玻纤行业纯氧燃烧的关键问题分析
玻璃生产中的全氧燃烧
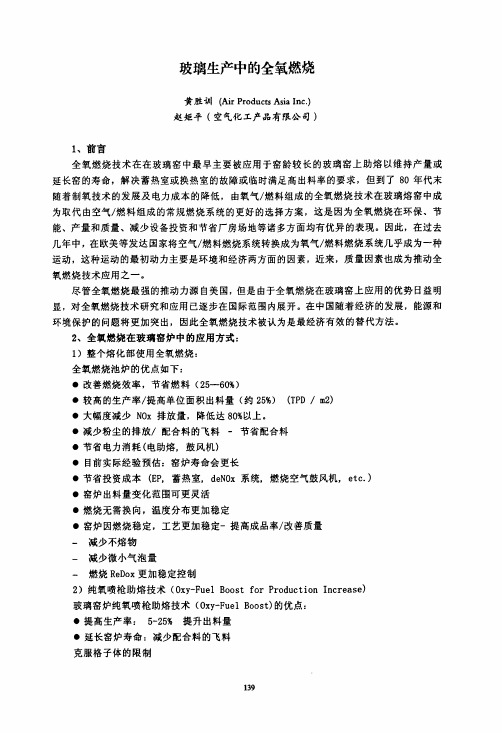
(b)Cleanfire’H酽(具有较高的热传导效率,较大的火焰覆盖面积,较低的碹顶、胸墙 温度等特点):
(c)Cleanflre。HR,“
该系列烧咀是AirProducts最新研制的新型燃烧设备,它是在2004年第一季度在用户开始 使用。由于它具有:对玻璃液更好的传热效率(和其它烧咀相比,至少节能5%);维护方便(不 积磺):燃烧范围广(O 25--20kOd Btu/hr)等特点。受到用户的高度赞扬。
·改善质量: 减少气泡/夹杂
●提高热效率:—2-1—0%燃料节省
●减少污染排放: 5-20%减少(Ibs/吨玻璃)
3、Air Products全氧燃烧技术在中国应用的事例
a)某合资公司(产品为电子玻璃,燃料为:天然气):
普通空气助燃池炉
纯氧燃烧池炉
出料量
260TPD
272TPD
池炉面积
240
210
燃料用量
2950nm3/hr
1595nm3/hr
氧气用量 N0x
N/A 10.2
3190nm3/hr 2.4 Ib/ton
玻璃质量
Improved
燃料单耗
271.6nm3/hr
140.3nm3/hr
碎玻璃率
52%
32%
童丝
4.6% -12.5%
-46% N7K 一76%
-48.3% -38%
b)某外资玻璃公司进行氧枪助熔改造(产品为玻璃保温棉,燃料为:LPG)
】43
原普通空气助燃池 坦
完成氧枪助熔改造后池炉
出料量
40TPD
60TPD
池炉面积
28.6
全氧燃烧技术
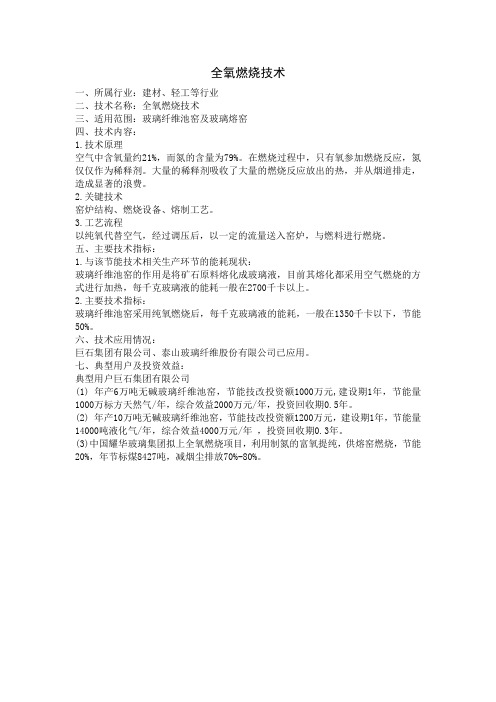
全氧燃烧技术一、所属行业:建材、轻工等行业二、技术名称:全氧燃烧技术三、适用范围:玻璃纤维池窑及玻璃熔窑四、技术内容:1.技术原理空气中含氧量约21%,而氮的含量为79%。
在燃烧过程中,只有氧参加燃烧反应,氮仅仅作为稀释剂。
大量的稀释剂吸收了大量的燃烧反应放出的热,并从烟道排走,造成显著的浪费。
2.关键技术窑炉结构、燃烧设备、熔制工艺。
3.工艺流程以纯氧代替空气,经过调压后,以一定的流量送入窑炉,与燃料进行燃烧。
五、主要技术指标:1.与该节能技术相关生产环节的能耗现状:玻璃纤维池窑的作用是将矿石原料熔化成玻璃液,目前其熔化都采用空气燃烧的方式进行加热,每千克玻璃液的能耗一般在2700千卡以上。
2.主要技术指标:玻璃纤维池窑采用纯氧燃烧后,每千克玻璃液的能耗,一般在1350千卡以下,节能50%。
六、技术应用情况:巨石集团有限公司、泰山玻璃纤维股份有限公司已应用。
七、典型用户及投资效益:典型用户巨石集团有限公司(1) 年产6万吨无碱玻璃纤维池窑,节能技改投资额1000万元,建设期1年,节能量1000万标方天然气/年,综合效益2000万元/年,投资回收期0.5年。
(2) 年产10万吨无碱玻璃纤维池窑,节能技改投资额1200万元,建设期1年,节能量14000吨液化气/年,综合效益4000万元/年,投资回收期0.3年。
(3)中国耀华玻璃集团拟上全氧燃烧项目,利用制氮的富氧提纯,供熔窑燃烧,节能20%,年节标煤8427吨,减烟尘排放70%-80%。
八、推广前景和节能潜力:(1)6万吨玻璃纤维池窑,“十一五”末达到10条线,总投资8000万元,总节能量12000万标方天然气/年;(2)浮法玻璃窑,“十一五”期间完成浮法玻璃窑试点,总投资5亿元,年节能量5000吨重油左右。
九、推广措施及建议:玻璃纤维池窑全氧燃烧技术,其技术水平将达到国际前沿水平,填补国内空白。
“十一五”期间,该项技术可在大型玻璃纤维池窑上推广。
玻璃熔窑全氧燃烧技术问答
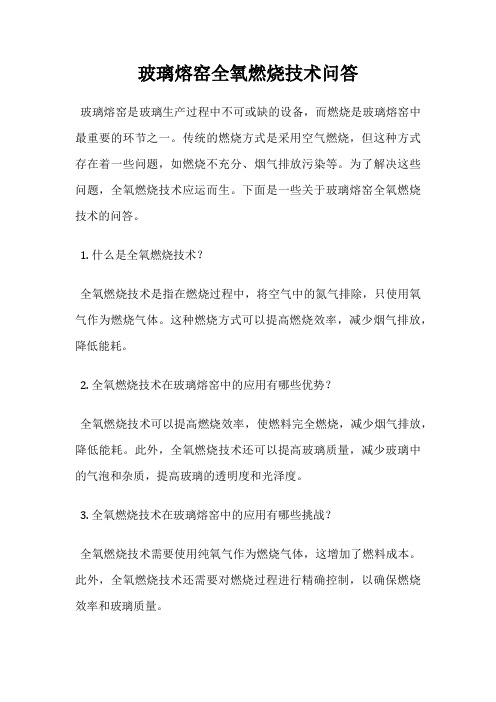
玻璃熔窑全氧燃烧技术问答
玻璃熔窑是玻璃生产过程中不可或缺的设备,而燃烧是玻璃熔窑中最重要的环节之一。
传统的燃烧方式是采用空气燃烧,但这种方式存在着一些问题,如燃烧不充分、烟气排放污染等。
为了解决这些问题,全氧燃烧技术应运而生。
下面是一些关于玻璃熔窑全氧燃烧技术的问答。
1. 什么是全氧燃烧技术?
全氧燃烧技术是指在燃烧过程中,将空气中的氮气排除,只使用氧气作为燃烧气体。
这种燃烧方式可以提高燃烧效率,减少烟气排放,降低能耗。
2. 全氧燃烧技术在玻璃熔窑中的应用有哪些优势?
全氧燃烧技术可以提高燃烧效率,使燃料完全燃烧,减少烟气排放,降低能耗。
此外,全氧燃烧技术还可以提高玻璃质量,减少玻璃中的气泡和杂质,提高玻璃的透明度和光泽度。
3. 全氧燃烧技术在玻璃熔窑中的应用有哪些挑战?
全氧燃烧技术需要使用纯氧气作为燃烧气体,这增加了燃料成本。
此外,全氧燃烧技术还需要对燃烧过程进行精确控制,以确保燃烧效率和玻璃质量。
4. 全氧燃烧技术在玻璃熔窑中的应用现状如何?
全氧燃烧技术已经在玻璃熔窑中得到了广泛应用。
许多玻璃生产企业已经采用了全氧燃烧技术,以提高生产效率和玻璃质量。
随着技术的不断发展,全氧燃烧技术在玻璃熔窑中的应用前景将会更加广阔。
全氧燃烧技术是一种高效、环保的燃烧方式,可以提高玻璃熔窑的生产效率和玻璃质量。
虽然全氧燃烧技术在应用过程中存在一些挑战,但随着技术的不断发展,这些问题将会得到解决。
浮法玻璃生产纯氧助燃技术推广的因素分析
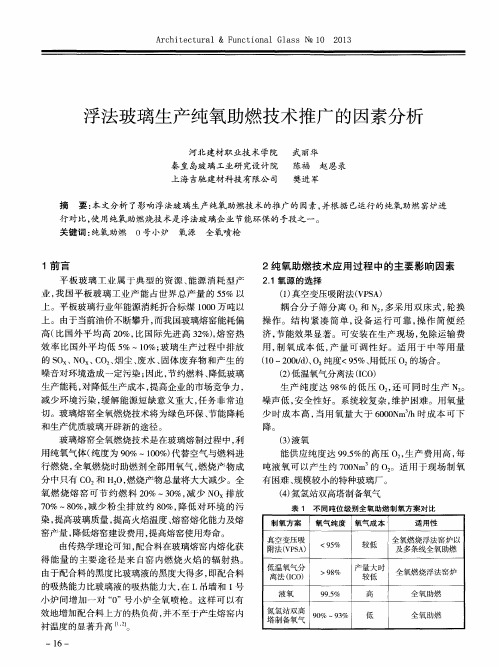
耦 合分子筛分离 O 和N , 多采用双床式 , 轮换 操作。结构 紧凑简单 , 设备 运行可 靠 , 操 作 简 便 经
济, 节能 效 果 显著 。可安 装 在生 产 现 场 , 免 除运 输 费 用, 制氧 成本低 , 产 量 可 调 性 好 。适 用 于 中 等 用 量 ( 1 0~2 0 0  ̄ d ) 、 O 纯度 <9 5 %、 用低 压 0 : 的场合 。
能 供 应 纯 度达 9 9 . 5 %的高 压 O , , 生产费用高, 每 吨 液 氧可 以产 生 约 7 0 0 N m 的O , 。适 用 于 现 场制 氧
有 困难 、 规模 较小 的特种 玻璃 厂 。
( 4 ) 氮氢站双高塔制备氧气
表 1 不 同 吨位 级 别 全 氧 助 燃 制 氧方 案对 比
制氧方 案 真空变压吸 附法( V P S A ) 低温氧气分 离法 ( I C O )
液氧
氧气纯度 氧气成本
适用- 陛
窑产量 , 降低熔窑建设费用 , 提高熔窑使用寿命。 由传热学理论可知 , 配合料在玻璃熔窑内熔化获
得 能 量 的 主要 途 径 是 来 自窑 内燃 烧 火 焰 的 辐 射 热 。
的S O N O C O 、 烟尘 、 废水 、 固体废弃物和产生的 噪 音对 环境 造成一 定 污染 ; 因此 , 节约 燃料 、 降低 玻璃 生产能耗 , 对降低生产成本 , 提高企业的市场竞争力 , 减少环境污染 , 缓解能源短缺意义重大, 任务非常迫 切 。玻璃 熔 窑全氧 燃烧 技术 将 为绿色 环保 、 节能 降耗 和 生产优 质玻 璃开辟 新 的途径 。 玻璃 熔 窑全氧 燃烧 技术 是在 玻璃熔 制 过程 中 , 利
一
>9 8 % 9 9 . 5 %
玻璃池窑炉采用纯氧燃烧技术的认识
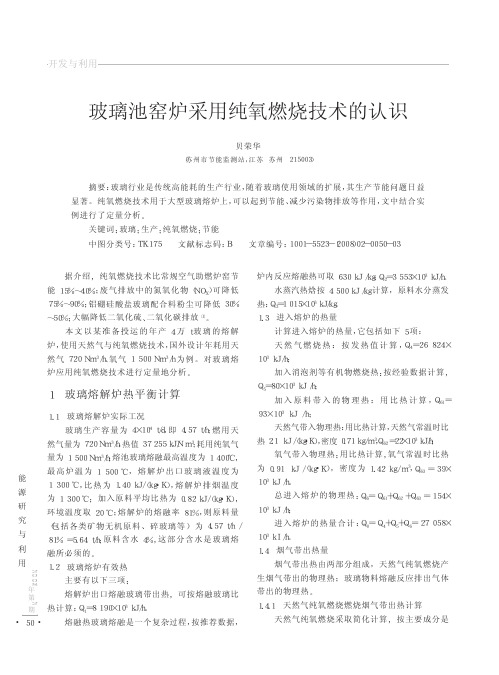
"""""""""""""""""$
%%%%%%%%%%%%%%%%%%%%$
9 158×103(kJ /h)= 2.0 倍。如果全用来产生蒸汽, 可 得蒸汽量约为 4.0 t/h。
显见, 回收这些热量, 比起两个庞大的空气预热 器— ——蓄热室( 不是蓄热式燃烧) 的投资和维修、增 大了的熔炉炉膛设计等, 则未必合算。
空气助燃燃烧时产生的烟气量为9742kgh那么烟气带出热量为排烟温度为13001823710kjh212空气助燃燃烧比纯氧助燃燃烧烟气多带出热考虑燃烧过剩空气系数携带粉尘等因素乘11系数则空气助燃燃烧比纯氧助燃燃烧烟气多带出热量为1823710kjh111289410kjh
开发与利用
玻璃池窑炉采用纯氧燃烧技术的认识
带出的物理热。
1.4.1 天然气纯氧燃烧燃烧烟气带出热计算
天然气纯氧燃烧采取简化计算, 按主要成分是
贝荣华, 玻璃池窑炉采用纯氧燃烧技术的认识
开发与利用
甲烷, 其燃烧耗氧量应是天然气量的两倍。 CH4+2O2 = CO2 +2H2O H2O 分 子 量 为 18, 1 300 ℃平 均 比 热 为 2.7 k
kJ /( kg·K) , CO2 分子量为 44, 1 300 ℃平均 比 热 为 1.34 kJ /( kg·K) , 简化为 理 想 气 体 , 以 此 计 算 燃 烧 烟 气 重 度 为 1.19 kg/Nm3, 燃 烧 烟 气 平 均 比 热 为 1.95 kJ/( kg·K) ; 烟气量为 2 570 kg /h; 排烟温度为 1 300 ℃计算, 烟气带出热量 Q71 = 6 515×103 kJ /h。 1.4.2 反应排出气体的带出热量
玻纤窑炉纯氧顶烧技术研究

中图法分类号:TQ171.77+6.21 文献标识码:A玻纤窑炉纯氧顶烧技术研究杨平原,曾勇,李奉云,党旭峰,额文泉,马韦韦(重庆国际复合材料股份有限公司,重庆 404100)摘 要:近年来,随着玻纤窑炉逐步向大型化、绿色方向发展,在产量和品质不断提升的同时,持续降低生产成本是行业提高竞争力的有效手段,纯氧燃烧技术因其自身诸多优势已在玻纤行业广泛运用。
结合公司纯氧顶烧实际改造情况,以改造后的效益为出发点,为行业从业人员在纯氧顶烧改造和使用方面提供相关经验借鉴和参考。
关键词:纯氧燃烧;侧烧;顶烧;产量;熔化率Oxy-fuel Top Firing Technology Research for Glass Fiber FurnaceYang Pingyuan, Zeng Yong, Li Fengyun, Dang Xufeng, E Wenquan, Ma Weiwei(Chongqing Polycomp International Corp., Chongqing 404100)Abstract: In recent years, with the gradual development of glass fiber furnaces towards high capacity and green production, continuous reduction of production cost while constantly improving the output and quality is an effective method to enhance the competitiveness of the industry. Oxy-fuel combustion technology has been widely used in the glass fiber industry due to its own advantages. Based on the actual transformation to oxy-fuel top firing technology in the company and the benefits brought by the transformation, this paper provides relevant experience and reference to the industry practitioners for their transformation to and use of oxy-fuel top firing technology.Key words: oxy-fuel combustion; side firing; top firing; output; melting rate1 纯氧燃烧技术纯氧燃烧技术是把燃料与90%~100%的纯氧按预定燃烧比混合、比空气燃烧更充分完全的节能综合技术[1]。
玻璃熔窑全氧燃烧技术及发展方向
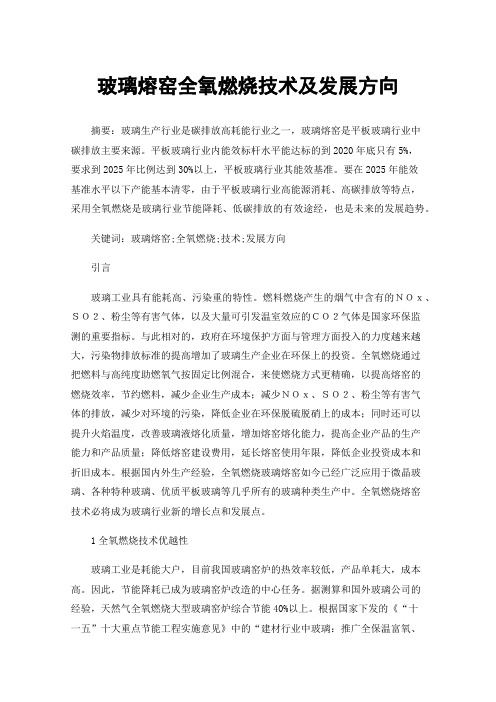
玻璃熔窑全氧燃烧技术及发展方向摘要:玻璃生产行业是碳排放高耗能行业之一,玻璃熔窑是平板玻璃行业中碳排放主要来源。
平板玻璃行业内能效标杆水平能达标的到2020年底只有5%,要求到2025年比例达到30%以上,平板玻璃行业其能效基准。
要在2025年能效基准水平以下产能基本清零,由于平板玻璃行业高能源消耗、高碳排放等特点,采用全氧燃烧是玻璃行业节能降耗、低碳排放的有效途经,也是未来的发展趋势。
关键词:玻璃熔窑;全氧燃烧;技术;发展方向引言玻璃工业具有能耗高、污染重的特性。
燃料燃烧产生的烟气中含有的NOx、SO2、粉尘等有害气体,以及大量可引发温室效应的CO2气体是国家环保监测的重要指标。
与此相对的,政府在环境保护方面与管理方面投入的力度越来越大,污染物排放标准的提高增加了玻璃生产企业在环保上的投资。
全氧燃烧通过把燃料与高纯度助燃氧气按固定比例混合,来使燃烧方式更精确,以提高熔窑的燃烧效率,节约燃料,减少企业生产成本;减少NOx、SO2、粉尘等有害气体的排放,减少对环境的污染,降低企业在环保脱硫脱硝上的成本;同时还可以提升火焰温度,改善玻璃液熔化质量,增加熔窑熔化能力,提高企业产品的生产能力和产品质量;降低熔窑建设费用,延长熔窑使用年限,降低企业投资成本和折旧成本。
根据国内外生产经验,全氧燃烧玻璃熔窑如今已经广泛应用于微晶玻璃、各种特种玻璃、优质平板玻璃等几乎所有的玻璃种类生产中。
全氧燃烧熔窑技术必将成为玻璃行业新的增长点和发展点。
1全氧燃烧技术优越性玻璃工业是耗能大户,目前我国玻璃窑炉的热效率较低,产品单耗大,成本高。
因此,节能降耗已成为玻璃窑炉改造的中心任务。
据测算和国外玻璃公司的经验,天然气全氧燃烧大型玻璃窑炉综合节能40%以上。
根据国家下发的《“十一五”十大重点节能工程实施意见》中的“建材行业中玻璃:推广全保温富氧、全氧燃烧浮法玻璃熔窑,降低烟道散热损失”精神,优化全氧超白压延玻璃生产线熔窑设计是必要的。
玻璃熔窑全氧燃烧技术及发展方向

“十四五”期间,对我国玻璃行业来说,面临着如何将“玻璃熔窑全氧燃烧技术”成果进一步产业化并为行业尽早实现节能减排和碳达峰碳中和,寻找可靠技术措施的重大工程技术问题。
玻璃熔窑全氧燃烧技术最显著的特点一是节能减排,二是提高玻璃质量,目前只有使用重油、天然气等高热值燃料,生产优质玻璃的企业才有动力和需求采用全氧燃烧技术。
通过近年的科研设计和生产实践,玻璃熔窑全氧燃烧技术已经在光伏玻璃、玻璃纤维、玻璃器皿、微晶玻璃等生产领域中广泛应用,其优异的提高玻璃质量、节能减排效果得到了充分验证,但广泛实施浮法玻璃全氧燃烧技术仍然面临着一些重大工程技术和经济问题,总的来说主要需要在以下几个方面开展技术创新:1优化全氧熔窑三维仿真模拟体系通过研究全氧燃烧玻璃熔窑火焰空间和玻璃液流场的三维数学模型,开发界面友好、操作方便、参数设置容易的全氧燃烧浮法玻璃熔窑三维仿真系统,使参与玻璃熔窑设计和仿真的工程技术人员只要输入熔窑结构、燃气布置和相关边界条件等参数,玻璃熔窑三维仿真系统将自动根据使用者提供的设计要求,完成CFD建模、求解和后处理三个步骤。
图1为全氧燃烧数学模拟火焰空间温度分布图。
图1 全氧燃烧数学模拟火焰空间温度分布图进一步形成玻璃原料COD值的快速测定、玻璃的Redox控制、熔体性能、澄清新工艺、火焰空间的数值模拟等理论与关键技术,为全氧燃烧条件下排除玻璃液中的微气泡,保证优质玻璃的熔制提供工艺指导。
2全氧浮法熔窑耐火材料国产化大型全氧浮法熔窑池宽超过11 m,比国内最大的全氧玻壳、玻璃纤维窑池宽30%以上。
到目前为止,国内已经建成了600 t/d、800 t/d规模的全氧燃烧平板玻璃生产线,主要耐火材料也都是国内配套,但要使窑炉达到高质量、长寿命,对大型全氧熔窑的结构安全、关键部位耐火材料的国产化还需要深入研究。
通过总结成功经验,克服存在的不足,持续改进、不断推进全氧玻璃熔窑关键耐火材料的国产化进程。
全氧窑的长宽比是一项重要指标。
- 1、下载文档前请自行甄别文档内容的完整性,平台不提供额外的编辑、内容补充、找答案等附加服务。
- 2、"仅部分预览"的文档,不可在线预览部分如存在完整性等问题,可反馈申请退款(可完整预览的文档不适用该条件!)。
- 3、如文档侵犯您的权益,请联系客服反馈,我们会尽快为您处理(人工客服工作时间:9:00-18:30)。
玻纤行业纯氧燃烧的关键问题分析唐宇,唐秀凤(中材科技股份有限公司,南京 210000)摘要:介绍了纯氧燃烧技术在玻纤池窑上的应用,通过理论分析研究来阐述纯氧燃烧技术的先进性,通过实际应用案例来验证该技术良好的经济性和社会效益性。
指出纯氧燃烧技术是先进的玻璃熔化技术,能够广泛应用于熔制各种成分玻璃配合料,使玻纤生产能够实现高质量、低排放、降能耗的目标。
关键字:纯氧燃烧;玻璃纤维;单元窑;节能减排1.概述纯氧燃烧是一种氧化反应,即燃料(天然气、液化气、柴油、重油等)与氧气在高温下发生剧烈的氧化反应而发光发热。
任何燃烧过程都包括三个要素——燃料、氧气及高温,传统空气燃烧就是利用空气中21%的氧气来进行助燃,但是空气中约79%的氮气在高温下也会部分与氧气发生氧化反应产生大量有害物质NOx,空气燃烧产生的烟气量较大,79%的氮气也会加热至高温,带走部分热量,因此空气燃烧的热效率较低,且浪费能源污染大气[1]。
由此可见提高助燃气体中氧气的浓度是提高燃烧效率的关键措施。
随着工业化的技术进步,从空气中分离氧气的技术日渐成熟,不但制得氧气的浓度越来越高,而且制氧的成本也在不断降低,这就为纯氧燃烧创造了有利的工业化基础。
使用纯度大于91%的氧气,按照一定的氧/燃比与燃料混合燃烧,产生低动量火焰的纯氧燃烧技术应运而生。
相比空气助燃技术,纯氧燃烧技术具有火焰温度高、热量传导快、燃烧效率高、废气排放少等节能环保的优良特点。
随着工业化的持续高速发展,我国对燃料的需求越来越多,同时随着环境污染导致的问题不断恶化,对环保的要求也越来越高,因此高耗能低排放的玻纤生产线采用纯氧燃烧技术成为了一种必然的趋势。
我国工信部在2012年8月1日起宣布开始实施的新玻璃纤维行业准入条件中,明确指出新建玻璃纤维池窑拉丝生产线必须采用纯氧燃烧技术,这将大大推动我国纯氧燃烧技术的发展,同时也将为我国的节能减排事业做出巨大的贡献。
2.纯氧燃烧在玻纤池窑上的应用随着环保要求的不断提高,玻纤生产尾气中的硼酸及氟化物的污染问题也日渐突出,同时由于硼钙石与硼镁石价格较高,减少硼含量也是玻纤降低成本的一个有效途径,因此出现了不含硼和氟的无碱料方,其熔制温度以及成型温度也相应提高了,所以要求玻璃纤维的熔制技术也需要随之提高,纯氧燃烧技术的出现既满足了玻璃对熔制温度的要求,又满足了节能减排的环保要求[2]。
同时在中碱与普通无碱玻纤窑炉上采用纯氧燃烧技术,可提高玻璃液的温度使澄清均化效果更佳,这样可以进一步提高玻璃纤维的质量,并能一定程度扩大窑炉的生产能力。
2.1玻纤纯氧燃烧的特点根据纯氧燃烧技术的发展和实际应用情况,玻璃纤维池窑上纯氧燃烧一般值采用纯度≥91%的氧气为助燃介质的燃烧,它相对于传统空气助燃主要有以下燃烧特点:2.1.1热效率高,提高熔化率纯氧燃烧因氮气含量少,比空气助燃时烟气的黑度大得多,且火焰传播速度快,火焰温度高(焰芯温度可达2800℃),辐射系数大,对玻璃液辐射加强,对玻璃液的传热量增加,热效率高,熔化率增大[3]。
由于烟气量的减少,窑炉火焰空间热点向投料口方向移动,可以加速配合料熔化。
同时纯氧燃烧火焰波长短,对E玻璃的穿透性很好,池深方向温度梯度小,可提高窑炉熔化率,加强玻璃液的澄清均化,提高玻璃液的产量和质量,最大可提高窑炉熔化能力20%左右。
2.1.2 烟气量小,节能减排纯氧燃烧废气排放量减少60%以上,既减少了氮气进入的动力,又大大减少了废气带出的热量。
废气中NOx也下降80%~90%,相应减少了原料挥发,所以SO2和F2排量可下降20%,粉尘含量也可降低50%以上,减少了原料的飞扬,节省了配合料。
同时由于烟气量大幅减少,燃烧产生的烟气在窑炉中停留的时间也有所增加,这就延长了热交换的时间,提高了热传导的效率,因此纯氧燃烧带来了明显的节能减排的效果。
2.2纯氧燃烧应用实例以采用天然气作为主燃料的年产3万吨的无碱玻璃纤维池窑为例,窑炉可以节省燃料35%~40%,通路则可以节省燃料50%~60%。
表1.国内一座年产2.5万吨无碱玻纤池窑生产线纯氧改造前后的数据对比(无电助熔)玻璃量(吨/天)熔化部天然气量(Nm³/h)熔化部能耗(kcal/kg)通路天然气量(Nm³/h)通路能耗(kcal/kg)空气燃烧时68 862 2500 185 540纯氧燃烧时74 550 1502 90 243 从上表中可以看出在熔化部和通路原有空气燃烧系统改为纯氧燃烧系统后,窑炉玻璃液产量提高了8.8%,熔化部能耗降低了39.9%,通路能耗更是降低了55%。
由于纯氧燃烧后烟气量减少,废气处理量也相应减少,因此可以减少废气处理设备的投入,同时降低废气处理原料的用量及动力的消耗量。
因此纯氧燃烧在玻璃纤维池窑上应用,在经济效益上能够切实降低燃料耗量,提高产品质量,减少建设及运行投资;在社会效益上又能大大减少对环境的污染,满足国家提出的关于可持续发展的要求。
2.3玻璃纤维池窑纯氧燃烧的主要技术环节2.3.1 玻纤纯氧燃烧窑炉由于纤维玻璃相对普通平板、器皿玻璃而言,熔化温度较高,玻璃液的熔化质量和稳定性要求较高,因此熔制均采用具有较大长宽比的单元窑窑型,燃料多采用重油、天然气等优质燃料,同时对耐火材料的要求也较高。
由于采用纯氧燃烧技术后,窑炉的空间温度提高,火焰的热辐射能力增加,因此选用窑炉及通路的耐火材料时应注意这一特点。
窑炉及通路中与玻璃液接触的池壁池底耐火材料与采用空气燃烧的窑炉相差不多,但是窑炉的碹顶砖、胸墙砖以及通路的盖板砖需要选择具有优良抗高温蠕变性和耐热震性好的电熔莫来石砖,垂直烟道选用电熔锆刚玉砖;同时全窑采用良好的保温层,以提高保温节能效果。
为了更好的发挥纯氧燃烧技术的特点,提高玻璃纤维的生产质量,纯氧燃烧窑炉一般还会配套设置其他技术手段来达到最佳的综合熔制状态。
如采用电助熔进一步提高热效率,采用鼓泡器促进窑内玻璃液更加合理的流动,获取更高质量的玻璃液等。
当前综合先进的燃烧熔制技术可使E纤维玻璃熔化热效率超过40%。
2.3.2氧气的来源纯氧燃烧对氧气的浓度要求需要达到91%以上,由于使用液氧的成本较高,因此大部分玻纤生产线都是采用自建氧站或者购买管道氧气来解决氧气来源问题,同时在厂区设置液氧储罐储存液氧作为备用,这样就可以实现在制氧站检修或者故障时仍然能够向窑炉供应助燃氧气。
目前主要制氧技术有变压吸附与深冷两种。
变压吸附制氧就是空气经除尘后,由鼓风机鼓入盛有多种专用吸附剂(分子筛等)的吸附塔底部,绝大部分CO2、N2、SO2、H2O及少量O2在塔内被吸附剂吸咐,而大部分O2则透过床层从塔顶排出,得到氧含量约93%左右的纯氧。
深冷制氧设备主要由空气压缩机组(包括过滤器、压缩机、供油系统等)、空气冷却系统(空气冷却塔、水冷却塔、氟里昂冷冻机组、水泵、水过滤器等)、分子筛净化系统(净化器、加热器等)、透平膨胀机、分馏塔(上塔、下塔、过冷器等)、换热器等组成,空气经过制氧机组分离后,可获得纯氧(含氧量99%)、纯氮及各种纯净的稀有气体。
从工艺过程来看深冷法比变压吸附法工艺过程长,工艺较复杂,需用设备的种类和台数较多,且需耐受高压或超低温,投资成本高,同时制氧量越低单位耗电量也越高,但装置能力可达到较大规模,所以一般用氧量超过10000Nm³/h时采用深冷法比较合适。
变压吸附制氧法具有基建投资小、水电消耗少、经营成本低、安全性能好、操作维修简单、启动供氧特快、自动化程度高、用工少等许多优点,缺点是不能制得氧含量95%以上纯氧,且制氧量不大,一般适用于10000Nm³/h以下规模[4]。
而玻纤生产线对氧气的消耗量较低,单线一般不超3000Nm³/h,且玻纤窑炉纯氧浓度达到91%以上即可,所以综合考虑技术经济成本,年产3万t玻纤生产线一般均采用变压吸附法生产氧气。
目前,国内已有优秀的变压吸附厂家的装置工艺水平达到了国际先进水平。
例如,河南林州光远新材料有限公司选用北京北大先锋科技有限公司生产的变压吸附制氧设备,产氧量为1600 Nm³/h,产品纯度91%,投产两年多以来,设备运行一直保持稳定,100%纯氧电耗保持在0.40kwh/m3左右(含压氧),优秀的能耗指标进一步降低了生产成本。
近年来多数变压吸附厂家将制氧设备由轴向床改为径向床工艺,经此优化后,采用径向床工艺的变压吸附制氧设备比轴向床装置的电耗水平更低,工艺指标也随之提升。
北京北大先锋科技有限公司在工艺的升级与改进上做出了多方努力,是我国变压吸附制氧技术的典型代表。
2.3.3纯氧燃烧系统的组成由于纯氧燃烧是氧气与燃气直接混合燃烧,燃烧速度快,火焰温度高,因此要实现最佳稳定的燃烧状态就需要完善的系统和精密的控制来分别调节燃气与氧气的压力与流量。
符合要求的燃气、氧气进入池窑车间,经过滤、调压后,按燃烧工艺要求,分别供给窑炉两侧的燃烧器,混合后进行燃烧。
燃气量与窑内火焰空间控制点的温度联锁,随着温度的变化,由精密流量调节阀自动调节窑炉每支枪的燃气量,相应的氧气量也由精密流量调节阀按比例调节,保证燃烧充分。
在燃气系统中需设置流量计、调压稳压阀、快速切断阀、精密流量调节阀以及各参量变送器等,以保证系统安全稳定供气及燃烧完整。
3玻纤纯氧燃烧带来的问题及解决方法玻纤池窑采用纯氧燃烧后带来好处的同时也会带来一些问题,这些问题如果不引起我们的重视也会影响玻纤生产线的正常生产。
3.1泡沫问题由于采用纯氧燃烧,如控制不好极易造成窑炉内氧化性气氛过高,残氧含量约有3.5%~5%。
玻纤窑炉生产需要弱氧化性气氛来保证玻璃液不会产生还原性物质以致影响拉丝作业,但是氧化性气氛过强就会快速与配合料中的C和S反应,产生大量CO2、SO2气体,在玻璃液表面形成较厚的泡沫层,泡沫层既影响了火焰辐射热对玻璃液的传导,又会使气泡随玻璃液流入通路中影响拉丝作业。
因此采用纯氧燃烧技术后,如何消除泡沫就成了首要问题。
降低玻璃液表面泡沫至合理厚度需要注意以下几点:(1)需要严格控制配合料的COD值。
由于CO2气泡受热后体积变化较大,较易从玻璃液中排出及破裂,因此玻璃液表面泡沫中的主要气体为SO2,所以如何减少配合料中S的含量成为消泡的关键。
中碱及普通无碱料方中就需要降低甚至取消芒硝的使用量,同时严格控制其他原料中S的含量。
(2)调节火焰空间气氛,尽量降低残氧量,从而降低较高的氧化性气氛,同时可以将窑炉澄清均化区的燃烧器(最后一支或一对)火焰调节成弱还原性,进一步减少泡沫;(3)在配合料中添加碳粉。
因产生的CO2气泡较易排出,所以适当的碳粉可以消耗一部分残氧减少泡沫的产生,但是一旦碳粉添加量过多,在玻璃液熔制过程中不能被反应掉,极易造成玻璃液变成还原性,影响拉丝生产线安全,所以此方法不建议采用。