的制动性能良好,但在某些条件下仍存在改进空间。
进一步的研究可以帮助提升汽车制动性能,从而更好地保障驾驶人的安全。
- 1、下载文档前请自行甄别文档内容的完整性,平台不提供额外的编辑、内容补充、找答案等附加服务。
- 2、"仅部分预览"的文档,不可在线预览部分如存在完整性等问题,可反馈申请退款(可完整预览的文档不适用该条件!)。
- 3、如文档侵犯您的权益,请联系客服反馈,我们会尽快为您处理(人工客服工作时间:9:00-18:30)。
第50巷第10期V01.50No.10:==========:=:=::=:====:一=农业装备与车辆工程AGRICUI,TURAI.EQUIPMENT&VEHICI.EENGINEERING2012年10月October2012doi:1f)3969/j.issn.1673—3142.2012.10.007基于LabView汽车制动性试验系统的开发谢继鹏1一,李守成1,刘海燕2,孙成全1(1.210094汀苏省南京市南京理1:大学机械-丁=程学院;2.210046江苏省南京市南京理]:大学紫金学院)[摘要]利用虚拟仪器开发软件LabView开发实时测量与分析的汽车道路制动性试验系统。
在分析汽车道路试验系统技术要求的基础上,详细介绍试验系统的硬件组成,给出可实时进行汽车制动动态参数信号测量、采集以及可视化处理的道路试验系统的软件流程以及基于频率法计算车速与基于斜率法计算制动减/加速度等关键技术的实现过程,最后结合实车的汽车道路制动试验验证该试验系统的可行性以及可靠性。
[关键词]汽车;制动性;道路测试;LabView[中图分类号】U467.1+l;¥229[文献标志码]A[文章编号】1673-3142(2012)10-0024-04StudyonAutomobileBrakingRoadTestSystemUsingLabViewXIEJi—pen91一,LIShou-cheng’,LIUHai-yan2,SUNCheng-quanl(1.SchoolofMechanicalEngineering,NanjingUniversityofScienceandTechnology,NanjingCity,JiangsuProvince210094,China;2.ZijinCollege,NanjingUniversityofScienceandTechnology,NanjingCity,JiangsuProvince210046,China)[Abstract]Anautomobilebrakingroadtestsystemforrealtimemeasuringandanalyzingthedynamicparametersofautomo-bilewasdevelopedbasedonthevirtualinstrumentplatformIJabView.Theintroductionoftheautomobileroadtestsystemwasintroducedbasedontheanalysisoftheroadtestrequirements.Thesoftwareflowsweregiventoimplementsignalmeasuring,dataacquisitionandvisualization.Therelativekeytechniquesofthespeedbasedonfrequencymethodanddeceleration/accel—erationbasedonslopemethodweredemonstrated.Theexperimentalresultsprovethefeasibilityandvalidityofautomobileroadtests.ystem.[Keywords]automotive;brakingperformance;roadtest;LabView0引言汽车制动性是汽车的主要性能之一,制动性直接关系到交通安全,重大交通事故往往与制动距离太长、紧急制动时发生侧滑等情况有关,改善汽车的制动性,始终是汽车设计制造和使用部门的重要任务.也是目前汽车发展的研究的热点之一…。
传统的测试系统基本上是以硬件或固化的软件形式存在的,仪器由生产厂家来定义和制造,设计复杂、灵活性差,测试参数少且不能对采集的数据作进一步处理、分析,在一些较为复杂和测试参数较多的场合。
使用极不方便。
本文基于虚拟仪器LabView软件开发平台,利用实验室现有的光栅车速传感器、踏板力传感器以及高速数据采集器构建实时动态监测实验数据的汽车道路制动性测试系统。
1制动性试验系统的硬件组成收稿【l期:2012-()7—02修回H期:2012-07-12开发试验系统应满足足够的测控精度。
同时应简单可靠、实用,能适应各类标准要求,并能保存相应的试验数据.以使试验后进一步的处理和分析等原则。
系统硬件连接如图l。
试验系统采用GDS一1I型光栅车速传感器,车速误差小于0.2%;踏板力传感器为MLA—IKNA型,精度为±O.0lN;高速数据采集器为某公司的DH5923,采样频率最高可达10MHz,支持多通道同时采样.与上位机通信为1394高速通信接口;以及ThinkPad笔记本作上位搬,Jf々感器I:sI)一11光栅1i速f0感器圈1试验系统硬件莲揍豳Fig.1Componentsoftheroadtestsystem万方数据第50卷第10期谢继鹏等:基于LabVieW汽车制动性试验系统的开发25机供实时数据显示、数据存储以及数据后处理等,以上设备保证了试验系统有较高的试验精度。
,2制动性试验系统的软件设计LabVieW是使用“所见即所得”的可视化技术建立人机界面的图形化编程语言。
如今它作为一种强大的虚拟仪器平台,广泛地被T业界、学术界和研究实验室所接受.被视为一个标准的数据采集仪器和控制软件。
基于LabView的特点,试验系统选用LabView8.2作为软件的开发平台.根据制动性试验的国家标准开发设计制动性试验系统软件。
,2.1流程设计该试验系统的流程图,如图2所示。
首先进入系统。
可进行1394接口以及对DH5923采集参数进行设计,参数设置好之后即可进行数据的采集,若硬件T作正常主界面会显示即时车速,若按照制动性试验要求输人正确的起始测试初始值,进入等待试验状态,当试验条件满足后,系统自动采集试验对数据进行实时数据处理、图形绘制。
当车速为零后.系统自动判断停止试验,数据保存后返同到主界面。
图2制动性试验系统溉程圈Fig.2Theflowchartofbrakingperformancetestsystem2.2基于1394高速通信与数据采集通道的配置系统采集参数首先调用DH5923设备的l394接口通信的子vl程序12・引,如图3所示,通过该接LI可以设置需要采集的光栅车速传感器、踏板力传感器模拟信号的采集参数,如通道号、采样频率、采样时电压的最大值与最小值,缓存区大小、采样启停等功能。
若参数设置正确则可开始读取数据.即可获取需要的实时参数,并在主界面上实时刷新.显示当前的车速值,供随时的试验需要,但显示数据系统不保存,处理完毕后随即丢弃,而试验结束后.采集与车速数值都正常显示,只是关闭满足试验条件的数据的存储,只有退出主界面后才关闭采集卡。
围31394接口通信程序Fig.3Theprogramfor1394interface3试验参数的采集与分析计算3.1基于频率法的车速采集与计算试验测试系统中光栅车速传感器的测速范围是0.5~250km/h.对应的正弦波频率范围是0.035~17.5kHz,每个脉冲对应的位移为4mm,以此硬件精度作为最低稳定车速的设计依据,根据其工作原理,设置采样频率为100kHz,每个波形使用2048个点数来描述显示,则可得到软件设置的最低车速对应正弦波频率为50Hz,满足硬件的最低稳定车速对应的正弦波频率要求。
由于该光栅传感器每个脉冲对应的位移为4ram,由此可得正弦波频率与车速的关系为U.--0.0144Xfo由桑浓采样定理可知.在进行模拟/数字信号的转换过程中,当采样频率.疋。
大于信号中最高频率.‘。
的2倍时(‘~>=Z厂眦),采样之后的数字信号完整地保留了原始信号中的信息,一般实际应用中保证采样频率为信号最高频率的5.10倍。
则可得到该测试系统中稳定的最高速的光栅车速正弦波频率为10kHz,即最高车速为144km/h.该最高车速满足道路测试对车速的要求。
由于系统电源采用蓄电池独立供电.蓄电池须对含有60W照明的光栅车速传感器供电。
由于长时间供电后其输出电压及电流出现不稳定现象,导致光栅车速传感器的输出波形出现高频干扰信号如图4所示。
系统软件中采用卡尔曼滤波万方数据26农业装备与车辆工程算法对车速信号进行滤波【4]与信号处理后,将得到的方波信号进行频率计数.得到输出的波形频率及该系统所需的车速值。
州lm图4车速信号中的高频干扰信号Fig.4High-frequencyinterferencesignalsofspeedsignal综上所述。
使用LabView建立的车速的采集与计算程序框图如图5所示。
图5车速滤波及车速计算程序Fig.5Theprogramforfilteringandcalculatationofthespeedsignal3.2基于斜率法的制动减/加速度计算由于减速度传感器比车速传感器的测试误差要大很多.故本试验系统没有采用直接测量加速度的方法而是采用车速数值计算得到。
由于车速的高频噪声不可避免,很小的车速变化都可能引起剧烈的加速度抖动,造成许多“锯齿”.容易造成误判,故直接微分法计算的减/lm速度在本试验系统的数据处理中不适用。
本文采用斜率法计算制动减/加速度,即计算某时刻前连续N点车速曲线的斜率,将此斜率作为此时刻的制动减/加速度。
假设每段曲线斜率的方程为y=ao+a舭根据最小二乘法原理【5],每次取Ⅳ点,即各点(轧Y,),(轧Y:),…,(z。
,yN)使得、^∑产∑I,,i一(%+nl誓)】2I商=min。
(1)Ii=I最小.即对参数ao一的最佳估计,要求观测值yl的偏差的平方和最小,最后可得到斜率n,的最佳估计值的表达式为诂毫xiy'--N;-蓦i=,!.薹..=,兰。
㈤∑簟z一百1(∑工∥此斜率仍即为此时刻的减/加速度值。
使用LabView建立其程序框图如图6所示。
圈黾。
….。
锄ⅡI∥莎一一够护。
嘲.bIb三.■1II愿泸图6基于斜率法的制动减/加速度计算程序Fig.6Theprogramforbrakingdeceleration/accelerationbasedonslopemethod3.3踏板力的采集由于系统对两个通道的模拟信号进行并行采样.由DH5923传送到LabView软件缓存区中的数据是车速与踏板力这两通道的交替信号,首先使用LabView软件本身的多线程技术同时采集来自多个传感器的信号,并对每通道信号分别处理,以保证多个传感器的信号并行传递,互不影响,实现测试系统数据的同步采集以及实时显示。
4测试系统的实车验证该试验系统主要用于测试汽车制动性的制动效能即紧急制动时的制动时间、制动距离以及制动减/加速度。